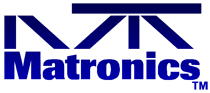 |
Matronics Email Lists Web Forum Interface to the Matronics Email Lists
|
View previous topic :: View next topic |
Author |
Message |
nuckolls.bob(at)aeroelect Guest
|
Posted: Mon Feb 21, 2011 11:18 pm Post subject: DIY CBOVM: variations on a theme |
|
|
Quote: | I am still wondering if a zener diode could be used instead of the SBS. If not, it would be interesting to know what the disadvantages of the zener diode are, or if it would even work at all.
Thanks for any advice.
Joe |
Joe,
Feeling adventuresome? I pondered the idea
of exploiting the LM431's precise voltage set
point with a design goal of eliminating the
potentiometer and the post assembly calibration.
Here's what I came up with.
[img]cid:7.1.0.9.0.20110222010338.01f7bff8(at)aeroelectric.com.0[/img]
The parts count is unchanged but it should be
calibrated as soon as the last solder joint is
cool. Temperature stability should be as good
or better than any previous versions.
Bob . . .
| - The Matronics AeroElectric-List Email Forum - | | Use the List Feature Navigator to browse the many List utilities available such as the Email Subscriptions page, Archive Search & Download, 7-Day Browse, Chat, FAQ, Photoshare, and much more:
http://www.matronics.com/Navigator?AeroElectric-List |
|
Description: |
|
Filesize: |
37.72 KB |
Viewed: |
9918 Time(s) |
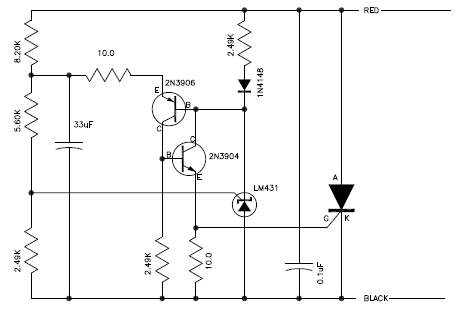
|
|
|
Back to top |
|
 |
user9253
Joined: 28 Mar 2008 Posts: 1929 Location: Riley TWP Michigan
|
Posted: Tue Feb 22, 2011 9:58 am Post subject: Re: DIY CBOVM: variations on a theme |
|
|
Thanks for that O.V. circuit using the LM431, Bob. I will add that IC to my next electronics parts order.
Joe
Do not archive
| - The Matronics AeroElectric-List Email Forum - | | Use the List Feature Navigator to browse the many List utilities available such as the Email Subscriptions page, Archive Search & Download, 7-Day Browse, Chat, FAQ, Photoshare, and much more:
http://www.matronics.com/Navigator?AeroElectric-List |
|
_________________ Joe Gores |
|
Back to top |
|
 |
user9253
Joined: 28 Mar 2008 Posts: 1929 Location: Riley TWP Michigan
|
Posted: Mon Mar 24, 2014 10:41 am Post subject: Re: DIY CBOVM: variations on a theme |
|
|
I built Bob's circuit. To test it, I wired it in series with an automotive lamp to a DC-DC converter like this one: http://tinyurl.com/kmpqcb8
I slowly turned the pot to increase the voltage. The lamp illuminated at almost 17 volts. Since my Rotax rectifier/regulator puts out about 13.8 volts, I decided to lower the set point of the over-voltage protector by substituting a 5.1K resistor for the 5.6K. Now the test lamp comes on at 16.2 volts. When the voltage increases above 15.8, the circuit becomes sensitive. Just touching the circuit with a digital voltmeter probe is enough to fire the SCR. Using a different voltmeter had the same affect. No doubt that in an electrically noisy environment like an airplane, the circuit will trip at 15.8 volts. That is not a problem though. 15.8 volts is 2 volts above my aircraft system voltage. If spring weather ever comes to Michigan, I will install it in the airplane.
Thanks for designing the circuit, Bob. You are my mentor.
