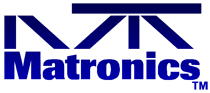 |
Matronics Email Lists Web Forum Interface to the Matronics Email Lists
|
View previous topic :: View next topic |
Author |
Message |
Tim Olson
Joined: 25 Jan 2007 Posts: 2879
|
Posted: Sun Mar 15, 2020 1:15 pm Post subject: Engine driven fuel Pump replacement tips |
|
|
Hi all, this was sent to me by Dan Masys to be posted as he is having issues posting.
With about 1200 hrs and 13 years since new, my factory-new IO-540 D4A5 is beginning to show signs of not being so factory-new any more. In the past month or so, fuel pressures have been drifting down to as low as 10-12 psi on extended climbs to altitudes above 10,000 MSL and although the engine has never stumbled, I figured it would be prudent to swap out the engine driven pump before anything dramatic happened. Â
Turns out replacing the pump on the back of the accessory case is quite a bit trickier than it should be, given that it is just held on by a couple of specialized allen head capscrew/bolts. After several of thrashing and cussing, I figured I'd better Google the topic and see what the story is. I found the difficulty replacing the Lycoming pump has been experienced by lots of RV builders, and there is a fair amount of creative disinformation out there -- workarounds that RVers took to grind down or shorten bolts, weird installation techniques, etc. But I did find the correct method, and when using it, the installation was pretty much a breeze. Â
Since this is all fresh in my mind, I thought I would pay it forward with a little tutorial on the subject as it relates to the RV-10. Here goes:
The issues
1. This is a big deal. There is at least one NTSB report of a fatal RV-7 crash caused by incorrect replacement installation of the engine driven fuel pump.
2. There are more ways to do it wrong than to do it right. The instructions that came with the Tempest replacement pump I got from Spruce show you the incorrect positionings to avoid, and tell you that the pushrod that presses from above onto the pump's actuator arm has to be in full up position, but they don't tell you how to do either of those things. Â
3. Although the RV-10 has lots more space between the engine and the firewall than most RV's, for this procedure all kinds of things are going to be in your way: spark plug cable bundles, SCAT tubing for oil cooler, wiring to magnetos and/or electronic ignition. Â
4. The major gotcha is that the lever arm of the fuel pump has to be positioned under the end of the vertical pushrod that drives it before bolting anything in place, but the special bolts can't be inserted in the fuel pump flange if you do that first -- they hit the body of the pump and can't be lined up with the threaded holes in the case. Â
The solutions to the above issues
1. Start with the right set of tools. You will need a small ladder to get up and over the engine (probably the same one you use to change the oil filter.) You also need a set of stubby combination wrenches, a 5/16 allen wrench with a ball/swivel style head and about a 4 inch long shaft or so. A 5/16 inch standard length combination wrench can be used to turn the allen wrench from the side for tightening and loosening the special bolts.
2. Once you have removed the old pump with its hoses disconnected but fittings still attached, put it aside on a workbench.
3. Remove one spark plug from all six cylinders -- bottom plugs are easiest.Â
4. Key point: in order to determine whether the engine driven pushrod is in its maximum up position, you have to put your hand into the fuel pump mounting hole and *put your finger on the bottom of the pushrod.* Push it up as far as it will go. Then, while holding it up, rotate the prop with the other hand at least two full turns so you can determine where 'top dead center' is on the pushrod. When you are satisfied that you know where the full up position is, leave the prop in that position and don't move it again until the new pump is in. Now take your finger off the pushrod. You will notice it immediately slides back down to its lowest position (!!) even though the cam driving it is in its highest position. (This is why you can't use an inspection mirror to determine the position of the pushrod.)
Some RVers apparently have gone to great lengths to try to get the shaft to stay up so the pump arm can be inserted, but it turns out this is not necessary. Just let it fall to its lowest position.
5. On the bench, swap the B nut fittings from the old pump to the new one. I found that I had to leave off the overflow fitting during initial installation due to interference with spark plug wire bundles and oil cooler SCAT tubing.
