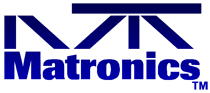 |
Matronics Email Lists Web Forum Interface to the Matronics Email Lists
|
View previous topic :: View next topic |
Author |
Message |
Beemer
Joined: 26 Aug 2006 Posts: 87 Location: Middle Georgia
|
Posted: Mon Aug 11, 2008 7:06 am Post subject: John Deere dynamo |
|
|
Hi all,
I have a question concerning using a dynamo at higher engine speeds. I am looking at reducing my FWF weight, and considering some of the smaller alternator installs. I am currently using a ND IR alt, which is fine, but in lurking around, I'm becoming rather concerned about the weaknesses of these units. Unfortunately, not much else is available in this class; i.e. size and weight. All of the externally regulated alternators I've seen are much too large and heavy for my application.
I'm installing Z-13RB on my new plane, and plan on incorporating Z-24 alt disconnect contactor in line with the OV module.
However, my Suzuki G10 three cylinder runs at 5000rpm in cruise, and 5500rpm on takeoff. The JD AM877557 PM alt puts out 20amps at 2500rpm. I'm running double that. Short of re-doing my belt drive setup with a 12 inch pulley, what are the ramifications of running this little alt at these speeds? by the looks of it, the small pulley on the unit would spin it up to 10,000 rpm. I'm aware of the mechanical limits (bearings, etc), my question concerns the power output to the system.
Any help would be much appreciated.
Bradley
Kitfox 2/3
Middle Georgia
| - The Matronics AeroElectric-List Email Forum - | | Use the List Feature Navigator to browse the many List utilities available such as the Email Subscriptions page, Archive Search & Download, 7-Day Browse, Chat, FAQ, Photoshare, and much more:
http://www.matronics.com/Navigator?AeroElectric-List |
|
Description: |
John Deere AM877557 dynamo |
|
Filesize: |
960.05 KB |
Viewed: |
1101 Time(s) |
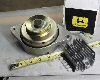
|
_________________ Beemer
KF2 (and now an M3!)
Suzuki G10 three-banger
Middle Georgia |
|
Back to top |
|
 |
nuckolls.bob(at)cox.net Guest
|
Posted: Mon Aug 11, 2008 2:34 pm Post subject: John Deere dynamo |
|
|
At 07:52 AM 8/11/2008 -0700, you wrote:
Quote: |
Hi all,
I have a question concerning using a dynamo at higher engine speeds. I am
looking at reducing my FWF weight, and considering some of the smaller
alternator installs. I am currently using a ND IR alt, which is fine, but
in lurking around, I'm becoming rather concerned about the weaknesses of
these units.
|
Can you give us your perceptions of "weakness"?
Quote: | Unfortunately, not much else is available in this class; i.e. size and
weight. All of the externally regulated alternators I've seen are much
too large and heavy for my application.
I'm installing Z-13RB on my new plane, and plan on incorporating Z-24 alt
disconnect contactor in line with the OV module.
??? I got lost here. Z-24 speaks to classic,
|
wound field alternators like ND . . . are you
looking for a wound field or permanent magnet
fielded machine?
Quote: | However, my Suzuki G10 three cylinder runs at 5000rpm in cruise, and
5500rpm on takeoff. The JD AM877557 PM alt puts out 20amps at 2500rpm. I'm
running double that. Short of re-doing my belt drive setup with a 12 inch
pulley, what are the ramifications of running this little alt at these speeds?
|
Mechanically, no problem. Raising the speed increased the
AC voltage to be "rectified and regulated" down to
14v for operating your equipment. There ARE switch-mode
regulator designs that would handle this job nicely
but that's a whole separate development program.
Quote: | by the looks of it, the small pulley on the unit would spin it up to
10,000 rpm. I'm aware of the mechanical limits (bearings, etc), my
question concerns the power output to the system.
|
Valid concerns as I've suggested above. Those things
run 20-30 VAC output at 5000 rpm so you need to plan
on 2x that at 10,000. Increasing speed is a good way
to get more energy OUT of the PM package as long as
the electronics can handle it but it's doubtful that
any regulator presently exists that fill your
requirements.
Bob . . .
| - The Matronics AeroElectric-List Email Forum - | | Use the List Feature Navigator to browse the many List utilities available such as the Email Subscriptions page, Archive Search & Download, 7-Day Browse, Chat, FAQ, Photoshare, and much more:
http://www.matronics.com/Navigator?AeroElectric-List |
|
|
|
Back to top |
|
 |
echristley(at)nc.rr.com Guest
|
Posted: Mon Aug 11, 2008 5:47 pm Post subject: John Deere dynamo |
|
|
Beemer wrote:
Quote: | However, my Suzuki G10 three cylinder runs at 5000rpm in cruise, and 5500rpm on takeoff. The JD AM877557 PM alt puts out 20amps at 2500rpm. I'm running double that. Short of re-doing my belt drive setup with a 12 inch pulley, what are the ramifications of running this little alt at these speeds? by the looks of it, the small pulley on the unit would spin it up to 10,000 rpm. I'm aware of the mechanical limits (bearings, etc), my question concerns the power output to the system.
Any help would be much appreciated.
