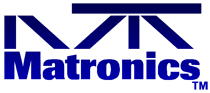 |
Matronics Email Lists Web Forum Interface to the Matronics Email Lists
|
View previous topic :: View next topic |
Author |
Message |
nuckolls.bob(at)aeroelect Guest
|
Posted: Wed Apr 03, 2013 9:34 am Post subject: heat treat problem |
|
|
I've got a project that hit a bit of a snag. I'm
building a recovery parachute control system that
uses a t-handle to deploy the parachute. I found
a really handy size T-handle in McMaster-Carr
and proceed with my endeavors.
One of the last operations during assembly called for
cutting the shaft of the t-handle to length and then
drilling a 3/16" hole in the last 1/2". The hole
accepts a roll-pin that runs in the slot on a guide
collar to set stroke of the handle and to restrain
rotation.
[img]cid:.0[/img]
When I cut the shaft with an abrasive cut-off wheel, the
it turned out to bet harder than the hubs-of-you-know-what.
It's the right length but now I need to drill the hole. No
chance with any tools I have.
I think I recall that steel can be heated to some pretty
ordinary temperatures (less than incandescent) and cooled
slowly to remove the heat treat. Strength in this area is
very un-critical. I can put a thermocouple on it and heat
with a torch. I've browsed some heat-treat documents
but the without some time consuming study, no immediate
notions of process jumped out. I need to soften this part
so that I can drill it with ordinary high-speed drills.
Are there any folks on the list with some practical experience
in this area? Hoping to deliver this thing tomorrow but
it ain't gonna happen without the pin installed. Any
suggestions from the List?
Bob . . .
| - The Matronics AeroElectric-List Email Forum - | | Use the List Feature Navigator to browse the many List utilities available such as the Email Subscriptions page, Archive Search & Download, 7-Day Browse, Chat, FAQ, Photoshare, and much more:
http://www.matronics.com/Navigator?AeroElectric-List |
|
Description: |
|
Filesize: |
142.22 KB |
Viewed: |
8392 Time(s) |
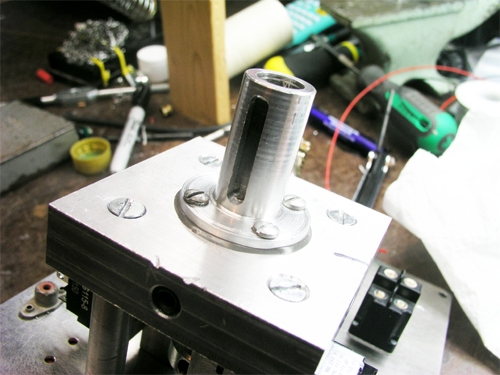
|
|
|
Back to top |
|
 |
racerjerry
Joined: 15 Dec 2009 Posts: 202 Location: Deer Park, NY
|
Posted: Wed Apr 03, 2013 9:43 am Post subject: Re: heat treat problem |
|
|
EDM aka Electrical Discharge Machining. Google it for a machine shop that has that capability in your area. EDM easily penetrates any conductive material.
Good luck, Bob
P.S. You would need to locate a RAM type (plunge) EDM setup as opposed to a wire type EDM machine if you intend to go this route.
| - The Matronics AeroElectric-List Email Forum - | | Use the List Feature Navigator to browse the many List utilities available such as the Email Subscriptions page, Archive Search & Download, 7-Day Browse, Chat, FAQ, Photoshare, and much more:
http://www.matronics.com/Navigator?AeroElectric-List |
|
_________________ Jerry King
Last edited by racerjerry on Wed Apr 03, 2013 9:57 am; edited 1 time in total |
|
Back to top |
|
 |
klehman(at)albedo.net Guest
|
Posted: Wed Apr 03, 2013 9:43 am Post subject: heat treat problem |
|
|
I don't do a lot of this but if it is carbon steel just heat it up to a
nice red color and air cool it. The hardening only occurs if it is shock
cooled in oil or water or the attached heat sink is relatively massive.
