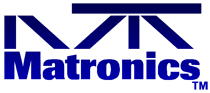 |
Matronics Email Lists Web Forum Interface to the Matronics Email Lists
|
View previous topic :: View next topic |
Author |
Message |
Propellerjan
Joined: 11 Jan 2013 Posts: 21 Location: Sweden
|
Posted: Fri Jan 11, 2013 2:36 pm Post subject: KIS TR-1 Airfoil |
|
|
KIS TR-1 Airfoil
In the search for information to calculate an optimum propeller for the KIS I0-240 I found a lot of information and thoughts about its handling especially during landing.
When picking an airfoil for a airplane project that is about the last thing to do before the design is set in stone. The wing area is determined in respect of stall speed with flap arrangement.
When having MTOW, wing aspect ratio and wing area, we can calculate speed and lift coefficient, CL
The speed we use for this will be where we spend most of the time, not stall speed and not top speed, but climb and normal cruise speed. So in this range the airfoil should have the lowest drag, if it was an airliner that spend most of its time climbing and cruising at high altitude at low indicated speed it will be at similar CL most of the time (but Mach Nr will play its roll)
All aircrafts that see any production see an increase in installed power and weight. If this was in the design of the KIS from start I don’t know, but the prototype had a Limbach from start if understand it correctly, and several hundred lbs less weight.
Most seem to have the I0-240B engine installed now and a MTOW of 1450 lb or so. And it is cruising at around 140 kts. This give an lift coefficient, of around CL 0.3 at cruise, it mean that an airfoil with higher camber would have been better then the current N-63A215, where the 3:d last digit tell the designed CL So it have an airfoil designed for higher speeds, but no meaning to have that, no one cruise at WOT at SL, but most cruise at 65-75% power from 2000´ to 8000 or 12000´
The NACA 6x- series isn’t the best with today standard, rumour says that the NACA screwed up when publishing these new airfoils with a faulty design that they could not take back.
An Harry Riblett GA-37A315 would be a better choice, it have gentler stall, and will show less drag at both cruise and climb, The difference between Riblett and NACA is that the nose radii is placed correctly on the Riblett. The Riblett will have about 7-8% higher CLmax.
I draw up both airfoils for evaluation and when aligning the portion where main and after spar will be, it is a different of 1 degree at the chord line. (From nose radii to trailing edge)
The NACA is in Green
From the main spar and back there is very little difference in shape, meaning the lift at same angle will be about the same with this difference in angle
The chord line is just a reference line that is convenient to draw and measure, but aerodynamically it is almost a fictive line, the important line or angle of an airfoil is the zero lift angle, from this line the lift is generated if it is given an angle to the relative wind, think of an symmetric airfoil where the zero lift line and chord line is the same, and at alpha zero it will not produce any lift.
An airfoil with camber will produce lift even if the chord line is at alpha zero, or slightly negative, because the zero lift line will have a positive alpha to the wind.
To make a cambered airfoil to produce zero lift, the nose have to be lowered until the zero lift line is parallel to the wind, so an cambered airfoil is said to have a zero lift angle of minus some degree depending of the camber, it can be -1 to -6 degree on common airfoils and camber.
The NACA 63A-215 have a zero lift angle of -1.64 degree, and the Riblett GA-37A315 -2.14 degree.
A difference of 0.50 degree.
The lift slope Cl alpha´ is depending on the wing aspect ratio, for a AR of 6, the slope of the lift curve is CLµ = 2Phi / 1+2/A2 = 2Phi / 1 + 2 / 6 = 4.71239 per radian
Or 4.71239 / 57.3 = 0.08224 per degree
The original wing is 3 degree up from chord line to fuselage reference line, so if we fly it with the reference line horizontal the wing CL is 3 - -1.64 = 4.64 degree a 0,08224 = 0,38 CL.
The GA-37A315 will be 1 degree less measured at the chord line, so 2 - -2.14 = 4.14. so CL with fuselage level will be 0.34
It means that at higher speeds the nose down angle will be 0.5 degree less.
Lets say we cruse at 165 MPH TAS (at) 8000´ and 1450 Lb the CL will be 0.30 plus the fact that the wing have to carry the down force from tail plane. Both airfoils have a negative pitch moment of 0.05, the Riblett just a little more then the NACA due to more camber.
The load at the tail is its moment times the wing chord and area, times dynamic pressure.
Divided with tail length.
It will be about 84-85 lb down force at cruise if CG is at 25% chord
So the wing then will carry 1535 lb or CL 0.32
A CG further back will reduce negative lift and then reduce induced drag. (And reversed.)
1450 lb at after limit will reduce down force at the tail with 10 lb
at forward limit it will ad 35 lb to a total lift the wing have to do of 1570 lb or CL 0.33
A CG to forward and the elevator will not be able to hold the nose up with flaps, to far back and it will be sensitive on the stick. Then we come into:
Nose drop at landing, sounds like ground effect, when closer to ground the down wash from wing is flattened out, meaning the tail will have less down force.
With a horizontal stab area of just a bit over 17% of the wing area, seems small, even if the tail arm is long.
One reason for the elevator not be up to the job can also be the tail incidence, 0.5 - 0.75 degree down might help. (but hard to fix that now)
Seems like, longer elevators chords is a good thing, 1,75” longer chord move the hinge line to 60% chord/40% elevator. (about “normal”)
And VG's, seems to help, it means something is wrong from start, to small elevator or wrong incidence. Or to small H.- tail area or all three.
The Wing – Fuselage fairing should be expanding and 10% of the chord at the trailing edge, according to Raymer, It mean in my eyes it should be 10% of the local chord, so mid chord it is 5% of the total chord length.
I don’t see anyone on Matronics talks about if they sealed the control surface hinge gaps with tape. That will make a big difference. Tape them with Tesa fabric tape on the bottom side of the Hinge line, inside the elevator, inside the rudder, inside the aileron, and bottom of the flap hinge line.
Having them unsealed is like driving with the parking brake on.
On a Kitfox it is the difference of being able to make a 3-point or not with or without sealing the elevator gap.