Have you considered running a motorcycle generator coaxially?
|
http://ernest.isa-geek.org/Delta/Pictures/EngineGeneratorParts.jpg
http://ernest.isa-geek.org/Delta/Pictures/EngineGeneratorTest.jpg
http://ernest.isa-geek.org/Delta/Pictures/EngineGeneratorMount.jpg
http://ernest.isa-geek.org/Delta/Pictures/EngineGeneratorMounted2.jpg
http://ernest.isa-geek.org/Delta/Pictures/EngineGeneratorAirIntakeAndCooling.jpg
--
http://www.ernest.isa-geek.org
| - The Matronics AeroElectric-List Email Forum - | | Use the List Feature Navigator to browse the many List utilities available such as the Email Subscriptions page, Archive Search & Download, 7-Day Browse, Chat, FAQ, Photoshare, and much more:
http://www.matronics.com/Navigator?AeroElectric-List |
|
|
|
Back to top |
|
 |
klehman(at)albedo.net Guest
|
Posted: Mon Aug 11, 2008 5:50 pm Post subject: John Deere dynamo |
|
|
Bradley
I have a couple of hundred hours on a JD 20 amp PM alternator spinning
at about 8500 rpm with the JD regulator. Occasionally up to around
11,000 rpm. My somewhat hazy memory is that it needs more like 6500 rpm
to put out 20 amps. Someone (Langford??) has a website with a bunch of
info on using these. I fitted a multi-v pulley that probably loads the
bearings a bit less than the original single v pulley.
From memory the unit is around 4.5 lb plus regulator compared to around
6 lb for the conventional 40 amp ND alternator that I mentioned earlier,
so not a big weight saver. I don't have any reason to think either is
more reliable. In fact it seems that the JD regulator will fail if you
start the engine with a totally dead or disconnected battery. A small OV
relay will suffice on the JD unit instead of a heavy contactor though
and mine is wired between the alternator and the regulator. There are
smaller PM units available such as Kubota units.
Ken
Beemer wrote:
Quote: |
Hi all,
I have a question concerning using a dynamo at higher engine speeds. I am looking at reducing my FWF weight, and considering some of the smaller alternator installs. I am currently using a ND IR alt, which is fine, but in lurking around, I'm becoming rather concerned about the weaknesses of these units. Unfortunately, not much else is available in this class; i.e. size and weight. All of the externally regulated alternators I've seen are much too large and heavy for my application.
I'm installing Z-13RB on my new plane, and plan on incorporating Z-24 alt disconnect contactor in line with the OV module.
However, my Suzuki G10 three cylinder runs at 5000rpm in cruise, and 5500rpm on takeoff. The JD AM877557 PM alt puts out 20amps at 2500rpm. I'm running double that. Short of re-doing my belt drive setup with a 12 inch pulley, what are the ramifications of running this little alt at these speeds? by the looks of it, the small pulley on the unit would spin it up to 10,000 rpm. I'm aware of the mechanical limits (bearings, etc), my question concerns the power output to the system.
Any help would be much appreciated.
Bradley
Kitfox 2/3
Middle Georgia
--------
Beemer
KF2 (and now an M3!)
Middle Georgia
|
| - The Matronics AeroElectric-List Email Forum - | | Use the List Feature Navigator to browse the many List utilities available such as the Email Subscriptions page, Archive Search & Download, 7-Day Browse, Chat, FAQ, Photoshare, and much more:
http://www.matronics.com/Navigator?AeroElectric-List |
|
|
|
Back to top |
|
 |
Beemer
Joined: 26 Aug 2006 Posts: 87 Location: Middle Georgia
|
Posted: Tue Aug 12, 2008 5:38 am Post subject: Re: John Deere dynamo |
|
|
nuckolls.bob(at)cox.net wrote: | At 07:52 AM 8/11/2008 -0700, you wrote:
<snip>
>>>Can you give us your perceptions of "weakness"?
|
Only what I've read of your attitude/opinion (for lack of a better term) on them around the list. Correct me if I'm wrong, but I get the overall impression that you do not believe IR alternators belong on aircraft. Of course, it is possible that you don't agree with how John Q Builder tends to install them, i.e. no OV protect, no Alt disconnect contactor, etc. I get this from some old postings on the subject, and the deletion of any schematics that show IR alternator installations. I should add that there isn't much available for my type of engine (Geo Metro auto conversion), and weight is a significant issue up on the nose of the Kitfox.
Quote: | <snip>
>>> ??? I got lost here. Z-24 speaks to classic,
>>>wound field alternators like ND . . . are you
>>>looking for a wound field or permanent magnet
>>>fielded machine?
|
What I'm looking for, ultimately, is to shave about 10lbs from the nose of my aircraft. To that end, I'm exploring options for various components. More specifically, I'm looking for 20-40 reliable amps for my electrically dependent FI engine. Beyond that, I'm open to suggestions.
I was referring to the old Z-24 that depicted the alternator disconnect contactor for the IR alternator, driven by the alt field wire, that completely disconnects the alternator from the battery (system) in case of OV condition. That's what I'm running now on my current install. The note on the new Z-24 again leads me to believe you are not in favor of IR alternators on aircraft. Again, correct me if I'm wrong here.
Quote: | <snip>
>>> Mechanically, no problem. Raising the speed increased the
>>>AC voltage to be "rectified and regulated" down to
>>>14v for operating your equipment. There ARE switch-mode
>>>regulator designs that would handle this job nicely
>>> but that's a whole separate development program.
|
That's why I'm asking. I should point out that I'm not very electrically/electronically savvy (..got to know my limitations). That's why you, this list, and Aeroelectric.com are such valuable resources for me. I'm asking the advice of those much smarter than I on such things.
Quote: | <snip>
>>>Valid concerns as I've suggested above. Those things
>>>run 20-30 VAC output at 5000 rpm so you need to plan
>>>on 2x that at 10,000. Increasing speed is a good way
>>>to get more energy OUT of the PM package as long as
>>>the electronics can handle it but it's doubtful that
>>>any regulator presently exists that fill your
>>>requirements.