6. Place the new gasket on the mounting flange of the new pump. You might need a little dab of fuel lube to hold it in place even though it is a dry gasket seal. Insert the two mounting bolts fully before starting the attach procedure (they won't fit later if not inserted now.)
7. Key point: While holding the pump with its actuator arm pointed into the engine case, engage the bolt holes for the two mounting bolts, but only advance the bolts *one turn* or at most two. This is the difference between success and failure. With the bolts engaged only one turn, you will be able to tilt the fuel pump actuator down so that it slips underneath that pesky pushrod which fell to its lowest position. If you tighten the bolts any more than that, the actuator arm will hit the side of the pushrod and you will not be able to seat the pump.
8. You will know you are successful if the pump flange slides forward easily on the bolts and mates to the mounting surface of the engine accessory case with no resistance whatsoever. Anything else is no bueno -- pull the pump out and start again. (The fatal RV crash occurred because the builder cranked the bolts down in spite of interference and bent the pushrod shaft.)
9. Once the pump flange sits flat against the engine, hold the pump in place with one hand and tighten the bolts on both sides with the 5/16 inch allen wrench with the other. Â
10. Safety wire the special bolts to each other. (Also a bit of an adventure, but this one is left as an exercise for the student. ).
11. Reconnect in inflow, outflow and overflow lines to the pump. Replace lower spark plugs (new gaskets, of course), and oil filter. Start engine and do a leak test and fuel pressure test.
Hope this helps if you should find yourself needing to replace the engine driven pump on your Lycoming. Remember, if you are having to force anything, the new pump is not in its correct position. Happy flying.
Dan Masys
RV-10 N104LD
Tech counselor, EAA chapter 1541
----------------------------------------------------
In addition to Dan's comments, I would add this: As Dan notes, the holes are oblong and it appears designed to tilt the pump as you install it under the pushrod. That said, what I have had good luck with is this: I have used fine safety wire, or you could use dental floss, to run a couple of twists around that push rod, and then pull the thread out and tie it to the engine case or engine mount snugly. That will hold the push rod up. If you follow Dan's guidance, it shouldn't be necessary to hold the rod up, but myself I would prefer to have as much gap there as possible to ensure the rod gets in proper position on top of the lever. Just make sure whatever you use is removed completely before you fully seat the pump.
Hopefully Dan's post comes in handy for some of you.
Tim
| - The Matronics RV10-List Email Forum - | | Use the List Feature Navigator to browse the many List utilities available such as the Email Subscriptions page, Archive Search & Download, 7-Day Browse, Chat, FAQ, Photoshare, and much more:
http://www.matronics.com/Navigator?RV10-List |
|
|
|
Back to top |
|
 |
philperry9
Joined: 23 Nov 2011 Posts: 381
|
Posted: Sun Mar 15, 2020 1:34 pm Post subject: Engine driven fuel Pump replacement tips |
|
|
That's a good technique. I replaced two of them and it never was easy.
Next time I will have to try and tilt the pump a bit and see if that does
the trick.
I have always used the safety wire method too and it has worked reasonably
well. I've also heard of people jamming a tooth pick alongside the
actuator to hold it up; then snapping off the toothpick. The tip of the
tooth pick later passed through the system (supposedly). I'm not a fan of
that method.
Thanks for another alternative.
Phil
On Sun, Mar 15, 2020 at 4:20 PM Tim Olson <Tim(at)myrv10.com> wrote:
[quote] Hi all, this was sent to me by Dan Masys to be posted as he is having
issues posting.
With about 1200 hrs and 13 years since new, my factory-new IO-540 D4A5 is
beginning to show signs of not being so factory-new any more. In the past
month or so, fuel pressures have been drifting down to as low as 10-12 psi
on extended climbs to altitudes above 10,000 MSL and although the engine
has never stumbled, I figured it would be prudent to swap out the engine
driven pump before anything dramatic happened.
Turns out replacing the pump on the back of the accessory case is quite a
bit trickier than it should be, given that it is just held on by a couple
of specialized allen head capscrew/bolts. After several of thrashing and
cussing, I figured I'd better Google the topic and see what the story is.
