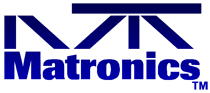 |
Matronics Email Lists Web Forum Interface to the Matronics Email Lists
|
View previous topic :: View next topic |
Author |
Message |
flagstone(at)cox.net Guest
|
Posted: Wed Jan 09, 2008 1:17 am Post subject: Shielded Wire |
|
|
Bob:
I've read thru the various sections of the book on grounding, wire selection, noise etc, as well as the Blue Mountain article and the FAQ.
I already done some wiring in my wing and I'm concerned now that I may have done it incorrectly.
Electrically, my wing contains:
Strobe light, power supply mounted at wing tip
Nav Light
Landing light
Taxi light
Pitot heat power
Pitot heat controller
Fuel pump
Fuel flow sensor
Remote compass
Potentiometer
I used twisted shielded wire for all wires with return wires for all power supplies. It was intended that all the return wires would terminate at what you call a "single point" ground. All power leads/returns are routed thru the nose ribs, all control/sensor wires are routed along the rear spar. They don't come together until the panel. The wing is all metal, fuselage is truss tube.
For each power lead, I connected the shielding and the return wire together at the load location and grounded them locally as well as running the return wire back to the "single point" ground. Then, I was going to connect the return wire and the shielding at the "single point" and ground again there.
In reading Blue Mountain's comment, "Shields are connected at the source end, and cut off flush at the load end" and your comment on pg 18-14, "I'll further suggest that there's is greater risk that shielding improperly terminated at both ends is 100x more likely to be the root cause of a noise problem.....", indicates that what I have done may cause problems. It was my understanding at the time that that was the correct way to do it. Now I can't find what led me to that understanding.
For better or worse, I'm stuck using the shielded wire so what should I do to properly install it. Does it cause problems to ground the shield at both ends. Does it cause problems to ground the return wire locally and back at the "single point ground."
Your comments and explanation would be appreciated.
Thanks
Mark
[quote][b]
| - The Matronics AeroElectric-List Email Forum - | | Use the List Feature Navigator to browse the many List utilities available such as the Email Subscriptions page, Archive Search & Download, 7-Day Browse, Chat, FAQ, Photoshare, and much more:
http://www.matronics.com/Navigator?AeroElectric-List |
|
|
|
Back to top |
|
 |
nuckolls.bob(at)cox.net Guest
|
Posted: Wed Jan 09, 2008 8:34 am Post subject: Shielded Wire |
|
|
At 08:31 AM 1/9/2008 -0800, you wrote:
Quote: | Bob:
I've read thru the various sections of the book on grounding, wire
selection, noise etc, as well as the Blue Mountain article and the FAQ.
I already done some wiring in my wing and I'm concerned now that I may
have done it incorrectly.
Electrically, my wing contains:
Strobe light, power supply mounted at wing tip
Nav Light
Landing light
Taxi light
Pitot heat power
Pitot heat controller
Fuel pump
Fuel flow sensor
Remote compass
Potentiometer
I used twisted shielded wire for all wires with return wires for all power
supplies. It was intended that all the return wires would terminate at
what you call a "single point" ground. All power leads/returns are routed
thru the nose ribs, all control/sensor wires are routed along the rear
spar. They don't come together until the panel. The wing is all metal,
fuselage is truss tube.
|
It's not necessary to separate these bundles . . .
but it doesn't hurt.
Quote: |
For each power lead, I connected the shielding and the return wire
together at the load location and grounded them locally as well as running
the return wire back to the "single point" ground. Then, I was going to
connect the return wire and the shielding at the "single point" and ground
again there.
|
One and only one ground . . . local is probably fine
but not both places . . .
