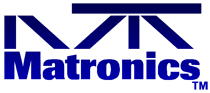 |
Matronics Email Lists Web Forum Interface to the Matronics Email Lists
|
View previous topic :: View next topic |
Author |
Message |
kenryan
Joined: 20 Oct 2009 Posts: 426
|
Posted: Wed Apr 11, 2018 8:00 am Post subject: Please critique my electrical design |
|
|
Thanks Charlie.
On Wed, Apr 11, 2018 at 4:41 AM, Charlie England <ceengland7(at)gmail.com (ceengland7(at)gmail.com)> wrote:
Quote: | Well, the 1st issue is establishing what Mark meant when he mentioned that 10.6V limit. Because unless he's using a truly massively oversized battery, it will *always* drop below 10.6V during cranking. That's why old Kettering ignition (points & condenser) cars had ballast resistors in series with their points. The points actually run on around 6-8 volts, and resistor gets switched out of the circuit during cranking because of the battery voltage drop due to cranking loads. Dropping down around 10V (sometimes even lower) is fairly common during starting. Look back through the archives for all the complaints about EFISs rebooting while cranking the engine.Â
So....I'm betting that Mark meant he's measuring 10.6V *after* 15 seconds of cranking, but with no/minimal load on the battery. Now, go back to the Corvette/Chevette example. If you accelerate the Corvette for 15 seconds, it'll still have 400 HP, but you may only have 3 seconds of capacity (gas) left.Â
Mark's test is even less valid if one has chosen a Lithium chemistry battery; their voltage has much less decline until it 'falls off the cliff' at full discharge.
The real test is monitoring *how long* voltage remains above the voltage that indicates complete discharge (which is around 10.5 V), while the typical load from the plane's required (endurance bus) electronics is applied.
On Tue, Apr 10, 2018 at 11:24 PM, Ken Ryan <keninalaska(at)gmail.com (keninalaska(at)gmail.com)> wrote:
Quote: | Charlie, It seems to me that your response does not address that the test involves monitoring the voltage drop that occurs when the consistent load is applied. The test is not simply, "will the battery spin the prop." The test is, "what is the voltage drop caused by spinning the prop."Â
It seems to me that if the voltage drops down further on a worn out battery than it does on a fresh battery, there is at least the possibility that this test could be quite useful. It does not seem to me that the simple fact the battery "can be down 50% capacity and still reliably crank the engine" is germane to whether or not monitoring voltage under a consistent load (in this case spinning the propeller for a specific time) can be useful as a way to determine whether or not it is time to replace a battery.
I'm not saying that the spin-the-prop-and-monitor-voltage test is valid. But it seems to me like it might be. I just can't see where simply noting that a depleted battery can still spin a prop says anything about the usefulness of such a test. Sorry, but I just can't seem to make that connection. Probably I am a little bit dense -- it wouldn't be the first time.
In evaluating the suggested test, as a starting point I would like to know if the voltage drop would be significantly different on a new vs a worn out battery. If the answer is no, the drop would be about the same, then case closed. Test invalid. But if it turns out the voltage drop is significantly greater on a worn out battery, then I think there is reason to believe that the test might be useful.
On Tue, Apr 10, 2018, 20:04 Charlie England <ceengland7(at)gmail.com (ceengland7(at)gmail.com)> wrote:
Quote: | If the only use for the battery is starting, then it's a valid test. But if the battery is backup electrical power for the alternator and you need electrical power to keep the flight safe to its conclusion, then it isn't a valid test.
It can be down to 50% capacity & still reliably crank the engine. But if the alternator dies and you need the battery to keep the engine running (electronic ignition, glass panel in IFR, etc), then you'd only have half or less the time you thought you'd have, based on the battery's rated capacity.
It's the difference between power and energy. 400 HP Corvette with 1/2 gallon of gas, vs 80 HP Chevette with 15 gallons.
That help?