I found the difficulty replacing the Lycoming pump has been experienced by
lots of RV builders, and there is a fair amount of creative disinformation
out there -- workarounds that RVers took to grind down or shorten bolts,
weird installation techniques, etc. But I did find the correct method, and
when using it, the installation was pretty much a breeze.
Since this is all fresh in my mind, I thought I would pay it forward with
a little tutorial on the subject as it relates to the RV-10. Here goes:
The issues
1. This is a big deal. There is at least one NTSB report of a fatal RV-7
crash caused by incorrect replacement installation of the engine driven
fuel pump.
2. There are more ways to do it wrong than to do it right. The
instructions that came with the Tempest replacement pump I got from Spruce
show you the incorrect positionings to avoid, and tell you that the pushrod
that presses from above onto the pump's actuator arm has to be in full up
position, but they don't tell you how to do either of those things.
3. Although the RV-10 has lots more space between the engine and the
firewall than most RV's, for this procedure all kinds of things are going
to be in your way: spark plug cable bundles, SCAT tubing for oil cooler,
wiring to magnetos and/or electronic ignition.
4. The major gotcha is that the lever arm of the fuel pump has to be
positioned under the end of the vertical pushrod that drives it before
bolting anything in place, but the special bolts can't be inserted in the
fuel pump flange if you do that first -- they hit the body of the pump and
can't be lined up with the threaded holes in the case.
The solutions to the above issues
1. Start with the right set of tools. You will need a small ladder to get
up and over the engine (probably the same one you use to change the oil
filter.) You also need a set of stubby combination wrenches, a 5/16 allen
wrench with a ball/swivel style head and about a 4 inch long shaft or so.
A 5/16 inch standard length combination wrench can be used to turn the
allen wrench from the side for tightening and loosening the special bolts
| - The Matronics RV10-List Email Forum - | | Use the List Feature Navigator to browse the many List utilities available such as the Email Subscriptions page, Archive Search & Download, 7-Day Browse, Chat, FAQ, Photoshare, and much more:
http://www.matronics.com/Navigator?RV10-List |
|
|
|
Back to top |
|
 |
Lenny Iszak
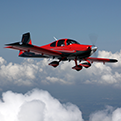
Joined: 23 Mar 2008 Posts: 270
|
Posted: Sun Mar 15, 2020 1:50 pm Post subject: Engine driven fuel Pump replacement tips |
|
|
I used lacing tape, it’s nice and grippy. One turn around the actuator pin and then tied it to the engine mount. Once the pump is in place untie the tape and it comes right out.
Lenny
Quote: | On Mar 15, 2020, at 5:41 PM, Phil Perry <philperry9(at)gmail.com> wrote:
That's a good technique. I replaced two of them and it never was easy. Next time I will have to try and tilt the pump a bit and see if that does the trick.
I have always used the safety wire method too and it has worked reasonably well. I've also heard of people jamming a tooth pick alongside the actuator to hold it up; then snapping off the toothpick. The tip of the tooth pick later passed through the system (supposedly). I'm not a fan of that method.
Thanks for another alternative.
Phil
On Sun, Mar 15, 2020 at 4:20 PM Tim Olson <Tim(at)myrv10.com (Tim(at)myrv10.com)> wrote:
Quote: | Hi all, this was sent to me by Dan Masys to be posted as he is having issues posting.
With about 1200 hrs and 13 years since new, my factory-new IO-540 D4A5 is beginning to show signs of not being so factory-new any more. In the past month or so, fuel pressures have been drifting down to as low as 10-12 psi on extended climbs to altitudes above 10,000 MSL and although the engine has never stumbled, I figured it would be prudent to swap out the engine driven pump before anything dramatic happened.
Turns out replacing the pump on the back of the accessory case is quite a bit trickier than it should be, given that it is just held on by a couple of specialized allen head capscrew/bolts. After several of thrashing and cussing, I figured I'd better Google the topic and see what the story is. I found the difficulty replacing the Lycoming pump has been experienced by lots of RV builders, and there is a fair amount of creative disinformation out there -- workarounds that RVers took to grind down or shorten bolts, weird installation techniques, etc. But I did find the correct method, and when using it, the installation was pretty much a breeze.
