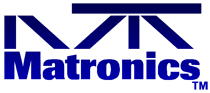 |
Matronics Email Lists Web Forum Interface to the Matronics Email Lists
|
View previous topic :: View next topic |
Author |
Message |
alec(at)alecmyers.com Guest
|
Posted: Fri Feb 01, 2019 1:45 pm Post subject: Overvoltage protection and other stuff |
|
|
Bob et al.
I’m working with my engineering representative to modify a TC aircraft to replace a 28V Gill flooded battery with a pair of 12V Odyssey AGM in a different location.
The new location while not “sealed”, is not provided with ventilation to the outside.
Today’s task is to demonstrate the new installation will comply with 23.1353(d) which reads:
"No explosive or toxic gases emitted by any battery in normal operation, or as the result of any probable malfunction in the charging system or battery installation, may accumulate in hazardous quantities within the airplane.”
After conversation with Odyssey and after reading their and other technical material I am happy to argue that the only “probable” malfunction in the charging system or battery installation that could result in a release of a hazardous quantity of gas would be a prolonged over-voltage event (>30V for the two batteries in series). That would release some quantity of hydrogen.
The aircraft charging system is based on a Bosch 28V automotive alternator; I don’t have any technical details of whether it has any inbuilt over-voltage protection. The Approved Flight Manual indicates that an over-voltage condition has to be noticed by the pilot and pilot action is required to take the alternator off-line manually by pulling the c/b. So it’s probable there’s no automatic protection included.
To demonstrate that I’m compliant with 23.1353(d) I’m thinking of including in the modification the installation of a crowbar protection module on the alternator field coil.
So… to get to the question… can anyone suggest a part number/supplier for a 28V OV module (30V trigger voltage)? Ideally one that is already in use on a TC airplane somewhere, which will make it easier to have that part approved as part of the modification.
Or are there any other ways I could provide comfort with respect to 23.1353?
Thanks for any ideas
| - The Matronics AeroElectric-List Email Forum - | | Use the List Feature Navigator to browse the many List utilities available such as the Email Subscriptions page, Archive Search & Download, 7-Day Browse, Chat, FAQ, Photoshare, and much more:
http://www.matronics.com/Navigator?AeroElectric-List |
|
|
|
Back to top |
|
 |
user9253
Joined: 28 Mar 2008 Posts: 1930 Location: Riley TWP Michigan
|
|
Back to top |
|
 |
ceengland7(at)gmail.com Guest
|
|
Back to top |
|
 |
nuckolls.bob(at)aeroelect Guest
|
Posted: Sat Feb 02, 2019 7:36 am Post subject: Overvoltage protection and other stuff |
|
|
At 03:43 PM 2/1/2019, you wrote:
Quote: | --> AeroElectric-List message posted by: Alec Myers <alec(at)alecmyers.com>
Bob et al.
I’m working with my engineering representative to modify a TC aircraft to replace a 28V Gill flooded battery with a pair of 12V Odyssey AGM in a different location.
The new location while not “sealed”, is not provided with ventilation to the outside.
Today’s task is to demonstrate the new installation will comply with 23.1353(d) which reads:
"No explosive or toxic gases emitted by any battery in normal operation, or as the result of any probable malfunction in the charging system or battery installation, may accumulate in hazardous quantities within the airplane.” |
There HAVE been H-O explosions associated with
SVLA batteries. The only two I've been privy
to were (1) an internal explosion on a 44AH
bizjet battery that suffered an open, inter-cell
weld in the top of the battery. The explosion
cracked the case but did not cause damage
to the aircraft.
A second case was in a GlasAir fitted with
a battery box behind the passenger seat. The
battery contactor was inside the box too.
The battery had been subjected to a sustained
ov condition. The pilot was engaged in some
exploratory, switch-flipping diagnostics
that ignited the trapped gasses inside the
battery box and blew it up.
The WORST policy for dealing with an
outgassing battery is to enclose it. The
battery box was originally intended to
conduct SPILLS over overboard. It had
nothing to do with venting of gasses.
The abused SLVA battery is LEAST likely
to provoke a bad day in the cockpit by
strapping it down to an open tray. Any
dangerous gasses that do escape the
battery simply waft away. Explosions
occur when fuel is ignited within a
tightly closed space.
If 'fuel' is generated by an abused battery,
the best prophylactic against explosion
is to let it waft way. It won't explode
or burn even if you ARE a smoker.
Quote: | After conversation with Odyssey and after reading their and other technical material I am happy to argue that the only “probable” malfunction in the charging system or battery installation that could result in a release of a hazardous quantity of gas would be a prolonged over-voltage event (>30V for the two batteries in series). That would release some quantity of hydrogen. |
Not the point. Proper conduct of FMEA
considers ONLY one failure at a time.
