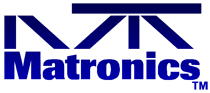 |
Matronics Email Lists Web Forum Interface to the Matronics Email Lists
|
View previous topic :: View next topic |
Author |
Message |
nuckolls.bob(at)aeroelect Guest
|
Posted: Wed Feb 04, 2009 8:29 am Post subject: Dual Plasma III and Z-13/8 |
|
|
At 10:50 PM 2/3/2009, you wrote:
Quote: | Hoo-boy....
Thanks Bob and others for recommending Z13/8....happy to continue with your dwgs and single battery..... till I read about the Lightspeed manual stating at paragraph ..2.7..
Electrical System Requirements
All Plasma CDI systems can be used with 12 or 24 volt electrical systems. Input voltages above 35 volts or reversed polarity will cause system dammage. |
Aha! A number. Okay, until we're offered different
values, we can work with the idea that DO-160 upper
operating voltage limits for 28v systems apply here . . .
[img]cid:.0[/img]
Quote: | For this reason it is mandatory that all aircraft using Plasma CD Ignitions are equipped with over-voltage protection in their alternator charging system(s). Over-voltage is a requirement for certified aircraft. |
. . . yes.
Quote: | Power connection must be directly to the battery terminals to avoid voltage spikes and electrical noise. |
??? The "noise" and "spike" levels at the battery
terminals are essentially consistent with those throughout
the airplane's electrical bus structure.
In fact, I'm revising the 'Connection's chapter on batteries
to confess my own deprogramming from membership in the cult
of "Batteries are Ultimate Defenders from Electrical Evils".
It's an easy notion to buy into and yours truly did it for
decades. After all, here's an electro-chemical energy system
with a huge capability as both storage and delivery of
Joules (watt-seconds). OBVIOUSLY . . . this big wad of
lead and acid must offer a great deal of inertia . . . a
sort of electrical flywheel that resists all perturbations
of bus voltage.
I will refer the readers to the same simple ideas we've
always understood about batteries when it came to selecting
the LV warning setpoint. We KNOW that batteries cannot deliver
significant amounts of energy at voltages GREATER than
the chemistry's physics. I.e. 12.5 volts and below. We also
KNOW that to effectively recharge a battery, i.e. stuff
significant amounts of energy back into it, the bus voltage
must be on the order of 13.5 and higher.
It follows then that a bus voltage of 13.0 or higher means
that system loads are being supported by a functioning
alternator. Ergo, this is a good place to set the LV
annunciation system.
Well duh . . . what about this no battery's land of 12.5
to 13.5 volts? Exactly what does the battery do for us
in terms of resisting "wiggles" of voltage within these
bounds? Answer: Nothing.
I was most chagrined to make this connection so late in
my career. I had been parroting the mantra of battery
performance as a starter of engines, a repository of
alternator out energy AND being the "best filter of noise
on the bus".
The battery's benefits with respect to noise is not
insignificant when the alternator is running . . . this
is because the bus is being supported at or above the
threshold for the battery to be a significant LOAD on
perturbations . . . especially on positive excursions.
But look at this trace:
http://www.aeroelectric.com/Pictures/Curves/Safari_Bus_Noise_1.gif
This was taken from my GMC van and shows noises on the
bus on the order of 1.5 volts peak-to-peak. This was
measured AT the battery. A similar trace was delivered
by a measurement at the cigar lighter plug.
Aluminum should never be used as an electrical conductor for the Plasma CDI.
When and how would aluminum wire EVER be considered? I'm
mystified as to why it's even mentioned.
Use only the supplied aircraft quality stranded wire.
Quote: | Electrical Operating Instructions
Dual Systems only: If you have installed an aux battery per the LSE supplied drawing, monitor your voltmeter and do not switch to the aux battery until the supply voltage of the main battery is below 6.5 Volts or the engine is not running smoothly. After switching to the aux battery, your voltmeter will read the voltage remaining in your aux battery. |
When a lead acid battery falls below 11.0 volts, it is 95+
percent used up and falling fast. "Monitoring" is an
activity that adds to pilot workload for dealing with
alternator-out operations. NOT good design. When the
alternator quits, the prudent design calls for a simple
activity that requires no further attention as systems
manager or diagnostician until after the airplane
is on the ground.