On 4/10/2018 10:06 PM, Ken Ryan wrote:
Quote: | Charlie, It would seem to me that putting a consistent load (turning the starter, similar temperatures) on the battery, and noting the voltage drop would constitute a valid test. It is surely not the most accurate, but if done in a consistent manner, it is seems it would be much better than doing nothing at all. Also, I don't see how the fact that it only takes 5% of battery capacity to start the engine has any relevance on whether such a rudimentary engine spinning stress test is valid, or not. Are you saying that it is likely that one would note the same voltage drop on a brand new battery as on a battery that is nearing the end of its useful life? Enlighten!
On Tue, Apr 10, 2018 at 6:39 PM, Charlie England <ceengland7(at)gmail.com (ceengland7(at)gmail.com)> wrote:
Quote: | 615151073569806401m_-960492680129280463m_6581499881476749600moz-cite-prefix">Since it only takes around 5% of capacity to start the engine, that might not be the most reliable test.
On 4/10/2018 7:06 PM, Mark Moyle wrote:
Quote: | Quick load test on a battery is…mags grounded or off and mixture pulled. Crank the engine and monitor the battery voltage. If after 15 seconds the battery voltage does NOT drop below 10.6 volts DC the battery is good. If not charge the battery and test again.
Mark Moyle
Platinum AlaskaÂ
615151073569806401m_-960492680129280463m_6581499881476749600OLK_SRC_BODY_SECTION"> From: <owner-aeroelectric-list-server(at)matronics.com (owner-aeroelectric-list-server(at)matronics.com)> on behalf of Rene <rene(at)felker.com (rene(at)felker.com)>
Reply-To: <aeroelectric-list(at)matronics.com (aeroelectric-list(at)matronics.com)>
Date: Tuesday, April 10, 2018 at 3:35 PM
To: <aeroelectric-list(at)matronics.com (aeroelectric-list(at)matronics.com)>
Subject: RE: Please critique my electrical design
I do not know about what sells…..but I have mine load tested at Batteries +.
Â
I have two batteries and two alternators. I have one battery that is 10+ years and the other is about 5 now. I had two battery failures….one self induced and the other was infant mortality.
Â
Rene'
801-721-6080
Â
From: owner-aeroelectric-list-server(at)matronics.com (owner-aeroelectric-list-server(at)matronics.com) <owner-aeroelectric-list-server(at)matronics.com (owner-aeroelectric-list-server(at)matronics.com)> On Behalf Of FLYaDIVE
Sent: Tuesday, April 10, 2018 5:15 PM
To: aeroelectric-list(at)matronics.com (aeroelectric-list(at)matronics.com)
Subject: Re: Please critique my electrical design
Â
Bob:
Â
Let's get a show of hands...
How many Pilots out there have a LOAD tester?
I can't get owners to check their tires and you want them to load test a battery!
Granted! This is a aero-electric email list and many are builders. So, if there are fellows out there that do have a load tester I doubt that would cover the rest of the BUYERS that only purchased the plane and did not build.
What do you think would sell a plane faster:
'Oh, and this plane has Dual Alternators and Dual Batteries.'
Or...
'And every year at annual I Load Test the battery."
Â
Barry
Â
Â
On Tue, Apr 10, 2018 at 4:44 PM, Robert L. Nuckolls, III <nuckolls.bob(at)aeroelectric.com (nuckolls.bob(at)aeroelectric.com)> wrote: Quote: |
At 03:01 PM 4/10/2018, you wrote:
Quote: |
 With two alternators, why a backup battery?
 Bob . . .
​Because what if the battery fails?
G-5's can have the Garmin $150 TINNY battery or ​you can apply that money to a much larger second battery which will be big enough to start the plane and supply days of power for the G-5. I have not installed the G-3, but I have installed 2 planes with Dual G-5's (AI & HSI). With dual G-5's in a certified plane you are required toÂ
have dual Garmin batteries... That is $300 for a stinking 1 or 2 AH battery. Yea, I would be very happy to install a second battery - a small one - With just enough to start the plane in a 24:00 DARK stranded situation. Â
Yea, happened to me one night. No Fun!