Assume that the battery WILL be abused
as some point in the future. Then eliminate
probability that the failure escalates
into a more excited situation or propagation
out to the rest of the system.
Strap it down in the open air and you're
good to go.
Quote: | The aircraft charging system is based on a Bosch 28V automotive alternator; I don’t have any technical details of whether it has any inbuilt over-voltage protection. The Approved Flight Manual indicates that an over-voltage condition has to be noticed by the pilot and pilot action is required to take the alternator off-line manually by pulling the c/b. So it’s probable there’s no automatic protection included.
To demonstrate that I’m compliant with 23.1353(d) I’m thinking of including in the modification the installation of a crowbar protection module on the alternator field coil.
So� to get to the question� can anyone suggest a part number/supplier for a 28V OV module (30V trigger voltage)? Ideally one that is already in use on a TC airplane somewhere, which will make it easier to have that part approved as part of the modification.
.
Or are there any other ways I could provide comfort with respect to 23.1353? |
Adding ov protection is called for
by FMEA on the alternator irrespective
of any other components on the aircraft.
For decades, builders and some manufactures
have modified internally regulated alternators
to (1) remove internal regulators and (2)
install legacy regulator/ov protection.
I'll suggest that the confident fast-track
is to do that mod to the alternator and install
a regulator qualified for TC aircraft like
https://tinyurl.com/yb6o5vtn
or for OBAM aircraft
https://tinyurl.com/y9tlkpyo
Depending on your airplane's station in
the aviation hierarchy.
Both of these examples will come with
OV protection . . . the B&C product
also offers OV annunciation.
Bob . . .
| - The Matronics AeroElectric-List Email Forum - | | Use the List Feature Navigator to browse the many List utilities available such as the Email Subscriptions page, Archive Search & Download, 7-Day Browse, Chat, FAQ, Photoshare, and much more:
http://www.matronics.com/Navigator?AeroElectric-List |
|
|
|
Back to top |
|
 |
alec(at)alecmyers.com Guest
|
Posted: Sat Feb 02, 2019 11:47 am Post subject: Overvoltage protection and other stuff |
|
|
Quote: | Strap it down in the open air and you're
good to go.
|
It is (they are) going to be located under the seat. The airframe is composite, and the seat frame is part of the airframe, forming a well, but the seat top doesn’t seal tight, so let’s assume that that the seat void is adequately ventilated for lighter-than-air gas to the rest of the cabin. Being a modern airframe, the cabin is relatively leak and draught free. The bubble canopy seals well with a rubber cushion all the way around. When the cabin ventilation system is shut off, there are no draughts.
The lower explosive limit for Hydrogen is 4%. Taking a factor of 4 safety, and assuming a cabin volume of 3m^3, a hazardous amount of H2 is 30 litres.
Outgassing from all lead acid batteries during a significant over voltage event is 7.6ml H2 / cell / amp / minute. RG technology works great to reduce outgassing at low charge rates but isn’t a lot of use at high currents.
The alternator is fitted with a 30A breaker. The worst case continuous release of hydrogen would occur when the alternator produces a voltage sufficient to charge the already-charged battery with a current of exactly 30A. Any more and the breaker will trip.
There are 12 cells between the two batteries. That means that the worst case production of H2 is 2.7 litres / minute. A hazardous environment would follow, for regulatory purposes, in approximately 10-15 minutes, assuming no ventilation.
I am *not* permitted to assume that the pilot will take the appropriate corrective action within that period and shut down the alternator. If I want to claim that the level of cabin ventilation is guaranteed to vent hydrogen at a rate sufficient to prevent buildup of 30l of H2 in that sort of time frame, I will have to justify that with adequate data.
Alternatively if there is an over-voltage trip that prevents the bus voltage rising above 32V, then the battery would have to be limiting the overcharging current to less than 4A. The time to a hazardous buildup of H2 in the cabin would be 7.5 times greater, or more than one hour.
At a current of 4A, I can carry out an experiment with the proposed battery and a power supply in the actual aircraft in a hangar, in still air conditions, to measure the cabin H2 concentration rate of rise. (I don’t think I could find a power supply with sufficient voltage overhead to force 30A through a lead acid battery, nor would I feel comfortable doing so.)
Another way to satisfy regulatory requirement is to use a Concorde RG-11M that has a manifold and a vent tube. I can connect the vent tube to the original vent provided for the flooded battery, and the requirement is satisfied because all gas will vent to the outside. The disadvantages are that it’s a lot more expensive than two odyssey batteries. And at 27lbs, harder to mount.