Quote: |
In reading Blue Mountain's comment, "Shields are connected at the source
end, and cut off flush at the load end" and your comment on pg 18-14,
"I'll further suggest that there's is greater risk that shielding
improperly terminated at both ends is 100x more likely to be the root
cause of a noise problem.....", indicates that what I have done may cause
problems. It was my understanding at the time that that was the correct
way to do it. Now I can't find what led me to that understanding.
|
How many shielded wires do you have? Generally
speaking, p-leads, strobe-head leads and the occasional
avionics signal leads are shielded and the installation
instructions for those systems should be followed for
how to handle shield grounds. In some cases, a shield may
be PART of a signal or power distribution path and is CONNECTED
at both ends . . . but only one of those ends will be 'ground'.
Quote: |
For better or worse, I'm stuck using the shielded wire so what should I do
to properly install it. Does it cause problems to ground the shield at
both ends. Does it cause problems to ground the return wire locally and
back at the "single point ground."
Your comments and explanation would be appreciated.
|
Where, if any place have you arbitrarily added
shields where they were not called for by
manufacturer's installation instructions?
I am reminded of a telephone call I received from
a LongEz builder about 15 years ago. He recited
the fact that he had wired his airplane with shielded
wire throughout and added a litany of devices on which
he had added "noise filters". He ended the recitation
with, "What else do I need?" I was somewhat taken aback
and had to inquire, "What kind of noise problems are
you experiencing?"
"Oh, none yet. The airplane hasn't flown. I'm just
trying to make sure that I don't have a noise
problem when I'm finished."
I had to inform him that he'd added a lot of unnecessary
pounds and much $time$ to the effort of assembling
his project. I had to advise him to rip it all out
and start over but taking his cues from (1) manufacturer's
installation instructions and (2) observations of
the recipes for success by others - get the service
manual for a C-172 and see what wires are shielded.
I'm curious as to your statement about "stuck using
shielded wire" . . . let's first explore what wires
are shielded and why . . . and then sort out the
best methodology for handling the shields.
Bob . . .
| - The Matronics AeroElectric-List Email Forum - | | Use the List Feature Navigator to browse the many List utilities available such as the Email Subscriptions page, Archive Search & Download, 7-Day Browse, Chat, FAQ, Photoshare, and much more:
http://www.matronics.com/Navigator?AeroElectric-List |
|
|
|
Back to top |
|
 |
flagstone(at)cox.net Guest
|
Posted: Wed Jan 09, 2008 6:14 pm Post subject: Shielded Wire |
|
|
Bob:
Maybe this is a little clearer:
All the wires in the wing are shielded.
The wire used is MIL-DTL-27500TG2T14. That particular one is 12AWG, two
conductor, twisted pair, shielded and sheathed. The unshielded version was
not available without special order and long lead time. The weight
difference between shielded and unshielded was 2.75lbs for 1,000 feet so I
got the shielded version.
There are no manufacturer's recommendations per se. Sizing for loads was
done as per AC43-13-2A based on the power consumption rating for each load.
All power loads have a power lead and a return lead. The sensors have how
ever many wires are required by the sensor.
Ignoring connectors, fuses, switches, ground buss etc, all power loads were
to be routed as follows:
Power lead: Bat(+) -to- Load.
Return lead: Load -to- Bat (-) and, Load -to- Airframe (at Local
Ground) -to- Bat (-)
Shielding: - Bat(-) -to- Airframe (at Local Ground)
I can't find where I read it but something led me to believe that if you
were going to use shielded wire it was OK to do it the way I did.
So, given that I am going to use the wire I have, that I am going to run a
return lead for all power loads and that I want to hook up the shielding on
the wire, what is the correct way to do it?
Regarding the return lead, I'm pretty clear that the return lead should not
be grounded at the Bat (-) and at a Local ground. Quote from your response:
" One and only one ground . . . local is probably fine
but not both places . . ."
No problem changing it but why is it such a bad thing to do it that way.
Using the landing light as an example. What harm does it cause to ground it
locally and also run a lead back to the bat (-). Why is that worse than
only grounding locally and the corollary, why is that not better than only
running the lead back to the bat (-). Is the same applicable to the
strobe's power unit and the fuel pump. Would it be the same for something
like a flap actuator motor.
Regarding the shielding: I'm less clear on this. Removing the local ground
from the return lead will also take the shielding out of the ground path
from the Load to the Bat(-). But what about grounding the shielding itself.