Barry |
 Was this in spite of a considered preventative
 maintenance program? What was the battery's last
 cap-check value before the failure?
 A battery that is watched and maintained as
 carefully as tires, belts, propeller nicks
 air cleaners and engine oil is very unlikely
 to fail. Dual alternators virtually assures
 you of engine driven energy in spite of the
 loss of one alternator.
 The rule of thumb for battery replacement
 in the TC world is when it falls to less than
 75% of original capacity . . . in the modern
 RG battery world, this means it probably
 still cranks the engine but is in substantial
 decline on an ever increasing slope to failure
 yet unlikely to go belly up away from your
 home hangar.
 Few light aircraft owner's manuals speak to
 affirmative-action maintenance programs . . .
 but I'd bet that top-billing in the cast of performers
 virtually all dark-n-stormy night stories that
 speak to battery failure is a beyond-service-life
 battery.
Â
 Bob . . .
|
Â
|
Virus-free. www.avast.com [url=#m_-3808612535981414965_m_-6378004472635657997_m_-615151073569806401_m_-960492680129280463_m_6581499881476749600_DAB4FAD8-2DD7-40BB-A1B8-4E2AA1F9FDF2] [/url]
|
|
|
|
|
| - The Matronics AeroElectric-List Email Forum - | | Use the List Feature Navigator to browse the many List utilities available such as the Email Subscriptions page, Archive Search & Download, 7-Day Browse, Chat, FAQ, Photoshare, and much more:
http://www.matronics.com/Navigator?AeroElectric-List |
|
|
|
Back to top |
|
 |
nuckolls.bob(at)aeroelect Guest
|
Posted: Wed Apr 11, 2018 10:04 am Post subject: Please critique my electrical design |
|
|
At 06:14 PM 4/10/2018, you wrote:
Quote: | Bob:
Let's get a show of hands...
How many Pilots out there have a LOAD tester? |
not load . . . capacity
Quote: | I can't get owners to check their tires and you want them to load test a battery! |
That's a separate issue. Lots of folks
fail to take their drugs as prescribed.
Quote: | Granted! This is a aero-electric email list and many are builders. So, if there are fellows out there that do have a load tester I doubt that would cover the rest of the BUYERS that only purchased the plane and did not build. |
I don't design systems for marketability.
I strive for failure tolerance and
risk reduction.
Quote: | What do you think would sell a plane faster:
'Oh, and this plane has Dual Alternators and Dual Batteries.'
Or...
'And every year at annual I Load Test the battery." |
If you've got an e-bus, then a cap test
is easy. While doing other things on the
airplane, set the cockpit up for endurance
mode and see if the battery will run your
electro-whizzies for at least 75 percent
of time as when the battery was new.
Failure to honor critical axioms in aviation
present increased risks . . . you have to
make sure that fuel aboard is MORE than
sufficient to the mission. Some builders
with e-bus structures will size the battery
and endurance mode operations such that
electrical capacity exceeds fuel capacity.
The point being offered is that an electrical
system can be configured and used in a manner
that makes an electrical emergency exceedingly
unlikely. I try to remind people that when
'standby' equipment is being installed, it comes
with cost, weight and maintenance issues.
Therefore, is it not useful to consider ways that
standby equipment becomes smaller, lighter, less
expensive and/or more efficient . . . if not
eliminated all together? If one is unwilling to
put a dip-stick into the energy contained in the
ship's main battery . . . how is a standby battery
going to be treated any differently?