Joe
| - The Matronics AeroElectric-List Email Forum - | | Use the List Feature Navigator to browse the many List utilities available such as the Email Subscriptions page, Archive Search & Download, 7-Day Browse, Chat, FAQ, Photoshare, and much more:
http://www.matronics.com/Navigator?AeroElectric-List |
|
_________________ Joe Gores |
|
Back to top |
|
 |
nuckolls.bob(at)aeroelect Guest
|
Posted: Mon Mar 24, 2014 7:04 pm Post subject: DIY CBOVM: variations on a theme |
|
|
At 01:41 PM 3/24/2014, you wrote:
I built Bob's circuit. To test it, I wired it in series with an
automotive lamp to a DC-DC converter like this one: http://tinyurl.com/kmpqcb8
I slowly turned the pot to increase the voltage. The lamp
illuminated at almost 17 volts. Since my Rotax rectifier/regulator
puts out about 13.8 volts, I decided to lower the set point of the
over-voltage protector by substituting a 5.1K resistor for the
5.6K. Now the test lamp comes on at 16.2 volts. When the voltage
increases above 15.8, the circuit becomes sensitive. Just touching
the circuit with a digital voltmeter probe is enough to fire the
SCR. Using a different voltmeter had the same affect. No doubt that
in an electrically noisy environment like an airplane, the circuit
will trip at 15.8 volts. That is not a problem though. 15.8 volts
is 2 volts above my aircraft system voltage. If spring weather ever
comes to Michigan, I will install it in the airplane.
That should not be so sensitive to probing.
How is this circuit packaged? Can you send me a pucture?
Bob . . .
| - The Matronics AeroElectric-List Email Forum - | | Use the List Feature Navigator to browse the many List utilities available such as the Email Subscriptions page, Archive Search & Download, 7-Day Browse, Chat, FAQ, Photoshare, and much more:
http://www.matronics.com/Navigator?AeroElectric-List |
|
|
|
Back to top |
|
 |
user9253
Joined: 28 Mar 2008 Posts: 1929 Location: Riley TWP Michigan
|
Posted: Wed Mar 26, 2014 6:40 am Post subject: Re: DIY CBOVM: variations on a theme |
|
|
I repeated testing of the over-voltage circuit today, doing a better job of connecting wires. If the voltage is steadily increased, the SCR fires at 16.2 volts. But if the voltage is set at 16.0 volts and held there, the SCR would fire after waiting a couple of minutes. Probing the input with a voltmeter intermittently caused the SCR to fire only when the voltage was above 15.9. Circuit instability, if any, is within 0.1 volt of the set-point. The adjustable voltage power supply only cost $6. Who knows how stable that is. The components are all through-hole, not surface mounted, and are mounted to a 1 x 2 inch area of PCB. I am happy with the circuit.
I intend to connect the over-voltage circuit in series with a relay coil that is powered by a 3 amp fuse.. The normally closed contacts of the relay will be in series with the AC output of the permanent magnet dynamo. In case of high voltage, the SCR will fire, connecting one leg of the coil to ground to energize the relay, opening the AC circuit to the rectifier/voltage regulator. The SCR will continue to hold the relay energized until battery power is disconnected from the relay coil.
This will not be a crowbar type of over-voltage protection. So no circuit breaker is required. High voltage will not blow the fuse.
Joe
| - The Matronics AeroElectric-List Email Forum - | | Use the List Feature Navigator to browse the many List utilities available such as the Email Subscriptions page, Archive Search & Download, 7-Day Browse, Chat, FAQ, Photoshare, and much more:
http://www.matronics.com/Navigator?AeroElectric-List |
|
_________________ Joe Gores |
|
Back to top |
|
 |
jluckey(at)pacbell.net Guest
|
Posted: Wed Mar 26, 2014 7:25 am Post subject: DIY CBOVM: variations on a theme |
