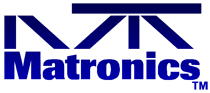 |
Matronics Email Lists Web Forum Interface to the Matronics Email Lists
|
View previous topic :: View next topic |
Author |
Message |
Dennis Johnson
Joined: 10 Jan 2006 Posts: 89 Location: N. Calif.
|
Posted: Sun Apr 27, 2008 9:11 am Post subject: Epoxy to Aluminum |
|
|
Greetings,
As part of building a composite airplane, I studied everything I could find about epoxies, materials, and adhesive bonding in general. I concluded that I did not have the ability to make an epoxy bond to aluminum that I could be confident that it wouldn't fail.
The problem is that aluminum begins oxidizing immediately after cleaning. No matter how quick you are, unless you use extraordinary measures, there will be aluminum oxide on the surface you are bonding. Aluminum oxide has relatively low strength. The epoxy bonds well to the aluminum oxide, but the aluminum oxide isn't stuck very well to the underlying aluminum. After some number of hot/cold and wet/dry cycles, the bond may weaken enough to fail.
Obviously, Boeing and others solved this problem long ago. However, based on the great reference book, "Composite Basics," by Andrew Marshall, their methods aren't practical for most of us homebuilders. >From chapter 11, Marshall says, "Unfortunately, both the FPL etch and the PAA treatments (the ones widely and successfully used in the industry) involve extensive chemical control and a large investment in equipment."
As an interesting aside, he describes an industry standard "wedge" test where two .125" thick aluminum pieces are bonded together. After curing, a wedge is driven into the end of the assembly, between the two pieces of aluminum, which forces the bond to break at that point. A mark is placed at the point where the fracture stops. The test piece is then placed into a warm, wet chamber for one hour. The assembly is then removed and the additional distance the crack propagated during the warm/wet test is measured. If the crack grew less than three-fourths of an inch, the bond is considered to be good for life. Marshall says that if the aluminum was cleaned but not chemically treated, the assembly will likely totally delaminate during the one hour test!
Since I didn't have the ability to duplicate Boeing's chemical treatment process, I didn't make any bond to aluminum that would cause anything more than inconvenience if it failed. Heat and humidity seem to be the culprits, which might explain why some people report long lasting bonds and others have failures.
Best,
Dennis
[quote][b]
| - The Matronics AeroElectric-List Email Forum - | | Use the List Feature Navigator to browse the many List utilities available such as the Email Subscriptions page, Archive Search & Download, 7-Day Browse, Chat, FAQ, Photoshare, and much more:
http://www.matronics.com/Navigator?AeroElectric-List |
|
|
|
Back to top |
|
 |
ceengland(at)bellsouth.ne Guest
|
Posted: Sun Apr 27, 2008 10:07 am Post subject: Epoxy to Aluminum |
|
|
Dennis Johnson wrote:
Quote: | Greetings,
As part of building a composite airplane, I studied everything I could
find about epoxies, materials, and adhesive bonding in general. I
concluded that I did not have the ability to make an epoxy bond to
aluminum that I could be confident that it wouldn't fail.
The problem is that aluminum begins oxidizing immediately after
cleaning. No matter how quick you are, unless you use
extraordinary measures, there will be aluminum oxide on the surface
you are bonding. Aluminum oxide has relatively low strength. The
epoxy bonds well to the aluminum oxide, but the aluminum oxide isn't
stuck very well to the underlying aluminum. After some number of
hot/cold and wet/dry cycles, the bond may weaken enough to fail.
Obviously, Boeing and others solved this problem long ago. However,
based on the great reference book, "/Composite Basics/," by Andrew
Marshall, their methods aren't practical for most of us homebuilders.
From chapter 11, Marshall says, "Unfortunately, both the FPL etch and
the PAA treatments (the ones widely and successfully used in the
industry) involve extensive chemical control and a large investment in
equipment."
As an interesting aside, he describes an industry standard "wedge"
test where two .125" thick aluminum pieces are bonded together. After
curing, a wedge is driven into the end of the assembly, between the
two pieces of aluminum, which forces the bond to break at that point.
A mark is placed at the point where the fracture stops. The test
piece is then placed into a warm, wet chamber for one hour. The
assembly is then removed and the additional distance the crack
propagated during the warm/wet test is measured. If the crack grew
less than three-fourths of an inch, the bond is considered to be good
for life. Marshall says that if the aluminum was cleaned but not
chemically treated, the assembly will likely totally delaminate during
the one hour test!
