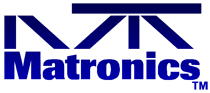 |
Matronics Email Lists Web Forum Interface to the Matronics Email Lists
|
View previous topic :: View next topic |
Author |
Message |
teamgrumman(at)yahoo.com Guest
|
Posted: Sat Nov 19, 2011 10:16 am Post subject: Flying with a level |
|
|
HS= horizontal stabilizer
From what I've been able to determine,
1. the wing is at 3 to 3.5 degrees up with respect to the fuselage.
• the wing needs some lift with the fuselage at 0 degrees angle-of-attack (AOA).
• as speed increases, lift increases on both the fuselage and wing. trim nose down.
2. the horizontal stabilizer is at 0 degrees with respect to the fuselage.
• this is necessary for elevator response during landing angle-of-attack; this is a compromise.
3. minimum drag AOA varies with depending on fuel load, passenger loading, baggage compartment loading
• the ideal situation would be a battery mounted in the aft fuselage on a slide so that it can be moved fore-aft to maintain minimum drag.
4. minimum drag AOA of the fuselage by itself is immaterial. The aircraft acts as a system.
5. zero lift AOA of the wings, by themselves, is immaterial. The aircraft acts as a system.
6. zero lift of the entire system depends GREATLY on the airspeed.
• as with 'Galloping Ghost,' you will need to trim more nose down as speed goes above the design speed of 120 knots.
- Note: I say design speed based on what I've measured and calculated. I do not know what speed, if any, the plane was designed.
6. I'm not convinced that minimum drag occurs when the elevator is in trail with the horizontal stabilizer.
7. Looking for max speed in my Cheetah, N9988U, I tried a lot of things. Full fuel, no passengers.
• I setup all of the control surfaces, flaps, and trim, as close as possible to zero degrees with respect to their parent surface
(I removed the aileron trim and rudder trim)
- this did not make the plane as fast as I eventually got it
• I set up the ailerons at +2 to +4 degrees up in straight and level.
- this did not make the plane as fast as I eventually got it
• I set the flaps as high as +7 degrees up in straight and level
- this did not make the plane as fast as I eventually got it
• I set up the elevator trim at various setting with respect to the horizontal stabilizer.
- any setting away from the stock setting had negligible effects at speeds between 135 and 140 knots.
8. it was at this point that I started looking at the individual systems as a complete system.
• it was also at this point that I began looking at other parts of the plane to reduce drag.
From: "n76lima(at)mindspring.com" <n76lima(at)mindspring.com>
To: 923TE(at)att.net; bob.hodo(at)yahoo.com; teamgrumman(at)yahoo.com
Sent: Saturday, November 19, 2011 5:46 AM
Subject: Flying with a level
Ned brings up an interesting point. Flying with a level on or coordinated with the canopy rails, such that one knows when the waterlines of the plane are lined up with the actual "level" per the Earth's gravity might be significant.
What we don't know is what is the lowest drag attitude of the fuselage, since it isn't a symmetrical shape, and what is the zero lift angle of the wings, since our airfoil has no NACA data and has never been blown on in the increasingly non-existent wind tunnels of this digital age.
That means that flying with the canopy rails "level", and the elevator tips even with the HS, can only be assumed to be the ideal from a drag reduction standpoint.
Maynard's assertion that the HS incidence is "0" seems odd, in that we know that the tail must provide down force to counter the wing's nose down pitching moment. If set at Zero incidence, a symmetrical airfoil is going to provide NO lift (up or down). If we can see that the elevator tips are in alignment with the HS in flight, we can also approximate the trim tab location by centering the elevator, rolling the trim to the point that the trim tabs are streamlined, and then marking the console to show the trim zero point.