Quote: | > I'll suggest that the confident fast-track
is to do that mod to the alternator and install
|
a regulator qualified for TC aircraft like
There is merit in this idea, but I am concerned about project creep. To the extent that the existing IR alternator passed certification, it’s not an absolute requirement to upgrade it.
On Feb 2, 2019, at 10:36 AM, Robert L. Nuckolls, III <nuckolls.bob(at)aeroelectric.com> wrote:
At 03:43 PM 2/1/2019, you wrote:
Quote: |
Bob et al.
Iâm working with my engineering representative to modify a TC aircraft to replace a 28V Gill flooded battery with a pair of 12V Odyssey AGM in a different location.
The new location while not âsealedâ, is not provided with ventilation to the outside.
Todayâs task is to demonstrate the new installation will comply with 23.1353(d) which reads:
"No explosive or toxic gases emitted by any battery in normal operation, or as the result of any probable malfunction in the charging system or battery installation, may accumulate in hazardous quantities within the airplane.â
|
There HAVE been H-O explosions associated with
SVLA batteries. The only two I've been privy
to were (1) an internal explosion on a 44AH
bizjet battery that suffered an open, inter-cell
weld in the top of the battery. The explosion
cracked the case but did not cause damage
to the aircraft.
A second case was in a GlasAir fitted with
a battery box behind the passenger seat. The
battery contactor was inside the box too.
The battery had been subjected to a sustained
ov condition. The pilot was engaged in some
exploratory, switch-flipping diagnostics
that ignited the trapped gasses inside the
battery box and blew it up.
The WORST policy for dealing with an
outgassing battery is to enclose it. The
battery box was originally intended to
conduct SPILLS over overboard. It had
nothing to do with venting of gasses.
The abused SLVA battery is LEAST likely
to provoke a bad day in the cockpit by
strapping it down to an open tray. Any
dangerous gasses that do escape the
battery simply waft away. Explosions
occur when fuel is ignited within a
tightly closed space.
If 'fuel' is generated by an abused battery,
the best prophylactic against explosion
is to let it waft way. It won't explode
or burn even if you ARE a smoker.
Quote: | After conversation with Odyssey and after reading their and other technical material I am happy to argue that the only âprobableâ malfunction in the charging system or battery installation that could result in a release of a hazardous quantity of gas would be a prolonged over-voltage event (>30V for the two batteries in series). That would release some quantity of hydrogen.
|
Not the point. Proper conduct of FMEA
considers ONLY one failure at a time.
Assume that the battery WILL be abused
as some point in the future. Then eliminate
probability that the failure escalates
into a more excited situation or propagation
out to the rest of the system.
Strap it down in the open air and you're
good to go.
Quote: | The aircraft charging system is based on a Bosch 28V automotive alternator; I donât have any technical details of whether it has any inbuilt over-voltage protection. The Approved Flight Manual indicates that an over-voltage condition has to be noticed by the pilot and pilot action is required to take the alternator off-line manually by pulling the c/b. So itâs probable thereâs no automatic protection included.
To demonstrate that Iâm compliant with 23.1353(d) Iâm thinking of including in the modification the installation of a crowbar protection module on the alternator field coil.
So
> to get to the question
> can anyone suggest a part number/supplier for a 28V OV module (30V trigger voltage)? Ideally one that is already in use on a TC airplane somewhere, which will make it easier to have that part approved as part of the modification.
.
Or are there any other ways I could provide comfort with respect to 23.1353?
|
Adding ov protection is called for
by FMEA on the alternator irrespective
of any other components on the aircraft.
For decades, builders and some manufactures
have modified internally regulated alternators
to (1) remove internal regulators and (2)
install legacy regulator/ov protection.
I'll suggest that the confident fast-track
is to do that mod to the alternator and install
a regulator qualified for TC aircraft like
https://tinyurl.com/yb6o5vtn
or for OBAM aircraft
https://tinyurl.com/y9tlkpyo
Depending on your airplane's station in
the aviation hierarchy.
Both of these examples will come with
OV protection . . . the B&C product
also offers OV annunciation.
Bob . . .
| - The Matronics AeroElectric-List Email Forum - | | Use the List Feature Navigator to browse the many List utilities available such as the Email Subscriptions page, Archive Search & Download, 7-Day Browse, Chat, FAQ, Photoshare, and much more:
http://www.matronics.com/Navigator?AeroElectric-List |
|
|
|
Back to top |
|
 |
art(at)zemon.name Guest
|
Posted: Sat Feb 02, 2019 3:52 pm Post subject: Overvoltage protection and other stuff |
|
|
On Sat, Feb 2, 2019 at 2:04 PM Alec Myers <alec(at)alecmyers.com (alec(at)alecmyers.com)> wrote:
Quote: | It is (they are) going to be located under the seat. The airframe is composite, and the seat frame is part of the airframe, forming a well, but the seat top doesn’t seal tight, |
Alec,
How about a low tech solution? Add a small vent from the well to the outside of the fuselage so that, whenever the airplane is in motion, low pressure on the outside draws air past the seat top, past the batteries, and out.
