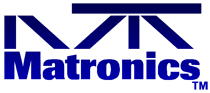 |
Matronics Email Lists Web Forum Interface to the Matronics Email Lists
|
View previous topic :: View next topic |
Author |
Message |
jindoguy(at)gmail.com Guest
|
Posted: Fri Dec 01, 2006 6:51 am Post subject: Cables, pulleys and nico press swages |
|
|
All snowed in and no where to go here on the Great Grass Desert.
First, a single nico sleeve of the proper size and properly swaged is as strong as the cable it is installed on. A second nico actually decreases the cables strength. If you leave cable sticking out of the second one, then it has no purpose whatsoever. Its only function is to keep you from getting those nasty little holes in your finger.
Those who have mentioned finding broken strands don't say what type of cable they have. 7 X 7? 7 X 19? 1 X 19? Each type of construction has its own place. Since pulleys are mentioned, it probably isn't 1 X 19. This is what throttle and choke cables are made from because it's pretty stiff and will take a bit of a compression load when the cable is pushed instead of pulled. 7 X 19 on the other hand is very soft, relatively speaking, and will work better when a small pulley must be used. Generally speaking 7 X 7 construction is probably what most of us have. Incidentally, the numbers refer to the number of wires in each bundle and the number of bundles in the cable. 1 X 19 has 1 wire in each bundle and 19 bundles in the cable. 7 X 19 has 7 wires per bundle and 19 bundles per cable.
What material? Common aircraft cable is just carbon steel, hence the oil to protect it from corrosion. Stainless Steel is dry, usually, and if you get it from a boat shop, like West Marine, is usually pre stretched. Whenever possible I try to use pre stretched SS 7 X 7 rather than carbon steel because the lubricant attracts dirt and gets all over everything it touches.
Pulleys are sized by the cable and degree of bend the cable must make. Too small a pulley increases the internal strain on the individual wire in the cable, and eventually these little wires give up. All of this can be found in FAA publication AC 43.13 1b and 2a, "Acceptable Methods, Techniques, and Practices - Aircraft Inspection and Repair", about $20 from ASA and available from shops like Sporty's. It's also available on line at FAA.gov. Go to Advisory Circulars (AC's).
Cable strengths are deceiving, the numbers sound high but don't take into account dynamic loads. In the early days of hang gliding at least one manufacturer used 1/8" 7 X 7 with swaged on terminals as a hang strap for the pilot. They looked at the stregth of the cable and thought 9G load, perfect. What they didn't count on was the dynamic loads produced, in this case, when the aircraft was transitioning the shear at the boundary of a thermal. The pilot would go weightless and put slack in the cable, when he fell back the cable snapped. Those who had backup hang straps of tubular nylon strap lived to tell the tale, others didn't. My point here is don't look at breaking strength, look at safe working load and use that number instead.
Rick
--
Rick Girard
"Ya'll drop on in"
takes on a whole new meaning
when you live at the airport. [quote][b]
| - The Matronics Kolb-List Email Forum - | | Use the List Feature Navigator to browse the many List utilities available such as the Email Subscriptions page, Archive Search & Download, 7-Day Browse, Chat, FAQ, Photoshare, and much more:
http://www.matronics.com/Navigator?Kolb-List |
|
|
|
Back to top |
|
 |
Jim Baker
Joined: 30 Mar 2006 Posts: 181 Location: Sayre, PA
|
Posted: Fri Dec 01, 2006 10:40 am Post subject: Cables, pulleys and nico press swages |
|
|
Rick has some good points.....
Quote: | A second nico actually decreases the cables strength.
|
Any supporting data? Testing?
If you leave cable sticking out
Quote: | of the second one, then it has no purpose whatsoever. Its only function is to keep you from
getting those nasty little holes in your finger.
|
Perhaps on the second but necessary on the first Nicopress
sleeve if that is the only one used. The sleeve elongates from
the press and having the end stick out ensures full coverage. I
suspect the second sleeve was to cover those who don't know
about proper procedures or didn't take the time to measure the
final swaged product for conformity.
Quote: | Stainless Steel is dry, usually, and if you get it from a boat shop, like West Marine, is
usually pre stretched.
|
Just for clarity.....
Elastic stretch is the result of the inherent elasticity, or
recoverable deformation, of the metal itself. Since the elastic
properties of a given cable can be determined, elongation due to
elastic stretch is predictable. This is not the pre-stretch
mentioned.
Constructional stretch occurs when cable is loaded for the first
time. When a cable is first loaded, the helically-wound wires
and strands are pulled more tightly together, compressing the
core and bringing all of the cable elements into closer contact.
This results in a slight reduction in diameter and a corresponding
increase in length. Some types of high strength cable, such as
prestressing strand,are commercially available with
constructional stretch removed by preloading at the factory.
Such cable will conform to the requirements for ASTM
Designation A586 (structural strand) or ASTM Designation A603
(structural rope), and will be clearly identified as prestretched
cable.
