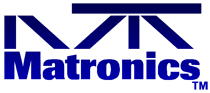 |
Matronics Email Lists Web Forum Interface to the Matronics Email Lists
|
View previous topic :: View next topic |
Author |
Message |
revenson(at)comcast.net Guest
|
Posted: Tue Jan 14, 2014 7:20 am Post subject: Change to Shottky? |
|
|
p { margin: 0; }I wired Z11 with the earlier recommended endurance bus diode w/15 watt heatsink. My loads are 11.5 amps intermittent maximum, 6.1a. typical, and if alternator quits, I could shut things off to get to about 3.3 amps for comfortable endurance use. I see 13.1-13.3 volts on this bus during flight. I have had no issues in 350 hours.
Since completing my RV in 2010, I have been absent from the aeroelectric list. I have noticed that the Shottky diode is now recommended.
Did a search to attempt to 'catch up' with the discussion and have tentatively concluded that this change would be purely optional, and not 'highly recommended' for some electrical reason.
I'm on a weight reduction kick, so my only objective to change to the Shottky would only be to eliminate the 1/2 lb. of the heatsink.
Bob, et al: I'm looking for some assurance. Have I missed something pertinent to this decision or am I on track?
Roger
"For I know the plans I have for you," declares the Lord, "plans to prosper you and not to harm you, plans to give you hope and a future." Jeremiah 29:11
[quote][b]
| - The Matronics AeroElectric-List Email Forum - | | Use the List Feature Navigator to browse the many List utilities available such as the Email Subscriptions page, Archive Search & Download, 7-Day Browse, Chat, FAQ, Photoshare, and much more:
http://www.matronics.com/Navigator?AeroElectric-List |
|
|
|
Back to top |
|
 |
jluckey(at)pacbell.net Guest
|
Posted: Tue Jan 14, 2014 8:50 am Post subject: Change to Shottky? |
|
|
Roger,
The advantage of Schottky diodes is that they have less voltage drop than silicon diodes. Silicon is approx 0.7 volts and Schottky about 0.5 volts. The advantage being that Schottkys dissipate a little less energy.
Using your numbers for typical load:
Existing diode:
P = IE
6 * .7 = 4.2W
Schottky diode:
6 * .5 = 3.0W
I agree w/ your conclusion, probably not worth changing anything for a delta of 1.2W.
-Jeff
From: Roger Evenson <revenson(at)comcast.net>
To: AeroElectric-List(at)matronics.com
Sent: Tuesday, January 14, 2014 7:19 AM
Subject: Change to Shottky?
#yiv1059132124 p {margin:0;}#yiv1059132124 p {margin:0;}I wired Z11 with the earlier recommended endurance bus diode w/15 watt heatsink. My loads are 11.5 amps intermittent maximum, 6.1a. typical, and if alternator quits, I could shut things off to get to about 3.3 amps for comfortable endurance use. I see 13.1-13.3 volts on this bus during flight. I have had no issues in 350 hours.
Since completing my RV in 2010, I have been absent from the aeroelectric list. I have noticed that the Shottky diode is now recommended.
Did a search to attempt to 'catch up' with the discussion and have tentatively concluded that this change would be purely optional, and not 'highly recommended' for some electrical reason.
I'm on a weight reduction kick, so my only objective to change to the Shottky would only be to eliminate the 1/2 lb. of the heatsink.
Bob, et al: I'm looking for some assurance. Have I missed something pertinent to this decision or am I on track?
Roger
"For I know the plans I have for you," declares the Lord, "plans to prosper you and not to harm you, plans to give you hope and a future." Jeremiah 29:11
| - The Matronics AeroElectric-List Email Forum - | | Use the List Feature Navigator to browse the many List utilities available such as the Email Subscriptions page, Archive Search & Download, 7-Day Browse, Chat, FAQ, Photoshare, and much more:
http://www.matronics.com/Navigator?AeroElectric-List |
|
|
|
Back to top |
|
 |
teblejw
Joined: 19 Nov 2013 Posts: 14
|
Posted: Tue Jan 14, 2014 11:21 am Post subject: Change to Shottky? |
|
|
At Bob's suggestion, I've been looking at double anode - single cathode arrangements in a TO-247 case, wired so that current goes through both diodes. My average amperage will be 6-7 amps (12 to 14 total) and I can find packages that will have voltage drops of 0.3 volts or less. The tradeoff is higher leakage, but I don't see how a few tens of mA will cause problems. With only 4 watts or so, Bob suggested using the aluminum already behind the panel. Even if you don't have enough sheet aluminum, there are light-weight heat sinks for the TO-247 package that only cost a couple of bucks and weigh an ounce or so. The TO-247 does have to be solder connected and mounted with an electrically resistive pad, which adds little to cost or weight.
