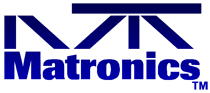 |
Matronics Email Lists Web Forum Interface to the Matronics Email Lists
|
View previous topic :: View next topic |
Author |
Message |
Tom Jones
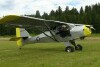
Joined: 12 Mar 2006 Posts: 752 Location: Ellensburg, WA
|
Posted: Fri Jan 23, 2015 6:06 am Post subject: 503 oil pump cable end wearing |
|
|
This 503 came from the factory without oil injection. At 80 hours I installed an injection system. The engine now has 136 hours so only 56 hours on this cable. You can see it is worn about 1/4 of the way through the barrel swedge on both ends where it contacts the oil pump lever. The pump lever is not worn at all. I noticed the swedge is brass. Too soft??? I have lubed it with LPS about every 10 hours.
The engine is on a Kitfox so I had California Power Sports make a cable with the 503 oiler swedge on the pump end and a barrel swedge to fit the Kitfox throttle reverser bellcrank on the other end. I think I gave them measurements either too short for the inner cable or too long for the outer cable.
I had to put both lock nuts on the adjuster below the bracket as shown to make the line on the lever line up at 3000 rpm. This caused the cable to not pull straight up on the lever at full throttle as shown in the photos. Could that be my problem
I really like the convenience of the injection and it is supposed to be better for the engine but this is no good. Anyone else have this problem or have any ideas. I called CPS and they do not custom make cables anymore.
I iknow this is not a Kolb but I have had better luck asking two stroke questions here. On the Kitfox forums if you don't have a 912 you might as well not show up at the dance on Saturday night.
| - The Matronics Kolb-List Email Forum - | | Use the List Feature Navigator to browse the many List utilities available such as the Email Subscriptions page, Archive Search & Download, 7-Day Browse, Chat, FAQ, Photoshare, and much more:
http://www.matronics.com/Navigator?Kolb-List |
|
Description: |
|
Filesize: |
43.32 KB |
Viewed: |
22320 Time(s) |
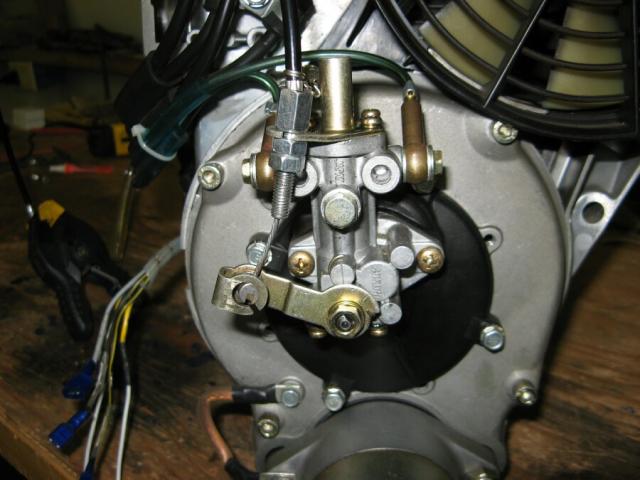
|
Description: |
|
Filesize: |
39.06 KB |
Viewed: |
22318 Time(s) |
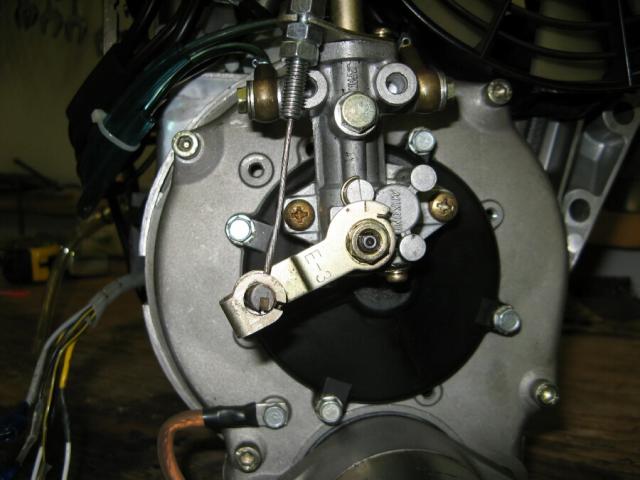