Jan Carlsson
JC Propeller Design
Ps. Sorry to say, I have never been onboard a KIS.
| - The Matronics KIS-List Email Forum - | | Use the List Feature Navigator to browse the many List utilities available such as the Email Subscriptions page, Archive Search & Download, 7-Day Browse, Chat, FAQ, Photoshare, and much more:
http://www.matronics.com/Navigator?KIS-List |
|
Description: |
|
Filesize: |
91.45 KB |
Viewed: |
20380 Time(s) |

|
Description: |
|
Filesize: |
72.39 KB |
Viewed: |
20380 Time(s) |

|
_________________ www.jcpropellerdesign.com |
|
Back to top |
|
 |
Flyinisfun(at)aol.com Guest
|
Posted: Sat Jan 12, 2013 8:30 pm Post subject: KIS TR-1 Airfoil |
|
|
Jan,
I used a Lyc. 0-320 and in order to compensate for forward weight Rich
suggested I move the tail (as I built) rear 1 1/2" to the rear of the fuselage
shell. I put the 1 1/2" extension to the elevator as suggested and
enlarged the wing fillet. As you've probably seen on this blog the problems I've
expressed landing etc. By moving the tail surfaces rearward, would this
have changed the dianamics of the air foil, lift? As you probably noticed,
I installed VG's on the top of the wing and under the horizontal stab and
it changed the lift situation, lowering the touch-down speed and has even
given me some float down the runway. By taping the hinge line, are you
suggesting this would do what the VG's are doing? Any comment?
TR-1 owner and builer,
Jesse Wright
In a message dated 1/12/2013 1:43:47 P.M. Mountain Standard Time,
propellerdesign(at)tele2.se writes:
KIS TR-1 Airfoil
In the search for information to calculate an optimum propeller for the
KIS I0-240 I found a lot of information and thoughts about its handling
especially during landing.
When picking an airfoil for a airplane project that is about the last
thing to do before the design is set in stone. The wing area is determined in
respect of stall speed with flap arrangement.
When having MTOW, wing aspect ratio and wing area, we can calculate speed
and lift coefficient, CL
The speed we use for this will be where we spend most of the time, not
stall speed and not top speed, but climb and normal cruise speed. So in this
range the airfoil should have the lowest drag, if it was an airliner that
spend most of its time climbing and cruising at high altitude at low
indicated speed it will be at similar CL most of the time (but Mach Nr will play
its roll)
All aircrafts that see any production see an increase in installed power
and weight. If this was in the design of the KIS from start I don’t know,
but the prototype had a Limbach from start if understand it correctly, and
several hundred lbs less weight.
Most seem to have the I0-240B engine installed now and a MTOW of 1450 lb
or so. And it is cruising at around 140 kts. This give an lift coefficient,
of around CL 0.3 at cruise, it mean that an airfoil with higher camber
would have been better then the current N-63A215, where the 3:d last digit tell
the designed CL So it have an airfoil designed for higher speeds, but no
meaning to have that, no one cruise at WOT at SL, but most cruise at 65-75%
power from 2000´ to 8000 or 12000´
The NACA 6x- series isn’t the best with today standard, rumour says
that the NACA screwed up when publishing these new airfoils with a faulty
design that they could not take back.
An Harry Riblett GA-37A315 would be a better choice, it have gentler
stall, and will show less drag at both cruise and climb, The difference between
Riblett and NACA is that the nose radii is placed correctly on the Riblett.
The Riblett will have about 7-8% higher CLmax.
I draw up both airfoils for evaluation and when aligning the portion where
main and after spar will be, it is a different of 1 degree at the chord
line. (From nose radii to trailing edge)
The NACA is in Green
Quote: | From the main spar and back there is very little difference in shape,
meaning the lift at same angle will be about the same with this difference in
|
angle
The chord line is just a reference line that is convenient to draw and
measure, but aerodynamically it is almost a fictive line, the important line
or angle of an airfoil is the zero lift angle, from this line the lift is
generated if it is given an angle to the relative wind, think of an symmetric
airfoil where the zero lift line and chord line is the same, and at alpha
zero it will not produce any lift.
An airfoil with camber will produce lift even if the chord line is at
alpha zero, or slightly negative, because the zero lift line will have a
positive alpha to the wind.
To make a cambered airfoil to produce zero lift, the nose have to be
lowered until the zero lift line is parallel to the wind, so an cambered airfoil
is said to have a zero lift angle of minus some degree depending of the
camber, it can be -1 to -6 degree on common airfoils and camber.
The NACA 63A-215 have a zero lift angle of -1.64 degree, and the Riblett
GA-37A315 -2.14 degree.
A difference of 0.50 degree.
The lift slope Cl alpha´ is depending on the wing aspect ratio, for a AR
of 6, the slope of the lift curve is CLµ = 2Phi / 1+2/A2 = 2Phi / 1 + 2 /
6 = 4.71239 per radian
Or 4.71239 / 57.3 = 0.08224 per degree
The original wing is 3 degree up from chord line to fuselage reference
line, so if we fly it with the reference line horizontal the wing CL is 3 -
-1.64 = 4.64 degree a 0,08224 = 0,38 CL.
The GA-37A315 will be 1 degree less measured at the chord line, so 2 -
-2.14 = 4.14. so CL with fuselage level will be 0.34
It means that at higher speeds the nose down angle will be 0.5 degree less
| - The Matronics KIS-List Email Forum - | | Use the List Feature Navigator to browse the many List utilities available such as the Email Subscriptions page, Archive Search & Download, 7-Day Browse, Chat, FAQ, Photoshare, and much more:
http://www.matronics.com/Navigator?KIS-List |
|
|
|
Back to top |
|
 |
Propellerjan
Joined: 11 Jan 2013 Posts: 21 Location: Sweden
|
Posted: Sat Jan 12, 2013 11:45 pm Post subject: Re: KIS TR-1 Airfoil |
|
|
If the VG's help, it suggest something is wrong from start, it is also reported a difference when using flaps with and without VG's.
So I say the airfoil is wrong or no good, if VG's fix that it is good, but it is no longer a laminar airfoil, so a NACA 23015 (or -13,5 as on RV's) would have been just as good, it have a higher max CL and a lot less Cm ( - moment) If making a new wing, or still building, the GA-37A315 will be great, with lower drag, higher Max CL, same Cm as the N-63A215
There is soft VG's made and sold in Australia.
http://www.stolspeed.com/
It seems that it is not just one plane or pilot that have problem, so it is plane related not pilot.
