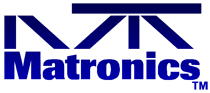 |
Matronics Email Lists Web Forum Interface to the Matronics Email Lists
|
View previous topic :: View next topic |
Author |
Message |
k7wx
Joined: 24 May 2010 Posts: 117
|
Posted: Tue Apr 28, 2020 6:37 am Post subject: Mag timing |
|
|
Gents,
I ordered two of Richard’s mag coils a while ago. Lovely workmanship and quality. Highly recommend.
After taking apart the mags to install the coils, my mechanic told me that for the timing, there is an easier way to connect the alligator clips from the E-50 buzz box that does not involve taking the rotor cap off.
Using an extra set of P-lead connectors (George Coy has these), it’s possible to make a simple adaptor using a 6-32 brass nut, a 2-inch 6-32 brass machine screw with the head cut off and some teflon spacers. Attached are some images. Here are the steps and some images.
1. Drill (7/64) and tap the metal center of the phenolic connector for a 6-32 thread.
2. Grind down a 6-32 brass nut so it’s a snug fit inside the the phenolic connector. This adds support for the machine screw.
3. Tin just the tip of a 2-inch 6-32 brass machine screw with the head cut off. Be careful not to damage the threads.
4. Add the brass nut. Assemble and advance the 6-32 brass screw down to the end of the metal tip.
6. Solder the tip of the brass screw in place.
7. Screw on the P-lead cap.
8. Place 1-2 mm of heat shrink tubing to the machine screw just above the brass nut.
9. Grind down some teflon washers so they fit securely inside the brass sleeve. Enough if these are needed so they extend several mm beyond the top of the brass sleeve.
10. A washer and nut secures everything tightly. The alligator clip attaches to the protruding machine screw.
Screwing one of these into the P-lead hole of each mag now allows you to check the timing without taking off the rotor cap. An adaptor like this should last forever.
Warren Hill
N464TW
Mesa, AZ
[img]cid:7A027A75-1FE8-417F-B451-C6ECAF6E351C(at)Home[/img] [img]cid:3B8B07A1-9B0B-43C9-BF6E-13C6520AFB71(at)Home[/img] [img]cid:67CF71CD-D04D-4176-A9F6-CBFF047CE85C(at)Home[/img] [img]cid:8815B25A-D846-4FAD-82BD-6F12E75AE576(at)Home[/img]
Quote: | On Apr 20, 2020, at 6:45 AM, Richard Goode <richard.goode(at)russianaeros.com (richard.goode(at)russianaeros.com)> wrote:
I hope that Matt will allow me a little bit of advertising!
We have known for a number of years that the original Russian coils are failing and indeed in Europe have had several forced landings as result of this. We consulted with a UK company who overhaul magnetos for historic racing cars who felt that the main problem was that the capacitor, an important part of the coil sits inside the coil of hotwire and over a period of time through a combination of age and heat will slowly degrade until it fails, and even if it is only in one magneto, the symptoms are a total, if momentary stoppage. Over a period of time this will get worse until the engine will stop for a significant period.
Working with this company we developed, some 30 months ago, a new coil with a high-technology Panasonic capacitor bonded to the outside of the coil, as well as improvements to the materials used. These have been very successful, but this small company could not produce sufficient coils for us. Then, UK CAA realise that we were selling coils, but without any paperwork – this being deliberate. Of course we do not have the freedoms that you lucky guys have in the USA, and they began grounding various perfectly airworthy aircraft belonging to our customers. And at the same time, they asked us (quite nicely) if we could make a formal application to certify the coils.
I had absolutely no idea of the amount of bureaucracy and testing that this would involve – but I suspect it would be the same if one wanted to get full certification for a new coil with the FAA! Before this, we had also decided to investigate a larger capacity manufacturing unit, and came to an agreement with AYC Ltd in China. They are one of the largest oil manufacturers in the world; making over 1 million a year, ranging from lawnmowers up to Ferrari cars. Although we represent incredibly small business in their terms, they were extremely enthusiastic about getting into the aviation business. We have found them superb partners; technically incredibly capable and very responsive. So it has been the AYC coils that went through this testing process for certification, and through the use of much better materials, these coils give a spark that is 15% to 20% stronger than a perfect Russian coil, and we now have them in full production.
Importantly we now have full certification from UK CAA and EASA who control all aviation in Europe, which must be an indication of quality!
Please contact us if you need any more information about these coils.