Quote: | Do not switch your main alternator breaker in flight to avoid potentially damaging voltage spikes. This does not apply to the alternator field breaker.
|
This has been discussed at length here on the List.
The simple ideas and their effects are well understood.
Many airplanes don't even have b-lead breakers having
been replaced by current limiters on the firewall. All
the Z-figures speak to this
Quote: |
And further at para.2.8A....
A. Power Supply -
· When connecting the power supply, route the positive lead to a pull-able breaker, 4-cyl systems use 5A ..., and then directly to the battery plus terminal, bypassing any electrical buss or master solenoid. Refer to the Input Connector Diagram & the Electrical Requirements section 2.7.
|
This blazes a "new trail" in the woods. There are
no accessories offered to TC aviation where such
practice would be considered.
These words go to the notion that prudent designs
do the failure modes effects analysis to insure that
no single failure of a failure-probable component puts
the airplane at risk. Exactly how that is accomplished
is normally left up to the system integrator. Acceptable
FMEA has been a consistent design goal for each of the
Z-figures.
I can deduce no reason that a Lightspeed or any other
ignition system should not run happily from a battery
bus fuse.
Quote: |
How do I incorporate these- the 2 x "pullable" C/bs and 2 x batteries - within Z13/8...? |
Put second battery in place by . . .
http://www.aeroelectric.com/PPS/Adobe_Architecture_Pdfs/Z35A.pdf
and feed each ignition from one battery using . . .
http://aeroelectric.com/Pictures/Schematics/Battery_Feed_for_Ignition.pdf
Now, understand that I offer the suggestions in deference
to Lightspeed requirements. Please understand that
I find significant shortcomings in Lightspeed requirements
with respect to parts count, reliability, and failure
mode effects analysis.
Summary:
If the ov trip on these systems is equal to or greater
than 32.2 volts, then installation in a 14v system
with switches and fuses should be no big deal. This
ASSUMES that the crowbar ov protection system has
no parasitic trip modes. We've encountered this
phenomenon a couple of times and instituted design
changes to mitigate the problems as they were
discovered.
At the same time, it begs the question as to value
of including fail-inactive OV protection internal to the
product. Given what we know right now, I'll suggest
that:
(1) The feature adds no demonstrable value. The setpoint
is probably WAY above any level the product would
encounter in a well crafted 14v system.
(2) It inserts new risks for unacceptable malfunction
(single event kills the engine).
(3) Benefits for connection directly to the battery
are not demonstrable with a study of simple-ideas.
The practice is contrary to design goals and
practice for hundreds of thousands of airplanes
for nearly a century.
(4) The feature prevents learned and experienced
system integrators from incorporating the product
into new designs. Designes that embrace a rich history
of lessons learned and accepted practice, i.e.
powering the product from fuse-protected battery
busses.
Bob . . .
| - The Matronics AeroElectric-List Email Forum - | | Use the List Feature Navigator to browse the many List utilities available such as the Email Subscriptions page, Archive Search & Download, 7-Day Browse, Chat, FAQ, Photoshare, and much more:
http://www.matronics.com/Navigator?AeroElectric-List |
|
Description: |
|
Filesize: |
29.68 KB |
Viewed: |
210 Time(s) |
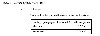
|
|
|
Back to top |
|
 |
longg(at)pjm.com Guest
|
Posted: Wed Feb 04, 2009 9:36 am Post subject: Dual Plasma III and Z-13/8 |
|
|
Bob,
If I choose the routed suggested by your diagram to run both ign boxes, would you duplicate the fuse & 14 AWG from the batt buss or simply run the 14 AWG to a bus bar such that I could hook up both 5 amp cb’s?
It appears that this is only adding hardware from the already existing entry point of the buss and further extending it to cb’s. The only valid argument I see is the ability to reset a cb in crisis mode (after a big OV event has blown both fuses) and continue down the road – albeit with just about everything else riding on the buss blown as well.
Thanks so much for your input on this topic. I’m sorry you are not getting paid for this prime time activity. Hopefully there is a way we can donate to your cause. Recently I read a thread from some FAA lawyers who were talking about mechanical standards and regulation. One said that the FAA regulations for mechanical compliance (not design) are designed to be debated. He was referring to the often vague terms in which the regulations are written. They should be left open enough for debate, but not too wide open as to allow broad deviation from normal practices (depends who’s calling what normal).