Unless I saw the ASTM designation for the cable involved, I'd
consider the seller's statement of pre-stretch as marketing hype.
Does pre-stretch make a difference in UL applications? Do the
math and see if you have any concerns....
Delta CS = (applied load / (.65 x Cable strength)) x (CS%) x (L)
CS in feet, CS% as given by the mfg, L in feet, and applied load
and cable strength in pounds.
Jim Baker
580.788.2779
Elmore City, OK
| - The Matronics Kolb-List Email Forum - | | Use the List Feature Navigator to browse the many List utilities available such as the Email Subscriptions page, Archive Search & Download, 7-Day Browse, Chat, FAQ, Photoshare, and much more:
http://www.matronics.com/Navigator?Kolb-List |
|
|
|
Back to top |
|
 |
John Hauck
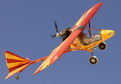
Joined: 09 Jan 2006 Posts: 4639 Location: Titus, Alabama (hauck's holler)
|
Posted: Fri Dec 01, 2006 11:23 am Post subject: Cables, pulleys and nico press swages |
|
|
----- | If you leave cable sticking out
| > of the second one, then it has no purpose whatsoever. Its only
function is to keep you from
| > getting those nasty little holes in your finger.
Folks:
We went through this cable thing several years ago, especially leaving
a short piece of the cable tail extended past the sleeve.
If I understand correctly, keeping the tail inside the second sleeve
is like putting the cable in a shear. Most folks would cut the cable
end square. Then put this under tremendous load from the compression
tool on the sleeve against the other cable. What we have is a 90
degree shearing force from the tucked end on the opposite cable. I am
willing to take the nicks from the cable ends over the possibility of
weakening the splice with a tucked end. Through the years I have seen
several ultralight manufacturers tuck the ends of cables. Most
notably, Eipper. When questioned about this practice I got the
standard answer of, "that's the way we do it."
Some where I have read about using second sleeve for 3/32 and smaller
cable. Might have been Tony Bingelis' Book, or one of his books.
Have to get them out, dust them off, and do some refresher training.
Take care,
john h
mkIII
| - The Matronics Kolb-List Email Forum - | | Use the List Feature Navigator to browse the many List utilities available such as the Email Subscriptions page, Archive Search & Download, 7-Day Browse, Chat, FAQ, Photoshare, and much more:
http://www.matronics.com/Navigator?Kolb-List |
|
_________________ John Hauck
MKIII/912ULS
hauck's holler
Titus, Alabama |
|
Back to top |
|
 |
jindoguy(at)gmail.com Guest
|
Posted: Fri Dec 01, 2006 12:24 pm Post subject: Cables, pulleys and nico press swages |
|
|
John, I'll go with AC 43.13, National Telephone Co (the people who developed the Nico process) and 20 years of flying Wills Wing hang gliders. Do the swage right, leave the tail out, and use a piece of heavy, clear heat shrink tubing to protect your fingers. Anything more is excess weight and work.
What can go wrong with a second swage? Bubbles, where the cable does not lay back parallel to itself, and twists where the two nicos are not parallel. Both will work the cable and are unacceptable workmanship. I still think Mike Riggs had it right in the Seagull 3 plans. The second nico does nothing but tie down the wire tail.
Rick
On 12/1/06, John Hauck <jhauck(at)elmore.rr.com (jhauck(at)elmore.rr.com)> wrote:[quote] --> Kolb-List message posted by: "John Hauck" <jhauck(at)elmore.rr.com (jhauck(at)elmore.rr.com)>
----- | If you leave cable sticking out
| > of the second one, then it has no purpose whatsoever. Its only
function is to keep you from
| > getting those nasty little holes in your finger.
Folks:
We went through this cable thing several years ago, especially leaving
a short piece of the cable tail extended past the sleeve.
If I understand correctly, keeping the tail inside the second sleeve
is like putting the cable in a shear. Most folks would cut the cable
end square. Then put this under tremendous load from the compression
tool on the sleeve against the other cable. What we have is a 90
degree shearing force from the tucked end on the opposite cable. I am
willing to take the nicks from the cable ends over the possibility of
weakening the splice with a tucked end. Through the years I have seen
several ultralight manufacturers tuck the ends of cables. Most
notably, Eipper. When questioned about this practice I got the
standard answer of, "that's the way we do it."
Some where I have read about using second sleeve for 3/32 and smaller [quote][b]
| - The Matronics Kolb-List Email Forum - | | Use the List Feature Navigator to browse the many List utilities available such as the Email Subscriptions page, Archive Search & Download, 7-Day Browse, Chat, FAQ, Photoshare, and much more:
http://www.matronics.com/Navigator?Kolb-List |
|
|
|
Back to top |
|
 |
|
|
You cannot post new topics in this forum You cannot reply to topics in this forum You cannot edit your posts in this forum You cannot delete your posts in this forum You cannot vote in polls in this forum You cannot attach files in this forum You can download files in this forum
|
Powered by phpBB © 2001, 2005 phpBB Group
|