Tom
[quote]
From: Jeff Luckey <jluckey(at)pacbell.net>
To: "aeroelectric-list(at)matronics.com" <aeroelectric-list(at)matronics.com>
Sent: Tuesday, January 14, 2014 9:49 AM
Subject: Re: AeroElectric-List: Change to Shottky?
Roger,
The advantage of Schottky diodes is that they have less voltage drop than silicon diodes. Silicon is approx 0.7 volts and Schottky about 0.5 volts. The advantage being that Schottkys dissipate a little less energy.
Using your numbers for typical load:
Existing diode:
P = IE
6 * .7 = 4.2W
Schottky diode:
6 * .5 = 3.0W
I agree w/ your conclusion, probably not worth changing anything for a delta of 1.2W.
-Jeff
From: Roger Evenson <revenson(at)comcast.net>
To: AeroElectric-List(at)matronics.com
Sent: Tuesday, January 14, 2014 7:19 AM
Subject: Change to Shottky?
#yiv525709406 p {margin:0;}#yiv525709406 p {margin:0;}I wired Z11 with the earlier recommended endurance bus diode w/15 watt heatsink. My loads are 11.5 amps intermittent maximum, 6.1a. typical, and if alternator quits, I could shut things off to get to about 3.3 amps for comfortable endurance use. I see 13.1-13.3 volts on this bus during flight. I have had no issues in 350 hours.
Since completing my RV in 2010, I have been absent from the aeroelectric list. I have noticed that the Shottky diode is now recommended.
Did a search to attempt to 'catch up' with the discussion and have tentatively concluded that this change would be purely optional, and not 'highly recommended' for some electrical reason.
I'm on a weight reduction kick, so my only objective to change to the Shottky would only be to eliminate the 1/2 lb. of the heatsink.
Bob, et al: I'm looking for some assurance. Have I missed something pertinent to this decision or am I on track?
Roger
"For I know the plans I have for you," declares the Lord, "plans to prosper you and not to harm you, plans to give you hope and a future." Jeremiah 29:11
[b]
| - The Matronics AeroElectric-List Email Forum - | | Use the List Feature Navigator to browse the many List utilities available such as the Email Subscriptions page, Archive Search & Download, 7-Day Browse, Chat, FAQ, Photoshare, and much more:
http://www.matronics.com/Navigator?AeroElectric-List |
|
|
|
Back to top |
|
 |
nuckolls.bob(at)aeroelect Guest
|
Posted: Wed Jan 15, 2014 12:46 pm Post subject: Change to Shottky? |
|
|
At 01:20 PM 1/14/2014, you wrote:
At Bob's suggestion, I've been looking at double anode - single
cathode arrangements in a TO-247 case, wired so that current goes
through both diodes. My average amperage will be 6-7 amps (12 to 14
total) and I can find packages that will have voltage drops of 0.3
volts or less. The tradeoff is higher leakage, but I don't see how a
few tens of mA will cause problems. With only 4 watts or so, Bob
suggested using the aluminum already behind the panel. Even if you
don't have enough sheet aluminum, there are light-weight heat sinks
for the TO-247 package that only cost a couple of bucks and weigh an
ounce or so. The TO-247 does have to be solder connected and mounted
with an electrically resistive pad, which adds little to cost or weight.
You're not going to find Schottky devices with rated
for such low voltage drops at their rated current.
To push the drop down, you use oversized to grossly
oversized diodes lightly loaded and yes, your
drop will go down a tad.
The advantage of Schottky diodes is that they have less voltage drop
than silicon diodes. Silicon is approx 0.7 volts and Schottky about
0.5 volts. The advantage being that Schottkys dissipate a little less energy.
Using your numbers for typical load:
Existing diode:
P = IE
6 * .7 = 4.2W
Schottky diode:
6 * .5 = 3.0W
I agree w/ your conclusion, probably not worth changing anything for
a delta of 1.2W.'
Agreed . . . The only time the diode is 'wasting'
energy is when the alternator is running and if you're
running a 40A+ alternator, the energy 'savings'
is trivial.
