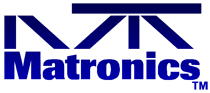 |
Matronics Email Lists Web Forum Interface to the Matronics Email Lists
|
View previous topic :: View next topic |
Author |
Message |
italianjon
Joined: 05 Aug 2015 Posts: 68
|
Posted: Fri Mar 25, 2016 7:06 am Post subject: Arplast PV50 - Help with Vibration Data |
|
|
Dear All,
I need some help in understanding the information I have gathered on the diagnostics of my propeller.
I used the Smart Avionics PB-3, the configuration for the setup is illustrated in the diagram. The PB-3 was mounted on the port side of the manifold and the pick up reflective strip was mounted on blade 3. The red block shows the PB-3 vibration sensor and the blue line highlights the x-axis orientation.
Forgive the handwriting, I did it with a mouse
Ignore the axis in grey. I have used an illustration from the Rotax Installation manual to give context to my diagram, and are not used for my purposes.
Point 1 is my starting reference.
Point 2 had 1 washer (ca. 4g.) removed from blade 3.
Point 3 had the washer returned to blade 3, and 1 washer from blade 2 to blade 1.
Point 4 had a washer from blade 1 moved to blade 3
Point 5 had 2 washers removed and moved 1 to blade 1 and 1 to blade 2.
In total blade 2 ended up 3 washer down on the start, blade 3 ended up 2 washers up on the start and blade 1 ended up 1 washer up on the start.
As far as I understand the PB-3 0º is the alignment in the X-axis, when is X-axis mode on the PB-3 app. Plus it registers the out of balance when the force pulls it in the X-direction. Therefore the propeller has to rotate between the 225º and the 284º for the out of balance to be register (Very simplistically speaking).
From my first diagram, and given 120º between blades, then blade 2 sits at 240º… or basically where I understand the imbalance to be if I have interpreted my data correctly.
With so much weight removed from the blade 2 I would have expected the imbalance to move inwards, but instead it remains in more or less the same spot. Leading me to conclude that a “bigger” effect than a mass imbalance is at play.
Blade 2 is also the one that I previously mentioned, in another post as having more play than the other blades.
I know the Arplast PV50 has play in the blades when it is at rest. This time I attempted to measure the at rest play. Blades 1 and 3 are fairly consistent with each other and approximately 1º of play. Blade 2 has approximately 4º.
I think what I am looking for, and the reason for this post, is for someone else to think about my workings to sanity check if I have missed anything; or also to check the conclusion is genuine and I am not just “looking for evidence of blade 2 because that is my apparent problem”.
Thanks all
Jon
| - The Matronics Europa-List Email Forum - | | Use the List Feature Navigator to browse the many List utilities available such as the Email Subscriptions page, Archive Search & Download, 7-Day Browse, Chat, FAQ, Photoshare, and much more:
http://www.matronics.com/Navigator?Europa-List |
|
Description: |
|
Filesize: |
52.53 KB |
Viewed: |
3373 Time(s) |
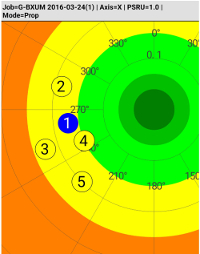
|
Description: |
|
Filesize: |
38.34 KB |
Viewed: |
3373 Time(s) |
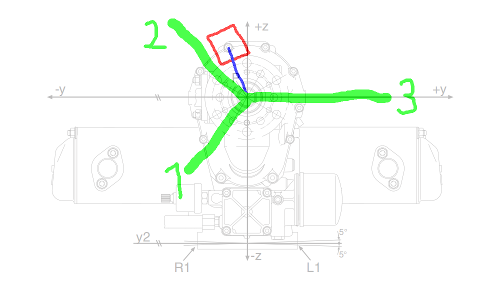
|
Description: |
Text results of captured points |
|
Filesize: |
11.65 KB |
Viewed: |
3373 Time(s) |
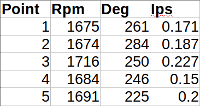
|
|
|
Back to top |
|
 |
grahamsingleton(at)btinte Guest
|
Posted: Fri Mar 25, 2016 9:13 am Post subject: Arplast PV50 - Help with Vibration Data |
|
|
Jon
First thing I used to do was check each blade statically on the bench (prop not assembled) Jerry Davis used to offer a description of how to do this, basically mock up a wood support for the blade, the fulcrum at one end represents the centre of the prop. (I knocked in 2 nails on a line at right angles to the blade span) The blade is then set on the rig so that it's root end is at the equivalent distance from the centre of the assembled prop (you need to measure this carefully). A small block on the rig near the fulcrum gives a way to butt the prop against at it's correct spanwise position.
A third nail roughly 2/3 of blade span knocked through the rig acts as the datum.
Now measure the weight of each blade at this datum point when placed on the rig. This weight will be proportional to the moment of the blade and all three need to be equal. Use an accurate digital balance.