-- Art Z.
--
https://CheerfulCurmudgeon.com/"Be kind, for everyone you meet is fighting a hard battle."
| - The Matronics AeroElectric-List Email Forum - | | Use the List Feature Navigator to browse the many List utilities available such as the Email Subscriptions page, Archive Search & Download, 7-Day Browse, Chat, FAQ, Photoshare, and much more:
http://www.matronics.com/Navigator?AeroElectric-List |
|
|
|
Back to top |
|
 |
alec(at)alecmyers.com Guest
|
Posted: Sat Feb 02, 2019 4:20 pm Post subject: Overvoltage protection and other stuff |
|
|
I love low-tech! I don’t think that’s definitive enough for the powers that be, however. And… I don’t think my structures person will enjoy me drilling holes in a composite stressed fuselage just for a look see.
On the subject of over-voltage trips, I have discovered that both Carling and Sensata (Klixon) make circuit breakers with, for instance, a second coil that you can use to trip the breaker via an isolated circuit (that could easily be triggered by an over-voltage, in addition to the regular over-current coil. So one of those could be used to replace the b-lead CB. It will be a challenge to find small quantities of what is a very specialized part though.
On Feb 2, 2019, at 5:42 PM, Art Zemon <art(at)zemon.name> wrote:
On Sat, Feb 2, 2019 at 2:04 PM Alec Myers <alec(at)alecmyers.com> wrote:
It is (they are) going to be located under the seat. The airframe is composite, and the seat frame is part of the airframe, forming a well, but the seat top doesn’t seal tight,
Alec,
How about a low tech solution? Add a small vent from the well to the outside of the fuselage so that, whenever the airplane is in motion, low pressure on the outside draws air past the seat top, past the batteries, and out.
-- Art Z.
--
https://CheerfulCurmudgeon.com/
"Be kind, for everyone you meet is fighting a hard battle."
| - The Matronics AeroElectric-List Email Forum - | | Use the List Feature Navigator to browse the many List utilities available such as the Email Subscriptions page, Archive Search & Download, 7-Day Browse, Chat, FAQ, Photoshare, and much more:
http://www.matronics.com/Navigator?AeroElectric-List |
|
|
|
Back to top |
|
 |
nuckolls.bob(at)aeroelect Guest
|
Posted: Sun Feb 03, 2019 8:20 am Post subject: Overvoltage protection and other stuff |
|
|
At 01:46 PM 2/2/2019, you wrote:
Quote: | --> AeroElectric-List message posted by: Alec Myers <alec(at)alecmyers.com>
> Strap it down in the open air and you're
good to go.
It is (they are) going to be located under the seat. The airframe is composite, and the seat frame is part of the airframe, forming a well, but the seat top doesn’t seal tight, so let’s assume that that the seat void is adequately ventilated for lighter-than-air gas to the rest of the cabin. Being a modern airframe, the cabin is relatively leak and draught free. The bubble canopy seals well with a rubber cushion all the way around. When the cabin ventilation system is shut off, there are no draughts. |
<snip>
Quote: | The alternator is fitted with a 30A breaker. The worst case continuous release of hydrogen would occur when the alternator produces a voltage sufficient to charge the already-charged battery with a current of exactly 30A. Any more and the breaker will trip. |
B-lead protection should not be so small
as to be vulnerable to trip from alternator
output . . . b-lead protection is located
at the battery end of the b-lead feeder and
intended to mitigate shorts in the alternator
that are fed from the battery . . .
Quote: | There are 12 cells between the two batteries. That means that the worst case production of H2 is 2.7 litres / minute. A hazardous environment would follow, for regulatory purposes, in approximately 10-15 minutes, assuming no ventilation. |
Can't argue the numbers based on what I have
immediately in hand. I need to dig through
the archives and see what I gathered from
some studies at both Hawker-Enersys and
Concorde waaayyy back when.
Quote: | At a current of 4A, I can carry out an experiment with the proposed battery and a power supply in the actual aircraft in a hangar, in still air conditions, to measure the cabin H2 concentration rate of rise. (I don’t think I could find a power supply with sufficient voltage overhead to force 30A through a lead acid battery, nor would I feel comfortable doing so.) |
An SVLA battery is also referred to as a 'starved
electrolyte' battery. This refers to the fact that
a design goal is to minimize the water it contains.
The separators are tissue thin and about 90%
saturated with electrolyte. If you disassembled
a new battery and wrung out a separator with your
fingers, you would be unable to produce liquid.
