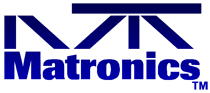 |
Matronics Email Lists Web Forum Interface to the Matronics Email Lists
|
View previous topic :: View next topic |
Author |
Message |
Bill Schlatterer
Joined: 09 Jan 2006 Posts: 195
|
Posted: Sun Mar 09, 2008 10:13 am Post subject: Diodes versus switches 101 ? |
|
|
There was some discussion about Z19 using diodes in a critical ECU circuit and the question arose as to what kind of failure modes apply to diodes and their reliability as compared to switches. I think the trust of that thread (sub list) and post below is that diodes might be "automatic" but switches are safer and less likely to fail? ( I have no opinion but would like to understand the rationale ) This was posted and I was just wondering what the thought might be on the AE list since most of Bobs diagrams "suggest" a diode in the E-Bus circuit as opposed to a switch. That might not be AS critical as the ECU/EFI circuit on an all electric engine but the same concerns still apply?
Posted to the Sub list:
"After 30 years in the industrial electrical construction and maintenance field I can say without equivocation that a robust switch is much less likely to fail than a robust diode. The science of the switch is much simpler - use a lot of good conducting material that is not likely to corrode and support it with stout mechanical parts that hold tightly.
Now, by contrast, the science of the diode starts with getting good silicon material and contaminating it in just the right proportion with just the right material at just the right temperature for just the right time. THEN you can start on building the junctions onto some sort of heat dissipating holder. I have replaced dozens of solid state devices that failed (always failed open) and I never found the root cause of failure. I put in an exact replacement and the circuit worked just fine for years. The trade off you get for the "automatic" switching of a diode vs. the manual switch is in the area of RELIABILITY. I'll be using manual switches for all critical loads."
Not wanting to stir anything up, just want to understand the thinking and factual matter in the post above?
Thanks Bill S
7a Z13/8 Z32(HD E-Bus) Z35(7ah) [quote][b]
| - The Matronics AeroElectric-List Email Forum - | | Use the List Feature Navigator to browse the many List utilities available such as the Email Subscriptions page, Archive Search & Download, 7-Day Browse, Chat, FAQ, Photoshare, and much more:
http://www.matronics.com/Navigator?AeroElectric-List |
|
|
|
Back to top |
|
 |
retasker(at)optonline.net Guest
|
Posted: Sun Mar 09, 2008 11:45 am Post subject: Diodes versus switches 101 ? |
|
|
Here is an excerpt of something I posted on the Sub list which relates
to this email:
Regarding the reliability of switches and diodes... According to Mil handbook 217F - the "bible" of reliability prediction - a Schottky power diode (which is the only type anyone should be using in any power circuit in an airplane) has a predicted failure rate of 0.0028 failures per million hours. A mil rated toggle switch has a predicted failure rate of 0.1 failures per million hours. Now, realistically, this prediction for a switch is partially related to the toggle mechanics and partially related to the individual contacts. The mil handbook relates to a single set of contacts while the specified switch has four sets of contacts so the switch in question is probably less reliable that the handbook predicts for a simple toggle switch. But even if we ignore that detail, for what it is worth, a diode of the type that should be used is 35 times more reliable than the type switch specified. So much for the superiority reliability of a switch that some have been bandying ab
out...
A properly designed diode circuit provides automatic, uninterrupted power transfer in the event of the loss of the main supply. A switched circuit requires the pilot to notice the problem and take some action (toggle the switch to the other position).
A diode circuit has not been specified (in the Subaru application), so one is on their own if that were to be the choice of a user. While this is not an insurmountable problem, the diode circuit is more susceptible to a poor design. One must choose a diode with sufficient current and voltage ratings for the desired circuit conditions. Additionally, since there can be considerable heat generated in a power diode, proper heat sinking must be provided (not particularly hard to do as long as you know how to calculate what is needed).
So... If you are electrically challenged use the factory recommended circuit design - good or bad as it may be, it has full factory support.
If you really know what you are doing, a diode circuit has certain advantages. However, if you choose to depart from the factory design, do not expect any assistance or support from the factory for your design and if you have a problem it is your problem.