IMO this type of debate should strive to improve the quality/design of the products offered in such a way that the improvements are both advantageous in technological design and add a factor of safety for the end user. For my $$ pure technology advancement that adds little or takes away from the integrity of well known systems is a bad investment.
So, debate is good and I hope Klaus and others accept the forward thinking on which their products are offered.
Great stuff.
Glenn
Do Not Archive
From: owner-aeroelectric-list-server(at)matronics.com [mailto:owner-aeroelectric-list-server(at)matronics.com] On Behalf Of Robert L. Nuckolls, III
Sent: Wednesday, February 04, 2009 11:27 AM
To: aeroelectric-list(at)matronics.com
Subject: Dual Plasma III and Z-13/8
At 10:50 PM 2/3/2009, you wrote:
Hoo-boy....
Thanks Bob and others for recommending Z13/8....happy to continue with your dwgs and single battery..... till I read about the Lightspeed manual stating at paragraph ..2.7..
Electrical System Requirements
All Plasma CDI systems can be used with 12 or 24 volt electrical systems. Input voltages above 35 volts or reversed polarity will cause system dammage.
Aha! A number. Okay, until we're offered different
values, we can work with the idea that DO-160 upper
operating voltage limits for 28v systems apply here . . .
[img]cid:image001.jpg(at)01C986C3.BBBA8E40[/img]
For this reason it is mandatory that all aircraft using Plasma CD Ignitions are equipped with over-voltage protection in their alternator charging system(s). Over-voltage is a requirement for certified aircraft.
. . . yes.
Power connection must be directly to the battery terminals to avoid voltage spikes and electrical noise.
??? The "noise" and "spike" levels at the battery
terminals are essentially consistent with those throughout
the airplane's electrical bus structure.
In fact, I'm revising the 'Connection's chapter on batteries
to confess my own deprogramming from membership in the cult
of "Batteries are Ultimate Defenders from Electrical Evils".
It's an easy notion to buy into and yours truly did it for
decades. After all, here's an electro-chemical energy system
with a huge capability as both storage and delivery of
Joules (watt-seconds). OBVIOUSLY . . . this big wad of
lead and acid must offer a great deal of inertia . . . a
sort of electrical flywheel that resists all perturbations
of bus voltage.
I will refer the readers to the same simple ideas we've
always understood about batteries when it came to selecting
the LV warning setpoint. We KNOW that batteries cannot deliver
significant amounts of energy at voltages GREATER than
the chemistry's physics. I.e. 12.5 volts and below. We also
KNOW that to effectively recharge a battery, i.e. stuff
significant amounts of energy back into it, the bus voltage
must be on the order of 13.5 and higher.
It follows then that a bus voltage of 13.0 or higher means
that system loads are being supported by a functioning
alternator. Ergo, this is a good place to set the LV
annunciation system.
Well duh . . . what about this no battery's land of 12.5
to 13.5 volts? Exactly what does the battery do for us
in terms of resisting "wiggles" of voltage within these
bounds? Answer: Nothing.
I was most chagrined to make this connection so late in
my career. I had been parroting the mantra of battery
performance as a starter of engines, a repository of
alternator out energy AND being the "best filter of noise
on the bus".
The battery's benefits with respect to noise is not
insignificant when the alternator is running . . . this
is because the bus is being supported at or above the
threshold for the battery to be a significant LOAD on
perturbations . . . especially on positive excursions.
But look at this trace:
http://www.aeroelectric.com/Pictures/Curves/Safari_Bus_Noise_1.gif
This was taken from my GMC van and shows noises on the
bus on the order of 1.5 volts peak-to-peak. This was
measured AT the battery. A similar trace was delivered
by a measurement at the cigar lighter plug.
Aluminum should never be used as an electrical conductor for the Plasma CDI.
When and how would aluminum wire EVER be considered? I'm
mystified as to why it's even mentioned.
Use only the supplied aircraft quality stranded wire.
Electrical Operating Instructions
Dual Systems only: If you have installed an aux battery per the LSE supplied drawing, monitor your voltmeter and do not switch to the aux battery until the supply voltage of the main battery is below 6.5 Volts or the engine is not running smoothly. After switching to the aux battery, your voltmeter will read the voltage remaining in your aux battery.