RICHARD GOODE AEROBATICS
Rhodds Farm, Lyonshall, Hereford, HR5 3LW, UK
Tel: +44 (0)1544 340120 Fax: +44 (0)1544 340129
e-mail: richard.goode(at)russianaeros.com (richard.goode(at)russianaeros.com)
www.russianaeros.com
WORLD LEADERS IN RUSSIAN SPORTING AIRCRAFT & ENGINES
In partnership with Aerometal Kft, Hungary.
|
| - The Matronics Yak-List Email Forum - | | Use the List Feature Navigator to browse the many List utilities available such as the Email Subscriptions page, Archive Search & Download, 7-Day Browse, Chat, FAQ, Photoshare, and much more:
http://www.matronics.com/Navigator?Yak-List |
|
Description: |
|
Filesize: |
170.29 KB |
Viewed: |
6964 Time(s) |
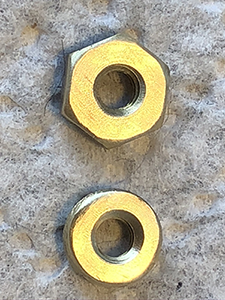
|
Description: |
|
Filesize: |
175.85 KB |
Viewed: |
6964 Time(s) |
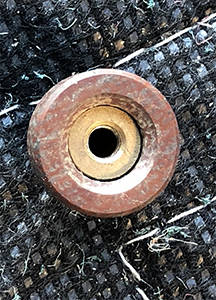
|
Description: |
|
Filesize: |
161.31 KB |
Viewed: |
6964 Time(s) |
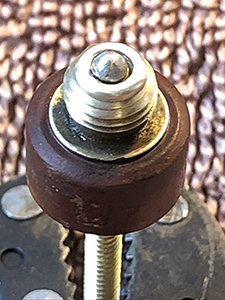
|
Description: |
|
Filesize: |
190.97 KB |
Viewed: |
6964 Time(s) |
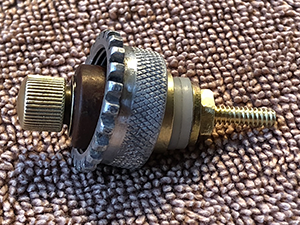
|
|
|
Back to top |
|
 |
dsavarese0812(at)bellsout Guest
|
Posted: Tue Apr 28, 2020 8:32 am Post subject: Mag timing |
|
|
That’s all well and good, except;One - you can not verify the point gap without removing the mag cap. And the point gap directly affects the timing. And you can not check the wear on the point foot either. The foot wear (mostly because the oil wick is dry or worn to the point where it is not rubbing on the point cam) will cause the point gap to change. Ultimately to the point where the mag goes dead because the points won’t open.
Secondly, without removing the mag cap you can not “fine tune” the mag timing which includes easily synchronizing the mags.
Third, and this is something many people ignore; unless you remove the mag cap you can not check the “E gap” which is aligning the rotor finger to the scribe mark on the mag cover surface precisely when the points open.
These are the steps required when you check the timing which I don’t believe you can do without removing the mag cover and distributor cap.
Dennis
Sent from my iPhone
Quote: | On Apr 28, 2020, at 10:40 AM, Warren Hill <k7wx(at)earthlink.net> wrote:
Gents,
I ordered two of Richard’s mag coils a while ago. Lovely workmanship and quality. Highly recommend.
After taking apart the mags to install the coils, my mechanic told me that for the timing, there is an easier way to connect the alligator clips from the E-50 buzz box that does not involve taking the rotor cap off.
Using an extra set of P-lead connectors (George Coy has these), it’s possible to make a simple adaptor using a 6-32 brass nut, a 2-inch 6-32 brass machine screw with the head cut off and some teflon spacers. Attached are some images. Here are the steps and some images.
1. Drill (7/64) and tap the metal center of the phenolic connector for a 6-32 thread.
2. Grind down a 6-32 brass nut so it’s a snug fit inside the the phenolic connector. This adds support for the machine screw.
3. Tin just the tip of a 2-inch 6-32 brass machine screw with the head cut off. Be careful not to damage the threads.
4. Add the brass nut. Assemble and advance the 6-32 brass screw down to the end of the metal tip.
6. Solder the tip of the brass screw in place.
7. Screw on the P-lead cap.
8. Place 1-2 mm of heat shrink tubing to the machine screw just above the brass nut.
9. Grind down some teflon washers so they fit securely inside the brass sleeve. Enough if these are needed so they extend several mm beyond the top of the brass sleeve.
10. A washer and nut secures everything tightly. The alligator clip attaches to the protruding machine screw.
Screwing one of these into the P-lead hole of each mag now allows you to check the timing without taking off the rotor cap. An adaptor like this should last forever.
Warren Hill
N464TW
Mesa, AZ
<nut.png>
<support.png>
<tip.png>
<Assembled.png>
Quote: | On Apr 20, 2020, at 6:45 AM, Richard Goode <richard.goode(at)russianaeros.com (richard.goode(at)russianaeros.com)> wrote:
I hope that Matt will allow me a little bit of advertising!
We have known for a number of years that the original Russian coils are failing and indeed in Europe have had several forced landings as result of this. We consulted with a UK company who overhaul magnetos for historic racing cars who felt that the main problem was that the capacitor, an important part of the coil sits inside the coil of hotwire and over a period of time through a combination of age and heat will slowly degrade until it fails, and even if it is only in one magneto, the symptoms are a total, if momentary stoppage. Over a period of time this will get worse until the engine will stop for a significant period.