At the rear end we talk about tail volume, so longer arm and more area give a more stable airplane, by moving the H-stab 1,5 inch you increase tail volume by 1,11%
But increasing the chord by 1,5" it increase with 6%
One thought i got was to (when building) to split and move the elevators out 2" each way, glass in a new part in the middle before cutting the clearance for rudder. then fill the gap between counter balance and stab.
And strengthening the H- spar some.
VH = SH x LH / SW x m.a.c
KIS original..
SH 15,2
SW 88
m.a.c 3,833
LH 11,025
15,2 * 11,025 / 88 * 3,833 = 0.497
+1,5” chord =
16,11 * 11,025 / 88 * 3,833 = 0.526
4” larger span and 1,75” chord =
SH = 2,226´* 7,663= 17,06 sq-ft
17 * 11,025 / 88 * 3,833 = 0,555
1. The tail volume coefficient determines several aspects of airplane performance, the chief of which is the range over which the CG is allowed to move. The magnitude of the number is then driven by several items, including the airfoil section selected by the designer, as well as the type and size of flap you want to consider. Gliders and ultralights do not need a very large CG range since they do not have too much variability in their payload configuration and flaps are minimal or nonexistent.
An airplane like a Cessna 172 on the other hand, has a larger TVC due to the need for a wider range of CG due to the four seats, and capacity of the baggage compartment, and of course the sizable deflection of the Fowler flap.
Historically, for most simple aircraft a TVC of .5 should be considered as the minimum. A value of .7 or more sounds about right for a larger, more capable airplane.
By the late Bill “Orion” Husa.
Because the VG's under the stab helps, it suggest that larger up elevator will not help, the underside of the elevator is probably stalled, It is common to have the H-stab incidence -0,5 - -0,75 degree (nose down) to help with flare in ground effect.
Taping the hinge gap air tight will help, having an mm or two of airstream blowing straight up here will not help anything, but it need to be sealed, the glider plane style convex mylar seal just reduce drag from the gap itself air will still leak under the TE of that seal, air will get in at the ends of the control surface and at the gap opposite of the hinge line.
Drag wise it will not be so noticeable as on a glider with a L/D of 40-50, but many small creaks will end up in a big river.
Jan Carlsson
www.jcpropellerdesign.com
| - The Matronics KIS-List Email Forum - | | Use the List Feature Navigator to browse the many List utilities available such as the Email Subscriptions page, Archive Search & Download, 7-Day Browse, Chat, FAQ, Photoshare, and much more:
http://www.matronics.com/Navigator?KIS-List |
|
_________________ www.jcpropellerdesign.com |
|
Back to top |
|
 |
mantafs(at)earthlink.net Guest
|
Posted: Sun Jan 13, 2013 12:12 pm Post subject: KIS TR-1 Airfoil |
|
|
Hello Galin,
Is your elevator linkage stock as per the plans or modified to allow for more up elevator? I think this modification is very important and may prevent the need for VG's. The stock method had the control tube hit the bottom of the horizontal inside the tail before a reasonable up elevator deflection limit could be reached.
Mark
--
| - The Matronics KIS-List Email Forum - | | Use the List Feature Navigator to browse the many List utilities available such as the Email Subscriptions page, Archive Search & Download, 7-Day Browse, Chat, FAQ, Photoshare, and much more:
http://www.matronics.com/Navigator?KIS-List |
|
|
|
Back to top |
|
 |
galinhdz(at)gmail.com Guest
|
Posted: Sun Jan 13, 2013 7:35 pm Post subject: KIS TR-1 Airfoil |
|
|
As far as I can tell it is stock as per the plans. Maybe that is why the VG's made a significant difference.
�
Galin
On Sun, Jan 13, 2013 at 2:12 PM, Mark Kettering <mantafs(at)earthlink.net (mantafs(at)earthlink.net)> wrote:
[quote]--> KIS-List message posted by: Mark Kettering <mantafs(at)earthlink.net (mantafs(at)earthlink.net)>
Hello Galin,
Is your elevator linkage stock as per the plans or modified to allow for more up elevator? �I think this modification is very important and may prevent the need for VG's. �The stock method had the control tube hit the bottom of the horizontal inside the tail before a reasonable up elevator deflection limit could be reached.
Mark
--
| - The Matronics KIS-List Email Forum - | | Use the List Feature Navigator to browse the many List utilities available such as the Email Subscriptions page, Archive Search & Download, 7-Day Browse, Chat, FAQ, Photoshare, and much more:
http://www.matronics.com/Navigator?KIS-List |
|
|
|
Back to top |
|
 |
Propellerjan
Joined: 11 Jan 2013 Posts: 21 Location: Sweden
|
Posted: Mon Jan 14, 2013 9:26 am Post subject: Re: KIS TR-1 Airfoil |
|
|
I put all data in from the KIS, with airfoil data, and the KIS handbook from Norway using the original size of H-stab and elevator, and Hans Christan's forward and most after CG load example into Neil Willford's excellent excel spreads.
the CG ended up exactly the same as in Hans Christan's book, good work both of them.
with 5" stick travel (what is original layout?) I got little over the 4,4 lb/g recommended as minimum, for this 4,4G aircraft with sticks.
the most forward CG with this setup with flaps was aerodynamically said to be right at the forward limit 18% MAC, in ground effect and with flaps, so no margins there. All dimensions for the H-stab and elevator is at the lower recommended numbers, both the Tail volume Nr's with Fwd and rear CG Tv=0,49-0,50 ( 0,5 is recommended for single seat or 2-seat without flap, 0,7 for four seat, and 0,6 for 2-seat with flaps)
I then increased the H-tail to 17 sq/ft and elevator percent to 40% of the tail chord, this moved the most forward CG limit possible to 16,2% MAC in ground effect and with flaps, and stick force gradient up to about 6 lb/g
Aileron stick force with +- 12 deg. was something like 36 lb, also with 5" travel each way. sounds heavy to me, but is what we can expect from those plates.
So much for theory, but it agree with what you guys learned from flying the KIS. and the agreement was highly surprising but rewarding
it need bigger elevator and tail volume.
Anyone have the original unmodified stick travel (at top) and yours if modified ?
