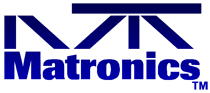 |
Matronics Email Lists Web Forum Interface to the Matronics Email Lists
|
View previous topic :: View next topic |
Author |
Message |
grahamsingleton(at)btinte Guest
|
Posted: Sat Jun 09, 2012 2:49 am Post subject: Contact detail & Help |
|
|
Ken
the two people I know who've done most research on the cooling of Europas, with some success, are
PaulMcAllister <paul.the.aviator(at)gmail.com>; FransVeldman <frans(at)privatepilots.nl>;
Both have the XS installation, not Classic.
Link to the forum is <europa-list(at)matronics.com>;
Graham
From: "ken(at)ardenrich.co.uk" <ken(at)ardenrich.co.uk>
To: GRAHAM SINGLETON <grahamsingleton(at)btinternet.com>
Sent: Saturday, 9 June 2012, 10:01
Subject: Contact detail & Help
Graham,
The Canadian contact details;
seth.g.london(at)ca.pwc.com (seth.g.london(at)ca.pwc.com)
Have you any chapter on verse or can could point me in the right direction where to look for the best on a/c engine cooling-cowl design principles.
Also if poss could you send me the link over to get back on to the Europa Forum please
All would be much appreciated,
Ken
[quote][b]
| - The Matronics Europa-List Email Forum - | | Use the List Feature Navigator to browse the many List utilities available such as the Email Subscriptions page, Archive Search & Download, 7-Day Browse, Chat, FAQ, Photoshare, and much more:
http://www.matronics.com/Navigator?Europa-List |
|
|
|
Back to top |
|
 |
budyerly(at)msn.com Guest
|
Posted: Sat Jun 09, 2012 8:22 pm Post subject: Contact detail & Help |
|
|
<?xml:namespace prefix="v" /><?xml:namespace prefix="o" /><![endif]--> Ken and Graham,
I've attached my modifications and techniques briefing used for Europa Cooling with the XS cowl which written up in the Europa Flyer .
If I do say so myself, I never have cooling issues in Florida at 95 degree summer days using 50/50 Anitifreeze. Judging by the calls and email success stories, these simple techniques work pretty much world wide.
References for further study are at the end of the document.
Those who have followed these techniques with a stock cowl have no problems cooling especially with the trigear. In fact it gets a bit too cool in cooler climates and this is with no modifications to the existing cowl, only treating the airflow around the coolers.
I have worked these issues over the last six years and we just finished three more aircraft at the shop, all Rotax and we reworked a clients Jab 3300, and all the Rotax's have no cooling issues and the Jab is tolerable except taxi times must be short, 10 or 15 minutes max or it gets a bit too hot for a takeoff on a summer day.
I'll do another briefing/article on the Jabiru before long.
Call or email me at the office in Florida below if you have need of more specifics or are having problems getting the references on line.
Regards,
Bud Yerly
Europa Tech Support
US Europa Dealer
Custom Flight Creations, Inc.
www.customflightcreations.com
(813) 653-4989
[quote] ---
| - The Matronics Europa-List Email Forum - | | Use the List Feature Navigator to browse the many List utilities available such as the Email Subscriptions page, Archive Search & Download, 7-Day Browse, Chat, FAQ, Photoshare, and much more:
http://www.matronics.com/Navigator?Europa-List |
|
Description: |
|
 Download |
Filename: |
Aircraft_Cooling_101_for_Tractor_Engine_Installation2.pdf |
Filesize: |
1.48 MB |
Downloaded: |
1782 Time(s) |
|
|
Back to top |
|
 |
carlmeek(at)gmail.com Guest
|
Posted: Sun Jun 10, 2012 12:49 am Post subject: Contact detail & Help |
|
|
Hi Bud,
I would love to hear what you have to say on the Jabiru, my engineer is about to start modifications to the cowl, cylinder baffles, etc – our goal is to try and improve CHT temperatures. While we're at it, I'd also like to try and lean the engine and get some better economy, mine is a guzzler.
I've already chatted with various people, including Doug at Jabiru, and I personally feel that my own aircraft's solutions are (a) sealing off oil cooler to prevent airflow entering the lower cowl and (b) putting a lip on the front of the cowl exit in order to help with the exit of air entering the main 2 holes by the prop. However my engineer (who is a fluid dynamics expert) disagrees with this approach and doesn't feel it will work - I need to get more information from him on why. In photographs of my aircraft in the flare, a similar attitude to a climb, you can see how forward airflow enters the bottom of the cowl, so to me it looks a no-brainer that we need a lip.
Regards,
-Carl.
From: Bud Yerly <budyerly(at)msn.com (budyerly(at)msn.com)>
Reply-To: <europa-list(at)matronics.com (europa-list(at)matronics.com)>
Date: Sun, 10 Jun 2012 00:21:08 -0400
To: <europa-list(at)matronics.com (europa-list(at)matronics.com)>, <ken(at)ardenrich.co.uk (ken(at)ardenrich.co.uk)>
Subject: Re: Re: Contact detail & Help
<?xml:namespace prefix="v" /><?xml:namespace prefix="o" /><![endif]-->Ken and Graham,
I've attached my modifications and techniques briefing used for Europa Cooling with the XS cowl which written up in the Europa Flyer .
If I do say so myself, I never have cooling issues in Florida at 95 degree summer days using 50/50 Anitifreeze. Judging by the calls and email success stories, these simple techniques work pretty much world wide.
References for further study are at the end of the document.
Those who have followed these techniques with a stock cowl have no problems cooling especially with the trigear. In fact it gets a bit too cool in cooler climates and this is with no modifications to the existing cowl, only treating the airflow around the coolers.
I have worked these issues over the last six years and we just finished three more aircraft at the shop, all Rotax and we reworked a clients Jab 3300, and all the Rotax's have no cooling issues and the Jab is tolerable except taxi times must be short, 10 or 15 minutes max or it gets a bit too hot for a takeoff on a summer day.
I'll do another briefing/article on the Jabiru before long.
Call or email me at the office in Florida below if you have need of more specifics or are having problems getting the references on line.
Regards,
Bud Yerly
Europa Tech Support
US Europa Dealer
Custom Flight Creations, Inc.
www.customflightcreations.com
(813) 653-4989
[quote] ---
| - The Matronics Europa-List Email Forum - | | Use the List Feature Navigator to browse the many List utilities available such as the Email Subscriptions page, Archive Search & Download, 7-Day Browse, Chat, FAQ, Photoshare, and much more:
http://www.matronics.com/Navigator?Europa-List |
|
|
|
Back to top |
|
 |
grahamsingleton(at)btinte Guest
|
Posted: Sun Jun 10, 2012 1:25 am Post subject: Contact detail & Help |
|
|
Bud
apologies for forgetting to mention you! Careless, or a bit senile perhaps {{
The thing I like about Frans' and Paul's work is the attempt to reduce cooling drag.
regards
Graham
From: Bud Yerly <budyerly(at)msn.com>
To: europa-list(at)matronics.com; ken(at)ardenrich.co.uk
Sent: Sunday, 10 June 2012, 5:21
Subject: Re: Re: Contact detail & Help
Ken and Graham,
I've attached my modifications and techniques briefing used for Europa Cooling with the XS cowl which written up in the Europa Flyer .
If I do say so myself, I never have cooling issues in Florida at 95 degree summer days using 50/50 Anitifreeze. Judging by the calls and email success stories, these simple techniques work pretty much world wide.
References for further study are at the end of the document.
Those who have followed these techniques with a stock cowl have no problems cooling especially with the trigear. In fact it gets a bit too cool in cooler climates and this is with no modifications to the existing cowl, only treating the airflow around the coolers.
I have worked these issues over the last six years and we just finished three more aircraft at the shop, all Rotax and we reworked a clients Jab 3300, and all the Rotax's have no cooling issues and the Jab is tolerable except taxi times must be short, 10 or 15 minutes max or it gets a bit too hot for a takeoff on a summer day.
I'll do another briefing/article on the Jabiru before long.
Call or email me at the office in Florida below if you have need of more specifics or are having problems getting the references on line.
Regards,
Bud Yerly
Europa Tech Support
US Europa Dealer
Custom Flight Creations, Inc.
www.customflightcreations.com
(813) 653-4989
[quote] ---
| - The Matronics Europa-List Email Forum - | | Use the List Feature Navigator to browse the many List utilities available such as the Email Subscriptions page, Archive Search & Download, 7-Day Browse, Chat, FAQ, Photoshare, and much more:
http://www.matronics.com/Navigator?Europa-List |
|
|
|
Back to top |
|
 |
grahamsingleton(at)btinte Guest
|
Posted: Sun Jun 10, 2012 3:43 am Post subject: Contact detail & Help |
|
|
Bud
your explanation of the problems is excellent. I haven't done much work with Europas for years but I have
been working on my Long EZ. I can confirm that exhaust extraction is very effective. I can run full throttle
static on the ground for up to ten minutes on a warm English day.
Do you know Steve Volovsek? I think he is based in Florida, his Long is the one I copied, we have the same
Lycoming engine and his cooling air inlets are quite small. No slipstream either when static! Have a look at the attached photos.
It's worth noting that the cross sectional area of the gaps between the cooling fins is pretty small, the important thing is recovering enough pressure
from the inlet ambient (total energy) pressure to force the air through them. Worth looking at for the Jab.
The center inlet btw is to the throttle body. Total cooling air inlet is less than 30 square inches for a 160 bhp air cooled engine.
