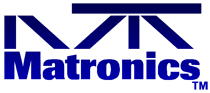 |
Matronics Email Lists Web Forum Interface to the Matronics Email Lists
|
View previous topic :: View next topic |
Author |
Message |
henry(at)pericynthion.org Guest
|
Posted: Sun Oct 28, 2012 4:36 pm Post subject: B&C alternator diagnosis |
|
|
Dear Bob et al,
I'm the owner but not the builder of a 1979 VariEze equipped with a
starterless O-200 and a B&C alternator (the 12-amp 200G model, I
believe). I don't have an ammeter in the cockpit. I do have an LED
bar-graph voltmeter in which I have placed little trust over the past
year or so, since it was showing around 12 volts rather than the
expected 13+. Perhaps I should have been more trusting.
Last week I had an electrical failure in flight, on a nice day over
familiar terrain. The first sign of trouble was the backlight
brightness decreasing on my Garmin 480; it subsequently reset itself
and then failed entirely. I have one magneto and one Lightspeed
electronic ignition, and not much else in the way of electronics in
the cockpit. Turning off the magneto resulted in rough running -
presumably the EI was trying its best to keep up with the low bus
voltage but didn't have enough juice to fire every time. Anyway I got
the green light signal from Livermore tower and landed without
incident. The battery measured 11.7 volts open-circuit.
This weekend I tried to diagnose the problem. The alternator circuit
breaker seems to be fine. I removed the regulator (see pics linked
below). The B&C alternator is a brushless model and only has two
wires coming out of it; I think the regulator is essentially a bridge
rectifier and a linear voltage regulator. B&C currently seems to sell
a separate "rectifier-type regulator" [1] and "crowbar" overvoltage
protection circuit [2]. I'm not sure if what I have is just the
regulator or a combination of the two. It looks to be completely
potted in resin except for one adjustment screw. It has four wires -
red (bus +), black (gnd) and two blue (alternator).
With a multimeter on diode mode I measured 0.55V drop from either blue
wire to the red, as you'd expect with a bridge rectifier. There was
also 1.2V drop from black to red, again as would be expected. But it
showed "open circuit" from black to either blue. Adjusting the screw
(which appeared to turn freely for 20+ revolutions, like one of those
multi-turn pots with the clutch) made no difference.
I plugged the regulator back in to the alternator (but not to the
aircraft bus), started the engine and observed 0.0V output on the red
and black wires. I disconnected the regulator again, measured the
alternator wires directly and saw around 17V AC.
So - the regulator's bad, right? It's not just trying to do something
clever in response to an open bus connection? I just want to be sure
I'm not missing something before I order a new one.
Thanks very much,
Henry
Photos:
Alternator - http://i.imgur.com/nIWgG.jpg
http://i.imgur.com/w8WlE.jpg http://i.imgur.com/ihwXI.jpg
Regulator - http://i.imgur.com/QXQUr.jpg http://i.imgur.com/ng9TH.jpg
[1] http://www.bandc.biz/regulator14vhomebuilt.aspx
[2] http://www.bandc.biz/pmovfilterandovprotectionkit14v.aspx
| - The Matronics AeroElectric-List Email Forum - | | Use the List Feature Navigator to browse the many List utilities available such as the Email Subscriptions page, Archive Search & Download, 7-Day Browse, Chat, FAQ, Photoshare, and much more:
http://www.matronics.com/Navigator?AeroElectric-List |
|
|
|
Back to top |
|
 |
henry(at)pericynthion.org Guest
|
Posted: Sun Oct 28, 2012 5:05 pm Post subject: B&C alternator diagnosis |
|
|
The mystery deepens. I connected the regulator to the alternator and
hooked the output of the regulator directly to the battery. Ran the
engine, saw the battery voltage increase from 12.15V (to which I had
previously trickle-charged it) to 12.4V and gradually over a few
minutes up to 12.8V. I removed the regulator output from the battery
(engine still running) and saw the output voltage from the regulator
rise to 15.0V. Connected it back to the battery via an ammeter and
saw 3.5A charge current - roughly what I should expect for an engine
idling around 1100 rpm. Adjusting the regulator's screw while all
this was happening didn't seem to change much.
So now I'm at a loss - it seems to be working again. Do you think
it's still a good idea to replace the regulator? The only other thing
I noticed is that one screw terminal on the battery was not tight -
not terribly loose, but I could undo it with just my fingers. I guess
I will put it all back together with a trusted voltmeter in the
cockpit and go fly in VMC for a while, but I'd love to hear ideas.