I have already wired my RV9A (long before this discussion and long before "diode" became a dirty word) and I am using two very beefy Schottky diodes to connect both battery buses to the engine bus. If either bus goes down for whatever reason, the engine keeps on running and an annunciator tells me which bus is down. Additionally, a voltmeter on each bus keeps me informed of its health continuously.
It should also be noted that in the instance in question that the ECU was provided power from a, probably, inadequately heat sinked bridge that was, possibly, underrated for the application.
For what Bob recommends the bridge - the Ebus - it is an excellent solution for the typical experimental plane builder.
Dick Tasker
Bill Schlatterer wrote:
Quote: |
There was some discussion about Z19 using diodes in a critical ECU
circuit and the question arose as to what kind of failure modes apply
to diodes and their reliability as compared to switches. I think the
trust of that thread (sub list) and post below is that diodes might be
"automatic" but switches are safer and less likely to fail? ( I have
no opinion but would like to understand the rationale ) This was
posted and I was just wondering what the thought might be on the AE
list since most of Bobs diagrams "suggest" a diode in the E-Bus
circuit as opposed to a switch. That might not be AS critical as the
ECU/EFI circuit on an all electric engine but the same concerns still
apply?
Posted to the Sub list:
"After 30 years in the industrial electrical construction and
maintenance field I can say without equivocation that a robust switch
is much less likely to fail than a robust diode. The science of the
switch is much simpler - use a lot of good conducting material that is
not likely to corrode and support it with stout mechanical parts that
hold tightly.
Now, by contrast, the science of the diode starts with getting good
silicon material and contaminating it in just the right proportion
with just the right material at just the right temperature for just
the right time. THEN you can start on building the junctions onto some
sort of heat dissipating holder. I have replaced dozens of solid state
devices that failed (always failed open) and I never found the root
cause of failure. I put in an exact replacement and the circuit worked
just fine for years. The trade off you get for the "automatic"
switching of a diode vs. the manual switch is in the area of
RELIABILITY. I'll be using manual switches for all critical loads."
Not wanting to stir anything up, just want to understand the thinking
and factual matter in the post above?
Thanks Bill S
7a Z13/8 Z32(HD E-Bus) Z35(7ah)
|
--
Please Note:
No trees were destroyed in the sending of this message. We do concede, however,
that a significant number of electrons may have been temporarily inconvenienced.
--
| - The Matronics AeroElectric-List Email Forum - | | Use the List Feature Navigator to browse the many List utilities available such as the Email Subscriptions page, Archive Search & Download, 7-Day Browse, Chat, FAQ, Photoshare, and much more:
http://www.matronics.com/Navigator?AeroElectric-List |
|
|
|
Back to top |
|
 |
matronics(at)rtist.nl Guest
|
Posted: Sun Mar 09, 2008 12:25 pm Post subject: Diodes versus switches 101 ? |
|
|
I think it's important to take into account what the purpose of the switch
and/or diode is, and more important, what the failure modes of the circuits
around it is. A diode may be much more reliable when used within it's
designed specs, but if you overload it, it will fail much quicker than a
switch. Compare a diode and a switch, both rated at 25A. A short-circuit
current of 100A through the diode for a few seconds will make it fail, most
likely open circuit. The same current through a switch may heat it up and
damage the contacts, even cause some sparks, but it may still limp along.
Rob
---
| - The Matronics AeroElectric-List Email Forum - | | Use the List Feature Navigator to browse the many List utilities available such as the Email Subscriptions page, Archive Search & Download, 7-Day Browse, Chat, FAQ, Photoshare, and much more:
http://www.matronics.com/Navigator?AeroElectric-List |
|
|
|
Back to top |
|
 |
retasker(at)optonline.net Guest
|
Posted: Sun Mar 09, 2008 5:39 pm Post subject: Diodes versus switches 101 ? |
|
|
True, but it is easy to get a diode that is rated for far over the
normal operating current. In fact, doing so costs very little extra and
has other advantages.
Additionally, while your example as started is true, hopefully no one on
this forum would end up with a design where it is possible to draw 100A
on a 25A circuit without some sort of protective device interrupting the
current before "a few seconds" are up...