Jan Carlsson
www.jcpropellerdesign.com
| - The Matronics KIS-List Email Forum - | | Use the List Feature Navigator to browse the many List utilities available such as the Email Subscriptions page, Archive Search & Download, 7-Day Browse, Chat, FAQ, Photoshare, and much more:
http://www.matronics.com/Navigator?KIS-List |
|
_________________ www.jcpropellerdesign.com |
|
Back to top |
|
 |
mantafs(at)earthlink.net Guest
|
Posted: Mon Jan 14, 2013 12:43 pm Post subject: KIS TR-1 Airfoil |
|
|
Quote: | From my calculations when I worked for Tri-R, the elevator push pull tube was undersized for it's length. Then talking with Vance it came up that the up throw was well less than calculated due to contact between the push tube and horizontal. The solution talked about was to put an additional idler well aft in the fuselage and as low as possible and then the most aft tube would no longer contact the horizontal. This would solve two issues at the same time.
|
I also like the idea of increasing the length of the control arm on the elevator and changing the ratio on the current idler. This would reduce the load on the push tube and increase the clearance from the tube to the horizontal.
Mark
--
| - The Matronics KIS-List Email Forum - | | Use the List Feature Navigator to browse the many List utilities available such as the Email Subscriptions page, Archive Search & Download, 7-Day Browse, Chat, FAQ, Photoshare, and much more:
http://www.matronics.com/Navigator?KIS-List |
|
|
|
Back to top |
|
 |
sstearns2(at)yahoo.com Guest
|
Posted: Mon Jan 14, 2013 1:37 pm Post subject: KIS TR-1 Airfoil |
|
|
Another�option would be to make a reducer fitting and transition to a smaller tube for the portion that goes under the horizontal. An ideal push tube is tapered and you only need the full diameter at the center. The fantasy push tube is tapered unidirectional boron fiber.
Can someone post the tube length and diameter/wall thickness and the distance from the LE of the horizontal tail to the point where the tube bolts to the elevator?
Another option is to switch the whole tube to a smaller diameter steel tube. It would be the easiest solution, but it would add some wieght. 3-4 pounds probably.
My forward pitch control tube is 3/4" diameter steel on my much modified TR-1 to minimize the width of the center console.
Scott
From: Mark Kettering <mantafs(at)earthlink.net>
To: kis-list(at)matronics.com
Sent: Monday, January 14, 2013 12:43 PM
Subject: Re: KIS-List: KIS TR-1 Airfoil
--> KIS-List message posted by: Mark Kettering <mantafs(at)earthlink.net (mantafs(at)earthlink.net)>
Quote: | From my calculations when I worked for Tri-R, the elevator push pull tube was undersized for it's length. Then talking with Vance it came up that the up throw was well less than calculated due to contact between the push tube and horizontal. The solution talked about was to put an additional idler well aft in the fuselage and as low as possible and then the most aft tube would no longer contact the horizontal. This would solve two issues at the same time.
|
I also like the idea of increasing the length of the control arm on the elevator and changing the ratio on the current idler. This would reduce the load on the push tube and increase the clearance from the tube to the horizontal.
Mark
--
| - The Matronics KIS-List Email Forum - | | Use the List Feature Navigator to browse the many List utilities available such as the Email Subscriptions page, Archive Search & Download, 7-Day Browse, Chat, FAQ, Photoshare, and much more:
http://www.matronics.com/Navigator?KIS-List |
|
|
|
Back to top |
|
 |
mantafs(at)earthlink.net Guest
|
Posted: Mon Jan 14, 2013 5:49 pm Post subject: KIS TR-1 Airfoil |
|
|
The current aft elevator tube is 6061 T6, 120" long, 1.25" dia, 0.065" wall with a margin of safety of -0.39. FYI, the forward steel tube is 4130, 51.25" long, 0.74" dia, 0.035" wall with a margin of safety of -0.35. The margin of safety must be positive to be safe.
Steel or aluminum is a wash for weight to stiffness ratio. But for the long elevator tube to be 1" dia steel it would need to be 0.075 wall or thicker. This would make it over 6 times more heavy than the aluminum tube (about 10 lbs more) and only give you 0.125" more clearance on the horizontal. Diameter really helps for tube compression buckling resistance.
Using two tubes really reduces the load. If 2 tubes were used and they were each 60" long they could be 6061 T6, 1" dia, 0.058" wall and still have a 0.11 margin of safety.
As Scott said, double tapered would really help.
I think the most simple solution is to increase the length of the rudder control horn (from 4' to 5") and slightly change the idler ratio (change the long side to 5"). Not only does this increase the clearance but it also reduces the load on the push tube. Still not a positive margin but only about half as negative.
Mark
--
| - The Matronics KIS-List Email Forum - | | Use the List Feature Navigator to browse the many List utilities available such as the Email Subscriptions page, Archive Search & Download, 7-Day Browse, Chat, FAQ, Photoshare, and much more:
http://www.matronics.com/Navigator?KIS-List |
|
|
|
Back to top |
|
 |
Flyinisfun(at)aol.com Guest
|
Posted: Mon Jan 14, 2013 6:09 pm Post subject: KIS TR-1 Airfoil |
|
|
This is Jesse,
I built and used the materials that came with the kit. I achieved the
degrees of up elevator called for in the prints. How close the down arm from
the elevator comes to hitting something I don't know now. "I'm surprised
these problems didn't surface before now. Maybe they did and I missed them,
which is it? I'm assuming we're still talking about the TR-1.
In a message dated 1/14/2013 6:49:26 P.M. Mountain Standard Time,
mantafs(at)earthlink.net writes:
The current aft elevator tube is 6061 T6, 120" long, 1.25" dia, 0.065"
wall with a margin of safety of -0.39. FYI, the forward steel tube is 4130,
51.25" long, 0.74" dia, 0.035" wall with a margin of safety of -0.35. The
margin of safety must be positive to be safe.
Steel or aluminum is a wash for weight to stiffness ratio. But for the
long elevator tube to be 1" dia steel it would need to be 0.075 wall or
thicker. This would make it over 6 times more heavy than the aluminum tube
(about 10 lbs more) and only give you 0.125" more clearance on the horizontal.
Diameter really helps for tube compression buckling resistance.
Using two tubes really reduces the load. If 2 tubes were used and they
were each 60" long they could be 6061 T6, 1" dia, 0.058" wall and still have
a 0.11 margin of safety.
As Scott said, double tapered would really help.
I think the most simple solution is to increase the length of the rudder
control horn (from 4' to 5") and slightly change the idler ratio (change the
long side to 5"). Not only does this increase the clearance but it also
reduces the load on the push tube. Still not a positive margin but only
about half as negative.