Thanks,
Henry
On Sun, Oct 28, 2012 at 5:34 PM, Henry Hallam <henry(at)pericynthion.org> wrote:
Quote: |
Dear Bob et al,
I'm the owner but not the builder of a 1979 VariEze equipped with a
starterless O-200 and a B&C alternator (the 12-amp 200G model, I
believe). I don't have an ammeter in the cockpit. I do have an LED
bar-graph voltmeter in which I have placed little trust over the past
year or so, since it was showing around 12 volts rather than the
expected 13+. Perhaps I should have been more trusting.
Last week I had an electrical failure in flight, on a nice day over
familiar terrain. The first sign of trouble was the backlight
brightness decreasing on my Garmin 480; it subsequently reset itself
and then failed entirely. I have one magneto and one Lightspeed
electronic ignition, and not much else in the way of electronics in
the cockpit. Turning off the magneto resulted in rough running -
presumably the EI was trying its best to keep up with the low bus
voltage but didn't have enough juice to fire every time. Anyway I got
the green light signal from Livermore tower and landed without
incident. The battery measured 11.7 volts open-circuit.
This weekend I tried to diagnose the problem. The alternator circuit
breaker seems to be fine. I removed the regulator (see pics linked
below). The B&C alternator is a brushless model and only has two
wires coming out of it; I think the regulator is essentially a bridge
rectifier and a linear voltage regulator. B&C currently seems to sell
a separate "rectifier-type regulator" [1] and "crowbar" overvoltage
protection circuit [2]. I'm not sure if what I have is just the
regulator or a combination of the two. It looks to be completely
potted in resin except for one adjustment screw. It has four wires -
red (bus +), black (gnd) and two blue (alternator).
With a multimeter on diode mode I measured 0.55V drop from either blue
wire to the red, as you'd expect with a bridge rectifier. There was
also 1.2V drop from black to red, again as would be expected. But it
showed "open circuit" from black to either blue. Adjusting the screw
(which appeared to turn freely for 20+ revolutions, like one of those
multi-turn pots with the clutch) made no difference.
I plugged the regulator back in to the alternator (but not to the
aircraft bus), started the engine and observed 0.0V output on the red
and black wires. I disconnected the regulator again, measured the
alternator wires directly and saw around 17V AC.
So - the regulator's bad, right? It's not just trying to do something
clever in response to an open bus connection? I just want to be sure
I'm not missing something before I order a new one.
Thanks very much,
Henry
Photos:
Alternator - http://i.imgur.com/nIWgG.jpg
http://i.imgur.com/w8WlE.jpg http://i.imgur.com/ihwXI.jpg
Regulator - http://i.imgur.com/QXQUr.jpg http://i.imgur.com/ng9TH.jpg
[1] http://www.bandc.biz/regulator14vhomebuilt.aspx
[2] http://www.bandc.biz/pmovfilterandovprotectionkit14v.aspx
|
| - The Matronics AeroElectric-List Email Forum - | | Use the List Feature Navigator to browse the many List utilities available such as the Email Subscriptions page, Archive Search & Download, 7-Day Browse, Chat, FAQ, Photoshare, and much more:
http://www.matronics.com/Navigator?AeroElectric-List |
|
|
|
Back to top |
|
 |
nuckolls.bob(at)aeroelect Guest
|
Posted: Mon Oct 29, 2012 8:34 am Post subject: B&C alternator diagnosis |
|
|
Quote: | Adjusting the regulator's screw while all
this was happening didn't seem to change much.
|
This alternator output is too small to be set
reliably at combinations of low rpm and significant
load.
Quote: | So now I'm at a loss - it seems to be working again. Do you think
it's still a good idea to replace the regulator? The only other thing
I noticed is that one screw terminal on the battery was not tight -
not terribly loose, but I could undo it with just my fingers. I guess
I will put it all back together with a trusted voltmeter in the
cockpit and go fly in VMC for a while, but I'd love to hear ideas.
|
The regulator can be accurately adjusted ONLY
with a fully charged battery, very light sytem
loads (suggest 2A or less) and SIGNIFICANT rpm,
like something 2000 or better.
The alternator is exceedingly robust . . . very
unlikely to fail. The rectifier/regulator has
a very low parts count, is potted for mechanical
ruggedness and is vulnerable to few stresses OTHER
than overheat.
If it has a history of good performance (Not accurately
known without an accurate voltmeter) what appears to
be a transient failure may have been a poor connection
that got 'cured' as a product of removal and replacement.
