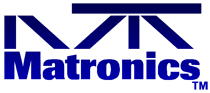 |
Matronics Email Lists Web Forum Interface to the Matronics Email Lists
|
View previous topic :: View next topic |
Author |
Message |
victorbravo(at)sbcglobal. Guest
|
Posted: Fri May 06, 2016 2:15 pm Post subject: Kolb Firestar Progress report |
|
|
I was out last night working on the Firestar project, and wanted to report my progress.
As of this writing, I have completed two horizontal stabilizers, and have completed just about everything on the vertical fin assembly. The only thing left on that is to drill the hole for the lower tail brace wire bolt, but I'm sure this can wait until I have the tail installed on the fuselage tube and can line everything up better.
I started to lay out the rudder last night, cut the main upright tube, and started laying out the gussets. After looking closely at the standard rudder and elevator, I decided to make a slight change in the method of attaching the parts together. To make a slightly more robust and more rigid set of controls I will be using the same style of thin "tube and gusset" construction as the stabilizer. This will allow two rivets at each intersection instead of one, and provide a small triangular gusset to stiffen and brace the intersection. The extra weight and "control surface balance" will very likely be negligible.
I had made a decision to not attempt to build a showplane, and not attempt to make everything perfect. An engineer friend of mine has a saying... "perfection is the enemy of completion" So my efforts will be used to build a safe, solid, but not show quality aircraft. Since this one will be used as a dirt and sand airplane fairly often, any extra effort on a shiny finish will have been wasted. This whole thing may be left Stits silver anyway, to make dings, repairs and bullhead thorn repairs easier.
As an esoteric note, I just realized that the serial number on my fuselage (F-1203) is different than the number in the instruction manual I got (690-something). Can anyone tell me if there were any changes to the manual that would affect this? How can I verify that I have the latest and most applicable instruction manual and/or plans?
Bill Berle
www.ezflaphandle.com - safety & performance upgrade for light aircraft
www.grantstar.net      - winning proposals for non-profit and for-profit entities
--------------------------------------------
On Fri, 5/6/16, Bill Berle <victorbravo(at)sbcglobal.net> wrote:
Subject: Re: Re: ground aerobatics...
To: kolb-list(at)matronics.com
Date: Friday, May 6, 2016, 11:16 AM
Bill Berle <victorbravo(at)sbcglobal.net>
By normal flight training standards, based on very old
memories, a steep turn is one that uses a bank angleÂ
45 degrees or higher. 60 degrees is considered the "steep
turn" benchmark when you do FAA private pilot training (at
least it was in the 1970's when we had real pilot
training).
A 60 degree banked level flight turn in calm air results in
exactly a 2G load on the airframe. I'm pretty sure that the
Kolb was designed to withstand far far more than 2G. (if
not, I have a Firestar kit for sale cheap).
However, bank angle alone does not determine G forces. A 60
degree banked coordinated level flight turn will give you
2G. But a "wingover" maneuver is not a level turn, and most
of the time the high bank angle comes at a time when the
airplane is "unloaded". So the reality is that the wingover
maneuver shown in the video could easily have been at
ZERO-G. (I do zero-G wingovers all the time in an old Cessna
172 and it puts zero stress on the airframe)
You can do a simple "aileron roll" that puts no stress
whatsoever on the airplane for 3/4 of the maneuver, and only
1.3 or 1.4G on the airplane during the other 1/4 of the
maneuver. There is a very famous incident of a Boeing test
pilot named Tex Johnson doing a full 360 degree aileron roll
in the first prototype 707, with a bunch of news reporters
on board, and it didn't even ruffle anyone's hair on board
the airplane. You can find the video on youtube I'm sure.
The FAA definition of "Aerobatics" is an excursion from
level flight of more than 30 degrees of pitch and 60 degrees
of bank. But "aerobatic" maneuvers can easily be done that
exceed these numbers without putting any abnormal stress or
loads on the airplane... and are in reality not "dangerous"
in any way. What gets dangerous is when the pilot misjudges
or mishandles the recovery from these maneuvers, and can
easily accidentally exceed the speed or G load limits that
the airframe can handle. THAT is the dangerous part, and
THAT is why any pilot with a brain in his head will get
aerobatic or "upset recovery" training before playing around
with these kinds of maneuvers.
The Kolb was of course not designed for aerobatics. It does
not make any sense to do intentional aerobatics in a Kolb.
As mentioned by others, if you are going to go out and do
hard aerobatics on purpose then go rent a Citabria.
Bill Berle
www.ezflaphandle.com - safety & performance upgrade
for light aircraft
www.grantstar.net      - winning proposals for
non-profit and for-profit entities
--------------------------------------------
On Fri, 5/6/16, flywithme <constrjh(at)pldi.net>
wrote:
Subject: Re: ground aerobatics...