Again using the landing light as an example, what is the difference between
grounding at both ends and grounding only at the Bat(-). Is the same
applicable to the strobe's power unit, fuel pump and flap motor.
Looking forward to your explanations.
Thanks
Mark
| - The Matronics AeroElectric-List Email Forum - | | Use the List Feature Navigator to browse the many List utilities available such as the Email Subscriptions page, Archive Search & Download, 7-Day Browse, Chat, FAQ, Photoshare, and much more:
http://www.matronics.com/Navigator?AeroElectric-List |
|
|
|
Back to top |
|
 |
nuckolls.bob(at)cox.net Guest
|
Posted: Thu Jan 10, 2008 1:02 pm Post subject: Shielded Wire |
|
|
At 06:12 AM 1/10/2008 -0800, you wrote:
Quote: |
Bob:
Maybe this is a little clearer:
All the wires in the wing are shielded.
|
?Why?
Quote: | The wire used is MIL-DTL-27500TG2T14. That particular one is 12AWG, two
conductor, twisted pair, shielded and sheathed. The unshielded version was
not available without special order and long lead time. The weight
difference between shielded and unshielded was 2.75lbs for 1,000 feet so I
got the shielded version.
There are no manufacturer's recommendations per se. Sizing for loads was
done as per AC43-13-2A based on the power consumption rating for each load.
All power loads have a power lead and a return lead. The sensors have how
ever many wires are required by the sensor.
Ignoring connectors, fuses, switches, ground buss etc, all power loads were
to be routed as follows:
Power lead: Bat(+) -to- Load.
Return lead: Load -to- Bat (-) and, Load -to- Airframe (at Local
Ground) -to- Bat (-)
Shielding: - Bat(-) -to- Airframe (at Local Ground)
I can't find where I read it but something led me to believe that if you
were going to use shielded wire it was OK to do it the way I did.
|
I'm not sure I'm interpreting you words into an
accurate schematic of your architecture but since
the use of shielding where shielding adds no value,
then exactly how you wire it has no significance
with respect to performance.
Quote: | So, given that I am going to use the wire I have, that I am going to run a
return lead for all power loads and that I want to hook up the shielding on
the wire, what is the correct way to do it?
Regarding the return lead, I'm pretty clear that the return lead should not
be grounded at the Bat (-) and at a Local ground. Quote from your response:
" One and only one ground . . . local is probably fine
but not both places . . ."
No problem changing it but why is it such a bad thing to do it that way.
Using the landing light as an example. What harm does it cause to ground it
locally and also run a lead back to the bat (-). Why is that worse than
only grounding locally and the corollary, why is that not better than only
running the lead back to the bat (-). Is the same applicable to the
strobe's power unit and the fuel pump. Would it be the same for something
like a flap actuator motor.
|
My personal goals for system design are to achieve
the desired level of performance with a minimum of
parts and minimized $time$ to acquire/install/maintain.
You appear to be asking advice for doing things that
I would not choose to do because they do not add
value under the design goals stated. Doing doesn't
necessarily degrade performance but it's certain
not to enhance it. Are there risks for venturing outside
the simple ideas that support conventional wisdom?
Difficult to predict but probably not.
Quote: | Regarding the shielding: I'm less clear on this. Removing the local ground
from the return lead will also take the shielding out of the ground path
from the Load to the Bat(-). But what about grounding the shielding itself.
Again using the landing light as an example, what is the difference between
grounding at both ends and grounding only at the Bat(-). Is the same
applicable to the strobe's power unit, fuel pump and flap motor.
Looking forward to your explanations.
|
A detailed trek through the physics from which
conventional wisdom and common practices evolved
is beyond the scope of what I can do here on
the List. I did a short-course on noise propagation
issues and solutions a few years ago at Hawker-
Beech . . . and that was a 4-hour, Power-Point
presentation.
