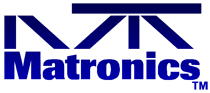 |
Matronics Email Lists Web Forum Interface to the Matronics Email Lists
|
View previous topic :: View next topic |
Author |
Message |
glcasey(at)adelphia.net Guest
|
Posted: Thu Sep 14, 2006 5:35 am Post subject: Fuel Pump Switch(es |
|
|
Quote: |
Subject: Re: Fuel Pump Switch(es)
Fuel system problems are a major cause of engine stoppage in �
homebuilt aircraft.� Any fuel system that deviates from the norm, in �
either design or installation details, opens the door to unexpected �
problems.� You have made a bunch of assumptions on how the system �
will perform following various types of failures.� It would be wise �
to validate those assumptions via actual tests, either on the ground, �
or in the air over a nice long runway.
Kevin Horton |
Here is the reply below the reference, as suggested by another lister..
Yes, perhaps the biggest disadvantage of using two separate fuel valves is the one you suggest - it deviates from the "norm."� And changing tanks takes two motions - opening the new valve, followed by closing the old valve. �Since the weakest link in any safety system is usually the operator, what would happen if he (me) did something wrong?� If you shut off one tank before turning the other on the engine will quit immediately - instant feedback and obviously correctable. �If you turn one on and forget to turn the other off nothing will immediately happen, but before the engine will suck air one tank has to go completely empty and in the case of my installation there are gages and both audio and visual warnings of that event. �I felt these disadvantages are compensated for by the advantages of being able to shut the fuel off before it enters the cockpit, reduction in the number of fittings in the cockpit (someone correctly pointed out that the total number of fittings might not change), and completely independent fuel controls.� But I don't think I've made any "assumptions" regarding the operation - the failure modes and results are fairly straightforward - valve off, no flow - valve on, flow.� Perhaps the only unknown is what happens with low tanks and both valves open, and that has been discovered by others - the empty tank can allow air into the system, preventing the use of the fuel in the other tank.� To verify this one would have to fly with one tank empty and the other almost empty, and I am not willing to do that.� Regarding the number of fittings I recall counting the possible in-cockpit leaks in the standard ES system at something over 30 with one moving seal and quite a number of those remain "wet" even though the fuel valve is turned off.� My system has a total of 7 potential leak paths in the cockpit and no moving seals, all of which go "dry" with the fuel valves off.� The builder with the "electric" engine and one electric pump in each wing can probably has even fewer, except he can't positively shut anything off.
Gary Casey�
[quote][b]
| - The Matronics AeroElectric-List Email Forum - | | Use the List Feature Navigator to browse the many List utilities available such as the Email Subscriptions page, Archive Search & Download, 7-Day Browse, Chat, FAQ, Photoshare, and much more:
http://www.matronics.com/Navigator?AeroElectric-List |
|
|
|
Back to top |
|
 |
khorton01(at)rogers.com Guest
|
Posted: Thu Sep 14, 2006 2:41 pm Post subject: Fuel Pump Switch(es |
|
|
On 14 Sep 2006, at 09:33, Gary Casey wrote:
Quote: |
Quote: | Subject: Re: Fuel Pump Switch(es)
Fuel system problems are a major cause of engine stoppage in �
homebuilt aircraft.� Any fuel system that deviates from the norm, in �
either design or installation details, opens the door to unexpected �
problems.� You have made a bunch of assumptions on how the system �
will perform following various types of failures.� It would be wise �
to validate those assumptions via actual tests, either on the ground, �
or in the air over a nice long runway.
Kevin Horton
|
Here is the reply below the reference, as suggested by another lister..
Yes, perhaps the biggest disadvantage of using two separate fuel valves is the one you suggest - it deviates from the "norm."� And changing tanks takes two motions - opening the new valve, followed by closing the old valve. �Since the weakest link in any safety system is usually the operator, what would happen if he (me) did something wrong?� If you shut off one tank before turning the other on the engine will quit immediately - instant feedback and obviously correctable. �If you turn one on and forget to turn the other off nothing will immediately happen, but before the engine will suck air one tank has to go completely empty and in the case of my installation there are gages and both audio and visual warnings of that event. �I felt these disadvantages are compensated for by the advantages of being able to shut the fuel off before it enters the cockpit, reduction in the number of fittings in the cockpit (someone correctly pointed out that the total number of fittings might not change), and completely independent fuel controls.� But I don't think I've made any "assumptions" regarding the operation - the failure modes and results are fairly straightforward - valve off, no flow - valve on, flow.� Perhaps the only unknown is what happens with low tanks and both valves open, and that has been discovered by others - the empty tank can allow air into the system, preventing the use of the fuel in the other tank.� To verify this one would have to fly with one tank empty and the other almost empty, and I am not willing to do that.� Regarding the number of fittings I recall counting the possible in-cockpit leaks in the standard ES system at something over 30 with one moving seal and quite a number of those remain "wet" even though the fuel valve is turned off.� My system has a total of 7 potential leak paths in the cockpit and no moving seals, all of which go "dry" with the fuel valves off.� The builder with the "electric" engine and one electric pump in each wing can probably has even fewer, except he can't positively shut anything off.
|
I've worked full time in the flight test world since 1987.� I've seen numerous cases where aircraft systems did not perform as expected.� In every case the system designer had an apparently solid analysis that predicted how the system should perform, yet he overlooked some aspect, and tests showed that the system did not perform as expected.� If this is not a critical system, then it doesn't really matter.� But, here we have a critical system, and you have based the decision on the system�architecture on some assumptions about how the system will work.� Someday those assumptions will be tested.� If you test the assumptions during the flight test program, you can structure the test so you are still safe even if the system does not perform as expected.� If you don't do the test then, someday you may stumble across that condition when you hadn't planned it.� If the system works as expected, then everything is OK.� But if the system does not perform, then you may lose the aircraft.
For example, what is the engine restart procedure after you have shut one tank down, and were slow opening the other fuel valve, resulting in engine stoppage?� When would you rather try out your planned restart procedure for the first time?� Overhead a long runway at 5,000 ft when you were mentally prepared for problems?� Or over rough country with no fields or runways in sight when a stoppage would be a complete surprise?
Kevin Horton� �� �� �RV-8 (finishing kit)
Ottawa, Canada
http://www.kilohotel.com/rv8
[quote][b]
| - The Matronics AeroElectric-List Email Forum - | | Use the List Feature Navigator to browse the many List utilities available such as the Email Subscriptions page, Archive Search & Download, 7-Day Browse, Chat, FAQ, Photoshare, and much more:
http://www.matronics.com/Navigator?AeroElectric-List |
|
|
|
Back to top |
|
 |
|
|
You cannot post new topics in this forum You cannot reply to topics in this forum You cannot edit your posts in this forum You cannot delete your posts in this forum You cannot vote in polls in this forum You cannot attach files in this forum You can download files in this forum
|
Powered by phpBB © 2001, 2005 phpBB Group
|