When a lead acid battery falls below 11.0 volts, it is 95+
percent used up and falling fast. "Monitoring" is an
activity that adds to pilot workload for dealing with
alternator-out operations. NOT good design. When the
alternator quits, the prudent design calls for a simple
activity that requires no further attention as systems
manager or diagnostician until after the airplane
is on the ground.
Do not switch your main alternator breaker in flight to avoid potentially damaging voltage spikes. This does not apply to the alternator field breaker.
This has been discussed at length here on the List.
The simple ideas and their effects are well understood.
Many airplanes don't even have b-lead breakers having
been replaced by current limiters on the firewall. All
the Z-figures speak to this
And further at para.2.8A....
A. Power Supply -
· When connecting the power supply, route the positive lead to a pull-able breaker, 4-cyl systems use 5A ...., and then directly to the battery plus terminal, bypassing any electrical buss or master solenoid. Refer to the Input Connector Diagram & the Electrical Requirements section 2.7.
This blazes a "new trail" in the woods. There are
no accessories offered to TC aviation where such
practice would be considered.
See here..... http://www.lightspeedengineering.com/Manuals/CdiManual_PlasmaII_II+_III.htm
And then for Dual Plasma CDI, Klaus further recommends.....
For Dual PLASMA CDI Installations, an auxiliary battery and dual ignition indicator lights are recommended. Please click here for an aux battery wiring diagram.
See Figure 4 for the dual ignition indicator lights diagram: click here.
See here for the AUX Batt Diagram..........http://www.lightspeedengineering.com/Manuals/PS_Diagram.htm
These words go to the notion that prudent designs
do the failure modes effects analysis to insure that
no single failure of a failure-probable component puts
the airplane at risk. Exactly how that is accomplished
is normally left up to the system integrator. Acceptable
FMEA has been a consistent design goal for each of the
Z-figures.
I can deduce no reason that a Lightspeed or any other
ignition system should not run happily from a battery
bus fuse.
How do I incorporate these- the 2 x "pullable" C/bs and 2 x batteries - within Z13/8...?
Put second battery in place by . . .
http://www.aeroelectric.com/PPS/Adobe_Architecture_Pdfs/Z35A.pdf
and feed each ignition from one battery using . . .
http://aeroelectric.com/Pictures/Schematics/Battery_Feed_for_Ignition.pdf
Now, understand that I offer the suggestions in deference
to Lightspeed requirements. Please understand that
I find significant shortcomings in Lightspeed requirements
with respect to parts count, reliability, and failure
mode effects analysis.
Summary:
If the ov trip on these systems is equal to or greater
than 32.2 volts, then installation in a 14v system
with switches and fuses should be no big deal. This
ASSUMES that the crowbar ov protection system has
no parasitic trip modes. We've encountered this
phenomenon a couple of times and instituted design
changes to mitigate the problems as they were
discovered.
At the same time, it begs the question as to value
of including fail-inactive OV protection internal to the
product. Given what we know right now, I'll suggest
that:
(1) The feature adds no demonstrable value. The setpoint
is probably WAY above any level the product would
encounter in a well crafted 14v system.
(2) It inserts new risks for unacceptable malfunction
(single event kills the engine).
(3) Benefits for connection directly to the battery
are not demonstrable with a study of simple-ideas.
The practice is contrary to design goals and
practice for hundreds of thousands of airplanes
for nearly a century.
(4) The feature prevents learned and experienced
system integrators from incorporating the product
into new designs. Designes that embrace a rich history
of lessons learned and accepted practice, i.e.
powering the product from fuse-protected battery
busses.
Bob . . .
| - The Matronics AeroElectric-List Email Forum - | | Use the List Feature Navigator to browse the many List utilities available such as the Email Subscriptions page, Archive Search & Download, 7-Day Browse, Chat, FAQ, Photoshare, and much more:
http://www.matronics.com/Navigator?AeroElectric-List |
|
Description: |
|
Filesize: |
29.68 KB |
Viewed: |
189 Time(s) |
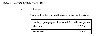
|
|
|
Back to top |
|
 |
echristley(at)nc.rr.com Guest
|
Posted: Wed Feb 04, 2009 9:48 am Post subject: Dual Plasma III and Z-13/8 |
|
|
Robert L. Nuckolls, III wrote:
Quote: | >
> And further at para.2.8A....