Since this is all fresh in my mind, I thought I would pay it forward with a little tutorial on the subject as it relates to the RV-10. Here goes:
The issues
1. This is a big deal. There is at least one NTSB report of a fatal RV-7 crash caused by incorrect replacement installation of the engine driven fuel pump.
2. There are more ways to do it wrong than to do it right. The instructions that came with the Tempest replacement pump I got from Spruce show you the incorrect positionings to avoid, and tell you that the pushrod that presses from above onto the pump's actuator arm has to be in full up position, but they don't tell you how to do either of those things.
3. Although the RV-10 has lots more space between the engine and the firewall than most RV's, for this procedure all kinds of things are going to be in your way: spark plug cable bundles, SCAT tubing for oil cooler, wiring to magnetos and/or electronic ignition.
4. The major gotcha is that the lever arm of the fuel pump has to be positioned under the end of the vertical pushrod that drives it before bolting anything in place, but the special bolts can't be inserted in the fuel pump flange if you do that first -- they hit the body of the pump and can't be lined up with the threaded holes in the case.
The solutions to the above issues
1. Start with the right set of tools. You will need a small ladder to get up and over the engine (probably the same one you use to change the oil filter.) You also need a set of stubby combination wrenches, a 5/16 allen wrench with a ball/swivel style head and about a 4 inch long shaft or so. A 5/16 inch standard length combination wrench can be used to turn the allen wrench from the side for tightening and loosening the special bolts.
2. Once you have removed the old pump with its hoses disconnected but fittings still attached, put it aside on a workbench.
3. Remove one spark plug from all six cylinders -- bottom plugs are easiest.
4. Key point: in order to determine whether the engine driven pushrod is in its maximum up position, you have to put your hand into the fuel pump mounting hole and *put your finger on the bottom of the pushrod.* Push it up as far as it will go. Then, while holding it up, rotate the prop with the other hand at least two full turns so you can determine where 'top dead center' is on the pushrod. When you are satisfied that you know where the full up position is, leave the prop in that position and don't move it again until the new pump is in. Now take your finger off the pushrod. You will notice it immediately slides back down to its lowest position (!!) even though the cam driving it is in its highest position. (This is why you can't use an inspection mirror to determine the position of the pushrod.)
Some RVers apparently have gone to great lengths to try to get the shaft to stay up so the pump arm can be inserted, but it turns out this is not necessary. Just let it fall to its lowest position.
5. On the bench, swap the B nut fittings from the old pump to the new one. I found that I had to leave off the overflow fitting during initial installation due to interference with spark plug wire bundles and oil cooler SCAT tubing.
6. Place the new gasket on the mounting flange of the new pump. You might need a little dab of fuel lube to hold it in place even though it is a dry gasket seal. Insert the two mounting bolts fully before starting the attach procedure (they won't fit later if not inserted now.)
7. Key point: While holding the pump with its actuator arm pointed into the engine case, engage the bolt holes for the two mounting bolts, but only advance the bolts *one turn* or at most two. This is the difference between success and failure. With the bolts engaged only one turn, you will be able to tilt the fuel pump actuator down so that it slips underneath that pesky pushrod which fell to its lowest position. If you tighten the bolts any more than that, the actuator arm will hit the side of the pushrod and you will not be able to seat the pump.
8. You will know you are successful if the pump flange slides forward easily on the bolts and mates to the mounting surface of the engine accessory case with no resistance whatsoever. Anything else is no bueno -- pull the pump out and start again. (The fatal RV crash occurred because the builder cranked the bolts down in spite of interference and bent the pushrod shaft.)
9. Once the pump flange sits flat against the engine, hold the pump in place with one hand and tighten the bolts on both sides with the 5/16 inch allen wrench with the other.
10. Safety wire the special bolts to each other. (Also a bit of an adventure, but this one is left as an exercise for the student. ).
11. Reconnect in inflow, outflow and overflow lines to the pump. Replace lower spark plugs (new gaskets, of course), and oil filter. Start engine and do a leak test and fuel pressure test.