Suffice it to say that if my mental image
for what you've described is correct,
then there is no reason to expect degradation
of performance and no reason to expect an
enhancement of performance. I.e, shielding
added without specific noise propagation
problems to be solved only adds to weight
of the airplane and cost of ownership. It
follows then that I have no advice based
on physics to offer for "doing it right".
Bob . . .
| - The Matronics AeroElectric-List Email Forum - | | Use the List Feature Navigator to browse the many List utilities available such as the Email Subscriptions page, Archive Search & Download, 7-Day Browse, Chat, FAQ, Photoshare, and much more:
http://www.matronics.com/Navigator?AeroElectric-List |
|
|
|
Back to top |
|
 |
Eric M. Jones
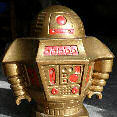
Joined: 10 Jan 2006 Posts: 565 Location: Massachusetts
|
Posted: Thu Jan 10, 2008 2:54 pm Post subject: Re: Shielded Wire |
|
|
Okay, cut this message out and punch three holes into it and stick it into your book. This is the cat's meow on coaxial cable shielding and grounding from Kimmel Gerke Associates. I hope they balance my liberal use of their stuff with the free advertising given here.
http://www.emiguru.com/kgb/sum1996.htm Kimmel Gerke Bullets.
"For many designers, cables and connectors are an afterthought. After all, they just connect things together, right? But cables and connectors are major entry and exit points for EMI into and out of electronic systems. They act as "hidden antennas" for radiated energy, and "hidden conduits" for conducted energy.
"In fact, cables and connectors are so important, they are the often the first things we check out when troubleshooting EMI problems in a system. Here are a few thoughts on cable and connector design for EMI.
Trade off shielding for filtering. If you don't filter I/O interfaces, then you must assume that the highest frequencies inside the unit will end up on the cable wires. (Or you must assume the cables will intercept the highest frequencies and bring them into the unit.)
"Just because that RS-232 interface is only operating in the kilobaud range doesn't stop higher frequencies from hitching a "free ride" on the cables. We've solved many radiated problems (emissions and immunity) by adding simple filters to interfaces that were only supposed to carry "slow" or "low frequency" signals.
"The alternate to filtering the cables is shielding the cables. We generally prefer to filter slower cables, since it's usually more cost effective and easier to maintain EMI integrity.
"Ground the cable shield. If you do decide to use shielded cables, then the immediate question becomes how best to ground the cable shield. The correct method depends on both threat frequencies and circuit impedance levels.
"For problem frequencies below 10 kHz [audio], the preferred approach is to ground one only one end of the shield. This is to prevent "ground loop" coupling from the cable shield to the inner wires. This is particularly important for preventing 60 Hz coupling into low level/high impedance circuits used in audio or instrumentation systems.
"Unfortunately, this is exactly the wrong thing to do for high frequency threats. For most RF situations [above 10 kHz], the preferred approach is to ground both ends of the cable shield, to minimize coupling at the open end due to standing wave effects. So what do you do if both threats exist? You can ground one end with a small capacitor (1,000- 10,000 pf typical) or you can use two shields - one grounded on one end, and the other grounded on both ends. In the latter case, the shields must be insulated from each other.
"One more case where both ends must be grounded is the low frequency/low impedance case, where magnetic fields are the major culprit. In this case, the strategy is to minimize "loop size" by providing an adjacent return path for noise currents. This is often necessary in electrical sub-stations, where large 60 Hz magnetic fields exist due to the high current levels. Most of the time, however, single point grounding at low frequencies is the preferred approach.
"Use Care With Connector Terminations. This is extremely important for shielded cables with EMI threats above about 1 MHz. Poor joints (or worse, "pigtail" connections from the shield to the connector) are a leading cause EMI-induced failures on shielded cables. We've seen 20 dB increases in emissions, and 10 fold reductions in ESD immunity due to poor connections. (Remember, with a 1 nsec edge rate, ESD is a 300 MHz EMI problem.)
"To maintain high frequency cable shield integrity, you need a circumferential bond between the cable shield and the connector shell. In addition you need full metal-to-metal between the mating connectors.