|
|
Joe,
1. How much power can the dynamo produce?
2. Are there only 2 wires for the AC output? (I've never worked w/ a PM type alternator but most non-PM machines have 3 wires for AC output)
3. As you probably already know, on some relays, the current-handling capability of the NC contacts is less than the NO contacts
-Jeff
From: user9253 <fransew(at)gmail.com>
To: aeroelectric-list(at)matronics.com
Sent: Wednesday, March 26, 2014 7:40 AM
Subject: Re: DIY CBOVM: variations on a theme
--> AeroElectric-List message posted by: "user9253" <fransew(at)gmail.com (fransew(at)gmail.com)>
I repeated testing of the over-voltage circuit today, doing a better job of connecting wires. If the voltage is steadily increased, the SCR fires at 16.2 volts. But if the voltage is set at 16.0 volts and held there, the SCR would fire after waiting a couple of minutes. Probing the input with a voltmeter intermittently caused the SCR to fire only when the voltage was above 15.9. Circuit instability, if any, is within 0.1 volt of the set-point. The adjustable voltage power supply only cost $6. Who knows how stable that is. The components are all through-hole, not surface mounted, and are mounted to a 1 x 2 inch area of PCB. I am happy with the circuit.
I intend to connect the over-voltage circuit in series with a relay coil that is powered by a 3 amp fuse.. The normally closed contacts of the relay will be in series with the AC output of the permanent magnet dynamo. In case of high voltage, the SCR will fire, connecting one leg of the coil to ground to energize the relay, opening the AC circuit to the rectifier/voltage regulator. The SCR will continue to hold the relay energized until battery power is disconnected from the relay coil.
This will not be a crowbar type of over-voltage protection. So no circuit breaker is required. High voltage will not blow the fuse.
Joe
--------
Joe Gores
Read this topic online here:
http://forums.matronics.com/viewtopic//www.matronics.com/Navigator?AeroElectric-List" target="_blank">http://w--> http://fo= - List Contribution Web Site &nbs="http://www.matronics.com/contribution" target="_blank">http://www.mat=====================
[quote][b]
| - The Matronics AeroElectric-List Email Forum - | | Use the List Feature Navigator to browse the many List utilities available such as the Email Subscriptions page, Archive Search & Download, 7-Day Browse, Chat, FAQ, Photoshare, and much more:
http://www.matronics.com/Navigator?AeroElectric-List |
|
|
|
Back to top |
|
 |
kleh(at)dialupatcost.ca Guest
|
Posted: Wed Mar 26, 2014 8:45 am Post subject: DIY CBOVM: variations on a theme |
|
|
In regards to stability you might check that there is a capacitor across
the voltage reference diode and another from the SCR gate to ground. If
you happen to have an old circuit diagram dated before about 2005 it may
not show that update.
One nice thing about the crowbar and circuit breaker in the Z diagrams
is that the voltage is brought under control immediately when the SCR
fires. If I understand your post it sounds like your implementation
waits for the relay to open and for any subsequent arcing to extinguish.
Perhaps that is good enough but it seems preferable to use the circuit
breaker as per the Z diagrams so that the SCR clamps the voltage faster.
Might be other small advantages as well such as a subsequent dead
battery could not cause the alternator to come back on line.
Ken
On 26/03/2014 10:40 AM, user9253 wrote:
Quote: |
<fransew(at)gmail.com>
I repeated testing of the over-voltage circuit today, doing a better
job of connecting wires. If the voltage is steadily increased, the
SCR fires at 16.2 volts. But if the voltage is set at 16.0 volts and
held there, the SCR would fire after waiting a couple of minutes.
Probing the input with a voltmeter intermittently caused the SCR to
fire only when the voltage was above 15.9. Circuit instability, if
any, is within 0.1 volt of the set-point. The adjustable voltage
power supply only cost $6. Who knows how stable that is. The
components are all through-hole, not surface mounted, and are mounted
to a 1 x 2 inch area of PCB. I am happy with the circuit. I intend
to connect the over-voltage circuit in series with a relay coil that
is powered by a 3 amp fuse.. The normally closed contacts of the
relay will be in series with the AC output of the permanent magnet
dynamo. In case of high voltage, the SCR will fire, connecting one
leg of the coil to ground to energize the relay, opening the AC
circuit to the rectifier/voltage regulator. The SCR will continue to
hold the relay energized until battery power is disconnected from the
relay coil. This will not be a crowbar type of over-voltage
protection. So no circuit breaker is required. High voltage will
not blow the fuse. Joe
-------- Joe Gores
Read this topic online here:
http://forums.matronics.com/viewtopic.php?p=421067#421067
|
| - The Matronics AeroElectric-List Email Forum - | | Use the List Feature Navigator to browse the many List utilities available such as the Email Subscriptions page, Archive Search & Download, 7-Day Browse, Chat, FAQ, Photoshare, and much more:
http://www.matronics.com/Navigator?AeroElectric-List |
|
|
|
Back to top |
|
 |
user9253
Joined: 28 Mar 2008 Posts: 1929 Location: Riley TWP Michigan
|
Posted: Wed Mar 26, 2014 8:54 am Post subject: Re: DIY CBOVM: variations on a theme |
|
|
Jeff,
1. The Rotax 912 dynamo can generate up to about 20 amps. Although many recommend not loading it to more than 16 amps. My plane uses about 10 amps.