A room temperature slow cool should take out the hardness.
A good carbide masonry bit running slow will sometimes go through pretty
hard steel. A hardware store cobalt bit is dramatically better than an
High Speed Steel bit.
Ken
Quote: |
<nuckolls.bob(at)aeroelectric.com>
|
Quote: |
I've got a project that hit a bit of a snag. I'm
building a recovery parachute control system that
uses a t-handle to deploy the parachute. I found
a really handy size T-handle in McMaster-Carr
and proceed with my endeavors.
One of the last operations during assembly called for
cutting the shaft of the t-handle to length and then
drilling a 3/16" hole in the last 1/2". The hole
accepts a roll-pin that runs in the slot on a guide
collar to set stroke of the handle and to restrain
rotation.
Emacs!
When I cut the shaft with an abrasive cut-off wheel, the
it turned out to bet harder than the hubs-of-you-know-what.
It's the right length but now I need to drill the hole. No
chance with any tools I have.
I think I recall that steel can be heated to some pretty
ordinary temperatures (less than incandescent) and cooled
slowly to remove the heat treat. Strength in this area is
very un-critical. I can put a thermocouple on it and heat
with a torch. I've browsed some heat-treat documents
but the without some time consuming study, no immediate
notions of process jumped out. I need to soften this part
so that I can drill it with ordinary high-speed drills.
Are there any folks on the list with some practical experience
in this area? Hoping to deliver this thing tomorrow but
it ain't gonna happen without the pin installed. Any
suggestions from the List?
Bob . . .
|
| - The Matronics AeroElectric-List Email Forum - | | Use the List Feature Navigator to browse the many List utilities available such as the Email Subscriptions page, Archive Search & Download, 7-Day Browse, Chat, FAQ, Photoshare, and much more:
http://www.matronics.com/Navigator?AeroElectric-List |
|
|
|
Back to top |
|
 |
csmale(at)bak.rr.com Guest
|
Posted: Wed Apr 03, 2013 10:02 am Post subject: heat treat problem |
|
|
| - The Matronics AeroElectric-List Email Forum - | | Use the List Feature Navigator to browse the many List utilities available such as the Email Subscriptions page, Archive Search & Download, 7-Day Browse, Chat, FAQ, Photoshare, and much more:
http://www.matronics.com/Navigator?AeroElectric-List |
|
|
|
Back to top |
|
 |
rv7a.builder(at)yahoo.com Guest
|
Posted: Wed Apr 03, 2013 10:20 am Post subject: heat treat problem |
|
|
Is EDM an option?
From: "Robert L. Nuckolls, III" <nuckolls.bob(at)aeroelectric.com>
To: aeroelectric-list(at)matronics.com
Sent: Wednesday, April 3, 2013 10:32 AM
Subject: heat treat problem
I've got a project that hit a bit of a snag. I'm
building a recovery parachute control system that
uses a t-handle to deploy the parachute. I found
a really handy size T-handle in McMaster-Carr
and proceed with my endeavors.
One of the last operations during assembly called for
cutting the shaft of the t-handle to length and then
drilling a 3/16" hole in the last 1/2". The hole
accepts a roll-pin that runs in the slot on a guide
collar to set stroke of the handle and to restrain
rotation.
[img]cid:1.2922996926(at)web163601.mail.gq1.yahoo.com[/img]
When I cut the shaft with an abrasive cut-off wheel, the
it turned out to bet harder than the hubs-of-you-know-what.
It's the right length but now I need to drill the hole. No
chance with any tools I have.
I think I recall that steel can be heated to some pretty
ordinary temperatures (less than incandescent) and cooled
slowly to remove the heat treat. Strength in this area is
very un-critical. I can put a thermocouple on it and heat
with a torch. I've browsed some heat-treat documents
but the without some time consuming study, no immediate
notions of process jumped out. I need to soften this part
so that I can drill it with ordinary high-speed drills.