One thing to note, it's important not to have hot air flowing down the side of the fuselage, it needs mixing with cooler air.
regards
Graham
From: Bud Yerly <budyerly(at)msn.com>
To: europa-list(at)matronics.com; ken(at)ardenrich.co.uk
Sent: Sunday, 10 June 2012, 5:21
Subject: Re: Re: Contact detail & Help
I have worked these issues over the last six years and we just finished three more aircraft at the shop, all Rotax and we reworked a clients Jab 3300, and all the Rotax's have no cooling issues and the Jab is tolerable except taxi times must be short, 10 or 15 minutes max or it gets a bit too hot for a takeoff on a summer day.
I'll do another briefing/article on the Jabiru before long.
Regards, Bud Yerly
| - The Matronics Europa-List Email Forum - | | Use the List Feature Navigator to browse the many List utilities available such as the Email Subscriptions page, Archive Search & Download, 7-Day Browse, Chat, FAQ, Photoshare, and much more:
http://www.matronics.com/Navigator?Europa-List |
|
Description: |
|
Filesize: |
810.74 KB |
Viewed: |
9366 Time(s) |
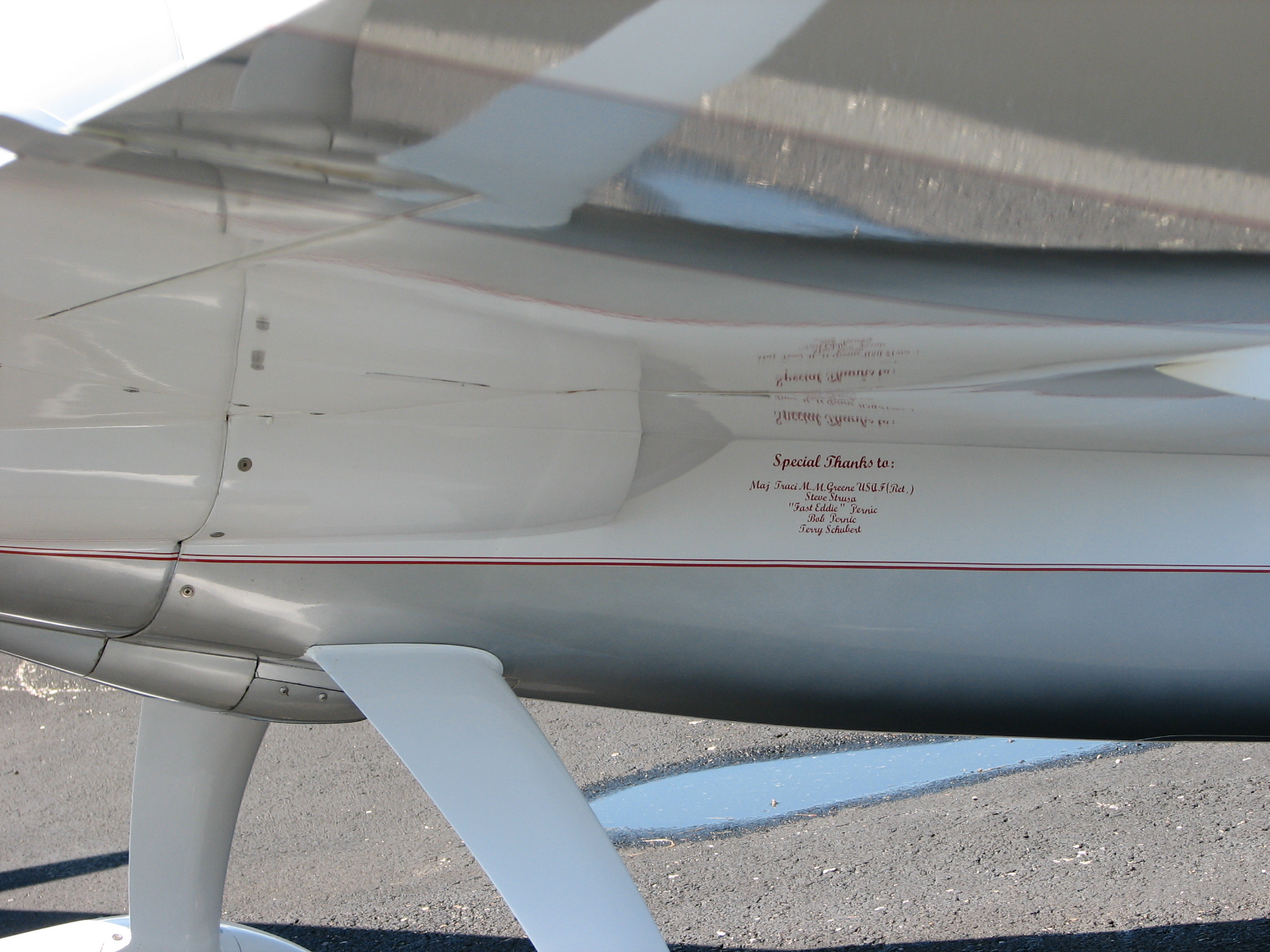
|
Description: |
|
Filesize: |
142.54 KB |
Viewed: |
9366 Time(s) |
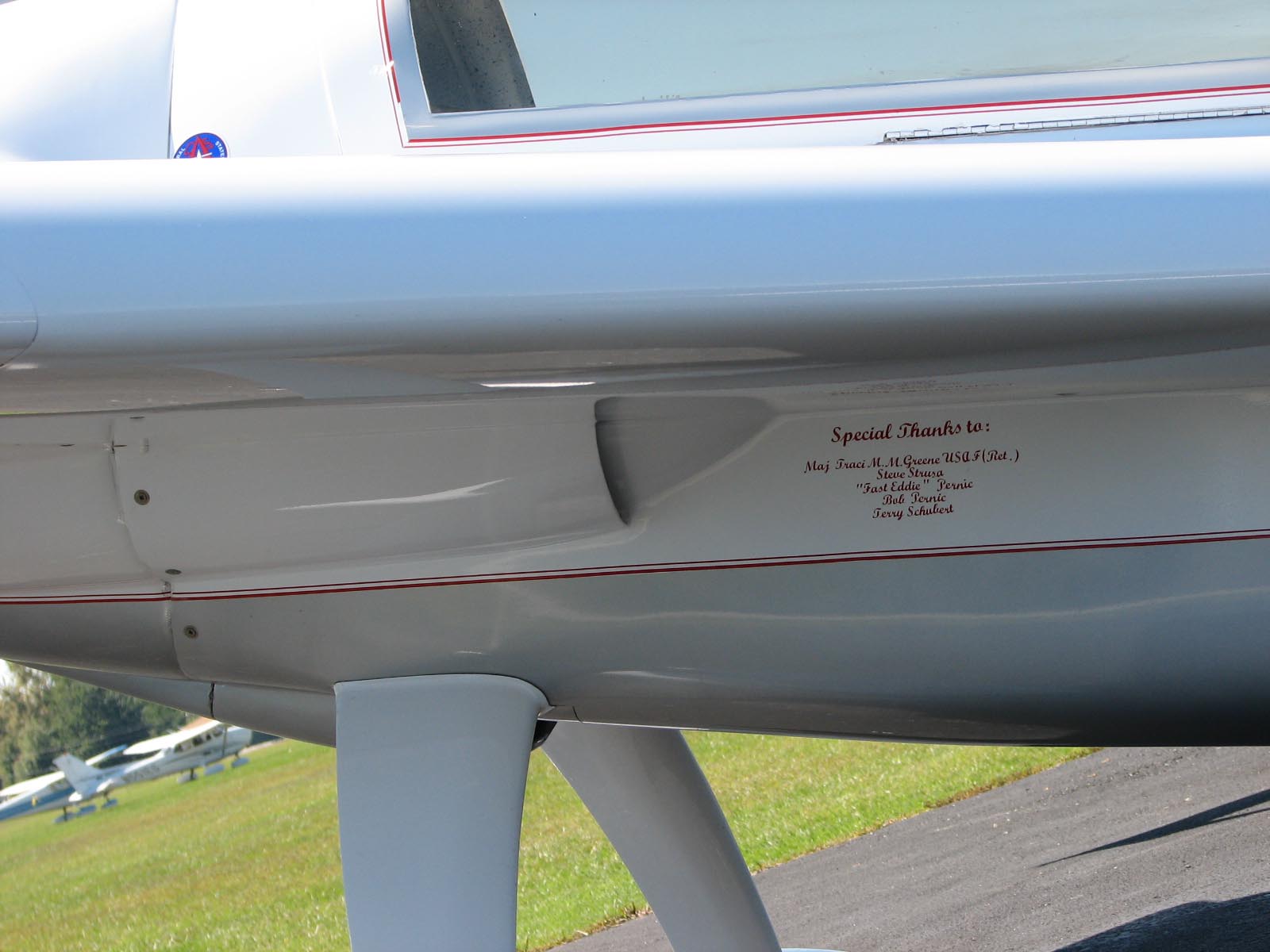
|
|
|
Back to top |
|
 |
nigel_graham(at)m-tecque. Guest
|
Posted: Tue Jun 12, 2012 4:04 am Post subject: Contact detail & Help |
|
|
Bud,
A fascinating article - thanks. It would seem that I have spent the last God knows how many years researching the same data as you (mostly 1940's and 50's NACA papers) and come up with much the same conclusions regarding cooling and cooling drag reduction. By a curious coincidence, I have been busy this weekend buried in my workshop - laminating. Compare the results, hot-out-of-the-mould, with the computer generated cowl design on page 16 of your report. My design concepts would all appear to have come out of your "Lets's get radical" section!