To: kolb-list(at)matronics.com
Date: Friday, May 6, 2016, 9:48 AM
"flywithme" <constrjh(at)pldi.net>
i see in some posts reference to the first pilot making a
steep banking turn as being a dangerous maneuver in a
kolb.
is this really such a dangerous maneuver
Read this topic online here:
http://forums.matronics.com/viewtopic.php?p=455928#455928
Forum -
   - MATRONICS WEB FORUMS -
MATRONICS LIST WIKI -
List Contribution Web Site -
       -Matt
Dralle, List Admin.
Forum -
   - MATRONICS WEB FORUMS -
MATRONICS LIST WIKI -
List Contribution Web Site -
       -Matt
Dralle, List Admin.
| - The Matronics Kolb-List Email Forum - | | Use the List Feature Navigator to browse the many List utilities available such as the Email Subscriptions page, Archive Search & Download, 7-Day Browse, Chat, FAQ, Photoshare, and much more:
http://www.matronics.com/Navigator?Kolb-List |
|
|
|
Back to top |
|
 |
neilsenrm(at)gmail.com Guest
|
Posted: Sat May 07, 2016 5:22 am Post subject: Kolb Firestar Progress report |
|
|
Bill
Control surfaces on Kolbs can flutter if made heavier than designed.
Rick Neilsen
Redrive VW Powered MKIII
Sent from my iPhone
Quote: | On May 6, 2016, at 5:15 PM, Bill Berle <victorbravo(at)sbcglobal.net> wrote:
I was out last night working on the Firestar project, and wanted to report my progress.
As of this writing, I have completed two horizontal stabilizers, and have completed just about everything on the vertical fin assembly. The only thing left on that is to drill the hole for the lower tail brace wire bolt, but I'm sure this can wait until I have the tail installed on the fuselage tube and can line everything up better.
I started to lay out the rudder last night, cut the main upright tube, and started laying out the gussets. After looking closely at the standard rudder and elevator, I decided to make a slight change in the method of attaching the parts together. To make a slightly more robust and more rigid set of controls I will be using the same style of thin "tube and gusset" construction as the stabilizer. This will allow two rivets at each intersection instead of one, and provide a small triangular gusset to stiffen and brace the intersection. The extra weight and "control surface balance" will very likely be negligible.
I had made a decision to not attempt to build a showplane, and not attempt to make everything perfect. An engineer friend of mine has a saying... "perfection is the enemy of completion" So my efforts will be used to build a safe, solid, but not show quality aircraft. Since this one will be used as a dirt and sand airplane fairly often, any extra effort on a shiny finish will have been wasted. This whole thing may be left Stits silver anyway, to make dings, repairs and bullhead thorn repairs easier.
As an esoteric note, I just realized that the serial number on my fuselage (F-1203) is different than the number in the instruction manual I got (690-something). Can anyone tell me if there were any changes to the manual that would affect this? How can I verify that I have the latest and most applicable instruction manual and/or plans?
Bill Berle
www.ezflaphandle.com - safety & performance upgrade for light aircraft
www.grantstar.net - winning proposals for non-profit and for-profit entities
--------------------------------------------
On Fri, 5/6/16, Bill Berle <victorbravo(at)sbcglobal.net> wrote:
Subject: Re: Re: ground aerobatics...
To: kolb-list(at)matronics.com
Date: Friday, May 6, 2016, 11:16 AM
Bill Berle <victorbravo(at)sbcglobal.net>
By normal flight training standards, based on very old
memories, a steep turn is one that uses a bank angle
45 degrees or higher. 60 degrees is considered the "steep
turn" benchmark when you do FAA private pilot training (at
least it was in the 1970's when we had real pilot
training).
A 60 degree banked level flight turn in calm air results in
exactly a 2G load on the airframe. I'm pretty sure that the
Kolb was designed to withstand far far more than 2G. (if
not, I have a Firestar kit for sale cheap).
However, bank angle alone does not determine G forces. A 60
degree banked coordinated level flight turn will give you
2G. But a "wingover" maneuver is not a level turn, and most
of the time the high bank angle comes at a time when the
airplane is "unloaded". So the reality is that the wingover
maneuver shown in the video could easily have been at
ZERO-G. (I do zero-G wingovers all the time in an old Cessna
172 and it puts zero stress on the airframe)
You can do a simple "aileron roll" that puts no stress
whatsoever on the airplane for 3/4 of the maneuver, and only
1.3 or 1.4G on the airplane during the other 1/4 of the
maneuver. There is a very famous incident of a Boeing test
pilot named Tex Johnson doing a full 360 degree aileron roll
in the first prototype 707, with a bunch of news reporters
on board, and it didn't even ruffle anyone's hair on board
the airplane. You can find the video on youtube I'm sure.