|
Description: |
|
Filesize: |
84.97 KB |
Viewed: |
22318 Time(s) |
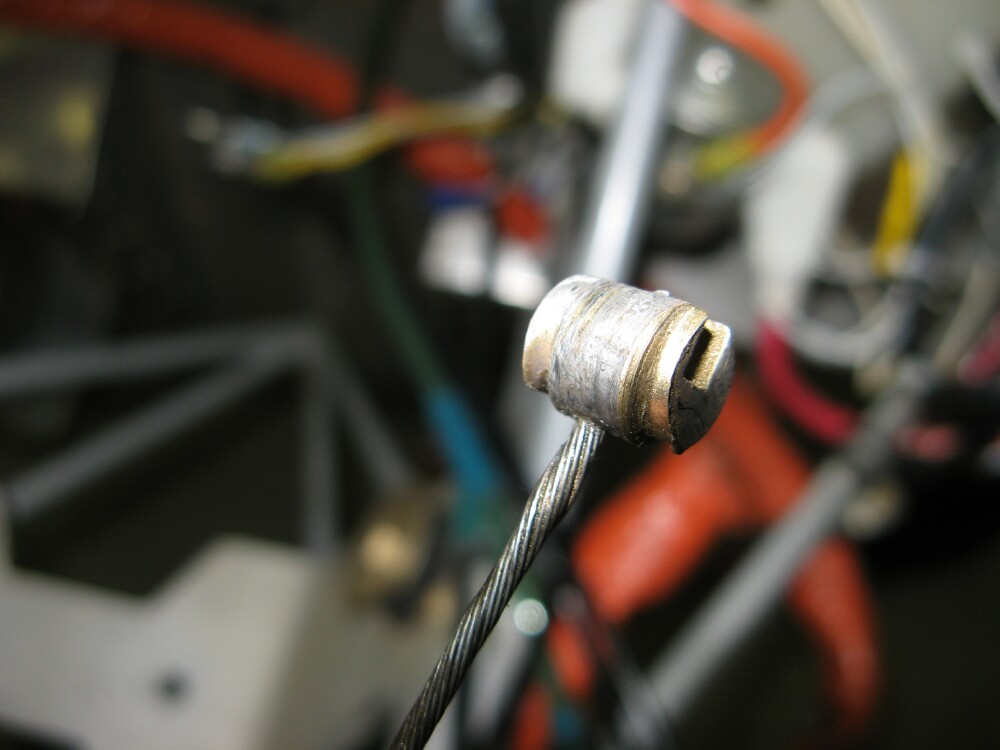
|
_________________ Tom Jones
Classic IV
503 Rotax, 72 inch Two blade Warp
Ellensburg, WA |
|
Back to top |
|
 |
John Hauck
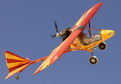
Joined: 09 Jan 2006 Posts: 4639 Location: Titus, Alabama (hauck's holler)
|
Posted: Fri Jan 23, 2015 6:32 am Post subject: 503 oil pump cable end wearing |
|
|
Have you tried Matronic's ROTAX Engine List?
Guessing engine vibration is causing your cable stop to wear. Oiling the
fitting may be attracting dirt and grit which is accelerating wear.
john h
mkIII
Titus, Alabama
--
| - The Matronics Kolb-List Email Forum - | | Use the List Feature Navigator to browse the many List utilities available such as the Email Subscriptions page, Archive Search & Download, 7-Day Browse, Chat, FAQ, Photoshare, and much more:
http://www.matronics.com/Navigator?Kolb-List |
|
_________________ John Hauck
MKIII/912ULS
hauck's holler
Titus, Alabama |
|
Back to top |
|
 |
Tom Jones
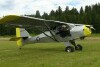
Joined: 12 Mar 2006 Posts: 752 Location: Ellensburg, WA
|
Posted: Fri Jan 23, 2015 7:21 am Post subject: Re: 503 oil pump cable end wearing |
|
|
Okay, I'll try the Rotax Engines List. Thanks
| - The Matronics Kolb-List Email Forum - | | Use the List Feature Navigator to browse the many List utilities available such as the Email Subscriptions page, Archive Search & Download, 7-Day Browse, Chat, FAQ, Photoshare, and much more:
http://www.matronics.com/Navigator?Kolb-List |
|
_________________ Tom Jones
Classic IV
503 Rotax, 72 inch Two blade Warp
Ellensburg, WA |
|
Back to top |
|
 |
baberdk
Joined: 23 Jan 2014 Posts: 53 Location: East Moline, Il
|
Posted: Sat Jan 24, 2015 5:09 am Post subject: 503 oil pump cable end wearing |
|
|
I would try LEAF (Leading Edge Air Foils) Here are some of the parts you'll need. http://store.leadingedgeairfoils.com/index.php?cPath=522_284 After you make the cable, it is dipped in solder pot to make it secure.Also, I have shortened the cable sheath with a pipe cutter. It's just as good as lengthening the cable. The kind with a cutting wheel and you can adjust the pressure on the wheel with a knob.