Since I didn't have the ability to duplicate Boeing's chemical
treatment process, I didn't make any bond to aluminum that would cause
anything more than inconvenience if it failed. Heat and humidity seem
to be the culprits, which might explain why some people report long
lasting bonds and others have failures.
Best,
Dennis
When was the book written? There are some pretty impressive bonding
|
agents available now (not all are 'epoxy').
Even if you limit the discussion to epoxies, consider JB Weld. There are
*lots* of aluminum things flying around on homebuilts that were repaired
(or assembled) using JB Weld, including engine components.
The BD-4's original assembly method for the wing was to bond the
fiberglass wing ribs to the aluminum tube spar. Just about every one of
them leaked fuel through the poor quality 'glass rib/skin assemblies,
but I've never heard of a debonding event at the rib/spar joints. Note
that this joint was glued with what amounts to fuel sealant (commonly
called 'pro-seal'), not a true epoxy adhesive. It wasn't even designed
to be a structural adhesive.
FWIW,
Charlie
| - The Matronics AeroElectric-List Email Forum - | | Use the List Feature Navigator to browse the many List utilities available such as the Email Subscriptions page, Archive Search & Download, 7-Day Browse, Chat, FAQ, Photoshare, and much more:
http://www.matronics.com/Navigator?AeroElectric-List |
|
|
|
Back to top |
|
 |
raymondj(at)frontiernet.n Guest
|
Posted: Sun Apr 27, 2008 12:02 pm Post subject: Epoxy to Aluminum |
|
|
Greetings,
The following is intended for hardware mounting on boats.
After proper dry preparation per the manual, West System epoxy technical
manual ( catalogue number 002-950, 1994) on page 9, item 5, in bonding
hardware ( continued from page says: "Coat the bottom contact surface of
the hardware with unthickened epoxy.Wire brush or sand the wet epoxy into
the surface with 50 grit sandpaper. Sanding the base with, coated with
epoxy, will expose the epoxy directly to fresh metal with no chance for the
metal to oxidize."
Raymond Julian
Kettle River, MN
"Hope for the best,
but prepare for the worst."
---
| - The Matronics AeroElectric-List Email Forum - | | Use the List Feature Navigator to browse the many List utilities available such as the Email Subscriptions page, Archive Search & Download, 7-Day Browse, Chat, FAQ, Photoshare, and much more:
http://www.matronics.com/Navigator?AeroElectric-List |
|
|
|
Back to top |
|
 |
bakerocb
Joined: 15 Jan 2006 Posts: 727 Location: FAIRFAX VA
|
Posted: Mon Apr 28, 2008 3:28 am Post subject: Epoxy to Aluminum |
|
|
4/28/2008
Hello Dennis, Thanks for your interesting input.
One technique that may be used, if appropriate to the situation, to improve
joint holding, is to make holes in the aluminum. This permits the epoxy to
ooze through and form sort of a rivet effect for the glue line.
'OC' Says: "The best investment we can make is the effort to gather and
understand knowledge."
-----------------------------------------------------------
Time: 10:11:16 AM PST US
From: "Dennis Johnson" <pinetownd(at)volcano.net>
Subject: Epoxy to Aluminum
Greetings,
As part of building a composite airplane, I studied everything I could
find about epoxies, materials, and adhesive bonding in general. I
concluded that I did not have the ability to make an epoxy bond to
aluminum that I could be confident that it wouldn't fail.
The problem is that aluminum begins oxidizing immediately after
cleaning. No matter how quick you are, unless you use extraordinary
measures, there will be aluminum oxide on the surface you are bonding.
Aluminum oxide has relatively low strength. The epoxy bonds well to the
aluminum oxide, but the aluminum oxide isn't stuck very well to the
underlying aluminum. After some number of hot/cold and wet/dry cycles,
the bond may weaken enough to fail.
Obviously, Boeing and others solved this problem long ago. However,
based on the great reference book, "Composite Basics," by Andrew
Marshall, their methods aren't practical for most of us homebuilders.
Quote: | From chapter 11, Marshall says, "Unfortunately, both the FPL etch and
the PAA treatments (the ones widely and successfully used in the
|
industry) involve extensive chemical control and a large investment in
equipment."