Mark
--
| - The Matronics KIS-List Email Forum - | | Use the List Feature Navigator to browse the many List utilities available such as the Email Subscriptions page, Archive Search & Download, 7-Day Browse, Chat, FAQ, Photoshare, and much more:
http://www.matronics.com/Navigator?KIS-List |
|
|
|
Back to top |
|
 |
sstearns2(at)yahoo.com Guest
|
Posted: Mon Jan 14, 2013 7:10 pm Post subject: KIS TR-1 Airfoil |
|
|
If a 60" long 1" diameter tube will take the load then just reduce the last 30" of the tube to 1" diameter.
We are talking about the Cruiser right?
Scott
From: Mark Kettering <mantafs(at)earthlink.net>
To: kis-list(at)matronics.com
Sent: Monday, January 14, 2013 5:49 PM
Subject: Re: KIS TR-1 Airfoil
--> KIS-List message posted by: Mark Kettering <mantafs(at)earthlink.net (mantafs(at)earthlink.net)>
The current aft elevator tube is 6061 T6, 120" long, 1.25" dia, 0.065" wall with a margin of safety of -0.39. FYI, the forward steel tube is 4130, 51.25" long, 0.74" dia, 0.035" wall with a margin of safety of -0.35. The margin of safety must be positive to be safe.
Steel or aluminum is a wash for weight to stiffness ratio. But for the long elevator tube to be 1" dia steel it would need to be 0.075 wall or thicker. This would make it over 6 times more heavy than the aluminum tube (about 10 lbs more) and only give you 0.125" more clearance on the horizontal. Diameter really helps for tube compression buckling resistance.
Using two tubes really reduces the load. If 2 tubes were used and they were each 60" long they could be 6061 T6, 1" dia, 0.058" wall and still have a 0.11 margin of safety.
As Scott said, double tapered would really help.
I think the most simple solution is to increase the length of the rudder control horn (from 4' to 5") and slightly change the idler ratio (change the long side to 5"). Not only does this increase the clearance but it also reduces the load on the push tube. Still not a positive margin but only about half as negative.
Mark
--
| - The Matronics KIS-List Email Forum - | | Use the List Feature Navigator to browse the many List utilities available such as the Email Subscriptions page, Archive Search & Download, 7-Day Browse, Chat, FAQ, Photoshare, and much more:
http://www.matronics.com/Navigator?KIS-List |
|
|
|
Back to top |
|
 |
sstearns2(at)yahoo.com Guest
|
Posted: Mon Jan 14, 2013 7:47 pm Post subject: KIS TR-1 Airfoil |
|
|
Hi Jesse,
Mark's numbers are based on part 23 certified airplane loads. Which means a 100 pound push/pull on the control stick. I doubt I have or will ever pull more than 20 pounds on my stick. If I were designing an airplane I would use part 23 control loads, but it probably isn't anything to lose sleep over in our kisi.
Scott
From: "Flyinisfun(at)aol.com" <Flyinisfun(at)aol.com>
To: kis-list(at)matronics.com
Sent: Monday, January 14, 2013 6:08 PM
Subject: Re: KIS TR-1 Airfoil
This is Jesse,
I built and used the materials that came with the kit. I achieved the degrees of up elevator called for in the prints. How close the down arm from the elevator comes to hitting something I don't know now. "I'm surprised these problems didn't surface before now. Maybe they did and I missed them, which is it? I'm assuming we're still talking about the TR-1.
In a message dated 1/14/2013 6:49:26 P.M. Mountain Standard Time, mantafs(at)earthlink.net writes:
[quote]--> KIS-List message posted by: Mark Kettering <mantafs(at)earthlink.net>
The current aft elevator tube is 6061 T6, 120" long, 1.25" dia, 0.065" wall with a margin of safety of -0.39. FYI, the forward steel tube is 4130, 51.25" long, 0.74" dia, 0.035" wall with a margin of safety of -0.35. The margin of safety must be positive to be safe.
Steel or aluminum is a wash for weight to stiffness ratio. But for the long elevator tube to be 1" dia steel it would need to be 0.075 wall or thicker. This would make it over 6 times more heavy than the aluminum tube (about 10 lbs more) and only give you 0.125" more clearance on the horizontal.� Diameter really helps for tube compression buckling resistance.
Using two tubes really reduces the load. If 2 tubes were used and they were each 60" long they could be 6061 T6, 1" dia, 0.058" wall and still have a 0.11 margin of safety.
As Scott said, double tapered would really help.
I think the most simple solution is to increase the length of the rudder control horn (from 4' to 5") and slightly change the idler ratio (change the long side to 5"). Not only does this increase the clearance but it also reduces the load on the push tube. Still not a positive margin but only about half as negative.
Mark
--
| - The Matronics KIS-List Email Forum - | | Use the List Feature Navigator to browse the many List utilities available such as the Email Subscriptions page, Archive Search & Download, 7-Day Browse, Chat, FAQ, Photoshare, and much more:
http://www.matronics.com/Navigator?KIS-List |
|
|
|
Back to top |
|
 |
Flyinisfun(at)aol.com Guest
|
Posted: Mon Jan 14, 2013 7:52 pm Post subject: KIS TR-1 Airfoil |
|
|
Thanks Mark, I'm going to bed and get a good nights sleep.
Jesse
In a message dated 1/14/2013 8:47:24 P.M. Mountain Standard Time, sstearns2(at)yahoo.com writes:
Quote: | Hi Jesse,
Mark's numbers are based on part 23 certified airplane loads.� Which means a 100 pound push/pull on the control stick. I doubt I have or will ever pull more than 20 pounds on my stick. If I were designing an airplane I would use part 23 control loads, but it probably isn't anything to lose sleep over in our kisi.
Scott
From: "Flyinisfun(at)aol.com" <Flyinisfun(at)aol.com>
To: kis-list(at)matronics.com
Sent: Monday, January 14, 2013 6:08 PM
Subject: Re: KIS-List: KIS TR-1 Airfoil
This is Jesse,
I built and used the materials that came with the kit. I achieved the degrees of up elevator called for in the prints. How close the down arm from the elevator comes to hitting something I don't know now. "I'm surprised these problems didn't surface before now. Maybe they did and I missed them, which is it? I'm assuming we're still talking about the TR-1.