>>>
>>>Bob . . .
|
My electronics are minimal. I'm running an EFIS that draws about 100mA max, my GPS and Radio are handhelds that are plugged in to charge, and a small portable intercom. I've got Kuntzleman strobes and LED Navs, and two 55watt landing lights. If it all dies, my pressure driven AoA gives me speed, and a ball keeps me centered, the rest is VFR (blue up/brown down). GPS gets me to "Nearest", and my radio will last a while all by itself. I'm strictly Day VFR, with no provision or desire to night or IFR. Night someday, NEVER IFR in this plane. So my number one concern is keeping the EFI and fuel pump running. My new plane will have Z-13RB installed to this end. I don't even plan to put in the endurance bus, as I've got nothing that needs it. It even works to the end of having the second small battery in the back to help offset the CG of the heavier engine, rather than just putting in dead weight.
In the end, I think the JD dynamo will not be cost effective. For what they cost, I'd be shelling out $40 per lb for the weight savings. Probably not worth it overall.
Bradley
| - The Matronics AeroElectric-List Email Forum - | | Use the List Feature Navigator to browse the many List utilities available such as the Email Subscriptions page, Archive Search & Download, 7-Day Browse, Chat, FAQ, Photoshare, and much more:
http://www.matronics.com/Navigator?AeroElectric-List |
|
_________________ Beemer
KF2 (and now an M3!)
Suzuki G10 three-banger
Middle Georgia |
|
Back to top |
|
 |
nuckolls.bob(at)cox.net Guest
|
Posted: Wed Aug 13, 2008 3:33 pm Post subject: John Deere dynamo |
|
|
At 06:38 AM 8/12/2008 -0700, you wrote:
Quote: |
nuckolls.bob(at)cox.net wrote:
> At 07:52 AM 8/11/2008 -0700, you wrote:
>
> > >>>Can you give us your perceptions of "weakness"?
Only what I've read of your attitude/opinion (for lack of a better term)
on them around the list. Correct me if I'm wrong, but I get the overall
impression that you do not believe IR alternators belong on aircraft.
|
That's a popular myth promulgated mostly by two individuals
who are demonstrably un-qualified to judge my work.
They appear to have never read and/or understood design
goals I (and hundreds of my colleagues) have embraced as
aircraft system integrators and component designers for 30+ years.
Quote: | Of course, it is possible that you don't agree with how John Q Builder
tends to install them, i.e. no OV protect, no Alt disconnect contactor,
etc. I get this from some old postings on the subject, and the deletion
of any schematics that show IR alternator installations. I should add
that there isn't much available for my type of engine (Geo Metro auto
conversion), and weight is a significant issue up on the nose of the Kitfox.
|
I'm not sure you understand the spirit and intent of
my offerings here on the List and elsewhere. I think we
can agree that airplanes, with all the potential for
utility and pleasure, are exceedingly unforgiving machines.
The environment in which we operate them can be equally
unforgiving. Everything I've bolted to an airplane has
these design goals in mind. (1) Utility (function as
specified/advertised). (2) Weight. (3) Cost of ownership.
and last but not least (4) Risk Mitigation.
In categories 1-3, the stock automotive alternator is
a stellar performer and quite suited to the task aboard
airplanes but with two shortcomings"
In the category of UTILITY: ON/OFF control at any time
under any conditions without risk to itself or other
components in the system. This is how alternators/generators
have functioned in aircraft since day-one. There are both
operational and risk mitigation advantages for giving the pilot
and OV protection systems a means of managing alternator operations . . .
and RISK MITIGATION: I have seen no design to data for
which the risk of OV runaway is zero. Further, the potential
for a high-energy even in a runaway alternator is significant.
See:
http://aeroelectric.com/articles/When_is_110V_not_Over_Voltage.pdf
Since day one in aircraft, independent monitoring of bus voltage
COMBINED with the ability to shut an alternator/generator off
at will relieves the system designer of a time-consuming
and costly effort of designing, proving and maintaining a system
reliability in the 10-to-the-minus-9-failures-per-flight-hour
category (FAA-speak for 'never happens').
Failure tolerance is integral to every design and goes directly
to both Cost of Ownership and Risk Mitigation.
Example: I'm working on a line of smart actuators that communicate
on serial data busses, move flight surfaces, and while failure to
move does not generate a serious situation for aircraft and
crew, a failure that produces an un-commanded is bad. The neat
thing is that there are flight systems management computers
on all these aircraft that control everything. Hence Level-A
qualification for software. Normally, an actuator such as
we've proposed would require Level-A qualification too . . .
except.
Since Level-A software already exists that sends me commands
and monitors my response to those commands, all I need to
do is place the entire monitoring duties on the machines already
endowed with the ability to monitor abnormal behavior. I
provide a hard discrete enable line to that computer that
actually powers the level shifters between low level logic
and the motor drivers. If that 28v disappears, the actuator
cannot move.
Now, my software can be crafter to Level-C or even Level-D
because it has no ability to generate hazardous conditions
that are not already being monitored and controlled by another
part of the system qualified to Level-A.
By making my part of the program failure tolerant without
adding risk to the overall flight system, costs of ownership
goes down, and parts-count goes down (driving reliability
up). But even if my gizmo craps every 1000 hours, it's not
a safety of flight issue - only a cost of ownership issue.
>
Quote: | > >>> ??? I got lost here. Z-24 speaks to classic,
> >>>wound field alternators like ND . . . are you
> >>>looking for a wound field or permanent magnet
> >>>fielded machine?
What I'm looking for, ultimately, is to shave about 10lbs from the nose of
my aircraft. To that end, I'm exploring options for various components.