As an interesting aside, he describes an industry standard "wedge" test
where two .125" thick aluminum pieces are bonded together. After
curing, a wedge is driven into the end of the assembly, between the two
pieces of aluminum, which forces the bond to break at that point. A
mark is placed at the point where the fracture stops. The test piece is
then placed into a warm, wet chamber for one hour. The assembly is then
removed and the additional distance the crack propagated during the
warm/wet test is measured. If the crack grew less than three-fourths of
an inch, the bond is considered to be good for life. Marshall says that
if the aluminum was cleaned but not chemically treated, the assembly
will likely totally delaminate during the one hour test!
Since I didn't have the ability to duplicate Boeing's chemical treatment
process, I didn't make any bond to aluminum that would cause anything
more than inconvenience if it failed. Heat and humidity seem to be the
culprits, which might explain why some people report long lasting bonds
and others have failures.
Best,
Dennis
| - The Matronics AeroElectric-List Email Forum - | | Use the List Feature Navigator to browse the many List utilities available such as the Email Subscriptions page, Archive Search & Download, 7-Day Browse, Chat, FAQ, Photoshare, and much more:
http://www.matronics.com/Navigator?AeroElectric-List |
|
|
|
Back to top |
|
 |
Eric M. Jones
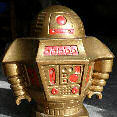
Joined: 10 Jan 2006 Posts: 565 Location: Massachusetts
|
Posted: Mon Apr 28, 2008 7:32 am Post subject: Re: Epoxy to Aluminum |
|
|
Quote: | Greetings,
After proper dry preparation per the manual, West System epoxy technical manual (catalogue number 002-950, 1994) on page 9, item 5, in bonding hardware ( continued from page says: "Coat the bottom contact surface of the hardware with unthickened epoxy. Wire brush or sand the wet epoxy into the surface with 50 grit sandpaper. Sanding the base with, coated with epoxy, will expose the epoxy directly to fresh metal with no chance for the metal to oxidize."
Raymond Julian
Kettle River, MN |
The West System method seems brilliant to me. It seems to use the approach often used in soldering aluminum where a stainless-wire brush removes the oxide while being protected from re-oxidation by the solder (and flux). Nice.
| - The Matronics AeroElectric-List Email Forum - | | Use the List Feature Navigator to browse the many List utilities available such as the Email Subscriptions page, Archive Search & Download, 7-Day Browse, Chat, FAQ, Photoshare, and much more:
http://www.matronics.com/Navigator?AeroElectric-List |
|
_________________ Eric M. Jones
www.PerihelionDesign.com
113 Brentwood Drive
Southbridge, MA 01550
(508) 764-2072
emjones(at)charter.net |
|
Back to top |
|
 |
Speedy11(at)aol.com Guest
|
Posted: Mon Apr 28, 2008 6:50 pm Post subject: Epoxy to Aluminum |
|
|
Dennis,
Very interesting information. Thanks for sharing it.
I had never thought about it, but your explanation makes sense. It also may explain why I had such poor results with the Click-Bond nutplate adhesion. Perhaps the Click-Bond products are most ideal for composite airplanes and regular nutplates are better for aluminum airplanes.
Thanks again,
Stan Sutterfield
Do not archive
Quote: | Greetings,
As part of building a composite airplane, I studied everything I could
find about epoxies, materials, and adhesive bonding in general. I
concluded that I did not have the ability to make an epoxy bond to
aluminum that I could be confident that it wouldn't fail.
The problem is that aluminum begins oxidizing immediately after
cleaning. No matter how quick you are, unless you use extraordinary
measures, there will be aluminum oxide on the surface you are bonding.
Aluminum oxide has relatively low strength. The epoxy bonds well to the
aluminum oxide, but the aluminum oxide isn't stuck very well to the
underlying aluminum. After some number of hot/cold and wet/dry cycles,
the bond may weaken enough to fail.
Obviously, Boeing and others solved this problem long ago. However,
based on the great reference book, "Composite Basics," by Andrew
Marshall, their methods aren't practical for most of us homebuilders.
Quote: | From chapter 11, Marshall says, "Unfortunately, both the FPL etch and
the PAA treatments (the ones widely and successfully used in the
|
industry) involve extensive chemical control and a large investment in
equipment."
