nuckolls.bob(at)aeroelect Guest
|
Posted: Thu Nov 07, 2013 1:04 pm Post subject: Copper sheet specs redux |
|
|
I've had some direct emails asking about the selection
of copper sheet for fabrication of bus bars. It seems
that copper is sold in a market that adopted the Birmingham
guage system as opposed to the Brown and Sharp tables
common to the brass and aluminum markets. Then there's
the stainless steel guys who have their own tables
. . . sigh . . .
This excerpt from a copper sheet gauge table
illustrates the reason why our calculated weight
earlier this morning was a bit different than
the cited weight in the Ebay ad. The "48 oz"
copper being offered was indeed a couple mils
thicker than 1/16" thus explaining the difference.
[img]cid:.0[/img]
When bussing breakers the maximum loads you might
see on a bus bar can't be more than alternator
rating. Assume 60A alternator. 10AWG wire example
I cited earlier this morning has a cross section
of 0.0082 sq-in. 10AWG round wire will produce
a 10C rise with 30A of current flowing in it.
If ALL alternator current is fed to the center
of a one-piece bus bar and equally distributed
to half the bus on each side, then the bus carries
30 A max, probably much less.
A 16 Gauge copper buss bar (.065" thick) 1/2"
wide has a copper cross section of .065 x .5 or
0.032 square inches. This is 4x larger than a
10AWG wire so we can expect temperature rise to
be no more than 2.5 degrees C.
Run all the current to one end of the bus bar
such that the whole 60A flows through the copper.
Heating value rises by the square of current. So
2x current is 4x heat or 4x temperature rise so
we're back up to 10C max at end where the feeder
is attached.
The nice thing is that flat copper sheet will reject
heat better than a round wire so the expected rise
will be LESS than the round wire equivalent.
Now, consider the same, 0.064" copper jumped between
two contactor FAT wire terminals. Let's make the jumper
1" wide for 1/2 the resistance per inch of the bus bar
example above. So 60A of alternator current would bring
our rise down to 5C. Hit it with a 200A starter current
for 3x current, 9x rise and the strip of copper could
be expected to rise about 50C during cranking. But it's
got more area than wire and is heat-sinked to the studs
on either end so the heating will be less than 50C. Even
less considering that most cranking intervals are but
a few seconds . . . too short for the rise to stabilize.
This little exercise suggests that .065" copper in 1/2"
wide strips is just fine behind the panel . . . and 1"
strips is okay between contactors, probably no more
marginal for heat rejection than the starter itself. A
piece of 1/8" copper would drop the 50C rise to 25C at
200A in 10AWG wire equivalents . . . MUCH more headroom.
One could fabricate a thicker contactor-jumper from
two layers of 1/16" copper. Get all the joints bright
and clean. Torque the fasteners down tight. All will
be right with the universe.
Bob . . .
| - The Matronics AeroElectric-List Email Forum - | | Use the List Feature Navigator to browse the many List utilities available such as the Email Subscriptions page, Archive Search & Download, 7-Day Browse, Chat, FAQ, Photoshare, and much more:
http://www.matronics.com/Navigator?AeroElectric-List |
|
Description: |
|
Filesize: |
111.07 KB |
Viewed: |
640 Time(s) |
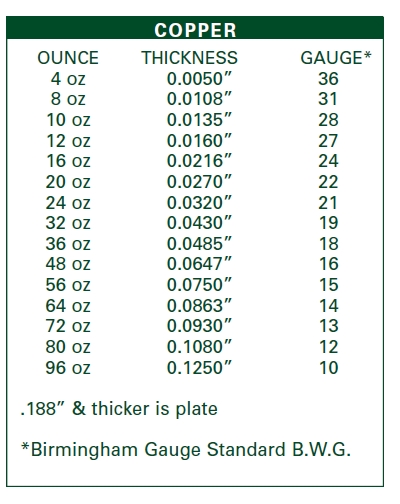
|
|
|