Bob . . .
| - The Matronics AeroElectric-List Email Forum - | | Use the List Feature Navigator to browse the many List utilities available such as the Email Subscriptions page, Archive Search & Download, 7-Day Browse, Chat, FAQ, Photoshare, and much more:
http://www.matronics.com/Navigator?AeroElectric-List |
|
|
|
Back to top |
|
 |
nuckolls.bob(at)aeroelect Guest
|
Posted: Wed Apr 11, 2018 11:09 am Post subject: Please critique my electrical design |
|
|
Quote: |
I followed B&C's parts list, but when they switched it from a generic Ford regulator to the LR3C I didn't realize I should have used the Z-12 architecture for that component. Z-12 doesn't include a fuseable link or crowbar -- should I take those out? |
The ovm14 can come out, that's built into the LR3.
If your using a fused bus, then the fusible link
and remotely located field breaker stays in.
Quote: | I put the LV Warn light back in my design for now like the Z-12 has, but I'm sure the G3X has an input for that, so a stand-alone light won't be required. |
the G3x has its own low voltage sense, resolution
and display feature. If you don't wish to use the
separate light featured in the LR3C installation,
just leave that terminal unused.
Quote: | I'll also have to figure out if I still need the Lo Volt Warn CB in that arrangement. |
YES! that is your bus voltage sense lead.
Bob . . .
| - The Matronics AeroElectric-List Email Forum - | | Use the List Feature Navigator to browse the many List utilities available such as the Email Subscriptions page, Archive Search & Download, 7-Day Browse, Chat, FAQ, Photoshare, and much more:
http://www.matronics.com/Navigator?AeroElectric-List |
|
|
|
Back to top |
|
 |
kenryan
Joined: 20 Oct 2009 Posts: 426
|
Posted: Wed Apr 11, 2018 11:13 am Post subject: Please critique my electrical design |
|
|
Bob, thanks for reiterating the difference between a load test and a capacity test. Is there any possibility of gaining insight into a battery's capacity by studying the results of load testing?
On Wed, Apr 11, 2018 at 10:03 AM, Robert L. Nuckolls, III <nuckolls.bob(at)aeroelectric.com (nuckolls.bob(at)aeroelectric.com)> wrote:
Quote: | At 06:14 PM 4/10/2018, you wrote:
Quote: | Bob:
Let's get a show of hands...
How many Pilots out there have a LOAD tester? |
 not load . . . capacity
Quote: | I can't get owners to check their tires and you want them to load test a battery! |
 That's a separate issue. Lots of folks
 fail to take their drugs as prescribed.
Quote: | Granted! This is a aero-electric email list and many are builders. So, if there are fellows out there that do have a load tester I doubt that would cover the rest of the BUYERS that only purchased the plane and did not build. |
  I don't design systems for marketability.
  I strive for failure tolerance and
  risk reduction.
Quote: | What do you think would sell a plane faster:
'Oh, and this plane has Dual Alternators and Dual Batteries.'
Or...
'And every year at annual I Load Test the battery." |
  If you've got an e-bus, then a cap test
  is easy. While doing other things on the
  airplane, set the cockpit up for endurance
  mode and see if the battery will run your
  electro-whizzies for at least 75 percent
  of time as when the battery was new.
  Failure to honor critical axioms in aviation
  present increased risks . . . you have to
  make sure that fuel aboard is MORE than
  sufficient to the mission. Some builders
  with e-bus structures will size the battery
  and endurance mode operations such that
  electrical capacity exceeds fuel capacity.
 Â
  The point being offered is that an electrical
  system can be configured and used in a manner
  that makes an electrical emergency exceedingly
  unlikely. I try to remind people that when
  'standby' equipment is being installed, it comes
  with cost, weight and maintenance issues.
  Therefore, is it not useful to consider ways that
  standby equipment becomes smaller, lighter, less
  expensive and/or more efficient . . . if not
  eliminated all together? If one is unwilling to
  put a dip-stick into the energy contained in the
  ship's main battery . . . how is a standby battery
  going to be treated any differently?