Rob Turk wrote:
[quote]
I think it's important to take into account what the purpose of the
switch and/or diode is, and more important, what the failure modes of
the circuits around it is. A diode may be much more reliable when used
within it's designed specs, but if you overload it, it will fail much
quicker than a switch. Compare a diode and a switch, both rated at
25A. A short-circuit current of 100A through the diode for a few
seconds will make it fail, most likely open circuit. The same current
through a switch may heat it up and damage the contacts, even cause
some sparks, but it may still limp along.
Rob
---
| - The Matronics AeroElectric-List Email Forum - | | Use the List Feature Navigator to browse the many List utilities available such as the Email Subscriptions page, Archive Search & Download, 7-Day Browse, Chat, FAQ, Photoshare, and much more:
http://www.matronics.com/Navigator?AeroElectric-List |
|
|
|
Back to top |
|
 |
nuckolls.bob(at)cox.net Guest
|
Posted: Mon Mar 10, 2008 7:44 am Post subject: Diodes versus switches 101 ? |
|
|
At 09:21 PM 3/9/2008 +0100, you wrote:
Quote: |
I think it's important to take into account what the purpose of the switch
and/or diode is, and more important, what the failure modes of the
circuits around it is. A diode may be much more reliable when used within
it's designed specs, but if you overload it, it will fail much quicker
than a switch. Compare a diode and a switch, both rated at 25A. A
short-circuit current of 100A through the diode for a few seconds will
make it fail, most likely open circuit. The same current through a switch
may heat it up and damage the contacts, even cause some sparks, but it may
still limp along.
|
I've never replaced a diode that failed open. I don't
mean to imply that they NEVER fail open but in what must
be dozens of personal observations, I've never seen one
open. Oh yeah, take that back. I did have a plastic 1A
device that blew up such that the stuff between the wires
just disappeared. I guess that could be classified as
an "open".
Diodes are generally pretty robust. Exemplar devices
might include the diminutive 1A, plastic 1N4001 described
here . . .
http://www.aeroelectric.com/Mfgr_Data/Semiconductors/1N4001.pdf
and his big brother 25A bridge rectifier . . .
http://www.aeroelectric.com/Mfgr_Data/Semiconductors/gbpc12.pdf
Note that the single cycle surge (approx 8 milliseconds) for
the 1A device is 30A. The 25A device will stand off 300A
for 8 mS.
Power diodes for steering energy amongst the busses in
the heavy iron birds have been used for 50+ years. Their
failure rates have been exceedingly low.
Diodes also have an exceedingly long service life. I've
never seen one 'wear out'. On the other hand, switches do
have a service life . . . one that is profoundly affected
by numbers of operations per year and under what electrical
load and environmental conditions. I've seen switches open
up with very few cycles on them after ten+ years of sitting
in an airplane.
99.9% of observed diode failures in light aircraft were
in alternators where the designers of the installation
did not exercise due diligence with respect to cooling.
Concerns for a 25A diode used as the e-bus normal feedpath
management are not well founded.
Bob . . .
| - The Matronics AeroElectric-List Email Forum - | | Use the List Feature Navigator to browse the many List utilities available such as the Email Subscriptions page, Archive Search & Download, 7-Day Browse, Chat, FAQ, Photoshare, and much more:
http://www.matronics.com/Navigator?AeroElectric-List |
|
|
|
Back to top |
|
 |
ceengland(at)bellsouth.ne Guest
|
Posted: Wed Mar 12, 2008 1:33 pm Post subject: Diodes versus switches 101 ? |
|
|
Quote: |
Bill Schlatterer wrote:
>
> There was some discussion about Z19 using diodes in a critical ECU
> circuit and the question arose as to what kind of failure modes apply
> to diodes and their reliability as compared to switches. I think the
> trust of that thread (sub list) and post below is that diodes might
> be "automatic" but switches are safer and less likely to fail? ( I
> have no opinion but would like to understand the rationale ) This
> was posted and I was just wondering what the thought might be on the
> AE list since most of Bobs diagrams "suggest" a diode in the E-Bus
> circuit as opposed to a switch. That might not be AS critical as the
> ECU/EFI circuit on an all electric engine but the same concerns still
> apply?