Keep up the good work.
Nigel
On 10/06/2012 05:21, Bud Yerly wrote: Quote: | <?xml:namespace prefix="v" /><?xml:namespace prefix="o" /><![endif]--> Ken and Graham,
I've attached my modifications and techniques briefing used for Europa Cooling with the XS cowl which written up in the Europa Flyer .
If I do say so myself, I never have cooling issues in Florida at 95 degree summer days using 50/50 Anitifreeze. Judging by the calls and email success stories, these simple techniques work pretty much world wide.
References for further study are at the end of the document.
Those who have followed these techniques with a stock cowl have no problems cooling especially with the trigear. In fact it gets a bit too cool in cooler climates and this is with no modifications to the existing cowl, only treating the airflow around the coolers.
I have worked these issues over the last six years and we just finished three more aircraft at the shop, all Rotax and we reworked a clients Jab 3300, and all the Rotax's have no cooling issues and the Jab is tolerable except taxi times must be short, 10 or 15 minutes max or it gets a bit too hot for a takeoff on a summer day.
I'll do another briefing/article on the Jabiru before long.
Call or email me at the office in Florida below if you have need of more specifics or are having problems getting the references on line.
Regards,
Bud Yerly
Europa Tech Support
US Europa Dealer
Custom Flight Creations, Inc.
www.customflightcreations.com
(813) 653-4989
|
| - The Matronics Europa-List Email Forum - | | Use the List Feature Navigator to browse the many List utilities available such as the Email Subscriptions page, Archive Search & Download, 7-Day Browse, Chat, FAQ, Photoshare, and much more:
http://www.matronics.com/Navigator?Europa-List |
|
Description: |
|
 Download |
Filename: |
120610_-_Cowl.pdf |
Filesize: |
1.01 MB |
Downloaded: |
580 Time(s) |
|
|
Back to top |
|
 |
klinefelter.kevin(at)gmai Guest
|
Posted: Tue Jun 12, 2012 4:48 am Post subject: Contact detail & Help |
|
|
Nigel,
Oh my, what a beautiful work of art. I hope you will keep us informed of results regarding the boy with nose job!
Kevin
Do not archive
On Jun 12, 2012, at 5:02 AM, "nigel_graham(at)m-tecque.co.uk (nigel_graham(at)m-tecque.co.uk)" <nigel_graham(at)m-tecque.co.uk (nigel_graham(at)m-tecque.co.uk)> wrote:
[quote] Bud,
A fascinating article - thanks. It would seem that I have spent the last God knows how many years researching the same data as you (mostly 1940's and 50's NACA papers) and come up with much the same conclusions regarding cooling and cooling drag reduction. By a curious coincidence, I have been busy this weekend buried in my workshop - laminating. Compare the results, hot-out-of-the-mould, with the computer generated cowl design on page 16 of your report. My design concepts would all appear to have come out of your "Lets's get radical" section!
Keep up the good work.
Nigel
On 10/06/2012 05:21, Bud Yerly wrote: Quote: | <?xml:namespace prefix="v" /><?xml:namespace prefix="o" /><![endif]--> Ken and Graham,
I've attached my modifications and techniques briefing used for Europa Cooling with the XS cowl which written up in the Europa Flyer .
If I do say so myself, I never have cooling issues in Florida at 95 degree summer days using 50/50 Anitifreeze. Judging by the calls and email success stories, these simple techniques work pretty much world wide.
References for further study are at the end of the document.
Those who have followed these techniques with a stock cowl have no problems cooling especially with the trigear. In fact it gets a bit too cool in cooler climates and this is with no modifications to the existing cowl, only treating the airflow around the coolers.
I have worked these issues over the last six years and we just finished three more aircraft at the shop, all Rotax and we reworked a clients Jab 3300, and all the Rotax's have no cooling issues and the Jab is tolerable except taxi times must be short, 10 or 15 minutes max or it gets a bit too hot for a takeoff on a summer day.
I'll do another briefing/article on the Jabiru before long.
Call or email me at the office in Florida below if you have need of more specifics or are having problems getting the references on line.
Regards,
Bud Yerly
Europa Tech Support
US Europa Dealer
Custom Flight Creations, Inc.
www.customflightcreations.com
(813) 653-4989
|
<120610 - Cowl.pdf>
[b]
| - The Matronics Europa-List Email Forum - | | Use the List Feature Navigator to browse the many List utilities available such as the Email Subscriptions page, Archive Search & Download, 7-Day Browse, Chat, FAQ, Photoshare, and much more:
http://www.matronics.com/Navigator?Europa-List |
|
|
|
Back to top |
|
 |
rlborger(at)mac.com Guest
|
Posted: Tue Jun 12, 2012 5:05 am Post subject: Contact detail & Help |
|
|
Nigel,
Holy Cow! That's gorgeous! If it works as well as it looks it should be worth 25 Kts.
Keep us posted as work progresses and it flies. And take good care of those molds as you may have to spend all your spare time making copies for the rest of us.
Blue skies & tailwinds,
Bob Borger
Europa XS Tri, Rotax 914, Airmaster C/S Prop.
Little Toot Sport Biplane, Lycoming Thunderbolt AEIO-320 EXP
3705 Lynchburg Dr.
Corinth, TX 76208-5331
Cel: 817-992-1117
rlborger(at)mac.com (rlborger(at)mac.com)
On Jun 12, 2012, at 7:02 AM, nigel_graham(at)m-tecque.co.uk (nigel_graham(at)m-tecque.co.uk) wrote:
Bud,
A fascinating article - thanks. It would seem that I have spent the last God knows how many years researching the same data as you (mostly 1940's and 50's NACA papers) and come up with much the same conclusions regarding cooling and cooling drag reduction. By a curious coincidence, I have been busy this weekend buried in my workshop - laminating. Compare the results, hot-out-of-the-mould, with the computer generated cowl design on page 16 of your report. My design concepts would all appear to have come out of your "Lets's get radical" section!
Keep up the good work.
Nigel
On 10/06/2012 05:21, Bud Yerly wrote: Quote: | <?xml:namespace prefix="v" /><?xml:namespace prefix="o" /><![endif]--> Ken and Graham,
I've attached my modifications and techniques briefing used for Europa Cooling with the XS cowl which written up in the Europa Flyer .
If I do say so myself, I never have cooling issues in Florida at 95 degree summer days using 50/50 Anitifreeze. Judging by the calls and email success stories, these simple techniques work pretty much world wide.
References for further study are at the end of the document.
Those who have followed these techniques with a stock cowl have no problems cooling especially with the trigear. In fact it gets a bit too cool in cooler climates and this is with no modifications to the existing cowl, only treating the airflow around the coolers.
I have worked these issues over the last six years and we just finished three more aircraft at the shop, all Rotax and we reworked a clients Jab 3300, and all the Rotax's have no cooling issues and the Jab is tolerable except taxi times must be short, 10 or 15 minutes max or it gets a bit too hot for a takeoff on a summer day.
I'll do another briefing/article on the Jabiru before long.
Call or email me at the office in Florida below if you have need of more specifics or are having problems getting the references on line.
Regards,
Bud Yerly
Europa Tech Support
US Europa Dealer
Custom Flight Creations, Inc.
www.customflightcreations.com
(813) 653-4989
|
<120610 - Cowl.pdf>
| - The Matronics Europa-List Email Forum - | | Use the List Feature Navigator to browse the many List utilities available such as the Email Subscriptions page, Archive Search & Download, 7-Day Browse, Chat, FAQ, Photoshare, and much more:
http://www.matronics.com/Navigator?Europa-List |
|
|
|
Back to top |
|
 |
max8992
Joined: 28 Jul 2011 Posts: 142
|
Posted: Tue Jun 12, 2012 5:24 am Post subject: Contact detail & Help |
|
|
Hi Nigel,
I should say « Master Nigel », really Best-in-Class!
Assuming there is few hundreds of Europa flying word wide, I thing you have a market for it.
Otherwise, will you loan the mold or at least share the way to build it?
Max Cointe
F-PMLH TriGear Kit #560
912ULS Airmaster 420 hours
mcointe(at)free.fr (mcointe(at)free.fr)
De : owner-europa-list-server(at)matronics.com [mailto:owner-europa-list-server(at)matronics.com] De la part de nigel_graham(at)m-tecque.co.uk
Envoyé : mardi 12 juin 2012 14:03
Ŕ : europa-list(at)matronics.com
Objet : Re: Re: Contact detail & Help
Bud,
A fascinating article - thanks. It would seem that I have spent the last God knows how many years researching the same data as you (mostly 1940's and 50's NACA papers) and come up with much the same conclusions regarding cooling and cooling drag reduction. By a curious coincidence, I have been busy this weekend buried in my workshop - laminating. Compare the results, hot-out-of-the-mould, with the computer generated cowl design on page 16 of your report. My design concepts would all appear to have come out of your "Lets's get radical" section!
Keep up the good work.
Nigel
On 10/06/2012 05:21, Bud Yerly wrote:
Ken and Graham,
I've attached my modifications and techniques briefing used for Europa Cooling with the XS cowl which written up in the Europa Flyer .
If I do say so myself, I never have cooling issues in Florida at 95 degree summer days using 50/50 Anitifreeze. Judging by the calls and email success stories, these simple techniques work pretty much world wide.
References for further study are at the end of the document.
Those who have followed these techniques with a stock cowl have no problems cooling especially with the trigear. In fact it gets a bit too cool in cooler climates and this is with no modifications to the existing cowl, only treating the airflow around the coolers.