2. Yes, the AC output has two wires and is single phase.
3. If I am interpreting this data sheet correctly http://pewa.panasonic.com/assets/pcsd/catalog/cb-catalog.pdf
the normally closed contacts can handle 30 amps. I suspect that, over the long term, corrosion due to lack of exercise will be more of a problem than the contact rating.
Joe
| - The Matronics AeroElectric-List Email Forum - | | Use the List Feature Navigator to browse the many List utilities available such as the Email Subscriptions page, Archive Search & Download, 7-Day Browse, Chat, FAQ, Photoshare, and much more:
http://www.matronics.com/Navigator?AeroElectric-List |
|
_________________ Joe Gores |
|
Back to top |
|
 |
nuckolls.bob(at)aeroelect Guest
|
Posted: Wed Mar 26, 2014 9:05 am Post subject: DIY CBOVM: variations on a theme |
|
|
At 10:23 AM 3/26/2014, you wrote:
Quote: | Joe,
1. How much power can the dynamo produce?
|
Most are limited to about 30A. The single phase
(2-wire) offerings by B&C, Rotax and others
are in the 8-20A class. The 3-phase, 3-wire
devices for the larger 'tractors' can
get you 30A or so.
The problem with PM alternators is not the
power generating ability of the mechanism but
the power handling ability of the rectifier/
regulator. Unlike the 3-phase automotive
alternator that runs output power through
simple junction diodes. The regulator carries
only a couple amps of field current.
In the PM regulator, total output current of
up to 30A flows through regulator semiconductors.
Hence the heat sinks and limited size with
respect to power.
Bob . . .
| - The Matronics AeroElectric-List Email Forum - | | Use the List Feature Navigator to browse the many List utilities available such as the Email Subscriptions page, Archive Search & Download, 7-Day Browse, Chat, FAQ, Photoshare, and much more:
http://www.matronics.com/Navigator?AeroElectric-List |
|
|
|
Back to top |
|
 |
user9253
Joined: 28 Mar 2008 Posts: 1929 Location: Riley TWP Michigan
|
Posted: Wed Mar 26, 2014 9:23 am Post subject: Re: DIY CBOVM: variations on a theme |
|
|
Ken,
Thanks for suggesting the capacitors. The circuit is stable unless the voltage gets very close to the trip point. That is OK with me as long as there is no nuisance tripping. Time will tell.
Good point about the crowbar circuit acting immediately by clamping the supply to ground. The data sheet for my relay says it will operate in 15 milliseconds. I am hoping the battery will limit the voltage until the relay contacts open. I will try to land before the battery runs down enough (almost completely dead) to drop out the relay.
Joe
| - The Matronics AeroElectric-List Email Forum - | | Use the List Feature Navigator to browse the many List utilities available such as the Email Subscriptions page, Archive Search & Download, 7-Day Browse, Chat, FAQ, Photoshare, and much more:
http://www.matronics.com/Navigator?AeroElectric-List |
|
_________________ Joe Gores |
|
Back to top |
|
 |
kleh(at)dialupatcost.ca Guest
|
Posted: Wed Mar 26, 2014 9:59 am Post subject: DIY CBOVM: variations on a theme |
|
|
Joe
600 hours on two of the OVMs and never a nuisance trip.