>
> Posted to the Sub list:
>
> "After 30 years in the industrial electrical construction and
> maintenance field I can say without equivocation that a robust switch
> is much less likely to fail than a robust diode. The science of the
> switch is much simpler - use a lot of good conducting material that
> is not likely to corrode and support it with stout mechanical parts
> that hold tightly.
>
> Now, by contrast, the science of the diode starts with getting good
> silicon material and contaminating it in just the right proportion
> with just the right material at just the right temperature for just
> the right time. THEN you can start on building the junctions onto
> some sort of heat dissipating holder. I have replaced dozens of solid
> state devices that failed (always failed open) and I never found the
> root cause of failure. I put in an exact replacement and the circuit
> worked just fine for years. The trade off you get for the "automatic"
> switching of a diode vs. the manual switch is in the area of
> RELIABILITY. I'll be using manual switches for all critical loads."
>
> Not wanting to stir anything up, just want to understand the thinking
> and factual matter in the post above?
> Thanks Bill S
> 7a Z13/8 Z32(HD E-Bus) Z35(7ah)
>
Not a direct answer to the question of whether a diode is more likely to
|
fail than a switch, but a response to the method used to reach his answer.
Old pre-1970's era point-type ignitions are based around switches (the
points). Just about every production car since then has used variations
on diodes (doped semiconductor junctions) in all the various components
of modern solid state ignitions (transistors, FETs, photocells, etc).
Using his analysis technique, it's obvious that point-type ignitions are
the way to go, since they are in fact cheaper & *much* simpler. Yet we
don't see them in new cars.
The real question is, which is more reliable in real world applications?
Charlie
| - The Matronics AeroElectric-List Email Forum - | | Use the List Feature Navigator to browse the many List utilities available such as the Email Subscriptions page, Archive Search & Download, 7-Day Browse, Chat, FAQ, Photoshare, and much more:
http://www.matronics.com/Navigator?AeroElectric-List |
|
|
|
Back to top |
|
 |
nuckolls.bob(at)cox.net Guest
|
Posted: Wed Mar 12, 2008 6:47 pm Post subject: Diodes versus switches 101 ? |
|
|
There was some discussion about Z19 using diodes in a critical ECU circuit
and the question arose as to what kind of failure modes apply to diodes and
their reliability as compared to switches. I think the trust of that
thread (sub list) and post below is that diodes might be "automatic" but
switches are safer and less likely to fail? ( I have no opinion but would
like to understand the rationale ) This was posted and I was just
wondering what the thought might be on the AE list since most of Bobs
diagrams "suggest" a diode in the E-Bus circuit as opposed to a
switch. That might not be AS critical as the ECU/EFI circuit on an all
electric engine but the same concerns still apply?
Posted to the Sub list:
"After 30 years in the industrial electrical construction and maintenance
field I can say without equivocation that a robust switch is much less
likely to fail than a robust diode. The science of the switch is much
simpler - use a lot of good conducting material that is not likely to
corrode and support it with stout mechanical parts that hold tightly.
Now, by contrast, the science of the diode starts with getting good silicon
material and contaminating it in just the right proportion with just the
right material at just the right temperature for just the right time. THEN
you can start on building the junctions onto some sort of heat dissipating
holder. I have replaced dozens of solid state devices that failed (always
failed open)
Interesting! Most solid state failures I've observed were
shorted devices (overheated and or voltage spiked). The
devices that did go OPEN were transistors that shorted first
and then opened their emitter bond-wires due to over current.
. . . and I never found the root cause of failure. I put in an exact
replacement and the circuit worked just fine for years. The trade off you
get for the "automatic" switching of a diode vs. the manual switch is in
the area of RELIABILITY. I'll be using manual switches for all critical loads."
Not wanting to stir anything up, just want to understand the thinking and
factual matter in the post above?
About 1980 I was designing a new solid state speed
controller and runaway monitor system for the Lear 55
and ultimately the entire fleet of 30 series aircraft.
It was the first time I was tasked with doing a formal
failure mode effects analysis and mean-time-between-failures
(MTBF) study on a new product.
I dug out Mil-HDK-217 and began slogging through the
part-by-part service life prediction algorithms.
By the time some 200+ items of solder joints, transistors,
resistors, capacitors, etc were all accounted for, I was
pleased to turn the crank and a really nice MTBF number
on the order of 10,000 hours fell out. But wait, there
was this really expensive, mil-spec, hermetically sealed
25A power relay used as a last-ditch backup disconnect.
