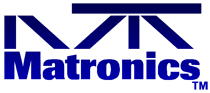 |
Matronics Email Lists Web Forum Interface to the Matronics Email Lists
|
View previous topic :: View next topic |
Author |
Message |
nuckolls.bob(at)aeroelect Guest
|
Posted: Thu Jan 03, 2013 5:34 am Post subject: Advisability of using anti-corrosion lubricant on contacts |
|
|
At 10:58 PM 1/2/2013, you wrote:
--> AeroElectric-List message posted by: "bobbarrow" <bobbarrow(at)bigpond.com>
What kind of connectors and what finish on the pins?
Power through Mil-C-26482 circular connectors with M39029 crimped contacts. Signals through M24308 DSub connectors with M39029 crimped contacts.
The M39029 contacts are typically gold plated copper alloy. However the female contact for the circular connector seems to have a stainless steel socket.
I have Corrosion X and LPS 1, 2, and 3 in stock.
I note that the spec on Corrosion X says it can be applied to "electrical and avionics components such as micro switches, Cannon plugs, antenna bases, circuit breakers, and bus bars.
The warning on Corrosion X in aircraft pertains to a research paper into the the affects that the lubricity of Corrosion X could have on friction mated structural components in shear. Nothing to do with use on electrical components.
I also have the normal run of behind-the-firewall connectors in the form of spades and ring terminals (forest of spade tabs for ground, bus bar ring terminals etc). These might benefit from some corrosion protection as well.
What do you think. Is a little corrosion X in order.
Qualification for the connector materials you've cited is rigorous. Their suitability to task has be demonstrated by decades of service history in a full range of applications. I cannot recall having encountered a connector failure due to environmental stresses within limits for which the connector was designed. Connectors fail mostly due to installation error or gross abuse that would affect not only the connector but much of the system hardware around it.
Other than addition of moisture displacing 'stuff' in the faying services of bolt-up joints, I see no value in application of 'more protection' for a condition that has no demonstrable risk. Indiscriminate use of such products seems more likely to raise risks for unintended consequences (like just plain messy) than to mitigate real risks.
Bob . . . [quote][b]
| - The Matronics AeroElectric-List Email Forum - | | Use the List Feature Navigator to browse the many List utilities available such as the Email Subscriptions page, Archive Search & Download, 7-Day Browse, Chat, FAQ, Photoshare, and much more:
http://www.matronics.com/Navigator?AeroElectric-List |
|
|
|
Back to top |
|
 |
nuckolls.bob(at)aeroelect Guest
|
Posted: Fri Jan 04, 2013 7:18 am Post subject: Advisability of using anti-corrosion lubricant on contacts |
|
|
At 07:06 AM 1/4/2013, you wrote:
Quote: |
<public(at)toddheffley.com>
Wow....Talk about the subject that will not die!
|
Not sure why anyone would want it to 'die' . . .
Quote: | I have watched this controversy in my industry (large cabin
executive jet maintenance) for some time now, and much like the
discussion here, it will not die.
Some airframers do not want corrosion inhibitors between the antenna
and the airframe.
Conversely, I worked for a MRO that requires Pentrox Type 2 (grey)
for every antanna installation. (conductive paste, feels like
toothpaste, non-hardening)
|
There's a BIG difference between the situation you
are citing and the conversations we've had here on
the list.
Quote: | My anecdotal experience tells me that antenna footprints are the
first and worst hideouts for corrosion on many aircraft.
Particularly lower antennas. My experience is 1 to 1 without
exception. If a removed antenna has Pentrox under the foot print, it
has no corrosion. I come down as a strong advocate for adding Penetrox.
|
Absolutely. But the identification of successful
remedies for specific issues does not translate
into a general applicability as a prophylactic
measure. I.e. using Penetrox to offset a specific
vulnerability does not suggest that dipping the
whole airplane into Penetrox is a good idea.
Quote: | I have two theories: one is that Airframers live in perfectly clean
factories with brand new airplanes that never corrode. Antennas are
installed on perfectly clean ground planes, and that thinking is
inviolate. MRO's live with 30 year old airplanes, thus the
difference between the two.
Theory number 2 is that the clamp up force of an antenna is very low
because of the large size of the footprint. Use of some type of
"magic goo" seems more reasonable, because one can never achieve
a vapor tight fit up over the entire footprint of the antenna.
I doubt there is a wooden stake for this vampire, but I would like
Bob's thoughts related to HBC background vs. OBAM background.
|
Some years ago I published this drawing
http://tinyurl.com/6rwodso
that spoke to the value of high mate-up forces
in the vicinity of mounting hardware along
with a suggestion that paint be removed from
skin ONLY around the holes. It was a toss-up
then as to how moisture might be prevented from
taking up long term residence under the antenna.
THIS is a problem. I suggested a bead of RTV on
the outside because it can be inspected and renewed
as needed. A gasket is NOT called for because it upsets
the design goal for gas-tight bonding at the bolt holes.
Silicon grease would be good for protecting the bonds
and is probably the preferred technique . . . but that
stuff is a high viscosity liquid with very good wetting
properties. This means that the stuff migrates out from
under the antenna base and stains surrounding surface
while adding dust collection. Looks like (at)#$(at)#.
Quote: | I come from a maintenance background , not a build background, so
....grain of salt....
|
So you're quite right that there's a unique and
challenging problem to seek the elegant process
by which long-lived antenna installations can
be made . . . certainly more than a 'grain of salt'.
In retrospect, given that electronic grade
RTV in the uncured state has no significant
compression strength, It would be interesting
to try an overall, liquid gasket approach
under the antenna using the silicone sealant.
I think it would extrude out of the gas-tight
contact areas as the bolts are torqued up. Squeeze-
out around the base is easily cleaned after
the bolts are tightened. Overall water tightness
should be quite good.
I'll put that into my list of experiments to
try . . . One could overlap 3" wide strips of
say 1/8" and equivalent thicknesses for skin
and doubler. Do the 'bonding' thing around 4
holes with 10-32 hardware in them. Dope the
interface between 1/8" and 'skin' with rtv
and clamp it up.
Do a test on bonding integrity of the two
surfaces after the RTV has cured. Repeat
without RTV and compare.
Bob . . .
| - The Matronics AeroElectric-List Email Forum - | | Use the List Feature Navigator to browse the many List utilities available such as the Email Subscriptions page, Archive Search & Download, 7-Day Browse, Chat, FAQ, Photoshare, and much more:
http://www.matronics.com/Navigator?AeroElectric-List |
|
|
|
Back to top |
|
 |
|
|
You cannot post new topics in this forum You cannot reply to topics in this forum You cannot edit your posts in this forum You cannot delete your posts in this forum You cannot vote in polls in this forum You cannot attach files in this forum You can download files in this forum
|
Powered by phpBB © 2001, 2005 phpBB Group
|