I have worked these issues over the last six years and we just finished three more aircraft at the shop, all Rotax and we reworked a clients Jab 3300, and all the Rotax's have no cooling issues and the Jab is tolerable except taxi times must be short, 10 or 15 minutes max or it gets a bit too hot for a takeoff on a summer day.
I'll do another briefing/article on the Jabiru before long.
Call or email me at the office in Florida below if you have need of more specifics or are having problems getting the references on line.
Regards,
Bud Yerly
Europa Tech Support
US Europa Dealer
Custom Flight Creations, Inc.
www.customflightcreations.com
(813) 653-4989
[quote][b]
| - The Matronics Europa-List Email Forum - | | Use the List Feature Navigator to browse the many List utilities available such as the Email Subscriptions page, Archive Search & Download, 7-Day Browse, Chat, FAQ, Photoshare, and much more:
http://www.matronics.com/Navigator?Europa-List |
|
_________________ Max8992
Europa XS #560 F-PMLH |
|
Back to top |
|
 |
Fred Klein
Joined: 26 Mar 2012 Posts: 503
|
Posted: Tue Jun 12, 2012 4:37 pm Post subject: Contact detail & Help |
|
|
On Jun 12, 2012, at 5:02 AM, nigel_graham(at)m-tecque.co.uk wrote:
Quote: | It would seem that I have spent the last God knows how many years
researching the same data as you (mostly 1940's and 50's NACA
papers) and come up with much the same conclusions regarding cooling
and cooling drag reduction. By a curious coincidence, I have been
busy this weekend buried in my workshop - laminating.
|
Nigel...do you Brits still shout "Huzzah?
What outstanding work...absolutely superb...I can appreciate your many
talents, dedication, hard work, and the HOURS you've devoted to this
beauty. Here, here!!
Two questions:
- weight: ?
- distance from front face of cowl (not including spinner) to edge of
cowl which overlaps the firewall?
Fred
| - The Matronics Europa-List Email Forum - | | Use the List Feature Navigator to browse the many List utilities available such as the Email Subscriptions page, Archive Search & Download, 7-Day Browse, Chat, FAQ, Photoshare, and much more:
http://www.matronics.com/Navigator?Europa-List |
|
|
|
Back to top |
|
 |
nigel_graham(at)m-tecque. Guest
|
Posted: Wed Jun 13, 2012 1:35 am Post subject: Contact detail & Help |
|
|
Hi Fred, Kevin, Bob and Max,
Thank you all for your kind words, worth all the more coming from people whose opinions I respect and appreciate.
Fred, I've answered your questions below.
Nigel
On 13/06/2012 01:36, Fred Klein wrote: Quote: | --> Europa-List message posted by: Fred Klein <fklein(at)orcasonline.com> (fklein(at)orcasonline.com)
On Jun 12, 2012, at 5:02 AM, nigel_graham(at)m-tecque.co.uk (nigel_graham(at)m-tecque.co.uk) wrote:
Quote: | It would seem that I have spent the last God knows how many years researching the same data as you (mostly 1940's and 50's NACA papers) and come up with much the same conclusions regarding cooling and cooling drag reduction. By a curious coincidence, I have been busy this weekend buried in my workshop - laminating.
|
Nigel...do you Brits still shout "Huzzah?
| Not as much as we used to Fred. There's not a lot of call for it at the moment, though I did startle the neighbours with a hearty "Yeeeee Ha" when it popped out of the mould without sticking.
Quote: |
What outstanding work...absolutely superb...I can appreciate your many talents, dedication, hard work, and the HOURS you've devoted to this beauty. Here, here!!
| Thanks.
Quote: | Two questions:
- weight: ?
| Top Cowl = 2139g
Bottom cowl = 2856g
Spinner = 545g
Quote: | - distance from front face of cowl (not including spinner) to edge of cowl which overlaps the firewall?
| 850mm or about 33.5 of Her Majesty's finest inches into the "Joggle" (should be the same as an XS). The real trick was making a short and dumpy cowl look long and sleek.
On 12/06/2012 14:22, Max Cointe wrote: Quote: |
Assuming there is few hundreds of Europa flying word wide, I thing you have a market for it.
Otherwise, will you loan the mold or at least share the way to build it? | Max, The cowling is only part of a programme of extensive "face-lift" mods for the Europa, so until I have finished mine and tested it and had it approved, I do not really want to sell on copies. I would however be happy to give any hints or tips on how to create "plugs" and moulds to allow you to create your own in a typical home environment (I.e. without full composite factory facilities). If interested, contact me off-list.
Nigel
[quote][b]
| - The Matronics Europa-List Email Forum - | | Use the List Feature Navigator to browse the many List utilities available such as the Email Subscriptions page, Archive Search & Download, 7-Day Browse, Chat, FAQ, Photoshare, and much more:
http://www.matronics.com/Navigator?Europa-List |
|
|
|
Back to top |
|
 |
budyerly(at)msn.com Guest
|
Posted: Thu Jun 14, 2012 8:47 pm Post subject: Contact detail & Help |
|
|
<?xml:namespace prefix="v" /><?xml:namespace prefix="o" /><![endif]--> Nigel,
Where do you find the time.
Don't you just hate paying that much for carbon? Disgusting, isn't it. It is great stuff.
I assisted our local engineering college at the University of Central Florida with some senior design project supervision and we got the carbon donated. The young engineering students didn't understand....
Regards,
Bud
[quote] ---
| - The Matronics Europa-List Email Forum - | | Use the List Feature Navigator to browse the many List utilities available such as the Email Subscriptions page, Archive Search & Download, 7-Day Browse, Chat, FAQ, Photoshare, and much more:
http://www.matronics.com/Navigator?Europa-List |
|
|
|
Back to top |
|
 |
frans(at)privatepilots.nl Guest
|
Posted: Wed Jun 20, 2012 3:11 am Post subject: Contact detail & Help |
|
|
On 06/10/2012 06:21 AM, Bud Yerly wrote:
Quote: | If I do say so myself, I never have cooling issues in Florida at 95
degree summer days using 50/50 Anitifreeze. Judging by the calls and
email success stories, these simple techniques work pretty much world wide.
|
Although your solution might indeed work world wide it is less suitable
for Europeans.
There are a few reasons for this:
1) Your solution is focussed on more cooling air flow. Unfortunately
more cooling air also means more cooling drag. More cooling drag means
that higher power settings are required to achieve a desired cruise
speed. Although that might not be significant for those living in a part
of the world where fuel prices are only a fraction from what it is here,
for many of us here the fuel price is by far the largest cost involved
with flying our Europa's.
In another posting you wrote:
"135 with the old pants at 5500/34 inches at 1000 MSL,"
"His trigear only goes 130 at max cruise."
I do 130 with 27", about 155 with 34". This is a heavy hi-top tri-gear.
Although I selected a very efficient prop and have Fred Kleins wing root
fairings, I believe that a large portion of the reduction in drag is
achieved by my modified cooling system.
2) Climate. I believe that in your area the weather is somewhat more
constant than it is here. This month I have been flying in cruise mode
in freezing temperature conditions (high altitude in Norway) and in
prolonged full power climbs with 35C OAT (Croatia). Unless you use
thermostats you can't achieve constant temperatures in all conditions.
After numerous experiments this is what I have learned:
0) Cooling drag is the main drag of modern efficient airplanes. Imagine
the air swirling around in the cowling, colliding in all kind of
obstacles, and flowing over tubular objects (worst airodynamic shape
possible) and finally leaving the airplane in the wrong direction and
with the wrong speed...
1) The Rotax engine is for 95% liquid (oil, coolant) cooled. Forget
about airflow over the engine, apart from the cylinder walls no cooling
air is needed at all. Sure you can compensate for a poor liquid cooling
with air flow, but it is extremely inefficient. Once you have the liquid
cooling working correctly, you can close off all holes. That's right,
ALL holes. This includes the two "eye's". the gills, the naca inlets,
the nose wheel opening, everything. There is only one small opening
needed to connect the Rotax shroud for cylinder wall cooling.
2) The main problem in the stock setup is the radiator. The stock
radiator is too thick (not even to mention the tandem design). The
pressure difference required to maintain enough air flow is too large,
and you need very large openings to keep enough air flowing. I have
tried many carefully designed diffusers but I never got the stock
radiator working sufficient enough for prolonged full power climbs in
hot weather.
3) Use an oil to water heat exchanger. This means that you have to focus
on the air flow of only one radiator, and also don't need an oil
thermostat and still have superfast warm-up times.
4) Get away with the entire "dog house". It is ugly and it serves no
purpose.
5) Use an adjustable cowl flap to control engine temperatures.
6) Reroute the exhaust so the cowl opening points to the rear. I tried
to build an exhaust augmentor but I'm not sure if it really works. In
any case, the cowling air escaping around the exhaust opening flows in
the correct direction and doesn't upset the air stream.
So. what I'm using now is a thin radiator, mounted flush with the
underside of the cowling. (Custom made, 300 Euro's). It is slanted so it
follows the shape of the cowling. Because of the angle the horizontal
frontal area is very small, you can say it forms a natural diffuser.
Flow is controlled by an exit cowl flap. If the air flow is restricted
by the cowl flap, the air in front of the radiator even doesn't "see"
the radiator, the air flows over the surface and follows the shape of
the cowling as if the radiator doesn't exist at all.
The air leaving the radiator is recycled because it flows under the
engine, taking the heat of exhaust and turbo with it on its way out. No
separate openings for these items are necessary.