After factoring this device into the grand scheme
of things, my shinning MTBF number fell to something
on the order of 900 hours!
Several times over the last 25 years I've asked the
guys at Electromech's field service shop how the Lear
trim controllers are holding up. The failure items
they have to report were surprising. MOST of the field
failures were in mass-terminated ribbon cable connectors
followed by loss of ground through the mounting hardware
that held the two boards together. Seems this was before
I learned about having solid, on-purpose wiring grounds
and NOT to depend on mountings that loosen and/or corrode.
Electronically, most failures were the usual gang of
jelly bean components, solder joints, etc. Most failures
were in the monitor boards that had 3x the parts count
of a controller board. There were NO failures of the
controller that caused a runaway and a tiny fraction
of the failures incapacitated the system. There had
been no failures for that piece-o-#(at)(at)$, high-dollar
relay that crashed my MTBF study.
Bottom line: Was this relay badly misjudged? No,
I had a pretty good understanding of contact physics
and designed the electronics such that relay contacts
were closed before electronics actually caused the motor
to run. Similarly, electronics shut the motor down and
waited some tens of milliseconds before opening the
relay. Hence, the relay was never required to actually
switch any power. No current was flowing when the relay
contacts opened or closed and current was not allowed to
flow until contacts stopped bouncing on closure.
This is why Lear bought my design with the somewhat
distorted MTBF numbers because in thousands of hours
of flight, the relay never really saw any switching
service. Nowadays, there are more accurate considerations
of how a part is used that will provide a more realistic
prediction of failure rates.
Does this mean that the very robust, mil-spec relay
is the golden child of the design and the electronics
were left holding the bag for all the failures?
No, most failures were due to bonding/connection
issues. This controller resides in the vertical fin,
just under the leading edge of the stabilizer. This
has to be the worst environment in the airplane for
environmental extremes. For the most part, the electronics
seem to be living up to predictions for a long and
quite satisfactory service life in thousands of hours.
My personal experience since supports an assertion
that the silicon rectifier diode has an expected
service life that will far outpace any electro-mechanical
device (relay or switch) that is tasked with controlling
current flow.
Some of my most vexing field failures problems to solve
involve relays or switches. I've never had to chase down
root cause for failures of energy steering diodes
in an airplane.
Now, let us consider the gentleman's contrary assertion.
No doubt he has replaced blown diodes and perceives them
to be less robust than a switch. I cannot help but wonder
if his problem children were not subject to overheating
and or over-voltage due to industrial line transients
or local lightning. Whatever the root cause of his
observed failures, there is nothing in my experience
or that of my colleagues in the aircraft industry that
parallels his experience. I'm not suggesting that he is
being untruthful; only that we're probably observing
an apples/oranges situation. The environments
in which our diodes live and the manner in which they
are applied in airplanes are sufficiently different
from his industrial environment to prevent a useful
comparison.
So please folks, don't rip out your diodes and put
in switches. There are two reasons to support this
suggestion:
First, we design for failure tolerance.
What are the risks if a diode DOES fail? How will
the pilot know it? Is it pre-flight detectable? Will
the failure cripple the system such that it becomes
a hazard? If the answers to any of these questions
give you cause for concern about comfortable termination
of flight, then redesign the system to eliminate
the potential for stress. Consider his statement:
"I'll be using manual switches for all critical loads."
Our common usage of steering diodes for power is
one of TWO power paths to an e-bus. So even if it
does fail open, it has backup. If it fails shorted,
we can detect this during pre-flight.
Second, there is nothing in the service history of
diodes (or any other solid state device) to suggest
they are recognized problem children waiting for a
chance to ruin your day or drive up your cost of
ownership.