Working with this company we developed, some 30 months ago, a new coil with a high-technology Panasonic capacitor bonded to the outside of the coil, as well as improvements to the materials used. These have been very successful, but this small company could not produce sufficient coils for us. Then, UK CAA realise that we were selling coils, but without any paperwork – this being deliberate. Of course we do not have the freedoms that you lucky guys have in the USA, and they began grounding various perfectly airworthy aircraft belonging to our customers. And at the same time, they asked us (quite nicely) if we could make a formal application to certify the coils.
I had absolutely no idea of the amount of bureaucracy and testing that this would involve – but I suspect it would be the same if one wanted to get full certification for a new coil with the FAA! Before this, we had also decided to investigate a larger capacity manufacturing unit, and came to an agreement with AYC Ltd in China. They are one of the largest oil manufacturers in the world; making over 1 million a year, ranging from lawnmowers up to Ferrari cars. Although we represent incredibly small business in their terms, they were extremely enthusiastic about getting into the aviation business. We have found them superb partners; technically incredibly capable and very responsive. So it has been the AYC coils that went through this testing process for certification, and through the use of much better materials, these coils give a spark that is 15% to 20% stronger than a perfect Russian coil, and we now have them in full production.
Importantly we now have full certification from UK CAA and EASA who control all aviation in Europe, which must be an indication of quality!
Please contact us if you need any more information about these coils.
RICHARD GOODE AEROBATICS
Rhodds Farm, Lyonshall, Hereford, HR5 3LW, UK
Tel: +44 (0)1544 340120 Fax: +44 (0)1544 340129
e-mail: richard.goode(at)russianaeros.com (richard.goode(at)russianaeros.com)
www.russianaeros.com
WORLD LEADERS IN RUSSIAN SPORTING AIRCRAFT & ENGINES
In partnership with Aerometal Kft, Hungary.
|
|
| - The Matronics Yak-List Email Forum - | | Use the List Feature Navigator to browse the many List utilities available such as the Email Subscriptions page, Archive Search & Download, 7-Day Browse, Chat, FAQ, Photoshare, and much more:
http://www.matronics.com/Navigator?Yak-List |
|
|
|
Back to top |
|
 |
hill(at)doctor-hill.com Guest
|
Posted: Tue Apr 28, 2020 11:53 am Post subject: Mag timing |
|
|
All good points Dennis.
Warren
Quote: | On Apr 28, 2020, at 9:29 AM, Anthony Savarese <dsavarese0812(at)bellsouth.net (dsavarese0812(at)bellsouth.net)> wrote:
That’s all well and good, except;One - you can not verify the point gap without removing the mag cap. And the point gap directly affects the timing. And you can not check the wear on the point foot either. The foot wear (mostly because the oil wick is dry or worn to the point where it is not rubbing on the point cam) will cause the point gap to change. Ultimately to the point where the mag goes dead because the points won’t open.
Secondly, without removing the mag cap you can not “fine tune” the mag timing which includes easily synchronizing the mags.
Third, and this is something many people ignore; unless you remove the mag cap you can not check the “E gap” which is aligning the rotor finger to the scribe mark on the mag cover surface precisely when the points open.
These are the steps required when you check the timing which I don’t believe you can do without removing the mag cover and distributor cap.
DennisSent from my iPhone
Quote: | On Apr 28, 2020, at 10:40 AM, Warren Hill <k7wx(at)earthlink.net (k7wx(at)earthlink.net)> wrote:Gents,
I ordered two of Richard’s mag coils a while ago. Lovely workmanship and quality. Highly recommend.
After taking apart the mags to install the coils, my mechanic told me that for the timing, there is an easier way to connect the alligator clips from the E-50 buzz box that does not involve taking the rotor cap off.
Using an extra set of P-lead connectors (George Coy has these), it’s possible to make a simple adaptor using a 6-32 brass nut, a 2-inch 6-32 brass machine screw with the head cut off and some teflon spacers. Attached are some images. Here are the steps and some images.
1. Drill (7/64) and tap the metal center of the phenolic connector for a 6-32 thread.
2. Grind down a 6-32 brass nut so it’s a snug fit inside the the phenolic connector. This adds support for the machine screw.
3. Tin just the tip of a 2-inch 6-32 brass machine screw with the head cut off. Be careful not to damage the threads.
4. Add the brass nut. Assemble and advance the 6-32 brass screw down to the end of the metal tip.
6. Solder the tip of the brass screw in place.
7. Screw on the P-lead cap.
8. Place 1-2 mm of heat shrink tubing to the machine screw just above the brass nut.
9. Grind down some teflon washers so they fit securely inside the brass sleeve. Enough if these are needed so they extend several mm beyond the top of the brass sleeve.