Electrolyte is added to cells at Enersys by
an automated process that injects precise
amounts into each cell in order to achieve that
90% number. At Concorde, I saw cells being
'topped off' with liquid and left to stand for
a period of time before the batteries were turned
over and allowed to drain before the pressure
relief caps were installed. Again, a technique
intended to limit the amount of retained water.
I'll have to find the data but I think there
is so little water in the typical SE battery
that risks from an H2 + 0 explosion in anything
but the smallest of containments is essentially
zero.
Battery explosions I'm aware of and those
cited on 'net are INTERNAL to the battery; a product
of some external energy source combined with a
failure internal to the battery. If we're going
to mitigate that failure mode, then yes, a
MECHANICALLY robust container is called for.
An SVLA battery in overcharge distress is not
limited too dissolution of the water into
H and O. There is chemical conversion
and I(squared)R heat generated. When an SVLA
battery begins to vent, no doubt there will be
some free hydrogen but other constituents that
smell really bad.
An alternator runaway in flight still has
some system loads in addition to the battery's
over-charge loads which reduces the alternator's
ability to abuse the battery.
A lightly loaded 60A alternator in runaway
pushes the battery up into the 17-18 volt
range whereupon the battery grunts the overcharge
begins its death throes. The 20v for 1 second
withstand rule for 14v avionics recognizes
that it takes time for a battery-mitigated
ov condition to evolve. Plenty of time
for an ov management system to operate.
But assuming that the fault is allowed
to go to completion, it takes many minutes
and produces noxious vapors. Many pilots
who experienced uncontrolled runaways for
batteries mounted behind the cabin report
their first awareness of the condition by
the smell that managed to get forward.
I'm having trouble wrapping my head around
the idea that the worst possible failure
in the charging system would even begin to risk
blowing up a cabin dangerously charged with
hydrogen.
Quote: | >> I'll suggest that the confident fast-track
is to do that mod to the alternator and install
a regulator qualified for TC aircraft like
There is merit in this idea, but I am concerned about project creep. To the extent that the existing IR alternator passed certification, it’s not an absolute requirement to upgrade it. |
Not a requirement. Just a simple duplication
of a process that was experimentally
derived and repeated thousands of times
over the past 30+ years. It's one of
several recipes for success to meet
the design goal.
Bob . . .
| - The Matronics AeroElectric-List Email Forum - | | Use the List Feature Navigator to browse the many List utilities available such as the Email Subscriptions page, Archive Search & Download, 7-Day Browse, Chat, FAQ, Photoshare, and much more:
http://www.matronics.com/Navigator?AeroElectric-List |
|
|
|
Back to top |
|
 |
nuckolls.bob(at)aeroelect Guest
|
Posted: Sun Feb 03, 2019 8:27 am Post subject: Overvoltage protection and other stuff |
|
|
At 06:19 PM 2/2/2019, you wrote:
Quote: | --> AeroElectric-List message posted by: Alec Myers <alec(at)alecmyers.com>
I love low-tech! I don’t think that’s definitive enough for the powers that be, however. And� I don’t think my structures person will enjoy me drilling holes in a composite stressed fuselage just for a look see.
On the subject of over-voltage trips, I have discovered that both Carling and Sensata (Klixon) make circuit breakers with, for instance, a second coil that you can use to trip the breaker via an isolated circuit (that could easily be triggered by an over-voltage, in addition to the regular over-current coil. So one of those could be used to replace the b-lead CB. It will be a challenge to find small quantities of what is a very specialized part though. |
I proposed an ov protection system that was
based on the external trip feature for some
magnetic breakers . . . I think it was for
Swearingen Aircraft. The cost-benefit ratio
didn't ring their bells either.
Further, doing ov protection in the B-lead
is less than optimum. That's a VERY HIGH
ENERGY switching event that would continue
to produce voltage and ultimately destroy
the alternator too. Opening the field
circuit has been the legacy approach
since the first generators were strapped
to aircraft engines.
Bob . . .
| - The Matronics AeroElectric-List Email Forum - | | Use the List Feature Navigator to browse the many List utilities available such as the Email Subscriptions page, Archive Search & Download, 7-Day Browse, Chat, FAQ, Photoshare, and much more:
http://www.matronics.com/Navigator?AeroElectric-List |
|
|
|
Back to top |
|
 |
nuckolls.bob(at)aeroelect Guest
|
Posted: Sun Feb 03, 2019 8:50 am Post subject: Overvoltage protection and other stuff |
|
|
At 10:19 AM 2/3/2019, you wrote:
Quote: | At 01:46 PM 2/2/2019, you wrote:
Quote: | --> AeroElectric-List message posted by: Alec Myers <alec(at)alecmyers.com>
> Strap it down in the open air and you're
good to go.
