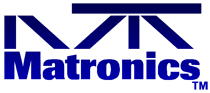 |
Matronics Email Lists Web Forum Interface to the Matronics Email Lists
|
View previous topic :: View next topic |
Author |
Message |
mark_trickel
Joined: 13 Dec 2011 Posts: 101 Location: Philadelphia, PA, USA
|
|
Back to top |
|
 |
bakerocb
Joined: 15 Jan 2006 Posts: 727 Location: FAIRFAX VA
|
Posted: Sun Mar 26, 2017 7:45 am Post subject: Can anybody confirm this? |
|
|
3/26/2017
Hello Mark, Yes. I can confirm this event. Here is the back story:
1) I was never happy with my first (#1) Lyle Hendricks round tube nose gear
strut. It was very sturdy, but it had two manufacturing / design defects in
my opinion.
a) The bottom vertical 3/4-16 threaded stud potion was too short. This meant
that a thin AN320-12 castle nut must be used instead of the normal
thickness AN310-12 castle nut. This further meant that the total nut-to-stud
thread interface holding the aluminum shoe and any washer stack up into
place was pretty limited. I was concerned that that interface could fail and
the entire shoe and nose wheel could fall off in flight.
b) The cotter pin hole through the bottom of that stud did not pass through
the center of the stud. This off set meant that the pin would not pass
through the normal castle notches in the AN320-12 nut. A person had to grind
/ file the nut notches wider in order for the cotter pin to pass through the
nut. This had two effects: ONE) The nut could not be rotated one notch at a
time to adjust the friction keeping the shoe from shimmying on landing roll
out unless each pair of notches was ground or filed wider. TWO) Grinding or
filing all pairs of notches wider further reduced the nut-to-stud thread
interface.
2) So my solution after over 500 flight hours with no problems other than
dealing with the two irritating issues described above was to have Lyle make
for me a new nose gear strut (#2) with modifications to eliminate the two
issues. I also had Lyle make some other design modifications to this #2
strut assembly such as a longer threaded portion at the top of the
compression rod and a welded cross bar at the bottom of the rod. The longer
threaded portion at the top of the rod gave more vertical adjustment
opportunity for the rod and the welded bar permitted one to hold the rod
from rotating when wrenching nuts at the top of the rod.
3) The #2 strut assembly was installed and I set off on its first test
flight. Unfortunately, not having any numerical figure available to measure
the shimmy prevention friction for the shoe, I used the TFAR (That Feels
About Right) criteria in tightening the AN310-12 nut holding the (new to me)
two Belleville washers up against the aluminum shoe. TFAR worked fine for a
few touch and go landings at an outlying field, but when I returned to my
home field (KHEF Manassas Virginia) for one final landing trouble showed up.
4) At a very slow speed on the final landing roll out the nose wheel began
to shimmy violently from side to side. This shimmy broke the two aluminum
nose wheel brackets at the bottom of the fire wall and allowed the strut
assembly to flop over sideways and the airplane nose to be lowered to the
runway surface. The damage consisted of grinding off a small portion of the
bottom of the #2 strut weldment, grinding off a bit of each wooden propeller
tip, and some scrapes off the bottom of the spinner, lower engine cowl, and
one of the main landing gear wheel pants. This event falls into the
categories of: "No good deed goes unpunished" or "If it ain't broke, don't
fix it". Take your choice.
5) The airplane was recovered to my hangar, Lyle graciously agreed to build
me strut assembly #3, Prince Aircraft repaired the propeller tips, I
replaced the spinner, repaired the engine cowling and the wheel pants, and
had them painted. I put everything back together once I had all pieces in
hand and used a 27 pound pull at the axle as my base figure for measuring
the friction for tightening the AN310-12 nut. I flew again for the first
time since the reported event on 10/18/2016. No nose wheel strut problems
since then. Thanks again go to Lyle.
Any questions?
OC
=====================================
From: mark_trickel
Sent: Sunday, March 26, 2017 3:57 AM
To: kis-list(at)matronics.com
Subject: Can anybody confirm this?
http://www.kathrynsreport.com/2016/08/kis-tr-1-n660c-incident-occurred-august.html
OC?
MT
| - The Matronics KIS-List Email Forum - | | Use the List Feature Navigator to browse the many List utilities available such as the Email Subscriptions page, Archive Search & Download, 7-Day Browse, Chat, FAQ, Photoshare, and much more:
http://www.matronics.com/Navigator?KIS-List |
|
|
|
Back to top |
|
 |
aeromomentum(at)yahoo.com Guest
|
Posted: Sun Mar 26, 2017 8:30 am Post subject: Can anybody confirm this? |
|
|
Hello OC,
How much weight do you have on your nose gear? Have you moved you main gear forward? As you may know the more weight on the nose the more energy to the shimmy. With more energy the less effective the friction damping. The geometry (pivot axis angle) could maybe use some tweaking to reduce shimmy.
Mark K.
--------------------------------------------
On Sun, 3/26/17, Owen Baker <bakerocb(at)cox.net> wrote:
Subject: Re: Can anybody confirm this?
To: kis-list(at)matronics.com, "TRICKEL MARK" <marktrickel(at)gmail.com>
Date: Sunday, March 26, 2017, 11:45 AM
"Owen Baker " <bakerocb(at)cox.net>
3/26/2017
Hello Mark, Yes. I can confirm this event. Here is the back
story:
1) I was never happy with my first (#1) Lyle Hendricks round
tube nose gear
strut. It was very sturdy, but it had two manufacturing /
design defects in
my opinion.
a) The bottom vertical 3/4-16 threaded stud potion was too
short. This meant
that a thin AN320-12 castle nut must be used instead
of the normal
thickness AN310-12 castle nut. This further meant that the
total nut-to-stud
thread interface holding the aluminum shoe and any washer
stack up into
place was pretty limited. I was concerned that that
interface could fail and
the entire shoe and nose wheel could fall off in flight.
b) The cotter pin hole through the bottom of that stud did
not pass through
the center of the stud. This off set meant that the pin
would not pass
through the normal castle notches in the AN320-12 nut. A
person had to grind
/ file the nut notches wider in order for the cotter pin to
pass through the
nut. This had two effects: ONE) The nut could not be rotated
one notch at a
time to adjust the friction keeping the shoe from shimmying
on landing roll
out unless each pair of notches was ground or filed wider.
TWO) Grinding or
filing all pairs of notches wider further reduced the
nut-to-stud thread
interface.
2) So my solution after over 500 flight hours with no
problems other than
dealing with the two irritating issues described above was
to have Lyle make
for me a new nose gear strut (#2) with modifications to
eliminate the two
issues. I also had Lyle make some other design modifications
to this #2
strut assembly such as a longer threaded portion at the top
of the
compression rod and a welded cross bar at the bottom of the
rod. The longer
threaded portion at the top of the rod gave more vertical
adjustment
opportunity for the rod and the welded bar permitted one to
hold the rod
from rotating when wrenching nuts at the top of the rod.
3) The #2 strut assembly was installed and I set off on its
first test
flight. Unfortunately, not having any numerical figure
available to measure
the shimmy prevention friction for the shoe, I used the TFAR
(That Feels
About Right) criteria in tightening the AN310-12 nut holding
the (new to me)
two Belleville washers up against the aluminum shoe. TFAR
worked fine for a
few touch and go landings at an outlying field, but when I
returned to my
home field (KHEF Manassas Virginia) for one final landing
trouble showed up.
4) At a very slow speed on the final landing roll out the
nose wheel began
to shimmy violently from side to side. This shimmy broke the
two aluminum
nose wheel brackets at the bottom of the fire wall and
allowed the strut
assembly to flop over sideways and the airplane nose to be
lowered to the
runway surface. The damage consisted of grinding off a small
portion of the
bottom of the #2 strut weldment, grinding off a bit of each
wooden propeller
tip, and some scrapes off the bottom of the spinner, lower
engine cowl, and
one of the main landing gear wheel pants. This event falls
into the
categories of: "No good deed goes unpunished" or "If it
ain't broke, don't
fix it". Take your choice.
5) The airplane was recovered to my hangar, Lyle graciously
agreed to build
me strut assembly #3, Prince Aircraft repaired the propeller
tips, I
replaced the spinner, repaired the engine cowling and the
wheel pants, and
had them painted. I put everything back together once I had
all pieces in
hand and used a 27 pound pull at the axle as my base figure
for measuring
the friction for tightening the AN310-12 nut. I flew again
for the first
time since the reported event on 10/18/2016. No nose wheel
strut problems
since then. Thanks again go to Lyle.
Any questions?
OC
=====================================
From: mark_trickel
Sent: Sunday, March 26, 2017 3:57 AM
To: kis-list(at)matronics.com
Subject: Can anybody confirm this?
http://www.kathrynsreport.com/2016/08/kis-tr-1-n660c-incident-occurred-august.html
OC?
MT
Forum -
- MATRONICS WEB FORUMS -
MATRONICS LIST WIKI -
List Contribution Web Site -
-Matt
Dralle, List Admin.
| - The Matronics KIS-List Email Forum - | | Use the List Feature Navigator to browse the many List utilities available such as the Email Subscriptions page, Archive Search & Download, 7-Day Browse, Chat, FAQ, Photoshare, and much more:
http://www.matronics.com/Navigator?KIS-List |
|
|
|
Back to top |
|
 |
bakerocb
Joined: 15 Jan 2006 Posts: 727 Location: FAIRFAX VA
|
Posted: Sun Mar 26, 2017 2:30 pm Post subject: Can anybody confirm this? |
|
|
3/26/2017
Hello Mark K, Thanks for your input. You wrote:
1) "Have you moved you main gear forward?"
Yes, I wedged it forward with flox. The main landing gear axles are 72.25
inches aft of the 0.00 datum point.
That datum point is, in turn, 32.00 inches forward of the engine cowling
joggle on the fuselage.
2) "How much weight do you have on your nose gear?"
Right now, in operational configuration and without reweighing, I don't
know.
The original empty aircraft weighing showed 242 pounds on the nose gear.
Since then there have been a few misc items (quart of oil, jar for fuel
testing, rags, etc.)
that are normally kept in the right baggage well.
Also there are some other misc items (hand held radio, small tool bag, water
bottle, roll of tape, etc.) that have taken up permanent lodging on the hat
shelf aft of the seats.
Not too long ago I double bagged sand into two kitchen sliding lock plastic
gallon bags (they totaled 23 pounds) and placed them over the battery box in
the far right rear corner of the right baggage well (I mostly fly solo in
the left seat) because I was unhappy that the nose gear was descending to
meet the runway too quickly after the main gear touched down. I am not sure
if that has helped, or if so how much.
3) "The geometry (pivot axis angle) could maybe use some tweaking to reduce
shimmy."
