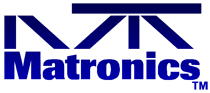 |
Matronics Email Lists Web Forum Interface to the Matronics Email Lists
|
View previous topic :: View next topic |
Author |
Message |
gommone7(at)bellsouth.net Guest
|
Posted: Tue Oct 03, 2006 8:35 am Post subject: vhf antennas |
|
|
Hi ,I'm building an rv10,and I have contradictories informations about how install the antennas,the counselor and a couple of "masters" say clean the metal from any paint and install the antenna,but the manufacturer send it with a cork gasket(one of the best insulation ),to install .
any logical for this.
Thanks.
Hugo
| - The Matronics AeroElectric-List Email Forum - | | Use the List Feature Navigator to browse the many List utilities available such as the Email Subscriptions page, Archive Search & Download, 7-Day Browse, Chat, FAQ, Photoshare, and much more:
http://www.matronics.com/Navigator?AeroElectric-List |
|
|
|
Back to top |
|
 |
nuckollsr(at)cox.net Guest
|
Posted: Tue Oct 03, 2006 9:10 am Post subject: vhf antennas |
|
|
At 12:33 PM 10/3/2006 -0400, you wrote:
Quote: |
Hi ,I'm building an rv10,and I have contradictories informations about how
install the antennas,the counselor and a couple of "masters" say clean the
metal from any paint and install the antenna,but the manufacturer send it
with a cork gasket(one of the best insulation ),to install .
any logical for this.
Thanks.
Hugo
|
See:
http://www.aeroelectric.com/Pictures/Antenna/Antenna_Installation.gif
From some earlier posts:
>A while back you had some words of wisdom for a person who'd asked about
>getting enough metal to metal contact for ground plane purposes with his
>comm antenna. You mentioned to him that riveting his doubler plates to the
>skin would provide plenty of contact when paint and other debris was
>squeezed out during the riveting process. I have a little different twist
>on this question. I made doubler plates to go inside the fuselage but don't
>really want to rivet them on. The number of fasteners that hold the
>antennas to the airplane will hold doublers to the skin and I don't see a
>need to rivet the doublers on. This however, could cause trouble. Since
>I've already primed the inside of the aluminum fuselage skin, would like to
>prime the doublers so they don't corrode when water gets between them and
>the fuselage skin and don't want to remove the primer from the skin......I
>fear I will have insufficient connection to get good ground plane action.
>The comm antennas come with a cork gasket that's supposed to go between the
>outside skin and the antenna so that limits ground plane connection on the
>outside skin (presently bare aluminum). Am I gonna have to bite the bullet
>and rivet the doublers to get some connection or ????(the doublers have
>nutplates riveted to them to accept the antenna fasteners). Any words of
>wisdom here? The antennas are the standard store bought COMANT bent whips.
>Thanks.
Welcome to the club. When somebody decides to design a new airplane,
they start with aero and power plant guys. Then come the structures
and processes folks. After awhile the systems folks put in fuel,
hydraulics and flight controls. When the 'airplane' is done, some
guy with radios, cabin entertainment systems, etc is told, "Okay,
you can have whatever space is left over . . . but don't CHANGE
anything."
This approach to an HF antenna installation (without CHANGING
anything) has resulted in a situation where other equipment items
inside the all metal airplane are suffering huge interfering
energies from the HF transmitter. Had the structures and processes
guys been involved since day-one to make the metal serve as both
airplane and antenna, we'd have several $millions$ still in the
corporate pockets instead of blowing that cash on band-aid
fixes to delivered aircraft.
Now, on a much smaller scale, you're presented with the same
kind of problem. The laws of physics are immutable. The primary,
long term, gas-tight connections between your antenna base and
airframe happen right under the head and nut of the fasteners.
If you need a doubler, then it needs to be well bonded
to the airframe . . . and that means rivets or high pressure
joints between ground conductors. If you choose not to
rivet the doubler, you need to clean 2 extra surfaces before
installation. See:
http://www.aeroelectric.com/Pictures/Antenna/Antenna_Installation.gif
If the doubler is riveted, then surfaces between doubler
and skin can be left as-manufactured but it wouldn't hurt
to clean these too. I'd pitch the cork gasket and go for a
thin bead of moisture sealant around outside edge of antenna
base that extrudes out to zero-thickness at time of
installation. PRESSURE and CLEANLINESS around the immediate
circumference of the mounting screws is where it all happens.
Quote: | Bob,
Speaking of the magic (grounding the base) - looking at the
Antenna_Installation.gif ,
I have seen toothed lock washers used between the doubler plate and skin.