Bob . . .
| - The Matronics AeroElectric-List Email Forum - | | Use the List Feature Navigator to browse the many List utilities available such as the Email Subscriptions page, Archive Search & Download, 7-Day Browse, Chat, FAQ, Photoshare, and much more:
http://www.matronics.com/Navigator?AeroElectric-List |
|
|
|
Back to top |
|
 |
Bill Schlatterer
Joined: 09 Jan 2006 Posts: 195
|
Posted: Wed Mar 12, 2008 8:02 pm Post subject: Diodes versus switches 101 ? |
|
|
Thanks Bob, that tells me what I need to know. Wasn't planning on taking
the diode out anyway but it's good to understand the why and why not? My
only regret about my building process is that once I'm done, I won't have
much use for the things I have come to understand from this list. Education
is a good thing but practical use makes it excellent. In my case, I have
learned just enough from this list to recognize what I don't know yet? That
may be the reason I become a repeat builder
Thanks Bill S
--
| - The Matronics AeroElectric-List Email Forum - | | Use the List Feature Navigator to browse the many List utilities available such as the Email Subscriptions page, Archive Search & Download, 7-Day Browse, Chat, FAQ, Photoshare, and much more:
http://www.matronics.com/Navigator?AeroElectric-List |
|
|
|
Back to top |
|
 |
ZuluZephyr
Joined: 12 Mar 2008 Posts: 6 Location: Upland CA
|
Posted: Wed Mar 12, 2008 8:50 pm Post subject: Re: Diodes versus switches 101 ? |
|
|
I have followed the switch vs diode controversy on a number of forums with interest since I am building a Sportsman with a Subaru H6 Engine. I am aware of crash involving a failed diode. I believe the diode was not rated for the actual amp load which was the most likely reason for the diode failure and the ensuing controversy.
There is another design recommending the elimination of the diodes and using one switch to supply the fuel pumps, ECU and EFI. This provides a single point of failure which I think violates the design goals of the Z19 drawing of providing redundant paths, components and circuits.
Being a committed party ( I have the engine) and wanting the simplest most reliable electrical system possible, I have designed a variation of the Z19 drawing using the same parts count with diodes (rated for the load) than includes a bypass circuit in case of diode failure (unlikely).
Please see attached drawing. I welcome all comments and suggestions.
Rocky Morrison
| - The Matronics AeroElectric-List Email Forum - | | Use the List Feature Navigator to browse the many List utilities available such as the Email Subscriptions page, Archive Search & Download, 7-Day Browse, Chat, FAQ, Photoshare, and much more:
http://www.matronics.com/Navigator?AeroElectric-List |
|
Description: |
|
 Download |
Filename: |
Proposed Fuel Pump-ECI-EFI Circuit for Eggenfellner Subaru H6.pdf |
Filesize: |
53.13 KB |
Downloaded: |
762 Time(s) |
|
|
Back to top |
|
 |
nuckolls.bob(at)cox.net Guest
|
Posted: Thu Mar 13, 2008 2:09 am Post subject: Diodes versus switches 101 ? |
|
|
At 10:57 PM 3/12/2008 -0500, you wrote:
Quote: |
<billschlatterer(at)sbcglobal.net>
Thanks Bob, that tells me what I need to know. Wasn't planning on taking
the diode out anyway but it's good to understand the why and why not? My
only regret about my building process is that once I'm done, I won't have
much use for the things I have come to understand from this list. Education
is a good thing but practical use makes it excellent. In my case, I have
learned just enough from this list to recognize what I don't know yet? That
may be the reason I become a repeat builder
|
Correct . . . presuming that you do not take what
you've learned and share it with others. Knowledge and
understanding are commodities that grow in value the more they
are given away. We all benefit every day from associations
with individuals who are willing to share what they've learned.
After your airplane is finished, you can satisfy your debt
to all the teachers who participated in your success by
"paying it forward". See:
http://en.wikipedia.org/wiki/Pay_it_forward
http://tinyurl.com/32cfym
Bob . . .
| - The Matronics AeroElectric-List Email Forum - | | Use the List Feature Navigator to browse the many List utilities available such as the Email Subscriptions page, Archive Search & Download, 7-Day Browse, Chat, FAQ, Photoshare, and much more:
http://www.matronics.com/Navigator?AeroElectric-List |
|
|
|
Back to top |
|
 |
nuckolls.bob(at)cox.net Guest
|
Posted: Thu Mar 13, 2008 2:19 am Post subject: Diodes versus switches 101 ? |
|
|
At 09:50 PM 3/12/2008 -0700, you wrote:
Quote: |
I have followed the switch vs diode controversy on a number of forums with
interest since I am building a Sportsman with a Subaru H6 Engine. I am
aware of crash involving a failed diode. I believe the diode was not
rated for the actual amp load which was the most likely reason for the
diode failure and the ensuing controversy.
|
Due diligence in design cannot be discounted. It
could just as easily have been a failure due to an
improperly tightened nut. Had it been a fastener failure,
is there value in responding to that knowledge by
replacing all the fasteners in our machines with
grade 8 hardware and metal locknuts?