The FAA definition of "Aerobatics" is an excursion from
level flight of more than 30 degrees of pitch and 60 degrees
of bank. But "aerobatic" maneuvers can easily be done that
exceed these numbers without putting any abnormal stress or
loads on the airplane... and are in reality not "dangerous"
in any way. What gets dangerous is when the pilot misjudges
or mishandles the recovery from these maneuvers, and can
easily accidentally exceed the speed or G load limits that
the airframe can handle. THAT is the dangerous part, and
THAT is why any pilot with a brain in his head will get
aerobatic or "upset recovery" training before playing around
with these kinds of maneuvers.
The Kolb was of course not designed for aerobatics. It does
not make any sense to do intentional aerobatics in a Kolb.
As mentioned by others, if you are going to go out and do
hard aerobatics on purpose then go rent a Citabria.
Bill Berle
www.ezflaphandle.com - safety & performance upgrade
for light aircraft
www.grantstar.net - winning proposals for
non-profit and for-profit entities
--------------------------------------------
On Fri, 5/6/16, flywithme <constrjh(at)pldi.net>
wrote:
Subject: Re: ground aerobatics...
To: kolb-list(at)matronics.com
Date: Friday, May 6, 2016, 9:48 AM
"flywithme" <constrjh(at)pldi.net>
i see in some posts reference to the first pilot making a
steep banking turn as being a dangerous maneuver in a
kolb.
is this really such a dangerous maneuver
Read this topic online here:
http://forums.matronics.com/viewtopic.php?p=455928#455928
Forum -
- MATRONICS WEB FORUMS -
MATRONICS LIST WIKI -
List Contribution Web Site -
-Matt
Dralle, List Admin.
Forum -
- MATRONICS WEB FORUMS -
MATRONICS LIST WIKI -
List Contribution Web Site -
-Matt
Dralle, List Admin.
|
| - The Matronics Kolb-List Email Forum - | | Use the List Feature Navigator to browse the many List utilities available such as the Email Subscriptions page, Archive Search & Download, 7-Day Browse, Chat, FAQ, Photoshare, and much more:
http://www.matronics.com/Navigator?Kolb-List |
|
|
|
Back to top |
|
 |
victorbravo(at)sbcglobal. Guest
|
Posted: Sun May 08, 2016 12:11 am Post subject: Kolb Firestar Progress report |
|
|
Just came back from building 80% of the rudder.
Thank you Richard, I do understand that flutter can happen on control surfaces. If it becomes necessary I will put a balance weight on but hopefully that will not be necessary. The Cub, Taylorcraft, Champ, etc. have welded steel rudders and elevators that are much more "out of balance", and their flutter speeds are higher. My goal was to make the controls stiffer and more robust, which also helps prevent flutter.
I will make a better analysis of how much weight gain there actually was; I believe it will be very little. But the short version is that I used .032 triangular gussets, about 1.5 inches long and wide at the leading and trailing edge intersections, rather than riveting the "rib" tube directly to the leading and trailing edge with one rivet. Using the gussets allowed me to use two rivets, and not have to squash the small tube. Using the gussets at the trailing edge also allowed me to have a far better attachment where the ribs go all the way to the trailing edge, instead of joining the two rib tubes with only one rivet.
I also "curled" the gussets around the tubes to create less protrusion into the fabric. This was more than cosmetic... it allows you to have the full, correct, safe "edge distance" between the hole and the edge of the part. The stock Kolb drawings have you building parts that simply do not meet the time-honored "2D" minimum edge distance (AC 43-13 and many other references). I know that the Kolb factory did not do this by mistake, they were trying to prevent the edges of the gussets from protruding as much. But the price for this is that they gave up a very long-standing safety margin that has been built into sheet metal and rivet structures since the 1920's.
I believe that there will be something like 3-4 inches of etra 5/16 x .035 tube for each "rib" station. There will also be the extra weight of the gussets, and a handful of additional rivets. Definitely more material, but hopefully still down in the "negligible" range.
I also made a cosmetic, strutcural and serodynamic improvement at the trailing edge. To keep the trailing edge of the rudder as thin as possible, I flightly offset the two "rib" tubes at the trailing edge so the ribs would be flush with the trailing edge tube.
Bill Berle
www.ezflaphandle.com - safety & performance upgrade for light aircraft
www.grantstar.net      - winning proposals for non-profit and for-profit entities
--------------------------------------------
On Sat, 5/7/16, Richard Neilsen <neilsenrm(at)gmail.com> wrote:
Subject: Re: Kolb Firestar Progress report
To: kolb-list(at)matronics.com
Date: Saturday, May 7, 2016, 6:22 AM
Richard Neilsen <neilsenrm(at)gmail.com>
Bill
Control surfaces on Kolbs can flutter if made heavier than
designed.
Rick Neilsen
Redrive VW Powered MKIII
Sent from my iPhone
> On May 6, 2016, at 5:15 PM, Bill Berle <victorbravo(at)sbcglobal.net>
wrote:
>
>
>
> I was out last night working on the Firestar project,
and wanted to report my progress.