Are there any folks on the list with some practical experience
in this area? Hoping to deliver this thing tomorrow but
it ain't gonna happen without the pin installed. Any
suggestions from the List?
Bob . . .
| - The Matronics AeroElectric-List Email Forum - | | Use the List Feature Navigator to browse the many List utilities available such as the Email Subscriptions page, Archive Search & Download, 7-Day Browse, Chat, FAQ, Photoshare, and much more:
http://www.matronics.com/Navigator?AeroElectric-List |
|
Description: |
|
Filesize: |
142.22 KB |
Viewed: |
8381 Time(s) |
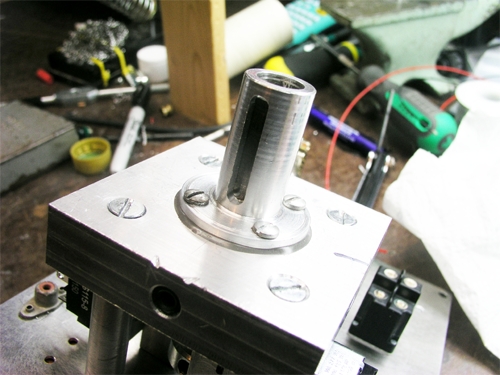
|
|
|
Back to top |
|
 |
Mark(at)wessonair.com Guest
|
Posted: Wed Apr 03, 2013 10:47 am Post subject: heat treat problem |
|
|
There are many people that will say duh, but there may be a few that will
later thank me.
I have heard many complain about drilling the stainless firewall and taking
an hour and one drill bit per hole.
I will share what I learned the hard way.
I am able to drill the stainless in less that one minute and not dull a bit.
It is all about removing heat from the drill bit and the part you are
drilling.
If you use a high speed and it doesn't cut it will burn up the bit.
In order to remove the heat you need to have chips flying.
Aluminum is soft so the 4000rpm air drills we use work fine.
The chips are a flying carring the heat away.
For harder metals you need to increase the pressure and slow the bit down
until the chips fly.
It is as easy as that. Slow the drill speed down and increase the pressure
until the heat is removed by flying metal chips.
Now I have not tried anything too hard since I learned this but I sure have
made butter out of the stainless that other people complain about.
Mark W
| - The Matronics AeroElectric-List Email Forum - | | Use the List Feature Navigator to browse the many List utilities available such as the Email Subscriptions page, Archive Search & Download, 7-Day Browse, Chat, FAQ, Photoshare, and much more:
http://www.matronics.com/Navigator?AeroElectric-List |
|
|
|
Back to top |
|
 |
BobsV35B(at)aol.com Guest
|
Posted: Wed Apr 03, 2013 10:52 am Post subject: heat treat problem |
|
|
Good Afternoon Bob,
Maybe this will jog a few memories.
Back when I was in High School (Seventy Years Ago) My shop teacher taught us how to make great hunting knives out of worn out files, We heated them with an acetylene torch to bright red then stuck them into some sort of powder to cool. Once they had cooled they were very easy to grind to the knife shape.
We then heated them back up again and quenched them in a light oil to harden the edge.
My thought is that the powder we slow cooled them in was ordinary baking flour. Anyone know for sure?
I am also fuzzy on just what liquid we used for the quick cool. May have been something other than light oil. All very far back in my faulty memory, but maybe that will jog some one else's memory. Worked like a champ to turn those files in hunting knives.
Happy Skies,
Old Bob
In a message dated 4/3/2013 1:13:38 P.M. Central Daylight Time, nuckolls.bob(at)aeroelectric.com writes:
Quote: | I've got a project that hit a bit of a snag. I'm
building a recovery parachute control system that
uses a t-handle to deploy the parachute. I found
a really handy size T-handle in McMaster-Carr
and proceed with my endeavors.