If it were my airplane, I'd fit it with a voltmeter of
trustworthy accuracy. Also, a low voltage warning
light so that future failures are not a surprise.
Find out where the system voltage stabilizes under light
load after some sustained operations . . . say just before
descent to land on your next trip. Make little tweeks
of the potentiometer setting based on these observations.
Shoot for 14.2 but settle for 14.0 to 14.5.
The successful resolution starts with trustworthy
measurement and observation. Where's your rectifier/
regulator mounted? Where does it tie into the electrical
system? Do you have a wiring diagram for this airplane
that can be scanned/shared?
Bob . . .
| - The Matronics AeroElectric-List Email Forum - | | Use the List Feature Navigator to browse the many List utilities available such as the Email Subscriptions page, Archive Search & Download, 7-Day Browse, Chat, FAQ, Photoshare, and much more:
http://www.matronics.com/Navigator?AeroElectric-List |
|
|
|
Back to top |
|
 |
henry(at)pericynthion.org Guest
|
Posted: Mon Oct 29, 2012 7:02 pm Post subject: B&C alternator diagnosis |
|
|
On Mon, Oct 29, 2012 at 9:33 AM, Robert L. Nuckolls, III
<nuckolls.bob(at)aeroelectric.com> wrote:
Quote: |
<nuckolls.bob(at)aeroelectric.com>
> Adjusting the regulator's screw while all
> this was happening didn't seem to change much.
This alternator output is too small to be set
reliably at combinations of low rpm and significant
load.
|
Thanks for the insights! I also found this doc on B&C's site:
http://www.bandc.biz/pdfs/sd8trbreva.pdf that agrees with everything
you've said.
Quote: | The successful resolution starts with trustworthy
measurement and observation. Where's your rectifier/
regulator mounted? Where does it tie into the electrical
system? Do you have a wiring diagram for this airplane
that can be scanned/shared?
Bob . . .
|
I will definitely be fitting a reliable voltmeter and warning light.
Unfortunately I don't have a wiring diagram, though I'm working on
putting one together from my own notes taken during maintenance and
upgrades. My rectifier/regulator is mounted on the engine side of the
firewall, in what I think is a relatively cool location (on the high
pressure side of the updraft cooling system). The positive output
goes via a 14 AWG wire to a 10-amp CB on the instrument panel and from
there to the positive battery terminal (battery in the nose of the
canard-pusher airplane). The negative output goes to a general ground
terminal on the engine mount frame and from there via a similar 14 AWG
wire to the negative battery terminal. The instrument power bus is
connected to the battery terminals by another set of wires, and
there's a third set for the electronic ignition.
Any reason not to tune the regulator voltage setpoint on the bench
with a constant-current bench supply on the blue wires and my airplane
battery on the red+black?
Thanks again for the advice.
Henry
| - The Matronics AeroElectric-List Email Forum - | | Use the List Feature Navigator to browse the many List utilities available such as the Email Subscriptions page, Archive Search & Download, 7-Day Browse, Chat, FAQ, Photoshare, and much more:
http://www.matronics.com/Navigator?AeroElectric-List |
|
|
|
Back to top |
|
 |
nuckolls.bob(at)aeroelect Guest
|
Posted: Tue Oct 30, 2012 5:17 am Post subject: B&C alternator diagnosis |
|
|
Quote: | I will definitely be fitting a reliable voltmeter and warning light.
Unfortunately I don't have a wiring diagram, though I'm working on
putting one together from my own notes taken during maintenance and
upgrades. My rectifier/regulator is mounted on the engine side of the
firewall, in what I think is a relatively cool location (on the high
pressure side of the updraft cooling system).
|
Good
Quote: | The positive output
goes via a 14 AWG wire to a 10-amp CB on the instrument panel and from
there to the positive battery terminal (battery in the nose of the
canard-pusher airplane).
|
Does your airplane have a starter? If so, where
is the starter contactor located?
Quote: | The negative output goes to a general ground
terminal on the engine mount frame and from there via a similar 14 AWG
wire to the negative battery terminal.
|
Hmmmm . . . I deduce that there is no starter
and the 14AWG ground is the only conductor between
the crankcase and the battery(-)?
Quote: | The instrument power bus is
connected to the battery terminals by another set of wires, and
there's a third set for the electronic ignition.
|
Hmmmm . . . battery terminal used as a power distribution
point. Is there a battery switch?
Quote: | Any reason not to tune the regulator voltage setpoint on the bench
with a constant-current bench supply on the blue wires and my airplane
battery on the red+black?
|
Yes, this is a crude form of switchmode regulator.