I wired Z11 with the earlier recommended endurance bus diode w/15
watt heatsink. My loads are 11.5 amps intermittent maximum, 6.1a.
typical, and if alternator quits, I could shut things off to get to
about 3.3 amps for comfortable endurance use. I see 13.1-13.3 volts
on this bus during flight. I have had no issues in 350 hours.
That heatsink is WAaayyyy bigger than you need for this
application.
Since completing my RV in 2010, I have been absent from the
aeroelectric list. I have noticed that the Shottky diode is now recommended.
It's an OPTION . . . one of several.
Did a search to attempt to 'catch up' with the discussion and have
tentatively concluded that this change would be purely optional, and
not 'highly recommended' for some electrical reason.
EXACTLY. I would not recommend anyone swap out
an existing rectifier installation. The Schotty devices
are attractive for new construction. My product uses
the airframe for heat management . . . a bit more compact
than the rectifier . . .
There are VERY few incarnations of the e-bus that
demands a finned heat-sink for the rectifier. Either
the silicon junction rectifier -OR- the Schottky
device should exist quite happily simply sinked
to the airplane.
Products like this
http://tinyurl.com/mfp9k7a
probably make sense in a composite airplane but I
suspect that few installations in metal airplanes
need the extra heat-sink.
I'm on a weight reduction kick, so my only objective to change to the
Shottky would only be to eliminate the 1/2 lb. of the heat-sink.
1/2 pound? Which heat-sink are you using?
Bob, et al: I'm looking for some assurance. Have I missed something
pertinent to this decision or am I on track?
Is this a metal airplane? Have you looked at simply
bolting the diode to local sheet metal?
Bob . . .
| - The Matronics AeroElectric-List Email Forum - | | Use the List Feature Navigator to browse the many List utilities available such as the Email Subscriptions page, Archive Search & Download, 7-Day Browse, Chat, FAQ, Photoshare, and much more:
http://www.matronics.com/Navigator?AeroElectric-List |
|
|
|
Back to top |
|
 |
revenson(at)comcast.net Guest
|
Posted: Wed Jan 15, 2014 1:30 pm Post subject: Change to Shottky? |
|
|
Bob: To answer your questions, this is an RV7, all metal airplane. The heat sink I used was the 15 watt one, the larger of the two offered at B&C. It weighs 7 oz.
I will remove it and install directly to the aluminum subpanel.
Would you change your recommendation if you knew I was in Arizona, occasionally flying in 100+ temperatures?
Thanks. Roger
From: "Robert L. Nuckolls, III" <nuckolls.bob(at)aeroelectric.com>
To: aeroelectric-list(at)matronics.com
Sent: Wednesday, January 15, 2014 1:43:39 PM
Subject: Re: Change to Shottky?
--> AeroElectric-List message posted by: "Robert L. Nuckolls, III" <nuckolls.bob(at)aeroelectric.com>
At 01:20 PM 1/14/2014, you wrote:
At Bob's suggestion, I've been looking at double anode - single
cathode arrangements in a TO-247 case, wired so that current goes
through both diodes. My average amperage will be 6-7 amps (12 to 14
total) and I can find packages that will have voltage drops of 0.3
volts or less. The tradeoff is higher leakage, but I don't see how a
few tens of mA will cause problems. With only 4 watts or so, Bob
suggested using the aluminum already behind the panel. Even if you
don't have enough sheet aluminum, there are light-weight heat sinks
for the TO-247 package that only cost a couple of bucks and weigh an
ounce or so. The TO-247 does have to be solder connected and mounted
with an electrically resistive pad, which adds little to cost or weight.
You're not going to find Schottky devices with rated
for such low voltage drops at their rated current.
To push the drop down, you use oversized to grossly
oversized diodes lightly loaded and yes, your
drop will go down a tad.
The advantage of Schottky diodes is that they have less voltage drop
than silicon diodes. Silicon is approx 0.7 volts and Schottky about
0.5 volts. The advantage being that Schottkys dissipate a little less energy.
Using your numbers for typical load:
Existing diode:
P = IE
6 * .7 = 4.2W
Schottky diode:
6 * .5 = 3.0W
I agree w/ your conclusion, probably not worth changing anything for
a delta of 1.2W.'
Agreed . . . The only time the diode is 'wasting'
energy is when the alternator is running and if you're
running a 40A+ alternator, the energy 'savings'
is trivial.