>
> As of this writing, I have completed two horizontal
stabilizers, and have completed just about everything on the
vertical fin assembly. The only thing left on that is to
drill the hole for the lower tail brace wire bolt, but I'm
sure this can wait until I have the tail installed on the
fuselage tube and can line everything up better.
>
> I started to lay out the rudder last night, cut the
main upright tube, and started laying out the gussets. After
looking closely at the standard rudder and elevator, I
decided to make a slight change in the method of attaching
the parts together. To make a slightly more robust and more
rigid set of controls I will be using the same style of thin
"tube and gusset" construction as the stabilizer. This will
allow two rivets at each intersection instead of one, and
provide a small triangular gusset to stiffen and brace the
intersection. The extra weight and "control surface balance"
will very likely be negligible.
>
> I had made a decision to not attempt to build a
showplane, and not attempt to make everything perfect. An
engineer friend of mine has a saying... "perfection is the
enemy of completion" So my efforts will be used to build
a safe, solid, but not show quality aircraft. Since this one
will be used as a dirt and sand airplane fairly often, any
extra effort on a shiny finish will have been wasted. This
whole thing may be left Stits silver anyway, to make dings,
repairs and bullhead thorn repairs easier.
>
> As an esoteric note, I just realized that the serial
number on my fuselage (F-1203) is different than the number
in the instruction manual I got (690-something). Can anyone
tell me if there were any changes to the manual that would
affect this? How can I verify that I have the latest and
most applicable instruction manual and/or plans?
>
>
> Bill Berle
> www.ezflaphandle.com - safety & performance
upgrade for light aircraft
> www.grantstar.net   Â
   - winning proposals for non-profit and
for-profit entities
>
> --------------------------------------------
> On Fri, 5/6/16, Bill Berle <victorbravo(at)sbcglobal.net>
wrote:
>
> Subject: Re: Re: ground aerobatics...
> To: kolb-list(at)matronics.com
> Date: Friday, May 6, 2016, 11:16 AM
>
>
> Bill Berle <victorbravo(at)sbcglobal.net>
>
> By normal flight training standards, based on very old
> memories, a steep turn is one that uses a bank angle
> 45 degrees or higher. 60 degrees is considered the
"steep
> turn" benchmark when you do FAA private pilot training
(at
> least it was in the 1970's when we had real pilot
> training).
>
> A 60 degree banked level flight turn in calm air
results in
> exactly a 2G load on the airframe. I'm pretty sure that
the
> Kolb was designed to withstand far far more than 2G.
(if
> not, I have a Firestar kit for sale cheap).
>
> However, bank angle alone does not determine G forces.
A 60
> degree banked coordinated level flight turn will give
you
> 2G. But a "wingover" maneuver is not a level turn, and
most
> of the time the high bank angle comes at a time when
the
> airplane is "unloaded". So the reality is that the
wingover
> maneuver shown in the video could easily have been at
> ZERO-G. (I do zero-G wingovers all the time in an old
Cessna
> 172 and it puts zero stress on the airframe)
>
> You can do a simple "aileron roll" that puts no stress
> whatsoever on the airplane for 3/4 of the maneuver, and
only
> 1.3 or 1.4G on the airplane during the other 1/4 of
the
> maneuver. There is a very famous incident of a Boeing
test
> pilot named Tex Johnson doing a full 360 degree aileron
roll
> in the first prototype 707, with a bunch of news
reporters
> on board, and it didn't even ruffle anyone's hair on
board
> the airplane. You can find the video on youtube I'm
sure.
>
> The FAA definition of "Aerobatics" is an excursion
from
> level flight of more than 30 degrees of pitch and 60
degrees
> of bank. But "aerobatic" maneuvers can easily be done
that
> exceed these numbers without putting any abnormal
stress or
> loads on the airplane... and are in reality not
"dangerous"
> in any way. What gets dangerous is when the pilot
misjudges
> or mishandles the recovery from these maneuvers, and
can
> easily accidentally exceed the speed or G load limits
that
> the airframe can handle. THAT is the dangerous part,
and
> THAT is why any pilot with a brain in his head will
get
> aerobatic or "upset recovery" training before playing
around
> with these kinds of maneuvers.
>
> The Kolb was of course not designed for aerobatics. It
does
> not make any sense to do intentional aerobatics in a
Kolb.
> As mentioned by others, if you are going to go out and
do
> hard aerobatics on purpose then go rent a Citabria.
>
> Bill Berle
> www.ezflaphandle.com - safety & performance
upgrade
> for light aircraft
> www.grantstar.net   Â
   - winning proposals for
> non-profit and for-profit entities
>
> --------------------------------------------
> On Fri, 5/6/16, flywithme <constrjh(at)pldi.net>
> wrote:
>
>Â Subject: Re: ground aerobatics...
