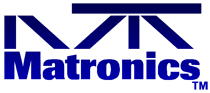 |
Matronics Email Lists Web Forum Interface to the Matronics Email Lists
|
View previous topic :: View next topic |
Author |
Message |
user9253
Joined: 28 Mar 2008 Posts: 1929 Location: Riley TWP Michigan
|
Posted: Sun Jun 17, 2012 1:34 pm Post subject: Viking Schematic |
|
|
I am helping a friend with a schematic for his Viking powered airplane. See the attached pdf. Is it safe to eliminate the Schottky diode in the lower left corner? I want to remove the diode because it is one more failure point and I do not know if it can handle the full load of the main bus, perhaps as much as 25 or 30 amps. The concern is a short in the alternator or starter circuit (Or is this a remote possibility?) with no way to isolate it without stopping the electrically dependent engine.
Thanks for any advice.
Joe
| - The Matronics AeroElectric-List Email Forum - | | Use the List Feature Navigator to browse the many List utilities available such as the Email Subscriptions page, Archive Search & Download, 7-Day Browse, Chat, FAQ, Photoshare, and much more:
http://www.matronics.com/Navigator?AeroElectric-List |
|
Description: |
|
 Download |
Filename: |
Viking RV-12e.pdf |
Filesize: |
71.15 KB |
Downloaded: |
490 Time(s) |
_________________ Joe Gores |
|
Back to top |
|
 |
nuckolls.bob(at)aeroelect Guest
|
Posted: Tue Jun 19, 2012 6:43 am Post subject: Viking Schematic |
|
|
At 04:34 PM 6/17/2012, you wrote:
I am helping a friend with a schematic for his Viking powered
airplane. See the attached pdf. Is it safe to eliminate the
Schottky diode in the lower left corner? I want to remove the diode
because it is one more failure point and I do not know if it can
handle the full load of the main bus, perhaps as much as 25 or 30
amps. The concern is a short in the alternator or starter circuit
(Or is this a remote possibility?) with no way to isolate it without
stopping the electrically dependent engine.
Thanks for any advice.
Joe
--------
Joe Gores
The rationale for this design is not clear just
from the schematic. It appears to borrow nothing
from the design philosophies for failure tolerance
offered in the Z-figures. I'd have to know more about
why it was all wired this way. What are the
current demands for the two ignition systems?
Bob . . .
| - The Matronics AeroElectric-List Email Forum - | | Use the List Feature Navigator to browse the many List utilities available such as the Email Subscriptions page, Archive Search & Download, 7-Day Browse, Chat, FAQ, Photoshare, and much more:
http://www.matronics.com/Navigator?AeroElectric-List |
|
|
|
Back to top |
|
 |
user9253
Joined: 28 Mar 2008 Posts: 1929 Location: Riley TWP Michigan
|
Posted: Tue Jun 19, 2012 9:22 am Post subject: Re: Viking Schematic |
|
|
Bob,
My friend is building an RV-12 with an automotive engine, the Viking, which is fuel injected and electrically dependent. The power requirements for the ECU are not known but Viking uses 15 amp fuses.
http://www.vikingaircraftengines.com/Wiring%20page.html
I do not like the electrical drawing on the Viking website because there are several possible points of failure all in series and supplying power to the engine through only one wire.
I suggested to my friend that he use one of your drawings but he said they were too complicated. I tried to simplify by removing the E-Bus and E-Bus diode, while still having a redundant power source for the ignition and fuel pumps without having always hot wires pass through the firewall. The ignition and fuel pumps are located on the opposite side (aft) of the firewall from the engine.
If the Alternate Feed Switch is turned on, the engine start circuit is disabled. This will prevent starting current from flowing through the Alternate Feed Relay and damaging its contacts. It is intended that the Alternate Feed Switch be turned on after starting and left on for the remainder of the flight.
My friend prefers circuit breakers even though I recommended fuses. He also wants to keep weight down by not having a starter contactor.
The Main Bus receives power at each end of the bus. If one connection should fail, the other will still provide power to the bus.