I wired Z11 with the earlier recommended endurance bus diode w/15
watt heatsink. My loads are 11.5 amps intermittent maximum, 6.1a.
typical, and if alternator quits, I could shut things off to get to
about 3.3 amps for comfortable endurance use. I see 13.1-13.3 volts
on this bus during flight. I have had no issues in 350 hours.
That heatsink is WAaayyyy bigger than you need for this
application.
Since completing my RV in 2010, I have been absent from the
aeroelectric list. I have noticed that the Shottky diode is now recommended.
It's an OPTION . . . one of several.
Did a search to attempt to 'catch up' with the discussion and have
tentatively concluded that this change would be purely optional, and
not 'highly recommended' for some electrical reason.
EXACTLY. I would not recommend anyone swap out
an existing rectifier installation. The Schotty devices
are attractive for new construction. My product uses
the airframe for heat management . . . a bit more compact
than the rectifier . . .
There are VERY few incarnations of the e-bus that
demands a finned heat-sink for the rectifier. Either
the silicon junction rectifier -OR- the Schottky
device should exist quite happily simply sinked
to the airplane.
Products like this
http://tinyurl.com/mfp9k7a
probably make sense in a composite airplane but I
suspect that few installations in metal airplanes
need the extra heat-sink.
I'm on a weight reduction kick, so my only objective to change to the
Shottky would only be to eliminate the 1/2 lb. of the heat-sink.
1/2 pound? Which heat-sink are you using?
Bob, et al: I'm looking for some assurance. Have I missed something
pertinent to this decision or am I on track?
Is this a metal airplane? Have you looked at simply
bolting the diode to local sheet metal?; -Matt Dralle, List Admin.========
[quote][b]
| - The Matronics AeroElectric-List Email Forum - | | Use the List Feature Navigator to browse the many List utilities available such as the Email Subscriptions page, Archive Search & Download, 7-Day Browse, Chat, FAQ, Photoshare, and much more:
http://www.matronics.com/Navigator?AeroElectric-List |
|
|
|
Back to top |
|
 |
nuckolls.bob(at)aeroelect Guest
|
Posted: Thu Jan 16, 2014 6:15 am Post subject: Change to Shottky? |
|
|
At 03:29 PM 1/15/2014, you wrote:
Quote: | Bob: To answer your questions, this is an RV7, all metal
airplane. The heat sink I used was the 15 watt one, the larger of
the two offered at B&C. It weighs 7 oz.
I will remove it and install directly to the aluminum subpanel.
Would you change your recommendation if you knew I was in Arizona,
occasionally flying in 100+ temperatures?
|
Nope. 100+ isn't 'hot' for a semiconductor.
The it's only 30F or 16C hotter than what
people like to exist in. Most semiconductor
devices are rated to operate up to 175C
AT THE JUNCTIONS . . . that is hot.
The only time your 100F hypothesis would put
a device at risk is if the heat sink were
marginal in the first place. After operating
your system loads for say 30 minutes or so
(time for temps to stabilize) put your fingers
on the device . . . you may find it 'toasty' but
it probably wouldn't 'sizzle spit' . . . most
of the time you'll find it warm but not dangerous
for the epidermis.
If you're really curious, you can put a temp
sensor on the bolt that mounts the device and get
some real numbers . . . good thing to know
and share.
If you don't have a capable remote temperature
measuring instrument, you might consider this
one . . .
http://tinyurl.com/lomcyp3
Comes with two probes and is shipped from US
location . . . fast.
No matter how convincing I might be by offering
advice from experience, there's nothing better
than to go measure it for yourself and then
report the results.
Bob . . .
| - The Matronics AeroElectric-List Email Forum - | | Use the List Feature Navigator to browse the many List utilities available such as the Email Subscriptions page, Archive Search & Download, 7-Day Browse, Chat, FAQ, Photoshare, and much more:
http://www.matronics.com/Navigator?AeroElectric-List |
|
|
|
Back to top |
|
 |
Eric M. Jones
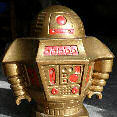
Joined: 10 Jan 2006 Posts: 565 Location: Massachusetts
|
Posted: Thu Jan 16, 2014 7:14 am Post subject: Re: Change to Shottky? |
|
|
The calculation here on the dissipation and voltage drops of Schottkys and P/N diodes are simply being pulled out of the air. What diodes are you referring to? You show me yours and I'll show you mine.
A "standard" 15A 50V P/N diode is 1.5 Volts Vf like 1N3208. So at 13V you get 11.5V out.