Have had a real trip on the Dynamo one when I started up with one of my
two small Z-14 AGM batteries dead. The totally dead battery wouldn't
accept current and the John Deere regulator immediately failed full on.
The battery did eventually charge but initially it would not accept current.
Note to self - if I leave a switch on by mistake for a week and can't
charge the battery first - at least run with that alternator off and the
batteries paralleled to the other alternator for awhile with engine
speed low enough to keep the charge current reasonable.
Ken
do not archive
On 26/03/2014 1:23 PM, user9253 wrote:
Quote: |
<fransew(at)gmail.com>
Ken, Thanks for suggesting the capacitors. The circuit is stable
unless the voltage gets very close to the trip point. That is OK
with me as long as there is no nuisance tripping. Time will tell.
Good point about the crowbar circuit acting immediately by clamping
the supply to ground. The data sheet for my relay says it will
operate in 15 milliseconds. I am hoping the battery will limit the
voltage until the relay contacts open. I will try to land before the
battery runs down enough (almost completely dead) to drop out the
relay. Joe
-------- Joe Gores
|
| - The Matronics AeroElectric-List Email Forum - | | Use the List Feature Navigator to browse the many List utilities available such as the Email Subscriptions page, Archive Search & Download, 7-Day Browse, Chat, FAQ, Photoshare, and much more:
http://www.matronics.com/Navigator?AeroElectric-List |
|
|
|
Back to top |
|
 |
nuckolls.bob(at)aeroelect Guest
|
Posted: Wed Mar 26, 2014 11:47 am Post subject: DIY CBOVM: variations on a theme |
|
|
At 11:45 AM 3/26/2014, you wrote:
Quote: |
In regards to stability you might check that there is a capacitor
across the voltage reference diode and another from the SCR gate to
ground. If you happen to have an old circuit diagram dated before
about 2005 it may not show that update.
One nice thing about the crowbar and circuit breaker in the Z
diagrams is that the voltage is brought under control immediately
when the SCR fires. If I understand your post it sounds like your
implementation waits for the relay to open and for any subsequent
arcing to extinguish. Perhaps that is good enough but it seems
preferable to use the circuit breaker as per the Z diagrams so that
the SCR clamps the voltage faster. Might be other small advantages
as well such as a subsequent dead battery could not cause the
alternator to come back on line.
|
For the run-of-the-mill ov conditions with a good
battery, an ov even is not one of extreme urgency.
The ships air-worthy battery will stand off a runaway
alternator for significant intervals. If one waited
100 mS to evaluate an ov condition for a true runaway
alternator, it wouldn't be a bad thing.
In fact, the next generation ov module will do just
that. Sensing an ov condition start a 100mS timer
that continue to run as long as the voltage does not
drop back below 16V before the timer runs out.
On the other hand, a second threshold at 20V assumes
no air worthy battery is present and an immediate trip
is initiated.
We're still going to pull down on the field supply
breaker . . .
Bob . . .
| - The Matronics AeroElectric-List Email Forum - | | Use the List Feature Navigator to browse the many List utilities available such as the Email Subscriptions page, Archive Search & Download, 7-Day Browse, Chat, FAQ, Photoshare, and much more:
http://www.matronics.com/Navigator?AeroElectric-List |
|
|
|
Back to top |
|
 |
jan_de_jong(at)casema.nl Guest
|
Posted: Mon Mar 31, 2014 9:16 am Post subject: DIY CBOVM: variations on a theme |
|
|
That's another issue with a lithium battery - it does not keep OV down
well - even if not fitted with a BMS. And it seriously dislikes
overvoltage. It thus requires a fast OV switch at the alternator.
And if it has a BMS it will also have a battery OV cutoff switch built
in. Making the battery unavailable just when it is needed.
My conclusion has been that if I want Lithium I will have to make the
under/over cell voltage and cell temperature monitoring and top
balancing myself.
With backed up OV protection at the alternator.
And have the individual cells accessible to thermistors.
Jan de Jong
On 3/26/2014 8:45 PM, Robert L. Nuckolls, III wrote:
Quote: |
<nuckolls.bob(at)aeroelectric.com>
At 11:45 AM 3/26/2014, you wrote:
>
>
> In regards to stability you might check that there is a capacitor
> across the voltage reference diode and another from the SCR gate to
> ground. If you happen to have an old circuit diagram dated before
> about 2005 it may not show that update.