This was on a Cessna. The doubler plate was not riveted to the skin (it
came with with the antenna replacement kit). The lock washer assured better
el contact (grounding). They used externally toothed lock washers, as per
attached. Maybe a better idea would be to use the external-internal toothed
type washers (also attached). Opinions?
|
We're really slice'n and dice'n mouse hairs here. Obviously
the goal is to get a low ohms connection between the antenna
base and the skin that is as good 10 years from now as it is
the day we bolt it on. This comes down to a few simple-ideas:
(1) pressure high enough to bring two clean surfaces into intimate
gas tight contact with each other and (2) exclusion of environmental
effects that include (a) contaminants and (b) loosening that work
against condition (1).
Some designers embrace the idea that the toothed lockwashers
provide a multitude of very high pressure points . . . even to
the point of upsetting metal at the points of contact to achieve
(1). My concerns are that a toothed washer is a spacer between
the two surfaces that may contribute to initial joint quality (1)
but leaves the gap "open" for ingress of (a).
In all of our bonding specs at RAC, the use of lockwashers is
never suggested. Self locking all metal nuts are the preferred
anti-loosening technology. In the sketch I published, 99% of the
magic needs to happen in the area just around the screw hole and
between skin and antenna base. All other "prepared" areas add
only marginally to the quality of the joint.
Obviously, the "99% conductivity area" is of very small gap and
the only thing one might add is sealant or anti-moisture guckum (Like
silocone grease) to fill the tiny void around the periphery
of the 99% area to prevent entry of oxidizing agents. Beyond
that, maintainance of pressure over time is enhanced by use
of largest practical hardware torqued to upper limits and
secured with some form of locking technology . . . all metal
locknuts being the technology of choice.
When we were selling contactors with treaded studs for fat wires,
the split-ring, steel washers supplied were discarded and replaced with
internal tooth, phosphor bronze lockwashers. The supplied steel
nuts were replaced with brass. Again, the lion's share of conductive
magic happens were the terminal comes down against the bottom nut.
The lockwasher and nut on top contributes to conductivity but
only a tiny fraction of the total.
Bob. . .
| - The Matronics AeroElectric-List Email Forum - | | Use the List Feature Navigator to browse the many List utilities available such as the Email Subscriptions page, Archive Search & Download, 7-Day Browse, Chat, FAQ, Photoshare, and much more:
http://www.matronics.com/Navigator?AeroElectric-List |
|
|
|
Back to top |
|
 |
gommone7(at)bellsouth.net Guest
|
Posted: Tue Oct 03, 2006 9:58 am Post subject: vhf antennas |
|
|
Ok, thats made everybody against the manufacturers,I will follow the mass.
Thanks
Quote: |
From: "Robert L. Nuckolls, III" <nuckollsr(at)cox.net>
Date: 2006/10/03 Tue PM 01:08:28 EDT
To: aeroelectric-list(at)matronics.com
Subject: Re: vhf antennas
At 12:33 PM 10/3/2006 -0400, you wrote:
>
>
>Hi ,I'm building an rv10,and I have contradictories informations about how
>install the antennas,the counselor and a couple of "masters" say clean the
>metal from any paint and install the antenna,but the manufacturer send it
>with a cork gasket(one of the best insulation ),to install .
>any logical for this.
>Thanks.
>Hugo
See:
http://www.aeroelectric.com/Pictures/Antenna/Antenna_Installation.gif
From some earlier posts:
>A while back you had some words of wisdom for a person who'd asked about
>getting enough metal to metal contact for ground plane purposes with his
>comm antenna. You mentioned to him that riveting his doubler plates to the
>skin would provide plenty of contact when paint and other debris was
>squeezed out during the riveting process. I have a little different twist
>on this question. I made doubler plates to go inside the fuselage but don't
>really want to rivet them on. The number of fasteners that hold the
>antennas to the airplane will hold doublers to the skin and I don't see a
>need to rivet the doublers on. This however, could cause trouble. Since
>I've already primed the inside of the aluminum fuselage skin, would like to
>prime the doublers so they don't corrode when water gets between them and
>the fuselage skin and don't want to remove the primer from the skin......I
>fear I will have insufficient connection to get good ground plane action.
>The comm antennas come with a cork gasket that's supposed to go between the
>outside skin and the antenna so that limits ground plane connection on the
>outside skin (presently bare aluminum). Am I gonna have to bite the bullet
>and rivet the doublers to get some connection or ????(the doublers have
>nutplates riveted to them to accept the antenna fasteners). Any words of
>wisdom here? The antennas are the standard store bought COMANT bent whips.
