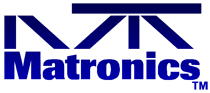 |
Matronics Email Lists Web Forum Interface to the Matronics Email Lists
|
View previous topic :: View next topic |
Author |
Message |
nuckolls.bob(at)cox.net Guest
|
Posted: Mon Jan 07, 2008 8:29 am Post subject: Electrical System Reliability (and other ???) |
|
|
At 02:23 AM 1/7/2008 -0800, you wrote:
Quote: | Hi Bob:
I'm in the beginning phase of designing my electrical system. The
following are the particulars of my setup:
Aircraft Mission - IFR (IMC is a likelihood), night and remote
backcountry operations.
Engine - Lycoming IO-540.
Glass Panel - One Dynon D180 EFIS/EMS and one Dynon D120 EFIS
both with internal battery backup. They are supposed to be able
to cross-display via Dynon's D-SAB.
Avionics - Garmin GMA-340 Audio, SL30 Nav/Com, SL40 Com, GTX 327
Transponder, GPS 496, Dynon AOA/Heated pitot tube. All of
the avionics were pre-wired by Approach/FastStack using their connecting
hub. The GPS 496 has internal batteries as well as an
external power source. I also have a ICOM IC-A23 handheld Com/VOR that I
always carry with me.
Electronic Ignition - LASAR controller with dual Slick mags. One
mag is equiped with a sensor for the LASAR system and the
other is impulse coupled. Both are inop while the electronic system is
operating. The system has the "Bush Kit" which is
supposed to default to operating on the mags alone in the event of
electrical or software failure. The controller is supposed
to operate with voltages down to 5.5volts.
Vacuum System - None
Alternator/Regulator - B&C L-60 Alternator and B&C LR3C-14
Regulator.
Fuel Injection - Bendix style fuel injection with Airfllow
Performance auxiliary fuel pump.
Electrical Controls - Three axis RAC trim system, Electric
flaps, Electric cowl flaps.
Lighting - Dual Strobe lights, Nav Lights, Dual taxi lights, Dual
landing lights, Dual "Type C4A" military style cockpit lights.
Autopilot - TruTrak Digiflight II two-axis autopilot.
Battery(s) - My intent is to use the Odyssey series battery(s).
Before I go any further with the design I need to make the following
decisions:
1. Single or Dual Alternator. If dual alternator, size of second
alternator and type of second regulator.
2. Single or Dual Battery. If dual battery, isolated systems or
combined and capacity of each battery.
3. Glass Panel alone or Glass Panel with back-up "Steam
Gauges", Airspeed, Altimeter, Turn Coordinator, Compass.
I have read through Sections 2, 3 and 17 of your book several times as
well as the wiring diagrams and various articles on your site. These
offer a great amount of information and advice which I'm sure would allow
a knowledgeable person to make the proper decisions. However, my
knowledge, experience and confidence are limited so I would like to
confirm with you my interpretation of the information and get your
confirmation/critique thereof. Here goes:
The first is that designing for complete battery failure i.e. a
dead short that would take down the whole system in
NOT necessary. This seems to be covered well on page
17-11 in a paragraph that contains the following, "Last, the
antiquated concerns for battery "failure"....RG battery
reliability....drives the probability of gross battery failure to
zero." However, I would like to confirm that the Odyssey
batteries would fall under the same class as "RG battery reliability" and
that I would NOT need to design for battery failure given my
intended mission and battery selection. Would you concur with that??
Regarding decision number #1: Your comments on several pages of
sec. 17 clearly indicate your preference for
dual alternators. My setup in heavily dependent on
electrical systems for normal operations. Based on that and on
your comments, I would opt for a second alternator
using B&C SD-20 Alternator and B&C SB1B-14 Standby Controller. Given
the need of a second alternator, the weight penalty between the
20amp and 8 amp models is 3 pounds. It would seem
the 20amp would provide near normal operations for as
long as it works should the primary alternator fail. Would you concur
with that??
|
Is it your design goal to have 100% capability of
the panel with one alternator out . . . or sufficient
snort to comfortably complete the mission?
Quote: | Regarding decision number #2: This has several sub-parts.
A - Your comments in sec. 17 seem to indicate that with a
dual alternator setup as I opted for in #1, dual batteries
with isolated systems are NOT necessary as a design point
for in-flight electrical failure. I would like to avoid the
dual battery contactors and the crossfeed
contactor by using a single battery source. Would you concur with
that?? If it makes a difference, the battery(s),
regulators and LASAR controller will be located on the cabin side of the
firewall.
B - One of the mission requirements is backcountry
operations. Given that, one my design points was the ability to
start the plane with a completely dead primary (cranking)
battery, say as a result of leaving the master on.
|
Why would you even consider that? You're obviously very
concerned about NOT having necessary things operate 100%
of the time but stacking lots of hardware on top of the
probability that a pilot walks away from the airplane leaving
things turned on is running off in the wrong direction.
The most reliable system is that which has the fewest parts.
The most reliable flight system has a minimum of options for
the pilot consider when something is not working. A simple
flashing low voltage warning light (comes with the LR3) tells
you that a master switch is ON after engine shutdown . . .
so that scenario is unworthy of consideration . . .
Quote: | That is the reason I opted for the LASAR system with the
bush kit. However, given my configuration I would need some sort of
standby electrical power. To that end I am
considering two options:
Option 1: Design in a permanent Non-Cranking (Aux)
battery and bus as shown in fig. Z-35. to power the Fuel
Pump, LASAR system, and one EFIS/EMS.