One of the last operations during assembly called for
cutting the shaft of the t-handle to length and then
drilling a 3/16" hole in the last 1/2". The hole
accepts a roll-pin that runs in the slot on a guide
collar to set stroke of the handle and to restrain
rotation.
When I cut the shaft with an abrasive cut-off wheel, the
it turned out to bet harder than the hubs-of-you-know-what.
It's the right length but now I need to drill the hole. No
chance with any tools I have.
I think I recall that steel can be heated to some pretty
ordinary temperatures (less than incandescent) and cooled
slowly to remove the heat treat. Strength in this area is
very un-critical. I can put a thermocouple on it and heat
with a torch. I've browsed some heat-treat documents
but the without some time consuming study, no immediate
notions of process jumped out. I need to soften this part
so that I can drill it with ordinary high-speed drills.
Are there any folks on the list with some practical experience
in this area? Hoping to deliver this thing tomorrow but
it ain't gonna happen without the pin installed. Any
suggestions from the List?
Bob . . . |
| - The Matronics AeroElectric-List Email Forum - | | Use the List Feature Navigator to browse the many List utilities available such as the Email Subscriptions page, Archive Search & Download, 7-Day Browse, Chat, FAQ, Photoshare, and much more:
http://www.matronics.com/Navigator?AeroElectric-List |
|
Description: |
|
Filesize: |
142.22 KB |
Viewed: |
8379 Time(s) |
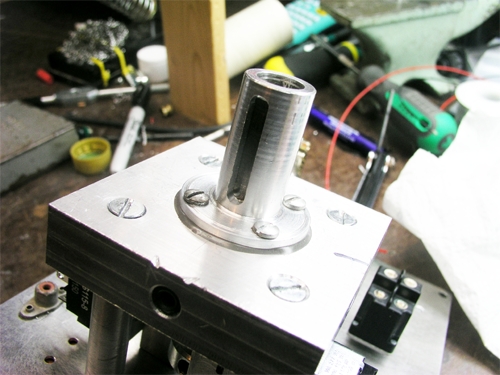
|
|
|
Back to top |
|
 |
N20DG
Joined: 02 Jan 2008 Posts: 61 Location: lancaster, texas
|
Posted: Wed Apr 03, 2013 11:00 am Post subject: heat treat problem |
|
|
Old Bob
Probably that far back in our high school days it was sand any how that is what my dad taught me to use when converting the worn out file to something useful
Older Dick
In a message dated 4/3/2013 1:54:16 P.M. Central Daylight Time, BobsV35B(at)aol.com writes:
Quote: | Good Afternoon Bob,
Maybe this will jog a few memories.
Back when I was in High School (Seventy Years Ago) My shop teacher taught us how to make great hunting knives out of worn out files, We heated them with an acetylene torch to bright red then stuck them into some sort of powder to cool. Once they had cooled they were very easy to grind to the knife shape.
We then heated them back up again and quenched them in a light oil to harden the edge.
My thought is that the powder we slow cooled them in was ordinary baking flour. Anyone know for sure?
I am also fuzzy on just what liquid we used for the quick cool. May have been something other than light oil. All very far back in my faulty memory, but maybe that will jog some one else's memory. Worked like a champ to turn those files in hunting knives.
Happy Skies,
Old Bob
In a message dated 4/3/2013 1:13:38 P.M. Central Daylight Time, nuckolls.bob(at)aeroelectric.com writes:
Quote: | I've got a project that hit a bit of a snag. I'm
building a recovery parachute control system that
uses a t-handle to deploy the parachute. I found
a really handy size T-handle in McMaster-Carr
and proceed with my endeavors.
One of the last operations during assembly called for
cutting the shaft of the t-handle to length and then
drilling a 3/16" hole in the last 1/2". The hole
accepts a roll-pin that runs in the slot on a guide
collar to set stroke of the handle and to restrain
rotation.