Can you please elaborate on the contribution of the pivot angle axis on
shimmy and how one would go about tweaking that angle in a KIS TR-1? Thanks.
Also a reminder that my shimmy problem with strut #2 was my fault for not
tightening the friction nut enough and I have had no shimmy problems since
installing strut #3 and using 27 pounds as a base figure for setting the
friction nut.
Also in my listing of the design / manufacturing defects in the #1 strut in
paragraph 1 below I forget to mention that the off center cotter pin hole
was also so close to the end of the vertical stub that I was concerned about
the possibility of break out.
OC
PS: I have your last name spelled Kettering in some old places in my
computer. Has there been a change?
========================================
From: M Ketteing
Sent: Sunday, March 26, 2017 12:30 PM
To: kis-list(at)matronics.com ; TRICKEL MARK
Subject: Re: Can anybody confirm this?
Hello OC,
How much weight do you have on your nose gear? Have you moved you main gear
forward? As you may know the more weight on the nose the more energy to the
shimmy. With more energy the less effective the friction damping. The
geometry (pivot axis angle) could maybe use some tweaking to reduce shimmy.
Mark K.
--------------------------------------------
On Sun, 3/26/17, Owen Baker <bakerocb(at)cox.net> wrote:
Subject: Re: Can anybody confirm this?
To: kis-list(at)matronics.com, "TRICKEL MARK" <marktrickel(at)gmail.com>
Date: Sunday, March 26, 2017, 11:45 AM
"Owen Baker " <bakerocb(at)cox.net>
3/26/2017
Hello Mark, Yes. I can confirm this event. Here is the back
story:
1) I was never happy with my first (#1) Lyle Hendricks round
tube nose gear
strut. It was very sturdy, but it had two manufacturing /
design defects in
my opinion.
a) The bottom vertical 3/4-16 threaded stud potion was too
short. This meant
that a thin AN320-12 castle nut must be used instead
of the normal
thickness AN310-12 castle nut. This further meant that the
total nut-to-stud
thread interface holding the aluminum shoe and any washer
stack up into
place was pretty limited. I was concerned that that
interface could fail and
the entire shoe and nose wheel could fall off in flight.
b) The cotter pin hole through the bottom of that stud did
not pass through
the center of the stud. This off set meant that the pin
would not pass
through the normal castle notches in the AN320-12 nut. A
person had to grind
/ file the nut notches wider in order for the cotter pin to
pass through the
nut. This had two effects: ONE) The nut could not be rotated
one notch at a
time to adjust the friction keeping the shoe from shimmying
on landing roll
out unless each pair of notches was ground or filed wider.
TWO) Grinding or
filing all pairs of notches wider further reduced the
nut-to-stud thread
interface.
2) So my solution after over 500 flight hours with no
problems other than
dealing with the two irritating issues described above was
to have Lyle make
for me a new nose gear strut (#2) with modifications to
eliminate the two
issues. I also had Lyle make some other design modifications
to this #2
strut assembly such as a longer threaded portion at the top
of the
compression rod and a welded cross bar at the bottom of the
rod. The longer
threaded portion at the top of the rod gave more vertical
adjustment
opportunity for the rod and the welded bar permitted one to
hold the rod
from rotating when wrenching nuts at the top of the rod.
3) The #2 strut assembly was installed and I set off on its
first test
flight. Unfortunately, not having any numerical figure
available to measure
the shimmy prevention friction for the shoe, I used the TFAR
(That Feels
About Right) criteria in tightening the AN310-12 nut holding
the (new to me)
two Belleville washers up against the aluminum shoe. TFAR
worked fine for a
few touch and go landings at an outlying field, but when I
returned to my
home field (KHEF Manassas Virginia) for one final landing
trouble showed up.
4) At a very slow speed on the final landing roll out the
nose wheel began
to shimmy violently from side to side. This shimmy broke the
two aluminum
nose wheel brackets at the bottom of the fire wall and
allowed the strut
assembly to flop over sideways and the airplane nose to be
lowered to the
runway surface. The damage consisted of grinding off a small
portion of the
bottom of the #2 strut weldment, grinding off a bit of each
wooden propeller
tip, and some scrapes off the bottom of the spinner, lower
engine cowl, and
one of the main landing gear wheel pants. This event falls
into the
categories of: "No good deed goes unpunished" or "If it
ain't broke, don't
fix it". Take your choice.
5) The airplane was recovered to my hangar, Lyle graciously
agreed to build
me strut assembly #3, Prince Aircraft repaired the propeller
tips, I
replaced the spinner, repaired the engine cowling and the
wheel pants, and
had them painted. I put everything back together once I had
all pieces in
hand and used a 27 pound pull at the axle as my base figure
for measuring
the friction for tightening the AN310-12 nut. I flew again
for the first
time since the reported event on 10/18/2016. No nose wheel
strut problems
since then. Thanks again go to Lyle.
Any questions?
OC
=====================================
From: mark_trickel
Sent: Sunday, March 26, 2017 3:57 AM
To: kis-list(at)matronics.com
Subject: Can anybody confirm this?
http://www.kathrynsreport.com/2016/08/kis-tr-1-n660c-incident-occurred-august.html
OC?
MT
| - The Matronics KIS-List Email Forum - | | Use the List Feature Navigator to browse the many List utilities available such as the Email Subscriptions page, Archive Search & Download, 7-Day Browse, Chat, FAQ, Photoshare, and much more:
http://www.matronics.com/Navigator?KIS-List |
|
|
|
Back to top |
|
 |
ftyoder(at)yoderbuilt.com Guest
|
Posted: Sun Mar 26, 2017 5:33 pm Post subject: Can anybody confirm this? |
|
|
OC,
My main gear on N52TY are 74.25" aft of the 0.00 datum point and the nose
gear weighs 245#. I added 1 1/2" to my elevator cord which helps hold the
nose gear off at touch down.
Tim
--
| - The Matronics KIS-List Email Forum - | | Use the List Feature Navigator to browse the many List utilities available such as the Email Subscriptions page, Archive Search & Download, 7-Day Browse, Chat, FAQ, Photoshare, and much more:
http://www.matronics.com/Navigator?KIS-List |
|
|
|
Back to top |
|
 |
mark_trickel
Joined: 13 Dec 2011 Posts: 101 Location: Philadelphia, PA, USA
|
Posted: Mon Mar 27, 2017 5:19 am Post subject: Re: Can anybody confirm this? |
|
|
OC, thank you for the details of this situation. When any occurrence happens within our small community I feel it is very important that all details are covered so we can learn from it. The unfortunate part is that only a very small percentage of our community frequent this forum.
I was aware you were having Lyle make you a new nose gear with changes. I was aware you were looking for torque specs, but I missed the mishap.
My questions are:
On nose gear #1 – That was a little disheartening to learn the stud was too short to allow for a proper stack, and that the hole was off center and too close to the end of the stud. Now that makes me fearful about the rest of the fleet that might have this nose gear version. I am curious to know if you might have considered milling the surface of the shoe to allow of a proper stack? That may have eliminated one of your two issues and a proper stack with Belleville washers in place could have remedied your second issue to only having to modified the castle nut in one cotter pin slot. What was in your original stack?
On nose gear #2 – What was in the stack? Did you have steel washers on both sides (above and below) of the Belleville washers? Did you have the Belleville washers in direct contact with the aluminum shoe?
Weight and balance – Where do you estimate your CG was at the time of this episode? We all know the forward and aft limits of the TR-1 but simply having the CG at the forward limit is not good enough (IMO). The CG needs to be closer to the center and in the best-case scenario closer to the aft limit as that is where it is most efficient.
So I understand you had a nose gear collapse similar to Galin. Your spinner hit the runway. The engine was most likely at idol say 800 to 900 rpm at the time of impact. How many times did each blade strike the runway? And this prop was repairable?
Nose gear #3 – third time is always a charm!
MT
| - The Matronics KIS-List Email Forum - | | Use the List Feature Navigator to browse the many List utilities available such as the Email Subscriptions page, Archive Search & Download, 7-Day Browse, Chat, FAQ, Photoshare, and much more:
http://www.matronics.com/Navigator?KIS-List |
|
|
|
Back to top |
|
 |
Keith.Miller(at)esa.int Guest
|
Posted: Mon Mar 27, 2017 6:52 am Post subject: Can anybody confirm this? |
|
|
I think it was a bit a bad luck with OC 's shortened stud . Mine was made a
few months later by Lyle and he had noted the problem and fixed it, so i
guess it depends upon when it was made in the production series
(See attached file: IMG_9929.JPG)
From: "mark_trickel" <marktrickel(at)gmail.com>
To: kis-list(at)matronics.com
Date: 03/27/2017 03:23 PM
Subject: Re: Can anybody confirm this?
Sent by: owner-kis-list-server(at)matronics.com
OC, thank you for the details of this situation. When any occurrence happens
within our small community I feel it is very important that all details are
covered so we can learn from it. The unfortunate part is that only a very
small percentage of our community frequent this forum.
I was aware you were having Lyle make you a new nose gear with changes. I was
aware you were looking for torque specs, but I missed the mishap.
My questions are:
On nose gear #1 ??? That was a little disheartening to learn the stud was too
short to allow for a proper stack, and that the hole was off center and too
close to the end of the stud. Now that makes me fearful about the rest of the
fleet that might have this nose gear version. I am curious to know if you
might have considered milling the surface of the shoe to allow of a proper
stack? That may have eliminated one of your two issues and a proper stack
with Belleville washers in place could have remedied your second issue to
only having to modified the castle nut in one cotter pin slot. What was in
your original stack?
On nose gear #2 ??? What was in the stack? Did you have steel washers on both
sides (above and below) of the Belleville washers? Did you have the
Belleville washers in direct contact with the aluminum shoe?
Weight and balance ??? Where do you estimate your CG was at the time of this
episode? We all know the forward and aft limits of the TR-1 but simply having
the CG at the forward limit is not good enough (IMO). The CG needs to be
closer to the center and in the best-case scenario closer to the aft limit as
that is where it is most efficient.
So I understand you had a nose gear collapse similar to Galin. Your spinner
hit the runway. The engine was most likely at idol say 800 to 900 rpm at the
time of impact. How many times did each blade strike the runway? And this
prop was repairable?
Nose gear #3 ??? third time is always a charm!
MT
Read this topic online here:
http://forums.matronics.com/viewtopic.php?p=467672#467672
This message and any attachments are intended for the use of the addressee or
addressees only.
The unauthorised disclosure, use, dissemination or copying (either in whole
or in part) of its
content is not permitted.
If you received this message in error, please notify the sender and delete it
from your system.
Emails can be altered and their integrity cannot be guaranteed by the sender.
Please consider the environment before printing this email.