>Â To: kolb-list(at)matronics.com
>Â Date: Friday, May 6, 2016, 9:48 AM
>
>Â
>Â "flywithme" <constrjh(at)pldi.net>
>
>Â i see in some posts reference to the first pilot
making a
>Â steep banking turn as being a dangerous maneuver
in a
> kolb.
>Â is this really such a dangerous maneuver
>
>
>
>
>Â Read this topic online here:
>
>Â http://forums.matronics.com/viewtopic.php?p=455928#455928
>
>
>
>
>
>
>
>Â Forum -
>Â Â Â Â - MATRONICS WEB FORUMS -
>Â MATRONICS LIST WIKI -
>Â List Contribution Web Site -
>Â Â Â Â Â Â Â Â
-Matt
>Â Dralle, List Admin.
>
>
>
>
>
> Forum -
>Â Â - MATRONICS WEB FORUMS -
> MATRONICS LIST WIKI -
> List Contribution Web Site -
>Â Â Â Â Â Â
   -Matt
> Dralle, List Admin.
>
>
>
>
>
>
>
>
Forum -
   - MATRONICS WEB FORUMS -
MATRONICS LIST WIKI -
List Contribution Web Site -
       -Matt
Dralle, List Admin.
| - The Matronics Kolb-List Email Forum - | | Use the List Feature Navigator to browse the many List utilities available such as the Email Subscriptions page, Archive Search & Download, 7-Day Browse, Chat, FAQ, Photoshare, and much more:
http://www.matronics.com/Navigator?Kolb-List |
|
|
|
Back to top |
|
 |
Richard Pike
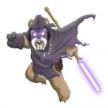
Joined: 09 Jan 2006 Posts: 1671 Location: Blountville, Tennessee
|
Posted: Sun May 08, 2016 4:16 am Post subject: Re: Kolb Firestar Progress report |
|
|
Rudder flutter on a Kolb is easy to test for: take your feet off the rudder pedals and wait. If, after a few seconds, the rudder pedals start to pulse back and forth, and the airplane starts to twitch from side to side, then you can build a counterbalance.
http://oh2fly.net/oldpoops/pg6.htm
Or else never take your feet off the pedals.
Also - recently there has been a growing trend of not snipping non-pertinent quote sections. This makes for some ridiculously long entries that do nothing to edify anybody. It is also contrary to the list guidelines:
"Remember that your post will be included for posterity in an archive
that is growing in size at an extraordinary rate. Try to be concise and
terse in your posts. Avoid overly wordy and lengthy posts and
responses.
- When responding, NEVER quote the *entire* original post in your
response. DO use lines from the original post to help "tune in" the
reader to the topic at hand, but be selective. The impact that
quoting the entire original post has on the size of the archive
can not be overstated!"
| - The Matronics Kolb-List Email Forum - | | Use the List Feature Navigator to browse the many List utilities available such as the Email Subscriptions page, Archive Search & Download, 7-Day Browse, Chat, FAQ, Photoshare, and much more:
http://www.matronics.com/Navigator?Kolb-List |
|
_________________ Richard Pike
Kolb MKIII N420P (420ldPoops)
Kingsport, TN 3TN0
Forgiving is tough, being forgiven is wonderful, and God's grace really is amazing. |
|
Back to top |
|
 |
John Hauck
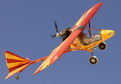
Joined: 09 Jan 2006 Posts: 4639 Location: Titus, Alabama (hauck's holler)
|
Posted: Sun May 08, 2016 5:03 am Post subject: Kolb Firestar Progress report |
|
|
Rudder flutter on a Kolb is easy to test for: take your feet off the rudder
pedals and wait. If, after a few seconds, the rudder pedals start to pulse
back and forth, and the airplane starts to twitch from side to side, then
you can build a counterbalance.
http://oh2fly.net/oldpoops/pg6.htm
Or else never take your feet off the pedals.
Richard Pike
Kolbers:
My MKIII rudder fluttered if I took my feet off the pedals or relaxed slight
foot pressure on them. So did the rudder on my Ultrastar and Firestar.
My fix, rather than add a large device on top of the rudder was the addition
of a second rudder pedal spring on each rudder pedal. Now I can fly with my
feet on the deck without fear of rudder flutter.
A cheap, simple, quick fix.
john h
MKIII
Titus, Alabama
| - The Matronics Kolb-List Email Forum - | | Use the List Feature Navigator to browse the many List utilities available such as the Email Subscriptions page, Archive Search & Download, 7-Day Browse, Chat, FAQ, Photoshare, and much more:
http://www.matronics.com/Navigator?Kolb-List |
|
_________________ John Hauck
MKIII/912ULS
hauck's holler
Titus, Alabama |
|
Back to top |
|
 |
Richard Pike
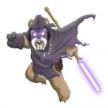
Joined: 09 Jan 2006 Posts: 1671 Location: Blountville, Tennessee
|
Posted: Sun May 08, 2016 1:09 pm Post subject: Re: Kolb Firestar Progress report |
|
|
Hi John, I forgot that. Yes, the double springs would indeed be quicker, simpler and lighter. Also, they don't give the birds a place to sit while they poop on your airplane.