The engine should keep running with power coming from only the Alternate Feed Relay or only from Master Contactor or only from the Alternator.
The Viking ECU has two independent (almost) units in one enclosure, although it only has one wire supplying power. There is no pin-out available for the ECU 37-Pin D-Sub. The only information comes from the Viking website.
The ECU has a SELECT wire that enables one of the two units, depending on whether the voltage on that wire is high or low. At least that is what I deduced from the scant information on the Viking website.
The major difference between your excellent drawings and my schematic is that I have eliminated the E-Bus diode and replaced it with part of the Alternate Feed switch to prevent starting current from flowing though the Alternate Feed Relay contacts.
Now, without that E-Bus diode, I am having second thoughts about possible reverse current due to faults in the starter or alternator circuit.
Joe
| - The Matronics AeroElectric-List Email Forum - | | Use the List Feature Navigator to browse the many List utilities available such as the Email Subscriptions page, Archive Search & Download, 7-Day Browse, Chat, FAQ, Photoshare, and much more:
http://www.matronics.com/Navigator?AeroElectric-List |
|
_________________ Joe Gores |
|
Back to top |
|
 |
nuckolls.bob(at)aeroelect Guest
|
Posted: Thu Jun 21, 2012 2:39 pm Post subject: Viking Schematic |
|
|
At 12:22 PM 6/19/2012, you wrote:
Quote: |
Bob,
My friend is building an RV-12 with an automotive engine, the
Viking, which is fuel injected and electrically dependent. The
power requirements for the ECU are not known but Viking uses 15 amp fuses.
|
I've looked over the published instructions
from Viking and the drawing you attached.
The 'instructions' from Viking bear no demonstrable
understanding of failure tolerant architecture
for aircraft applications. There's a similar
'disconnect' from legacy and modern processes
and techniques for aircraft wiring.
If your friend is willing to bring his project
to "The List" and submit performance numbers
to mission goals, I (and probably others) would
be willing to help him sort the bits and pieces
to arrive at the elegant solution.
But the drawing taken together with abysmal
instructions do not describe a 'sandbox'
in which I would want to play. I would further
advise you to distance yourself from this
project. I've been made aware of several problem
projects wherein the builders conversed with me
but for reasons of their own, chose to do other
things . . . yet they claim to have consulted
me in the crafting of their system.
The engine is VERY experimental . . . which
is not a singular cause for concern. But the
entire electrical system is even more "experimental".
Burt Rutan used to advise, "do your engine experiments
on a TC aircraft and your airframe experiments with
a TC engine." The overarching point is to drive
risks to a minimum which must INCLUDE educating the
owner/pilot on how the system works and what to do
when things don't work.
I suggest your worries over the bus isolation diode
is but the tip of an iceberg in terms of having
identified and crafted work-arounds for all perceived
risks. Driving those risks up with decidedly untried
or demonstrably unsuited techniques and materials.
Bob . . .
| - The Matronics AeroElectric-List Email Forum - | | Use the List Feature Navigator to browse the many List utilities available such as the Email Subscriptions page, Archive Search & Download, 7-Day Browse, Chat, FAQ, Photoshare, and much more:
http://www.matronics.com/Navigator?AeroElectric-List |
|
|
|
Back to top |
|
 |
user9253
Joined: 28 Mar 2008 Posts: 1929 Location: Riley TWP Michigan
|
Posted: Thu Jun 21, 2012 5:27 pm Post subject: Re: Viking Schematic |
|
|
Bob,
Thanks for your words of wisdom so eloquently stated.
I think that the Viking powered aircraft can be wired, for the most part, using one of your drawings. There is one item unique to the Viking that is not addressed: ECU SELECT. The Viking website recommends using one DPDT switch wired in parallel to act as a SPDT switch. This switch will select either a high or low voltage and send it to the dual ECUs to enable either ECU1 or ECU2. My concern is that if this switch fails, the pilot will not be able to switch to the backup ECU if needed. Or if the switch fails open, who knows which ECU will be enabled, if any. It is unknown what bad things might happen if both ECUs are enabled at the same time, even for a second.