More specifically, I'm looking for 20-40 reliable amps for my electrically
dependent FI engine. Beyond that, I'm open to suggestions.
|
If I were building an airplane, it WOULD have a
stock automotive alternator with Z-24 installed as
an interim solution to get flying and laying the
ground work for installation of a permanent solution
at a later date as described in:
http://www.aeroelectric.com/articles/Adapting_IR_Alternators_to_Aircraft.pdf
Quote: | I was referring to the old Z-24 that depicted the alternator disconnect
contactor for the IR alternator, driven by the alt field wire, that
completely disconnects the alternator from the battery (system) in case of
OV condition. That's what I'm running now on my current install. The note
on the new Z-24 again leads me to believe you are not in favor of IR
alternators on aircraft. Again, correct me if I'm wrong here.
|
Why would I have even crafted Z-24 if I were attempting
to quash the use of IR alternators? And why would I
follow up the Z-24 interim with the new-and-improved
alternative? I'll suggest that these two drawings are
a positive if not enthusiastic endorsement of the
value offered by a host of automotive alternator
products.
No, I have never said that IR alternators do not belong
on aircraft. I have said that I cannot RECOMMEND them because
the current state of our art does not allow me to integrate
them in satisfaction of the design goals cited above.
Z-24 was a first crack at meeting those design goals.
It has some short comings which are discussed in detail in
publications on my website. Those short comings will
be addressed in due course.
Quote: |
> >>> Mechanically, no problem. Raising the speed increased the
> >>>AC voltage to be "rectified and regulated" down to
> >>>14v for operating your equipment. There ARE switch-mode
> >>>regulator designs that would handle this job nicely
> >>> but that's a whole separate development program.
>
That's why I'm asking. I should point out that I'm not very
electrically/electronically savvy (..got to know my limitations). That's
why you, this list, and Aeroelectric.com are such valuable resources for
me. I'm asking the advice of those much smarter than I on such things.
|
First, there are ways to make ANY selection of engine driven
power source suited to use in the aircraft environment.
Further, if you choose not to embrace my design goals, then
there is still good value to be received from bolting a stock
automotive alternator to your airplane. As long as you
understand and accept the risks and perhaps lack of utility
compared to the majority of the GA fleet, then I have
no heartburn with it. But if you're being mis-advised into
believing there is little or no increased risks as
compared to contemporary aircraft design philosophies,
you owe it to yourself to at least elevate your understanding
to the level needed to make a well considered decision.
Don't do anything based on my (or anyone else's recommendations)
unless you understand and personally embrace the design
goals that go along with those recommendations.
Quote: | My electronics are minimal. I'm running an EFIS that draws about 100mA
max, my GPS and Radio are handhelds that are plugged in to charge, and a
small portable intercom. I've got Kuntzleman strobes and LED Navs, and two
55watt landing lights. If it all dies, my pressure driven AoA gives me
speed, and a ball keeps me centered, the rest is VFR (blue up/brown down).
GPS gets me to "Nearest", and my radio will last a while all by itself.
I'm strictly Day VFR, with no provision or desire to night or IFR. Night
someday, NEVER IFR in this plane. So my number one concern is keeping the
EFI and fuel pump running. My new plane will have Z-13RB installed to this
end. I don't even plan to put in the endurance bus, as I've got nothing
that needs it. It even works to the end of having the second small battery
in the back to help offset the CG of the heavier engine, rather than just
putting in dead weight.
|
Sounds like a 3.5# SD-8 would do nicely for you. There are
thousands of LongEz and VariEz aircraft flying with this
machine as the only source of engine driven power.
Quote: | In the end, I think the JD dynamo will not be cost effective. For what
they cost, I'd be shelling out $40 per lb for the weight savings. Probably
not worth it overall.
|
But if you wanted to put a little 35 or 40A wound
field alternator on, that would not be a bad
decision either . . . internally or externally
regulated.
Let's channel this discussion toward establishing
your design goals and then meeting them. Please set
aside any notions that I or anyone else here on the
list is going to twist your arm to do anything except
perhaps those things which are overtly foolhardy or
dangerous.
Have you completed a load analysis of just what
your energy requirements are?
See:
http://www.aeroelectric.com/PPS/Load_Analysis/Blank_Form.pdf
This form is designed to facilitate a study of your
true energy needs. Until those are known, may I
suggest that alternator selection for the purpose
of minimizing weight is premature?
Bob . . .
| - The Matronics AeroElectric-List Email Forum - | | Use the List Feature Navigator to browse the many List utilities available such as the Email Subscriptions page, Archive Search & Download, 7-Day Browse, Chat, FAQ, Photoshare, and much more:
http://www.matronics.com/Navigator?AeroElectric-List |
|
|
|
Back to top |
|
 |
Beemer
Joined: 26 Aug 2006 Posts: 87 Location: Middle Georgia
|
Posted: Thu Aug 14, 2008 1:15 pm Post subject: Re: John Deere dynamo |
|
|
nuckolls.bob(at)cox.net wrote: | At 06:38 AM 8/12/2008 -0700, you wrote:
<snip>
That's a popular myth promulgated mostly by two individuals
who are demonstrably un-qualified to judge my work.
They appear to have never read and/or understood design
goals I (and hundreds of my colleagues) have embraced as
aircraft system integrators and component designers for 30+ years. |
Well, my design goals are different than someone building a Lancair IV. They are also different than Cessna's. I think the overall objective should be the same - supply me 12 volts and don't hurt me. I see that you are leading us toward this objective.
I have no desire to re-hash opinion differences nor point fingers. I want to wire my Kitfox.