I use and sell IXYS DSSX61-0045A. Power_Deuce_Schottkys. At 15A they are 0.45Volts Vf. So at 13VDC you get 12.55VDC out.
I supply these on heatsink. They are isolated and paired so they can be used in Y-configurations or separate or paired.
I've looked and don't see any better diodes for general aircraft purposes. If the difference was as small as some here have erroneously stated, we wouldn't be having this conversation. Most modern battery operated equipment have no p/n diodes. They waste too much power.
Remember: With diodes the measurements are often at 50% duty cycle. Also remember that Vf is not reduced when diodes are in placed parallel (unlike R for resistors).
| - The Matronics AeroElectric-List Email Forum - | | Use the List Feature Navigator to browse the many List utilities available such as the Email Subscriptions page, Archive Search & Download, 7-Day Browse, Chat, FAQ, Photoshare, and much more:
http://www.matronics.com/Navigator?AeroElectric-List |
|
Description: |
|
 Download |
Filename: |
Power_Deuce_Schottky_ Manual.pdf |
Filesize: |
241.64 KB |
Downloaded: |
337 Time(s) |
_________________ Eric M. Jones
www.PerihelionDesign.com
113 Brentwood Drive
Southbridge, MA 01550
(508) 764-2072
emjones(at)charter.net |
|
Back to top |
|
 |
teblejw
Joined: 19 Nov 2013 Posts: 14
|
Posted: Thu Jan 16, 2014 2:10 pm Post subject: Change to Shottky? |
|
|
Eric,
I think that I misinterpreted the use of the word "average." (My aero, mechanical, and civil engineering degrees were not big on diodes.) Say, for the specific diode STPS60L30CW: http://www.st.com/en/resources/technical/document/cd00001857.pdf ,
Fig. 1 provides "average forward power dissipation versus average forward current (per diode)." I now understand that the term "average" is the average for the cycle (not the average between the two diodes), i.e., the average amperage for a square-wave cycle with a delta of 0.5 would be half the peak to peak amperage. So, if I understand you correctly, the voltage drop with both diodes connected to the same source should be calculated using the total current, as if there were only one diode connected. For this particular diode assembly and my system (14A max. at 13V), the voltage drop from Fig. 9 at a Tj of 125 degC is 0.31 to 0.32, for a power dissipation of slightly more than 4W. I would only use this diode if I were confident that I could keep the Tj low, because it has high leakage at high temperature and because this diode is only rated to 150 degC. But the leakage versus voltage drop is the tradeoff I see in the selection process. Not clear to me that we need extremely low leakage.
I don't understand why the voltage drop should be calculated as if all the current goes through only one diode. This implies that the current doesn't substantively split, because if it did, the voltage drop in each diode would be lower. If there is a good authoritative reference that you can suggest, I would appreciate it. I've Googled and found different views and opinions.
Thanks.
Tom
Quote: |
From: Eric M. Jones <emjones(at)charter.net>
To: aeroelectric-list(at)matronics.com
Sent: Thursday, January 16, 2014 8:14 AM
Subject: Re: Change to Shottky?
--> AeroElectric-List message posted by: "Eric M. Jones" <emjones(at)charter.net (emjones(at)charter.net)>
The calculation here on the dissipation and voltage drops of Schottkys and P/N diodes are simply being pulled out of the air. What diodes are you referring to? You show me yours and I'll show you mine.
A "standard" 15A 50V P/N diode is 1.5 Volts Vf like 1N3208. So at 13V you get 11.5V out.
I use and sell IXYS DSSX61-0045A. Power_Deuce_Schottkys. At 15A they are 0.45Volts Vf. So at 13VDC you get 12.55VDC out.
I supply these on heatsink. They are isolated and paired so they can be used in Y-configurations or separate or paired.
I've looked and don't see any better diodes for general aircraft purposes. If the difference was as small as some here have erroneously stated, we wouldn't be having this conversation. Most modern battery operated equipment have no p/n diodes. They waste too much power.
Remember: With diodes the measurements are often at 50% duty cycle. Also remember that Vf is not reduced when diodes are in placed parallel (unlike R for resistors).