Finally, you need a solid connector-to-chassis connection. One problem we often see here is with chassis connectors that overlap connector cutouts. The imprecise fit creates a slot that very effectively couples high frequency energy directly to/from the cable shield. Think in terms of a garden hose -you need a very tight connection at the faucet, or else it leaks.
"What About The Cable Shield Itself? Yes, this is a valid concern, but only after you have addressed the connector termination issues. For frequencies below about 10 MHz, most cable shielding materials behave about the same, and provide very respectable amounts of shielding. For frequencies above about 10 MHz, however, the cable construction becomes important. Loose single braids become increasingly leaky, so above 10 MHz, you may need high density braid shields. Double braids work very well here, as do braid over Mylar cable shields. For high frequencies, both shields should be connected together. "
| - The Matronics AeroElectric-List Email Forum - | | Use the List Feature Navigator to browse the many List utilities available such as the Email Subscriptions page, Archive Search & Download, 7-Day Browse, Chat, FAQ, Photoshare, and much more:
http://www.matronics.com/Navigator?AeroElectric-List |
|
_________________ Eric M. Jones
www.PerihelionDesign.com
113 Brentwood Drive
Southbridge, MA 01550
(508) 764-2072
emjones(at)charter.net |
|
Back to top |
|
 |
nuckolls.bob(at)cox.net Guest
|
Posted: Fri Jan 11, 2008 8:25 am Post subject: Shielded Wire |
|
|
Before folks get too obsessed with this exercise, know that
Bill Kimmel and Daryl Gerke are the acknowledged gurus of
EMI prevention and control. I've taken Bill's two-day
course and companies I work for have used their assistance
many times for solving protracted problems. I have the
course notebook on shelf above my desk.
MOST of what's addressed in this posting deals with situations
that are not found in your light aircraft electrical system and
only a few issues will be a part of your avionics installation.
Further, these "bullets" are all true but lifted out of context
of the several-to-many minutes of discussion that preceded or
followed it in the course of understanding the physics behind
the idea. "Bullets" or "rules of thumb" are exceedingly poor
substitutes for understanding, especially this set which deal
with situations that the astute system designer should have already
considered the issues before you bought the product.
This illustrates the rationale for my suggestion that the
manufacturer's installation instructions should be your golden
source for how shields should be treated and whether or not
they are even necessary. THOSE are the guys who should have
taken Bill's course (or equal) and they've already done the
homework (EMC lab or extensive field trials where the effects
of EMI were the focus of attention).
For the general population of OBAM aircraft builders to clutch
onto these "twigs of wisdom" in the flood of potential EMI problems
is not a good use of $time$. While the data are good, the likelihood
that the neophyte wire slinger in an RV is going to extract a
project-saving solution to a problem is small and the expenditure
of $time$ will be significant.
If anyone is motivated enough to acquire some skills in this
arena, then it needs to be supported by the sum total of books
and articles from which these gems of wisdom were plucked and
probably the support of a capable teacher to help assemble the
simple-ideas into good inventions. If you do encounter some form
of EMI problem in your project, the likelihood of cherry-picking a
solution from the list below is small.
Bob . . .
At 02:54 PM 1/10/2008 -0800, you wrote:
Quote: |
Okay, cut this message out and punch three holes into it and stick it into
your book. This is the cat's meow on coaxial cable shielding and grounding
from Kimmel Gerke Associates. I hope they balance my liberal use of their
stuff with the free advertising given here.
http://www.emiguru.com/kgb/sum1996.htm Kimmel Gerke Bullets.
"For many designers, cables and connectors are an afterthought. After all,
they just connect things together, right? But cables and connectors are
major entry and exit points for EMI into and out of electronic systems.
They act as "hidden antennas" for radiated energy, and "hidden conduits"
for conducted energy.
"In fact, cables and connectors are so important, they are the often the
first things we check out when troubleshooting EMI problems in a system.
Here are a few thoughts on cable and connector design for EMI.