The coolant is also used to cool (or heat!) the oil via a heat
exchanger. Apart from the heat-up time, the oil temperature is always 5C
higher than the coolant temperature, which I consider to be perfect. I
keep the water at 105C and the oil at 110C in all conditions. This is
the best for the engine and the efficiency.
For cylinder cooling you can use the standard Rotax shroud with the
opening under the propeller. I made my own shroud because of the vaccuum
pad alternator which prevents the use of the standard shroud, but the
idea is similar.
After one year of using this, I can state the following results:
1) Adequate cooling in ALL conditions. I have excecuted a full power
climb from 0ft to FL095 at 80 knots in an inversion layer with a OAT of
35C for most of the trajectory, with the water temp not exceeding 110C
and the oil not exceeding 120C. This was with the cowl flap not yet
fully open. Although not yet tested, I'm convinced that the cooling
would work ok in OAT's of 45C as well.
2) In cruise the cowl flap is typically only half an inch open; i.e. it
protrudes only a half inch below the belly of the airplane. Compare that
with the huge tunnelexit of the stock XS design!
3) Unlimited ground operations, even in very hot weather.
4) Superfast heat-up times. 5 minutes is even in the winter sufficient
to get the oil temp far enough up into the yellow arc to perform a take off.
5) Low cowling temperatures, despite the lack of ventilation.
Temperatures don't exceed 60C, except briefly after engine shut off. In
hot weather I open the oil tank access door after landing for a few
minutes to let the hot air out.
6) Weight savings. I have not weighed the difference, but I'm sure the
flat radiator and heat exchanger is lighter than the two stock radiators
and tunnel hard ware.
About the picture:
This was the unfinished design. The final version is even smoother.
The only exit opening here is the proptrusion of the "tunnel" against
the belly of the fuselage. The nose wheel opening is sealed off and
flush with the belly. The cowl flap can be extended further but this is
the typical cruise setting. Quite a difference compared to the stock
tunnel, eh?
In addition of the rectangular radiator opening I have two round inlets.
The one on the starboard side serves the intercooler for the turbo (via
a wedge diffuser and butterfly valve). You don't need this inlet if you
don't have an intercooler. The opening on the port side connects to the
cylinder wall shrouds. You could use the standard Rotax shroud with the
opening below the prop instead, but I made a round inlet on the port
side to maintain the symmetry. In most setups you can ommit these round
inlets. That would be an even cleaner nose!
The starboard inlet also facilitates the engine air intake. The port
inlet also connects to a very small auxilliary oil radiator. Without
this radiator the water-oil delta T was 10C, and with the extra radiator
I got my desired delta T of 5C. It is not really needed if you are
satisfied with the standard delta T.
On the top of the firewall you see a small servo, a similar model as the
vertical trim servo. This servo connects via a rod to the cowl flap. The
cowl flap hinges close to the radiator so even when it is fully open the
angle is very low. A simple but very efficent mechanism!
The front exhaust elbows are wrapped to save the cowling which is very
close.
If there is enough interest in this subject, I'm willing to write an
article about it. There is a lot of testing, reading, thinking, and
learning from failures behind this design.
Although I have been flying a year with it now, I have only recently
been able to test it in very hot and demanding conditions during our
just finished round trip in Corsica, Italy and Croatia and overflying
the Alps twice.
More about that trip later.
Frans
| - The Matronics Europa-List Email Forum - | | Use the List Feature Navigator to browse the many List utilities available such as the Email Subscriptions page, Archive Search & Download, 7-Day Browse, Chat, FAQ, Photoshare, and much more:
http://www.matronics.com/Navigator?Europa-List |
|
Description: |
|
Filesize: |
71.91 KB |
Viewed: |
9211 Time(s) |
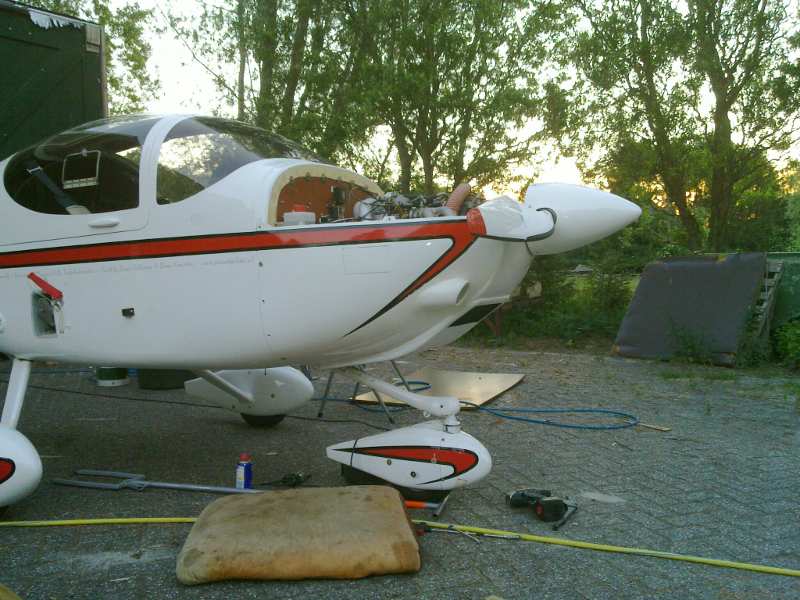
|
|
|
Back to top |
|
 |
davidjoyce(at)doctors.org Guest
|
Posted: Wed Jun 20, 2012 6:00 am Post subject: Contact detail & Help |
|
|
Frans, I for one and I am sure the entire Europa Club
committee would love to see you write an article for the
Europa Flyer detailing your design and flying findings.
Regards, David Joyce, G-XSDJ
On Wed, 20 Jun 2012 14:04:55 +0200
Frans Veldman <frans(at)privatepilots.nl> wrote:
Quote: | On 06/10/2012 06:21 AM, Bud Yerly wrote:
> If I do say so myself, I never have cooling issues in
>Florida at 95
> degree summer days using 50/50 Anitifreeze. Judging by
>the calls and
> email success stories, these simple techniques work
>pretty much world wide.
Although your solution might indeed work world wide it
is less suitable
for Europeans.
There are a few reasons for this:
1) Your solution is focussed on more cooling air flow.
Unfortunately
more cooling air also means more cooling drag. More
cooling drag means
that higher power settings are required to achieve a
desired cruise
speed. Although that might not be significant for those
living in a part
of the world where fuel prices are only a fraction from
what it is here,
for many of us here the fuel price is by far the largest
cost involved
with flying our Europa's.
In another posting you wrote:
"135 with the old pants at 5500/34 inches at 1000 MSL,"
"His trigear only goes 130 at max cruise."
I do 130 with 27", about 155 with 34". This is a heavy
hi-top tri-gear.
Although I selected a very efficient prop and have Fred
Kleins wing root
fairings, I believe that a large portion of the
reduction in drag is
achieved by my modified cooling system.
2) Climate. I believe that in your area the weather is
somewhat more
constant than it is here. This month I have been flying
in cruise mode
in freezing temperature conditions (high altitude in
Norway) and in
prolonged full power climbs with 35C OAT (Croatia).
Unless you use
thermostats you can't achieve constant temperatures in
all conditions.
After numerous experiments this is what I have learned:
0) Cooling drag is the main drag of modern efficient
airplanes. Imagine
the air swirling around in the cowling, colliding in all
kind of
obstacles, and flowing over tubular objects (worst
airodynamic shape
possible) and finally leaving the airplane in the wrong
direction and
with the wrong speed...
1) The Rotax engine is for 95% liquid (oil, coolant)
cooled. Forget
about airflow over the engine, apart from the cylinder
walls no cooling
air is needed at all. Sure you can compensate for a poor
liquid cooling
with air flow, but it is extremely inefficient. Once you
have the liquid
cooling working correctly, you can close off all holes.
That's right,
ALL holes. This includes the two "eye's". the gills, the
naca inlets,
the nose wheel opening, everything. There is only one
small opening
needed to connect the Rotax shroud for cylinder wall
cooling.
2) The main problem in the stock setup is the radiator.
The stock
radiator is too thick (not even to mention the tandem
design). The
pressure difference required to maintain enough air flow
is too large,
and you need very large openings to keep enough air
flowing. I have
tried many carefully designed diffusers but I never got
the stock
radiator working sufficient enough for prolonged full
power climbs in
hot weather.
3) Use an oil to water heat exchanger. This means that
you have to focus
on the air flow of only one radiator, and also don't
need an oil
thermostat and still have superfast warm-up times.
4) Get away with the entire "dog house". It is ugly and
it serves no
purpose.
5) Use an adjustable cowl flap to control engine
temperatures.
6) Reroute the exhaust so the cowl opening points to the
rear. I tried
to build an exhaust augmentor but I'm not sure if it
really works. In
any case, the cowling air escaping around the exhaust
opening flows in
the correct direction and doesn't upset the air stream.
So. what I'm using now is a thin radiator, mounted flush
with the
underside of the cowling. (Custom made, 300 Euro's). It
is slanted so it
follows the shape of the cowling. Because of the angle
the horizontal
frontal area is very small, you can say it forms a
natural diffuser.
Flow is controlled by an exit cowl flap. If the air flow
is restricted
by the cowl flap, the air in front of the radiator even
doesn't "see"
the radiator, the air flows over the surface and follows
the shape of
the cowling as if the radiator doesn't exist at all.
The air leaving the radiator is recycled because it
flows under the
engine, taking the heat of exhaust and turbo with it on
its way out. No
separate openings for these items are necessary.