--------
Eric M. Jones
http://www.periheliondesign.com/
113 Brentwood Drive
Southbridge, MA 01550
(508) 764-2072
emjones(at)charter.net
Read this topic online here:
http://forums.matronics.com/viewtopic.php?p=417007#417007
Attachments:
http://forums.matronics.com//files/power_deuce_schottky_manual_109.pdf
= &n-->
|
| - The Matronics AeroElectric-List Email Forum - | | Use the List Feature Navigator to browse the many List utilities available such as the Email Subscriptions page, Archive Search & Download, 7-Day Browse, Chat, FAQ, Photoshare, and much more:
http://www.matronics.com/Navigator?AeroElectric-List |
|
|
|
Back to top |
|
 |
Eric M. Jones
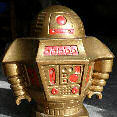
Joined: 10 Jan 2006 Posts: 565 Location: Massachusetts
|
Posted: Fri Jan 17, 2014 3:11 pm Post subject: Re: Change to Shottky? |
|
|
When using diodes in parallel, the Vf drop will stay the same as the lowest diodes’ Vf but reverse leakage Ir (and capacitance) will add. But it is often cited as a bad idea because as one diode heats up, its Vf will decrease…and it will draw more current, etc. This is called a thermal runaway failure. You can avoid this by placing the diodes in tight thermal contact with each other, or using a small resistor in series with each, or making certain the Vfs start and thermally track each other as closely as possible (and the diodes were made at the same time, same batch, etc.).
Schottky diodes especially trade off forward Vf with reverse leakage. So always look for this when trying to get a very low forward Vf. I can’t say reverse leakage is always a bad thing; it depends on the use. The spec sheet for STPS60L30 states:
Dual center tap Schottky rectifier suited for Switch Mode Power Supply and high frequency DC to DC converters. Packaged in TO247, this device is intended for use in low voltage, high frequency inverters, free-wheeling and polarity protection applications.
This statement by STM is a good indication that this part has a huge reverse leakage Ir, since HF inverter transformers in power supplies can allow for that reverse DC leakage easily while they benefit from the very low Vf. And it does. Ir(max) Tj=125C, 500 mA! Can your application accept that?
The spec sheet for IXYS DSSX61-0045A Ir (max) is 20 mA.
I don’t want to specify or analyze specific diode choices, but I think IXYS DSSX61-0045A represents a good compromise for power blocking diodes in price/performance /Vf/Ir mostly because it is packaged in an isolated SOT-227 package. There are lower Vf diodes, and lower Ir diodes, and diodes that are far pricier. But this is a great compromise and very versatile diode. Remember, Schottkys dissipate less and often require no heatsink compared to a similarly-rated P/N diode.
Quote: | >>From: Thomas Blejwas <tomblejwas>
Subject: Re: AeroElectric-List: Re: Change to Schottky?
-Eric, I think that I misinterpreted the use of the word "average."
- (My-aero, mechanical, and civil engineering degrees were not big on diodes.) -Say, for the specific diode STPS60L30CW: http://www.st.com/en/resources/technical/document/cd00001857.pdf- , Fig. 1 provides "average forward power dissipation versus average forward current (per diode)."- I
now understand that the term "average" is the average for-the cycle (not
the average between the two diodes), i.e., the average amperage for a square-wave cycle with a delta of 0.5 would be half the peak to peak amperage.
>>- So, if I understand you correctly, the voltage drop with both diodes connected to the same source-should be calculated using the total current, as if there were only one diode connected. |
Right, if I get what you're saying. Think of Vf standing for “Vertical fall” (waterfall). Adding waterfalls in parallel, doesn’t make each Vf waterfall taller. You can get more current, but you can’t reduce the Vf potential loss. It is what it is. At the top of the waterfall you have a potential; at the bottom you have lower potential.
Quote: | >>For this particular diode assembly-and my system (14A max.-at 13V), the voltage drop from Fig. 9 at a Tj of 125 degC is 0.31 to 0.32, for a power dissipation of-slightly more than 4W.- I would only use this diode if I were confident that I could keep the Tj low, because it has high leakage at high temperature and because this diode is only rated to 150 degC.- But the leakage versus voltage drop is the tradeoff I see in the selection process.-
|
True. But even at a Tj of 125 degC, used as an isolation diode, I’d be careful because it doesn’t isolate much. This might matter.
Quote: | >>Not clear to me that we need extremely low leakage. I don't understand-why the voltage drop should be calculated as if all the current goes through only one diode.- This implies that the current doesn't substantively split, because if it did, the voltage drop in each diode would be lower.- If there is a good authoritative-reference that you can suggest, I would appreciate it.- I've Googled and found different views and opinions. |
There is a substantial body of work on using Schottkys. Try: http://www.onsemi.com/pub_link/Collateral/AND9038-D.PDF or other application notes from major manufacturers.