>
> One nice thing about the crowbar and circuit breaker in the Z
> diagrams is that the voltage is brought under control immediately
> when the SCR fires. If I understand your post it sounds like your
> implementation waits for the relay to open and for any subsequent
> arcing to extinguish. Perhaps that is good enough but it seems
> preferable to use the circuit breaker as per the Z diagrams so that
> the SCR clamps the voltage faster. Might be other small advantages as
> well such as a subsequent dead battery could not cause the alternator
> to come back on line.
For the run-of-the-mill ov conditions with a good
battery, an ov even is not one of extreme urgency.
The ships air-worthy battery will stand off a runaway
alternator for significant intervals. If one waited
100 mS to evaluate an ov condition for a true runaway
alternator, it wouldn't be a bad thing.
In fact, the next generation ov module will do just
that. Sensing an ov condition start a 100mS timer
that continue to run as long as the voltage does not
drop back below 16V before the timer runs out.
On the other hand, a second threshold at 20V assumes
no air worthy battery is present and an immediate trip
is initiated.
We're still going to pull down on the field supply
breaker . . .
Bob . . .
|
| - The Matronics AeroElectric-List Email Forum - | | Use the List Feature Navigator to browse the many List utilities available such as the Email Subscriptions page, Archive Search & Download, 7-Day Browse, Chat, FAQ, Photoshare, and much more:
http://www.matronics.com/Navigator?AeroElectric-List |
|
|
|
Back to top |
|
 |
nuckolls.bob(at)aeroelect Guest
|
Posted: Mon Mar 31, 2014 10:13 am Post subject: DIY CBOVM: variations on a theme |
|
|
At 12:15 PM 3/31/2014, you wrote:
Quote: |
That's another issue with a lithium battery - it does not keep OV
down well - even if not fitted with a BMS. And it seriously dislikes
overvoltage. It thus requires a fast OV switch at the alternator.
And if it has a BMS it will also have a battery OV cutoff switch
built in. Making the battery unavailable just when it is needed.
My conclusion has been that if I want Lithium I will have to make
the under/over cell voltage and cell temperature monitoring and top
balancing myself.
With backed up OV protection at the alternator.
And have the individual cells accessible to thermistors.
|
Your perceptions of being inadequately informed
with respect to operating details of the various
lithium products are accurate.
There is no industry standard for the term "BMS".
I'm working the 4th installment on the series
of battery articles for Kitplanes. The past 7
weeks have been enlightening.
I'm not sure that alternator OV protection needs
to be anything beyond the ordinary . . . I'm still
stirring the stew of simple-ideas . . .
Bob . . .
| - The Matronics AeroElectric-List Email Forum - | | Use the List Feature Navigator to browse the many List utilities available such as the Email Subscriptions page, Archive Search & Download, 7-Day Browse, Chat, FAQ, Photoshare, and much more:
http://www.matronics.com/Navigator?AeroElectric-List |
|
|
|
Back to top |
|
 |
jan_de_jong(at)casema.nl Guest
|
Posted: Mon Mar 31, 2014 12:02 pm Post subject: DIY CBOVM: variations on a theme |
|
|
The implicit "trust us" attitude is in any case unwarranted. Full
specifications of the built-in electronics are absolutely necessary.
What I have seen is not very compatible with aircraft use. We do not
want OV cut-out built-in (should be done somewhere up in the charging
path). We probably do not want LV cut-out built-in either (saving the
battery may not always be the highest goal). But we want monitoring and
warning. And as a pilot I want to know about temperatures. When used
well (correct voltages and currents within limits, no recharging ever
after full discharge) the remaining danger is a manufacturing fault,
with temperature discrepancy the only available signal.
And a measure of top balancing is needed unless we are willing to adopt
a discipline of doing that externally. A certain minimum balancing
current per Ah, say 50mA or so is required. I've seen balancing currents
quoted for Chinese BMS products that are likely useless for any
realistic battery size (they may be intended for UPS batteries - very
long charging times and smallish charging currents).