The coolant is also used to cool (or heat!) the oil via
a heat
exchanger. Apart from the heat-up time, the oil
temperature is always 5C
higher than the coolant temperature, which I consider to
be perfect. I
keep the water at 105C and the oil at 110C in all
conditions. This is
the best for the engine and the efficiency.
For cylinder cooling you can use the standard Rotax
shroud with the
opening under the propeller. I made my own shroud
because of the vaccuum
pad alternator which prevents the use of the standard
shroud, but the
idea is similar.
After one year of using this, I can state the following
results:
1) Adequate cooling in ALL conditions. I have excecuted
a full power
climb from 0ft to FL095 at 80 knots in an inversion
layer with a OAT of
35C for most of the trajectory, with the water temp not
exceeding 110C
and the oil not exceeding 120C. This was with the cowl
flap not yet
fully open. Although not yet tested, I'm convinced that
the cooling
would work ok in OAT's of 45C as well.
2) In cruise the cowl flap is typically only half an
inch open; i.e. it
protrudes only a half inch below the belly of the
airplane. Compare that
with the huge tunnelexit of the stock XS design!
3) Unlimited ground operations, even in very hot
weather.
4) Superfast heat-up times. 5 minutes is even in the
winter sufficient
to get the oil temp far enough up into the yellow arc to
perform a take off.
5) Low cowling temperatures, despite the lack of
ventilation.
Temperatures don't exceed 60C, except briefly after
engine shut off. In
hot weather I open the oil tank access door after
landing for a few
minutes to let the hot air out.
6) Weight savings. I have not weighed the difference,
but I'm sure the
flat radiator and heat exchanger is lighter than the two
stock radiators
and tunnel hard ware.
About the picture:
This was the unfinished design. The final version is
even smoother.
The only exit opening here is the proptrusion of the
"tunnel" against
the belly of the fuselage. The nose wheel opening is
sealed off and
flush with the belly. The cowl flap can be extended
further but this is
the typical cruise setting. Quite a difference compared
to the stock
tunnel, eh?
In addition of the rectangular radiator opening I have
two round inlets.
The one on the starboard side serves the intercooler for
the turbo (via
a wedge diffuser and butterfly valve). You don't need
this inlet if you
don't have an intercooler. The opening on the port side
connects to the
cylinder wall shrouds. You could use the standard Rotax
shroud with the
opening below the prop instead, but I made a round inlet
on the port
side to maintain the symmetry. In most setups you can
ommit these round
inlets. That would be an even cleaner nose!
The starboard inlet also facilitates the engine air
intake. The port
inlet also connects to a very small auxilliary oil
radiator. Without
this radiator the water-oil delta T was 10C, and with
the extra radiator
I got my desired delta T of 5C. It is not really needed
if you are
satisfied with the standard delta T.
On the top of the firewall you see a small servo, a
similar model as the
vertical trim servo. This servo connects via a rod to
the cowl flap. The
cowl flap hinges close to the radiator so even when it
is fully open the
angle is very low. A simple but very efficent mechanism!
The front exhaust elbows are wrapped to save the cowling
which is very
close.
If there is enough interest in this subject, I'm willing
to write an
article about it. There is a lot of testing, reading,
thinking, and
learning from failures behind this design.
Although I have been flying a year with it now, I have
only recently
been able to test it in very hot and demanding
conditions during our
just finished round trip in Corsica, Italy and Croatia
and overflying
the Alps twice.
More about that trip later.
Frans
|
| - The Matronics Europa-List Email Forum - | | Use the List Feature Navigator to browse the many List utilities available such as the Email Subscriptions page, Archive Search & Download, 7-Day Browse, Chat, FAQ, Photoshare, and much more:
http://www.matronics.com/Navigator?Europa-List |
|
|
|
Back to top |
|
 |
paul.the.aviator(at)gmail Guest
|
Posted: Wed Jun 20, 2012 8:35 am Post subject: Contact detail & Help |
|
|
Ha ha.... I wondered who was going to be first out of the closet, me or Fran’s. Fran’s and I have been collaborating on a journey of discovery for the last couple of years.
I have been reluctant to share what I have been doing, mostly because up until now I have only been able to tell everyone what doesn't work! Both Fran's and I can share funny stories of tuft test showing air flow out where it should be flowing in, some take offs where we couldn't get back on the ground quick enough due overheating and lots of work and re work.
For me, I am still works in progress, but over the next winter I plan on a fourth iteration over next winter which will be a similar design to Fran’s. If I can persuade my friend Graham Singleton to come and visit, it might even a new carbon fiber cowling
At a high level the sources of design material we used were:
- Kays & London wedge diffuser
- Kuchemann & Weber trumpet diffuser
- Cooling design notes from the Central States Canard Group
- Taper diffuser design from the Canard group
- Oil Streaking presentations from the Central States Canard Group
- Think Vs. think radiator notes from Rotary Engine forums.
- Cooling Vs flow data from Rotax and Laminova
Our design criteria was:
Cooling that works in all phases of operation:
Operates over a range of -5c to 40c
Offers the lowest drag possible
This ultimately dictated a few design solutions:
Cowl Flap.
This is the only way we could get cooling over a large speed range and ambient temperature.
Laminova liquid oil heat exchanger.
In one of the design iterations that Fran's had created he had the oil and water radiators separated. Although this provided plenty of oil and liquid cooling it caused a long cycle time to bring the oil temperature up to operating temperature. The Laminova solves this problem. One problem that Fran's and I have not been able to solve is the need for a small axillary oil radiator.
Thick Vs. Thin Radiators.
I was ultimately able to make the thick radiator work with a Kuchemann & Weber trumpet diffuser, but I intend to abandon this. From our research we have discovered that 70 to 80% of the heat exchange occurs in the first 20mm of the radiator.
Diffused Inlets.
At first glance Fran's cowl appears to have no diffuser on the inlet side of the radiator, however it works very well. After reading the design notes for the Kays & London wedge diffuser our hypothesis is that because the coolant radiator is at an angle to the relative wind it behaves like a wedge diffusers.
Other thoughts & observations.
Fran’s has been flying a working solution for nearly a year and his design can be used as is. I am doing some experimentation with a single diffused inlet that provides the engine combustion air, inter cooler and the engine shroud. Given the level of effort this has proved to be I wouldn’t recommend anyone copying what I have done, and it remains to be seen if it even works.
Over next winter I plan on removing the thick radiator and I expect that this will be a lower drag configuration over what I have.
Pointing the exhaust back is offers a lot of drag reduction. I have some photographs that show the exhaust plume on the old style exhaust shooting out nearly 2 meters. For monowheel the exhaust needs to be much longer so that carbon monoxide does not find its way into cabin via the tunnel. Unfortunately this was complex bit of stainless steel to fabricate.
When my cowling is fully open it is the same angle as the standard cowling. I see 8 knots difference between fully open and fully closed. This isn't an exact comparison because when my cowl flap is open air will spill around the side and I expect this would be higher drag than the original cowl. I have done a number of long cross country trips and for the same manifold pressure settings I am seeing about 5 knots increase in my cruise. I have Warp drive blades and I do not wing root fairings so my set up is not as efficient as Fran’s.
Regards, Paul [quote][b]
| - The Matronics Europa-List Email Forum - | | Use the List Feature Navigator to browse the many List utilities available such as the Email Subscriptions page, Archive Search & Download, 7-Day Browse, Chat, FAQ, Photoshare, and much more:
http://www.matronics.com/Navigator?Europa-List |
|
|
|
Back to top |
|
 |
budyerly(at)msn.com Guest
|
Posted: Fri Jun 22, 2012 2:02 pm Post subject: Contact detail & Help |
|
|
Lovely design...
However, my comments are based on an installation that is stock. Takes 40 hours from openning the box to engine fully installed and ready for start and is reapeatable with only the parts in the box.
Esthetics aside, the dog box works but can be improved.
Many do not care to have any auto systems such as heat exchangers which may malfunction.
I do 146 at 5500/34 with a stock cowl.
By all means, an extra hundred hours and cost will get you those extra 9 knots. It just costs money and time.
The airplane is 20,000 compromises flying in close formation....Choose your changes wisely.
You have obviously enjoyed and profited from your changes. Congrats.
Bud Yerly Custom Flight Creations, Inc. www.customflightcreations.com (813) 653-4989
Quote: | Date: Wed, 20 Jun 2012 14:04:55 +0200
From: frans(at)privatepilots.nl
To: europa-list(at)matronics.com
Subject: Re: Re: Contact detail & Help
On 06/10/2012 06:21 AM, Bud Yerly wrote:
> If I do say so myself, I never have cooling issues in Florida at 95
> degree summer days using 50/50 Anitifreeze. Judging by the calls and
> email success stories, these simple techniques work pretty much world wide.
Although your solution might indeed work world wide it is less suitable
for Europeans.
There are a few reasons for this:
1) Your solution is focussed on more cooling air flow. Unfortunately
more cooling air also means more cooling drag. More cooling drag means
that higher power settings are required to achieve a desired cruise
speed. Although that might not be significant for those living in a part
of the world where fuel prices are only a fraction from what it is here,
for many of us here the fuel price is by far the largest cost involved
with flying our Europa's.
In another posting you wrote:
"135 with the old pants at 5500/34 inches at 1000 MSL,"
"His trigear only goes 130 at max cruise."
I do 130 with 27", about 155 with 34". This is a heavy hi-top tri-gear.
Although I selected a very efficient prop and have Fred Kleins wing root
fairings, I believe that a large portion of the reduction in drag is
achieved by my modified cooling system.