But now I have a ground plane for my antenna. 
| - The Matronics Kolb-List Email Forum - | | Use the List Feature Navigator to browse the many List utilities available such as the Email Subscriptions page, Archive Search & Download, 7-Day Browse, Chat, FAQ, Photoshare, and much more:
http://www.matronics.com/Navigator?Kolb-List |
|
_________________ Richard Pike
Kolb MKIII N420P (420ldPoops)
Kingsport, TN 3TN0
Forgiving is tough, being forgiven is wonderful, and God's grace really is amazing. |
|
Back to top |
|
 |
John Hauck
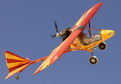
Joined: 09 Jan 2006 Posts: 4639 Location: Titus, Alabama (hauck's holler)
|
Posted: Sun May 08, 2016 3:12 pm Post subject: Kolb Firestar Progress report |
|
|
Hi John, I forgot that. Yes, the double springs would indeed be quicker,
simpler and lighter. Also, they don't give the birds a place to sit while
they poop on your airplane.
But now I have a ground plane for my antenna. [Wink]
--------
Richard Pike
The birds don't need a rudder counterbalance weight to roost and crap on my
MKIII. There is a lot of other places on and near the airplane they can
take advantage of.
I don't understand "But now I have a ground plane for my antenna. (Wink)"
john h - The clueless.
MKIII
Titus, AL
| - The Matronics Kolb-List Email Forum - | | Use the List Feature Navigator to browse the many List utilities available such as the Email Subscriptions page, Archive Search & Download, 7-Day Browse, Chat, FAQ, Photoshare, and much more:
http://www.matronics.com/Navigator?Kolb-List |
|
_________________ John Hauck
MKIII/912ULS
hauck's holler
Titus, Alabama |
|
Back to top |
|
 |
Richard Pike
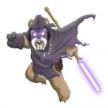
Joined: 09 Jan 2006 Posts: 1671 Location: Blountville, Tennessee
|
Posted: Mon May 09, 2016 9:38 am Post subject: Re: Kolb Firestar Progress report |
|
|
John Hauck wrote: |
<snip>
I don't understand "But now I have a ground plane for my antenna. (Wink)"
john h - The clueless.
MKIII
Titus, AL |
Clueless does not suit you well John, you are not that sort of guy - so here's a picture:
Several of us spent an afternoon a couple years ago testing various places on a Kolb for optimum antenna response. This works good on mine, ATC gives me a "5X5" from many miles away, with me using an ancient hand held. I suppose the counterbalance and top of the rudder is acting as a ground plane ahead and behind, and the brace wires on either side must do a better job than I would have expected.
| - The Matronics Kolb-List Email Forum - | | Use the List Feature Navigator to browse the many List utilities available such as the Email Subscriptions page, Archive Search & Download, 7-Day Browse, Chat, FAQ, Photoshare, and much more:
http://www.matronics.com/Navigator?Kolb-List |
|
Description: |
|
Filesize: |
205.35 KB |
Viewed: |
16555 Time(s) |
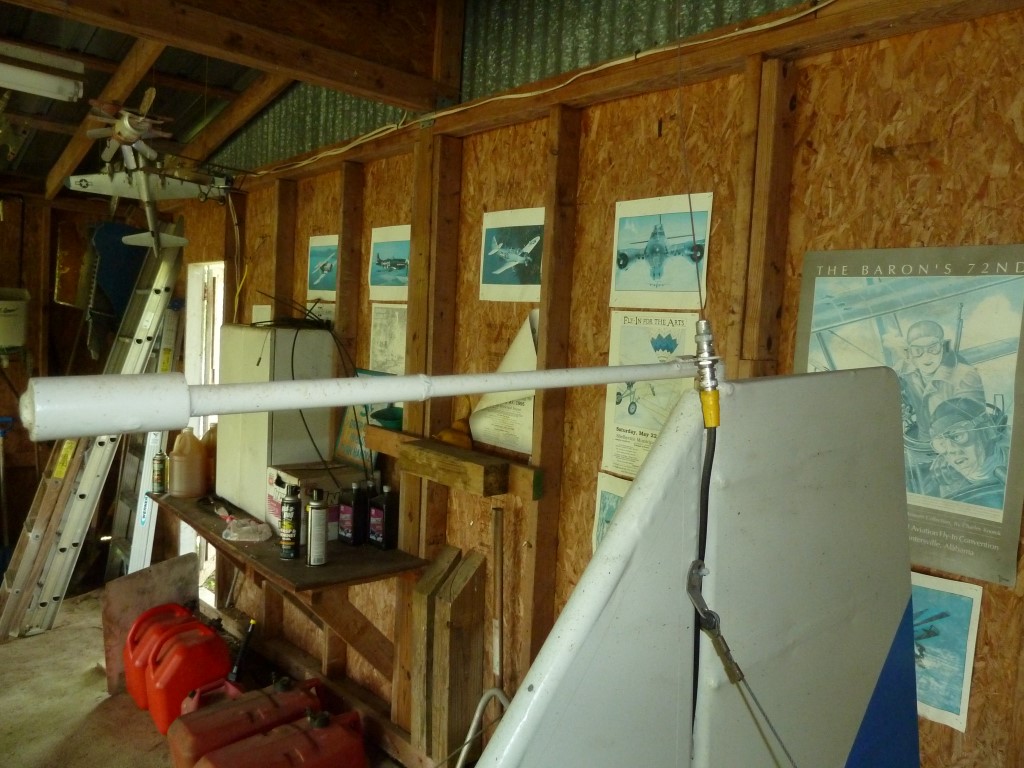
|
_________________ Richard Pike
Kolb MKIII N420P (420ldPoops)
Kingsport, TN 3TN0
Forgiving is tough, being forgiven is wonderful, and God's grace really is amazing. |
|
Back to top |
|
 |
John Hauck
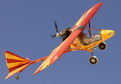