Respectfully,
Dennis Baber
Rough diamonds may sometimes be mistaken for worthless pebbles
[quote][b]
| - The Matronics Kolb-List Email Forum - | | Use the List Feature Navigator to browse the many List utilities available such as the Email Subscriptions page, Archive Search & Download, 7-Day Browse, Chat, FAQ, Photoshare, and much more:
http://www.matronics.com/Navigator?Kolb-List |
|
|
|
Back to top |
|
 |
Tom Jones
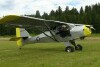
Joined: 12 Mar 2006 Posts: 752 Location: Ellensburg, WA
|
Posted: Sat Jan 24, 2015 6:19 am Post subject: Re: 503 oil pump cable end wearing |
|
|
Thanks Dennis. I ordered a cable splitter like that from Spruce. The parts places all seem to hold the information close to the chest on how the other end of the splitter connects to the throttle wire from the hand throttle.
When It gets here I'll then see what else I need to put it all together. I also notice the Lockwood catalog has a stainless Steel oil injection fitting for the 503. http://www.lockwood.aero/p-2127-oil-injection-cable-fitting-stainless-503-only.aspx . All the other suppliers seem to use the brass fitting like wore out on mine.
Doing a little more research I have run across a couple other 503 owners that have removed their oil injection for this same reason...the brass cable fitting wears out quickly.
| - The Matronics Kolb-List Email Forum - | | Use the List Feature Navigator to browse the many List utilities available such as the Email Subscriptions page, Archive Search & Download, 7-Day Browse, Chat, FAQ, Photoshare, and much more:
http://www.matronics.com/Navigator?Kolb-List |
|
_________________ Tom Jones
Classic IV
503 Rotax, 72 inch Two blade Warp
Ellensburg, WA |
|
Back to top |
|
 |
Richard Pike
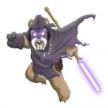
Joined: 09 Jan 2006 Posts: 1671 Location: Blountville, Tennessee
|
Posted: Sat Jan 24, 2015 7:19 am Post subject: Re: 503 oil pump cable end wearing |
|
|
Just looking at the top picture, it appears that the bracket is not properly aligned with the pump arm. Why not either twist the bracket a bit to line up, or fabricate a new bracket that puts the fitting in a better position?
Then you need a new end fitting, you can get one from CPS, I noticed they have 2 sizes, a smaller one for the 582 and a bigger one for the 503.
Looking at the close-up of the swedge, you can see where the solder has run up the cable for about 3/4". That will certainly retain it, but also make the cable stiffer. There is a foolproof way to solder a swedge end on without a solder pot, and the solder does not run up the cable as far.
The swedge end will typically have the cable hole on one side the exact diameter of the cable and it will be cut off flush with the surface. That is your entrance hole, the cable enters the swedge from that side. The other side has the hole somewhat flared or countersunk and also slightly larger in diameter. That is your exit hole. If it is not slightly oversize or countersunk & flared, make it so. Just a little bit, it doesn't take much.
With the cable extending slightly from the exit side, take a rib stitching needle, ice pick or similar, and thoroughly rat tail, unweave and debraid the cable, you goal is to physically enlarge the diameter of the cable so that it cannot pull back through even if you didn't solder it. You will be surprised how easy and effective this is. Now solder it, and you ought to see a bit of the solder flow back out through the cable on the entrance side. What the solder is doing is making it impossible for the steel cable to compress & get any smaller. The adhesion of the solder to the swedge is now no longer the primary securing method, it is now complimentary to the physical size difference between the cable & the swedge. Clean up the excessive rat tail by taking a Dremel wheel and trimming the rat tailed exit end back smooth with the swedge.
Now you have a cable that is oversized on its exit side, and cannot be compressed & pulled back through a tapered and smaller hole. Plus it is still soldered to the swedge anyway. Using the solder pot method, the hole and the cable are a constant diameter, and rely entirely on the strength of the solder joint, in which case a solder pot is mandatory.