>
> A. Power Supply -
>
> · When connecting the power supply, route the positive lead
> to a pull-able breaker, 4-cyl systems use 5A ...., and then directly
> to the battery plus terminal, bypassing any electrical buss or master
> solenoid. Refer to the Input Connector Diagram & the Electrical
> Requirements section 2.7.
This blazes a "new trail" in the woods. There are
no accessories offered to TC aviation where such
practice would be considered.
|
Considering that this replaces a mag, does it really? The mag is
connected directly without going through any bus or master solenoid.
It's just that the mag packages everything in one neat container.
I could be wrong.
| - The Matronics AeroElectric-List Email Forum - | | Use the List Feature Navigator to browse the many List utilities available such as the Email Subscriptions page, Archive Search & Download, 7-Day Browse, Chat, FAQ, Photoshare, and much more:
http://www.matronics.com/Navigator?AeroElectric-List |
|
|
|
Back to top |
|
 |
nuckolls.bob(at)aeroelect Guest
|
Posted: Wed Feb 04, 2009 9:56 am Post subject: Dual Plasma III and Z-13/8 |
|
|
11:47 AM 2/4/2009, you wrote:
Quote: |
Christley <echristley(at)nc.rr.com>
Robert L. Nuckolls, III wrote:
>>
>>And further at para.2.8A....
>>
>>A. Power Supply -
>>
>>· When connecting the power supply,
>>route the positive lead to a pull-able
>>breaker, 4-cyl systems use 5A ...., and then
>>directly to the battery plus terminal,
>>bypassing any electrical buss or master
>>solenoid. Refer to the Input Connector
>>Diagram & the Electrical Requirements section 2.7.
>
> This blazes a "new trail" in the woods. There are
> no accessories offered to TC aviation where such
> practice would be considered.
Considering that this replaces a mag, does it
really? The mag is connected directly without
going through any bus or master solenoid.
It's just that the mag packages everything in one neat container.
I could be wrong.
|
Don't understand. The mag is not directly connected
to nor does it depend on battery power.
Bob . . .
----------------------------------------)
( . . . a long habit of not thinking )
( a thing wrong, gives it a superficial )
( appearance of being right . . . )
( )
( -Thomas Paine 1776- )
----------------------------------------
| - The Matronics AeroElectric-List Email Forum - | | Use the List Feature Navigator to browse the many List utilities available such as the Email Subscriptions page, Archive Search & Download, 7-Day Browse, Chat, FAQ, Photoshare, and much more:
http://www.matronics.com/Navigator?AeroElectric-List |
|
|
|
Back to top |
|
 |
nuckolls.bob(at)aeroelect Guest
|
Posted: Wed Feb 04, 2009 10:30 am Post subject: Dual Plasma III and Z-13/8 |
|
|
At 11:34 AM 2/4/2009, you wrote:
Quote: | Bob,
If I choose the routed suggested by your diagram
to run both ign boxes, would you duplicate the
fuse & 14 AWG from the batt buss or simply run
the 14 AWG to a bus bar such that I could hook up both 5 amp cb’s?
|
If you create an ignition bus that services
contemporary conventions for minimizing the energy
exposure of battery-feed wires during crash
events, then you need a disconnect at the battery.
A design goal for inoculating the aircraft's
accessories from single-points of failure becoming
hazardous.
This suggests that dual ignition systems are either
powered from multiple busses that have low probability
of common failure or a single bus with a VERY low
probability of failure.
We've cited design and maintenance goals for making
sure that a battery bus connected to a well maintained
RG battery is the single bus with a very low
probability of failure.
This gave the writer comfort in suggesting that
separate fuses for two ignition systems fed from
an always hot bus supported was a good design
when that bus was supported by (1) well maintained
RG battery (2) main alternator (3) aux alternator
and (4) protected with very fast fuses that addressed
our goals for crash safety.
Quote: | It appears that this is only adding hardware
from the already existing entry point of the
buss and further extending it to cb’s. The only
valid argument I see is the ability to reset a
cb in crisis mode (after a big OV event has
blown both fuses) and continue down the road –
albeit with just about everything else riding on the buss blown as well.
|
That's the real sticking point. If we're doing due
diligence and honoring our past teachers, there's no
reason for the ignition system to even have such a
feature. No mater how honorable the motivation for
including it, it created FEMA issues that would
get the thing booted from a TC aircraft.