As an interesting aside, he describes an industry standard "wedge" test
where two .125" thick aluminum pieces are bonded together. After
curing, a wedge is driven into the end of the assembly, between the two
pieces of aluminum, which forces the bond to break at that point. A
mark is placed at the point where the fracture stops. The test piece is
then placed into a warm, wet chamber for one hour. The assembly is then
removed and the additional distance the crack propagated during the
warm/wet test is measured. If the crack grew less than three-fourths of
an inch, the bond is considered to be good for life. Marshall says that
if the aluminum was cleaned but not chemically treated, the assembly
will likely totally delaminate during the one hour test!
Since I didn't have the ability to duplicate Boeing's chemical treatment
process, I didn't make any bond to aluminum that would cause anything
more than inconvenience if it failed. Heat and humidity seem to be the
culprits, which might explain why some people report long lasting bonds
and others have failures.
Best,
Dennis |
Need a new ride? Check out the largest site for U.S. used car listings at AOL Autos.
[quote][b]
| - The Matronics AeroElectric-List Email Forum - | | Use the List Feature Navigator to browse the many List utilities available such as the Email Subscriptions page, Archive Search & Download, 7-Day Browse, Chat, FAQ, Photoshare, and much more:
http://www.matronics.com/Navigator?AeroElectric-List |
|
|
|
Back to top |
|
 |
rshannon
Joined: 05 Sep 2007 Posts: 62
|
Posted: Tue Apr 29, 2008 11:56 am Post subject: Epoxy to Aluminum |
|
|
Quote: | ... Perhaps the Click-Bond products are most ideal for composite airplanes and regular nutplates are better for aluminum airplanes.
|
FWIW, all my 200+ Click Bond fasteners are on aluminum. Surface prep is essential, but easy. Just a scuff with the provided Scotch Brite pad, a swipe with the provided solvent/cleaner, thoroughly mix the two part epoxy from the pre-measured packet... and on they go. Wait 24 hrs. to cure and bolts torque down fine.
Ron
[quote][b]
| - The Matronics AeroElectric-List Email Forum - | | Use the List Feature Navigator to browse the many List utilities available such as the Email Subscriptions page, Archive Search & Download, 7-Day Browse, Chat, FAQ, Photoshare, and much more:
http://www.matronics.com/Navigator?AeroElectric-List |
|
|
|
Back to top |
|
 |
Eric M. Jones
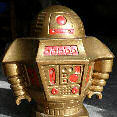
Joined: 10 Jan 2006 Posts: 565 Location: Massachusetts
|
Posted: Wed Apr 30, 2008 5:42 am Post subject: Re: Epoxy to Aluminum |
|
|
After following this thread it occurred to me that I had to learn ONE very important thing when using epoxy particularly--there must be epoxy in the bonded interface...Duh....It is easy to prepare the surfaces, put epoxy on one or both parts and press or clamp the parts together squeezing out virtually ALL the epoxy. Thus no bonded joint, or the bond has inadequate flexibility and fails.
Pay attention to the minimum bond-line specification, or failing that, if the joint is between two very flat surfaces, assure that a few thousandths bond-line remains.
"A witty saying proves nothing."
--Voltaire
| - The Matronics AeroElectric-List Email Forum - | | Use the List Feature Navigator to browse the many List utilities available such as the Email Subscriptions page, Archive Search & Download, 7-Day Browse, Chat, FAQ, Photoshare, and much more:
http://www.matronics.com/Navigator?AeroElectric-List |
|
_________________ Eric M. Jones
www.PerihelionDesign.com
113 Brentwood Drive
Southbridge, MA 01550
(508) 764-2072
emjones(at)charter.net |
|
Back to top |
|
 |
JohnInReno
Joined: 08 Sep 2007 Posts: 150
|
Posted: Sun May 04, 2008 6:19 am Post subject: Epoxy to Aluminum |
|
|
Has anyone tried re-using the click-bond "worms" with standard K1000
plate nuts? It seems to me that the rivet holes would aid in bonding and
the rubber "worm" provides alignment, compression, and protects the
threads from the adhesive.
john
bakerocb(at)cox.net wrote:
Quote: |
4/28/2008
Hello Dennis, Thanks for your interesting input.
One technique that may be used, if appropriate to the situation, to
improve joint holding, is to make holes in the aluminum. This permits
the epoxy to ooze through and form sort of a rivet effect for the glue
line.
'OC' Says: "The best investment we can make is the effort to gather
and understand knowledge."