Is it safe to use one switch to choose between ECUs? If not, is there a better way than to use 2 mechanically interlocked switches? Perhaps a solid state circuit powered by the aircraft supply so that it would not load down the ECU.
Joe
| - The Matronics AeroElectric-List Email Forum - | | Use the List Feature Navigator to browse the many List utilities available such as the Email Subscriptions page, Archive Search & Download, 7-Day Browse, Chat, FAQ, Photoshare, and much more:
http://www.matronics.com/Navigator?AeroElectric-List |
|
Description: |
|
Filesize: |
21.91 KB |
Viewed: |
7153 Time(s) |
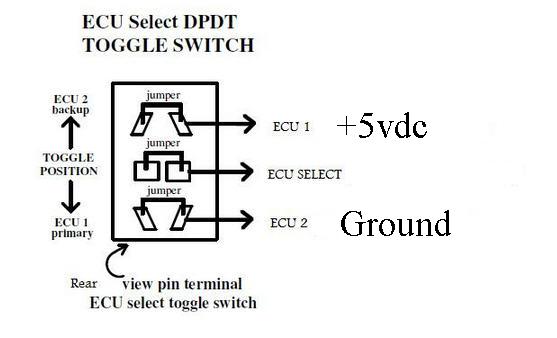
|
_________________ Joe Gores |
|
Back to top |
|
 |
nuckolls.bob(at)aeroelect Guest
|
Posted: Fri Jun 22, 2012 5:24 am Post subject: Viking Schematic |
|
|
At 08:27 PM 6/21/2012, you wrote:
Bob,
Thanks for your words of wisdom so eloquently stated.
I think that the Viking powered aircraft can be wired, for the most
part, using one of your drawings.
The exact architecture is not so important as
the overall philosophy for the design and materials
being considered. The Viking instructions did not
speak eloquently to wire insulation but did caution
about leaving your cowl open with the engine exposed
to the sun! They also suggested the use of screw-terminal
barrier strips . . . never used in TC aircraft to my
knowledge and certainly not on my watch. On those
two points alone, I would be inclined to comb the document
for fundamental points of fact for performance (which
there are precious few) and then pitch the document.
This builder needs to FIND OUT how much current each
of the ECU power inputs need. Then size wires, breakers
and ENERGY SOURCES accordingly. This is not much different
than a Lightspeed dual ignition system. If he is
truly interested in simplicity, then wire per C-150;
no e-bus or avionics bus. Run all normal ops equipment
from a single bus including #1 ECU. Then add an aux
battery sized to meet THE BUILDER's alternator out
endurance requirements and drive the #2 ECU from that
battery through it's own switch . . . not unlike the Lightspeed
recommendations. Separate switch for each ECU.
There is one item unique to the Viking that is not addressed: ECU
SELECT. The Viking website recommends using one DPDT switch wired in
parallel to act as a SPDT switch. This switch will select either a
high or low voltage and send it to the dual ECUs to enable either
ECU1 or ECU2. My concern is that if this switch fails, the pilot
will not be able to switch to the backup ECU if needed. Or if the
switch fails open, who knows which ECU will be enabled, if any. It
is unknown what bad things might happen if both ECUs are enabled at
the same time, even for a second.
Then find this out. Anyone willing to launch into the blue
without answers to such questions is an accident waiting
to happen . . . either from ignorance of this specific
question or others like it. There is a reason that flight
test pilots are required to have engineering degrees. It
is insufficient to simply be able to fly the airplane.
The pilot needs to (1) have an intimate understanding
of the airplane and (2) a well founded confidence in those
who say, "trust me, this will work." If this guy is in
the "trust me" mode of receiving data, then you and everyone
contributing that data are assuming risk that goes beyond
simple advise. An RV built per Van's instructions is a very
low risk flight system even for the "trust-me-it-will-work"
customer. A warm fuzzy to the FAA's utopian quest for spending
how ever much money it takes to drive the accident rate to zero.