Quote: |
Thanks so much for your input on this topic. I’m
sorry you are not getting paid for this prime
time activity. Hopefully there is a way we can donate to your cause.
|
I wouldn't do it if it were not useful to me
personally . . . so don't be concerned for any
overt lack of compensation . . .
Quote: | Recently I read a thread from some FAA lawyers
who were talking about mechanical standards and
regulation. One said that the FAA regulations
for mechanical compliance (not design) are
designed to be debated. He was referring to the
often vague terms in which the regulations are
written. They should be left open enough for
debate, but not too wide open as to allow broad
deviation from normal practices (depends who’s calling what normal).
|
Gee do they think? Do you suppose this is why
folks in the airframe services business will shop
around for the most compliant ACO to get their
STC or 337 on an airplane? Like our tax codes,
the FARS are a study in debate prompted by a
lack of teaching to simple-ideas.
The same phenomenon is infecting industry and
government with an MBA/Harvard-Law mentality that
curiosity, creativity and wisdom of experience
by honorable individuals can be replaced with
"The Plan".
Quote: |
IMO this type of debate should strive to improve
the quality/design of the products offered in
such a way that the improvements are both
advantageous in technological design and add a
factor of safety for the end user. For my $$
pure technology advancement that adds little or
takes away from the integrity of well known systems is a bad investment.
|
Absolutely.
Quote: |
So, debate is good and I hope Klaus and others
accept the forward thinking on which their products are offered.
|
Sure. I recall with great fondness the circumstances
of my last really rewarding job. I cannot recall a
single instance of walking with trepidation into
a come-to-jesus meeting in Beech's Targets Division.
We had many meetings were some portion of a program
was in trouble. As the problem was discussed and
ideas circulated around the table, new avenues of
attack would emerge. Folks freely volunteered to
help out. You always walked out of those meetings
with a feeling of accomplishment and renewal. This
is how I imagine the meetings in Kelly Johnson's
"Skunk Works" worked. This is a tribute to a handful
of individuals at the ship's wheel.
You can bet the bank on the idea that progress
was bench marked by the successful integration of
simple-ideas to satisfaction of design goals
by a group of honorable individuals. That's my
vision of what should happen here on the List.
Bob . . .
| - The Matronics AeroElectric-List Email Forum - | | Use the List Feature Navigator to browse the many List utilities available such as the Email Subscriptions page, Archive Search & Download, 7-Day Browse, Chat, FAQ, Photoshare, and much more:
http://www.matronics.com/Navigator?AeroElectric-List |
|
|
|
Back to top |
|
 |
echristley(at)nc.rr.com Guest
|
Posted: Wed Feb 04, 2009 12:18 pm Post subject: Dual Plasma III and Z-13/8 |
|
|
Robert L. Nuckolls, III wrote:
Quote: |
<nuckolls.bob(at)aeroelectric.com>
11:47 AM 2/4/2009, you wrote:
>
> <echristley(at)nc.rr.com>
>
> Robert L. Nuckolls, III wrote:
>>>
>>> And further at para.2.8A....
>>>
>>> A. Power Supply -
>>>
>>> · When connecting the power supply, route the positive lead
>>> to a pull-able breaker, 4-cyl systems use 5A ...., and then
>>> directly to the battery plus terminal, bypassing any electrical
>>> buss or master solenoid. Refer to the Input Connector Diagram &
>>> the Electrical Requirements section 2.7.
>>
>> This blazes a "new trail" in the woods. There are
>> no accessories offered to TC aviation where such
>> practice would be considered.
>
> Considering that this replaces a mag, does it really? The mag is
> connected directly without going through any bus or master solenoid.
> It's just that the mag packages everything in one neat container.
>
> I could be wrong.
Don't understand. The mag is not directly connected
to nor does it depend on battery power.
No, but abstracting out a bit. The mag is a integrated
|
generator/spark-maker. The Plasma is just a spark-maker.
We don't have total control of the mag. In fact, we're limited to
grounding the sparks that it makes. I'm not seeing much difference in
that and connecting the Plasma directly to the battery. In fact,
connecting it directly to the battery could be seen as sticking closer
to the previously blazed trail. If you view the Plasma as a part of the
engine that MUST work for the fan to keep turning, tying it directly to
the battery is making it more like a magneto, which keeps generating as
long as the engine is turning.