<snip>
Quote: |
I'm not sure you understand the spirit and intent of
my offerings here on the List and elsewhere. I think we
can agree that airplanes, with all the potential for
utility and pleasure, are exceedingly unforgiving machines.
The environment in which we operate them can be equally
unforgiving. Everything I've bolted to an airplane has
these design goals in mind. (1) Utility (function as
specified/advertised). (2) Weight. (3) Cost of ownership.
and last but not least (4) Risk Mitigation.
In categories 1-3, the stock automotive alternator is
a stellar performer and quite suited to the task aboard
airplanes but with two shortcomings"
In the category of UTILITY: ON/OFF control at any time
under any conditions without risk to itself or other
components in the system. This is how alternators/generators
have functioned in aircraft since day-one. There are both
operational and risk mitigation advantages for giving the pilot
and OV protection systems a means of managing alternator operations . . .
and RISK MITIGATION: I have seen no design to data for
which the risk of OV runaway is zero. Further, the potential
for a high-energy even in a runaway alternator is significant.
See:
http://aeroelectric.com/articles/When_is_110V_not_Over_Voltage.pdf
Since day one in aircraft, independent monitoring of bus voltage
COMBINED with the ability to shut an alternator/generator off
at will relieves the system designer of a time-consuming
and costly effort of designing, proving and maintaining a system
reliability in the 10-to-the-minus-9-failures-per-flight-hour
category (FAA-speak for 'never happens').
Failure tolerance is integral to every design and goes directly
to both Cost of Ownership and Risk Mitigation.
<snip>
By making my part of the program failure tolerant without
adding risk to the overall flight system, costs of ownership
goes down, and parts-count goes down (driving reliability
up). But even if my gizmo craps every 1000 hours, it's not
a safety of flight issue - only a cost of ownership issue.
|
I don't see any debate here. I'm not a fan of the "more is better" philosophy. KISS is the rule on the K'fox. I'm agonizing over following Z-19RB, but with my EFI engine, I feel the redundancy outweighs the complicity.
<snip>
Wow. Telling statement, that. It quite well answers the question "What would Bob do...?"
Quote: |
Why would I have even crafted Z-24 if I were attempting
to quash the use of IR alternators? And why would I
follow up the Z-24 interim with the new-and-improved
alternative? I'll suggest that these two drawings are
a positive if not enthusiastic endorsement of the
value offered by a host of automotive alternator
products.
No, I have never said that IR alternators do not belong
on aircraft. I have said that I cannot RECOMMEND them because
the current state of our art does not allow me to integrate
them in satisfaction of the design goals cited above.
Z-24 was a first crack at meeting those design goals.
It has some short comings which are discussed in detail in
publications on my website. Those short comings will
be addressed in due course.
|
But you just said you would use one, yet not recommend one. Am I mis-interpreting this somehow?
<snip>
Quote: |
First, there are ways to make ANY selection of engine driven
power source suited to use in the aircraft environment.
Further, if you choose not to embrace my design goals, then
there is still good value to be received from bolting a stock
automotive alternator to your airplane. As long as you
understand and accept the risks and perhaps lack of utility
compared to the majority of the GA fleet, then I have
no heartburn with it. But if you're being mis-advised into
believing there is little or no increased risks as
compared to contemporary aircraft design philosophies,
you owe it to yourself to at least elevate your understanding
to the level needed to make a well considered decision.
Don't do anything based on my (or anyone else's recommendations)
unless you understand and personally embrace the design
goals that go along with those recommendations.
|
By installing Z-13RB with Z-24 integrated, I'm providing for the bad alternator all together, by disconnecting it from the system entirely. From then on, I am carried by the battery(s), and need to design enough ah margin to get me home or nearest, anyway.
Quote: |
Sounds like a 3.5# SD-8 would do nicely for you. There are
thousands of LongEz and VariEz aircraft flying with this
machine as the only source of engine driven power.
|
Ummm, I'm sure they're great units, and would do fine. But I can't use the gear drive.
<snip>
Quote: |
But if you wanted to put a little 35 or 40A wound
field alternator on, that would not be a bad
decision either . . . internally or externally
regulated.
Let's channel this discussion toward establishing
your design goals and then meeting them. Please set
aside any notions that I or anyone else here on the
list is going to twist your arm to do anything except
perhaps those things which are overtly foolhardy or
dangerous.
Have you completed a load analysis of just what
your energy requirements are?
See:
http://www.aeroelectric.com/PPS/Load_Analysis/Blank_Form.pdf
This form is designed to facilitate a study of your
true energy needs. Until those are known, may I
suggest that alternator selection for the purpose
of minimizing weight is premature?
Bob . . . |
No ones talking me into anything. I'm trying to decide how to proceed on my new airplane.
I haven't analyzed it. I have no idea how to check the ECM and coil draw. Right now I have 55amps, Z-24, and 17ah running the motor just fine. I have two readily available alternator options, both 40amp, one weighs 6.5lbs, the other 4.5 lbs. I'm just trying to figure out if there's a better way to wire up the new airplane. If I can install the JD dynamo with external reg, spin it up to 9000rpm, and live to tell the tale, I'll consider it on its merits. But I would like to know if it's feasible to do so, or a bad choice due to something I'm not being told by the advertising.
Bradley
| - The Matronics AeroElectric-List Email Forum - | | Use the List Feature Navigator to browse the many List utilities available such as the Email Subscriptions page, Archive Search & Download, 7-Day Browse, Chat, FAQ, Photoshare, and much more:
http://www.matronics.com/Navigator?AeroElectric-List |
|
_________________ Beemer
KF2 (and now an M3!)