Joined: 09 Jan 2006 Posts: 4639 Location: Titus, Alabama (hauck's holler)
|
Posted: Mon May 09, 2016 12:00 pm Post subject: Kolb Firestar Progress report |
|
|
Now I remember your post. zzzzzzzzzzzzzzzzzz
Can't keep my eyes open.
I have had good luck with my ICOM A6 and 21" ss whip antenna mounted under
the nose cone. On departure from the Rock House, south of Burns Junction,
Oregon, I was sending and receiving 5X5, 85 sm east, almost to the Snake
River.
I wouldn't know what to do with a real radio.
john h
mkIII
Titus, Alabama
Several of us spent an afternoon a couple years ago testing various places
on a Kolb for optimum antenna response.
--------
Richard Pike
| - The Matronics Kolb-List Email Forum - | | Use the List Feature Navigator to browse the many List utilities available such as the Email Subscriptions page, Archive Search & Download, 7-Day Browse, Chat, FAQ, Photoshare, and much more:
http://www.matronics.com/Navigator?Kolb-List |
|
_________________ John Hauck
MKIII/912ULS
hauck's holler
Titus, Alabama |
|
Back to top |
|
 |
victorbravo(at)sbcglobal. Guest
|
Posted: Fri May 20, 2016 1:59 pm Post subject: Kolb Firestar Progress report |
|
|
Quote: | These are a few photos from the early
construction phase of the Firestar
If there is any forum rule that I am breaking or bending by
attaching these photos, please let me know. I have seen
photos attached to forum posts, but this is the first time I
have done so, so I would want to know if it is unwanted, or
problematic.
The airport bum holding the half built rudder is me. The
ribs have not all been attached to the trailing edge in this
photo, so it looks like some of them are hanging out in
space (which they are).
The other photos show the gusset method of attaching the
ribs to the leading and trailing edges.
One photo shows the fin assembly and the two stabilizers
under it. The red paint you can see at the gussets in that
photo is corrosion resistant paint that I applied, because I
used 2024 alloy instead of 6061 (had some 2024 on hand,
makes it stiffer and stronger at a critical area). I had run
out of Zinc Chromate, and had some corrosion resistant
enamel of a different color. Very hard to get Zinc Chromate
in California... the EPA guys are not happy with it !
Bill Berle
www.ezflaphandle.com - safety & performance upgrade
for light aircraft
www.grantstar.net      - winning proposals for
non-profit and for-profit entities
--------------------------------------------
On Wed, 5/18/16, Bill Berle <victorbravo(at)sbcglobal.net>
wrote:
Subject: Re: Kolb Firestar Progress report
To: "Bill Berle" <victorbravo(at)sbcglobal.net>
Date: Wednesday, May 18, 2016, 12:12 PM
Finished the rudder and started on
the elevators.
The rudder was built using two equal length 5/16" tubes at
each rib location, serving as upper and lower "structural
rib cap" members, as opposed to the half-length tubes on
the
bottom as shown on the plans. The aft (trailing edge) of
these rib tube pairs were installed "side by side", in
order
for the thickness of the trailing edge to remain
unchanged. Triangular sheet metal gussets were used to
attach these ribs to the leading and trailing edge tubes.