>Thanks.
Welcome to the club. When somebody decides to design a new airplane,
they start with aero and power plant guys. Then come the structures
and processes folks. After awhile the systems folks put in fuel,
hydraulics and flight controls. When the 'airplane' is done, some
guy with radios, cabin entertainment systems, etc is told, "Okay,
you can have whatever space is left over . . . but don't CHANGE
anything."
This approach to an HF antenna installation (without CHANGING
anything) has resulted in a situation where other equipment items
inside the all metal airplane are suffering huge interfering
energies from the HF transmitter. Had the structures and processes
guys been involved since day-one to make the metal serve as both
airplane and antenna, we'd have several $millions$ still in the
corporate pockets instead of blowing that cash on band-aid
fixes to delivered aircraft.
Now, on a much smaller scale, you're presented with the same
kind of problem. The laws of physics are immutable. The primary,
long term, gas-tight connections between your antenna base and
airframe happen right under the head and nut of the fasteners.
If you need a doubler, then it needs to be well bonded
to the airframe . . . and that means rivets or high pressure
joints between ground conductors. If you choose not to
rivet the doubler, you need to clean 2 extra surfaces before
installation. See:
http://www.aeroelectric.com/Pictures/Antenna/Antenna_Installation.gif
If the doubler is riveted, then surfaces between doubler
and skin can be left as-manufactured but it wouldn't hurt
to clean these too. I'd pitch the cork gasket and go for a
thin bead of moisture sealant around outside edge of antenna
base that extrudes out to zero-thickness at time of
installation. PRESSURE and CLEANLINESS around the immediate
circumference of the mounting screws is where it all happens.
>Bob,
>Speaking of the magic (grounding the base) - looking at the
>Antenna_Installation.gif ,
>I have seen toothed lock washers used between the doubler plate and skin.
>This was on a Cessna. The doubler plate was not riveted to the skin (it
>came with with the antenna replacement kit). The lock washer assured better
>el contact (grounding). They used externally toothed lock washers, as per
>attached. Maybe a better idea would be to use the external-internal toothed
>type washers (also attached). Opinions?
We're really slice'n and dice'n mouse hairs here. Obviously
the goal is to get a low ohms connection between the antenna
base and the skin that is as good 10 years from now as it is
the day we bolt it on. This comes down to a few simple-ideas:
(1) pressure high enough to bring two clean surfaces into intimate
gas tight contact with each other and (2) exclusion of environmental
effects that include (a) contaminants and (b) loosening that work
against condition (1).
Some designers embrace the idea that the toothed lockwashers
provide a multitude of very high pressure points . . . even to
the point of upsetting metal at the points of contact to achieve
(1). My concerns are that a toothed washer is a spacer between
the two surfaces that may contribute to initial joint quality (1)
but leaves the gap "open" for ingress of (a).
In all of our bonding specs at RAC, the use of lockwashers is
never suggested. Self locking all metal nuts are the preferred
anti-loosening technology. In the sketch I published, 99% of the
magic needs to happen in the area just around the screw hole and
between skin and antenna base. All other "prepared" areas add
only marginally to the quality of the joint.
Obviously, the "99% conductivity area" is of very small gap and
the only thing one might add is sealant or anti-moisture guckum (Like
silocone grease) to fill the tiny void around the periphery
of the 99% area to prevent entry of oxidizing agents. Beyond
that, maintainance of pressure over time is enhanced by use
of largest practical hardware torqued to upper limits and
secured with some form of locking technology . . . all metal
locknuts being the technology of choice.
When we were selling contactors with treaded studs for fat wires,
the split-ring, steel washers supplied were discarded and replaced with
internal tooth, phosphor bronze lockwashers. The supplied steel
nuts were replaced with brass. Again, the lion's share of conductive
magic happens were the terminal comes down against the bottom nut.
The lockwasher and nut on top contributes to conductivity but
only a tiny fraction of the total.
Bob. . .
|
| - The Matronics AeroElectric-List Email Forum - | | Use the List Feature Navigator to browse the many List utilities available such as the Email Subscriptions page, Archive Search & Download, 7-Day Browse, Chat, FAQ, Photoshare, and much more:
http://www.matronics.com/Navigator?AeroElectric-List |
|
|
|
Back to top |
|
 |
|
|
You cannot post new topics in this forum You cannot reply to topics in this forum You cannot edit your posts in this forum You cannot delete your posts in this forum You cannot vote in polls in this forum You cannot attach files in this forum You can download files in this forum
|
Powered by phpBB © 2001, 2005 phpBB Group
|