Hope this helps if you should find yourself needing to replace the engine driven pump on your Lycoming. Remember, if you are having to force anything, the new pump is not in its correct position. Happy flying.
Dan Masys
RV-10 N104LD
Tech counselor, EAA chapter 1541
----------------------------------------------------
In addition to Dan's comments, I would add this: As Dan notes, the holes are oblong and it appears designed to tilt the pump as you install it under the pushrod. That said, what I have had good luck with is this: I have used fine safety wire, or you could use dental floss, to run a couple of twists around that push rod, and then pull the thread out and tie it to the engine case or engine mount snugly. That will hold the push rod up. If you follow Dan's guidance, it shouldn't be necessary to hold the rod up, but myself I would prefer to have as much gap there as possible to ensure the rod gets in proper position on top of the lever. Just make sure whatever you use is removed completely before you fully seat the pump.
Hopefully Dan's post comes in handy for some of you.
Tim
|
--
Phil Perry, EAA Lifetime #834284
President, EAA Chapter 59 - Waco, Texas
EAA—The Spirit of Aviation
|
| - The Matronics RV10-List Email Forum - | | Use the List Feature Navigator to browse the many List utilities available such as the Email Subscriptions page, Archive Search & Download, 7-Day Browse, Chat, FAQ, Photoshare, and much more:
http://www.matronics.com/Navigator?RV10-List |
|
_________________ Lenny Iszak
Palm City, FL
2014 RV-10, N311LZ - 500 hrs |
|
Back to top |
|
 |
Kelly McMullen
Joined: 16 Apr 2008 Posts: 1188 Location: Sun Lakes AZ
|
Posted: Sun Mar 15, 2020 2:10 pm Post subject: Engine driven fuel Pump replacement tips |
|
|
Good write up. One tool tip that will give more clearance is to beg,
borrow, buy or steal the correct size allen socket. Much easier to use than
an L shaped allen wrench. Thankfully my RV hasn't needed one yet, but I did
have to change one on my previous Mooney. That was lots of fun as well.
Kelly
Sent from my TRS-80 Model 100
On Sun, Mar 15, 2020 at 2:38 PM Phil Perry <philperry9(at)gmail.com> wrote:
[quote] That's a good technique. I replaced two of them and it never was easy.
Next time I will have to try and tilt the pump a bit and see if that does
the trick.
I have always used the safety wire method too and it has worked reasonably
well. I've also heard of people jamming a tooth pick alongside the
actuator to hold it up; then snapping off the toothpick. The tip of the
tooth pick later passed through the system (supposedly). I'm not a fan of
that method.
Thanks for another alternative.
Phil
On Sun, Mar 15, 2020 at 4:20 PM Tim Olson <Tim(at)myrv10.com> wrote:
> Hi all, this was sent to me by Dan Masys to be posted as he is having
> issues posting.
>
> With about 1200 hrs and 13 years since new, my factory-new IO-540 D4A5 is
> beginning to show signs of not being so factory-new any more. In the past
> month or so, fuel pressures have been drifting down to as low as 10-12 psi
> on extended climbs to altitudes above 10,000 MSL and although the engine
> has never stumbled, I figured it would be prudent to swap out the engine
> driven pump before anything dramatic happened.
>
> Turns out replacing the pump on the back of the accessory case is quite a
> bit trickier than it should be, given that it is just held on by a couple
> of specialized allen head capscrew/bolts. After several of thrashing and
> cussing, I figured I'd better Google the topic and see what the story is
| - The Matronics RV10-List Email Forum - | | Use the List Feature Navigator to browse the many List utilities available such as the Email Subscriptions page, Archive Search & Download, 7-Day Browse, Chat, FAQ, Photoshare, and much more:
http://www.matronics.com/Navigator?RV10-List |
|
_________________ Kelly McMullen
A&P/IA, EAA Tech Counselor
KCHD |
|
Back to top |
|
 |
lyleapgmc
Joined: 19 Feb 2014 Posts: 57
|
Posted: Sun Mar 15, 2020 2:35 pm Post subject: Engine driven fuel Pump replacement tips |
|
|
Chevrolet V8s have the same problem with the push rod. It will fall out if not held in some way. What I use is a bit of grease on the push rod. Other materials may seem more suitable in an airplane engine. What ever you're comfortable with.