And the balancing algorithm is often primitive - most balancers only
balance at the very end of the charging process by comparing a cell
voltage with a high limit-voltage, not during the charging process by
comparing a cell voltage with the voltages of other cells. The latter
allows good balancing with a lower alternator set voltage. In exchange
for a few percent of charge you get much longer life - apparently.
I wish you wisdom with the 4th article on batteries (great articles so
far, I approve of the current editor in chief of KP!)
Jan de Jong
On 3/31/2014 8:12 PM, Robert L. Nuckolls, III wrote:
Quote: |
<nuckolls.bob(at)aeroelectric.com>
At 12:15 PM 3/31/2014, you wrote:
>
> <jan_de_jong(at)casema.nl>
>
> That's another issue with a lithium battery - it does not keep OV
> down well - even if not fitted with a BMS. And it seriously dislikes
> overvoltage. It thus requires a fast OV switch at the alternator.
> And if it has a BMS it will also have a battery OV cutoff switch
> built in. Making the battery unavailable just when it is needed.
>
> My conclusion has been that if I want Lithium I will have to make the
> under/over cell voltage and cell temperature monitoring and top
> balancing myself.
> With backed up OV protection at the alternator.
> And have the individual cells accessible to thermistors.
Your perceptions of being inadequately informed
with respect to operating details of the various
lithium products are accurate.
There is no industry standard for the term "BMS".
I'm working the 4th installment on the series
of battery articles for Kitplanes. The past 7
weeks have been enlightening.
I'm not sure that alternator OV protection needs
to be anything beyond the ordinary . . . I'm still
stirring the stew of simple-ideas . . .
Bob . . .
|
| - The Matronics AeroElectric-List Email Forum - | | Use the List Feature Navigator to browse the many List utilities available such as the Email Subscriptions page, Archive Search & Download, 7-Day Browse, Chat, FAQ, Photoshare, and much more:
http://www.matronics.com/Navigator?AeroElectric-List |
|
|
|
Back to top |
|
 |
nuckolls.bob(at)aeroelect Guest
|
Posted: Mon Mar 31, 2014 3:24 pm Post subject: DIY CBOVM: variations on a theme |
|
|
At 03:00 PM 3/31/2014, you wrote:
The implicit "trust us" attitude is in any case unwarranted. Full
specifications of the built-in electronics are absolutely necessary.
that will be a primary premise of the 'last' article.
What I have seen is not very compatible with aircraft use. We do not
want OV cut-out built-in (should be done somewhere up in the charging path).
This is certainly the legacy philosophy for lead-acid
and/or Ni-Cad batteries wherein the battery was a
'current sink' of demonstrable value for managing
a runaway generator/alternator.
But let's assume for the moment that one of our
future design goals is to craft and prove airworthiness
of an alternator-only operation protocol. Now we need
to show that the runaway alternator can be controlled
within the DO160/MilSTD704 envelope.
If that proves to be practical, then the electronics
in the battery need not assume any duties beyond those
for protecting the battery . . . the battery MIGHT be
relieved of duty for standing guard at the gates
standing off runaway alternators.
We probably do not want LV cut-out built-in either (saving the
battery may not always be the highest goal). But we want monitoring
and warning.
Yeah . . . but it depends on WHERE the l.v. cutout
occurs.
Toyota writes software intended to maintain their
lithium cells at some place between 30 and 85% capacity.
This is the ENERGY operating range that offers the
advertised cell life. But they don't force disconnect
the battery . . . as far as I've been able to learn
so far.
Depending on the BMS designer's charter from on-high . . .
he may well have other bounds. Without advocating for
any particular energy range . . . I'll suggest that any
offering that includes a BMS would do well to tell
all . . . inquiring pilots NEED to know.
And as a pilot I want to know about temperatures. When used well
(correct voltages and currents within limits, no recharging ever
after full discharge) the remaining danger is a manufacturing fault,
with temperature discrepancy the only available signal.