Suzuki G10 three-banger
Middle Georgia |
|
Back to top |
|
 |
ed(at)muellerartcover.com Guest
|
Posted: Thu Aug 14, 2008 3:44 pm Post subject: John Deere dynamo |
|
|
If you have the engine actually running, can't you turn all the other
electrics off and measure the draw of the ECM and coil?
Ed
On Aug 14, 2008, at 5:15 PM, Beemer wrote:
Quote: |
nuckolls.bob(at)cox.net wrote:
> At 06:38 AM 8/12/2008 -0700, you wrote:
>
> That's a popular myth promulgated mostly by two individuals
> who are demonstrably un-qualified to judge my work.
> They appear to have never read and/or understood design
> goals I (and hundreds of my colleagues) have embraced as
> aircraft system integrators and component designers for 30+ years.
Well, my design goals are different than someone building a Lancair
IV. They are also different than Cessna's. I think the overall
objective should be the same - supply me 12 volts and don't hurt me. I
see that you are leading us toward this objective.
I have no desire to re-hash opinion differences nor point fingers. I
want to wire my Kitfox.
>
> I'm not sure you understand the spirit and intent of
> my offerings here on the List and elsewhere. I think we
> can agree that airplanes, with all the potential for
> utility and pleasure, are exceedingly unforgiving machines.
> The environment in which we operate them can be equally
> unforgiving. Everything I've bolted to an airplane has
> these design goals in mind. (1) Utility (function as
> specified/advertised). (2) Weight. (3) Cost of ownership.
> and last but not least (4) Risk Mitigation.
>
> In categories 1-3, the stock automotive alternator is
> a stellar performer and quite suited to the task aboard
> airplanes but with two shortcomings"
>
> In the category of UTILITY: ON/OFF control at any time
> under any conditions without risk to itself or other
> components in the system. This is how alternators/generators
> have functioned in aircraft since day-one. There are both
> operational and risk mitigation advantages for giving the pilot
> and OV protection systems a means of managing alternator
> operations . . .
>
> and RISK MITIGATION: I have seen no design to data for
> which the risk of OV runaway is zero. Further, the potential
> for a high-energy even in a runaway alternator is significant.
> See:
>
> http://aeroelectric.com/articles/When_is_110V_not_Over_Voltage.pdf
>
> Since day one in aircraft, independent monitoring of bus voltage
> COMBINED with the ability to shut an alternator/generator off
> at will relieves the system designer of a time-consuming
> and costly effort of designing, proving and maintaining a system
> reliability in the 10-to-the-minus-9-failures-per-flight-hour
> category (FAA-speak for 'never happens').
>
> Failure tolerance is integral to every design and goes directly
> to both Cost of Ownership and Risk Mitigation.
>
> By making my part of the program failure tolerant without
> adding risk to the overall flight system, costs of ownership
> goes down, and parts-count goes down (driving reliability
> up). But even if my gizmo craps every 1000 hours, it's not
> a safety of flight issue - only a cost of ownership issue.
I don't see any debate here. I'm not a fan of the "more is better"
philosophy. KISS is the rule on the K'fox. I'm agonizing over
following Z-19RB, but with my EFI engine, I feel the redundancy
outweighs the complicity.
>
> If I were building an airplane, it WOULD have a
> stock automotive alternator with Z-24 installed as
> an interim solution to get flying and laying the
> ground work for installation of a permanent solution
> at a later date as described in:
>
> http://www.aeroelectric.com/articles/
> Adapting_IR_Alternators_to_Aircraft.pdf
Wow. Telling statement, that. It quite well answers the question "What
would Bob do...?"
>
>
> Why would I have even crafted Z-24 if I were attempting
> to quash the use of IR alternators? And why would I
> follow up the Z-24 interim with the new-and-improved
> alternative? I'll suggest that these two drawings are
> a positive if not enthusiastic endorsement of the
> value offered by a host of automotive alternator
> products.
>
> No, I have never said that IR alternators do not belong
> on aircraft. I have said that I cannot RECOMMEND them because
> the current state of our art does not allow me to integrate
> them in satisfaction of the design goals cited above.
> Z-24 was a first crack at meeting those design goals.
> It has some short comings which are discussed in detail in
> publications on my website. Those short comings will
> be addressed in due course.
>
But you just said you would use one, yet not recommend one. Am I
mis-interpreting this somehow?
>
> First, there are ways to make ANY selection of engine driven
> power source suited to use in the aircraft environment.
> Further, if you choose not to embrace my design goals, then
> there is still good value to be received from bolting a stock
> automotive alternator to your airplane. As long as you
> understand and accept the risks and perhaps lack of utility
> compared to the majority of the GA fleet, then I have
> no heartburn with it. But if you're being mis-advised into
> believing there is little or no increased risks as
> compared to contemporary aircraft design philosophies,
> you owe it to yourself to at least elevate your understanding
> to the level needed to make a well considered decision.
> Don't do anything based on my (or anyone else's recommendations)
> unless you understand and personally embrace the design
> goals that go along with those recommendations.
By installing Z-13RB with Z-24 integrated, I'm providing for the bad
alternator all together, by disconnecting it from the system entirely.
From then on, I am carried by the battery(s), and need to design
enough ah margin to get me home or nearest, anyway.
>
> Sounds like a 3.5# SD-8 would do nicely for you. There are
> thousands of LongEz and VariEz aircraft flying with this
> machine as the only source of engine driven power.
>
Ummm, I'm sure they're great units, and would do fine. But I can't use
the gear drive.
>
> But if you wanted to put a little 35 or 40A wound
> field alternator on, that would not be a bad
> decision either . . . internally or externally
> regulated.