This message and any attachments are intended for the use of the addressee or addressees only.
The unauthorised disclosure, use, dissemination or copying (either in whole or in part) of its
content is not permitted.
If you received this message in error, please notify the sender and delete it from your system.
Emails can be altered and their integrity cannot be guaranteed by the sender.
Please consider the environment before printing this email.
| - The Matronics KIS-List Email Forum - | | Use the List Feature Navigator to browse the many List utilities available such as the Email Subscriptions page, Archive Search & Download, 7-Day Browse, Chat, FAQ, Photoshare, and much more:
http://www.matronics.com/Navigator?KIS-List |
|
Description: |
|
Filesize: |
2.93 MB |
Viewed: |
17264 Time(s) |
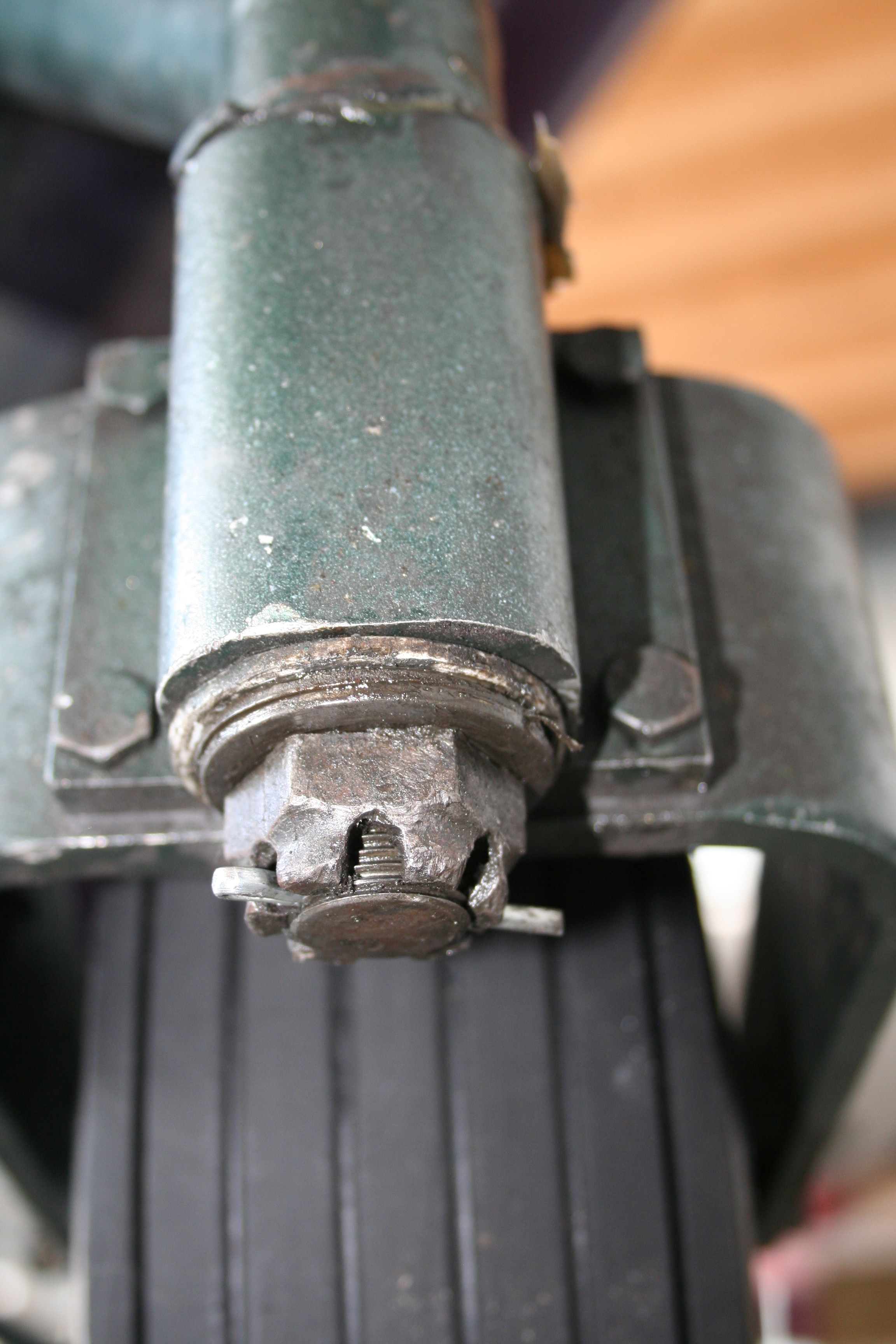
|
|
|
Back to top |
|
 |
bakerocb
Joined: 15 Jan 2006 Posts: 727 Location: FAIRFAX VA
|
Posted: Mon Mar 27, 2017 9:22 am Post subject: Can anybody confirm this? |
|
|
3/27/2017
Hello Keith, Thanks for your input. You wrote:
1) ".... he had noted the problem and fixed it..."
I don't think so. Your picture appears to also show a thin AN320-12 shear
type castle nut in place with a fairly thin washer stack up (Bellevilles?).
This would be consistent with the same length of the 3/4 inch diameter
portion of the vertical stub as my #1 Lyle gear. I have seen no evidence
that Lyle changed the length of the 3/4 inch diameter portion of the
vertical stub until (at my request) he made it a bit longer for my #2 and #3
weldments.
See the attached picture of the vertical stub on my #1 Lyle nose gear. I
initially thought that the 3/4 inch diameter portion of the vertical stub
was a machined out and threaded continuation of the vertical stub steel
immediately above it (all one solid piece). I later learned that I was wrong
and that the 3/4 inch diameter portion was, in fact, a separately obtained
bolt whose head (maybe machined round first) was inserted into a hole in the
steel above it and welded into place. Only after removing my #1 Lyle gear
from the plane and examining the end of the vertical stub with a bright
light and a magnifying glass was I able to see the evidence of a weld bead.
I speculate that Lyle obtained these bolts from McMaster-Carr and that the
quality control of the original manufacturer of these bolts was not
pristine. The cotter pin holes were not exactly through the center of the
bolt (I have noticed a bit of this on the bolts in my #2 and #3 Lyle gears
as well) and the cotter pin hole in the end of the bolt in my #1 Lyle gear
was too close to the end of the bolt for my comfort.
Any questions?
OC
=============================================
From: Keith.Miller(at)esa.int
Sent: Monday, March 27, 2017 10:45 AM
To: kis-list(at)matronics.com
Subject: Re: Re: Can anybody confirm this?
I think it was a bit a bad luck with OC 's shortened stud . Mine was made a
few months later by Lyle and he had noted the problem and fixed it, so i
guess it depends upon when it was made in the production series
| - The Matronics KIS-List Email Forum - | | Use the List Feature Navigator to browse the many List utilities available such as the Email Subscriptions page, Archive Search & Download, 7-Day Browse, Chat, FAQ, Photoshare, and much more:
http://www.matronics.com/Navigator?KIS-List |
|
Description: |
|
Filesize: |
638.4 KB |
Viewed: |
17263 Time(s) |
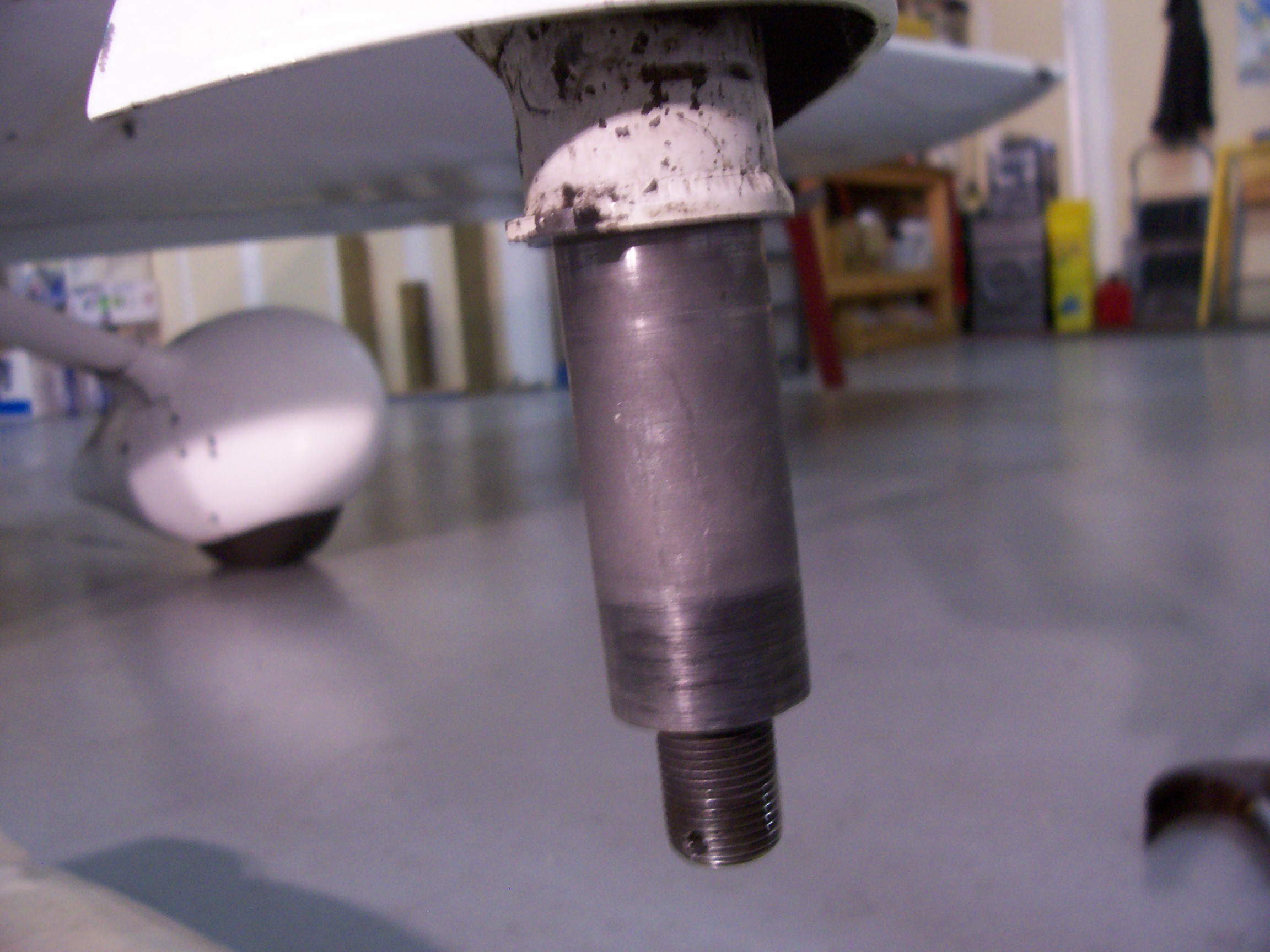
|
|
|
Back to top |
|
 |
pastormac62
Joined: 07 Sep 2015 Posts: 71 Location: Indiana
|
Posted: Mon Mar 27, 2017 9:50 am Post subject: Can anybody confirm this? |
|
|
Hi Guys,
Speaking of the nose gear. I'm getting quite a bit of shimmy on take off and landing. Is there an adjustment I can make?