In a message dated 1/14/2013 6:49:26 P.M. Mountain Standard Time, mantafs(at)earthlink.net writes:
Quote: | --> KIS-List message posted by: Mark Kettering <mantafs(at)earthlink.net>
The current aft elevator tube is 6061 T6, 120" long, 1.25" dia, 0.065" wall with a margin of safety of -0.39. FYI, the forward steel tube is 4130, 51.25" long, 0.74" dia, 0.035" wall with a margin of safety of -0.35. The margin of safety must be positive to be safe.
Steel or aluminum is a wash for weight to stiffness ratio. But for the long elevator tube to be 1" dia steel it would need to be 0.075 wall or thicker. This would make it over 6 times more heavy than the aluminum tube (about 10 lbs more) and only give you 0.125" more clearance on the horizontal. Diameter really helps for tube compression buckling resistance.
Using two tubes really reduces the load. If 2 tubes were used and they were each 60" long they could be 6061 T6, 1" dia, 0.058" wall and still have a 0.11 margin of safety.
As Scott said, double tapered would really help.
I think the most simple solution is to increase the length of the rudder control horn (from 4' to 5") and slightly change the idler ratio (change the long side to 5"). Not only does this increase the clearance but it also reduces the load on the push tube. Still not a positive margin but only about half as negative.
Mark
-----Original Message-----
From: Scott Stearns
Sent: Jan 14, 2013 4:37 PM
To: "kis-list(at)matronics.com"
Subject: Re: KIS TR-1 Airfoil
Another option would be to make a reducer fitting and transition to a smaller tube for the portion that goes under the horizontal. An ideal push tube is tapered and you only need the full diameter at the center. The fantasy push tube is tapered unidirectional boron fiber. Can someone post the tube length and diameter/wall thickness and the distance from the LE of the horizontal tail to the point where the tube bolts to the elevator? Another option is to switch the whole tube to a smaller diameter steel tube. It would be the easiest solution, but it would add some wieght. 3-4 pounds probably. My
forward pitch control tube is 3/4" diameter steel on my much modified TR-1 to minimize the width of the center console. Scott
From: Mark Kettering <mantafs(at)earthlink.net>
To: kis-list(at)matronics.com
Sent: Monday, January 14, 2013 12:43 PM
Subject: Re: KIS-List:
KIS TR-1 Airfoil
--> KIS-List message posted by: Mark Kettering <mantafs(at)earthlink.net>
Quote: | From my calculations when I worked for Tri-R, the elevator push pull tube was undersized for it's length. Then talking with Vance it came up that the up throw was well less than calculated due to contact between the push tube and horizontal. The solution talked about was to put an additional idler well aft in the fuselage and as low as possible and then the most aft tube would no longer contact the horizontal. This would solve two issues at the same time.
|
I also like the idea of increasing the length of the control arm on the elevator and changing the ratio on the current idler. This would reduce the load on the push tube and increase the clearance from the tube to the horizontal.
Mark
-----Original Message-----
From: Galin Hernandez
Sent: Jan 13, 2013 10:34 PM
To: kis-list(at)matronics.com
Subject: Re: KIS-List: KIS TR-1 Airfoil
As far as I can tell it is stock as per the plans. Maybe that is why the VG's made a significant difference. Galin
On Sun, Jan 13, 2013 at 2:12 PM, Mark Kettering <mantafs(at)earthlink.net> wrote:
--> KIS-List message posted by: Mark Kettering <mantafs(at)earthlink.net>
Hello Galin,
Is your elevator linkage stock as per the plans or modified to allow for more up elevator? I think this modification is very important and may prevent the need for VG's. The stock method had the control tube hit the bottom of
the horizontal inside the tail before a reasonable up elevator deflection limit could be reached.
Mark
-----Original Message-----
From: Galin Hernandez
Sent: Jan 13, 2013 10:20 AM
To: kis-list(at)matronics.com
Subject: Re: KIS TR-1 Airfoil
Jan; What do you mean when you say "Tape them with Tesa fabric tape on the bottom side of the Hinge line, inside the elevator, inside the rudder, inside the aileron, and bottom of the flap hinge line." Can you provide a photo of what you mean? This sounds like a viable option for those of us that have flying airplanes and can't re-work the wing/tail.
I used the VG's from Stolspeed.com on the elevator and they
made a significant improvement while landing my TR-4.
GalinN819PR
On Fri, Jan 11, 2013 at 4:36 PM, Propellerjan <propellerdesign(at)tele2.se> wrote:
--> KIS-List message posted by: "Propellerjan" <propellerdesign(at)tele2.se>
KIS TR-1 Airfoil
In the search for information to calculate an optimum propeller for the KIS I0-240 I found a lot of information and thoughts about its handling especially during landing.
When picking an airfoil for a airplane project that is about the last thing to do before the design is set in stone. The wing area is determined in respect of stall speed with flap arrangement.
When
having MTOW, wing aspect ratio and wing area, we can calculate speed and lift coefficient, CL
The speed we use for this will be where we spend most of the time, not stall speed and not top speed, but climb and normal cruise speed. So in this range the airfoil should have the lowest drag, if it was an airliner that spend most of its time climbing and cruising at high altitude at low indicated speed it will be at similar CL most of the time (but Mach Nr will play its roll)
All aircrafts that see any production see an increase in installed power and weight. If this was in the design of the KIS from start I don’t know, but the prototype had a Limbach from start if understand it correctly, and several hundred lbs less weight.
Most seem to have the I0-240B engine installed now and a MTOW of 1450 lb or so. And it is
cruising at around 140 kts. This give an lift coefficient, of around CL 0.3 at cruise, it mean that an airfoil with higher camber would have been better then the current N-63A215, where the 3:d last digit tell the designed CL So it have an airfoil designed for higher speeds, but no meaning to have that, no one cruise at WOT at SL, but most cruise at 65-75% power from 2000´ to 8000 or 12000´
The NACA 6x- series isn’t the best with today standard, rumour says that the NACA screwed up when publishing these new airfoils with a faulty design that they could not take back.
An Harry Riblett GA-37A315 would be a better choice, it have gentler stall, and will show less drag at both cruise and climb, The difference between Riblett and NACA is that the nose radii is placed correctly on the Riblett. The Riblett will have about 7-8% higher
CLmax.