 Bob . . .
|
| - The Matronics AeroElectric-List Email Forum - | | Use the List Feature Navigator to browse the many List utilities available such as the Email Subscriptions page, Archive Search & Download, 7-Day Browse, Chat, FAQ, Photoshare, and much more:
http://www.matronics.com/Navigator?AeroElectric-List |
|
|
|
Back to top |
|
 |
nuckolls.bob(at)aeroelect Guest
|
Posted: Wed Apr 11, 2018 11:47 am Post subject: Please critique my electrical design |
|
|
Quote: |
So....I'm betting that Mark meant he's measuring 10.6V *after* 15 seconds of cranking, but with no/minimal load on the battery. Now, go back to the Corvette/Chevette example. If you accelerate the Corvette for 15 seconds, it'll still have 400 HP, but you may only have 3 seconds of capacity (gas) left. |
The legacy LOAD TEST is an artifact carried
over from the automotive world. Automotive
load testers have a built in 15 second timer
that drives a light or perhaps a beeper.
[img]cid:.0[/img]
[img]cid:.1[/img] [img]cid:.2[/img]
When testing a battery, one starts the timer and then
cranks up the load knob to depress and hold voltage
at 9.0 volts. At the end of 15 seconds, you get a light
or a beep whereupon you read the current being delivered.
This is a 'cranking amps' kind of current and a figure of
merit for battery's suitability for continued service.
Quote: | Mark's test is even less valid if one has chosen a Lithium chemistry battery; their voltage has much less decline until it 'falls off the cliff' at full discharge. |
Absolutely. The legacy lead-acid load test is
not applicable to lithium.
Quote: | The real test is monitoring *how long* voltage remains above the voltage that indicates complete discharge (which is around 10.5 V), while the typical load from the plane's required (endurance bus) electronics is applied. |
Exactly. The load test numbers can give you a rough
idea of how the battery has degraded over time . . .
and tells you whether or not it will get your
engine going. But 8ut says NOTHING about capacity . . .
i.e. an ability to power ENDURANCE loads for the interval
you have established with design goals.
When the e-bus first appeared in OBAM aircraft,
a recommended design goal was to have electrical
endurance exceed fuel endurance. Obviously,
not a hard-n-fast rule but what every number
the builder chooses, it's really a pretty cool
thing to VERIFY that the number can be achieved.
There's a secondary benefit for replacing a
battery that fails to meet endurance requirements . . .
it's probably going to be replaced before its
cranking ability is seriously compromised. Hence,
exceedingly low probability of an off-home-base failure
of the battery.
Bob . . .
| - The Matronics AeroElectric-List Email Forum - | | Use the List Feature Navigator to browse the many List utilities available such as the Email Subscriptions page, Archive Search & Download, 7-Day Browse, Chat, FAQ, Photoshare, and much more:
http://www.matronics.com/Navigator?AeroElectric-List |
|
Description: |
|
Filesize: |
252.1 KB |
Viewed: |
8056 Time(s) |
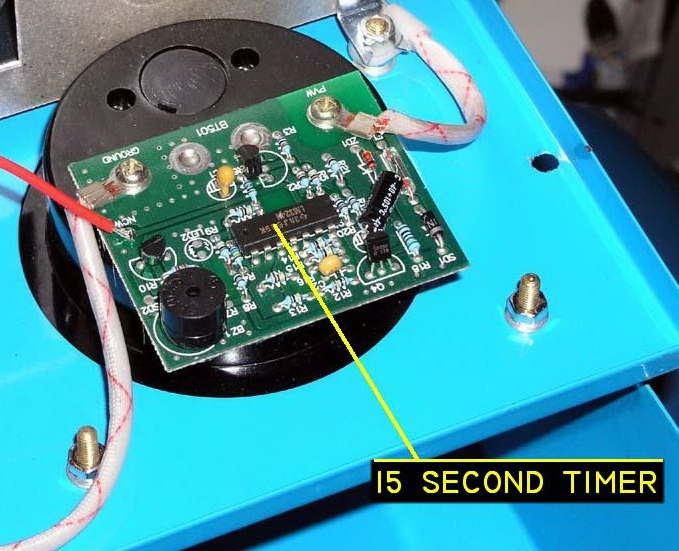