Trade off shielding for filtering. If you don't filter I/O interfaces,
then you must assume that the highest frequencies inside the unit will end
up on the cable wires. (Or you must assume the cables will intercept the
highest frequencies and bring them into the unit.)
"Just because that RS-232 interface is only operating in the kilobaud
range doesn't stop higher frequencies from hitching a "free ride" on the
cables. We've solved many radiated problems (emissions and immunity) by
adding simple filters to interfaces that were only supposed to carry
"slow" or "low frequency" signals.
"The alternate to filtering the cables is shielding the cables. We
generally prefer to filter slower cables, since it's usually more cost
effective and easier to maintain EMI integrity.
"Ground the cable shield. If you do decide to use shielded cables, then
the immediate question becomes how best to ground the cable shield. The
correct method depends on both threat frequencies and circuit impedance
levels.
"For problem frequencies below 10 kHz [audio], the preferred approach is
to ground one only one end of the shield. This is to prevent "ground loop"
coupling from the cable shield to the inner wires. This is particularly
important for preventing 60 Hz coupling into low level/high impedance
circuits used in audio or instrumentation systems.
"Unfortunately, this is exactly the wrong thing to do for high frequency
threats. For most RF situations [above 10 kHz], the preferred approach is
to ground both ends of the cable shield, to minimize coupling at the open
end due to standing wave effects. So what do you do if both threats exist?
You can ground one end with a small capacitor (1,000- 10,000 pf typical)
or you can use two shields - one grounded on one end, and the other
grounded on both ends. In the latter case, the shields must be insulated
from each other.
"One more case where both ends must be grounded is the low frequency/low
impedance case, where magnetic fields are the major culprit. In this case,
the strategy is to minimize "loop size" by providing an adjacent return
path for noise currents. This is often necessary in electrical
sub-stations, where large 60 Hz magnetic fields exist due to the high
current levels. Most of the time, however, single point grounding at low
frequencies is the preferred approach.
"Use Care With Connector Terminations. This is extremely important for
shielded cables with EMI threats above about 1 MHz. Poor joints (or worse,
"pigtail" connections from the shield to the connector) are a leading
cause EMI-induced failures on shielded cables. We've seen 20 dB increases
in emissions, and 10 fold reductions in ESD immunity due to poor
connections. (Remember, with a 1 nsec edge rate, ESD is a 300 MHz EMI problem.)
"To maintain high frequency cable shield integrity, you need a
circumferential bond between the cable shield and the connector shell. In
addition you need full metal-to-metal between the mating connectors.
Finally, you need a solid connector-to-chassis connection. One problem we
often see here is with chassis connectors that overlap connector cutouts.
The imprecise fit creates a slot that very effectively couples high
frequency energy directly to/from the cable shield. Think in terms of a
garden hose -you need a very tight connection at the faucet, or else it leaks.
"What About The Cable Shield Itself? Yes, this is a valid concern, but
only after you have addressed the connector termination issues. For
frequencies below about 10 MHz, most cable shielding materials behave
about the same, and provide very respectable amounts of shielding. For
frequencies above about 10 MHz, however, the cable construction becomes
important. Loose single braids become increasingly leaky, so above 10 MHz,
you may need high density braid shields. Double braids work very well
here, as do braid over Mylar cable shields. For high frequencies, both
shields should be connected together. "
--------
Eric M. Jones
www.PerihelionDesign.com
113 Brentwood Drive
Southbridge, MA 01550
(508) 764-2072
emjones(at)charter.net
|
| - The Matronics AeroElectric-List Email Forum - | | Use the List Feature Navigator to browse the many List utilities available such as the Email Subscriptions page, Archive Search & Download, 7-Day Browse, Chat, FAQ, Photoshare, and much more:
http://www.matronics.com/Navigator?AeroElectric-List |
|
|
|
Back to top |
|
 |
|
|
You cannot post new topics in this forum You cannot reply to topics in this forum You cannot edit your posts in this forum You cannot delete your posts in this forum You cannot vote in polls in this forum You cannot attach files in this forum You can download files in this forum
|
Powered by phpBB © 2001, 2005 phpBB Group
|