Builders new to electronics often wonder if there is a particular “best” component. There usually isn’t Furthermore sometimes (amazingly!) the manufacturer hides certain facts…like price, which is a really important characteristic unless you work for the military, or the 56-week lead-time, (happened to me!) or the fact that the parts are counterfeit. (I will send you some fake MC33030P parts if interested…straight from 4-Star Electronics…who wouldn’t return my money because it took me 32 days to come to the hard-to-believe conclusion that their parts were fakes.)
| - The Matronics AeroElectric-List Email Forum - | | Use the List Feature Navigator to browse the many List utilities available such as the Email Subscriptions page, Archive Search & Download, 7-Day Browse, Chat, FAQ, Photoshare, and much more:
http://www.matronics.com/Navigator?AeroElectric-List |
|
_________________ Eric M. Jones
www.PerihelionDesign.com
113 Brentwood Drive
Southbridge, MA 01550
(508) 764-2072
emjones(at)charter.net |
|
Back to top |
|
 |
nuckolls.bob(at)aeroelect Guest
|
Posted: Fri Jan 17, 2014 4:56 pm Post subject: Change to Shottky? |
|
|
At 09:14 AM 1/16/2014, you wrote:
Quote: |
The calculation here on the dissipation and voltage drops of
Schottkys and P/N diodes are simply being pulled out of the air.
What diodes are you referring to? You show me yours and I'll show you mine.
|
Okay, our MBR4060 mounted for convenient installation
heat-sinked to the airframe and provided with terminals
for attachment of wires.
With the pair carrying 10A I measure a drop of 0.45
volts, 20A drops 0.68 volts.
While one cannot expect two diodes to accurately
parallel and share a load, the fact that the voltage
drops at all when the second diode is added demonstrates that
SOME load sharing takes place. This offers a benefit,
(perhaps tiny but quantifiable) for spreading the thermal
stresses over the device's heat-sink surface combined
with a small drop in voltage. In no way is the practice of
paralleling expected to offer a critical performance
jump . . . the second diode was there in the package
. . . might as well do something useful with it . . .
Quote: |
A "standard" 15A 50V P/N diode is 1.5 Volts Vf like 1N3208.
So at 13V you get 11.5V out.
|
I just measured one of the RS 25A bridge diodes
at 10A and got 0.84 volts, 20A gave me 0.93 volts
Quote: | I use and sell IXYS DSSX61-0045A. Power_Deuce_Schottkys. At 15A
they are 0.45Volts Vf. So at 13VDC you get 12.55VDC out.
|
Don't know where the 13v comes from. The normal feedpath
diode takes a feed from the main bus which also drives
the voltage sense pin of the regulator. Hence, this bus
is expected to be at 14.2 +/0 0.2 volts any time the
alternator is operating normally. If the alternator is
running, the bus is >14v . . . if the alternator is
not running the system voltage is <12.5
Quote: | I supply these on heatsink. They are isolated and paired so they can
be used in Y-configurations or separate or paired.
I've looked and don't see any better diodes for general aircraft
purposes. If the difference was as small as some here have
erroneously stated, we wouldn't be having this conversation. Most
modern battery operated equipment have no p/n diodes. They waste too
much power.
|
Kumquats and watermelons. Diodes used inside
a piece of electronics have little in common
with design goals for steering diodes in
power distribution systems. There are some really
fat P/N diodes used throughout the Lear, Cessna
and Beech fleets (and no doubt others) that cannot
be Shottky due to requirements for lightning and abnormal
surge voltage requirements. Requirements that
are not levied onto the internal workings of an
appliance.
I think the Hawker 4000 had some Shottky power
steering in their DC system (Low current stuff
driven by TR-sets off wild frequency 208, 3-
phase) and they had to add a lot of monkey-
motion in the form of Transorbs, etc. to make
it through lightning testing.
We're discussing the return on investment in
light airplanes for saving a watt or two in
a system powered with a 500+ watt engine driven
power source is not quantifiable. Energy 'squandered'
is a fraction of a percent of the whole energy
bucket no matter what kind of diode you use.
At the same time, the 'rule of thumb' for selection
of wires says 5% voltage drop is an acceptable
compromise between loss of electrical performance
and unnecessary addition to aircraft empty weight.