10. A washer and nut secures everything tightly. The alligator clip attaches to the protruding machine screw.
Screwing one of these into the P-lead hole of each mag now allows you to check the timing without taking off the rotor cap. An adaptor like this should last forever.
Warren Hill
N464TW
Mesa, AZ
<nut.png>
<support.png>
<tip.png>
<Assembled.png>
Quote: | On Apr 20, 2020, at 6:45 AM, Richard Goode <richard.goode(at)russianaeros.com (richard.goode(at)russianaeros.com)> wrote:
I hope that Matt will allow me a little bit of advertising!
We have known for a number of years that the original Russian coils are failing and indeed in Europe have had several forced landings as result of this. We consulted with a UK company who overhaul magnetos for historic racing cars who felt that the main problem was that the capacitor, an important part of the coil sits inside the coil of hotwire and over a period of time through a combination of age and heat will slowly degrade until it fails, and even if it is only in one magneto, the symptoms are a total, if momentary stoppage. Over a period of time this will get worse until the engine will stop for a significant period.
Working with this company we developed, some 30 months ago, a new coil with a high-technology Panasonic capacitor bonded to the outside of the coil, as well as improvements to the materials used. These have been very successful, but this small company could not produce sufficient coils for us. Then, UK CAA realise that we were selling coils, but without any paperwork – this being deliberate. Of course we do not have the freedoms that you lucky guys have in the USA, and they began grounding various perfectly airworthy aircraft belonging to our customers. And at the same time, they asked us (quite nicely) if we could make a formal application to certify the coils.
I had absolutely no idea of the amount of bureaucracy and testing that this would involve – but I suspect it would be the same if one wanted to get full certification for a new coil with the FAA! Before this, we had also decided to investigate a larger capacity manufacturing unit, and came to an agreement with AYC Ltd in China. They are one of the largest oil manufacturers in the world; making over 1 million a year, ranging from lawnmowers up to Ferrari cars. Although we represent incredibly small business in their terms, they were extremely enthusiastic about getting into the aviation business. We have found them superb partners; technically incredibly capable and very responsive. So it has been the AYC coils that went through this testing process for certification, and through the use of much better materials, these coils give a spark that is 15% to 20% stronger than a perfect Russian coil, and we now have them in full production.
Importantly we now have full certification from UK CAA and EASA who control all aviation in Europe, which must be an indication of quality!
Please contact us if you need any more information about these coils.
RICHARD GOODE AEROBATICS
Rhodds Farm, Lyonshall, Hereford, HR5 3LW, UK
Tel: +44 (0)1544 340120 Fax: +44 (0)1544 340129
e-mail: richard.goode(at)russianaeros.com (richard.goode(at)russianaeros.com)
www.russianaeros.com
WORLD LEADERS IN RUSSIAN SPORTING AIRCRAFT & ENGINES
In partnership with Aerometal Kft, Hungary.
|
|
|
| - The Matronics Yak-List Email Forum - | | Use the List Feature Navigator to browse the many List utilities available such as the Email Subscriptions page, Archive Search & Download, 7-Day Browse, Chat, FAQ, Photoshare, and much more:
http://www.matronics.com/Navigator?Yak-List |
|
|
|
Back to top |
|
 |
pennington.construction.i Guest
|
Posted: Tue Apr 28, 2020 3:18 pm Post subject: Mag timing |
|
|
Hey guys.
All of you guys need to screen shot the info below and put that in your technical data folder for condition inspections. It doesn’t get any clearer than that.
If Dennis was one of the X-Men. He would be Mr Magneto.
Mark Pennington
N621CJ
On Tue, Apr 28, 2020 at 12:37 PM Anthony Savarese <dsavarese0812(at)bellsouth.net (dsavarese0812(at)bellsouth.net)> wrote:
Quote: | That’s all well and good, except;One - you can not verify the point gap without removing the mag cap. And the point gap directly affects the timing. And you can not check the wear on the point foot either. The foot wear (mostly because the oil wick is dry or worn to the point where it is not rubbing on the point cam) will cause the point gap to change. Ultimately to the point where the mag goes dead because the points won’t open.
Secondly, without removing the mag cap you can not “fine tune” the mag timing which includes easily synchronizing the mags.
Third, and this is something many people ignore; unless you remove the mag cap you can not check the “E gap” which is aligning the rotor finger to the scribe mark on the mag cover surface precisely when the points open.
These are the steps required when you check the timing which I don’t believe you can do without removing the mag cover and distributor cap.
Dennis
Sent from my iPhone
Quote: | On Apr 28, 2020, at 10:40 AM, Warren Hill <k7wx(at)earthlink.net (k7wx(at)earthlink.net)> wrote:
Gents,
I ordered two of Richard’s mag coils a while ago. Lovely workmanship and quality. Highly recommend.
After taking apart the mags to install the coils, my mechanic told me that for the timing, there is an easier way to connect the alligator clips from the E-50 buzz box that does not involve taking the rotor cap off.