I draw up both airfoils for evaluation and when aligning the portion where main and after spar will be, it is a different of 1 degree at the chord line. (>From nose radii to trailing edge)
The NACA is in Green
Quote: | From the main spar and back there is very little difference in shape, meaning the lift at same angle will be about the same with this difference in angle
|
The chord line is just a reference line that is convenient to draw and measure, but aerodynamically it is almost a fictive line, the important line or angle of an airfoil is the zero lift angle, from this line the lift is generated if it is given an angle to the relative wind, think of an symmetric airfoil where the zero lift line and chord line is the same, and at alpha zero it will not produce any
lift.
An airfoil with camber will produce lift even if the chord line is at alpha zero, or slightly negative, because the zero lift line will have a positive alpha to the wind.
To make a cambered airfoil to produce zero lift, the nose have to be lowered until the zero lift line is parallel to the wind, so an cambered airfoil is said to have a zero lift angle of minus some degree depending of the camber, it can be -1 to -6 degree on common airfoils and camber.
The NACA 63A-215 have a zero lift angle of -1.64 degree, and the Riblett GA-37A315 -2.14 degree.
A difference of 0.50 degree.
The lift slope Cl alpha´ is depending on the wing aspect ratio, for a AR of 6, the slope of the lift curve is CLµ = 2Phi / 1+2/A2 = 2Phi / 1 + 2 / 6 = 4.71239 per radian
Or
4.71239 / 57.3 = 0.08224 per degree
The original wing is 3 degree up from chord line to fuselage reference line, so if we fly it with the reference line horizontal the wing CL is 3 - -1.64 = 4.64 degree a 0,08224 = 0,38 CL.
The GA-37A315 will be 1 degree less measured at the chord line, so 2 - -2.14 = 4.14. so CL with fuselage level will be 0.34
It means that at higher speeds the nose down angle will be 0.5 degree less.
Lets say we cruse at 165 MPH TAS (at) 8000´ and 1450 Lb the CL will be 0.30 plus the fact that the wing have to carry the down force from tail plane. Both airfoils have a negative pitch moment of 0.05, the Riblett just a little more then the NACA due to more camber.
The load at the tail is its moment times the wing chord and area, times dynamic pressure.
Divided with
tail length.
It will be about 84-85 lb down force at cruise if CG is at 25% chord
So the wing then will carry 1535 lb or CL 0.32
A CG further back will reduce negative lift and then reduce induced drag. (And reversed.)
1450 lb at after limit will reduce down force at the tail with 10 lb
at forward limit it will ad 35 lb to a total lift the wing have to do of 1570 lb or CL 0.33
A CG to forward and the elevator will not be able to hold the nose up with flaps, to far back and it will be sensitive on the stick. Then we come into:
Nose drop at landing, sounds like ground effect, when closer to ground the down wash from wing is flattened out, meaning the tail will have less down force.
With a horizontal stab area of just a bit over 17% of the wing area, seems small, even if the tail arm
is long.
One reason for the elevator not be up to the job can also be the tail incidence, 0.5 - 0.75 degree down might help. (but hard to fix that now)
Seems like, longer elevators chords is a good thing, 1,75” longer chord move the hinge line to 60% chord/40% elevator. (about “normal”)
And VG's, seems to help, it means something is wrong from start, to small elevator or wrong incidence. Or to small H.- tail area or all three.
The Wing – Fuselage fairing should be expanding and 10% of the chord at the trailing edge, according to Raymer, It mean in my eyes it should be 10% of the local chord, so mid chord it is 5% of the total chord length.
I don’t see anyone on Matronics talks about if they sealed the control surface hinge gaps with tape. That will make a big difference. Tape them with Tesa fabric tape
on the bottom side of the Hinge line, inside the elevator, inside the rudder, inside the aileron, and bottom of the flap hinge line.
Having them unsealed is like driving with the parking brake on.
On a Kitfox it is the difference of being able to make a 3-point or not with or without sealing the elevator gap.
Jan Carlsson
JC Propeller Design
Ps. Sorry to say, I have never been onboard a KIS.
--------
www.jcpropellerdesign.com
Read this topic online here:
http://forums.matronics.com/viewtopic.php?p=392088#392088
Attachments:
http://forums.matronics.com//files/63a215_37a315_le_rad_133.jpg
http://forums.matronics.com//files/63a215_37a315_184.jpg
===========
rget="_blank">http://www.matronics.com/Navigator?KIS-List
===========
http://forums.matronics.com/
===========
le, List
Admin.
="_blank">http://www.matronics.com/contribution
===========
===========
rget="_blank">http://www.matronics.com/Navigator?KIS-List
===========
http://forums.matronics.com/
===========
le, List Admin.
="_blank">http://www.matronics.com/contribution
===========
="" http://www.======================
ies ay - MATRONICS WEB FORUMS - List Contribution Web Site p; �
|
Quote: | http://www.matronics.com/Navigator?KISom/" rel="nofollow" target="_blank">http://forums.matronics.com/
ef="http://www.matronics.com/contribution" rel="nofollow" target="_bl==
="http://www.matronics.com/Navigator?KIS-List">http://www.matronics.com/Navigator?KIS-List
s.matronics.com/">http://forums.matronics.com
p://www.matronics.com/contribution">http://www.matronics.com/contribution
|
|
[quote][b]
| - The Matronics KIS-List Email Forum - | | Use the List Feature Navigator to browse the many List utilities available such as the Email Subscriptions page, Archive Search & Download, 7-Day Browse, Chat, FAQ, Photoshare, and much more:
http://www.matronics.com/Navigator?KIS-List |
|
|
|
Back to top |
|
 |
mantafs(at)earthlink.net Guest
|
Posted: Tue Jan 15, 2013 5:53 am Post subject: KIS TR-1 Airfoil |
|
|
I am talking about the TR-4. The control parts on the TR-1 all have a positive margin of safety. Also due to the smaller horizontal and different geometry there is much less (if at all) of an elevator deflection problem on the TR-1.