The real issue is to understand what suite of
components are available to arrive at at an elegant
solution and then properly apply those components
to the task.
Quote: | There is another design recommending the elimination of the diodes and
using one switch to supply the fuel pumps, ECU and EFI. This provides a
single point of failure which I think violates the design goals of the Z19
drawing of providing redundant paths, components and circuits.
|
Consideration of design goals and failure mode
effects are important components of the process . . .
Quote: | Being a committed party ( I have the engine) and wanting the simplest most
reliable electrical system possible, I have designed a variation of the
Z19 drawing using the same parts count with diodes (rated for the load)
than includes a bypass circuit in case of diode failure (unlikely).
|
It's unfortunate that your lack of confidence leads
you to conclude that there is value in "backing
up" a diode. On the other hand, it's far better that
you fly this airplane free of worry about it. Worries
do not enhance your piloting skills and should be
assuaged irrespective of the physics and/or probabilities.
Bob . . .
| - The Matronics AeroElectric-List Email Forum - | | Use the List Feature Navigator to browse the many List utilities available such as the Email Subscriptions page, Archive Search & Download, 7-Day Browse, Chat, FAQ, Photoshare, and much more:
http://www.matronics.com/Navigator?AeroElectric-List |
|
|
|
Back to top |
|
 |
ZuluZephyr
Joined: 12 Mar 2008 Posts: 6 Location: Upland CA
|
Posted: Thu Mar 13, 2008 8:41 am Post subject: Re: Diodes versus switches 101 ? |
|
|
Bob,
I appreciate your comments, thoughts and efforts in helping all the builders develop more reliable and better electrical systems. A worrier I am not, but a simple change to the design that provides backup to a potential component failure makes logical sense to me. I plan on flying in remote places and reliability is high on my list of design goals. That is why I am here to learn and listen, ask questions and share if I think something is worthy of the groups time.
Keep up the great work. Your work has been invaluable to me in the building process.
Bob, Thanks!!
Rocky Morrison
| - The Matronics AeroElectric-List Email Forum - | | Use the List Feature Navigator to browse the many List utilities available such as the Email Subscriptions page, Archive Search & Download, 7-Day Browse, Chat, FAQ, Photoshare, and much more:
http://www.matronics.com/Navigator?AeroElectric-List |
|
|
|
Back to top |
|
 |
longg(at)pjm.com Guest
|
Posted: Thu Mar 13, 2008 10:06 am Post subject: Diodes versus switches 101 ? |
|
|
Bob,
Thanks for the background and scope of the diode. That said and given
the intended reliability of the diode, I would hope my e-bus capacity
remains below 20A in my Z19 setup. Assuming the use of the B & C cooled
diode setup, should I fear any continuous load up to the 25A suggested
rating?
Thanks too for the tips on switching. I can see a few 2-10's in my
future for saving valuable panel space. Some great examples through 8-9x
in your book.
Glenn
--
| - The Matronics AeroElectric-List Email Forum - | | Use the List Feature Navigator to browse the many List utilities available such as the Email Subscriptions page, Archive Search & Download, 7-Day Browse, Chat, FAQ, Photoshare, and much more:
http://www.matronics.com/Navigator?AeroElectric-List |
|
|
|
Back to top |
|
 |
nuckolls.bob(at)cox.net Guest
|
Posted: Thu Mar 13, 2008 12:29 pm Post subject: Diodes versus switches 101 ? |
|
|
At 02:02 PM 3/13/2008 -0400, you wrote:
Quote: |
Bob,
Thanks for the background and scope of the diode. That said and given
the intended reliability of the diode, I would hope my e-bus capacity
remains below 20A in my Z19 setup. Assuming the use of the B & C cooled
diode setup, should I fear any continuous load up to the 25A suggested
rating?