Thanks!!
Steve
Sent from my iPhone
Quote: | On Mar 27, 2017, at 1:21 PM, Owen Baker <bakerocb(at)cox.net> wrote:
3/27/2017
Hello Keith, Thanks for your input. You wrote:
1) ".... he had noted the problem and fixed it..."
I don't think so. Your picture appears to also show a thin AN320-12 shear type castle nut in place with a fairly thin washer stack up (Bellevilles?). This would be consistent with the same length of the 3/4 inch diameter portion of the vertical stub as my #1 Lyle gear. I have seen no evidence that Lyle changed the length of the 3/4 inch diameter portion of the vertical stub until (at my request) he made it a bit longer for my #2 and #3 weldments.
See the attached picture of the vertical stub on my #1 Lyle nose gear. I initially thought that the 3/4 inch diameter portion of the vertical stub was a machined out and threaded continuation of the vertical stub steel immediately above it (all one solid piece). I later learned that I was wrong and that the 3/4 inch diameter portion was, in fact, a separately obtained bolt whose head (maybe machined round first) was inserted into a hole in the steel above it and welded into place. Only after removing my #1 Lyle gear from the plane and examining the end of the vertical stub with a bright light and a magnifying glass was I able to see the evidence of a weld bead.
I speculate that Lyle obtained these bolts from McMaster-Carr and that the quality control of the original manufacturer of these bolts was not pristine. The cotter pin holes were not exactly through the center of the bolt (I have noticed a bit of this on the bolts in my #2 and #3 Lyle gears as well) and the cotter pin hole in the end of the bolt in my #1 Lyle gear was too close to the end of the bolt for my comfort.
Any questions?
OC
=============================================
From: Keith.Miller(at)esa.int
Sent: Monday, March 27, 2017 10:45 AM
To: kis-list(at)matronics.com
Subject: Re: Re: Can anybody confirm this?
I think it was a bit a bad luck with OC 's shortened stud . Mine was made a
few months later by Lyle and he had noted the problem and fixed it, so i
guess it depends upon when it was made in the production series
<4-9-16 CAMERA 003.JPG>
|
| - The Matronics KIS-List Email Forum - | | Use the List Feature Navigator to browse the many List utilities available such as the Email Subscriptions page, Archive Search & Download, 7-Day Browse, Chat, FAQ, Photoshare, and much more:
http://www.matronics.com/Navigator?KIS-List |
|
|
|
Back to top |
|
 |
bakerocb
Joined: 15 Jan 2006 Posts: 727 Location: FAIRFAX VA
|
Posted: Mon Mar 27, 2017 11:00 am Post subject: Can anybody confirm this? |
|
|
3/27/2017
Hello Mark, You wrote:
1) "I am curious to know if you might have considered milling the surface of
the shoe to allow of a proper stack?"
This is not a feasible solution. The bottom surface of the shoe must project
down below the shoulder above the 3/4 inch diameter portion of the vertical
stub so that any washers contact the bottom of the shoe and not the shoulder
of the stub. This washer contact with the bottom of the shoe is what applies
the friction force on the shoe that keeps it from shimmying. In one of the
newsletters there is an article, along with a sketch, that emphasizes this
point.
2) "... a proper stack with Belleville washers in place could have remedied
your second issue to only having to modified the castle nut in one cotter
pin slot."
I operated with only one pair of widened notches in the castle nut for some
period of time. This became a nuisance when I wanted to make a small
friction adjustment without disturbing and reshuffling the entire washer
stack.
What you are suggesting here is that the friction level be adjusted by
inserting or removing washers to obtain the desired results rather than just
turning the nut. This is a rather crude manner of adjusting the friction and
it could take many tries (and many different washer thicknesses) to achieve
the desired results. As a side note: Realize also that the nut must be
prevented from rotating by sticking an ice pick or something similar through
the cotter key passage every time the shoe is rotated for testing of the
friction level. It always bothered me a bit that the nut rotated back and
forth a little bit with the change in direction of the movement of the shoe
even with the cotter pin in place. I eventually solved that problem, if it
was a problem, by replacing the cotter pin with a #6 hex socket head cap
screw, two washers, and an elastic stop nut.
3) "What was in your original stack?"
One or more 1/8 inch thick nylon washers and flat metal washers as needed to
fit in the limited height available and obtained the desired friction level.
4) "On nose gear #2 – What was in the stack?"
Either two or four Belleville washers -- I can not exactly recall.
5) "Did you have steel washers on both sides (above and below) of the
Belleville washers?"
I did not. Even with the provided increased length of the 3/4 inch diameter
portion of the vertical stub there was insufficient room to accommodate flat
washers in addition to the Belleville washers and the full size AN310-12
castle nut. (I had asked Lyle to make the 3/4 inch portion of the vertical
stub longer than he provided, but he declined to do so.)
6) "Did you have the Belleville washers in direct contact with the aluminum
shoe?"
Yes, but it was not my desire to do it that way. See 5 above.
7) "Where do you estimate your CG was at the time of this episode?"
Some where between 61.50 and 65.60 inches aft of the datum point.
"How many times did each blade strike the runway?"
Here is how I responded to a local pilot who asked a similarly motivated
question about engine stoppage:
"The engine did not experience sudden stoppage in the current factory
documented concept in my opinion. First point: This is a
wooden prop and all the current literature assumes a metal prop which can
deliver a much more abrupt shock to an engine crankshaft. Second point: Each
of the propeller blades had a small and equal amount of material scraped off
of its tip with no significant impact rotational damage appearing any
further towards the propeller hub.
I considered pulling the engine and sending it to one of the three
organizations that the factory rep recommended when I talked to him about my
situation. I also reviewed the Continental documentation on what they
considered an acceptable tear down inspection. It was practically back to
the ore that the metal had been forged from -- no bit was to be left
connected to any other bit. I also thought back to my training at the
Continental factory before I bought my engine and remembered the tooling,
extreme precision, and care that was needed in assembling an engine. I just
did not believe that: a) That degree of disassembly was needed. b) No field
activity in their right mind would go to the disassembly level called for in
the Continental documentation. c) Regardless of the level of disassembly at
the field activity I doubted their ability to put the engine back together
as well as it was currently put together by the factory. I had more
confidence in the engine as it existed than after a tear down and reassembly
by some non factory field activity."
9) "And this prop was repairable?"
The tips were repaired by the Prince factory in a few weeks and the engine,
prop, plane, and pilot have flown 15 hours since the event.
OC
PS: I can appreciate that people are reading all sorts of things into this
event and asking all sorts of questions that I am willing to answer. But I
ask all to remember that this event was a direct result of the mechanic (me)
installing Lyle gear #2 with no numerical friction level information at hand
and using the criteria of TFAR (That Feels About Right) to set the friction
level. It was right for a few landings and then it wasn't.
===============================
From: mark_trickel
Sent: Monday, March 27, 2017 9:19 AM
To: kis-list(at)matronics.com
Subject: Re: Can anybody confirm this?
OC, thank you for the details of this situation. When any occurrence happens
within our small community I feel it is very important that all details are
covered so we can learn from it. The unfortunate part is that only a very
small percentage of our community frequent this forum.
I was aware you were having Lyle make you a new nose gear with changes. I
was aware you were looking for torque specs, but I missed the mishap.
My questions are:
On nose gear #1 – That was a little disheartening to learn the stud was
too short to allow for a proper stack, and that the hole was off center and
too close to the end of the stud. Now that makes me fearful about the rest
of the fleet that might have this nose gear version. I am curious to know if
you might have considered milling the surface of the shoe to allow of a
proper stack? That may have eliminated one of your two issues and a proper
stack with Belleville washers in place could have remedied your second issue
to only having to modified the castle nut in one cotter pin slot. What was
in your original stack?
On nose gear #2 – What was in the stack? Did you have steel washers on
both sides (above and below) of the Belleville washers? Did you have the
Belleville washers in direct contact with the aluminum shoe?
Weight and balance – Where do you estimate your CG was at the time of this
episode? We all know the forward and aft limits of the TR-1 but simply
having the CG at the forward limit is not good enough (IMO). The CG needs to
be closer to the center and in the best-case scenario closer to the aft
limit as that is where it is most efficient.
So I understand you had a nose gear collapse similar to Galin. Your spinner
hit the runway. The engine was most likely at idol say 800 to 900 rpm at the
time of impact. How many times did each blade strike the runway? And this
prop was repairable?
Nose gear #3 – third time is always a charm!
MT
| - The Matronics KIS-List Email Forum - | | Use the List Feature Navigator to browse the many List utilities available such as the Email Subscriptions page, Archive Search & Download, 7-Day Browse, Chat, FAQ, Photoshare, and much more:
http://www.matronics.com/Navigator?KIS-List |
|
|
|
Back to top |
|
 |
bakerocb
Joined: 15 Jan 2006 Posts: 727 Location: FAIRFAX VA
|
Posted: Mon Mar 27, 2017 12:27 pm Post subject: Can anybody confirm this? |
|
|
3/27/2017
Hello Steve, You wrote: "Is there an adjustment I can make?"
This is very dangerous. DO NOT FLY THIS PLANE until the friction nut on the
bottom of the nose gear has been properly adjusted.
See the photo from Keith Miller (thanks Keith) that is attached to this
email.
This shimmy can become violent enough to damage the nose gear linkages,
collapse the nose gear, and cause the nose of the airplane to fall down and
contact the runway surface.
I recommend:
1) Elevate the nose of the plane so that the nose tire is off the ground.
(Contact me if needed for tips on how to do this.)
2) Attach a fish scale to the shoe holding the nose wheel in the vicinity of
the wheel axle. See how many pounds of pull that it takes to move the shoe
from side to side. This is to establish what the friction level is now. If
it is several pounds less than 27 pounds (which it probably is because of
the shimmy) you must adjust the friction level.
3) Use a black sharpie pen to number the nut notch above the cotter pin
head as notch 1. Make a vertical mark on the shoe above notch 1 with the
sharpie.
4) Remove the cotter pin holding the large AN320-12 castle nut from turning.
Go around the nut with the sharpie numbering each notch in sequence. This is
so that you can keep track of the notch that is under the vertical mark.