-----------------------------------------------------------
Time: 10:11:16 AM PST US
From: "Dennis Johnson" <pinetownd(at)volcano.net>
Subject: Epoxy to Aluminum
Greetings,
As part of building a composite airplane, I studied everything I could
find about epoxies, materials, and adhesive bonding in general. I
concluded that I did not have the ability to make an epoxy bond to
aluminum that I could be confident that it wouldn't fail.
The problem is that aluminum begins oxidizing immediately after
cleaning. No matter how quick you are, unless you use extraordinary
measures, there will be aluminum oxide on the surface you are bonding.
Aluminum oxide has relatively low strength. The epoxy bonds well to the
aluminum oxide, but the aluminum oxide isn't stuck very well to the
underlying aluminum. After some number of hot/cold and wet/dry cycles,
the bond may weaken enough to fail.
Obviously, Boeing and others solved this problem long ago. However,
based on the great reference book, "Composite Basics," by Andrew
Marshall, their methods aren't practical for most of us homebuilders.
> From chapter 11, Marshall says, "Unfortunately, both the FPL etch and
the PAA treatments (the ones widely and successfully used in the
industry) involve extensive chemical control and a large investment in
equipment."
As an interesting aside, he describes an industry standard "wedge" test
where two .125" thick aluminum pieces are bonded together. After
curing, a wedge is driven into the end of the assembly, between the two
pieces of aluminum, which forces the bond to break at that point. A
mark is placed at the point where the fracture stops. The test piece is
then placed into a warm, wet chamber for one hour. The assembly is then
removed and the additional distance the crack propagated during the
warm/wet test is measured. If the crack grew less than three-fourths of
an inch, the bond is considered to be good for life. Marshall says that
if the aluminum was cleaned but not chemically treated, the assembly
will likely totally delaminate during the one hour test!
Since I didn't have the ability to duplicate Boeing's chemical treatment
process, I didn't make any bond to aluminum that would cause anything
more than inconvenience if it failed. Heat and humidity seem to be the
culprits, which might explain why some people report long lasting bonds
and others have failures.
Best,
Dennis
|
| - The Matronics AeroElectric-List Email Forum - | | Use the List Feature Navigator to browse the many List utilities available such as the Email Subscriptions page, Archive Search & Download, 7-Day Browse, Chat, FAQ, Photoshare, and much more:
http://www.matronics.com/Navigator?AeroElectric-List |
|
_________________ John Morgensen
RV-9A - Born on July 3, 2013
RV4 - for sale |
|
Back to top |
|
 |
Frank Davis
Joined: 05 Dec 2007 Posts: 3 Location: Minden, NV
|
Posted: Mon May 05, 2008 7:55 am Post subject: Epoxy to Aluminum |
|
|
Yes, I have re-used the "worms" with K1000 nutplates and J-B Weld.
Worked well. However if the plate is in a critical non-accesable
location, I spring for the more expensive Click-Bond adhesive (paranoia).
As an aside, Click-Bond is located at the Carson City Airport, NV,
where my EAA Chapter is. We have toured the factory several time. One
of the things discussed was the strength of the adhesive bond. They
said that while it doesn't have great peel strength, it has good shear
strength, which is required to counteract the torque of inserting the
fastener.
Frank
*Time: * */07:20:00 AM PST US/*
*From: * */John Morgensen <john(at)morgensen.com
<mailto:john(at)morgensen.com>>/*
*Subject: * /*_Re: Epoxy to Aluminum_*/
* Has anyone tried re-using the click-bond "worms" with standard K1000
plate nuts? It seems to me that the rivet holes would aid in bonding and
the rubber "worm" provides alignment, compression, and protects the
threads from the adhesive. john*
| - The Matronics AeroElectric-List Email Forum - | | Use the List Feature Navigator to browse the many List utilities available such as the Email Subscriptions page, Archive Search & Download, 7-Day Browse, Chat, FAQ, Photoshare, and much more:
http://www.matronics.com/Navigator?AeroElectric-List |
|
|
|
Back to top |
|
 |
|
|
You cannot post new topics in this forum You cannot reply to topics in this forum You cannot edit your posts in this forum You cannot delete your posts in this forum You cannot vote in polls in this forum You cannot attach files in this forum You can download files in this forum
|
Powered by phpBB © 2001, 2005 phpBB Group
|