asarangan(at)gmail.com Guest
|
Posted: Tue Oct 29, 2013 10:10 am Post subject: Europa-List: AN3 Nut Torque Values…….or any Torque Values de |
|
|
Tony
These torque values are presumably from the FAA Advisory Circular, which can be found in this document, plus a wealth of other information:
http://www.faa.gov/regulations_policies/advisory_circulars/index.cfm/go/document.information/documentid/99861. The torque values are listed in chapter 7.
However these numbers are for fastening metal parts. For composites I would be reluctant to apply the maximum recommended torque. I believe the maximum torque is a function of the compressive strength of the parts being fastened and the tensile strength of the bolt itself. There was a document from Cirrus which had lower numbers for AN bolts on composites, but I can't seem to find it now. So far I've been tightening the bolts based on how much compression I feel after the parts become clamped.I know this is not very scientific.
On the other hand, I am a bit surprised that your AN3 bolt broke during normal torqing. Is it possible that the bolt bottomed out at the end of the threaded portion? In that case I can see how that can break at the joint between the shank and the threads.. In fact, I had to replace several AN bolts called out in the Europa manual with shorter lengths because they were bottoming out before clamping the parts.
On Mon, Oct 28, 2013 at 5:58 PM, Tony Renshaw <tonyrenshaw268(at)gmail.com (tonyrenshaw268(at)gmail.com)> wrote:
Quote: | Gidday,
Yesterday I was tightening by hand one of the two AN3 bolts that clamp the flap cross tube to the articulating/hinge arms that are attached in the floor. So, in case there is the slightest movement and this would exacerbate in my flaps I decided to do them up "tight". Guess what, I snapped one, yep snapped. It broke at the top of the shank where the thread started, and did NOT strip the thread as many might have presumed. This got me thinking that normally most bolts are designed to effect a shear load, and not normally a clamping load. Anyway, I know there is counter arguments to all of this, but what matters is the applicable torque loads we use if we torque them using a wrench, and I just stumbled upon a reference I think is important. I found this on an VansForce website, and why it matters is the torque values are NOT for locknuts, which have an inherent friction drag torque value of 14 in-lbs. So, referring to the attached table an AN3 needs 20-25 in-lbw, but in actuality would be more like 34-39 in-lbs.
I think this could be easily overlooked, and if the friction drag torque of locknuts is not taken into account, people are under torquing their bolts.
Regards
Tony Renshaw
Sydney Aussie.
[img]cid:02FDA00C-82F0-44B0-8D91-DBF3B727A6A8(at)optusnet.com.au[/img]
|
| - The Matronics Europa-List Email Forum - | | Use the List Feature Navigator to browse the many List utilities available such as the Email Subscriptions page, Archive Search & Download, 7-Day Browse, Chat, FAQ, Photoshare, and much more:
http://www.matronics.com/Navigator?Europa-List |
|
Description: |
|
Filesize: |
94.29 KB |
Viewed: |
979 Time(s) |
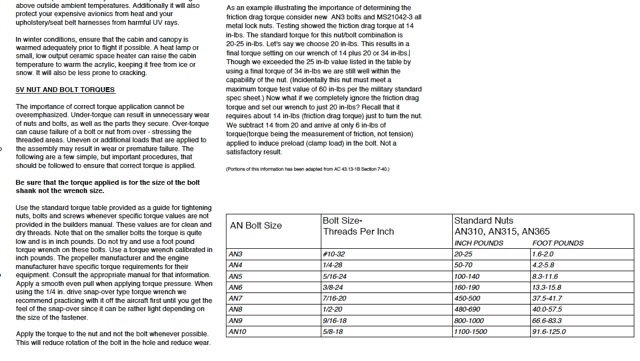
|
|
|