Using an extra set of P-lead connectors (George Coy has these), it’s possible to make a simple adaptor using a 6-32 brass nut, a 2-inch 6-32 brass machine screw with the head cut off and some teflon spacers. Attached are some images. Here are the steps and some images.
1. Drill (7/64) and tap the metal center of the phenolic connector for a 6-32 thread.
2. Grind down a 6-32 brass nut so it’s a snug fit inside the the phenolic connector. This adds support for the machine screw.
3. Tin just the tip of a 2-inch 6-32 brass machine screw with the head cut off. Be careful not to damage the threads.
4. Add the brass nut. Assemble and advance the 6-32 brass screw down to the end of the metal tip.
6. Solder the tip of the brass screw in place.
7. Screw on the P-lead cap.
8. Place 1-2 mm of heat shrink tubing to the machine screw just above the brass nut.
9. Grind down some teflon washers so they fit securely inside the brass sleeve. Enough if these are needed so they extend several mm beyond the top of the brass sleeve.
10. A washer and nut secures everything tightly. The alligator clip attaches to the protruding machine screw.
Screwing one of these into the P-lead hole of each mag now allows you to check the timing without taking off the rotor cap. An adaptor like this should last forever.
Warren Hill
N464TW
Mesa, AZ
<nut.png>
<support.png>
<tip.png>
<Assembled.png>
Quote: | On Apr 20, 2020, at 6:45 AM, Richard Goode <richard.goode(at)russianaeros.com (richard.goode(at)russianaeros.com)> wrote:
I hope that Matt will allow me a little bit of advertising!
We have known for a number of years that the original Russian coils are failing and indeed in Europe have had several forced landings as result of this. We consulted with a UK company who overhaul magnetos for historic racing cars who felt that the main problem was that the capacitor, an important part of the coil sits inside the coil of hotwire and over a period of time through a combination of age and heat will slowly degrade until it fails, and even if it is only in one magneto, the symptoms are a total, if momentary stoppage. Over a period of time this will get worse until the engine will stop for a significant period.
Working with this company we developed, some 30 months ago, a new coil with a high-technology Panasonic capacitor bonded to the outside of the coil, as well as improvements to the materials used. These have been very successful, but this small company could not produce sufficient coils for us. Then, UK CAA realise that we were selling coils, but without any paperwork – this being deliberate. Of course we do not have the freedoms that you lucky guys have in the USA, and they began grounding various perfectly airworthy aircraft belonging to our customers. And at the same time, they asked us (quite nicely) if we could make a formal application to certify the coils.
I had absolutely no idea of the amount of bureaucracy and testing that this would involve – but I suspect it would be the same if one wanted to get full certification for a new coil with the FAA! Before this, we had also decided to investigate a larger capacity manufacturing unit, and came to an agreement with AYC Ltd in China. They are one of the largest oil manufacturers in the world; making over 1 million a year, ranging from lawnmowers up to Ferrari cars. Although we represent incredibly small business in their terms, they were extremely enthusiastic about getting into the aviation business. We have found them superb partners; technically incredibly capable and very responsive. So it has been the AYC coils that went through this testing process for certification, and through the use of much better materials, these coils give a spark that is 15% to 20% stronger than a perfect Russian coil, and we now have them in full production.
Importantly we now have full certification from UK CAA and EASA who control all aviation in Europe, which must be an indication of quality!
Please contact us if you need any more information about these coils.
RICHARD GOODE AEROBATICS
Rhodds Farm, Lyonshall, Hereford, HR5 3LW, UK
Tel: +44 (0)1544 340120 Fax: +44 (0)1544 340129
e-mail: richard.goode(at)russianaeros.com (richard.goode(at)russianaeros.com)
www.russianaeros.com
WORLD LEADERS IN RUSSIAN SPORTING AIRCRAFT & ENGINES
In partnership with Aerometal Kft, Hungary.
|
|
|
| - The Matronics Yak-List Email Forum - | | Use the List Feature Navigator to browse the many List utilities available such as the Email Subscriptions page, Archive Search & Download, 7-Day Browse, Chat, FAQ, Photoshare, and much more:
http://www.matronics.com/Navigator?Yak-List |
|
|
|
Back to top |
|
 |
dsavarese0812(at)bellsout Guest
|
Posted: Tue Apr 28, 2020 3:45 pm Post subject: Mag timing |
|
|
You are too kind Mark.
Dennis
A. Dennis Savarese
334-546-8182 (mobile)
www.yak-52.com
Skype - Yakguy1
On 4/28/2020 7:04 PM, Mark Pennington wrote:
Quote: | Hey guys.
All of you guys need to screen shot the info below and put that in
your technical data folder for condition inspections. It doesn’t get
any clearer than that.
If Dennis was one of the X-Men. He would be Mr Magneto.