>
> Let's channel this discussion toward establishing
> your design goals and then meeting them. Please set
> aside any notions that I or anyone else here on the
> list is going to twist your arm to do anything except
> perhaps those things which are overtly foolhardy or
> dangerous.
>
> Have you completed a load analysis of just what
> your energy requirements are?
>
> See:
>
> http://www.aeroelectric.com/PPS/Load_Analysis/Blank_Form.pdf
>
> This form is designed to facilitate a study of your
> true energy needs. Until those are known, may I
> suggest that alternator selection for the purpose
> of minimizing weight is premature?
>
> Bob . . .
No ones talking me into anything. I'm trying to decide how to proceed
on my new airplane.
I haven't analyzed it. I have no idea how to check the ECM and coil
draw. Right now I have 55amps, Z-24, and 17ah running the motor just
fine. I have two readily available alternator options, both 40amp, one
weighs 6.5lbs, the other 4.5 lbs. I'm just trying to figure out if
there's a better way to wire up the new airplane. If I can install the
JD dynamo with external reg, spin it up to 9000rpm, and live to tell
the tale, I'll consider it on its merits. But I would like to know if
it's feasible to do so, or a bad choice due to something I'm not being
told by the advertising.
Bradley
--------
Beemer
KF2 (and now an M3!)
Middle Georgia
Read this topic online here:
http://forums.matronics.com/viewtopic.php?p=198613#198613
|
| - The Matronics AeroElectric-List Email Forum - | | Use the List Feature Navigator to browse the many List utilities available such as the Email Subscriptions page, Archive Search & Download, 7-Day Browse, Chat, FAQ, Photoshare, and much more:
http://www.matronics.com/Navigator?AeroElectric-List |
|
|
|
Back to top |
|
 |
nuckolls.bob(at)cox.net Guest
|
Posted: Thu Aug 14, 2008 4:51 pm Post subject: John Deere dynamo |
|
|
Quote: |
I have no desire to re-hash opinion differences nor point fingers. I want
to wire my Kitfox.
|
Understood.
Quote: |
I don't see any debate here. I'm not a fan of the "more is better"
philosophy. KISS is the rule on the K'fox. I'm agonizing over following
Z-19RB, but with my EFI engine, I feel the redundancy outweighs the complicity.
|
No debated intended. Are you interested in any time, any
conditions ON/OFF and/or ov protection for your alternator
of choice?
Quote: | > If I were building an airplane, it WOULD have a
> stock automotive alternator with Z-24 installed as
> an interim solution to get flying and laying the
> ground work for installation of a permanent solution
> at a later date as described in:
>
>
http://www.aeroelectric.com/articles/Adapting_IR_Alternators_to_Aircraft.pdf
>
>
Wow. Telling statement, that. It quite well answers the question "What
would Bob do...?"
|
Or anyone else who is interested in design goals cited . . .
Quote: | >
>
> Why would I have even crafted Z-24 if I were attempting
> to quash the use of IR alternators? And why would I
> follow up the Z-24 interim with the new-and-improved
> alternative? I'll suggest that these two drawings are
> a positive if not enthusiastic endorsement of the
> value offered by a host of automotive alternator
> products.
>
> No, I have never said that IR alternators do not belong
> on aircraft. I have said that I cannot RECOMMEND them because
> the current state of our art does not allow me to integrate
> them in satisfaction of the design goals cited above.
> Z-24 was a first crack at meeting those design goals.
> It has some short comings which are discussed in detail in
> publications on my website. Those short comings will
> be addressed in due course.
>
But you just said you would use one, yet not recommend one. Am I
mis-interpreting this somehow?
|
The time when I was unable to recommend them was BEFORE Z-24
was crafted . . . I've designed dozens of engine driven power
systems for both OBAM and TC aircraft. Until about 10 years
ago, the alternators of choice were externally regulated . . .
but mostly because that's the way we've been doing it for
quite some time.
The IR alternator was obviously future king-of-the-market
even in airplanes. The challenge was to figure out how
one could take any size, any brand, any pedigree IR
alternator and integrate it into an aircraft while not
giving up control and protection philosophies that have
served us well.
Z-24 was the first crack at it . . . but if the pilot
operates the system to turn the alternator OFF while
it's running loaded and at RPM, then there was risk
of a load-dump transient killing the alternator's own
regulator. A few folks experienced this unhappy event
which did place a cloud over the Z-24 control/protection
philosophy.
We went back to the drawing board and crafted a product
that will drop into an existing Z-24 installation that
takes care of the load-dump, protects the el-cheeso
contactor from arcing, provides any time, any
conditions ON/OFF control -AND- OV protection in
a single product.
Quote: | By installing Z-13RB with Z-24 integrated, I'm providing for the bad
alternator all together, by disconnecting it from the system entirely.
From then on, I am carried by the battery(s), and need to design enough
ah margin to get me home or nearest, anyway.
|
Yes, as long as you don't exercise the ON/OFF switch
except at low rpm (pre takeoff, pre parking) then
Z-24 does offer OV protection.
Quote: | >
> Sounds like a 3.5# SD-8 would do nicely for you. There are
> thousands of LongEz and VariEz aircraft flying with this
> machine as the only source of engine driven power.