When I cut the shaft with an abrasive cut-off wheel, the
it turned out to bet harder than the hubs-of-you-know-what.
It's the right length but now I need to drill the hole. No
chance with any tools I have.
I think I recall that steel can be heated to some pretty
ordinary temperatures (less than incandescent) and cooled
slowly to remove the heat treat. Strength in this area is
very un-critical. I can put a thermocouple on it and heat
with a torch. I've browsed some heat-treat documents
but the without some time consuming study, no immediate
notions of process jumped out. I need to soften this part
so that I can drill it with ordinary high-speed drills.
Are there any folks on the list with some practical experience
in this area? Hoping to deliver this thing tomorrow but
it ain't gonna happen without the pin installed. Any
suggestions from the List?
Bob . . . |
|
| - The Matronics AeroElectric-List Email Forum - | | Use the List Feature Navigator to browse the many List utilities available such as the Email Subscriptions page, Archive Search & Download, 7-Day Browse, Chat, FAQ, Photoshare, and much more:
http://www.matronics.com/Navigator?AeroElectric-List |
|
Description: |
|
Filesize: |
142.22 KB |
Viewed: |
8379 Time(s) |
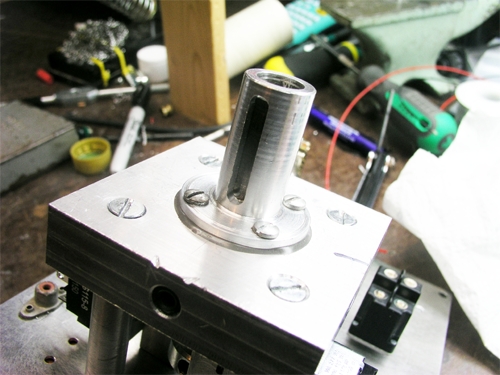
|
|
|
Back to top |
|
 |
billp(at)wwpc.com Guest
|
Posted: Wed Apr 03, 2013 11:26 am Post subject: heat treat problem |
|
|
| - The Matronics AeroElectric-List Email Forum - | | Use the List Feature Navigator to browse the many List utilities available such as the Email Subscriptions page, Archive Search & Download, 7-Day Browse, Chat, FAQ, Photoshare, and much more:
http://www.matronics.com/Navigator?AeroElectric-List |
|
|
|
Back to top |
|
 |
handainc(at)madisoncounty Guest
|
Posted: Wed Apr 03, 2013 11:36 am Post subject: heat treat problem |
|
|
Bob -
If the part is not critical, just heat it up red hot, hold it there for a minute or so, and let it air cool. Here is a fair discussion of the process. http://www.efunda.com/processes/heat_treat/softening/annealing.cfm
Alternatively, a very sharp drill bit, turned very slowly will also work with lots of cooling fluid. I set up my drill press for that very purpose (had to drill some spring steel with out having to re-treat it) by installing a secondary motor with small pulley. Liked it so well that way that I just left it set up. Doesn't do well on soft metals, but is not nearly as hard on drill bits, and works for nearly any type of steel.
M. Haught
On Apr 3, 2013, at 1:51 PM, BobsV35B(at)aol.com (BobsV35B(at)aol.com) wrote:[quote] Good Afternoon Bob,
Maybe this will jog a few memories.
Back when I was in High School (Seventy Years Ago) My shop teacher taught us how to make great hunting knives out of worn out files, We heated them with an acetylene torch to bright red then stuck them into some sort of powder to cool. Once they had cooled they were very easy to grind to the knife shape.
We then heated them back up again and quenched them in a light oil to harden the edge.
My thought is that the powder we slow cooled them in was ordinary baking flour. Anyone know for sure?
I am also fuzzy on just what liquid we used for the quick cool. May have been something other than light oil. All very far back in my faulty memory, but maybe that will jog some one else's memory. Worked like a champ to turn those files in hunting knives.
