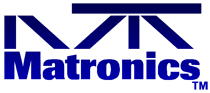 |
Matronics Email Lists Web Forum Interface to the Matronics Email Lists
|
View previous topic :: View next topic |
Author |
Message |
grs-pms(at)comcast.net Guest
|
Posted: Sat Jul 15, 2006 8:00 pm Post subject: Drag of a windmilling propellor |
|
|
I've looked at several old airplane performance texts to try to find some actual engineering data on this subject.� So far, the best I can find comes from "Aerodynamics For Naval Aviators" (Rev. 1965), pages 148 and 149.� This is a great reference for the non-engineer, by the way.�Very readable, and�no math beyond multiplication and division.
�
To quote a few sentences from page 148:� "At smaller blade angles near the flat pitch position, the drag added by the propeller is very large. �At these small blade angles, the propeller windmilling at high RPM can create such a tremendous amount of drag that the airplane may be uncontrollable.�The propeller windmilling at high speed in the low range of blade angles can produce an increase in parasite drag which may be as great as the parasite drag of the basic airplane.� An indication of this powerful drag is seen by the helicopter in autorotation.� The windmilling rotor is capable of producing autorotation rates of descent which approach that of a parachute canopy with the identical disc area loading.� Thus, the propeller rotating at high speed and small blade angle can produce an effective drag coefficient of the disc area which compares with that of a parachute canopy."
�
This seems to confirm the comparison of a windmilling prop to�a helicopter rotor or parachute.���The question remains though,�what is meant by "smaller blade angles", or "low range of blade angles"?�
�
On page 149�there is a chart which depicts the change in equivalent parasite area vs blade pitch angle.� At blade�pitch angles near zero the�parasite area, hence the�drag,�of the windmilling propeller goes clear off the top of the chart, as expected.� For a pitch angle around 15 degrees, somewhere close to a fixed pitch�(or ground adjustable) prop on a light airplane, the drag of the windmilling prop is about twice that of a stopped prop.� Somewhere between 20 and 25 degrees blade pitch the two curves cross over, and at higher blade angles the drag of the stopped prop is actually greater.� Of course, both are equal, and minimum,�at the 90 degree feathered position.�� The source of this chart is not indicated, so details of�blade planform, number of blades, RPM�etc. are lacking.
�
If anyone has�a good engineering reference on this subject, I'd appreciate knowing about it.
�
George
�
�
| - The Matronics Zenith-List Email Forum - | | Use the List Feature Navigator to browse the many List utilities available such as the Email Subscriptions page, Archive Search & Download, 7-Day Browse, Chat, FAQ, Photoshare, and much more:
http://www.matronics.com/Navigator?Zenith-List |
|
|
|
Back to top |
|
 |
ggower_99(at)yahoo.com Guest
|
Posted: Sat Jul 15, 2006 9:23 pm Post subject: Drag of a windmilling propellor |
|
|
Hello George and list,
�
Talking about first hand experience,� I had flown weight shift trikes for the last 12 years,� they glide lot better than most ultralights, so landing with the engine stoped was (still is) a very common manuver here.��
�
A few years ago (maybe about 4), there were at least two machines that where imported "full equiped",� "top of the hill"� by a couple of rich pilots,�� both had 582 Rotax �engines and they came with a new style of clutch for the propeller, �that in my personal opinon was a highly engineered� go kart centrifugal clutch ���
�
The engine could be started and run at idle,�the propeller will not move, will not engage until certain rpms...� This was an idea for safety in the ground...� Engine idled smooth.�
�
But also �when the engine�was stoped�at� altitude, the prop will freely windmill (no direct conection with the reducction unit).� They were so draggy (compared with same model of trikes but without�this�clutch), that the gliding distance was shortened at least more than�a half!� The pilots comment that they feeled like opening a droge shute...
�
Just a first hand witnessed comment, that came to my memory from your post.
�
Saludos
Gary Gower.
Flying from Chapala, Mexico.
Now in "normal" airplanes
Do not archive.
George Swinford <grs-pms(at)comcast.net> wrote:
Quote: | I've looked at several old airplane performance texts to try to find some actual engineering data on this subject.� So far, the best I can find comes from "Aerodynamics For Naval Aviators" (Rev. 1965), pages 148 and 149.� This is a great reference for the non-engineer, by the way.�Very readable, and�no math beyond multiplication and division.
�
To quote a few sentences from page 148:� "At smaller blade angles near the flat pitch position, the drag added by the propeller is very large. �At these small blade angles, the propeller windmilling at high RPM can create such a tremendous amount of drag that the airplane may be uncontrollable.�The propeller windmilling at high speed in the low range of blade angles can produce an increase in parasite drag which may be as great as the parasite drag of the basic airplane.� An indication of this powerful drag is seen by the helicopter in autorotation.� The windmilling rotor is capable of producing autorotation rates of descent which approach that of a parachute canopy with the identical disc area loading.� Thus, the propeller rotating at high speed and small blade angle can produce an effective drag coefficient of the disc area which compares with that of a parachute canopy."
�
This seems to confirm the comparison of a windmilling prop to�a helicopter rotor or parachute.���The question remains though,�what is meant by "smaller blade angles", or "low range of blade angles"?�
�
On page 149�there is a chart which depicts the change in equivalent parasite area vs blade pitch angle.� At blade�pitch angles near zero the�parasite area, hence the�drag,�of the windmilling propeller goes clear off the top of the chart, as expected.� For a pitch angle around 15 degrees, somewhere close to a fixed pitch�(or ground adjustable) prop on a light airplane, the drag of the windmilling prop is about twice that of a stopped prop.� Somewhere between 20 and 25 degrees blade pitch the two curves cross over, and at higher blade angles the drag of the stopped prop is actually greater.� Of course, both are equal, and minimum,�at the 90 degree feathered position.�� The source of this chart is not indicated, so details of�blade planform, number of blades, RPM�etc. are lacking.
�
If anyone has�a good engineering reference on this subject, I'd appreciate knowing about it.
�
George
�
�
|
Want to be your own boss? Learn how on [url=http://us.rd.yahoo.com/evt=41244/*http://smallbusiness.yahoo.com/r-index] Yahoo! Small Business.[/url]
| - The Matronics Zenith-List Email Forum - | | Use the List Feature Navigator to browse the many List utilities available such as the Email Subscriptions page, Archive Search & Download, 7-Day Browse, Chat, FAQ, Photoshare, and much more:
http://www.matronics.com/Navigator?Zenith-List |
|
|
|
Back to top |
|
 |
|
|
You cannot post new topics in this forum You cannot reply to topics in this forum You cannot edit your posts in this forum You cannot delete your posts in this forum You cannot vote in polls in this forum You cannot attach files in this forum You can download files in this forum
|
Powered by phpBB © 2001, 2005 phpBB Group
|