2) Climate. I believe that in your area the weather is somewhat more
constant than it is here. This month I have been flying in cruise mode
in freezing temperature conditions (high altitude in Norway) and in
prolonged full power climbs with 35C OAT (Croatia). Unless you use
thermostats you can't achieve constant temperatures in all conditions.
After numerous experiments this is what I have learned:
0) Cooling drag is the main drag of modern efficient airplanes. Imagine
the air swirling around in the cowling, colliding in all kind of
obstacles, and flowing over tubular objects (worst airodynamic shape
possible) and finally leaving the airplane in the wrong direction and
with the wrong speed...
1) The Rotax engine is for 95% liquid (oil, coolant) cooled. Forget
about airflow over the engine, apart from the cylinder walls no cooling
air is needed at all. Sure you can compensate for a poor liquid cooling
with air flow, but it is extremely inefficient. Once you have the liquid
cooling working correctly, you can close off all holes. That's right,
ALL holes. This includes the two "eye's". the gills, the naca inlets,
the nose wheel opening, everything. There is only one small opening
needed to connect the Rotax shroud for cylinder wall cooling.
2) The main problem in the stock setup is the radiator. The stock
radiator is too thick (not even to mention the tandem design). The
pressure difference required to maintain enough air flow is too large,
and you need very large openings to keep enough air flowing. I have
tried many carefully designed diffusers but I never got the stock
radiator working sufficient enough for prolonged full power climbs in
hot weather.
3) Use an oil to water heat exchanger. This means that you have to focus
on the air flow of only one radiator, and also don't need an oil
thermostat and still have superfast warm-up times.
4) Get away with the entire "dog house". It is ugly and it serves no
purpose.
5) Use an adjustable cowl flap to control engine temperatures.
6) Reroute the exhaust so the cowl opening points to the rear. I tried
to build an exhaust augmentor but I'm not sure if it really works. In
any case, the cowling air escaping around the exhaust opening flows in
the correct direction and doesn't upset the air stream.
So. what I'm using now is a thin radiator, mounted flush with the
underside of the cowling. (Custom made, 300 Euro's). It is slanted so it
follows the shape of the cowling. Because of the angle the horizontal
frontal area is very small, you can say it forms a natural diffuser.
Flow is controlled by an exit cowl flap. If the air flow is restricted
by the cowl flap, the air in front of the radiator even doesn't "see"
the radiator, the air flows over the surface and follows the shape of
the cowling as if the radiator doesn't exist at all.
The air leaving the radiator is recycled because it flows under the
engine, taking the heat of exhaust and turbo with it on its way out. No
separate openings for these items are necessary.
The coolant is also used to cool (or heat!) the oil via a heat
exchanger. Apart from the heat-up time, the oil temperature is always 5C
higher than the coolant temperature, which I consider to be perfect. I
keep the water at 105C and the oil at 110C in all conditions. This is
the best for the engine and the efficiency.
For cylinder cooling you can use the standard Rotax shroud with the
opening under the propeller. I made my own shroud because of the vaccuum
pad alternator which prevents the use of the standard shroud, but the
idea is similar.
After one year of using this, I can state the following results:
1) Adequate cooling in ALL conditions. I have excecuted a full power
climb from 0ft to FL095 at 80 knots in an inversion layer with a OAT of
35C for most of the trajectory, with the water temp not exceeding 110C
and the oil not exceeding 120C. This was with the cowl flap not yet
fully open. Although not yet tested, I'm convinced that the cooling
would work ok in OAT's of 45C as well.
2) In cruise the cowl flap is typically only half an inch open; i.e. it
protrudes only a half inch below the belly of the airplane. Compare that
with the huge tunnelexit of the stock XS design!
3) Unlimited ground operations, even in very hot weather.
4) Superfast heat-up times. 5 minutes is even in the winter sufficient
to get the oil temp far enough up into the yellow arc to perform a take off.
5) Low cowling temperatures, despite the lack of ventilation.
Temperatures don't exceed 60C, except briefly after engine shut off. In
hot weather I open the oil tank access door after landing for a few
minutes to let the hot air out.
6) Weight savings. I have not weighed the difference, but I'm sure the
flat radiator and heat exchanger is lighter than the two stock radiators
and tunnel hard ware.
About the picture:
This was the unfinished design. The final version is even smoother.
The only exit opening here is the proptrusion of the "tunnel" against
the belly of the fuselage. The nose wheel opening is sealed off and
flush with the belly. The cowl flap can be extended further but this is
the typical cruise setting. Quite a difference compared to the stock
tunnel, eh?
In addition of the rectangular radiator opening I have two round inlets.
The one on the starboard side serves the intercooler for the turbo (via
a wedge diffuser and butterfly valve). You don't need this inlet if you
don't have an intercooler. The opening on the port side connects to the
cylinder wall shrouds. You could use the standard Rotax shroud with the
opening below the prop instead, but I made a round inlet on the port
side to maintain the symmetry. In most setups you can ommit these round
inlets. That would be an even cleaner nose!
The starboard inlet also facilitates the engine air intake. The port
inlet also connects to a very small auxilliary oil radiator. Without
this radiator the water-oil delta T was 10C, and with the extra radiator
I got my desired delta T of 5C. It is not really needed if you are
satisfied with the standard delta T.
On the top of the firewall you see a small servo, a similar model as the
vertical trim servo. This servo connects via a rod to the cowl flap. The
cowl flap hinges close to the radiator so even when it is fully open the
angle is very low. A simple but very efficent mechanism!
The front exhaust elbows are wrapped to save the cowling which is very
close.
If there is enough interest in this subject, I'm willing to write an
article about it. There is a lot of testing, reading, thinking, and
learning from failures behind this design.
Although I have been flying a year with it now, I have only recently
been able to test it in very hot and demanding conditions during our
just finished round trip in Corsica, Italy and Croatia and overflying
the Alps twice.
More about that trip later.
Frans
|
[quote][b]
| - The Matronics Europa-List Email Forum - | | Use the List Feature Navigator to browse the many List utilities available such as the Email Subscriptions page, Archive Search & Download, 7-Day Browse, Chat, FAQ, Photoshare, and much more:
http://www.matronics.com/Navigator?Europa-List |
|
|
|
Back to top |
|
 |
grahamsingleton(at)btinte Guest
|
Posted: Sat Jun 23, 2012 2:44 am Post subject: Contact detail & Help |
|
|
Paul
you know I can't resist temptation! I suspect that a bit of work re exdhaust extraction might
be profitable, it seems to work well on Long EZs, hoping to verify with flight testing in the next month.
Graham
From: Paul McAllister <paul.the.aviator(at)gmail.com>
To: europa-list(at)matronics.com
Sent: Wednesday, 20 June 2012, 17:32
Subject: Re: Re: Contact detail & Help
Ha ha.... I wondered who was going to be first out of the closet, me or Fran’s. Fran’s and I have been collaborating on a journey of discovery for the last couple of years.
I have been reluctant to share what I have been doing, mostly because up until now I have only been able to tell everyone what doesn't work! Both Fran's and I can share funny stories of tuft test showing air flow out where it should be flowing in, some take offs where we couldn't get back on the ground quick enough due overheating and lots of work and re work.
For me, I am still works in progress, but over the next winter I plan on a fourth iteration over next winter which will be a similar design to Fran’s. If I can persuade my friend Graham Singleton to come and visit, it might even a new carbon fiber cowling
At a high level the sources of design material we used were:
- Kays & London wedge diffuser
- Kuchemann & Weber trumpet diffuser
- Cooling design notes from the Central States Canard Group
- Taper diffuser design from the Canard group
- Oil Streaking presentations from the Central States Canard Group
- Think Vs. think radiator notes from Rotary Engine forums.
- Cooling Vs flow data from Rotax and Laminova
Our design criteria was:
Cooling that works in all phases of operation:
Operates over a range of -5c to 40c
Offers the lowest drag possible
This ultimately dictated a few design solutions:
Cowl Flap.
This is the only way we could get cooling over a large speed range and ambient temperature.
Laminova liquid oil heat exchanger.
In one of the design iterations that Fran's had created he had the oil and water radiators separated. Although this provided plenty of oil and liquid cooling it caused a long cycle time to bring the oil temperature up to operating temperature. The Laminova solves this problem. One problem that Fran's and I have not been able to solve is the need for a small axillary oil radiator.
Thick Vs. Thin Radiators.
I was ultimately able to make the thick radiator work with a Kuchemann & Weber trumpet diffuser, but I intend to abandon this. From our research we have discovered that 70 to 80% of the heat exchange occurs in the first 20mm of the radiator.
Diffused Inlets.
At first glance Fran's cowl appears to have no diffuser on the inlet side of the radiator, however it works very well. After reading the design notes for the Kays & London wedge diffuser our hypothesis is that because the coolant radiator is at an angle to the relative wind it behaves like a wedge diffusers.
Other thoughts & observations.
Fran’s has been flying a working solution for nearly a year and his design can be used as is. I am doing some experimentation with a single diffused inlet that provides the engine combustion air, inter cooler and the engine shroud. Given the level of effort this has proved to be I wouldn’t recommend anyone copying what I have done, and it remains to be seen if it even works.
Over next winter I plan on removing the thick radiator and I expect that this will be a lower drag configuration over what I have.
Pointing the exhaust back is offers a lot of drag reduction. I have some photographs that show the exhaust plume on the old style exhaust shooting out nearly 2 meters. For monowheel the exhaust needs to be much longer so that carbon monoxide does not find its way into cabin via the tunnel. Unfortunately this was complex bit of stainless steel to fabricate.