Mark Pennington
N621CJ
On Tue, Apr 28, 2020 at 12:37 PM Anthony Savarese
<dsavarese0812(at)bellsouth.net <mailto:dsavarese0812(at)bellsouth.net>> wrote:
That’s all well and good, except;
One - you can not verify the point gap without removing the mag
cap. And the point gap directly affects the timing. And you can
not check the wear on the point foot either. The foot wear (mostly
because the oil wick is dry or worn to the point where it is not
rubbing on the point cam) will cause the point gap to change.
Ultimately to the point where the mag goes dead because the points
won’t open.
Secondly, without removing the mag cap you can not “fine tune” the
mag timing which includes easily synchronizing the mags.
Third, and this is something many people ignore; unless you remove
the mag cap you can not check the “E gap” which is aligning the
rotor finger to the scribe mark on the mag cover surface precisely
when the points open.
These are the steps required when you check the timing which I
don’t believe you can do without removing the mag cover and
distributor cap.
Dennis
Sent from my iPhone
> On Apr 28, 2020, at 10:40 AM, Warren Hill <k7wx(at)earthlink.net
> <mailto:k7wx(at)earthlink.net>> wrote:
>
>
> Gents,
>
> I ordered two of Richard’s mag coils a while ago. Lovely
> workmanship and quality. Highly recommend.
>
> After taking apart the mags to install the coils, my mechanic
> told me that for the timing, there is an easier way to connect
> the alligator clips from the E-50 buzz box that does not involve
> taking the rotor cap off.
>
> Using an extra set of P-lead connectors (George Coy has these),
> it’s possible to make a simple adaptor using a 6-32 brass nut, a
> 2-inch 6-32 brass machine screw with the head cut off and some
> teflon spacers. Attached are some images. Here are the steps and
> some images.
>
> 1. Drill (7/64) and tap the metal center of the phenolic
> connector for a 6-32 thread.
> 2. Grind down a 6-32 brass nut so it’s a snug fit inside the
> the phenolic connector. This adds support for the machine screw.
> 3. Tin just the tip of a 2-inch 6-32 brass machine screw with
> the head cut off. Be careful not to damage the threads.
> 4. Add the brass nut. Assemble and advance the 6-32 brass
> screw down to the end of the metal tip.
> 6. Solder the tip of the brass screw in place.
> 7. Screw on the P-lead cap.
> 8. Place 1-2 mm of heat shrink tubing to the machine screw
> just above the brass nut.
> 9. Grind down some teflon washers so they fit securely inside
> the brass sleeve. Enough if these are needed so they extend
> several mm beyond the top of the brass sleeve.
> 10. A washer and nut secures everything tightly. The alligator
> clip attaches to the protruding machine screw.
>
> Screwing one of these into the P-lead hole of each mag now allows
> you to check the timing without taking off the rotor cap. An
> adaptor like this should last forever.
>
> Warren Hill
> N464TW
> Mesa, AZ
>
> <nut.png>
> <support.png>
> <tip.png>
> <Assembled.png>
>
>> On Apr 20, 2020, at 6:45 AM, Richard Goode
>> <richard.goode(at)russianaeros.com
>> <mailto:richard.goode(at)russianaeros.com>> wrote:
>>
>> I hope that Matt will allow me a little bit of advertising!
>> We have known for a number of years that the original Russian
>> coils are failing and indeed in Europe have had several forced
>> landings as result of this. We consulted with a UK company who
>> overhaul magnetos for historic racing cars who felt that the
>> main problem was that the capacitor, an important part of the
>> coil sits inside the coil of hotwire and over a period of time
>> through a combination of age and heat will slowly degrade until
>> it fails, and even if it is only in one magneto, the symptoms
>> are a total, if momentary stoppage. Over a period of time this
>> will get worse until the engine will stop for a significant period.
>> Working with this company we developed, some 30 months ago, a
>> new coil with a high-technology Panasonic capacitor bonded to
>> the outside of the coil, as well as improvements to the
>> materials used. These have been very successful, but this small
>> company could not produce sufficient coils for us. Then, UK CAA
>> realise that we were selling coils, but without any paperwork –
>> this being deliberate. Of course we do not have the freedoms
>> that you lucky guys have in the USA, and they began grounding
>> various perfectly airworthy aircraft belonging to our customers.
>> And at the same time, they asked us (quite nicely) if we could
>> make a formal application to certify the coils.
>> I had absolutely no idea of the amount of bureaucracy and
>> testing that this would involve – but I suspect it would be the
>> same if one wanted to get full certification for a new coil with
>> the FAA! Before this, we had also decided to investigate a
>> larger capacity manufacturing unit, and came to an agreement
>> with AYC Ltd in China. They are one of the largest oil
>> manufacturers in the world; making over 1 million a year,
>> ranging from lawnmowers up to Ferrari cars. Although we
>> represent incredibly small business in their terms, they were
>> extremely enthusiastic about getting into the aviation business.