Food for thought, worth what ya paid for it.
| - The Matronics Kolb-List Email Forum - | | Use the List Feature Navigator to browse the many List utilities available such as the Email Subscriptions page, Archive Search & Download, 7-Day Browse, Chat, FAQ, Photoshare, and much more:
http://www.matronics.com/Navigator?Kolb-List |
|
_________________ Richard Pike
Kolb MKIII N420P (420ldPoops)
Kingsport, TN 3TN0
Forgiving is tough, being forgiven is wonderful, and God's grace really is amazing. |
|
Back to top |
|
 |
Tom Jones
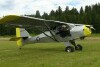
Joined: 12 Mar 2006 Posts: 752 Location: Ellensburg, WA
|
Posted: Sat Jan 24, 2015 8:16 am Post subject: Re: 503 oil pump cable end wearing |
|
|
Thanks for that tip on soldering the swedge Richard! I am going to order one of those stainless steel swedges from Lockwood and do that. I feel a lot better about getting this done now.
| - The Matronics Kolb-List Email Forum - | | Use the List Feature Navigator to browse the many List utilities available such as the Email Subscriptions page, Archive Search & Download, 7-Day Browse, Chat, FAQ, Photoshare, and much more:
http://www.matronics.com/Navigator?Kolb-List |
|
_________________ Tom Jones
Classic IV
503 Rotax, 72 inch Two blade Warp
Ellensburg, WA |
|
Back to top |
|
 |
Herbgh(at)nctc.com Guest
|
Posted: Sat Jan 24, 2015 8:28 am Post subject: 503 oil pump cable end wearing |
|
|
Good 'splanation.....Richard
Strikes me that silver solder would be more durable? Herb
On 01/24/2015 09:19 AM, Richard Pike wrote:
Quote: |
Just looking at the top picture, it appears that the bracket is not properly aligned with the pump arm. Why not either twist the bracket a bit to line up, or fabricate a new bracket that puts the fitting in a better position?
Then you need a new end fitting, you can get one from CPS, I noticed they have 2 sizes, a smaller one for the 582 and a bigger one for the 503.
Looking at the close-up of the swedge, you can see where the solder has run up the cable for about 3/4". That will certainly retain it, but also make the cable stiffer. There is a foolproof way to solder a swedge end on without a solder pot, and the solder does not run up the cable as far.
The swedge end will typically have the cable hole on one side the exact diameter of the cable and it will be cut off flush with the surface. That is your entrance hole, the cable enters the swedge from that side. The other side has the hole somewhat flared or countersunk and also slightly larger in diameter. That is your exit hole. If it is not slightly oversize or countersunk & flared, make it so. Just a little bit, it doesn't take much.
With the cable extending slightly from the exit side, take a rib stitching needle, ice pick or similar, and thoroughly rat tail, unweave and debraid the cable, you goal is to physically enlarge the diameter of the cable so that it cannot pull back through even if you didn't solder it. You will be surprised how easy and effective this is. Now solder it, and you ought to see a bit of the solder flow back out through the cable on the entrance side. What the solder is doing is making it impossible for the steel cable to compress & get any smaller. The adhesion of the solder to the swedge is now no longer the primary securing method, it is now complimentary to the physical size difference between the cable & the swedge. Clean up the excessive rat tail by taking a Dremel wheel and trimming the rat tailed exit end back smooth with the swedge.
Now you have a cable that is oversized on its exit side, and cannot be compressed & pulled back through a tapered and smaller hole. Plus it is still soldered to the swedge anyway. Using the solder pot method, the hole and the cable are a constant diameter, and rely entirely on the strength of the solder joint, in which case a solder pot is mandatory.
Food for thought, worth what ya paid for it.
--------
Richard Pike
Kolb MKIII N420P (420ldPoops)
Kingsport, TN 3TN0
My soul shall be joyful in the LORD; It shall rejoice in His salvation. Psalm 35:9
Read this topic online here:
http://forums.matronics.com/viewtopic.php?p=437551#437551
|
| - The Matronics Kolb-List Email Forum - | | Use the List Feature Navigator to browse the many List utilities available such as the Email Subscriptions page, Archive Search & Download, 7-Day Browse, Chat, FAQ, Photoshare, and much more:
http://www.matronics.com/Navigator?Kolb-List |
|
|
|
Back to top |
|
 |
Richard Pike
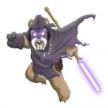
Joined: 09 Jan 2006 Posts: 1671 Location: Blountville, Tennessee
|
Posted: Sat Jan 24, 2015 11:24 am Post subject: Re: 503 oil pump cable end wearing |
|
|
I only ever did this with brass. Did not know that you could solder anything to stainless steel.