And a measure of top balancing is needed unless we are willing to
adopt a discipline of doing that externally. A certain minimum
balancing current per Ah, say 50mA or so is required. I've seen
balancing currents quoted for Chinese BMS products that are likely
useless for any realistic battery size (they may be intended for UPS
batteries - very long charging times and smallish charging currents).
Exactly. An these issues drive cost of ownership. Yes,
the lithium products have stellar performance in some
venues but with LIMITS that much be UNDERSTOOD and
incorporated into the user's operating philosophy.
$time$ fiddling with batteries is $time$ not available
to go flying.
And the balancing algorithm is often primitive - most balancers only
balance at the very end of the charging process by comparing a cell
voltage with a high limit-voltage, not during the charging process by
comparing a cell voltage with the voltages of other cells. The latter
allows good balancing with a lower alternator set voltage. In
exchange for a few percent of charge you get much longer life - apparently.
"Apparently" is the operative term. The family
of lithium cells available for incorporation into
finished goods is not large . . . There's probably
no more than a half dozen shakers-n-movers in
the cylindrical cell market. They're all pretty
big names . . . I doubt that core capabilities
of the range of offerings varies much. But we
see a large variation in proposed operating
philosophies across the spectrum of "assemblers"
who package these cells up for market.
I wish you wisdom with the 4th article on batteries (great articles
so far, I approve of the current editor in chief of KP!)
Thank you my friend. I'm learning. But I wish that the
questions were being answered faster than they surface!
This first past at lithium-for-airplanes will probably
be disappointing for many who hope that a an ideal
drop-in-replacement for SVRLA is going to emerge.
But as you've noted, no matter what the advertising
hype says, "Their ain't no such thing as a lithium
drop-in for lead-acid."
For anything beyond the day-vfr machine with
gravity flow fuel and magnetos, the prudent
owner/pilot would do well to understand the
limitations. Further, assuming a willingness to
$invest$ in weight savings know that changes to
ownership and operating philosophy are inevitable.
Thank you for contributing to the dialog . . .
Bob . . .
| - The Matronics AeroElectric-List Email Forum - | | Use the List Feature Navigator to browse the many List utilities available such as the Email Subscriptions page, Archive Search & Download, 7-Day Browse, Chat, FAQ, Photoshare, and much more:
http://www.matronics.com/Navigator?AeroElectric-List |
|
|
|
Back to top |
|
 |
jan_de_jong(at)casema.nl Guest
|
Posted: Tue Apr 01, 2014 2:44 am Post subject: DIY CBOVM: variations on a theme |
|
|
Quote: | What I have seen is not very compatible with aircraft use. We do not
want OV cut-out built-in (should be done somewhere up in the charging
path).
This is certainly the legacy philosophy for lead-acid
and/or Ni-Cad batteries wherein the battery was a
'current sink' of demonstrable value for managing
a runaway generator/alternator.
But let's assume for the moment that one of our
future design goals is to craft and prove airworthiness
of an alternator-only operation protocol. Now we need
to show that the runaway alternator can be controlled
within the DO160/MilSTD704 envelope.
If that proves to be practical, then the electronics
in the battery need not assume any duties beyond those
for protecting the battery . . . the battery MIGHT be
relieved of duty for standing guard at the gates
standing off runaway alternators.
|
The current lead-acid battery has 2 tasks when an OV event occurs:
1. slowing the event down to facilitate OVP without false triggering
2. keeping the battery-connected busses powered when the charging
system responsible for the OV event is disconnected from the bus
Both tasks must be covered or made unnecessary with any new alternative
use of a battery.
Jan de Jong
| - The Matronics AeroElectric-List Email Forum - | | Use the List Feature Navigator to browse the many List utilities available such as the Email Subscriptions page, Archive Search & Download, 7-Day Browse, Chat, FAQ, Photoshare, and much more:
http://www.matronics.com/Navigator?AeroElectric-List |
|
|
|
Back to top |
|
 |
|
|
You cannot post new topics in this forum You cannot reply to topics in this forum You cannot edit your posts in this forum You cannot delete your posts in this forum You cannot vote in polls in this forum You cannot attach files in this forum You can download files in this forum
|
Powered by phpBB © 2001, 2005 phpBB Group
|