The above should be considered in the context of the "zero" incidence is perhaps measured relative to the FUSELAGE, which is not what matters. It is the incidence relative to the WING, which is a measurement that I've never seen discussed. Somewhere in the deep dark recesses of FletchAir and now TrueFlight, there must be a drawing that shows the incidence of the WING relative to the fuselage, and then one can extrapolate the relative incidence of the HS to the wing. I submit that there is some difference in the angle of the wing and the tail. ie: If the wing is rolled nose down to "zero" relative to level with respect to the Earth, the fuselage is going to be pointing slightly nose down, so the elevator will have a leading edge down tilt with respect to the wing. This is the "incidence" that matters, because the wing is the part generating the force that the tail is trying to offset.
The tendency for the Grumman derived airfoil to "tuck" nose down as the plane flies faster gets to the point that the airflow is now striking the tail at lower and lower angle of attack (with the caveat that we know that the tail is "flying upside down"), so the perceived angle of attack by the HS is increasing, and at some point the elevators are reflexed trailing edge DOWN. This is why Grummans have such great visibility forward in cruise, because unlike Cessna, Piper, Beech, the nose rotates down, making the cowl disappear and the view forward becomes unobstructed.
Sadly, we have what is essentially the Hortol STOL kit on our planes, which drops the zero lift line of the wing to an even greater negative angle of attack, meaning that the fuselage has to rotate further nose down on an AA-1A/B/C and AA-5x than it does on the AA-1 Yankee as the speed increases. Might this indicate that the WING is set on the fuselage at the wrong angle of incidence relative to the angle of the least drag for the fuselage body's airflow? We may never know, without means to blow on the fuselage shape at different angles of attack.
Ned, perhaps you need the BD-8 style mod, where you can adjust the halves of the HS independently. <G> In case you didn't know, the BD-8 was Jim's idea for a serious aerobatic competitor, and it had a split elevator that would be set in opposition to increase the rolling on the vertical line.
http://www.sportaviationspecialties.com/BD8.htm
There truly is nothing new under the sun.
--Bob Steward
Occasional Crew Chief to One Pretty Quick Cheetah
[quote][b]
| - The Matronics TeamGrumman-List Email Forum - | | Use the List Feature Navigator to browse the many List utilities available such as the Email Subscriptions page, Archive Search & Download, 7-Day Browse, Chat, FAQ, Photoshare, and much more:
http://www.matronics.com/Navigator?TeamGrumman-List |
|
|
|
Back to top |
|
 |
teamgrumman(at)yahoo.com Guest
|
Posted: Sun Nov 20, 2011 7:06 pm Post subject: Flying with a level |
|
|
Oh, sorry Bob, I misunderstood the objective.
When I was a young engineer, I used to go to my supervisor with all of these ideas I had for projects that we'd likely never work on or problems that may or may not occur and I'd say, "Jay, what if . . . . " Then, he'd tell me to go solve a real problem. I always had lots of ideas that I thought would be interesting to try. He called it mental masturbation. He'd say, "At least you feel like you're accomplishing something whether or not you actually do."
OK, so, now I know the objective. Any ideas on where to start?
--------------- Ned writes . . . ----------------------------
Gary said "There isn't anything you can do now except to optimize what you have"
Gary, surely you jest???
of all people I would 've thought you'd be the last to say something like that....considering all the stuff you yourself does and have developedand are developing that ain't "already built"
Ned....he he he
---------------------------------------------------------------
Good point, Ned.
When I wrote that, I thinking in terms of "there isn't anything you can do now with respect to determining fuselage minimum drag independent of wing drag, the wings lift/drag independent of the fuselage or changing the wing or horizontal incidence (angle of attack) or related systems, wing length, wing shape, etc."
What I had in mind was optimizing things like wheel pants, wing tips, antennas, engine, prop, ways to get the weight down . . . you get the idea.
========
Bob,
A while back I read an article about a guy with a Luscombe who put a micro-switch, attached to the block, so that it touched the back side of his prop. When the engine was producing thrust, the crank pulled forward in its journals. At zero thrust, the prop would back off. He was able determine the lift/drag of his Luscombe and developed his own curves for parasitic drag and induced drag.
Admittedly, he treated the Luscombe as a system. But, it might be a start. His goal was to find minimum drag to optimize his range.