It is (they are) going to be located under the seat. The airframe is composite, and the seat frame is part of the airframe, forming a well, but the seat top doesn’t seal tight, so let’s assume that that the seat void is adequately ventilated for lighter-than-air gas to the rest of the cabin. Being a modern airframe, the cabin is relatively leak and draught free. The bubble canopy seals well with a rubber cushion all the way around. When the cabin ventilation system is shut off, there are no draughts. |
|
If one is hard-over with out-gassing
concerns, it's possible to add your
own vent plumbing to most batteries.
A PC-680 has a 'manifold" that just
doesn't happen to have a vent connection
[img]cid:.0[/img]
You could drill a hole though the vent gallery cover
and bond a tube fitting to the lid. Then add length
of Tygon or similar to conduct vented gasses anywhere
else you wished to go . . . perhaps to the
extreme end of the empennage? If there are two batteries,
the tubes could be Y-ed into a single tube for
remote disposal of the gasses. You might add some
robust sealant around the periphery of the gallery
cap . . . E6000 would be good.
The collection of pictures at . . .
https://tinyurl.com/blt9x3l
illustrates some extreme effects of overcharge
wherein excess energy produced effects in addition
to generating explosive gasses.
I'll keep digging in the library . . .
Bob . . .
| - The Matronics AeroElectric-List Email Forum - | | Use the List Feature Navigator to browse the many List utilities available such as the Email Subscriptions page, Archive Search & Download, 7-Day Browse, Chat, FAQ, Photoshare, and much more:
http://www.matronics.com/Navigator?AeroElectric-List |
|
Description: |
|
Filesize: |
150.88 KB |
Viewed: |
7301 Time(s) |
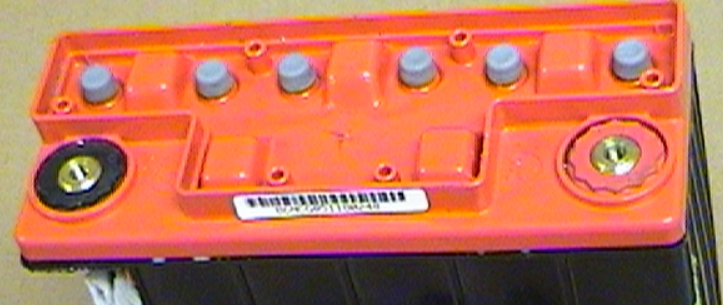
|
|
|
Back to top |
|
 |
alec(at)alecmyers.com Guest
|
Posted: Sun Feb 03, 2019 11:19 am Post subject: Overvoltage protection and other stuff |
|
|
That’s a possibility… I already have an overboard vent from the original installation of the (flooded) Gill battery. If I go the $$$ route and install the Concorde RG version it has a manifold I was planning to run a tube to it.
Do you have any data about what happened to that Odyssey?
On the subject of over voltage tripping, I was looking through the technical literature for (eg)
On Feb 3, 2019, at 11:49 AM, Robert L. Nuckolls, III <nuckolls.bob(at)aeroelectric.com> wrote:
At 10:19 AM 2/3/2019, you wrote:
Quote: | At 01:46 PM 2/2/2019, you wrote:
>
>
> > Strap it down in the open air and you're
> good to go.
>
> It is (they are) going to be located under the seat. The airframe is composite, and the seat frame is part of the airframe, forming a well, but the seat top doesnât seal tight, so letâs assume that that the seat void is adequately ventilated for lighter-than-air gas to the rest of the cabin. Being a modern airframe, the cabin is relatively leak and draught free. The bubble canopy seals well with a rubber cushion all the way around. When the cabin ventilation system is shut off, there are no draughts.
|
If one is hard-over with out-gassing
concerns, it's possible to add your
own vent plumbing to most batteries.
A PC-680 has a 'manifold" that just
doesn't happen to have a vent connection
<194a8106.jpg>
You could drill a hole though the vent gallery cover
and bond a tube fitting to the lid. Then add length
of Tygon or similar to conduct vented gasses anywhere
else you wished to go . . . perhaps to the
extreme end of the empennage? If there are two batteries,
the tubes could be Y-ed into a single tube for
remote disposal of the gasses. You might add some
robust sealant around the periphery of the gallery
cap . . . E6000 would be good.
The collection of pictures at . . .
https://tinyurl.com/blt9x3l
illustrates some extreme effects of overcharge
wherein excess energy produced effects in addition
to generating explosive gasses.
I'll keep digging in the library . . .