Not of the inductor-stored energy variety, but a
duty cycle switched series regulator with SCR's
that get triggered in a variable position along
each half-cycle of the incoming waveform.
It must be adjusted under operating conditions that
mimic the as-installed condition on the airplane.
Here's a schematic of an exemplar rectifier/regulator
for a PM alternator:
http://tinyurl.com/94585zs
When we crafted installation instructions for that
regulator/alternator combination on a no-starter
airplane years ago, I brought ac power to the
battery area on a twisted pair. The R-R was mounted
close to the battery so that series resistance in the
sense-lines shared with power-delivery lines did
not become significant impedances in the control
loop.
Later drawings published by B&C dropped that
configuration. That's been so long ago that I
don't recall if I had any conversation with them
about the change. I cannot prove that the old
configuration was demonstrably 'better' but it
was crafted with consideration for deleterious
effects of unnecessary resistance in sense
feeders shared with power feeders.
Don't know if it's an option for you but you
might consider using the 14AWG pair coming
forward as AC power feeders and move the R-R
to the forward space shared with the battery.
Bob . . .
| - The Matronics AeroElectric-List Email Forum - | | Use the List Feature Navigator to browse the many List utilities available such as the Email Subscriptions page, Archive Search & Download, 7-Day Browse, Chat, FAQ, Photoshare, and much more:
http://www.matronics.com/Navigator?AeroElectric-List |
|
|
|
Back to top |
|
 |
henry(at)pericynthion.org Guest
|
Posted: Tue Oct 30, 2012 9:23 am Post subject: B&C alternator diagnosis |
|
|
On Tue, Oct 30, 2012 at 6:11 AM, Robert L. Nuckolls, III
<nuckolls.bob(at)aeroelectric.com> wrote:
Quote: | > The positive output
> goes via a 14 AWG wire to a 10-amp CB on the instrument panel and from
> there to the positive battery terminal (battery in the nose of the
> canard-pusher airplane).
Does your airplane have a starter? If so, where
is the starter contactor located?
|
No starter.
Quote: |
> The negative output goes to a general ground
> terminal on the engine mount frame and from there via a similar 14 AWG
> wire to the negative battery terminal.
Hmmmm . . . I deduce that there is no starter
and the 14AWG ground is the only conductor between
the crankcase and the battery(-)?
|
Yes, except there are probably some other (skinnier) ground paths due
to engine sensors and the electronic ignition. The main ground
conductor might be 12 AWG rather than 14, I'll check tomorrow.
Quote: | > The instrument power bus is
> connected to the battery terminals by another set of wires, and
> there's a third set for the electronic ignition.
Hmmmm . . . battery terminal used as a power distribution
point. Is there a battery switch?
|
There's a switch labeled "battery" that supplies the instrument bus
(with individual CBs after that for each instrument). Is this
arrangement a bad idea?
Quote: |
> Any reason not to tune the regulator voltage setpoint on the bench
> with a constant-current bench supply on the blue wires and my airplane
> battery on the red+black?
Yes, this is a crude form of switchmode regulator.
Not of the inductor-stored energy variety, but a
duty cycle switched series regulator with SCR's
that get triggered in a variable position along
each half-cycle of the incoming waveform.
It must be adjusted under operating conditions that
mimic the as-installed condition on the airplane.
Here's a schematic of an exemplar rectifier/regulator
for a PM alternator:
http://tinyurl.com/94585zs
|
Makes sense, thanks!
Quote: |
When we crafted installation instructions for that
regulator/alternator combination on a no-starter
airplane years ago, I brought ac power to the
battery area on a twisted pair. The R-R was mounted
close to the battery so that series resistance in the
sense-lines shared with power-delivery lines did
not become significant impedances in the control
loop.
|
Interesting. It's great to get insight from the designer.
Quote: |
Later drawings published by B&C dropped that
configuration. That's been so long ago that I
don't recall if I had any conversation with them
about the change. I cannot prove that the old
configuration was demonstrably 'better' but it
was crafted with consideration for deleterious
effects of unnecessary resistance in sense
feeders shared with power feeders.
Don't know if it's an option for you but you
might consider using the 14AWG pair coming
forward as AC power feeders and move the R-R
to the forward space shared with the battery.
|
I'll look into it - I agree that sounds like a better arrangement
feedback-wise, but I don't think the existing wire run I have is a
twisted pair, so I'd be a bit concerned about EMI emissions from that
long of a run of chopped AC. I'll see how much trouble a new wire run
would be. If I had the time it could be a fun project to design my
own switching regulator with separate sense lines... for that matter,
do you know why these brushless alternator designs didn't use three
phases like a modern BLDC motor?