5) Using a 1 1/8 inch box wrench tighten the nut one notch. Use an ice pick
or similar item to ensure that the new nut notch and the cotter pin hole
through the vertical stub are aligned. Leave the ice pick in place.
6) Use the fish scale again to move the shoe back and forth to ensure that
you have adjusted the friction to the vicinity of 27 pounds.
7) Remove the ice pick and repeat 5 and 6 above if needed. When you have the
desired friction level set, install a new cotter pin and lower the nose tire
to the ground.
Go fly the plane.
Any questions?
OC
================================
From: pastormac(at)comcast.net
Sent: Monday, March 27, 2017 1:50 PM
To: kis-list(at)matronics.com
Subject: Re: Re: Can anybody confirm this?
Hi Guys,
Speaking of the nose gear. I'm getting quite a bit of shimmy on take off and
landing. Is there an adjustment I can make?
Thanks!!
Steve
| - The Matronics KIS-List Email Forum - | | Use the List Feature Navigator to browse the many List utilities available such as the Email Subscriptions page, Archive Search & Download, 7-Day Browse, Chat, FAQ, Photoshare, and much more:
http://www.matronics.com/Navigator?KIS-List |
|
Description: |
|
Filesize: |
2.93 MB |
Viewed: |
17262 Time(s) |
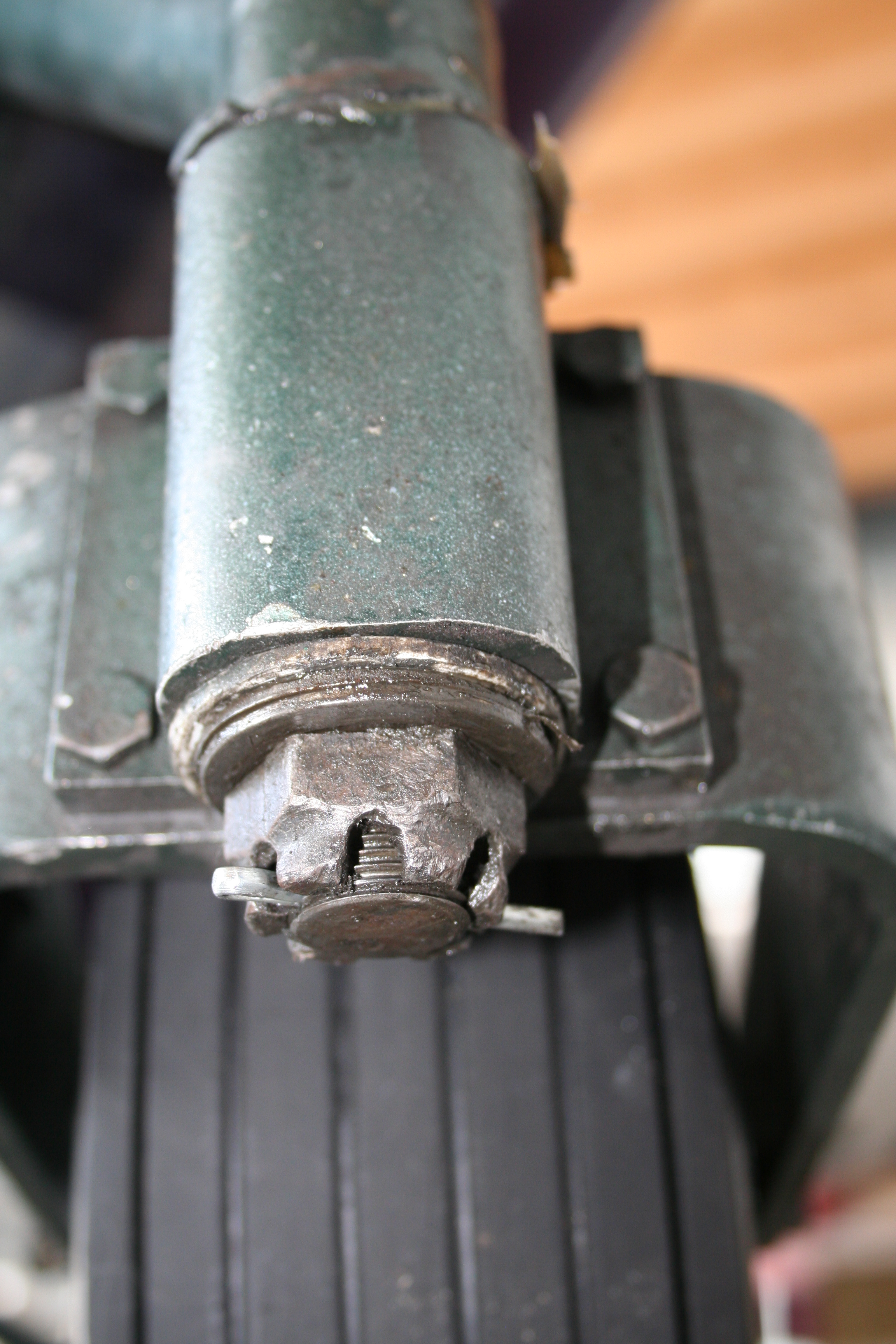
|
|
|
Back to top |
|
 |
galinhdz(at)gmail.com Guest
|
Posted: Mon Mar 27, 2017 12:47 pm Post subject: Can anybody confirm this? |
|
|
FWIW Rich told me to adjust the nose gear friction to between 20 and 35lbs of break force with 27lb being optimal. He did say that 20lbs was an absolute minimum, that 20lbs might not work in some cases and not to worry about being super accurate. I still have the cheap Walmart fish weight scale he got for me in El Salvador just like this one:
https://www.walmart.com/ip/Berkley-Scale-with-Tape/16637411
I try to adjust mine for 27lbs but take anything over 25lbs. This has worked well for me in the last 10yrs of flying my TR-4. YMMV
On Mon, Mar 27, 2017 at 1:50 PM, <pastormac(at)comcast.net (pastormac(at)comcast.net)> wrote:
Quote: | --> KIS-List message posted by: pastormac(at)comcast.net (pastormac(at)comcast.net)
Hi Guys,
Speaking of the nose gear. I'm getting quite a bit of shimmy on take off and landing. Is there an adjustment I can make?
Thanks!!
Steve
Sent from my iPhone
> On Mar 27, 2017, at 1:21 PM, Owen Baker <bakerocb(at)cox.net (bakerocb(at)cox.net)> wrote:
>
> 3/27/2017
>
> Hello Keith, Thanks for your input. You wrote:
>
> 1) ".... he had noted the problem and fixed it..."
>
> I don't think so. Your picture appears to also show a thin AN320-12 shear type castle nut in place with a fairly thin washer stack up (Bellevilles?). This would be consistent with the same length of the 3/4 inch diameter portion of the vertical stub as my #1 Lyle gear. I have seen no evidence that Lyle changed the length of the 3/4 inch diameter portion of the vertical stub until (at my request) he made it a bit longer for my #2 and #3 weldments.
>
> See the attached picture of the vertical stub on my #1 Lyle nose gear. I initially thought that the 3/4 inch diameter portion of the vertical stub was a machined out and threaded continuation of the vertical stub steel immediately above it (all one solid piece). I later learned that I was wrong and that the 3/4 inch diameter portion was, in fact, a separately obtained bolt whose head (maybe machined round first) was inserted into a hole in the steel above it and welded into place. Only after removing my #1 Lyle gear from the plane and examining the end of the vertical stub with a bright light and a magnifying glass was I able to see the evidence of a weld bead.
>
> I speculate that Lyle obtained these bolts from McMaster-Carr and that the quality control of the original manufacturer of these bolts was not pristine. The cotter pin holes were not exactly through the center of the bolt (I have noticed a bit of this on the bolts in my #2 and #3 Lyle gears as well) and the cotter pin hole in the end of the bolt in my #1 Lyle gear was too close to the end of the bolt for my comfort.
>
> Any questions?
>
> OC
>
> =============================================
>
> From: Keith.Miller(at)esa.int (Keith.Miller(at)esa.int)
> Sent: Monday, March 27, 2017 10:45 AM
> To: kis-list(at)matronics.com (kis-list(at)matronics.com)
> Subject: Re: Re: Can anybody confirm this?
>
> I think it was a bit a bad luck with OC 's shortened stud . Mine was made a
> few months later by Lyle and he had noted the problem and fixed it, so i
> guess it depends upon when it was made in the production series
>
>
Quote: | <4-9-16 CAMERA 003.JPG>
|
====================================
List" rel="noreferrer" target="_blank">http://www.matronics.com/Navigator?KIS-List
====================================
FORUMS -
eferrer" target="_blank">http://forums.matronics.com
====================================
WIKI -
errer" target="_blank">http://wiki.matronics.com
====================================
b Site -
-Matt Dralle, List Admin.
rel="noreferrer" target="_blank">http://www.matronics.com/contribution
====================================
|
| - The Matronics KIS-List Email Forum - | | Use the List Feature Navigator to browse the many List utilities available such as the Email Subscriptions page, Archive Search & Download, 7-Day Browse, Chat, FAQ, Photoshare, and much more:
http://www.matronics.com/Navigator?KIS-List |
|
|
|
Back to top |
|
 |
galinhdz(at)gmail.com Guest
|
Posted: Mon Mar 27, 2017 12:47 pm Post subject: Can anybody confirm this? |
|
|
Wrong Walmart link. THIS is the one I have
https://www.walmart.com/ip/Eagle-Claw-Scale-with-Tape-Measure-50-lb/45087468
On Mon, Mar 27, 2017 at 4:45 PM, Galin Hernandez <galinhdz(at)gmail.com (galinhdz(at)gmail.com)> wrote:
Quote: | FWIW Rich told me to adjust the nose gear friction to between 20 and 35lbs of break force with 27lb being optimal. He did say that 20lbs was an absolute minimum, that 20lbs might not work in some cases and not to worry about being super accurate. I still have the cheap Walmart fish weight scale he got for me in El Salvador just like this one:
https://www.walmart.com/ip/Berkley-Scale-with-Tape/16637411
I try to adjust mine for 27lbs but take anything over 25lbs. This has worked well for me in the last 10yrs of flying my TR-4. YMMV
On Mon, Mar 27, 2017 at 1:50 PM, <pastormac(at)comcast.net (pastormac(at)comcast.net)> wrote:
Quote: | --> KIS-List message posted by: pastormac(at)comcast.net (pastormac(at)comcast.net)
Hi Guys,
Speaking of the nose gear. I'm getting quite a bit of shimmy on take off and landing. Is there an adjustment I can make?
Thanks!!
Steve
Sent from my iPhone
> On Mar 27, 2017, at 1:21 PM, Owen Baker <bakerocb(at)cox.net (bakerocb(at)cox.net)> wrote:
>
> 3/27/2017
>
> Hello Keith, Thanks for your input. You wrote:
>
> 1) ".... he had noted the problem and fixed it..."