|
Description: |
|
Filesize: |
51.43 KB |
Viewed: |
8056 Time(s) |
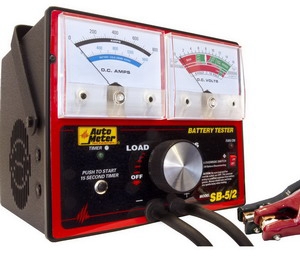
|
Description: |
|
Filesize: |
67.54 KB |
Viewed: |
8056 Time(s) |
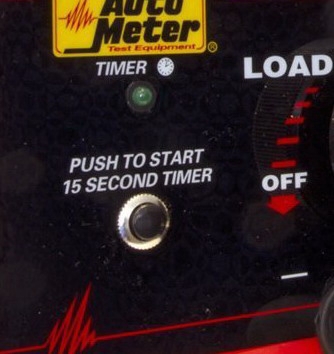
|
|
|
Back to top |
|
 |
nuckolls.bob(at)aeroelect Guest
|
Posted: Wed Apr 11, 2018 11:56 am Post subject: Please critique my electrical design |
|
|
At 02:12 PM 4/11/2018, you wrote:
Quote: | Bob, thanks for reiterating the difference between a load test and a capacity test. Is there any possibility of gaining insight into a battery's capacity by studying the results of load testing? |
Only very roughly . . . even then it's
something that needs to be conducted pretty
often and results TRACKED with time.
I've not conducted such testing so I
can't offer even a rough correlation
of capacity vs. load-test. But
I'm guessing it is roughly proportional.
If your brand new battery tested at
say 600A, then it's probably reaching
end of life when the load test falls to
400A . . . even tho it still cranks
the engine.
Bob . . .
| - The Matronics AeroElectric-List Email Forum - | | Use the List Feature Navigator to browse the many List utilities available such as the Email Subscriptions page, Archive Search & Download, 7-Day Browse, Chat, FAQ, Photoshare, and much more:
http://www.matronics.com/Navigator?AeroElectric-List |
|
|
|
Back to top |
|
 |
mmoyle
Joined: 15 Jun 2015 Posts: 10 Location: Platinum, Alaska
|
Posted: Wed Apr 11, 2018 12:30 pm Post subject: Please critique my electrical design |
|
|
Quote: | Quote: | 10.6V *after* 15 seconds of cranking, but with no/minimal load on the battery |
| Nope, The starter is the battery load tester. Continuously measure the voltage while the starter is engaged. If the voltage drops below 10.6 volts while cranking the battery needs to be charged and tested again. A health battery will return to 12 +volts after opening the starting circuit. Another piece of test gear is a an amp meter with amp shut between the negative terminal and battery post... (which I like better than the amp probe I use with the fluke 87) to test the health of the starter...say the load spikes to 250 amps to overcome the inertial mass of the rotating parts then drops to 125-150 amps...starter tests good. The only other charging system health test is charging voltage... automotive standards were 13.6 to 14.8 VDC...aircraft with solid state voltage regulator is 14.1 volts...I think.
Sent from my iPad
On 11 Apr 2018, at 11:46 AM, Robert L. Nuckolls, III <nuckolls.bob(at)aeroelectric.com (nuckolls.bob(at)aeroelectric.com)> wrote:
Quote: | Quote: |
So....I'm betting that Mark meant he's measuring 10.6V *after* 15 seconds of cranking, but with no/minimal load on the battery. Now, go back to the Corvette/Chevette example. If you accelerate the Corvette for 15 seconds, it'll still have 400 HP, but you may only have 3 seconds of capacity (gas) left. |
The legacy LOAD TEST is an artifact carried
over from the automotive world. Automotive
load testers have a built in 15 second timer
that drives a light or perhaps a beeper.