| - The Matronics Kolb-List Email Forum - | | Use the List Feature Navigator to browse the many List utilities available such as the Email Subscriptions page, Archive Search & Download, 7-Day Browse, Chat, FAQ, Photoshare, and much more:
http://www.matronics.com/Navigator?Kolb-List |
|
_________________ Richard Pike
Kolb MKIII N420P (420ldPoops)
Kingsport, TN 3TN0
Forgiving is tough, being forgiven is wonderful, and God's grace really is amazing. |
|
Back to top |
|
 |
neilsenrm(at)gmail.com Guest
|
Posted: Sat Jan 24, 2015 12:02 pm Post subject: 503 oil pump cable end wearing |
|
|
I don't know how the fittings are connected to the Rotax oil pump but most cable fittings rotate so that there is little or no ware on the soft cable ends or bending of the cable. Could you consider changing the attach fitting?
Rick Neilsen
Redrive VW Powered MKIIIC
On Sat, Jan 24, 2015 at 2:24 PM, Richard Pike <thegreybaron(at)charter.net (thegreybaron(at)charter.net)> wrote:
[quote]--> Kolb-List message posted by: "Richard Pike" <thegreybaron(at)charter.net (thegreybaron(at)charter.net)>
I only ever did this with brass. Did not know that you could solder anything to stainless steel.
--------
Richard Pike
Kolb MKIII N420P (420ldPoops)
Kingsport, TN 3TN0
My soul shall be joyful in the LORD; It shall rejoice in His salvation. Psalm 35:9
Read this topic online here:
http://forums.matronics.com/viewtopic.php?p=437568#437568
===========
-List" target="_blank">http://www.matronics.com/Navigator?Kolb-List
===========
FORUMS -
_blank">http://forums.matronics.com
===========
b Site -
-Matt Dralle, List Admin.
target="_blank">http://www.matronics.com/contribution
===========
[b]
| - The Matronics Kolb-List Email Forum - | | Use the List Feature Navigator to browse the many List utilities available such as the Email Subscriptions page, Archive Search & Download, 7-Day Browse, Chat, FAQ, Photoshare, and much more:
http://www.matronics.com/Navigator?Kolb-List |
|
|
|
Back to top |
|
 |
byoungplumbing(at)gmail.c Guest
|
Posted: Sat Jan 24, 2015 1:50 pm Post subject: 503 oil pump cable end wearing |
|
|
Soldering stainless steel requires a good flux. I did some experimenting..if I fluxed the SS cable and used a soldering iron without much success.... melted some solder in a half inch copper cap and dipped fluxed SS cable in the melted solder and it worked quite well
Boyd Young
[quote][b]
| - The Matronics Kolb-List Email Forum - | | Use the List Feature Navigator to browse the many List utilities available such as the Email Subscriptions page, Archive Search & Download, 7-Day Browse, Chat, FAQ, Photoshare, and much more:
http://www.matronics.com/Navigator?Kolb-List |
|
|
|
Back to top |
|
 |
Tom Jones
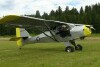
Joined: 12 Mar 2006 Posts: 752 Location: Ellensburg, WA
|
Posted: Sat Jan 24, 2015 2:17 pm Post subject: Re: 503 oil pump cable end wearing |
|
|
I was thinking of soldering the steel cable to secure it in the swedge using your method. The swedge is the only stainless part.
Richard Pike wrote: | I only ever did this with brass. Did not know that you could solder anything to stainless steel. |
Quote: | The adhesion of the solder to the swedge is now no longer the primary securing method, it is now complimentary to the physical size difference between the cable & the swedge. Clean up the excessive rat tail by taking a Dremel wheel and trimming the rat tailed exit end back smooth with the swedge. |
| - The Matronics Kolb-List Email Forum - | | Use the List Feature Navigator to browse the many List utilities available such as the Email Subscriptions page, Archive Search & Download, 7-Day Browse, Chat, FAQ, Photoshare, and much more:
http://www.matronics.com/Navigator?Kolb-List |
|
_________________ Tom Jones
Classic IV
503 Rotax, 72 inch Two blade Warp
Ellensburg, WA |
|
Back to top |
|
 |
rickofudall
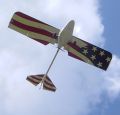
Joined: 19 Sep 2009 Posts: 1392 Location: Udall, KS, USA
|
Posted: Sat Jan 24, 2015 3:45 pm Post subject: 503 oil pump cable end wearing |
|
|
Tom, To solder the stainless steel you have to get through the oxide layer on the stainless. Most of the fluxes to accomplish this are acidic. The flux will wick up the cable and is difficult if not impossible to remove. On top of that you're going to have to get both parts red hot. Both operations are going to be bad for the cable.