Sorry again Bob, there was nothing after #8. I can't give away all of my secrets.
===========
Radical Race plane ideas: (these ideas are independent of one another. A classic example of mental masturbation)
1. Move the pilot, instruments, controls and everything, back to the back seat; about 2 feet.
2. Use a canopy from an AA1, cut the aft fuselage down to fit the canopy. Install AA1 seats.
3. Install a battery in the back, aft of the baggage compartment, on a slide to move the CG back as far as possible during flight. Return it for landing.
4. Max range:
a. Install fuel tanks in the foot wells in the back.
b. Make the wing tanks occupy all three bays in the inboard wing panel.
c. 30 gals of fuel in the baggage compartment
d. I forget the rest. At one point, I think I had max fuel load at 120 gallons.
5. Lower the engine 3 inches. Design a cowling that was more symmetric in side profile.
- This would lower the high pressure area ahead of the windshield
6. Carb/fuel injector intake ahead of the windshield. Duct it down the inside of the plane though an intercooler to drop the temp.
- duct through the firewall to the carb/fuel injector. Takes advantage of the high pressure area.
7. Design a cowling with the back of the cowling 6 to 10 inches higher in back with a shape that blends with the windshield.
- Again, move the high pressure area away from the windshield.
Those are just a few ideas. I have more.
Gary
From: Bob Steward <n76lima(at)mindspring.com>
To: Gary Vogt <teamgrumman(at)yahoo.com>
Sent: Sunday, November 20, 2011 11:02 AM
Subject: Re: Flying with a level
Gary, I (we?) am looking at this as a thought exercise, attempting to gain information and understanding, not a laundry list of proposed mods for immediate implementation on Ned's plane.
Bouncing these ideas off other knowledgeable Grumman enthusiasts is helpful, and I'd hope you'd participate with the same goal, of greater understanding and some input about things that might not have been considered before.
--Bob Steward
Sent from Samsung mobile
[quote][b]
| - The Matronics TeamGrumman-List Email Forum - | | Use the List Feature Navigator to browse the many List utilities available such as the Email Subscriptions page, Archive Search & Download, 7-Day Browse, Chat, FAQ, Photoshare, and much more:
http://www.matronics.com/Navigator?TeamGrumman-List |
|
|
|
Back to top |
|
 |
teamgrumman(at)yahoo.com Guest
|
Posted: Mon Nov 21, 2011 7:17 pm Post subject: Flying with a level |
|
|
One of the Tigers I maintain has one wing that is off by about a degree. It's tough to determine a degree using a laser at 30 feet, but I think one wing is off a bit. I read the manual about changing the incidence angle and it seems to me that without jigs, it would be a real MoFo.
I thought about the microswitch thing many years ago when I first read it. If anything, it determines the drag vs thrust at various speeds.
Bob, it's too bad you aren't closer. If you have enough spare parts, I'd be willing to investigate optimizing the wing/horizontal angles. I'd love to build a 1200 lb Tiger with 75 gallons of fuel.
We know that the minimum drag configuration of the wing is at zero degrees. So, if the fuselage tucks a couple of degrees as speed increases, that tells me that as the lift of the wing increases, it needs less lift and is naturally finding minimum total minimum drag; i.e., max L/D.
The drag on the fuselage could be modeled in a water tunnel. I would pick something near 1/5 scale minimum. Something in the 40 to 50 inch range. That would be something very interesting to model.
Trim drag amounts to less than 5% total drag on the plane. I'd be looking for big effects first. I think better wing tips would save that much.
Gary
From: "n76lima(at)mindspring.com" <n76lima(at)mindspring.com>
To: Gary Vogt <teamgrumman(at)yahoo.com>
Cc: 923te(at)att.net; bob.hodo(at)yahoo.com
Sent: Sunday, November 20, 2011 9:54 PM
Subject: Re: Flying with a level
>When I was a young engineer, I used to go to my supervisor with all of these ideas I had for projects >that we'd likely never work on or problems that may or may not occur and I'd say, "Jay, what if . . . ." >Then, he'd tell me to go solve a real problem. I always had lots of ideas that I thought would be >interesting to try. He called it mental masturbation. He'd say, "At least you feel like you're >accomplishing something whether or not you actually do."
