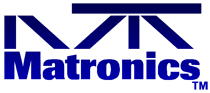 |
Matronics Email Lists Web Forum Interface to the Matronics Email Lists
|
View previous topic :: View next topic |
Author |
Message |
gordonrsmith921(at)yahoo. Guest
|
Posted: Sun Jun 28, 2009 12:41 pm Post subject: Internally Regulated Alternator Control |
|
|
I have followed posts to the list regarding internally regulated alternators and it appears to me that all are not the same regarding regulator functions and connections.
I am considering the use of an Eggenfellner E6.0 Subaru Auto conversion. The electrical system architecture will basically be Z-19.
The Egg is supplied with an internally regulated alternator and their installation manual shows the following:
ALTERNATOR CONNECTIONS - 4
1. B+ Lead Out – Large connection to Starter & Main Battery Contactor.
2. Fault – Goes to ground in case of alternator failure. For use of “idiot light”. I suppose this could be used as a low voltage warning but I would opt for an active and separate warning system that could also control my aux battery contactor.
3. Sense – This is a short jumper to the B+ output terminal; I assume for voltage info to the internal regulator. (I also assume that sense and enable connections could be jumpered together and fed from the panel alternator master switch through the 5A CB controlled by the OV module.)
4. Enable – Clip From manual below:
“5A Alternator Enable. To enable your alternator to produce charging current, this wire must be connected to a power source. This power source can be switched by the Master Switch or a subservient “Alternator” switch. People have come to know this function as an “alternator field”, however that is a term that has lingered on from years ago. It is actually just an enable signal going to a solid-state voltage regulator inside the alternator. It knows only ON or OFF, not specific voltages in between.
If you wish to have the ability to manually turn on and off the alternator, a switch should be provided. However, beware that turning an alternator on and off under heavy load can dramatically shorten the life of the alternator and cause substantial spikes and surges. If used, this switch should be left in the ON position, except when the alternator actually needs to be taken offline for some reason. For simplicity, this wire can simply be switched by the Master Switch or the Ignition Switch.”
End clip from manual.
I would take this to indicate that the alternator can be shut down using this enable circuit, by switching off the 12V+ that goes to it. And therefore the Z-24 (&/or Z-24A) circuitry including the Alternator OV Disconnect Contactor would not have to be used.
However, I believe that I have read on this list that these enable circuits will cause the alternator to power up when power is applied, but won’t necessarily shut the alternator down when power is removed.
Now I am confused. Is it possible/likely that the internally regulated alternator that Egg supplies will operate off and on through this “Enable” terminal; and all that one would need for OV protection (the manual does not say that the internal alternator regulator contains any circuitry for OV protection) is to add an OV module and 5A resettable CB in this circuit?
Gordon Smith
[quote][b]
| - The Matronics AeroElectric-List Email Forum - | | Use the List Feature Navigator to browse the many List utilities available such as the Email Subscriptions page, Archive Search & Download, 7-Day Browse, Chat, FAQ, Photoshare, and much more:
http://www.matronics.com/Navigator?AeroElectric-List |
|
|
|
Back to top |
|
 |
nuckolls.bob(at)aeroelect Guest
|
Posted: Sun Jun 28, 2009 3:40 pm Post subject: Internally Regulated Alternator Control |
|
|
At 03:28 PM 6/28/2009, you wrote:
I have followed posts to the list regarding
internally regulated alternators and it appears
to me that all are not the same regarding regulator functions and connections.
I am considering the use of an Eggenfellner E6.0
Subaru Auto conversion. The electrical system
architecture will basically be Z-19.
The Egg is supplied with an internally regulated
alternator and their installation manual shows the following:
ALTERNATOR CONNECTIONS - 4
1. B+ Lead Out � Large connection to Starter & Main Battery Contactor.
Yes . . .
2. Fault � Goes to ground in case of
alternator failure. For use of �idiot light�. I
suppose this could be used as a low voltage
warning but I would opt for an active and
separate warning system that could also control my aux battery contactor.
This was discussed earlier this week. The built-in
alternator failure light does not comport with
legacy design goals for separate and independent
monitoring and warning of low voltage.
The AEC9005 is discontinued but Eric Jones has
a clone. We'll have a new replacement in the form
of the AEC9011 later this year. Either approach
will satisfy the legacy design goals for low voltage
monitor and control.