>
> I don't think so. Your picture appears to also show a thin AN320-12 shear type castle nut in place with a fairly thin washer stack up (Bellevilles?). This would be consistent with the same length of the 3/4 inch diameter portion of the vertical stub as my #1 Lyle gear. I have seen no evidence that Lyle changed the length of the 3/4 inch diameter portion of the vertical stub until (at my request) he made it a bit longer for my #2 and #3 weldments.
>
> See the attached picture of the vertical stub on my #1 Lyle nose gear. I initially thought that the 3/4 inch diameter portion of the vertical stub was a machined out and threaded continuation of the vertical stub steel immediately above it (all one solid piece). I later learned that I was wrong and that the 3/4 inch diameter portion was, in fact, a separately obtained bolt whose head (maybe machined round first) was inserted into a hole in the steel above it and welded into place. Only after removing my #1 Lyle gear from the plane and examining the end of the vertical stub with a bright light and a magnifying glass was I able to see the evidence of a weld bead.
>
> I speculate that Lyle obtained these bolts from McMaster-Carr and that the quality control of the original manufacturer of these bolts was not pristine. The cotter pin holes were not exactly through the center of the bolt (I have noticed a bit of this on the bolts in my #2 and #3 Lyle gears as well) and the cotter pin hole in the end of the bolt in my #1 Lyle gear was too close to the end of the bolt for my comfort.
>
> Any questions?
>
> OC
>
> =============================================
>
> From: Keith.Miller(at)esa.int (Keith.Miller(at)esa.int)
> Sent: Monday, March 27, 2017 10:45 AM
> To: kis-list(at)matronics.com (kis-list(at)matronics.com)
> Subject: Re: Re: Can anybody confirm this?
>
> I think it was a bit a bad luck with OC 's shortened stud . Mine was made a
> few months later by Lyle and he had noted the problem and fixed it, so i
> guess it depends upon when it was made in the production series
>
>
Quote: | <4-9-16 CAMERA 003.JPG>
|
====================================
List" rel="noreferrer" target="_blank">http://www.matronics.com/Navigator?KIS-List
====================================
FORUMS -
eferrer" target="_blank">http://forums.matronics.com
====================================
WIKI -
errer" target="_blank">http://wiki.matronics.com
====================================
b Site -
-Matt Dralle, List Admin.
rel="noreferrer" target="_blank">http://www.matronics.com/contribution
====================================
|
|
| - The Matronics KIS-List Email Forum - | | Use the List Feature Navigator to browse the many List utilities available such as the Email Subscriptions page, Archive Search & Download, 7-Day Browse, Chat, FAQ, Photoshare, and much more:
http://www.matronics.com/Navigator?KIS-List |
|
|
|
Back to top |
|
 |
galinhdz(at)gmail.com Guest
|
Posted: Mon Mar 27, 2017 1:05 pm Post subject: Can anybody confirm this? |
|
|
OC wrote: "This shimmy can become violent enough to damage the nose gear linkages, collapse the nose gear, and cause the nose of the airplane to fall down and contact the runway surface." Heed these WORDS OF WISDOM!!! If you have experienced noticeable shimmy, I recommend you replace the bolts/pin that hold the nose gear "H" bracket.
With the nose elevated so no weight is on the nose gear, remove the bolts/pin and check them for any signs of failure. Especially the rear ones. Without magnafluxing or some other NDI, you probably won't be able to tell if they are failing. That is why I feel it isn't even worth inspecting them, just replace the bolts with new ones.
Cheap insurance.
On Mon, Mar 27, 2017 at 4:26 PM, Owen Baker <bakerocb(at)cox.net (bakerocb(at)cox.net)> wrote:
Quote: | 3/27/2017
Hello Steve, You wrote: "Is there an adjustment I can make?"
This is very dangerous. DO NOT FLY THIS PLANE until the friction nut on the bottom of the nose gear has been properly adjusted.
See the photo from Keith Miller (thanks Keith) that is attached to this email.
This shimmy can become violent enough to damage the nose gear linkages, collapse the nose gear, and cause the nose of the airplane to fall down and contact the runway surface.
I recommend:
1) Elevate the nose of the plane so that the nose tire is off the ground. (Contact me if needed for tips on how to do this.)
2) Attach a fish scale to the shoe holding the nose wheel in the vicinity of the wheel axle. See how many pounds of pull that it takes to move the shoe from side to side. This is to establish what the friction level is now. If it is several pounds less than 27 pounds (which it probably is because of the shimmy) you must adjust the friction level.
3) Use a black sharpie pen to number the nut notch above the cotter pin head as notch 1. Make a vertical mark on the shoe above notch 1 with the sharpie.
4) Remove the cotter pin holding the large AN320-12 castle nut from turning. Go around the nut with the sharpie numbering each notch in sequence. This is so that you can keep track of the notch that is under the vertical mark.
5) Using a 1 1/8 inch box wrench tighten the nut one notch. Use an ice pick or similar item to ensure that the new nut notch and the cotter pin hole through the vertical stub are aligned. Leave the ice pick in place.
6) Use the fish scale again to move the shoe back and forth to ensure that you have adjusted the friction to the vicinity of 27 pounds.
7) Remove the ice pick and repeat 5 and 6 above if needed. When you have the desired friction level set, install a new cotter pin and lower the nose tire to the ground.
Go fly the plane.
Any questions?
OC
=======
From: pastormac(at)comcast.net (pastormac(at)comcast.net)
Sent: Monday, March 27, 2017 1:50 PM
To: kis-list(at)matronics.com (kis-list(at)matronics.com)
Subject: Re: Re: Can anybody confirm this?
--> KIS-List message posted by: pastormac(at)comcast.net (pastormac(at)comcast.net)
Hi Guys,
Speaking of the nose gear. I'm getting quite a bit of shimmy on take off and landing. Is there an adjustment I can make?
Thanks!!
Steve |
| - The Matronics KIS-List Email Forum - | | Use the List Feature Navigator to browse the many List utilities available such as the Email Subscriptions page, Archive Search & Download, 7-Day Browse, Chat, FAQ, Photoshare, and much more:
http://www.matronics.com/Navigator?KIS-List |
|
|
|
Back to top |
|
 |
galinhdz(at)gmail.com Guest
|
Posted: Mon Mar 27, 2017 1:07 pm Post subject: Can anybody confirm this? |
|
|
Oh, and inspect the "H" bracket for any crack or sign of potential failure.
On Mon, Mar 27, 2017 at 5:04 PM, Galin Hernandez <galinhdz(at)gmail.com (galinhdz(at)gmail.com)> wrote:
Quote: | OC wrote: "This shimmy can become violent enough to damage the nose gear linkages, collapse the nose gear, and cause the nose of the airplane to fall down and contact the runway surface." Heed these WORDS OF WISDOM!!! If you have experienced noticeable shimmy, I recommend you replace the bolts/pin that hold the nose gear "H" bracket.
With the nose elevated so no weight is on the nose gear, remove the bolts/pin and check them for any signs of failure. Especially the rear ones. Without magnafluxing or some other NDI, you probably won't be able to tell if they are failing. That is why I feel it isn't even worth inspecting them, just replace the bolts with new ones.
Cheap insurance.
On Mon, Mar 27, 2017 at 4:26 PM, Owen Baker <bakerocb(at)cox.net (bakerocb(at)cox.net)> wrote:
Quote: | 3/27/2017
Hello Steve, You wrote: "Is there an adjustment I can make?"
This is very dangerous. DO NOT FLY THIS PLANE until the friction nut on the bottom of the nose gear has been properly adjusted.
See the photo from Keith Miller (thanks Keith) that is attached to this email.
This shimmy can become violent enough to damage the nose gear linkages, collapse the nose gear, and cause the nose of the airplane to fall down and contact the runway surface.
I recommend:
1) Elevate the nose of the plane so that the nose tire is off the ground. (Contact me if needed for tips on how to do this.)
2) Attach a fish scale to the shoe holding the nose wheel in the vicinity of the wheel axle. See how many pounds of pull that it takes to move the shoe from side to side. This is to establish what the friction level is now. If it is several pounds less than 27 pounds (which it probably is because of the shimmy) you must adjust the friction level.
3) Use a black sharpie pen to number the nut notch above the cotter pin head as notch 1. Make a vertical mark on the shoe above notch 1 with the sharpie.
4) Remove the cotter pin holding the large AN320-12 castle nut from turning. Go around the nut with the sharpie numbering each notch in sequence. This is so that you can keep track of the notch that is under the vertical mark.
5) Using a 1 1/8 inch box wrench tighten the nut one notch. Use an ice pick or similar item to ensure that the new nut notch and the cotter pin hole through the vertical stub are aligned. Leave the ice pick in place.
6) Use the fish scale again to move the shoe back and forth to ensure that you have adjusted the friction to the vicinity of 27 pounds.
7) Remove the ice pick and repeat 5 and 6 above if needed. When you have the desired friction level set, install a new cotter pin and lower the nose tire to the ground.
Go fly the plane.
Any questions?
OC
=======
From: pastormac(at)comcast.net (pastormac(at)comcast.net)
Sent: Monday, March 27, 2017 1:50 PM
To: kis-list(at)matronics.com (kis-list(at)matronics.com)
Subject: Re: Re: Can anybody confirm this?
--> KIS-List message posted by: pastormac(at)comcast.net (pastormac(at)comcast.net)
Hi Guys,
Speaking of the nose gear. I'm getting quite a bit of shimmy on take off and landing. Is there an adjustment I can make?
Thanks!!
Steve |
|
| - The Matronics KIS-List Email Forum - | | Use the List Feature Navigator to browse the many List utilities available such as the Email Subscriptions page, Archive Search & Download, 7-Day Browse, Chat, FAQ, Photoshare, and much more:
http://www.matronics.com/Navigator?KIS-List |
|
|
|
Back to top |
|
 |
aeromomentum(at)yahoo.com Guest
|
Posted: Mon Mar 27, 2017 1:08 pm Post subject: Can anybody confirm this? |
|
|
Hi OC,
In general you should have from 10% (max aft CG) to 25% (max forward CG) on the nose gear.
Assuming your empty weight is a portly 903 lbs and you are at max forward CG, you should have no more than 225 lbs on your nose gear. My guess is even at full empty your CG is still not at the front limit. So you (like most every TR-1) still have too much weight on the nose gear. You really should move the main gear more forward. Based on 10% on the nose gear at max gross and max aft CG the main should be about 70.5 inches. I would go with about 71 inches. You really will like landing and taking off much more with this main gear location. Plus the loads and stress on the nose gear will be much less.
