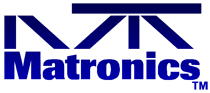 |
Matronics Email Lists Web Forum Interface to the Matronics Email Lists
|
View previous topic :: View next topic |
Author |
Message |
nuckolls.bob(at)aeroelect Guest
|
Posted: Fri Nov 22, 2013 2:03 pm Post subject: A clarification on relay/contactor coil suppression |
|
|
Recent coil suppression discussions on the List have
been tightly focused on a single aspect of suppression
philosophies.
My demonstrated assertions are simply this: For battery
and starter contactors, the use of plain-vanilla junction
diodes for coil suppression is
(1) . . . quite sufficient to the task of reducing
stress on contacts of the controlling device (starter
push button and/or battery switch) and . . .
(2) while it DOES increase release time - time delay
from breaking the coil current until the contacts first open.
I have asserted and demonstrated that this style of protection
does not increase arcing of contacts. It's easy to imagine
that a slowly decaying magnetic field in a relay coil
would promote a sedate spreading velocity of the contacts
and exacerbate any incidence of arcing in the gap.
However, this idea ignores the characteristic of the magnetics
that hold the contacts closed in the first place. In
relays and contactors, the very first motion in a release cycle
widens an AIR GAP in the magnetic circuit that holds
the contacts closed. Any increase in air-gap greatly
attenuates the magnetic's ability to keep a grip on
the armature . . . whether the magnetic field is allowed
to collapse instantly (no suppression), moderately
(fancy suppression) or slowly (el-cheapo suppression)
has only the tiniest effect on contact spreading velocity.
The air gap is a much more powerful influence on
magnetic force than the value of current flowing in the
coil.
Some readers have mis-interpreted my arguments as
being opposed to 'fancy suppression' of relay coil
spikes under any circumstances. This is NOT so. There
are instances where the fancy suppression is useful
if not necessary . . . not so much for management of
arcing at the relay contacts . . . but for achieving
the fastest possible release response while maintaining
a modicum of coil suppression.
A case in point:
The B400 Beechjet has complimentary roll trim
actuators on each wing. These are controlled
and synchronized by an array of 5 relays on this
plug-in ECB assembly.
http://tinyurl.com/m6xwy8v
In this instance, a delayed release would put the
system at risk for destructive fault currents should rapidly
alternating trim commands collide due to slow relay
release. Hence, these relays make good use of the
zener-based coil suppression.
http://tinyurl.com/kvaq6mh
I dug around in my 40+ year collection of $high$
relays and out of a dozen or so examples, only one
had ANY sort of built in coil suppression . . . it
was the one pictured above left over from the Beechjet
relay sticking study.
Oh, by the way, there WAS a contact arcing problem
with these relays that caused them to stick. Interestingly
enough, they would stick due to arc on CLOSURE bounce.
Since the form of coil suppression had no influence on relay
closure it was of no benefit or effect to manage the
arcing.
It took about a year of studies to track down root cause.
Even the folks who manufactured the relays couldn't
figure it out. I spend a goodly amount of my boss's
budget working on various experiments in the basement.
Turns out that root cause was a unique arcing
signature that arose from closing the contacts into
a 30' chunk of shielded wire that ran out into the
wing with far end bypassed by a radio noise suppressor.
Cutting the shield loose from ground (or removing
the noise suppressor - it wasn't needed anyhow) stopped
the sticking. It was the resonant ringing of the shorted
quarter-wave of transmission line that provided unique
arcing signature during the 4-10 bounces of relay
contacts every time they closed.
It has been asserted that 'folks who know what they're
doing' would not think of sticking plain-vanilla
diodes across their relay or contactor coils. A
short search through the catalogs revealed that the
vast majority of relays are offered without suppression
leaving the choice up to the system integrator. MOST
catalog items with suppression installed use plain
vanilla diodes . . . but just about everyone is
willing to offer the diode-zener combo for use in
system where rapid contact release is a design goal.