On 3/15/2020 5:07 PM, Kelly McMullen wrote:
Quote: | Good write up. One tool tip that will give more clearance is to beg, borrow, buy or steal the correct size allen socket. Much easier to use than an L shaped allen wrench. Thankfully my RV hasn't needed one yet, but I did have to change one on my previous Mooney. That was lots of fun as well.
Kelly
Quote: | Sent from my TRS-80 Model 100 |
On Sun, Mar 15, 2020 at 2:38 PM Phil Perry <philperry9(at)gmail.com (philperry9(at)gmail.com)> wrote:
Quote: | That's a good technique.  I replaced two of them and it never was easy. Next time I will have to try and tilt the pump a bit and see if that does the trick.
I have always used the safety wire method too and it has worked reasonably well. I've also heard of people jamming a tooth pick alongside the actuator to hold it up; then snapping off the toothpick.  The tip of the tooth pick later passed through the system (supposedly). I'm not a fan of that method.
Thanks for another alternative.
Phil
On Sun, Mar 15, 2020 at 4:20 PM Tim Olson <Tim(at)myrv10.com (Tim(at)myrv10.com)> wrote:
Quote: | Hi all, this was sent to me by Dan Masys to be posted as he is having issues posting.
With about 1200 hrs and 13 years since new, my factory-new IO-540 D4A5 is beginning to show signs of not being so factory-new any more. In the past month or so, fuel pressures have been drifting down to as low as 10-12 psi on extended climbs to altitudes above 10,000 MSL and although the engine has never stumbled, I figured it would be prudent to swap out the engine driven pump before anything dramatic happened. Â
Turns out replacing the pump on the back of the accessory case is quite a bit trickier than it should be, given that it is just held on by a couple of specialized allen head capscrew/bolts. After several of thrashing and cussing, I figured I'd better Google the topic and see what the story is. I found the difficulty replacing the Lycoming pump has been experienced by lots of RV builders, and there is a fair amount of creative disinformation out there -- workarounds that RVers took to grind down or shorten bolts, weird installation techniques, etc. But I did find the correct method, and when using it, the installation was pretty much a breeze. Â
Since this is all fresh in my mind, I thought I would pay it forward with a little tutorial on the subject as it relates to the RV-10. Here goes:
The issues
1. This is a big deal. There is at least one NTSB report of a fatal RV-7 crash caused by incorrect replacement installation of the engine driven fuel pump.
2. There are more ways to do it wrong than to do it right. The instructions that came with the Tempest replacement pump I got from Spruce show you the incorrect positionings to avoid, and tell you that the pushrod that presses from above onto the pump's actuator arm has to be in full up position, but they don't tell you how to do either of those things. Â
3. Although the RV-10 has lots more space between the engine and the firewall than most RV's, for this procedure all kinds of things are going to be in your way: spark plug cable bundles, SCAT tubing for oil cooler, wiring to magnetos and/or electronic ignition. Â
4. The major gotcha is that the lever arm of the fuel pump has to be positioned under the end of the vertical pushrod that drives it before bolting anything in place, but the special bolts can't be inserted in the fuel pump flange if you do that first -- they hit the body of the pump and can't be lined up with the threaded holes in the case. Â
The solutions to the above issues
1. Start with the right set of tools. You will need a small ladder to get up and over the engine (probably the same one you use to change the oil filter.) You also need a set of stubby combination wrenches, a 5/16 allen wrench with a ball/swivel style head and about a 4 inch long shaft or so. A 5/16 inch standard length combination wrench can be used to turn the allen wrench from the side for tightening and loosening the special bolts.
2. Once you have removed the old pump with its hoses disconnected but fittings still attached, put it aside on a workbench.