>> We have found them superb partners; technically incredibly
>> capable and very responsive. So it has been the AYC coils that
>> went through this testing process for certification, and through
>> the use of much better materials, these coils give a spark that
>> is 15% to 20% stronger than a perfect Russian coil, and we now
>> have them in full production.
>> Importantly we now have full certification from UK CAA and EASA
>> who control all aviation in Europe, which must be an indication
>> of quality!
>> Please contact us if you need any more information about these
>> coils.
>> *RICHARD GOODE AEROBATICS***
>> *Rhodds Farm, Lyonshall, Hereford, HR5 3LW, UK*
>> Tel: +44 (0)1544 340120 Fax: +44 (0)1544 340129
>> e-mail:richard.goode(at)russianaeros.com
>> <mailto:richard.goode(at)russianaeros.com>
>> www.russianaeros.com <http://www.russianaeros.com/>
>> *W**ORLD LEADERS IN RUSSIAN SPORTING AIRCRAFT & ENGINES***
>> *In partnership with Aerometal Kft, Hungary.*
>
|
| - The Matronics Yak-List Email Forum - | | Use the List Feature Navigator to browse the many List utilities available such as the Email Subscriptions page, Archive Search & Download, 7-Day Browse, Chat, FAQ, Photoshare, and much more:
http://www.matronics.com/Navigator?Yak-List |
|
|
|
Back to top |
|
 |
dsavarese0812(at)bellsout Guest
|
Posted: Tue Apr 28, 2020 3:45 pm Post subject: Mag timing |
|
|
Thank you Walt.
Dennis
A. Dennis Savarese
334-546-8182 (mobile)
www.yak-52.com
Skype - Yakguy1
On 4/28/2020 1:25 PM, Walter Lannon wrote:
Quote: | Well said Dennis!
Shortcuts in this business can be a direct line to serious consequences.
Walt
*From:* Anthony Savarese <mailto:dsavarese0812(at)bellsouth.net> u*Sent:*
Tuesday, April 28, 2020 9:29 AM
*To:* yak-list(at)matronics.com <mailto:yak-list(at)matronics.com>
*Subject:* Re: Mag timing
That’s all well and good, except;
One - you can not verify the point gap without removing the mag cap.
And the point gap directly affects the timing. And you can not check
the wear on the point foot either. The foot wear (mostly because the
oil wick is dry or worn to the point where it is not rubbing on the
point cam) will cause the point gap to change. Ultimately to the point
where the mag goes dead because the points won’t open.
Secondly, without removing the mag cap you can not “fine tune” the mag
timing which includes easily synchronizing the mags.
Third, and this is something many people ignore; unless you remove the
mag cap you can not check the “E gap” which is aligning the rotor
finger to the scribe mark on the mag cover surface precisely when the
points open.
These are the steps required when you check the timing which I don’t
believe you can do without removing the mag cover and distributor cap.
Dennis
Sent from my iPhone
> On Apr 28, 2020, at 10:40 AM, Warren Hill <k7wx(at)earthlink.net> wrote:
>
>
> Gents,
> I ordered two of Richard’s mag coils a while ago. Lovely workmanship
> and quality. Highly recommend.
> After taking apart the mags to install the coils, my mechanic told me
> that for the timing, there is an easier way to connect the alligator
> clips from the E-50 buzz box that does not involve taking the rotor
> cap off.
> Using an extra set of P-lead connectors (George Coy has these), it’s
> possible to make a simple adaptor using a 6-32 brass nut, a 2-inch
> 6-32 brass machine screw with the head cut off and some teflon
> spacers. Attached are some images. Here are the steps and some images.
> 1. Drill (7/64) and tap the metal center of the phenolic connector
> for a 6-32 thread.
> 2. Grind down a 6-32 brass nut so it’s a snug fit inside the the
> phenolic connector. This adds support for the machine screw.
> 3. Tin just the tip of a 2-inch 6-32 brass machine screw with the
> head cut off. Be careful not to damage the threads.
> 4. Add the brass nut. Assemble and advance the 6-32 brass screw
> down to the end of the metal tip.
> 6. Solder the tip of the brass screw in place.
> 7. Screw on the P-lead cap.
> 8. Place 1-2 mm of heat shrink tubing to the machine screw just
> above the brass nut.
> 9. Grind down some teflon washers so they fit securely inside the
> brass sleeve. Enough if these are needed so they extend several mm
> beyond the top of the brass sleeve.
> 10. A washer and nut secures everything tightly. The alligator
> clip attaches to the protruding machine screw.
> Screwing one of these into the P-lead hole of each mag now allows you
> to check the timing without taking off the rotor cap. An adaptor like
> this should last forever.
> Warren Hill
> N464TW
> Mesa, AZ
> <nut.png>
> <support.png>
> <tip.png>
> <Assembled.png>
>
>> On Apr 20, 2020, at 6:45 AM, Richard Goode
>> <richard.goode(at)russianaeros.com
>> <mailto:richard.goode(at)russianaeros.com>> wrote:
>> I hope that Matt will allow me a little bit of advertising!