By using electronic ignition or injection, haven't we already moved far
enough off of the previously blazed trail that certain electronic
devices can't really be considered "accessories" anymore? I can fly
till the fuels all gone without a working radio or map light, but I'll
immediately become a glider if the ignition goes tits up (I added a
gravity fed fuel drip line, so I'll be able to maintain straight and
level if the fuel pumps and injectors get tired.) Powering the ignition
is now as important as keeping fuel in the tank. Everything isn't in a
neat package like it is with a mag, but I would think that it is
important to provide as clean a path as possible between an electron
source and the spark plug.
| - The Matronics AeroElectric-List Email Forum - | | Use the List Feature Navigator to browse the many List utilities available such as the Email Subscriptions page, Archive Search & Download, 7-Day Browse, Chat, FAQ, Photoshare, and much more:
http://www.matronics.com/Navigator?AeroElectric-List |
|
|
|
Back to top |
|
 |
nuckolls.bob(at)aeroelect Guest
|
Posted: Wed Feb 04, 2009 1:30 pm Post subject: Dual Plasma III and Z-13/8 |
|
|
Quote: | >
> Don't understand. The mag is not directly connected
> to nor does it depend on battery power.
|
Quote: | No, but abstracting out a bit. The mag is a integrated
generator/spark-maker. The Plasma is just a spark-maker.
We don't have total control of the mag. In fact, we're limited to
grounding the sparks that it makes. I'm not seeing much difference
in that and connecting the Plasma directly to the battery. In fact,
connecting it directly to the battery could be seen as sticking
closer to the previously blazed trail. If you view the Plasma as a
part of the engine that MUST work for the fan to keep turning, tying
it directly to the battery is making it more like a magneto, which
keeps generating as long as the engine is turning.
|
Hmmmm . . . Still not grasping your idea. The
Lightspeed instructions allude to an idea that
direct connection to the battery is a hedge against
"noise and spikes". When the busses are connected to
the battery by means of very fat wires, this idea
is flawed in terms of the physics.
Quote: | By using electronic ignition or injection, haven't we already moved
far enough off of the previously blazed trail that certain
electronic devices can't really be considered "accessories" anymore?
|
The the crowds I run around with, an "accessory"
or "appliance" is a purchased device with performance,
reliability and quality features that are the responsibility
of an outside supplier. Criticality of the device is
deduced by reliability and failure modes studies.
The outcome of those studies drive the system integrator's
duties to craft a Plan-B and the supplier's duties not
to allow the certified reliability numbers to degrade
in production.
Quote: | I can fly till the fuels all gone without a working radio or map
light, but I'll immediately become a glider if the ignition goes
tits up (I added a gravity fed fuel drip line, so I'll be able to
maintain straight and level if the fuel pumps and injectors get
tired.) Powering the ignition is now as important as keeping fuel
in the tank. Everything isn't in a neat package like it is with a
mag, but I would think that it is important to provide as clean a
path as possible between an electron source and the spark plug.
|
Absolutely. But the Lightspeed recommendation for
connection directly to the battery is no more
"reliable" as a power source than powering through
a protected feeder off the battery bus. Failure rates
on wires with properly assembled terminals is exceedingly
low. He didn't make this recommendation to improve on
probability of power being available, it was to
improve on quality of power . . . which is (1)in
error and (2) disregards the 160/704 dissertations
that explain exactly what an accessory/appliance
should be designed to EXPECT in terms of power
quality.
Bob . . .
| - The Matronics AeroElectric-List Email Forum - | | Use the List Feature Navigator to browse the many List utilities available such as the Email Subscriptions page, Archive Search & Download, 7-Day Browse, Chat, FAQ, Photoshare, and much more:
http://www.matronics.com/Navigator?AeroElectric-List |
|
|
|
Back to top |
|
 |
|
|
You cannot post new topics in this forum You cannot reply to topics in this forum You cannot edit your posts in this forum You cannot delete your posts in this forum You cannot vote in polls in this forum You cannot attach files in this forum You can download files in this forum
|
Powered by phpBB © 2001, 2005 phpBB Group
|