Also keep in mind that when I checked the nose gear in 1999 (version 2.1, streamlined tube with added side plates) most everything did not meet FAR part 23 requirements. This includes the arms, pins and bolts along with the actual tube. I don't think most of these parts were upgraded with version 3.X.
Mark K.
--------------------------------------------
On Sun, 3/26/17, Owen Baker <bakerocb(at)cox.net> wrote:
Subject: Re: Can anybody confirm this?
To: kis-list(at)matronics.com, "TRICKEL MARK" <marktrickel(at)gmail.com>, "KETTERING MARK" <aeromomentum(at)yahoo.com>
Date: Sunday, March 26, 2017, 6:29 PM
"Owen Baker " <bakerocb(at)cox.net>
3/26/2017
Hello Mark K, Thanks for your input. You wrote:
1) "Have you moved you main gear forward?"
Yes, I wedged it forward with flox. The main landing gear
axles are 72.25
inches aft of the 0.00 datum point.
That datum point is, in turn, 32.00 inches forward of the
engine cowling
joggle on the fuselage.
2) "How much weight do you have on your nose gear?"
Right now, in operational configuration and without
reweighing, I don't
know.
The original empty aircraft weighing showed 242 pounds on
the nose gear.
Since then there have been a few misc items (quart of oil,
jar for fuel
testing, rags, etc.)
that are normally kept in the right baggage well.
Also there are some other misc items (hand held radio, small
tool bag, water
bottle, roll of tape, etc.) that have taken up permanent
lodging on the hat
shelf aft of the seats.
Not too long ago I double bagged sand into two kitchen
sliding lock plastic
gallon bags (they totaled 23 pounds) and placed them over
the battery box in
the far right rear corner of the right baggage well (I
mostly fly solo in
the left seat) because I was unhappy that the nose gear was
descending to
meet the runway too quickly after the main gear touched
down. I am not sure
if that has helped, or if so how much.
3) "The geometry (pivot axis angle) could maybe use some
tweaking to reduce
shimmy."
Can you please elaborate on the contribution of the pivot
angle axis on
shimmy and how one would go about tweaking that angle in a
KIS TR-1? Thanks.
Also a reminder that my shimmy problem with strut #2 was my
fault for not
tightening the friction nut enough and I have had no shimmy
problems since
installing strut #3 and using 27 pounds as a base figure for
setting the
friction nut.
Also in my listing of the design / manufacturing defects in
the #1 strut in
paragraph 1 below I forget to mention that the off center
cotter pin hole
was also so close to the end of the vertical stub that I was
concerned about
the possibility of break out.
OC
PS: I have your last name spelled Kettering in some old
places in my
computer. Has there been a change?
========================================
From: M Ketteing
Sent: Sunday, March 26, 2017 12:30 PM
To: kis-list(at)matronics.com
; TRICKEL MARK
Subject: Re: Can anybody confirm this?
Hello OC,
How much weight do you have on your nose gear? Have
you moved you main gear
forward? As you may know the more weight on the nose
the more energy to the
shimmy. With more energy the less effective the
friction damping. The
geometry (pivot axis angle) could maybe use some tweaking to
reduce shimmy.
Mark K.
--------------------------------------------
On Sun, 3/26/17, Owen Baker <bakerocb(at)cox.net>
wrote:
Subject: Re: Can anybody confirm this?
To: kis-list(at)matronics.com,
"TRICKEL MARK" <marktrickel(at)gmail.com>
Date: Sunday, March 26, 2017, 11:45 AM
"Owen Baker " <bakerocb(at)cox.net>
3/26/2017
Hello Mark, Yes. I can confirm this event. Here is the back
story:
1) I was never happy with my first (#1) Lyle Hendricks
round
tube nose gear
strut. It was very sturdy, but it had two manufacturing /
design defects in
my opinion.
a) The bottom vertical 3/4-16 threaded stud potion was too
short. This meant
that a thin AN320-12 castle nut must be used instead
of the normal
thickness AN310-12 castle nut. This further meant that the
total nut-to-stud
thread interface holding the aluminum shoe and any washer
stack up into
place was pretty limited. I was concerned that that
interface could fail and
the entire shoe and nose wheel could fall off in flight.
b) The cotter pin hole through the bottom of that stud did
not pass through
the center of the stud. This off set meant that the pin
would not pass
through the normal castle notches in the AN320-12 nut. A
person had to grind
/ file the nut notches wider in order for the cotter pin to
pass through the
nut. This had two effects: ONE) The nut could not be
rotated
one notch at a
time to adjust the friction keeping the shoe from shimmying
on landing roll
out unless each pair of notches was ground or filed wider.
TWO) Grinding or
filing all pairs of notches wider further reduced the
nut-to-stud thread
interface.
2) So my solution after over 500 flight hours with no
problems other than
dealing with the two irritating issues described above was
to have Lyle make
for me a new nose gear strut (#2) with modifications to
eliminate the two
issues. I also had Lyle make some other design
modifications
to this #2
strut assembly such as a longer threaded portion at the top
of the
compression rod and a welded cross bar at the bottom of the
rod. The longer
threaded portion at the top of the rod gave more vertical
adjustment
opportunity for the rod and the welded bar permitted one to
hold the rod
from rotating when wrenching nuts at the top of the rod.
3) The #2 strut assembly was installed and I set off on its
first test
flight. Unfortunately, not having any numerical figure
available to measure
the shimmy prevention friction for the shoe, I used the
TFAR
(That Feels
About Right) criteria in tightening the AN310-12 nut
holding
the (new to me)
two Belleville washers up against the aluminum shoe. TFAR
worked fine for a
few touch and go landings at an outlying field, but when I
returned to my
home field (KHEF Manassas Virginia) for one final landing
trouble showed up.
4) At a very slow speed on the final landing roll out the
nose wheel began
to shimmy violently from side to side. This shimmy broke
the
two aluminum
nose wheel brackets at the bottom of the fire wall and
allowed the strut
assembly to flop over sideways and the airplane nose to be
lowered to the
runway surface. The damage consisted of grinding off a
small
portion of the
bottom of the #2 strut weldment, grinding off a bit of each
wooden propeller
tip, and some scrapes off the bottom of the spinner, lower
engine cowl, and
one of the main landing gear wheel pants. This event falls
into the
categories of: "No good deed goes unpunished" or "If it
ain't broke, don't
fix it". Take your choice.
5) The airplane was recovered to my hangar, Lyle graciously
agreed to build
me strut assembly #3, Prince Aircraft repaired the
propeller
tips, I
replaced the spinner, repaired the engine cowling and the
wheel pants, and
had them painted. I put everything back together once I had
all pieces in
hand and used a 27 pound pull at the axle as my base figure
for measuring
the friction for tightening the AN310-12 nut. I flew again
for the first
time since the reported event on 10/18/2016. No nose wheel
strut problems
since then. Thanks again go to Lyle.
Any questions?
OC
=====================================
From: mark_trickel
Sent: Sunday, March 26, 2017 3:57 AM
To: kis-list(at)matronics.com
Subject: Can anybody confirm this?
http://www.kathrynsreport.com/2016/08/kis-tr-1-n660c-incident-occurred-august.html
OC?
MT
Forum -
- MATRONICS WEB FORUMS -
MATRONICS LIST WIKI -
List Contribution Web Site -
-Matt
Dralle, List Admin.
| - The Matronics KIS-List Email Forum - | | Use the List Feature Navigator to browse the many List utilities available such as the Email Subscriptions page, Archive Search & Download, 7-Day Browse, Chat, FAQ, Photoshare, and much more:
http://www.matronics.com/Navigator?KIS-List |
|
|
|
Back to top |
|
 |
pastormac62
Joined: 07 Sep 2015 Posts: 71 Location: Indiana
|
Posted: Mon Mar 27, 2017 3:42 pm Post subject: Can anybody confirm this? |
|
|
Thank you for the info! I just got back from a 10 hour flight time with several landings. I wish we could do a fly in weekend some where for especially for us novice TR-1 owners. It would be great to just here from other experienced owners!!
Steve
Sent from my iPhone
Quote: | On Mar 27, 2017, at 4:26 PM, Owen Baker <bakerocb(at)cox.net> wrote:
3/27/2017
Hello Steve, You wrote: "Is there an adjustment I can make?"
This is very dangerous. DO NOT FLY THIS PLANE until the friction nut on the bottom of the nose gear has been properly adjusted.
See the photo from Keith Miller (thanks Keith) that is attached to this email.
This shimmy can become violent enough to damage the nose gear linkages, collapse the nose gear, and cause the nose of the airplane to fall down and contact the runway surface.
I recommend:
1) Elevate the nose of the plane so that the nose tire is off the ground. (Contact me if needed for tips on how to do this.)
2) Attach a fish scale to the shoe holding the nose wheel in the vicinity of the wheel axle. See how many pounds of pull that it takes to move the shoe from side to side. This is to establish what the friction level is now. If it is several pounds less than 27 pounds (which it probably is because of the shimmy) you must adjust the friction level.
3) Use a black sharpie pen to number the nut notch above the cotter pin head as notch 1. Make a vertical mark on the shoe above notch 1 with the sharpie.
4) Remove the cotter pin holding the large AN320-12 castle nut from turning. Go around the nut with the sharpie numbering each notch in sequence. This is so that you can keep track of the notch that is under the vertical mark.
5) Using a 1 1/8 inch box wrench tighten the nut one notch. Use an ice pick or similar item to ensure that the new nut notch and the cotter pin hole through the vertical stub are aligned. Leave the ice pick in place.
6) Use the fish scale again to move the shoe back and forth to ensure that you have adjusted the friction to the vicinity of 27 pounds.
7) Remove the ice pick and repeat 5 and 6 above if needed. When you have the desired friction level set, install a new cotter pin and lower the nose tire to the ground.
Go fly the plane.
Any questions?
OC
================================
From: pastormac(at)comcast.net
Sent: Monday, March 27, 2017 1:50 PM
To: kis-list(at)matronics.com
Subject: Re: Re: Can anybody confirm this?
Hi Guys,
Speaking of the nose gear. I'm getting quite a bit of shimmy on take off and landing. Is there an adjustment I can make?
Thanks!!
Steve
<IMG_9929.JPG>
|
| - The Matronics KIS-List Email Forum - | | Use the List Feature Navigator to browse the many List utilities available such as the Email Subscriptions page, Archive Search & Download, 7-Day Browse, Chat, FAQ, Photoshare, and much more:
http://www.matronics.com/Navigator?KIS-List |
|
|
|
Back to top |
|
 |
galinhdz(at)gmail.com Guest
|
Posted: Mon Mar 27, 2017 4:13 pm Post subject: Can anybody confirm this? |
|
|
Sun-N-Fun is coming up. A GREAT way to meet up. I will be there Friday and Sunday.