Rick Girard
On Sat, Jan 24, 2015 at 4:17 PM, Tom Jones <nahsikhs(at)elltel.net (nahsikhs(at)elltel.net)> wrote:
Quote: | --> Kolb-List message posted by: "Tom Jones" <nahsikhs(at)elltel.net (nahsikhs(at)elltel.net)>
Richard Pike wrote:
> I only ever did this with brass. Did not know that you could solder anything to stainless steel.
I was thinking of soldering the steel cable to secure it in the swedge using your method. The swedge is the only stainless part.
> The adhesion of the solder to the swedge is now no longer the primary securing method, it is now complimentary to the physical size difference between the cable & the swedge. Clean up the excessive rat tail by taking a Dremel wheel and trimming the rat tailed exit end back smooth with the swedge.
--------
Tom Jones
Classic IV
503 Rotax, 72 inch Two blade Warp
Ellensburg, WA
Read this topic online here:
http://forums.matronics.com/viewtopic.php?p=437579#437579
===========
-List" target="_blank">http://www.matronics.com/Navigator?Kolb-List
===========
FORUMS -
_blank">http://forums.matronics.com
===========
b Site -
-Matt Dralle, List Admin.
target="_blank">http://www.matronics.com/contribution
===========
|
--
Believe those who are seeking the truth, doubt those who find it.
-Andre Gide
[quote][b]
| - The Matronics Kolb-List Email Forum - | | Use the List Feature Navigator to browse the many List utilities available such as the Email Subscriptions page, Archive Search & Download, 7-Day Browse, Chat, FAQ, Photoshare, and much more:
http://www.matronics.com/Navigator?Kolb-List |
|
_________________ The smallest miracle right in front of you is enough to make you happy.... |
|
Back to top |
|
 |
Tom Jones
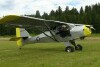
Joined: 12 Mar 2006 Posts: 752 Location: Ellensburg, WA
|
Posted: Sat Jan 24, 2015 4:11 pm Post subject: Re: 503 oil pump cable end wearing |
|
|
Well, I guess I'll go back to brass and hope for the best. I ordered 4 brass swedges so I can replace them every 20 hours or so I guess.
| - The Matronics Kolb-List Email Forum - | | Use the List Feature Navigator to browse the many List utilities available such as the Email Subscriptions page, Archive Search & Download, 7-Day Browse, Chat, FAQ, Photoshare, and much more:
http://www.matronics.com/Navigator?Kolb-List |
|
_________________ Tom Jones
Classic IV
503 Rotax, 72 inch Two blade Warp
Ellensburg, WA |
|
Back to top |
|
 |
Jim Baker
Joined: 30 Mar 2006 Posts: 181 Location: Sayre, PA
|
Posted: Sat Jan 24, 2015 7:28 pm Post subject: 503 oil pump cable end wearing |
|
|
I sure wouldn't settle for 20 hr replacement. Get inventive. The wear indicated, if truly from excessive vibration, would indicate that the barrel end had way too much room to move. The arm is, I believe, spring loaded...any thought to increasing that tension with an additional spring so the cable is under greater tension? I'd also think the grit induced wear theory is overblown. I would probably modify the cable end to the fork/swaged or soldered ball design and replace the brass barrel with a bolt. With a smaller ball one could forgo the fork and countersink the back of the bolt thru-cable hole to provide a seat for the ball. Any number of ways to modify. I'd also look at some large scale R/C aircraft fittings for ideas ( small all metal heim joint fittings come to mind ). http://store.rc4wd.com/High-Precision-Billet-Tie-Rod-End-M3-Silver_p_641.html Jim Baker [url=tel:4054265377]405.426.5377[/url]--
| - The Matronics Kolb-List Email Forum - | | Use the List Feature Navigator to browse the many List utilities available such as the Email Subscriptions page, Archive Search & Download, 7-Day Browse, Chat, FAQ, Photoshare, and much more:
http://www.matronics.com/Navigator?Kolb-List |
|
Description: |
|
Filesize: |
3.92 KB |
Viewed: |
22230 Time(s) |
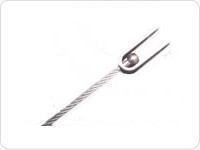
|
Description: |
|
Filesize: |
7.09 KB |
Viewed: |
22230 Time(s) |
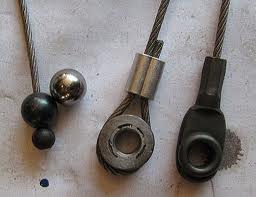
|
|
|
Back to top |
|
 |
Tom Jones
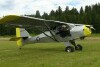
Joined: 12 Mar 2006 Posts: 752 Location: Ellensburg, WA
|
Posted: Sun Jan 25, 2015 5:57 am Post subject: Re: 503 oil pump cable end wearing |
|
|
Jim, thanks for those ideas. I have thought about your idea, "With a smaller ball one could forgo the fork and countersink the back of the bolt thru-cable hole to provide a seat for the ball".