<27063fc.jpg>
<270642b.jpg> <270643b.jpg>
When testing a battery, one starts the timer and then
cranks up the load knob to depress and hold voltage
at 9.0 volts. At the end of 15 seconds, you get a light
or a beep whereupon you read the current being delivered.
This is a 'cranking amps' kind of current and a figure of
merit for battery's suitability for continued service.
Quote: | Mark's test is even less valid if one has chosen a Lithium chemistry battery; their voltage has much less decline until it 'falls off the cliff' at full discharge. |
Absolutely. The legacy lead-acid load test is
not applicable to lithium.
Quote: | The real test is monitoring *how long* voltage remains above the voltage that indicates complete discharge (which is around 10.5 V), while the typical load from the plane's required (endurance bus) electronics is applied. |
Exactly. The load test numbers can give you a rough
idea of how the battery has degraded over time . . .
and tells you whether or not it will get your
engine going. But 8ut says NOTHING about capacity . . .
i.e. an ability to power ENDURANCE loads for the interval
you have established with design goals.
When the e-bus first appeared in OBAM aircraft,
a recommended design goal was to have electrical
endurance exceed fuel endurance. Obviously,
not a hard-n-fast rule but what every number
the builder chooses, it's really a pretty cool
thing to VERIFY that the number can be achieved.
There's a secondary benefit for replacing a
battery that fails to meet endurance requirements . . .
it's probably going to be replaced before its
cranking ability is seriously compromised. Hence,
exceedingly low probability of an off-home-base failure
of the battery.
Bob . . .
|
| - The Matronics AeroElectric-List Email Forum - | | Use the List Feature Navigator to browse the many List utilities available such as the Email Subscriptions page, Archive Search & Download, 7-Day Browse, Chat, FAQ, Photoshare, and much more:
http://www.matronics.com/Navigator?AeroElectric-List |
|
|
|
Back to top |
|
 |
N884RA
Joined: 22 Mar 2018 Posts: 6
|
Posted: Wed Apr 11, 2018 12:42 pm Post subject: Re: Please critique my electrical design |
|
|
Bob,
Thanks for the corrections.
nuckolls.bob(at)aeroelect wrote: |
The ovm14 can come out, that's built into the LR3. |
Okay, thanks. I've corrected that in the latest version.
Quote: | If your using a fused bus, then the fusible link
and remotely located field breaker stays in. |
Just to make sure I'm following -- I'm placing the Alt Fld CB on a bus bar along with three other CBs (Main Bus 2). In this case I don't need the fusible link, correct? I've kept the fusible link between Main Bus 1 (fuses) and Main Bus 2 (CBs) because the distance is about 18".
Quote: | The G3X has its own low voltage sense, resolution
and display feature. If you don't wish to use the
separate light featured in the LR3C installation,
just leave that terminal unused.
YES! that is your bus voltage sense lead. |
Thanks -- I removed the light and I'll use the G3X annunciator for LV, but I left the terminal 3 feed with the 2A CB.
https://www.dropbox.com/s/2l10pzbcba4z4k7/Electrical%20System%20Overview%20%28v13.11%29.pdf?dl=0
| - The Matronics AeroElectric-List Email Forum - | | Use the List Feature Navigator to browse the many List utilities available such as the Email Subscriptions page, Archive Search & Download, 7-Day Browse, Chat, FAQ, Photoshare, and much more:
http://www.matronics.com/Navigator?AeroElectric-List |
|
|
|
Back to top |
|
 |
nuckolls.bob(at)aeroelect Guest
|
Posted: Wed Apr 11, 2018 7:55 pm Post subject: Please critique my electrical design |
|
|
At 03:30 PM 4/11/2018, you wrote: Quote: | Quote: | Quote: | 10.6V *after* 15 seconds of cranking, but with no/minimal load on the battery |
| Nope, The starter is the battery load tester. Continuously measure the voltage while the starter is engaged. If the voltage drops below 10.6 volts while cranking the battery needs to be charged and tested again. A health battery will return to 12 +volts after opening the starting circuit. Another piece of test gear is a an amp meter with amp shut between the negative terminal and battery post... (which I like better than the amp probe I use with the fluke 87) to test the health of the starter...say the load spikes to 250 amps to overcome the inertial mass of the rotating parts then drops to 125-150 amps...starter tests good.