Happy Skies,
Old Bob
In a message dated 4/3/2013 1:13:38 P.M. Central Daylight Time, nuckolls.bob(at)aeroelectric.com (nuckolls.bob(at)aeroelectric.com) writes:
Quote: | I've got a project that hit a bit of a snag. I'm
building a recovery parachute control system that
uses a t-handle to deploy the parachute. I found
a really handy size T-handle in McMaster-Carr
and proceed with my endeavors.
One of the last operations during assembly called for
cutting the shaft of the t-handle to length and then
drilling a 3/16" hole in the last 1/2". The hole
accepts a roll-pin that runs in the slot on a guide
collar to set stroke of the handle and to restrain
rotation.
<1efc966e.jpg>
When I cut the shaft with an abrasive cut-off wheel, the
it turned out to bet harder than the hubs-of-you-know-what.
It's the right length but now I need to drill the hole. No
chance with any tools I have.
I think I recall that steel can be heated to some pretty
ordinary temperatures (less than incandescent) and cooled
slowly to remove the heat treat. Strength in this area is
very un-critical. I can put a thermocouple on it and heat
with a torch. I've browsed some heat-treat documents
but the without some time consuming study, no immediate
notions of process jumped out. I need to soften this part
so that I can drill it with ordinary high-speed drills.
Are there any folks on the list with some practical experience
in this area? Hoping to deliver this thing tomorrow but
it ain't gonna happen without the pin installed. Any
suggestions from the List?
Bob . . . |
[b]
| - The Matronics AeroElectric-List Email Forum - | | Use the List Feature Navigator to browse the many List utilities available such as the Email Subscriptions page, Archive Search & Download, 7-Day Browse, Chat, FAQ, Photoshare, and much more:
http://www.matronics.com/Navigator?AeroElectric-List |
|
|
|
Back to top |
|
 |
millner(at)me.com Guest
|
Posted: Wed Apr 03, 2013 1:14 pm Post subject: heat treat problem |
|
|
On 4/3/2013 11:51 AM, BobsV35B(at)aol.com (BobsV35B(at)aol.com) wrote:
Quote: | the powder we slow cooled them in was ordinary baking flour. Anyone know for sure? |
Flour is combustible, and if you generate flour dust, explosive... probably not a good thing to put very hot metal objects into.
Paul
[quote][b]
| - The Matronics AeroElectric-List Email Forum - | | Use the List Feature Navigator to browse the many List utilities available such as the Email Subscriptions page, Archive Search & Download, 7-Day Browse, Chat, FAQ, Photoshare, and much more:
http://www.matronics.com/Navigator?AeroElectric-List |
|
|
|
Back to top |
|
 |
raymondj(at)frontiernet.n Guest
|
Posted: Wed Apr 03, 2013 2:36 pm Post subject: heat treat problem |
|
|
| - The Matronics AeroElectric-List Email Forum - | | Use the List Feature Navigator to browse the many List utilities available such as the Email Subscriptions page, Archive Search & Download, 7-Day Browse, Chat, FAQ, Photoshare, and much more:
http://www.matronics.com/Navigator?AeroElectric-List |
|
|
|
Back to top |
|
 |
nuckolls.bob(at)aeroelect Guest
|
Posted: Wed Apr 03, 2013 3:08 pm Post subject: heat treat problem |
|
|
At 02:35 PM 4/3/2013, you wrote:
Essentially that's what I did.
Quote: | Alternatively, a very sharp drill bit, turned very slowly will also work with lots of cooling fluid. I set up my drill press for that very purpose (had to drill some spring steel with out having to re-treat it) by installing a secondary motor with small pulley. Liked it so well that way that I just left it set up. Doesn't do well on soft metals, but is not nearly as hard on drill bits, and works for nearly any type of steel. |
I tried that earlier but the stuff was so hard
my center punch wouldn't even mark it! Couldn't
get a bit to set still in one spot long enough to
remove any material.