Unfortunately, many of our brethren are plagued
by the words offered in a poorly authored work on
relay coil suppression . . . from Tyco electronics
no less . . . wherein it is claimed that 'fancy'
coil suppression goes to increased contact life
by shortening the arc on release . . . which simply
isn't true.
I am offering this to solidify my assertions that
there are elegant application opportunities for a
host of coil suppression techniques. Using a zener-diode
combo on the coil of your starter or battery contactor
is not as effective as the single junction diode. By
definition of zener performance, it allows delta-v
across the controlling switch contacts to rise much
higher than for the plain diode but more energy is
dissipated in the zener allowing for faster release.
Since release time is of no consequence for battery
and starter contactors, the plain diode remains the
elegant solution.
Bob . . .
| - The Matronics AeroElectric-List Email Forum - | | Use the List Feature Navigator to browse the many List utilities available such as the Email Subscriptions page, Archive Search & Download, 7-Day Browse, Chat, FAQ, Photoshare, and much more:
http://www.matronics.com/Navigator?AeroElectric-List |
|
|
|
Back to top |
|
 |
jluckey(at)pacbell.net Guest
|
Posted: Fri Nov 22, 2013 2:56 pm Post subject: A clarification on relay/contactor coil suppression |
|
|
Bob N. said:
... Turns out that root cause was a unique arcing
signature that arose from closing the contacts into
a 30' chunk of shielded wire that ran out into the
wing with far end bypassed by a radio noise suppressor.
Cutting the shield loose from ground (or removing
the noise suppressor - it wasn't needed anyhow) stopped
the sticking. It was the resonant ringing of the shorted
quarter-wave of transmission line that provided unique
arcing signature during the 4-10 bounces of relay
contacts every time they closed ...
How the hell did you figure that out? (did it require sacrificing a chicken or a deal with the devil? -- or was it Divine Inspiration?) Sometimes I have to chase down some pretty hairy bugs in software but that arcing problem would have kept me up at night.
Zeners:
Others have suggested the use of a bi-directional Zener. What is the benefit, either theoretical or actual, of using such a device? I'm not clear on what benefit the Zener provides nor do I understand what bi-directional buys you.
(In your answer please speak slowly and use small words;)
Thx,
-Jeff
From: "Robert L. Nuckolls, III" <nuckolls.bob(at)aeroelectric.com>
To: aeroelectric-list(at)matronics.com
Sent: Friday, November 22, 2013 2:02 PM
Subject: A clarification on relay/contactor coil suppression
--> AeroElectric-List message posted by: "Robert L. Nuckolls, III" <nuckolls.bob(at)aeroelectric.com (nuckolls.bob(at)aeroelectric.com)>
Recent coil suppression discussions on the List have
been tightly focused on a single aspect of suppression
philosophies.
My demonstrated assertions are simply this: For battery
and starter contactors, the use of plain-vanilla junction
diodes for coil suppression is
(1) . . . quite sufficient to the task of reducing
stress on contacts of the controlling device (starter
push button and/or battery switch) and . . .
(2) while it DOES increase release time - time delay
from breaking the coil current until the contacts first open.
I have asserted and demonstrated that this style of protection
does not increase arcing of contacts. It's easy to imagine
that a slowly decaying magnetic field in a relay coil
would promote a sedate spreading velocity of the contacts
and exacerbate any incidence of arcing in the gap.
However, this idea ignores the characteristic of the magnetics
that hold the contacts closed in the first place. In
relays and contactors, the very first motion in a release cycle
widens an AIR GAP in the magnetic circuit that holds
the contacts closed. Any increase in air-gap greatly
attenuates the magnetic's ability to keep a grip on
the armature . . . whether the magnetic field is allowed
to collapse instantly (no suppression), moderately
(fancy suppression) or slowly (el-cheapo suppression)
has only the tiniest effect on contact spreading velocity.