Bob . . .
| - The Matronics AeroElectric-List Email Forum - | | Use the List Feature Navigator to browse the many List utilities available such as the Email Subscriptions page, Archive Search & Download, 7-Day Browse, Chat, FAQ, Photoshare, and much more:
http://www.matronics.com/Navigator?AeroElectric-List |
|
|
|
Back to top |
|
 |
peter(at)sportingaero.com Guest
|
Posted: Sun Feb 03, 2019 2:13 pm Post subject: Overvoltage protection and other stuff |
|
|
Quote: | I love low-tech! I don’t think that’s definitive enough for the powers that be, however. And… I don’t think my structures person will enjoy me drilling holes in a composite stressed fuselage just for a look see.
|
Slightly off topic, but relevant to this thread, composite structures are very tolerant of small holes. Some airframes have reinforcing belts (uni-directional fibres, say 3" wide), as long as those are avoided a small hole for a vent pipe should be no problem from the structural perspective. Drag or aesthetically wise it may be a different story, but don't assume a composite structure behaves the same as metal!
Peter
--
| - The Matronics AeroElectric-List Email Forum - | | Use the List Feature Navigator to browse the many List utilities available such as the Email Subscriptions page, Archive Search & Download, 7-Day Browse, Chat, FAQ, Photoshare, and much more:
http://www.matronics.com/Navigator?AeroElectric-List |
|
|
|
Back to top |
|
 |
Peter(at)sportingaero.com Guest
|
Posted: Sun Feb 03, 2019 2:14 pm Post subject: Overvoltage protection and other stuff |
|
|
Quote: | I love low-tech! I don’t think that’s definitive enough for the powers that be, however. And… I don’t think my structures person will enjoy me drilling holes in a composite stressed fuselage just for a look see.
|
Slightly off topic, but relevant to this thread, composite structures are very tolerant of small holes. Some airframes have reinforcing belts (uni-directional fibres, say 3" wide), as long as those are avoided a small hole for a vent pipe should be no problem from the structural perspective. Drag or aesthetically wise it may be a different story, but don't assume a composite structure behaves the same as metal!
Peter
--
| - The Matronics AeroElectric-List Email Forum - | | Use the List Feature Navigator to browse the many List utilities available such as the Email Subscriptions page, Archive Search & Download, 7-Day Browse, Chat, FAQ, Photoshare, and much more:
http://www.matronics.com/Navigator?AeroElectric-List |
|
|
|
Back to top |
|
 |
alec(at)alecmyers.com Guest
|
Posted: Mon Feb 04, 2019 8:04 am Post subject: Overvoltage protection and other stuff |
|
|
The certification basis for this aircraft is FAR23 (amendments 1-32 inc.) and that includes:
"23.1351(c)(5) Each generator must have an over-voltage control designed and installed to prevent damage to the electrical system, or to equipment supplied by the electrical system, that could result if that generator were to develop an over-voltage condition."
AC23-17C explains the rationale behind this rule (introduced in 1977) saying
"Explanation. Complete electrical system failures on both single and twin engine aircraft continue to occur. The electrical failure that causes this problem is often the loss of voltage control in the voltage regulator. This usually results in a bus voltage well above the capabilities of the electrical equipment connected to the bus. This overvoltage condition frequently destroys electronic equipment and boils the electrolyte in the battery.”
Bill - you must have first hand knowledge of the introduction of this rule, am I right?
When I look at the circuit diagram for the alternator on this aircraft installation it has the following:
[img]cid:5FA70F90-2701-4C5E-9DB9-BA6469BB8EBB(at)home[/img]
The connection leaving the exerpt at the bottom goes to the master switch. And one of the diodes on the generator relay is (I think) shown reverse connected. But apart from that I can see no overvoltage protection. Does the FAA consider that it is included in the design of the generator? (It’s a BOSCH standard part.)
Any thoughts?
On Feb 3, 2019, at 11:26 AM, Robert L. Nuckolls, III <nuckolls.bob(at)aeroelectric.com (nuckolls.bob(at)aeroelectric.com)> wrote:At 06:19 PM 2/2/2019, you wrote: Quote: | --> AeroElectric-List message posted by: Alec Myers <alec(at)alecmyers.com (alec(at)alecmyers.com)>I love low-tech! I donât think thatâs definitive enough for the powers that be, however. And
I donât think my structures person will enjoy me drilling holes in a composite stressed fuselage just for a look see. On the subject of over-voltage trips, I have discovered that both Carling and Sensata (Klixon) make circuit breakers with, for instance, a second coil that you can use to trip the breaker via an isolated circuit (that could easily be triggered by an over-voltage, in addition to the regular over-current coil. So one of those could be used to replace the b-lead CB. It will be a challenge to find small quantities of what is a very specialized part though. | I proposed an ov protection system that was based on the external trip feature for some magnetic breakers . . . I think it was for Swearingen Aircraft. The cost-benefit ratio didn't ring their bells either. Further, doing ov protection in the B-lead is less than optimum. That's a VERY HIGH ENERGY switching event that would continue to produce voltage and ultimately destroy the alternator too. Opening the field circuit has been the legacy approach since the first generators were strapped to aircraft engines. Bob . . .