I am also wondering about the fit of the brass barrel being a little loose in the pump lever.
The only place these parts seem to be available is from after market parts suppliers...not directly from Rotax. The suppliers all specify the barrel is 5/16. Every other part on my Rotax engine is metric. I was wondering about using an 8mm bolt for a better fit.
| - The Matronics Kolb-List Email Forum - | | Use the List Feature Navigator to browse the many List utilities available such as the Email Subscriptions page, Archive Search & Download, 7-Day Browse, Chat, FAQ, Photoshare, and much more:
http://www.matronics.com/Navigator?Kolb-List |
|
_________________ Tom Jones
Classic IV
503 Rotax, 72 inch Two blade Warp
Ellensburg, WA |
|
Back to top |
|
 |
John Hauck
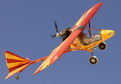
Joined: 09 Jan 2006 Posts: 4639 Location: Titus, Alabama (hauck's holler)
|
Posted: Sun Jan 25, 2015 6:01 am Post subject: 503 oil pump cable end wearing |
|
|
I think Jim B is correct, vibration and not grit.
I also think reinventing with bigger and different band aids won't fix the problem, which most likely is severe vibration.
Had a 582 with oil injection on my MKIII initially. Flew it about 225.0 hours in six months before I removed it permanently and went to a 912. As far as I know there was zero wear on this cable component. Replacing every 20 hours isn't the solution I'd be looking at.
Fix your vibration problem and most likely you will also fix your oil injection cable fitting problem.
john h
mkIII
Titus, Alabama
From: owner-kolb-list-server(at)matronics.com [mailto:owner-kolb-list-server(at)matronics.com] On Behalf Of jimbaker(at)npacc.net
Sent: Saturday, January 24, 2015 9:28 PM
To: kolb-list(at)matronics.com
Subject: Re: Re: 503 oil pump cable end wearing
I sure wouldn't settle for 20 hr replacement. Get inventive.
The wear indicated, if truly from excessive vibration, would indicate that the barrel end had way too much room to move. The arm is, I believe, spring loaded...any thought to increasing that tension with an additional spring so the cable is under greater tension? I'd also think the grit induced wear theory is overblown.
I would probably modify the cable end to the fork/swaged or soldered ball design and replace the brass barrel with a bolt. With a smaller ball one could forgo the fork and countersink the back of the bolt thru-cable hole to provide a seat for the ball. Any number of ways to modify. I'd also look at some large scale R/C aircraft fittings for ideas ( small all metal heim joint fittings come to mind ).