The air gap is a much more powerful influence on
magnetic force than the value of current flowing in the
coil.
Some readers have mis-interpreted my arguments as
being opposed to 'fancy suppression' of relay coil
spikes under any circumstances. This is NOT so. There
are instances where the fancy suppression is useful
if not necessary . . . not so much for management of
arcing at the relay contacts . . . but for achieving
the fastest possible release response while maintaining
a modicum of coil suppression.
A case in point:
The B400 Beechjet has complimentary roll trim
actuators on each wing. These are controlled
and synchronized by an array of 5 relays on this
plug-in ECB assembly.
http://tinyurl.com/m6xwy8v
In this instance, a delayed release would put the
system at risk for destructive fault currents should rapidly
alternating trim commands collide due to slow relay
release. Hence, these relays make good use of the
zener-based coil suppression.
http://tinyurl.com/kvaq6mh
I dug around in my 40+ year collection of $high$
relays and out of a dozen or so examples, only one
had ANY sort of built in coil suppression . . . it
was the one pictured above left over from the Beechjet
relay sticking study.
Oh, by the way, there WAS a contact arcing problem
with these relays that caused them to stick. Interestingly
enough, they would stick due to arc on CLOSURE bounce.
Since the form of coil suppression had no influence on relay
closure it was of no benefit or effect to manage the
arcing.
It took about a year of studies to track down root cause.
Even the folks who manufactured the relays couldn't
figure it out. I spend a goodly amount of my boss's
budget working on various experiments in the basement.
Turns out that root cause was a unique arcing
signature that arose from closing the contacts into
a 30' chunk of shielded wire that ran out into the
wing with far end bypassed by a radio noise suppressor.
Cutting the shield loose from ground (or removing
the noise suppressor - it wasn't needed anyhow) stopped
the sticking. It was the resonant ringing of the shorted
quarter-wave of transmission line that provided unique
arcing signature during the 4-10 bounces of relay
contacts every time they closed.
It has been asserted that 'folks who know what they're
doing' would not think of sticking plain-vanilla
diodes across their relay or contactor coils. A
short search through the catalogs revealed that the
vast majority of relays are offered without suppression
leaving the choice up to the system integrator. MOST
catalog items with suppression installed use plain
vanilla diodes . . . but just about everyone is
willing to offer the diode-zener combo for use in
system where rapid contact release is a design goal.
Unfortunately, many of our brethren are plagued
by the words offered in a poorly authored work on
relay coil suppression . . . from Tyco electronics
no less . . . wherein it is claimed that 'fancy'
coil suppression goes to increased contact life
by shortening the arc on release . . . which simply
isn't true.
I am offering this to solidify my assertions that
there are elegant application opportunities for a
host of coil suppression techniques. Using a zener-diode
combo on the coil of your starter or battery contactor
is not as effective as the single junction diode. By
definition of zener performance, it allows delta-v
across the controlling switch contacts to rise much
higher than for the plain diode but more energy is
dissipated in the zener allowing for faster release.
Since release time is of no consequence for battery
and starter contactors, the plain diode remains the
elegant solution.htsp; -========================; <a href="http://www.matronics.com/Navigator?AeroElectric-List" target="http://forums.matronics.com/" =======
| - The Matronics AeroElectric-List Email Forum - | | Use the List Feature Navigator to browse the many List utilities available such as the Email Subscriptions page, Archive Search & Download, 7-Day Browse, Chat, FAQ, Photoshare, and much more:
http://www.matronics.com/Navigator?AeroElectric-List |
|
|
|
Back to top |
|
 |
|
|
You cannot post new topics in this forum You cannot reply to topics in this forum You cannot edit your posts in this forum You cannot delete your posts in this forum You cannot vote in polls in this forum You cannot attach files in this forum You can download files in this forum
|
Powered by phpBB © 2001, 2005 phpBB Group
|