3. Remove one spark plug from all six cylinders -- bottom plugs are easiest.Â
4. Key point: in order to determine whether the engine driven pushrod is in its maximum up position, you have to put your hand into the fuel pump mounting hole and *put your finger on the bottom of the pushrod.* Push it up as far as it will go. Then, while holding it up, rotate the prop with the other hand at least two full turns so you can determine where 'top dead center' is on the pushrod. When you are satisfied that you know where the full up position is, leave the prop in that position and don't move it again until the new pump is in. Now take your finger off the pushrod. You will notice it immediately slides back down to its lowest position (!!) even though the cam driving it is in its highest position. (This is why you can't use an inspection mirror to determine the position of the pushrod.)
Some RVers apparently have gone to great lengths to try to get the shaft to stay up so the pump arm can be inserted, but it turns out this is not necessary. Just let it fall to its lowest position.
5. On the bench, swap the B nut fittings from the old pump to the new one. I found that I had to leave off the overflow fitting during initial installation due to interference with spark plug wire bundles and oil cooler SCAT tubing.
6. Place the new gasket on the mounting flange of the new pump. You might need a little dab of fuel lube to hold it in place even though it is a dry gasket seal. Insert the two mounting bolts fully before starting the attach procedure (they won't fit later if not inserted now.)
7. Key point: While holding the pump with its actuator arm pointed into the engine case, engage the bolt holes for the two mounting bolts, but only advance the bolts *one turn* or at most two. This is the difference between success and failure. With the bolts engaged only one turn, you will be able to tilt the fuel pump actuator down so that it slips underneath that pesky pushrod which fell to its lowest position. If you tighten the bolts any more than that, the actuator arm will hit the side of the pushrod and you will not be able to seat the pump.
8. You will know you are successful if the pump flange slides forward easily on the bolts and mates to the mounting surface of the engine accessory case with no resistance whatsoever. Anything else is no bueno -- pull the pump out and start again. (The fatal RV crash occurred because the builder cranked the bolts down in spite of interference and bent the pushrod shaft.)
9. Once the pump flange sits flat against the engine, hold the pump in place with one hand and tighten the bolts on both sides with the 5/16 inch allen wrench with the other. Â
10. Safety wire the special bolts to each other. (Also a bit of an adventure, but this one is left as an exercise for the student. ).
11. Reconnect in inflow, outflow and overflow lines to the pump. Replace lower spark plugs (new gaskets, of course), and oil filter. Start engine and do a leak test and fuel pressure test.
Hope this helps if you should find yourself needing to replace the engine driven pump on your Lycoming. Remember, if you are having to force anything, the new pump is not in its correct position. Happy flying.
Dan Masys
RV-10 N104LD
Tech counselor, EAA chapter 1541
----------------------------------------------------
In addition to Dan's comments, I would add this: As Dan notes, the holes are oblong and it appears designed to tilt the pump as you install it under the pushrod. That said, what I have had good luck with is this: I have used fine safety wire, or you could use dental floss, to run a couple of twists around that push rod, and then pull the thread out and tie it to the engine case or engine mount snugly. That will hold the push rod up. If you follow Dan's guidance, it shouldn't be necessary to hold the rod up, but myself I would prefer to have as much gap there as possible to ensure the rod gets in proper position on top of the lever. Just make sure whatever you use is removed completely before you fully seat the pump.
Hopefully Dan's post comes in handy for some of you.
Tim
|
--
Phil Perry, EAA Lifetime #834284
President, EAA Chapter 59 - Waco, Texas
EAA—The Spirit of Aviation
|
|
| - The Matronics RV10-List Email Forum - | | Use the List Feature Navigator to browse the many List utilities available such as the Email Subscriptions page, Archive Search & Download, 7-Day Browse, Chat, FAQ, Photoshare, and much more:
http://www.matronics.com/Navigator?RV10-List |
|
|
|
Back to top |
|
 |
|
|
You cannot post new topics in this forum You cannot reply to topics in this forum You cannot edit your posts in this forum You cannot delete your posts in this forum You cannot vote in polls in this forum You cannot attach files in this forum You can download files in this forum
|
Powered by phpBB © 2001, 2005 phpBB Group
|