Option 2: Design in an external power plug for the
fuel pump ONLY and carry a small battery with me
during backcountry operations
ONLY. With my configuration I do not need the EFIS/EMS or the LASAR
system to function to just start the
engine. The only thing I really need is a few seconds of fuel pump
operation to pressurize the system in order to hand
prop the engine. If I was backcountry I would have 12 volts of battery
power someplace anyway.
My choice would be for Option 2. Would you concur
with that???
C - Odyssey offers several batteries ranging in
capacity form 14 to 28AH, in cranking power from 535 to
925CCA and in weight from 12.0 to 26.0 lbs. In
the unlikely event of the same flight failure of both
alternator/regulator systems opted for in #1, and
according to the method used on page 17-6, any of the batteries would
satisfy the requirements of my E-bus. However, I am
not so sure about starting power for normal operations. My engine is
fuel injected and high compression. My space
limitations would preclude me from installing the 28AH/925CCA/26lb
battery. That would leave two preferred
batteries; The PC545 (14AH/545CCA/12.6lbs) and the PC680
(17AH/680CCA/15.4lbs). If necessary I could install
two of either the PC545 or PC680 batteries wired together to act as
one. My first preference would be a single PC680,
second would be two of the PC545's and lastly two of the PC680's.
Here I would simply ask for your recommendation as to
which way to go??.
Regarding decision #3: Well this started out to be a long and
involved question but as I was typing out my reasoning
and explanation, I made the decision to opt for the back up
gauges. I intend to file IFR for trips and that means at some point
I will probably be in IMC and there is just no way that I am
going into IMC without them. Thanks for helping me get that
one out of the way. Its been bothering me for months.
There are a couple of other questions I have:
On page 17-10 you say, "When you trade generators for
alternators, loss of a battery contactor may well precipitate total loss
of electrical power. Alternators, don't run well without a
battery". Yet when I look at Figs 17-2,3,4,5,6, and 8, all of them place
the Alt field switches on the main bus with the contactor in the path to
the battery. If I understand your statement correctly, it seems that if
you loose a single contactor in any except fig 17-5 & 6, Dual Batteries,
you would lose all charging systems. Shouldn't there be a pathway to
energize the Alt fields thru the E bus in case of a contactor
failure. Is my reasoning correct?? It looks like Fig Z-13/20 does that
for the Aux Alt only and Fig Z-12 doesn't for either Alt. Is that
correct?? Wouldn't you want to be able to energize both Alt systems from
the E-bus in case of contactor failure with a single battery??? Or
alternatively, what about two contactors for a single battery??? They're
cheap enough??? Would that work???
|
The z-figures are crafted to offer comfortable continued
flight to intended destination while having suffered the
failure of one piece of the DC power generation and distribution
system.
Quote: |
I really don't understand what P-leads are or the difference
between P-mags and E-mags. What do I have with the LASAR system???
|
A lot of unnecessarily complex and expensive hardware.
Quote: | I looked but couldn't find any articles to explain mag operation or
what they are. Could you point be to the proper article???
|
I'm not sure it would benefit you to delve into the technical
merits of the various ignition systems at this point. You're
getting wrapped around too many axles at the same time.
Unless you're anticipating replacing the Lasar system with
something else based on new knowledge, the I'll suggest you
go with what you have.
If I were building your airplane, I'd figure out a way to
make Z-13 work. The Lasar system doesn't need extra-ordinarily
reliable electrical energy . . . that's why it was designed
that way . . . which is true of the PMag as well. But Z-14
can and does offer the ultimate in overall system reliability
and versatility for keeping plenty of stuff on the panel
working in spite of one and in some cases two failures of
equipment on one tank full of fuel.
It's my recommendation that you go with Z-14 as published
and start filling out your load analysis forms for all the
busses. Go to my website and search on "load analysis". Then
print out copies of
http://www.aeroelectric.com/articles/LoadAnalysis.pdf
for each of the four buses and decide what items will
be fed from each bus.
I presume that you presently fly the same kinds of missions
in a type certificated aircraft. Know that ANY of the choices
offered in the Z-figures will offer you a "step up" from
that which is already flown in hundreds of thousands of
spam-cans for nearly 100 years. Electrical system failures
as the precipitating event in a disaster are an exceedingly
tiny portion of root cause.
Don't spend a lot of time worrying this. Your craftsmanship
is going to have a stronger influence on success than selection
of parts and/or architecture.
Bob . . .
| - The Matronics AeroElectric-List Email Forum - | | Use the List Feature Navigator to browse the many List utilities available such as the Email Subscriptions page, Archive Search & Download, 7-Day Browse, Chat, FAQ, Photoshare, and much more:
http://www.matronics.com/Navigator?AeroElectric-List |
|
|
|
Back to top |
|
 |
flagstone(at)cox.net Guest
|
Posted: Mon Jan 07, 2008 11:55 am Post subject: Electrical System Reliability (and other ???) |
|
|
Bob:
You're right. Ignorance is bliss. Z-14 it is.
Thanks.
Mark
| - The Matronics AeroElectric-List Email Forum - | | Use the List Feature Navigator to browse the many List utilities available such as the Email Subscriptions page, Archive Search & Download, 7-Day Browse, Chat, FAQ, Photoshare, and much more:
http://www.matronics.com/Navigator?AeroElectric-List |
|
|
|
Back to top |
|
 |
|
|
You cannot post new topics in this forum You cannot reply to topics in this forum You cannot edit your posts in this forum You cannot delete your posts in this forum You cannot vote in polls in this forum You cannot attach files in this forum You can download files in this forum
|
Powered by phpBB © 2001, 2005 phpBB Group
|