Failure mode effects analysis takes an intimate understanding
of how the device or system is built right down to the last
resistor. Baring that kind of knowledge, you 'partition off'
blocks of a system and treat them as unknowns to be accommodated
with failure tolerant design. This is reminiscent of the philosophy
I was applying some years back during the "great IR/ER alternator
debates". Conversations which were in fact not debates but
affirmations of faith buy individuals who had no intimate
knowledge of the systems and devices which they were
promoting as "trust me, this will work."
This airplane and it's prospective pilot would benefit
from a top-down review not only of the engine and it's
requirements/idiosyncrasies but the materials, power
sources, distribution, and in particular developing
the Plan-B, C and D that can be called upon with
CONFIDENCE to deal with specific failures. This data
needs to be combined with mission profiles . . . day
VFR only?
Is it safe to use one switch to choose between ECUs?
No airplane is safe . . . every airplane ever built will
terminate your existence in a heartbeat. Some more
easily than others. The BD-5 comes to mind. Each comes
with varying levels of risk that are dependent as much
upon pilot knowledge and skill as system reliability.
If not, is there a better way than to use 2 mechanically interlocked
switches? Perhaps a solid state circuit powered by the aircraft
supply so that it would not load down the ECU.
FIND OUT if the operating the two ECUs in tandem
presents a risk. FIND OUT also how much current these
systems demand in cruising flight. If dual ECU ops presents
risk and assuming that the builder is driven by the
ultimate in simplicity, then use two separate switches
with the #2 being annunciated with a really annoying
light and taking power from a separate battery. Might
even space the #2 switch off in it's own corner of the
panel.
The point being that if all this modern equipment
operates true to history in its automotive applications,
then it's unlikely that #2 ECU will ever be needed
in flight. The only time #2 is ever turned on is in
pre-flight, on the ground and in accordance with
check-list procedure. As you've already perceived,
this "keep me from throwing the wrong switch" interlock
philosophy may add more risk than simply having each
system stand alone.
The answers to the questions you've posed are stone
simple. They require no more information than any other
system integrator would DEMAND in the design of any
other machine that poses risks to people and property.
It matters not whether it's an airplane or a 10-story
tall construction crane.
The biggest question in my mind is to determine if
your friend is a cognizant beneficiary of your efforts
or whether you're simply putting band-aids onto a system
with more risk-issues (yet unidentified) than the choice
of an ECU select switches.
Bob . . .
| - The Matronics AeroElectric-List Email Forum - | | Use the List Feature Navigator to browse the many List utilities available such as the Email Subscriptions page, Archive Search & Download, 7-Day Browse, Chat, FAQ, Photoshare, and much more:
http://www.matronics.com/Navigator?AeroElectric-List |
|
|
|
Back to top |
|
 |
user9253
Joined: 28 Mar 2008 Posts: 1929 Location: Riley TWP Michigan
|
Posted: Fri Jun 22, 2012 2:41 pm Post subject: Re: Viking Schematic |
|
|
Quote: | This builder needs to FIND OUT how much current each
of the ECU power inputs need. |
Unfortunately there is only ONE power input to the Dual ECU. I find it hard to believe that the ECU manufacturer would provide only one power input to their dual ECUs. I suspect that the Viking Engine developer, Jan Eggenfellner , has elected NOT to use a second available power input. I do not know this to be a fact. It is just speculation on my part.
Quote: | Then find this out. Anyone willing to launch into the blue
without answers to such questions is an accident waiting
to happen . . . either from ignorance of this specific
question or others like it. |
Unfortunately, Mr Eggenfellner has not answered such questions, probably because he does not know the answers. He is a good mechanic but might lack electrical knowledge.
Quote: | FIND OUT if the operating the two ECUs in tandem
presents a risk. FIND OUT also how much current these
systems demand in cruising flight. |
This question has been asked on the Viking website with no response from Mr Eggenfellner. If my assumption is correct that a high signal enables ECU1 and a low signal enables ECU2, then it would be impossible to operate both at once. No one knows the consequences of the simultaneous application of both high and low signals to the SELECT wire or the consequences of an open floating input.