Thanks again
Henry
| - The Matronics AeroElectric-List Email Forum - | | Use the List Feature Navigator to browse the many List utilities available such as the Email Subscriptions page, Archive Search & Download, 7-Day Browse, Chat, FAQ, Photoshare, and much more:
http://www.matronics.com/Navigator?AeroElectric-List |
|
|
|
Back to top |
|
 |
nuckolls.bob(at)aeroelect Guest
|
Posted: Tue Oct 30, 2012 1:30 pm Post subject: B&C alternator diagnosis |
|
|
Quote: |
I'll look into it - I agree that sounds like a better arrangement
feedback-wise, but I don't think the existing wire run I have is a
twisted pair, so I'd be a bit concerned about EMI emissions from that
long of a run of chopped AC. |
I've not had an opportunity to run a PM alternator in
the lab . . . so the twisted pair was simple a prophylactic
derived from common sense. In any case, I doubt that
EMI products go very high in frequency. Given that ADF
is gone (taking am radio with it), the probability
for real interference is small. It would be a relatively
easy experiment. See if you can use the existing 14AWG
pair as an AC power feeder and then fly it.
Quote: | I'll see how much trouble a new wire run would be. |
Many moons ago, I was able to use an existing wire as
a pull-tape to run in a new instrumentation wire . . .
a shielded trio. The bundles between firewall and the nose
section were not tightly tied.
You might see if tugging on the 14AWG produces any
significant motion at non-scary forces.
Quote: | If I had the time it could be a fun project to design my
own switching regulator with separate sense lines... |
Yeah, I have such a design somewhere. I'll see if I
can dig it out. The design is a buck-regulator scaled
to run off the un-regulated, full wave rectified DC
out of the alternator. I looked at that product about
20 years ago but some new kids on the block might
re-open the door. Consider this:
A full wave rectifier on the firewall and local
capacitor would get you unregulated, HV dc. I don't
recall now what the open circuit AC votlage is for
your alternator at cruise . . . you might get a measurement
at some known ramp RPM from which we can extrapolate
the higher rpm value. Use a rectifier and filter capacitor
with a light load, say 100 ohms across it. Measure the resulting
DC at some handy RPM.
If max DC is below 28, then this regulator might have
promise:
http://tinyurl.com/8fm6reh
Given that you do not have a starter, there may not
be a good reason to keep a battery on board . . .
or the battery could be scaled down to deal with
only with taxi rpm situations. These regulators provide
constant, clean output as long as the input is
high enough. You might even consider two regulators.
They're light and smaller than a battery. One could
be a standby. It's exceedingly unlikely that you would
ever loose the alternator.
Food for thought.
for that matter,
Quote: | do you know why these brushless alternator designs didn't use three
phases like a modern BLDC motor? |
You could do that . . . here's an interesting
motor
[img]cid:.0[/img]
[img]cid:.0[/img]
BEMF of 6v/krpm says you'll get about 24 volts at
4000 pad drive speeds. The winding resistances are
low. It seems that you would get 10A plus out of this
motor back-driven as a PM, 3-phase alternator.
It would cost you about $200 to put your hands on one
to play with.
http://tinyurl.com/95jny8c
Bob . . .
| - The Matronics AeroElectric-List Email Forum - | | Use the List Feature Navigator to browse the many List utilities available such as the Email Subscriptions page, Archive Search & Download, 7-Day Browse, Chat, FAQ, Photoshare, and much more:
http://www.matronics.com/Navigator?AeroElectric-List |
|
Description: |
|
Filesize: |
48.08 KB |
Viewed: |
8720 Time(s) |

|
|
|
Back to top |
|
 |
nuckolls.bob(at)aeroelect Guest
|
Posted: Wed Oct 31, 2012 7:32 am Post subject: B&C alternator diagnosis |
|
|
At 07:14 PM 10/30/2012, you wrote:
Yeah, those little RC BLDC motors are amazing products.
I've got a couple here that have been played with a bit.
A few years ago, I was asked to proposed a table-top
demonstrator for quantifying both brushed and
brushless DC motor performance. Never got a response
back on my proposal. But it was an opportunity to
sample what was out there.
I've considered studying their application in a wind-driven
power source for ultra-lights and antiques. But that's
a project WAAAAaaayyy back on the burners!