The only other charging system health test is charging voltage... automotive standards were 13.6 to 14.8 VDC...aircraft with solid state voltage regulator is 14.1 volts...I think. |
Meaningful data confirming battery condition
is hard to come by. Variation in starter draw
due to the modulated torque loads presented
by reciprocating pistons produces a wildly
unstable value on an analog meter . . . and
can drive many digital displays nuts.
I've done energy demand studies using fast
data acquisition systems that sample several
hundred times per second combined with
'integration by parts' software that
yields very stable numbers.
But just as in most vehicles, a flagging starter
battery will make it's condition known because
of how it sounds . . . and the bottom line for
cranking demands only that the engine got going
yet one more time.
A battery that's demonstrating decreased
starter performance may already have sagged
below the ca[acotu for continued service as set by
design goals.
Bob . . .
| - The Matronics AeroElectric-List Email Forum - | | Use the List Feature Navigator to browse the many List utilities available such as the Email Subscriptions page, Archive Search & Download, 7-Day Browse, Chat, FAQ, Photoshare, and much more:
http://www.matronics.com/Navigator?AeroElectric-List |
|
|
|
Back to top |
|
 |
jan_de_jong(at)casema.nl Guest
|
Posted: Wed Apr 11, 2018 10:15 pm Post subject: Please critique my electrical design |
|
|
Anecdotally:
I replaced the 60Ah battery of the Ford Mondeo in preparation for a
skiing trip.
It wouldn't take more than an 18 Ah charge from empty. It still cranked
fine.
| - The Matronics AeroElectric-List Email Forum - | | Use the List Feature Navigator to browse the many List utilities available such as the Email Subscriptions page, Archive Search & Download, 7-Day Browse, Chat, FAQ, Photoshare, and much more:
http://www.matronics.com/Navigator?AeroElectric-List |
|
|
|
Back to top |
|
 |
rsmith52
Joined: 16 Mar 2017 Posts: 15 Location: Crawford, CO
|
Posted: Thu Apr 12, 2018 5:57 am Post subject: Re: Please critique my electrical design |
|
|
The GMU 11 takes power directly from the bus through a 2 amp breaker. Maybe you were thinking of the GMU 22 which is powered through the GSU 25.
| - The Matronics AeroElectric-List Email Forum - | | Use the List Feature Navigator to browse the many List utilities available such as the Email Subscriptions page, Archive Search & Download, 7-Day Browse, Chat, FAQ, Photoshare, and much more:
http://www.matronics.com/Navigator?AeroElectric-List |
|
|
|
Back to top |
|
 |
rsmith52
Joined: 16 Mar 2017 Posts: 15 Location: Crawford, CO
|
Posted: Thu Apr 12, 2018 5:59 am Post subject: Re: Please critique my electrical design |
|
|
The GMU 11 takes power directly from the bus through a 2 amp breaker. Maybe you were thinking of the GMU 22 which is powered through the GSU 25.
| - The Matronics AeroElectric-List Email Forum - | | Use the List Feature Navigator to browse the many List utilities available such as the Email Subscriptions page, Archive Search & Download, 7-Day Browse, Chat, FAQ, Photoshare, and much more:
http://www.matronics.com/Navigator?AeroElectric-List |
|
|
|
Back to top |
|
 |
|
|
You cannot post new topics in this forum You cannot reply to topics in this forum You cannot edit your posts in this forum You cannot delete your posts in this forum You cannot vote in polls in this forum You cannot attach files in this forum You can download files in this forum
|
Powered by phpBB © 2001, 2005 phpBB Group
|