http://store.rc4wd.com/High-Precision-Billet-Tie-Rod-End-M3-Silver_p_641.html
Jim Baker
[url=tel:4054265377]405.426.5377[/url]
--
| - The Matronics Kolb-List Email Forum - | | Use the List Feature Navigator to browse the many List utilities available such as the Email Subscriptions page, Archive Search & Download, 7-Day Browse, Chat, FAQ, Photoshare, and much more:
http://www.matronics.com/Navigator?Kolb-List |
|
_________________ John Hauck
MKIII/912ULS
hauck's holler
Titus, Alabama |
|
Back to top |
|
 |
Jim Baker
Joined: 30 Mar 2006 Posts: 181 Location: Sayre, PA
|
Posted: Sun Jan 25, 2015 6:17 am Post subject: 503 oil pump cable end wearing |
|
|
All these barrels are throwbacks to motorcycles and their associated cables. All the real old bikes used nothing but this kind of termination, even for brakes. The elegant solution are the heim joint fittings. Can remove all slop and the angle of the cable to the arm becomes less critical unless it is rubbing excessively on the outer sheath. The design becomes self capturing with tje only failure point being the bolt thrubthe heim ball. The bill of materials would be one female threaded heim, one drilled threaded shank to which the cable could be soldered, a nut to prevent the shank from rotating in the heim. Done. Jim Baker [url=tel:4054265377]405.426.5377[/url]--
| - The Matronics Kolb-List Email Forum - | | Use the List Feature Navigator to browse the many List utilities available such as the Email Subscriptions page, Archive Search & Download, 7-Day Browse, Chat, FAQ, Photoshare, and much more:
http://www.matronics.com/Navigator?Kolb-List |
|
|
|
Back to top |
|
 |
rickofudall
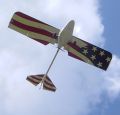
Joined: 19 Sep 2009 Posts: 1392 Location: Udall, KS, USA
|
Posted: Sun Jan 25, 2015 8:24 am Post subject: 503 oil pump cable end wearing |
|
|
Tom, There's .002" difference between 5/16 and 8 mm, .3125 vs .3145. I'd base the decision on which is cheaper, a brass cable stop or a steel oil pump bell crank. If it were me I'd rather the stop wear than the crank.Just a thought.
Rick Girard
do not archive
On Sun, Jan 25, 2015 at 7:57 AM, Tom Jones <nahsikhs(at)elltel.net (nahsikhs(at)elltel.net)> wrote:
Quote: | --> Kolb-List message posted by: "Tom Jones" <nahsikhs(at)elltel.net (nahsikhs(at)elltel.net)>
Jim, thanks for those ideas. I have thought about your idea, "With a smaller ball one could forgo the fork and countersink the back of the bolt thru-cable hole to provide a seat for the ball".
I am also wondering about the fit of the brass barrel being a little loose in the pump lever.
The only place these parts seem to be available is from after market parts suppliers...not directly from Rotax. The suppliers all specify the barrel is 5/16. Every other part on my Rotax engine is metric. I was wondering about using an 8mm bolt for a better fit.
--------
Tom Jones
Classic IV
503 Rotax, 72 inch Two blade Warp
Ellensburg, WA
Read this topic online here:
http://forums.matronics.com/viewtopic.php?p=437607#437607
===========
-List" target="_blank">http://www.matronics.com/Navigator?Kolb-List
===========
FORUMS -
_blank">http://forums.matronics.com
===========
b Site -
-Matt Dralle, List Admin.
target="_blank">http://www.matronics.com/contribution
===========
|
--
Believe those who are seeking the truth, doubt those who find it.
-Andre Gide
[quote][b]
| - The Matronics Kolb-List Email Forum - | | Use the List Feature Navigator to browse the many List utilities available such as the Email Subscriptions page, Archive Search & Download, 7-Day Browse, Chat, FAQ, Photoshare, and much more:
http://www.matronics.com/Navigator?Kolb-List |
|
_________________ The smallest miracle right in front of you is enough to make you happy.... |
|
Back to top |
|
 |
Tom Jones
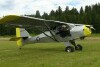
Joined: 12 Mar 2006 Posts: 752 Location: Ellensburg, WA
|
Posted: Sun Jan 25, 2015 8:34 am Post subject: Re: 503 oil pump cable end wearing |
|
|
Quote: | Tom, There's .002" difference between 5/16 and 8 mm, .3125 vs .3145. I'd base the decision on which is cheaper, a brass cable stop or a steel oil pump bell crank. If it were me I'd rather the stop wear than the crank.Just a thought.
Rick Girard
|
Our EAA club technical councilor has the same thinking as you do Rick. I asked him why they didn't make the swedge out of steel instead of brass. His reply was "Probably so the swedge will wear and not wear out the pump lever.
| - The Matronics Kolb-List Email Forum - | | Use the List Feature Navigator to browse the many List utilities available such as the Email Subscriptions page, Archive Search & Download, 7-Day Browse, Chat, FAQ, Photoshare, and much more:
http://www.matronics.com/Navigator?Kolb-List |
|
_________________ Tom Jones
Classic IV
503 Rotax, 72 inch Two blade Warp
Ellensburg, WA |
|
Back to top |
|
 |
|
|
You cannot post new topics in this forum You cannot reply to topics in this forum You cannot edit your posts in this forum You cannot delete your posts in this forum You cannot vote in polls in this forum You cannot attach files in this forum You can download files in this forum
|
Powered by phpBB © 2001, 2005 phpBB Group
|