On Mon, Mar 27, 2017 at 7:36 PM, <pastormac(at)comcast.net (pastormac(at)comcast.net)> wrote:
Quote: | --> KIS-List message posted by: pastormac(at)comcast.net (pastormac(at)comcast.net)
Thank you for the info! I just got back from a 10 hour flight time with several landings. I wish we could do a fly in weekend some where for especially for us novice TR-1 owners. It would be great to just here from other experienced owners!!
Steve
Sent from my iPhone
> On Mar 27, 2017, at 4:26 PM, Owen Baker <bakerocb(at)cox.net (bakerocb(at)cox.net)> wrote:
>
> 3/27/2017
>
> Hello Steve, You wrote: "Is there an adjustment I can make?"
>
> This is very dangerous. DO NOT FLY THIS PLANE until the friction nut on the bottom of the nose gear has been properly adjusted.
> See the photo from Keith Miller (thanks Keith) that is attached to this email.
>
> This shimmy can become violent enough to damage the nose gear linkages, collapse the nose gear, and cause the nose of the airplane to fall down and contact the runway surface.
>
> I recommend:
>
> 1) Elevate the nose of the plane so that the nose tire is off the ground. (Contact me if needed for tips on how to do this.)
>
> 2) Attach a fish scale to the shoe holding the nose wheel in the vicinity of the wheel axle. See how many pounds of pull that it takes to move the shoe from side to side. This is to establish what the friction level is now. If it is several pounds less than 27 pounds (which it probably is because of the shimmy) you must adjust the friction level.
>
> 3) Use a black sharpie pen to number the nut notch above the cotter pin head as notch 1. Make a vertical mark on the shoe above notch 1 with the sharpie.
>
> 4) Remove the cotter pin holding the large AN320-12 castle nut from turning. Go around the nut with the sharpie numbering each notch in sequence. This is so that you can keep track of the notch that is under the vertical mark.
>
> 5) Using a 1 1/8 inch box wrench tighten the nut one notch. Use an ice pick or similar item to ensure that the new nut notch and the cotter pin hole through the vertical stub are aligned. Leave the ice pick in place.
>
> 6) Use the fish scale again to move the shoe back and forth to ensure that you have adjusted the friction to the vicinity of 27 pounds.
>
> 7) Remove the ice pick and repeat 5 and 6 above if needed. When you have the desired friction level set, install a new cotter pin and lower the nose tire to the ground.
>
> Go fly the plane.
>
> Any questions?
>
> OC
>
> ================================
>
> From: pastormac(at)comcast.net (pastormac(at)comcast.net)
> Sent: Monday, March 27, 2017 1:50 PM
> To: kis-list(at)matronics.com (kis-list(at)matronics.com)
> Subject: Re: Re: Can anybody confirm this?
>
> --> KIS-List message posted by: pastormac(at)comcast.net (pastormac(at)comcast.net)
>
> Hi Guys,
> Speaking of the nose gear. I'm getting quite a bit of shimmy on take off and landing. Is there an adjustment I can make?
> Thanks!!
> Steve
====================================
List" target="_blank" rel="noreferrer">http://www.matronics.com/Navigator?KIS-List
====================================
FORUMS -
_blank" rel="noreferrer">http://forums.matronics.com
====================================
WIKI -
lank" rel="noreferrer">http://wiki.matronics.com
====================================
b Site -
-Matt Dralle, List Admin.
target="_blank" rel="noreferrer">http://www.matronics.com/contribution
====================================
|
| - The Matronics KIS-List Email Forum - | | Use the List Feature Navigator to browse the many List utilities available such as the Email Subscriptions page, Archive Search & Download, 7-Day Browse, Chat, FAQ, Photoshare, and much more:
http://www.matronics.com/Navigator?KIS-List |
|
|
|
Back to top |
|
 |
bakerocb
Joined: 15 Jan 2006 Posts: 727 Location: FAIRFAX VA
|
Posted: Tue Mar 28, 2017 7:48 am Post subject: Can anybody confirm this? |
|
|
3/28/2017
Hello Mark, Thanks for your input. You wrote:
1) "Assuming your empty weight is a portly 903 lbs and you are at max
forward CG, you should have no more than 225 lbs on your nose gear."
My empty weight is 972 pounds with 242 pounds on the nose landing gear. The
empty weight CG is at 60.10 inches. The aircraft manual shows 61.50 inches
as the forward operating CG limit.
2) "In general you should have from 10% (max aft CG) to 25% (max forward CG)
on the nose gear."
At empty weight I have 24.9 percent of the aircrafts total empty weight of
972 pounds on the nose gear with the CG at 60.10 inches, i.4 inches forward
of the 61.50 operating CG limit.
3) "You really should move the main gear more forward." and "I would go with
about 71 inches."
I agree. How do you recommend that this should be accomplished?** I have
already used a flox wedge to move the main landing forward to 72.25 inches.
4) "I don't think most of these parts were upgraded with version 3.X."
I think that the Lyle #1 and #2 nose landing gear made for me were sturdy
enough. Lyle beefed up the aluminum linkages when he made #3 for me.
OC
*PS: I have given some casual consideration to having Grove make a custom
main landing gear for me that would move the axle locations forward, but
have not pursued it. See here:
http://www.groveaircraft.com/designguide.html
and here:
http://www.groveaircraft.com/layout.html
================================
From: M Ketteing
Sent: Monday, March 27, 2017 5:07 PM
To: kis-list(at)matronics.com ; TRICKEL MARK
Subject: Re: Can anybody confirm this?
Hi OC,
In general you should have from 10% (max aft CG) to 25% (max forward CG) on
the nose gear.
Assuming your empty weight is a portly 903 lbs and you are at max forward
CG, you should have no more than 225 lbs on your nose gear. My guess is
even at full empty your CG is still not at the front limit. So you (like
most every TR-1) still have too much weight on the nose gear. You really
should move the main gear more forward. Based on 10% on the nose gear at
max gross and max aft CG the main should be about 70.5 inches. I would go
with about 71 inches. You really will like landing and taking off much more
with this main gear location. Plus the loads and stress on the nose gear
will be much less.
Also keep in mind that when I checked the nose gear in 1999 (version 2.1,
streamlined tube with added side plates) most everything did not meet FAR
part 23 requirements. This includes the arms, pins and bolts along with the
actual tube. I don't think most of these parts were upgraded with version
3.X.
Mark K.
| - The Matronics KIS-List Email Forum - | | Use the List Feature Navigator to browse the many List utilities available such as the Email Subscriptions page, Archive Search & Download, 7-Day Browse, Chat, FAQ, Photoshare, and much more:
http://www.matronics.com/Navigator?KIS-List |
|
|
|
Back to top |
|
 |
mark_trickel
Joined: 13 Dec 2011 Posts: 101 Location: Philadelphia, PA, USA
|
Posted: Wed Mar 29, 2017 4:42 am Post subject: Re: Can anybody confirm this? |
|
|
OC – Thank you for fielding a few of my goofy questions.
On Gear #1 – Thanks for pointing out there is a shoulder that the shoe fits around to take into account. I do not have a nose gear on my TR-1.
No, I did not mean to try and come up with dozens of washer combinations in order to get the right torque and have the cotter pin slot line up on a single oversized slot. I meant that the Belleville spring disks have a little leeway in them and a stack including them on this gear may have been adequate and you may have been able to zero in on the single oversized cotter pin slot. If you currently have the Belleville spring disks stacked up against the aluminum shoe on gear #3 they will eventually wear into the shoe and the torque setting will diminish and a shimmy may again develop. Even the thinnest of steel washers between the Belleville washers and the shoe would be better than none.
Belleville washers are commonly used in industrial equipment as well as consumer goods where a moving joint needs to maintain a given tension. I recently scrapped out an old lawnmower and was surprised to find many them in use. Rich included them on his homemade nose gear that still remains on the stolen KIS TR-1 #1.
I asked about the prop because some of the Prince P-tips are carbon fiber covered. I have recent experience working with carbon and that stuff is like steel. I did not mention the engine, when it comes to airplanes and the KIS project I’ve been around the block a few times and I know a wood prop strike is different than a metal prop strike. I understand the prop was factory repaired I just thought it was unusual.
I understand your desire to have a new main gear made mainly because canting the current gear forward enough to put the gear in the proper position will most likely result in the center part of the gear hanging below the well-depression molded into the bottom of the fuselage. This would require a very custom fairing to smooth the airfow under the belly. If you are considering this move I would consult with Lyle as he was the supplier of the main gears to Richard. Plus, I believe he would be a little more reasonable than the Grove guy. I have redesigned the rudder pedal set up on my TR-1 to lower the floor and make it a little more comfortable and I found that Matco master cylinder prices are considerably less than Grove.
A little history on the TR-1 landing gear:
Rich introduced his new airplane at Oshkosh in 1991, it had a carbon fiber main gear and his home-made nose gear. The airplane also had a 80 hp VW up front. Kits were selling pretty good and the first builders were flying by 1993. Metal parts were supplied by Ken Brock and a nose gear similar to Rich’s was designed and produced. Builders that were able to either go to the factory and fly Rich’s plane or those who had above average piloting skills did OK. Some builders were able to get Rich to come and do the first flights and get a few important pointers. But there were pilots that did not have the ability to figure it out quickly and a bunch of nose gears were getting banged. Back at the factory Rich and the engineers started beefing up the gear. I think there were three versions of the first gear. But still nose gears were getting banged. The engineers Nate and Vance did not always agree but Vance came up with the final articulated arrangement in 1996 or ‘97, and it was put into production. Builders on their own came up with the idea to extend the elevator and this fix was a great help but not a total solution. Sales slowed and despite Tri-R’s emphasis on the Super Cruiser there just wasn’t enough business to keep the company going. In 2000, the designs were sold to Pulsar. During the Tri-R years nobody was able to figure out what was going on, not until a certain young engineer bought a flying example of the TR-1. And it didn’t take to long for him to add the final piece to the puzzle – the main gear was in the wrong place! Weight on the nose gear needed to be reduced. Now those who frequent the forum are at least aware of the situation but there are many who builders and owners that are not computer savvy and are unaware and therein lies the problem.
MT
| - The Matronics KIS-List Email Forum - | | Use the List Feature Navigator to browse the many List utilities available such as the Email Subscriptions page, Archive Search & Download, 7-Day Browse, Chat, FAQ, Photoshare, and much more:
http://www.matronics.com/Navigator?KIS-List |
|
|
|
Back to top |
|
 |
|
|
You cannot post new topics in this forum You cannot reply to topics in this forum You cannot edit your posts in this forum You cannot delete your posts in this forum You cannot vote in polls in this forum You cannot attach files in this forum You can download files in this forum
|
Powered by phpBB © 2001, 2005 phpBB Group
|