It is not satisfactory to simply compare the actual weight of each blade. The moment, which is what's important, can be different even if weight is equal.
Arplast used to adjust the moment with lead shot dropped into a spanwise hole down the centre of the blades.
You should find it is about 8 or 9 inches deep.
Theoretically it should be possible to achieve good balance this way without running the engine but there are more than enough variables affecting dynamic balance, as you have not doubt realised.
Graham.
On Friday, 25 March 2016, 15:09, italianjon <jon.catilli(at)gmail.com> wrote:
--> Europa-List message posted by: "italianjon" <jon.catilli(at)gmail.com (jon.catilli(at)gmail.com)>
Dear All,
I need some help in understanding the information I have gathered on the diagnostics of my propeller.
I used the Smart Avionics PB-3, the configuration for the setup is illustrated in the diagram. The PB-3 was mounted on the port side of the manifold and the pick up reflective strip was mounted on blade 3. The red block shows the PB-3 vibration sensor and the blue line highlights the x-axis orientation.
Forgive the handwriting, I did it with a mouse
Ignore the axis in grey. I have used an illustration from the Rotax Installation manual to give context to my diagram, and are not used for my purposes.
Point 1 is my starting reference.
Point 2 had 1 washer (ca. 4g.) removed from blade 3.
Point 3 had the washer returned to blade 3, and 1 washer from blade 2 to blade 1.
Point 4 had a washer from blade 1 moved to blade 3
Point 5 had 2 washers removed and moved 1 to blade 1 and 1 to blade 2.
In total blade 2 ended up 3 washer down on the start, blade 3 ended up 2 washers up on the start and blade 1 ended up 1 washer up on the start.
As far as I understand the PB-3 0º is the alignment in the X-axis, when is X-axis mode on the PB-3 app. Plus it registers the out of balance when the force pulls it in the X-direction. Therefore the propeller has to rotate between the 225º and the 284º for the out of balance to be register (Very simplistically speaking).
Quote: | From my first diagram, and given 120º between blades, then blade 2 sits at 240º… or basically where I understand the imbalance to be if I have interpreted my data correctly.
|
With so much weight removed from the blade 2 I would have expected the imbalance to move inwards, but instead it remains in more or less the same spot. Leading me to conclude that a “bigger†effect than a mass imbalance is at play.
Blade 2 is also the one that I previously mentioned, in another post as having more play than the other blades.
I know the Arplast PV50 has play in the blades when it is at rest. This time I attempted to measure the at rest play. Blades 1 and 3 are fairly consistent with each other and approximately 1º of play. Blade 2 has approximately 4º.
I think what I am looking for, and the reason for this post, is for someone else to think about my workings to sanity check if I have missed anything; or also to check the conclusion is genuine and I am not just “looking for evidence of blade 2 because that is my apparent problemâ€.
Thanks all
Jon
Read this topic online here:
http://forums.matronics.com/viewtopic.php?p=454127#454127
Attachments:
http://forums.matronics.com//files/g_bxum_2016_03_241_polar_chart_20160325130741_984.jpg
http://forums.matronics.com//files/propeller_194.png
http://forums.matronics.com//files/results_105.pn &nbs//www.matronics.com/Navigator?Europa-List" target="_blank">http://www.mat= --> <a href="http://www.matronics.com/contribution" target=====
| - The Matronics Europa-List Email Forum - | | Use the List Feature Navigator to browse the many List utilities available such as the Email Subscriptions page, Archive Search & Download, 7-Day Browse, Chat, FAQ, Photoshare, and much more:
http://www.matronics.com/Navigator?Europa-List |
|
|
|
Back to top |
|
 |
italianjon
Joined: 05 Aug 2015 Posts: 68
|
Posted: Sat Mar 26, 2016 5:06 am Post subject: Re: Arplast PV50 - Help with Vibration Data |
|
|
Hi Graham,
Thanks for this reply. I will try that next weekend.
I tried searching for anything online from Jerry Davies, and couldn't find anything with the details. However your description is easy to follow. I have two questions:-
1) On the Arplast there is the mass-balance arm, sleeve, bearing and alignment dog - should I statically balance with these items on or off? I am assuming off.
2) I'm a little confused by your comment about the mass being the same. I have understood this to be the mass of the blade itself, not the reading on the scales. If the nail 2/3rds along the blade length was in the same position on each blade, then it should show the same reading, right? Or have I misunderstood something.
Best regards
Jon
| - The Matronics Europa-List Email Forum - | | Use the List Feature Navigator to browse the many List utilities available such as the Email Subscriptions page, Archive Search & Download, 7-Day Browse, Chat, FAQ, Photoshare, and much more:
http://www.matronics.com/Navigator?Europa-List |
|
|
|
Back to top |
|
 |
|
|
You cannot post new topics in this forum You cannot reply to topics in this forum You cannot edit your posts in this forum You cannot delete your posts in this forum You cannot vote in polls in this forum You cannot attach files in this forum You can download files in this forum
|
Powered by phpBB © 2001, 2005 phpBB Group
|