Thanks too for the tips on switching. I can see a few 2-10's in my
future for saving valuable panel space. Some great examples through 8-9x
in your book.
|
You're welcome. I would hope your endurance bus is below
20A too. I get about 2 or 3 drawings a month from builders
who are asking for a review of their particular implementation
of a Z-figure. The majority of these drawings have too much
stuff on the e-bus.
A review of the endurance bus philosophy might be useful here.
If one is flying one alternator and one battery, the e-bus is
intended to offer a minimum power load on a battery of known
capacity for the purpose of NOT turning an alternator failure
into an emergency. How much 'stuff' is necessary to stay on-course
for say 1 to 2 hours with the airplane configured for en route
phase of flight?
This list boils down to one nav receiver, transponder, minimal
panel lighting, etc. The nicely crafted e-bus for a one-alternator
airplane should be reduced to 4A or less total load. Now, other
things can drive from the e-bus but should be capable of being
switched off during alternator out operations.
If you have an auxiliary 8A alternator then the e-bus loads can
be elevated to 8A total. Likewise, a 20A aux alternator would
support a 20A e-bus . . . and perhaps there's little if any value
in even having an e-bus.
The 25A diode bridge recommended since day-one for the e-bus
normal feedpath diode was selected for its MECHANICAL convenience
of mounting and making connections via fast-on terminals. In
no way was it intended to imply that e-bus loads could total up
to that value. Anything over 10A should prompt a review of the
diode installation for the purpose of deducing thermal adequacy
of the mounting in carrying away heat.
Most of my fused feeders to the e-bus in the Z-figures are protected
at 7A. If you have an SD-8 second alternator, perhaps that fuse
should go up to 10A. But if your suite of proposed equipment
combined with an evaluation of how you plan to fly causes you
to pile everything but the kitchen sink on the e-bus, then
we need to talk.
If your e-bus loads are more than 10x the battery contactor
load then the advantages of shedding the contactor as a
battery only load are diminished considerably.
If most of the stuff you really need to run exceeds 8A then
you need an SD20 aux alternator and Figure Z-12 is probably
your minimum parts count approach to managing alternator
out conditions. Z-12 cannot fully exploit the design goals
for an e-bus so it would not be unreasonable to eliminate
it entirely and run the whole airplane from the main bus
with the SD-20 backing up the main alternator.
That takes care of the worries about diodes and e-bus
switches and makes the airplane simpler to operate.
Bob . . .
| - The Matronics AeroElectric-List Email Forum - | | Use the List Feature Navigator to browse the many List utilities available such as the Email Subscriptions page, Archive Search & Download, 7-Day Browse, Chat, FAQ, Photoshare, and much more:
http://www.matronics.com/Navigator?AeroElectric-List |
|
|
|
Back to top |
|
 |
mprather(at)spro.net Guest
|
Posted: Thu Mar 13, 2008 1:17 pm Post subject: Diodes versus switches 101 ? |
|
|
Quote: | A review of the endurance bus philosophy might be useful here.
If one is flying one alternator and one battery, the e-bus is
intended to offer a minimum power load on a battery of known
capacity for the purpose of NOT turning an alternator failure
into an emergency. How much 'stuff' is necessary to stay on-course
for say 1 to 2 hours with the airplane configured for en route
phase of flight?
This list boils down to one nav receiver, transponder, minimal
panel lighting, etc. The nicely crafted e-bus for a one-alternator
|
Plus any devices required to remain upright (in an all-electric airplane)
- aviate, then navigate? An EFIS (or an electric attitude indicator).
Regards,
Matt-
| - The Matronics AeroElectric-List Email Forum - | | Use the List Feature Navigator to browse the many List utilities available such as the Email Subscriptions page, Archive Search & Download, 7-Day Browse, Chat, FAQ, Photoshare, and much more:
http://www.matronics.com/Navigator?AeroElectric-List |
|
|
|
Back to top |
|
 |
|
|
You cannot post new topics in this forum You cannot reply to topics in this forum You cannot edit your posts in this forum You cannot delete your posts in this forum You cannot vote in polls in this forum You cannot attach files in this forum You can download files in this forum
|
Powered by phpBB © 2001, 2005 phpBB Group
|