Bob . . . [quote][b]
| - The Matronics AeroElectric-List Email Forum - | | Use the List Feature Navigator to browse the many List utilities available such as the Email Subscriptions page, Archive Search & Download, 7-Day Browse, Chat, FAQ, Photoshare, and much more:
http://www.matronics.com/Navigator?AeroElectric-List |
|
|
|
Back to top |
|
 |
user9253
Joined: 28 Mar 2008 Posts: 1929 Location: Riley TWP Michigan
|
Posted: Wed Oct 31, 2012 10:02 am Post subject: Re: B&C alternator diagnosis |
|
|
Quote: | do you know why these brushless alternator designs didn't use three
phases like a modern BLDC motor? |
This is pure speculation on my part; so correct me if wrong.
If the coils of a single phase alternator were rewired to make a 3 phase alternator, then voltage output would be only 1/3 of the single phase voltage. In order for a 3 phase alternator to have the same voltage output as a single phase alternator, it would have to have two more windings of the same size. Then it would weigh more and cost more.
Joe
| - The Matronics AeroElectric-List Email Forum - | | Use the List Feature Navigator to browse the many List utilities available such as the Email Subscriptions page, Archive Search & Download, 7-Day Browse, Chat, FAQ, Photoshare, and much more:
http://www.matronics.com/Navigator?AeroElectric-List |
|
_________________ Joe Gores |
|
Back to top |
|
 |
nuckolls.bob(at)aeroelect Guest
|
Posted: Wed Oct 31, 2012 12:11 pm Post subject: B&C alternator diagnosis |
|
|
At 01:02 PM 10/31/2012, you wrote:
> do you know why these brushless alternator designs didn't use three
> phases like a modern BLDC motor?
This is pure speculation on my part; so correct me if wrong.
If the coils of a single phase alternator were rewired to make a 3
phase alternator, then voltage output would be only 1/3 of the single
phase voltage. In order for a 3 phase alternator to have the same
voltage output as a single phase alternator, it would have to have
two more windings of the same size. Then it would weigh more and cost more.
Joe
--------
Joe Gores
The power output from an AC device is roughly proportional
to the weight of the active magnetic material (core), magnetic
strength and speed (rpm). I'm recalling from memory now but
back when I was winding my own transformers, a 1 pound core
was good for about 60 watts at 60 Hz. The same weight of core
in a 400 Hz system was good for 6.5 times that power . . .
400 watts. This assumes similar levels of magnetic flux
that can be carried in the core without saturation or
increases losses at higher frequencies.
An automotive alternator is already crafted as a 3-phase
device. The configuration requires that pole-pairs on the
rotating magnet come in some multiple of 3 (usually
6 pairs but can be more on larger machines).
The output voltage of any given widing is proportional
to speed x flux value x number of turns. When you 'rewind'
to get more voltage, it generally has to be done with
smaller wire . . . the winding window in the core is fixed.
The practical power output is not a linear function because
of heating effects of I-squared x R in the wires and the
windings ability to reject heat into the core and end turns.
There's not a great deal to be gained in power by going from
single to three-phase . . . it's that weight,flux,speed thing.
The BIG toe-stubber is pole piece configuration. The magnets
glued to the inside of the popular PM alternator shells (or
wound-field machines) are already optimized for their as-
manufactured condition. It takes more than a 'rewinding'
to morph from single to 3-phase configuration. But assuming
all other things are held the same, the watts-per-pound-per-
velocity will be the same for both configurations.
The BIG advantage of 3-phase is the smoother output with
simple full-wave rectification . . . about 5% ripple as
compared to 100% ripple for single-phase. But if the designer
sets out to do a clean piece of paper, 3-phase design it
will be only moderately more expensive. The power can be
a little better because the windings share duties . . . i.e.
there is never a time when current goes to zero in more than
one winding.
Bob . . .
Bob . . .
| - The Matronics AeroElectric-List Email Forum - | | Use the List Feature Navigator to browse the many List utilities available such as the Email Subscriptions page, Archive Search & Download, 7-Day Browse, Chat, FAQ, Photoshare, and much more:
http://www.matronics.com/Navigator?AeroElectric-List |
|
|
|
Back to top |
|
 |
|
|
You cannot post new topics in this forum You cannot reply to topics in this forum You cannot edit your posts in this forum You cannot delete your posts in this forum You cannot vote in polls in this forum You cannot attach files in this forum You can download files in this forum
|
Powered by phpBB © 2001, 2005 phpBB Group
|