>> We have known for a number of years that the original Russian coils
>> are failing and indeed in Europe have had several forced landings as
>> result of this. We consulted with a UK company who overhaul magnetos
>> for historic racing cars who felt that the main problem was that the
>> capacitor, an important part of the coil sits inside the coil of
>> hotwire and over a period of time through a combination of age and
>> heat will slowly degrade until it fails, and even if it is only in
>> one magneto, the symptoms are a total, if momentary stoppage. Over a
>> period of time this will get worse until the engine will stop for a
>> significant period.
>> Working with this company we developed, some 30 months ago, a new
>> coil with a high-technology Panasonic capacitor bonded to the
>> outside of the coil, as well as improvements to the materials used.
>> These have been very successful, but this small company could not
>> produce sufficient coils for us. Then, UK CAA realise that we were
>> selling coils, but without any paperwork – this being deliberate. Of
>> course we do not have the freedoms that you lucky guys have in the
>> USA, and they began grounding various perfectly airworthy aircraft
>> belonging to our customers. And at the same time, they asked us
>> (quite nicely) if we could make a formal application to certify the
>> coils.
>> I had absolutely no idea of the amount of bureaucracy and testing
>> that this would involve – but I suspect it would be the same if one
>> wanted to get full certification for a new coil with the FAA! Before
>> this, we had also decided to investigate a larger capacity
>> manufacturing unit, and came to an agreement with AYC Ltd in China.
>> They are one of the largest oil manufacturers in the world; making
>> over 1 million a year, ranging from lawnmowers up to Ferrari cars.
>> Although we represent incredibly small business in their terms, they
>> were extremely enthusiastic about getting into the aviation
>> business. We have found them superb partners; technically incredibly
>> capable and very responsive. So it has been the AYC coils that went
>> through this testing process for certification, and through the use
>> of much better materials, these coils give a spark that is 15% to
>> 20% stronger than a perfect Russian coil, and we now have them in
>> full production.
>> Importantly we now have full certification from UK CAA and EASA who
>> control all aviation in Europe, which must be an indication of quality!
>> Please contact us if you need any more information about these coils.
>> *RICHARD GOODE AEROBATICS***
>> *Rhodds Farm, Lyonshall, Hereford, HR5 3LW, UK*
>> Tel: +44 (0)1544 340120 Fax: +44 (0)1544 340129
>> e-mail:richard.goode(at)russianaeros.com
>> <mailto:richard.goode(at)russianaeros.com>
>> www.russianaeros.com <http://www.russianaeros.com/>
>> *W**ORLD LEADERS IN RUSSIAN SPORTING AIRCRAFT & ENGINES***
>> *In partnership with Aerometal Kft, Hungary.*
------------------------------------------------------------------------
Avast logo <https://www.avast.com/antivirus>
This email has been checked for viruses by Avast antivirus software.
www.avast.com <https://www.avast.com/antivirus>
<#DAB4FAD8-2DD7-40BB-A1B8-4E2AA1F9FDF2>
|
| - The Matronics Yak-List Email Forum - | | Use the List Feature Navigator to browse the many List utilities available such as the Email Subscriptions page, Archive Search & Download, 7-Day Browse, Chat, FAQ, Photoshare, and much more:
http://www.matronics.com/Navigator?Yak-List |
|
|
|
Back to top |
|
 |
stephen.hayne
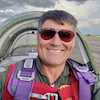
Joined: 01 Nov 2013 Posts: 59 Location: United States
|
Posted: Mon Jun 08, 2020 7:36 pm Post subject: Re: Mag timing |
|
|
pennington.construction.i wrote: |
All of you guys need to screen shot the info below and put that in your technical data folder for condition inspections. It doesn’t get any clearer than that.
If Dennis was one of the X-Men. He would be Mr Magneto.
Mark Pennington
N621CJ
|
This is so funny and right - I had just selected that text and printed it to put in my "important stuff" folder... !!
Thank you Dennis - appreciate your wisdom.
| - The Matronics Yak-List Email Forum - | | Use the List Feature Navigator to browse the many List utilities available such as the Email Subscriptions page, Archive Search & Download, 7-Day Browse, Chat, FAQ, Photoshare, and much more:
http://www.matronics.com/Navigator?Yak-List |
|
_________________ -
Stephen Hayne, Cyber Security Consultant, Professor Emeritus (retired)
443LM Nanchang CJA
http://selfsynchronize.com/hayne/plane/cj6.asp |
|
Back to top |
|
 |
|
|
You cannot post new topics in this forum You cannot reply to topics in this forum You cannot edit your posts in this forum You cannot delete your posts in this forum You cannot vote in polls in this forum You cannot attach files in this forum You can download files in this forum
|
Powered by phpBB © 2001, 2005 phpBB Group
|