Quote: | OK, so, now I know the objective. Any ideas on where to start?
|
I'd rather consider it an exercise in being open-minded about the possibilities, but I have collected up nearly all the parts needed to build an amateur-built "replica Tiger", from a handful of salvage planes, like you suggested you'd like -- AKA the Tiger "kit", so they aren't necessarily ideas that are never going to be put into practice.
In speaking with Roy LoPresti back in the 90's he remarked that he felt there was another 10-15 mph left on the table by Grumman when he did his Traveler conversion to the Tiger. But Grumman declined to fund additional research after he beat all the 200 HP retracts by at least 1 mph, so they had the advertising edge they wanted.
I'd like to explore where those theoretical knots are hiding and see what could be done to exploit some of them. Kevin Lancaster and I had a discussion recently when he visited my shop. I know his #1 priority has to be getting the Tiger LLC version of the AG-5B back on-line, but we talked about some potential mods for the future, IF there is a future for new planes in GA.
I learned from this recent exchange with you, Ned and Bob H. that you think the wing is set at ~3-3.5 degrees incidence relative to the fuselage waterlines, and from Ned and Bob H. that the fuselage DOES tuck nose down as the speed increases, something approaching 2 degrees as the speed exceeds 150 knots.
This is good information, and pushes my thought experiment further down the line, to asking "what if" the wing incidence could be altered. Each degree of incidence at the spar is less than 1/16" of hole movement, so doing the approved "repair" of the center section and wing spar tube of reaming over-size and putting bushings in, could be used to move the center section hole one way and the wing spar tube hole the other, and with 7/16" holes, the incidence could be lowered just over 2 degrees. Given Ned and Bob H.'s numbers, this would set the fuselage to be more aligned with the flow at 150 knots and above.
How much drag would this save? Don't know. I pinged Maynard about incidence and got a response I have not shared. But it is my understanding that the change in tail incidence he used to espouse was done by several (Mean Gene included) and that they saw very measurable gains. Yes the Tiger tail is bigger, and possibly the gains are not the same. I was wanting to get a consensus of what knowledgeable Grumman modifiers thought about such things, and hoped that someone might pipe up and say "we did that one time and it didn't do any good", or other comments that would either encourage the prospect of testing for an improvement, or anecdotal evidence that ideas being discussed were aerodynamic dead ends.
And changing the FUSELAGE incidence with respect to the wing would change things even more than Maynard's tail incidence adjustment that left the fuselage tilting nose down at high cruise. He was focused on the tail trim issues at high speeds where less and less down force was needed and the aerodynamic forces rise significantly at "high Q".
I rather imagine that there is little chance that many of these ideas will be tried, because as you point out, they are certified planes, and we are talking about things that would seem to be firmly in the Experimental R&D area, for which we probably don't have the budget. But if those parts sitting on the shelf to find themselves mixed with some new aluminum sheet, I'd want to have all the good ideas in one place, since the process of building ANY homebuilt is a multi-year commitment, and one doesn't want to have to go back and re-make things.
Thanks for your time.
--Bob Steward
[quote][b]
| - The Matronics TeamGrumman-List Email Forum - | | Use the List Feature Navigator to browse the many List utilities available such as the Email Subscriptions page, Archive Search & Download, 7-Day Browse, Chat, FAQ, Photoshare, and much more:
http://www.matronics.com/Navigator?TeamGrumman-List |
|
|
|
Back to top |
|
 |
|
|
You cannot post new topics in this forum You cannot reply to topics in this forum You cannot edit your posts in this forum You cannot delete your posts in this forum You cannot vote in polls in this forum You cannot attach files in this forum You can download files in this forum
|
Powered by phpBB © 2001, 2005 phpBB Group
|