3. Sense � This is a short jumper to the B+
output terminal; I assume for voltage info to the
internal regulator. (I also assume that sense
and enable connections could be jumpered together
and fed from the panel alternator master switch
through the 5A CB controlled by the OV module.)
Don't know. Does the alternator have a brand and
part number on it?
4. Enable � Clip From manual below:
�5A Alternator Enable. To enable your alternator
to produce charging current, this wire must be
connected to a power source. This power source
can be switched by the Master Switch or a
subservient �Alternator� switch. People have come
to know this function as an �alternator field�,
however that is a term that has lingered on from
years ago. It is actually just an enable signal
going to a solid-state voltage regulator inside
the alternator. It knows only ON or OFF, not specific voltages in between.
This is characteristic of ALL internally regulated
alternators. I.e. there are no stock provisions
for absolute control over the field supply source.
This is why both B&C and Plane Power opt for their
own modifications of stock alternators to provide
this functionality.
If you wish to have the ability to manually turn
on and off the alternator, a switch should be
provided. However, beware that turning an
alternator on and off under heavy load can
dramatically shorten the life of the alternator
and cause substantial spikes and surges. If
used, this switch should be left in the ON
position, except when the alternator actually
needs to be taken off line for some reason. For
simplicity, this wire can simply be switched by
the Master Switch or the Ignition Switch.�
Almost . . . Under the legacy design goals for
alternator control, turning the field supply line
on and off while a battery is on line offers no
particular risk to the alternator or the ship's
electro-whizzies.
Further, it's a design goal of any quality supplier
of alternators that their product be able to withstand
b-lead disconnects (load dumps) under hot, full load, high
rpm conditions. So adding Z-24 style OV protection
to the internally regulated alternator presents
no operational hazard for two reasons . . .
(1) there is no normal operating condition where
turning an alternator OFF under heavy load using
Z-24 is called for . . . but a quality alternator
would not be at risk anyhow.
(2) Z-24 style protection can be depended upon
to do it's intended job should the admittedly
rare OV event occur.
I would take this to indicate that the alternator
can be shut down using this enable circuit, by
switching off the 12V+ that goes to it. And
therefore the Z-24 (&/or Z-24A) circuitry
including the Alternator OV Disconnect Contactor would not have to be used.
Assuming the electronics of the internal
regulator is functioning as designed, then
external control by means of the little wire
at the back is possible and predictable. But
if the electronics fails (which is the definition
of an OV event) then all bets are off.
Legacy design goals call for separate and
independent control over the alternator during
an OV event . . . this is what drove the
design philosophy for Z-24.
Alternatively, you can modify your alternator
to adopt the control philosophy adopted by
Plane Power.
However, I believe that I have read on this list
that these enable circuits will cause the
alternator to power up when power is applied, but
wont necessarily shut the alternator down when power is removed.
As far as anyone KNOWS, the control lead will always
exert any time, ON/OFF control . . . as long as the
internal electronics are intact. Further, exercising
this control at any time under any conditions is
not a risky thing to do as long as the battery
is on line. This design goal is satisfied when you utilize
the progressive transfer DC PWR MASTER switch
architecture described in the Z-figures.
Now I am confused. Is it possible/likely that
the internally regulated alternator that Egg
supplies will operate off and on through this
�Enable� terminal; and all that one would need
for OV protection (the manual does not say that
the internal alternator regulator contains any
circuitry for OV protection) is to add an OV
module and 5A resettable CB in this circuit?
If it were my airplane, I would add OV protection
in the form of either Plane Power style modification
or Z-24 interim to be replaced by the Z-24 final solution
at a later time.
Bob . . .
| - The Matronics AeroElectric-List Email Forum - | | Use the List Feature Navigator to browse the many List utilities available such as the Email Subscriptions page, Archive Search & Download, 7-Day Browse, Chat, FAQ, Photoshare, and much more:
http://www.matronics.com/Navigator?AeroElectric-List |
|
|
|
Back to top |
|
 |
|
|
You cannot post new topics in this forum You cannot reply to topics in this forum You cannot edit your posts in this forum You cannot delete your posts in this forum You cannot vote in polls in this forum You cannot attach files in this forum You can download files in this forum
|
Powered by phpBB © 2001, 2005 phpBB Group
|