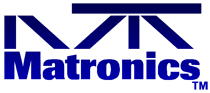 |
Matronics Email Lists Web Forum Interface to the Matronics Email Lists
|
View previous topic :: View next topic |
Author |
Message |
eagerlee
Joined: 28 Jan 2006 Posts: 35
|
Posted: Mon Mar 03, 2008 9:08 pm Post subject: lessons learned installing plexiglas with Weld-on 10 |
|
|
We just finished building our windscreen faring so now its on to bigger and better things like "trimming out" the final finish of the doors, windows and windscreen. The gluing of the door windows was easy. The first one we did on the bench per the directions except we applied freshly mixed glue to both the plexi and the fiberglass ledge. A few days later we installed the door to the cabin and then: AHH!! We found 3 small cracks on the edge where one of the clamps held the plexi tight against the fiberglass ledge. We stop drilled the cracks and changed technique for the second door/window installation. The door was installed on the cabin complete with hinges and latches and trimmed to give a good flush fit. We used four nylon straps around the entire fuselage and cabin with wooden blocks to apply pressure at the window edges. This pressure was left in place for about 22 hours and the results were great with NO cracks. We then did both rear cabin windows together using the four strap method of holding them in place and when we removed the straps and blocks we were saddened by the discovery of dozens of small "feathery" cracks at the pressure points. We thought of starting over with the rear windows but e-mailed Van's and when Scott said that other builders reported these cracks (Van's RV-10 with 1100 hours has them) but there have been ZERO failures, we decided to stress the cracks to see if we could get them to "run" into the center of the window. We applied heat to get the temperature of the window bond up to where the Summer Colorado sun might cause it to rise. Then we applied an ice pack to get the temperature down to where the lower flight levels might cause it to fall. An amazing result - the cracks disappeared. I don't mean that they went away - I mean they were VERY difficult (in some cases, impossible) to see. We did the windscreen with a combination of clamps on the sides and a strap around the cabin to give us holding pressure across the top. We got several small cracks at the pressure points of the clamps - none at the strap. Our final conclusion is that the cracks are caused by high clamping pressure over time and the best way to avoid them when using Weld-on 10 is to remove your clamps (or straps) after just a few hours, maybe three of four, and keep the pressure down to no more than is needed to keep the plexi flush with the cabin. We heated all our weld-on 10 bonds to stress relieve them.
Paul Hahn
#40203
| - The Matronics RV10-List Email Forum - | | Use the List Feature Navigator to browse the many List utilities available such as the Email Subscriptions page, Archive Search & Download, 7-Day Browse, Chat, FAQ, Photoshare, and much more:
http://www.matronics.com/Navigator?RV10-List |
|
|
|
Back to top |
|
 |
indigoonlatigo(at)msn.com Guest
|
Posted: Tue Mar 04, 2008 7:49 am Post subject: lessons learned installing plexiglas with Weld-on 10 |
|
|
You mention Colorado. How warm was the shop while instailing these windows?
John G. 409
Quote: | Subject: lessons learned installing plexiglas with Weld-on 10
From: eagerlee(at)comcast.net
Date: Mon, 3 Mar 2008 21:08:35 -0800
To: rv10-list(at)matronics.com
--> RV10-List message posted by: "eagerlee" <eagerlee(at)comcast.net>
We just finished building our windscreen faring so now its on to bigger and better things like "trimming out" the final finish of the doors, windows and windscreen. The gluing of the door windows was easy. The first one we did on the bench per the directions except we applied freshly mixed glue to both the plexi and the fiberglass ledge. A few days later we installed the door to the cabin and then: AHH!! We found 3 small cracks on the edge where one of the clamps held the plexi tight against the fiberglass ledge. We stop drilled the cracks and changed technique for the second door/window installation. The door was installed on the cabin complete with hinges and latches and trimmed to give a good flush fit. We used four nylon straps around the entire fuselage and cabin with wooden blocks to apply pressure at the window edges. This pressure was left in place for about 22 hours and the results were great with NO cracks. We then did both rear cabin windows together using !
the four strap method of holding them in place and when we removed the straps and blocks we were saddened by the discovery of dozens of small "feathery" cracks at the pressure points. We thought of starting over with the rear windows but e-mailed Van's and when Scott said that other builders reported these cracks (Van's RV-10 with 1100 hours has them) but there have been ZERO failures, we decided to stress the cracks to see if we could get them to "run" into the center of the window. We applied heat to get the temperature of the window bond up to where the Summer Colorado sun might cause it to rise. Then we applied an ice pack to get the temperature down to where the lower flight levels might cause it to fall. An amazing result - the cracks disappeared. I don't mean that they went away - I mean they were VERY difficult (in some cases, impossible) to see. We did the windscreen with a combination of clamps on the sides and a strap around the cabin to give us holding pre!
ssure across the top. We got several small cracks at the pres!
sure poi
nts of the clamps - none at the strap. Our final conclusion is that the cracks are caused by high clamping pressure over time and the best way to avoid them when using Weld-on 10 is to remove your clamps (or straps) after just a few hours, maybe three of four, and keep the pressure down to no more than is needed to keep the plexi flush with the cabin. We heated all our weld-on 10 bonds to stress relieve them.
Paul Hahn
#40203
Read this topic online here:
http://forums.matronics.com/viewtopic.php?p=167577#167577
=======================
|
&g==================
[quote][b]
| - The Matronics RV10-List Email Forum - | | Use the List Feature Navigator to browse the many List utilities available such as the Email Subscriptions page, Archive Search & Download, 7-Day Browse, Chat, FAQ, Photoshare, and much more:
http://www.matronics.com/Navigator?RV10-List |
|
|
|
Back to top |
|
 |
KiloPapa
Joined: 24 May 2006 Posts: 142 Location: Pearblossom, CA
|
Posted: Sat Mar 08, 2008 10:30 am Post subject: lessons learned installing plexiglas with Weld-on 10 |
|
|
Appreciate the write-up.
Kevin
40494
do not archive
| - The Matronics RV10-List Email Forum - | | Use the List Feature Navigator to browse the many List utilities available such as the Email Subscriptions page, Archive Search & Download, 7-Day Browse, Chat, FAQ, Photoshare, and much more:
http://www.matronics.com/Navigator?RV10-List |
|
_________________ Kevin
40494
do not archive |
|
Back to top |
|
 |
|
|
You cannot post new topics in this forum You cannot reply to topics in this forum You cannot edit your posts in this forum You cannot delete your posts in this forum You cannot vote in polls in this forum You cannot attach files in this forum You can download files in this forum
|
Powered by phpBB © 2001, 2005 phpBB Group
|