>
Ummm, I'm sure they're great units, and would do fine. But I can't use the
gear drive.
|
I didn't grasp until now that you were running an
automotive conversion . . . okay, how about the 3.5
pound cousin to the SD-8
http://aeroelectric.com/Pictures/Alternators/Kubota.jpg
This critter is good for about 12-15A when turned
fast enough and assuming that the companion regulator-
rectifier isn't over-stressed by the higher input
operating voltage. I've prayed a bit over the
schematics for an exemplar device . . .
http://aeroelectric.com/Pictures/Schematics/3-Phase_PM_Rectifier_Regulator.gif
. . . and it seems likely that the device would
tolerate the higher rpm. In a few months, I'll have
a drive stand up and running and will be able to
test the hypothesis in the shop. If you're willing
to invest in the experiment, you can supply results
that would be of interest to lots of other folks
here on the List.
Quote: | I haven't analyzed it. I have no idea how to check the ECM and coil draw.
Right now I have 55amps, Z-24, and 17ah running the motor just fine. I
have two readily available alternator options, both 40amp, one weighs
6.5lbs, the other 4.5 lbs. I'm just trying to figure out if there's a
better way to wire up the new airplane. If I can install the JD dynamo
with external reg, spin it up to 9000rpm, and live to tell the tale, I'll
consider it on its merits. But I would like to know if it's feasible to do
so, or a bad choice due to something I'm not being told by the advertising.
|
The risks for trying are low. The regulator's stability
might be less than idea and/or the regulator could fail due
to higher than design voltage. As long as you have OV protection,
risks are to the regulator only.
One thing we DO know is that automotive wound-field alternators
do live happily in airplanes running 10,000+ RPM. This is the
next-to-zero-risk approach.
How much time are you willing to invest in the experiment
to validate the 4.5# decision?
Bob . . .
| - The Matronics AeroElectric-List Email Forum - | | Use the List Feature Navigator to browse the many List utilities available such as the Email Subscriptions page, Archive Search & Download, 7-Day Browse, Chat, FAQ, Photoshare, and much more:
http://www.matronics.com/Navigator?AeroElectric-List |
|
|
|
Back to top |
|
 |
echristley(at)nc.rr.com Guest
|
Posted: Sat Aug 16, 2008 8:06 am Post subject: John Deere dynamo |
|
|
Robert L. Nuckolls, III wrote:
I'm using a PM generator, and I'm unsure about the regulator that came
with the kit. From what I can gather, it appears that Harley-Davidson is
still using linear regulators. I'd rather avoid that extra heat and
wear if possible.
--
http://www.ernest.isa-geek.org
| - The Matronics AeroElectric-List Email Forum - | | Use the List Feature Navigator to browse the many List utilities available such as the Email Subscriptions page, Archive Search & Download, 7-Day Browse, Chat, FAQ, Photoshare, and much more:
http://www.matronics.com/Navigator?AeroElectric-List |
|
|
|
Back to top |
|
 |
nuckolls.bob(at)cox.net Guest
|
Posted: Sat Aug 16, 2008 12:17 pm Post subject: John Deere dynamo |
|
|
At 12:05 PM 8/16/2008 -0400, you wrote:
Quote: |
<echristley(at)nc.rr.com>
Robert L. Nuckolls, III wrote:
>
> This critter is good for about 12-15A when turned
> fast enough and assuming that the companion regulator-
> rectifier isn't over-stressed by the higher input
> operating voltage. I've prayed a bit over the
> schematics for an exemplar device . . .
>
>http://aeroelectric.com/Pictures/Schematics/3-Phase_PM_Rectifier_Regulator.gif
>
Bob, this is a switching type regulator, isn't it?
|
Uhhh . . . I guess you could call it that. It's not the
legacy switch-mode regulator where duty-cycle controlled
switches, inductors, capacitors and catch diodes do high
efficiency voltage shifting.
These are simple series switches that either reduce
throughput by delaying the time between waveform zero-
crossing and the firing of an SCR at the optimum later
time to throttle throughput. It's exceedingly simple
and adequate to the task if not terribly efficient.
These regulators use single junction diodes AND
4-layer SCRs. Total voltage drop in the on-state,
especially in a 14v system chews up quite a chunk
of system efficiency. They're better at the higher
voltages so a 28v version is not quite so bad.
I've often thought about rewinding one of these
things for say 60-80 volts of 3-phase AC output
that would then be rectified and conditioned by
a REAL switch-mode supply. But pencilling the numbers
wasn't a BIG improvement in efficiency and a BIG
increase in parts-count.
Quote: | I'm using a PM generator, and I'm unsure about the regulator that came
with the kit. From what I can gather, it appears that Harley-Davidson is
still using linear regulators. I'd rather avoid that extra heat and wear
if possible.
|
I doubt that any one does a true linear regulator
at these power levels. They HAVE moved from the
pure shunt (waste what you don't need) type of
regulator common to 1970 designs) to a series
configuration that does not waste as much energy
overall. The only heat issue is in keeping the
regulator itself cool . . . and as you can see
in pictures of the various products offered, the
BIG guys are in cast housings with fins. There
are no significant wear advantages between the
various offerings as long as things stay cool
enough.
Bob . . .
----------------------------------------)
( . . . a long habit of not thinking )
( a thing wrong, gives it a superficial )
( appearance of being right . . . )
( )
( -Thomas Paine 1776- )
----------------------------------------
| - The Matronics AeroElectric-List Email Forum - | | Use the List Feature Navigator to browse the many List utilities available such as the Email Subscriptions page, Archive Search & Download, 7-Day Browse, Chat, FAQ, Photoshare, and much more:
http://www.matronics.com/Navigator?AeroElectric-List |
|
|
|
Back to top |
|
 |
|
|
You cannot post new topics in this forum You cannot reply to topics in this forum You cannot edit your posts in this forum You cannot delete your posts in this forum You cannot vote in polls in this forum You cannot attach files in this forum You can download files in this forum
|
Powered by phpBB © 2001, 2005 phpBB Group
|