Softening it up worked great.
Bob . . . [quote][b]
| - The Matronics AeroElectric-List Email Forum - | | Use the List Feature Navigator to browse the many List utilities available such as the Email Subscriptions page, Archive Search & Download, 7-Day Browse, Chat, FAQ, Photoshare, and much more:
http://www.matronics.com/Navigator?AeroElectric-List |
|
|
|
Back to top |
|
 |
raymondj(at)frontiernet.n Guest
|
Posted: Wed Apr 03, 2013 3:09 pm Post subject: heat treat problem |
|
|
Based on the old articles I've read about heat treating and tempering it could have been sifted wood ash, or asbestos. Just things I've read about people using. It was probably oil you dipped in to quench.
Quote: | Raymond Julian
Kettle River, MN.
"And you know that I could have me a million more friends,
and all I'd have to lose is my point of view." - John Prine | On 04/03/2013 01:51 PM, BobsV35B(at)aol.com (BobsV35B(at)aol.com) wrote:
Quote: | Good Afternoon Bob,
Maybe this will jog a few memories.
Back when I was in High School (Seventy Years Ago) My shop teacher taught us how to make great hunting knives out of worn out files, We heated them with an acetylene torch to bright red then stuck them into some sort of powder to cool. Once they had cooled they were very easy to grind to the knife shape.
We then heated them back up again and quenched them in a light oil to harden the edge.
My thought is that the powder we slow cooled them in was ordinary baking flour. Anyone know for sure?
I am also fuzzy on just what liquid we used for the quick cool. May have been something other than light oil. All very far back in my faulty memory, but maybe that will jog some one else's memory. Worked like a champ to turn those files in hunting knives.
Happy Skies,
Old Bob
In a message dated 4/3/2013 1:13:38 P.M. Central Daylight Time, nuckolls.bob(at)aeroelectric.com (nuckolls.bob(at)aeroelectric.com) writes:
Quote: | I've got a project that hit a bit of a snag. I'm
building a recovery parachute control system that
uses a t-handle to deploy the parachute. I found
a really handy size T-handle in McMaster-Carr
and proceed with my endeavors.
One of the last operations during assembly called for
cutting the shaft of the t-handle to length and then
drilling a 3/16" hole in the last 1/2". The hole
accepts a roll-pin that runs in the slot on a guide
collar to set stroke of the handle and to restrain
rotation.
|
|
Image removed
[quote] Quote: |
When I cut the shaft with an abrasive cut-off wheel, the
it turned out to bet harder than the hubs-of-you-know-what.
It's the right length but now I need to drill the hole. No
chance with any tools I have.
I think I recall that steel can be heated to some pretty
ordinary temperatures (less than incandescent) and cooled
slowly to remove the heat treat. Strength in this area is
very un-critical. I can put a thermocouple on it and heat
with a torch. I've browsed some heat-treat documents
but the without some time consuming study, no immediate
notions of process jumped out. I need to soften this part
so that I can drill it with ordinary high-speed drills.
Are there any folks on the list with some practical experience
in this area? Hoping to deliver this thing tomorrow but
it ain't gonna happen without the pin installed. Any
suggestions from the List?
Bob . . . |
[b]
| - The Matronics AeroElectric-List Email Forum - | | Use the List Feature Navigator to browse the many List utilities available such as the Email Subscriptions page, Archive Search & Download, 7-Day Browse, Chat, FAQ, Photoshare, and much more:
http://www.matronics.com/Navigator?AeroElectric-List |
|
|
|
Back to top |
|
 |
|
|
You cannot post new topics in this forum You cannot reply to topics in this forum You cannot edit your posts in this forum You cannot delete your posts in this forum You cannot vote in polls in this forum You cannot attach files in this forum You can download files in this forum
|
Powered by phpBB © 2001, 2005 phpBB Group
|