My friend is making the final decisions on wiring his airplane. He has accepted some of my recommendations and rejected some.
From my point of view, it is hard to design a fool proof system without knowing the requirements or answers to above questions. All I can do is ensure that power is always available to the lone ECU power wire, regardless of the failure of any one component. And ensure that there is either a high or low signal on the SELECT wire, but never both at once.
I think that we agree that the electrical system for the Viking engine has not been designed with a backup plan in the event of failure of key components.
I am happy with my Rotax 912 engine.
Joe
| - The Matronics AeroElectric-List Email Forum - | | Use the List Feature Navigator to browse the many List utilities available such as the Email Subscriptions page, Archive Search & Download, 7-Day Browse, Chat, FAQ, Photoshare, and much more:
http://www.matronics.com/Navigator?AeroElectric-List |
|
_________________ Joe Gores |
|
Back to top |
|
 |
nuckolls.bob(at)aeroelect Guest
|
Posted: Fri Jun 22, 2012 5:16 pm Post subject: Viking Schematic |
|
|
<snip>
From my point of view, it is hard to design a fool proof system
without knowing the requirements or answers to above questions. All
I can do is ensure that power is always available to the lone ECU
power wire, regardless of the failure of any one component. And
ensure that there is either a high or low signal on the SELECT wire,
but never both at once.
I think you're right . . .
I think that we agree that the electrical system for the Viking
engine has not been designed with a backup plan in the event of
failure of key components.
Hmmmm . . . I think this is a system I'd like to
steer clear of . . .
Bob . . .
| - The Matronics AeroElectric-List Email Forum - | | Use the List Feature Navigator to browse the many List utilities available such as the Email Subscriptions page, Archive Search & Download, 7-Day Browse, Chat, FAQ, Photoshare, and much more:
http://www.matronics.com/Navigator?AeroElectric-List |
|
|
|
Back to top |
|
 |
nuckolls.bob(at)aeroelect Guest
|
Posted: Sun Jun 24, 2012 7:03 am Post subject: Viking Schematic |
|
|
Quote: | From my point of view, it is hard to design a fool proof system
without knowing the requirements or answers to above
questions. All I can do is ensure that power is always available
to the lone ECU power wire, regardless of the failure of any one
component. And ensure that there is either a high or low signal on
the SELECT wire, but never both at once.
|
Quote: | I think that we agree that the electrical system for the Viking
engine has not been designed with a backup plan in the event of
failure of key components.
|
Joe,
I don't know your friend . . . and I hope that my
worst concerns for how his project is going together
are unfounded. You're in the best position to add
to his knowledge pool for making sure that his
airplane goes together with a minimum of built-in
risks.
I recall having tried to converse with Eggenfellner
some years back. Very uncooperative to the extent that
I was concerned about his knowledge and attitudes for
offering critical systems to aircraft.
If your friend has not already read and studied the
hindsight available on line surrounding the Dan
Lloyd, RV-10, Eggenfellner accident, please encourage
him to do so. The postings in part are available
here:
http://tinyurl.com/7292l3z
http://tinyurl.com/6lqzab2
http://tinyurl.com/7ho2w57
Maybe he's already 'plugged in' . . . without
having engaged him in conversation and observed
his work, we cannot know. I am particularly
miffed with the Eggenfellner design in that
supposedly dual, independent engine critical
systems are not fitted with independent power
and control paths. I don't recall the engine
being considered when Z-19 was being crafted,
it might have been the Eggenfellner product.
It suggests steering diodes mounted close to
the single-power input connection to one-of
power plant accessories. If I had no other
choices but to install a Viking engine I
would take a similar approach.
Normal and Alternate engine control switches.
One taking power from the Main Battery Bus,
one taking power from an Aux Battery Bus.
If the numbers of switches is to be kept
low, then use #1 switch to activate both
power and command to the ECU for Normal
Ops, the #2 switch to activate both power
and command for Survivable Failure Ops.