When my cowling is fully open it is the same angle as the standard cowling. I see 8 knots difference between fully open and fully closed. This isn't an exact comparison because when my cowl flap is open air will spill around the side and I expect this would be higher drag than the original cowl. I have done a number of long cross country trips and for the same manifold pressure settings I am seeing about 5 knots increase in my cruise. I have Warp drive blades and I do not wing root fairings so my set up is not as efficient as Fran’s.
Regards, Paul
[quote]http://www.matronics.com/Navigator?_blank" href="http://forums.matronics.com/">http://forums.matronics.com</ rel="nofollow" target="_blank" href="http://www.matronics.com/contri===
[b]
| - The Matronics Europa-List Email Forum - | | Use the List Feature Navigator to browse the many List utilities available such as the Email Subscriptions page, Archive Search & Download, 7-Day Browse, Chat, FAQ, Photoshare, and much more:
http://www.matronics.com/Navigator?Europa-List |
|
|
|
Back to top |
|
 |
paul.the.aviator(at)gmail Guest
|
Posted: Sat Jun 23, 2012 5:45 am Post subject: Contact detail & Help |
|
|
Hello Graham,
Frans has attempted this with his design, but for a mono wheel there is a
very real chance of CO entering the airplane through the tunnel.
Exhaust augmentation / extraction makes a whole range of issues go away.
Ground cooling gets better the faster the engine runs, and as I understand
it from the Long EZ guys, you no longer need to diffuse the inlet airstream
| - The Matronics Europa-List Email Forum - | | Use the List Feature Navigator to browse the many List utilities available such as the Email Subscriptions page, Archive Search & Download, 7-Day Browse, Chat, FAQ, Photoshare, and much more:
http://www.matronics.com/Navigator?Europa-List |
|
|
|
Back to top |
|
 |
grahamsingleton(at)btinte Guest
|
Posted: Sat Jun 23, 2012 10:19 am Post subject: Contact detail & Help |
|
|
agree with all you say, however: I used to get exhaust gas in cabin without it, it probably got in via the flap slots. There must be a significant drag penalty from the exhaust plume squirting out vertical to the airflow.
Graham
From: Paul McAllister <paul.the.aviator(at)gmail.com>
To: europa-list(at)matronics.com
Sent: Saturday, 23 June 2012, 14:44
Subject: Re: Re: Contact detail & Help
Hello Graham,
Frans has attempted this with his design, but for a mono wheel there is a very real chance of CO entering the airplane through the tunnel.
Exhaust augmentation / extraction makes a whole range of issues go away. Ground cooling gets better the faster the engine runs, and as I understand it from the Long EZ guys, you no longer need to diffuse the inlet airstream.
Alas, I am with Bud on this.... time for tinkering is long over. I would guess with research and building that Frans and I have spent many hundreds of hours and its time to go flying
Cheers, Paul
On Sat, Jun 23, 2012 at 5:44 AM, GRAHAM SINGLETON <grahamsingleton(at)btinternet.com (grahamsingleton(at)btinternet.com)> wrote:
[quote] Paul
you know I can't resist temptation! I suspect that a bit of work re exdhaust extraction might
be profitable, it seems to work well on Long EZs, hoping to verify with flight testing in the next month.
Graham
From: Paul McAllister <paul.the.aviator(at)gmail.com (paul.the.aviator(at)gmail.com)>
To: europa-list(at)matronics.com (europa-list(at)matronics.com)
Sent: Wednesday, 20 June 2012, 17:32
Subject: Re: Re: Contact detail & Help
Ha ha.... I wondered who was going to be first out of the closet, me or Fran’s. Fran’s and I have been collaborating on a journey of discovery for the last couple of years.
I have been reluctant to share what I have been doing, mostly because up until now I have only been able to tell everyone what doesn't work! Both Fran's and I can share funny stories of tuft test showing air flow out where it should be flowing in, some take offs where we couldn't get back on the ground quick enough due overheating and lots of work and re work.
For me, I am still works in progress, but over the next winter I plan on a fourth iteration over next winter which will be a similar design to Fran’s. If I can persuade my friend Graham Singleton to come and visit, it might even a new carbon fiber cowling
At a high level the sources of design material we used were:
- Kays & London wedge diffuser
- Kuchemann & Weber trumpet diffuser
- Cooling design notes from the Central States Canard Group
- Taper diffuser design from the Canard group
- Oil Streaking presentations from the Central States Canard Group
- Think Vs. think radiator notes from Rotary Engine forums.
- Cooling Vs flow data from Rotax and Laminova
Our design criteria was:
Cooling that works in all phases of operation:
Operates over a range of -5c to 40c
Offers the lowest drag possible
This ultimately dictated a few design solutions:
Cowl Flap.
This is the only way we could get cooling over a large speed range and ambient temperature.
Laminova liquid oil heat exchanger.
In one of the design iterations that Fran's had created he had the oil and water radiators separated. Although this provided plenty of oil and liquid cooling it caused a long cycle time to bring the oil temperature up to operating temperature. The Laminova solves this problem. One problem that Fran's and I have not been able to solve is the need for a small axillary oil radiator.
Thick Vs. Thin Radiators.
I was ultimately able to make the thick radiator work with a Kuchemann & Weber trumpet diffuser, but I intend to abandon this. From our research we have discovered that 70 to 80% of the heat exchange occurs in the first 20mm of the radiator.
Diffused Inlets.
At first glance Fran's cowl appears to have no diffuser on the inlet side of the radiator, however it works very well. After reading the design notes for the Kays & London wedge diffuser our hypothesis is that because the coolant radiator is at an angle to the relative wind it behaves like a wedge diffusers.
Other thoughts & observations.
Fran’s has been flying a working solution for nearly a year and his design can be used as is. I am doing some experimentation with a single diffused inlet that provides the engine combustion air, inter cooler and the engine shroud. Given the level of effort this has proved to be I wouldn’t recommend anyone copying what I have done, and it remains to be seen if it even works.
Over next winter I plan on removing the thick radiator and I expect that this will be a lower drag configuration over what I have.
Pointing the exhaust back is offers a lot of drag reduction. I have some photographs that show the exhaust plume on the old style exhaust shooting out nearly 2 meters. For monowheel the exhaust needs to be much longer so that carbon monoxide does not find its way into cabin via the tunnel. Unfortunately this was complex bit of stainless steel to fabricate.
When my cowling is fully open it is the same angle as the standard cowling. I see 8 knots difference between fully open and fully closed. This isn't an exact comparison because when my cowl flap is open air will spill around the side and I expect this would be higher drag than the original cowl. I have done a number of long cross country trips and for the same manifold pressure settings I am seeing about 5 knots increase in my cruise. I have Warp drive blades and I do not wing root fairings so my set up is not as efficient as Fran’s.
Regards, Paul
f="http://www.matronics.com/Navigator?Europa-List">http://www.matronics.c========================
" target="_blank" href="http://forums.matronics.com/">http://forums.mat --> [b]
| - The Matronics Europa-List Email Forum - | | Use the List Feature Navigator to browse the many List utilities available such as the Email Subscriptions page, Archive Search & Download, 7-Day Browse, Chat, FAQ, Photoshare, and much more:
http://www.matronics.com/Navigator?Europa-List |
|
|
|
Back to top |
|
 |
frans(at)privatepilots.nl Guest
|
Posted: Sun Jun 24, 2012 2:38 am Post subject: Contact detail & Help |
|
|
On 06/23/2012 12:01 AM, Bud Yerly wrote:
Thanks!
Quote: | However, my comments are based on an installation that is stock. Takes
40 hours from openning the box to engine fully installed and ready for
start and is reapeatable with only the parts in the box.
|
My solution would be even faster to build, if they would change the
contents of the box of course. It puzzles me why the contents of the box
has not been changed long time ago, when people started to complain
about inadequate cooling.
Quote: | Many do not care to have any auto systems such as heat exchangers which
may malfunction.
|
There is no auto system involved. The heat exchanger is just two fluid
channels thermo coupled to each other. No moving parts, no electronic
parts, just similar to a radiator, but now with two fluid channels
instead of one fluid and one gas channel.
Quote: | By all means, an extra hundred hours and cost will get you those extra 9
knots. It just costs money and time.
|
This argument is silly. Then why applying a finish on the airplane and
not painting the raw fabric? It just costs money and time to apply a
finish, for only 9 knots of speed or so.
9 knots of speed:
1) The difference between a mono and tri gear.
2) equals to 10% fuel savings when flying with equal speeds.
10% fuel saving means:
1) About 10% lower operational costs.
2) About 5 Kg's (10 lbs) of weight saving for the same flying distance
because you need to carry less fuel.
3) A 10% larger range on a full tank.
Quote: | The airplane is 20,000 compromises flying in close formation....Choose
your changes wisely.
|
If I wanted a stock airplane and didn't care about speed, I would
probably be flying a Cessna 152.
Frans
| - The Matronics Europa-List Email Forum - | | Use the List Feature Navigator to browse the many List utilities available such as the Email Subscriptions page, Archive Search & Download, 7-Day Browse, Chat, FAQ, Photoshare, and much more:
http://www.matronics.com/Navigator?Europa-List |
|
|
|
Back to top |
|
 |
|
|
You cannot post new topics in this forum You cannot reply to topics in this forum You cannot edit your posts in this forum You cannot delete your posts in this forum You cannot vote in polls in this forum You cannot attach files in this forum You can download files in this forum
|
Powered by phpBB © 2001, 2005 phpBB Group
|