That figures out to 0.7 volts per power feeder;
but that too is a 'rule of thumb' . . . were it
twice that amount, no airplane is going to fall
out of the sky and no pilots are going to be
squinting out into the dark because 'violation'
of rule by a factor of 2 or even 3 has dimmed
the lights. No dollars will be saved. So the choice
of components is driven by FMEA and human
factors for reducing risk.
For example, we could replace the normal feedpath
diode with a relay that is controlled by an
aux battery management module . . . relay closed
only when the bus voltage exceeds 13.0 volts.
Hard contacts, lower voltage drop, more complexity.
Or put a switch in. But then, the whole purposed
for the diode was to prevent inadvertent back-feeding
the main bus from the e-bus due to improper operation
of switches.
I've looked and don't see any better diodes for general aircraft
purposes. If the difference was as small as some here have
erroneously stated, we wouldn't be having this conversation. Most
modern battery operated equipment have no p/n diodes. They waste too
much power.
It's easy to avoid getting wrapped around
the weight/energy-savings axles in this application.
Energy savings is trivial . . . weight savings can
be as much as 1/2 pound if the builder discovers
that THEIR implementation of the e-bus normal feed
diode doesn't really need that big heat sink.
If some diode is dropping enough BTU's to require
a hefty heat-sink, then it's not driving an e-bus.
The Endurance Bus was conceived to offer a
narrowly defined benefit . . . electrical endurance
that exceeded fuel endurance. With the electrically
dependent engine needing something on the order
of 100W power for operation, the concept of an
E=Bus is no longer useful. It's unlikely that
anyone will opt to carry enough battery to run
an engine for 3 hours. At the same time,
diodes used to steer power can STILL be sized
in the 8-12 amp range without extra-ordinary
heat-sinking in an all metal airplane.
But in any case, there's no substitute for
confirmation of one's decisions by direct
measurement of effects and benefits. Toward that
end, I supported an RS bridge in air with no heat-sink
and loaded it to 10A. After 20 minutes, the mounting
surface stabilized out at just over 100C. Given
the very limited ability of this surface to reject
heat, the stress across the internal thermal resistance
would be low the diode junction was probably not much
hotter . . . perhaps 110-120C.
But the thing didn't self-destruct. Then I bolted
it to an airplane . . . well . . . a part of
an airplane .040 x 5 x 5 inches. Didn't use
heat-sink grease under the part but I did
put a fender-washer on the back side to stiffen
the aluminum around the mounting hole with
a notion of bringing the rectifier into better
contact with the aluminum sheet.
If one intends to run loads in the 10A class
through a device like this, some heat-sink grease
or Sil-Pad underneath plus a backside 'stiffener'
is probably a good thing to do.
The second experiment was rather profound.
After 20 minutes, the metal around the
rectifier was running 40C. 15C over ambient
for a rise of about 2C/watt. Assuming I had
a lousy thermal interface of . . . say
1.5C/W. These devices will typically
offer a to case resistance 1.5C/W. So the
8w dissipated in the diode was taking
the junction to 8 x 3 or 24C hotter
than the 'airplane' at 40C. This minimalist
approach to heat-sink gave us a junction
temperature about 40C over ambient or 65C
. . . . . .WAaaay less than the rated
150C maximum.
If your airplane isn't metal, then you can
use the same part-of-an-airplane that I just
demonstrated. 25 square inches of aluminum
goes a long way toward cooling things off.
If that were a Schottky running 5 watts
of loss, then the temperature of the junction
can be expected to drop into the neighborhood
of 25C over ambient . . . and a 'savings'
of 3 watts.
The point of this discussion is to put the
worries to bed for application of any diode
technology for steering power to either an
E-bus or M-P bus of the variety we're
discussing today.
Further, note that 'losses' associated with
these diodes can be eliminated from the
concerns for battery-only operations. That's
what the Z-07 discussion is all about.
Bob . . .
| - The Matronics AeroElectric-List Email Forum - | | Use the List Feature Navigator to browse the many List utilities available such as the Email Subscriptions page, Archive Search & Download, 7-Day Browse, Chat, FAQ, Photoshare, and much more:
http://www.matronics.com/Navigator?AeroElectric-List |
|
|
|
Back to top |
|
 |
|
|
You cannot post new topics in this forum You cannot reply to topics in this forum You cannot edit your posts in this forum You cannot delete your posts in this forum You cannot vote in polls in this forum You cannot attach files in this forum You can download files in this forum
|
Powered by phpBB © 2001, 2005 phpBB Group
|