They have a moral, ethical, professional and
even perhaps legal duty to make such data
available to customers. Alternatively,
they should offer their own iteration of Z-19
to provide failure tolerant functionality.
One or the other. If Dan Lloyd's engine
quit due to the disconnect of one wire and
could not be restarted by selection of
Plan-B . . . then somewhere along the line,
too many balls were fumbled . . . and not
for subtle, esoteric reasons. My perceptions
of risk for the Viking engine versus Eggenfellner
are disturbingly similar.
A discussion that really needs to be
conducted for mounting a concentrated
effort to acquire system integration data
from Viking Engines as to current demands and
consequences of having both ECU active at the
same time. This is simple data, easy to acquire
and absolutely necessary for competent
system integration.
Get me a name of a person that your friend
is working with at Viking and I'll make the
call.
Bob . . .
| - The Matronics AeroElectric-List Email Forum - | | Use the List Feature Navigator to browse the many List utilities available such as the Email Subscriptions page, Archive Search & Download, 7-Day Browse, Chat, FAQ, Photoshare, and much more:
http://www.matronics.com/Navigator?AeroElectric-List |
|
|
|
Back to top |
|
 |
user9253
Joined: 28 Mar 2008 Posts: 1929 Location: Riley TWP Michigan
|
Posted: Sun Jun 24, 2012 9:10 am Post subject: Re: Viking Schematic |
|
|
Bob,
My friend sent me a CC email today that he also sent to others who are installing a Viking engine. Here is a copy of that message:
Quote: | Joe introduced me to the Matronics forum, sponsored by Bob Nuckolls. There is an RV 12 section, and Joe submitted our concerns for public comments. Suggest you read the exchange and join the list. |
And so, my friend and others are aware of the inadequate electrical system illustrated on the Viking website.
Quote: | Get me a name of a person that your friend
is working with at Viking and I'll make the call. |
I am not aware of anyone at Viking giving electrical advice beside Jan E.
I think that it would benefit Jan Eggenfellner to make available all information about the electrical system, especially the ECU. Helping to prevent crashes of Viking powered aircraft will help his business. Even if Jan E is electrically challenged, others can use information that he provides to come up with an electrical system that will keep the engine running despite the failure of any one component.
Bob, I appreciate your concern. There may be some builders blindly following the Viking electrical drawings. But the builders that I am in contact with know the dangers and risks. Unfortunately the risks can not be mitigated without more knowledge of the ECU requirements and capabilities.
Joe
| - The Matronics AeroElectric-List Email Forum - | | Use the List Feature Navigator to browse the many List utilities available such as the Email Subscriptions page, Archive Search & Download, 7-Day Browse, Chat, FAQ, Photoshare, and much more:
http://www.matronics.com/Navigator?AeroElectric-List |
|
_________________ Joe Gores |
|
Back to top |
|
 |
nuckolls.bob(at)aeroelect Guest
|
Posted: Sun Jun 24, 2012 6:05 pm Post subject: Viking Schematic |
|
|
I am not aware of anyone at Viking giving electrical advice
beside Jan E. I think that it would benefit Jan Eggenfellner
to make available all information about the electrical system,
especially the ECU.
My face is red . . . I didn't realize that Viking was
direct descendant from the original Eggenfellner Subaru
operations.
Okay, I'll drop a note to Jan and see what, if any, information
he can share toward the goal of crafting a more failure tolerant
design
Bob . . .
| - The Matronics AeroElectric-List Email Forum - | | Use the List Feature Navigator to browse the many List utilities available such as the Email Subscriptions page, Archive Search & Download, 7-Day Browse, Chat, FAQ, Photoshare, and much more:
http://www.matronics.com/Navigator?AeroElectric-List |
|
|
|
Back to top |
|
 |
|
|
You cannot post new topics in this forum You cannot reply to topics in this forum You cannot edit your posts in this forum You cannot delete your posts in this forum You cannot vote in polls in this forum You cannot attach files in this forum You can download files in this forum
|
Powered by phpBB © 2001, 2005 phpBB Group
|