| - The Matronics AeroElectric-List Email Forum - | | Use the List Feature Navigator to browse the many List utilities available such as the Email Subscriptions page, Archive Search & Download, 7-Day Browse, Chat, FAQ, Photoshare, and much more:
http://www.matronics.com/Navigator?AeroElectric-List |
|
Description: |
|
Filesize: |
105.99 KB |
Viewed: |
7291 Time(s) |
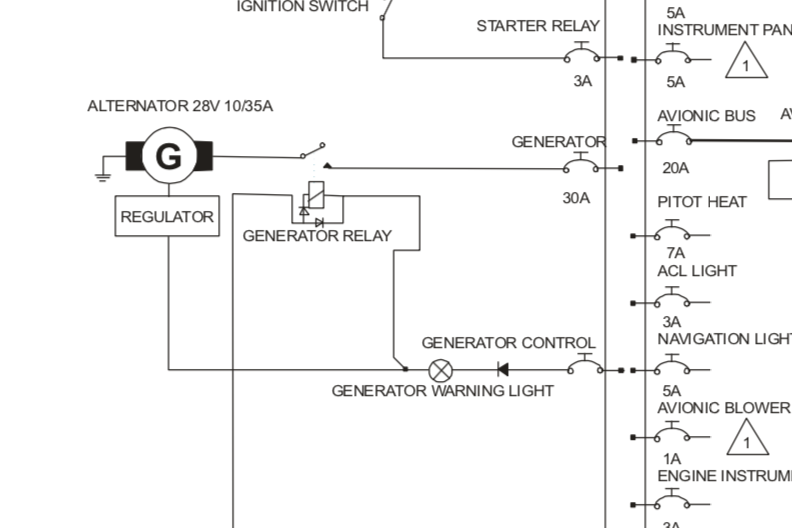
|
|
|
Back to top |
|
 |
nuckolls.bob(at)aeroelect Guest
|
Posted: Mon Feb 04, 2019 10:00 am Post subject: Overvoltage protection and other stuff |
|
|
At 10:04 AM 2/4/2019, you wrote:
Quote: | The certification basis for this aircraft is FAR23 (amendments 1-32 inc.) and that includes:
"23.1351(c)(5) Each generator must have an over-voltage control designed and installed to prevent damage to the electrical system, or to equipment supplied by the electrical system, that could result if that generator were to develop an over-voltage condition."
AC23-17C explains the rationale behind this rule (introduced in 1977) saying
"Explanation. Complete electrical system failures on both single and twin engine aircraft continue to occur. The electrical failure that causes this problem is often the loss of voltage control in the voltage regulator. This usually results in a bus voltage well above the capabilities of the electrical equipment connected to the bus. This overvoltage condition frequently destroys electronic equipment and boils the electrolyte in the battery.”
Bill - you must have first hand knowledge of the introduction of this rule, am I right? |
I had departed Cessna in 1969 (the second
time) when someone began stirring discussions
about adding ov protection. I did a prototype
design that I shared with my former colleagues.
The idea was adopted and became the Cessna C593001
OV sensor.
Here'a a collection of documents I've gathered
over he years on the history of the quantum-jump
into ov protection at Cessna Pawnee Plant in
the spring of 1971
https://tinyurl.com/yb4fljcf
Quote: | When I look at the circuit diagram for the alternator on this aircraft installation it has the following: |
It's a certainty that the system you've
illustrated has no OV protection. It can
be added in the form of a crowbar ov
protection module on the field supply
breaker:
https://tinyurl.com/ya3azjhk
or a DIY project
https://tinyurl.com/joeopsn
or by installing an alternator controller
that features self-contained ov protection.
Here's one set of examples . . .
https://tinyurl.com/y7dscw4y
There are many others.
Bob . . .
| - The Matronics AeroElectric-List Email Forum - | | Use the List Feature Navigator to browse the many List utilities available such as the Email Subscriptions page, Archive Search & Download, 7-Day Browse, Chat, FAQ, Photoshare, and much more:
http://www.matronics.com/Navigator?AeroElectric-List |
|
|
|
Back to top |
|
 |
|
|
You cannot post new topics in this forum You cannot reply to topics in this forum You cannot edit your posts in this forum You cannot delete your posts in this forum You cannot vote in polls in this forum You cannot attach files in this forum You can download files in this forum
|
Powered by phpBB © 2001, 2005 phpBB Group
|