Mark
--
| - The Matronics KIS-List Email Forum - | | Use the List Feature Navigator to browse the many List utilities available such as the Email Subscriptions page, Archive Search & Download, 7-Day Browse, Chat, FAQ, Photoshare, and much more:
http://www.matronics.com/Navigator?KIS-List |
|
|
|
Back to top |
|
 |
Propellerjan
Joined: 11 Jan 2013 Posts: 21 Location: Sweden
|
Posted: Tue Jan 15, 2013 6:58 am Post subject: Re: KIS TR-1 Airfoil |
|
|
I made this spread on push rod strenght couple of years ago, had a engineer looking it over, but I used 167 lb at stick instead of 100, over kill i say. just put your data in, force, stick length, gear ratio, idler arm lengths .. tube diameter and wall thickness, the strenght data is for 6061 tube. it will automatic pick the right formula if it is short or long, buckling or not.
Jan
| - The Matronics KIS-List Email Forum - | | Use the List Feature Navigator to browse the many List utilities available such as the Email Subscriptions page, Archive Search & Download, 7-Day Browse, Chat, FAQ, Photoshare, and much more:
http://www.matronics.com/Navigator?KIS-List |
|
Description: |
|
 Download |
Filename: |
Jans Push Tube.xls |
Filesize: |
86.5 KB |
Downloaded: |
617 Time(s) |
_________________ www.jcpropellerdesign.com |
|
Back to top |
|
 |
mantafs(at)earthlink.net Guest
|
Posted: Tue Jan 15, 2013 8:02 am Post subject: KIS TR-1 Airfoil |
|
|
Was there an attached file? If so, I did not receive it.
I use the FAR 23 loads of:
Aileron: 67 lbs
Elevator: 167 lbs
Rudder: 200 lbs
I also calculate the aerodynamic loads using FAR 23 methods. Again the TR-1 met these requirements when I worked for Rich. The aluminum control horn at the center of the flap torque tube on the TR-4 did not meet requirements in a few ways.
Mark
--
| - The Matronics KIS-List Email Forum - | | Use the List Feature Navigator to browse the many List utilities available such as the Email Subscriptions page, Archive Search & Download, 7-Day Browse, Chat, FAQ, Photoshare, and much more:
http://www.matronics.com/Navigator?KIS-List |
|
|
|
Back to top |
|
 |
Propellerjan
Joined: 11 Jan 2013 Posts: 21 Location: Sweden
|
Posted: Tue Jan 15, 2013 8:11 am Post subject: Re: KIS TR-1 Airfoil |
|
|
It is here, on the forum. do you read this in e-mail or on the forum
http://forums.matronics.com/viewtopic.php?t=95809
it is on the right hand side, say down load.
Jan
| - The Matronics KIS-List Email Forum - | | Use the List Feature Navigator to browse the many List utilities available such as the Email Subscriptions page, Archive Search & Download, 7-Day Browse, Chat, FAQ, Photoshare, and much more:
http://www.matronics.com/Navigator?KIS-List |
|
_________________ www.jcpropellerdesign.com
Last edited by Propellerjan on Tue Jan 15, 2013 8:20 am; edited 1 time in total |
|
Back to top |
|
 |
Propellerjan
Joined: 11 Jan 2013 Posts: 21 Location: Sweden
|
Posted: Tue Jan 15, 2013 8:19 am Post subject: Re: KIS TR-1 Airfoil |
|
|
I tried to understand the FAR 23.
there is A a and b, max and min.
as I understand it use max if the aerodynamic load is giving larger loads.
then you can not pull any harder then 167 in elevator.
and use min if the aerodynamic load is lower, with smaller loads on the control surface use b, others it will not take ground handling and transport loads,
then there is also the gust load from the rear on ground.
Jan
| - The Matronics KIS-List Email Forum - | | Use the List Feature Navigator to browse the many List utilities available such as the Email Subscriptions page, Archive Search & Download, 7-Day Browse, Chat, FAQ, Photoshare, and much more:
http://www.matronics.com/Navigator?KIS-List |
|
_________________ www.jcpropellerdesign.com |
|
Back to top |
|
 |
sstearns2(at)yahoo.com Guest
|
Posted: Tue Jan 15, 2013 8:59 am Post subject: KIS TR-1 Airfoil |
|
|
Is it not a range of loads?
It looks to me like
Elevator 100-167 lbs
Aileron 40-67 lbs
Rudder 200-150 lbs
I don't think either airplane would take 200 or even 150 lbs on each rudder pedal. Even with the extra structure I added I am sure the bellcrank would tear off the rear bulkhead with 150 lbs on each pedal.
Scott
From: Mark Kettering <mantafs(at)earthlink.net>
To: kis-list(at)matronics.com
Sent: Tuesday, January 15, 2013 8:01 AM
Subject: Re: Re: KIS TR-1 Airfoil
--> KIS-List message posted by: Mark Kettering <mantafs(at)earthlink.net (mantafs(at)earthlink.net)>
Was there an attached file? If so, I did not receive it.
I use the FAR 23 loads of:
Aileron: 67 lbs
Elevator: 167 lbs
Rudder: 200 lbs
I also calculate the aerodynamic loads using FAR 23 methods. Again the TR-1 met these requirements when I worked for Rich. The aluminum control horn at the center of the flap torque tube on the TR-4 did not meet requirements in a few ways.
Mark
--
| - The Matronics KIS-List Email Forum - | | Use the List Feature Navigator to browse the many List utilities available such as the Email Subscriptions page, Archive Search & Download, 7-Day Browse, Chat, FAQ, Photoshare, and much more:
http://www.matronics.com/Navigator?KIS-List |
|
|
|
Back to top |
|
 |
Propellerjan
Joined: 11 Jan 2013 Posts: 21 Location: Sweden
|
Posted: Tue Jan 15, 2013 9:10 am Post subject: Re: KIS TR-1 Airfoil |
|
|
Yes a range of aloud ables.
as I understand it, if the in case of elevator the air load will give a stick load of 200 use 167, if it is 120, use 120, if it is 90 use 100.?
Jan
| - The Matronics KIS-List Email Forum - | | Use the List Feature Navigator to browse the many List utilities available such as the Email Subscriptions page, Archive Search & Download, 7-Day Browse, Chat, FAQ, Photoshare, and much more:
http://www.matronics.com/Navigator?KIS-List |
|
_________________ www.jcpropellerdesign.com |
|
Back to top |
|
 |
|
|
You cannot post new topics in this forum You cannot reply to topics in this forum You cannot edit your posts in this forum You cannot delete your posts in this forum You cannot vote in polls in this forum You cannot attach files in this forum You can download files in this forum
|
Powered by phpBB © 2001, 2005 phpBB Group
|