The small tubes were attached to the leading edge using
triangular gussets as well, providing four rivets (two in
the large tube, two in the small tube) and a structural
brace (the gusset) at this critical location.Â
The first elevator was started last night. In an attempt
to
improve the accuracy and quality of the rivet layout
WITHOUT
spending a large amount of time, I sketched out an
alignment
tool on the commuter train. This tool was fabricated from
aluminum angle in two sizes. The angle is laid down on top
of the sheet metal gusset and underlying aluminum tube
blank. Keeping the angle in contact with the (exposed) end
of the tube keeps the guide holes centered over theÂ
part of the tube that you cannot see. It also holds the
drill bit from wandering off the apex of the round tubes,
which I'm sure everyone already knows is a very
frustrating
problem. Even the "snap punch" marking points do not
always
hold the drill from wandering.
Another helpful tip I found was to use the hand de-burring
tool (the one with a pointed sharp countersink bit mounted
on a weird shaped long screwdriver handle) to make the
snap
punch mark larger before drilling. This helped quite a
bit,
at the expense of a bit of time and changing tools back
and
forth between hands.
As mentioned previously, the very slight weight increase
by
using the gussets was accepted in return for a far more
robust attachment. This particular Firestar will never be
flown as a Part 103 ultralight.
I will try to attach some photos of a few of these details
to another post..... gotta find the photos taken by my
wife's cell phone....
Bill Berle
www.ezflaphandle.com - safety & performance upgrade
for light aircraft
www.grantstar.net      - winning proposals for
non-profit and for-profit entities
|
| - The Matronics Kolb-List Email Forum - | | Use the List Feature Navigator to browse the many List utilities available such as the Email Subscriptions page, Archive Search & Download, 7-Day Browse, Chat, FAQ, Photoshare, and much more:
http://www.matronics.com/Navigator?Kolb-List |
|
Description: |
|
Filesize: |
319.69 KB |
Viewed: |
16490 Time(s) |
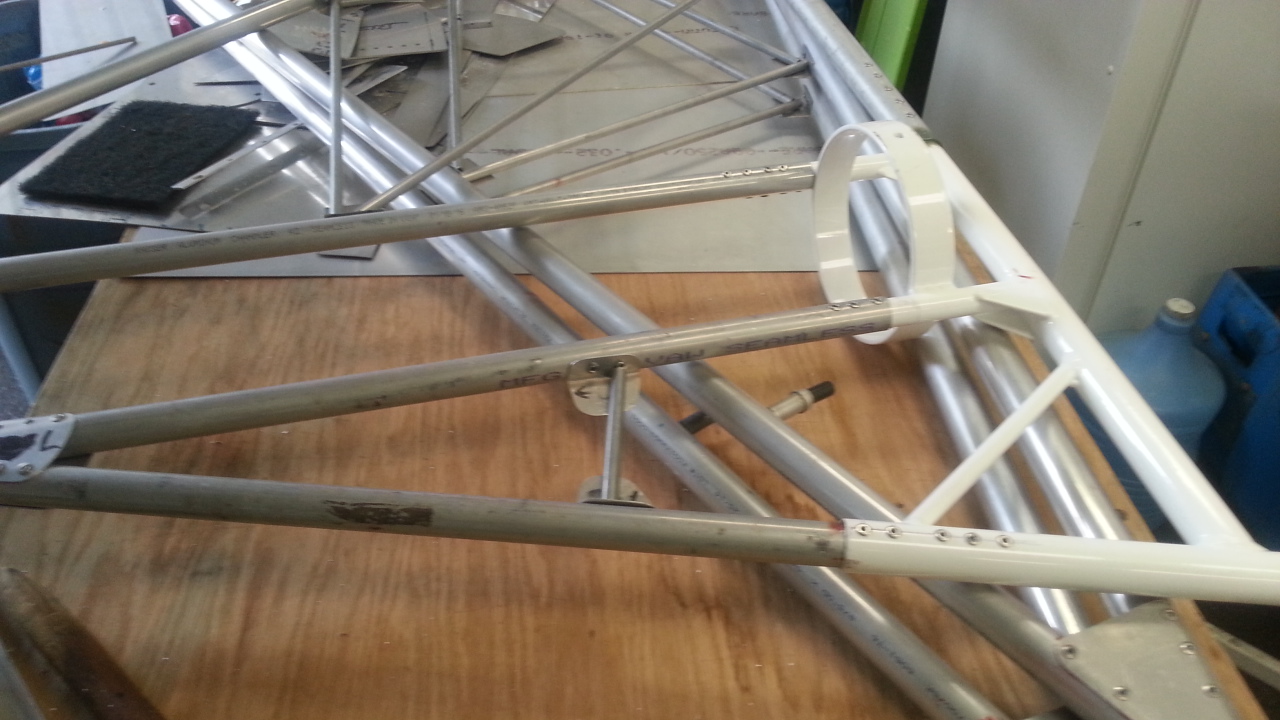
|
Description: |
|
Filesize: |
281.32 KB |
Viewed: |
16490 Time(s) |
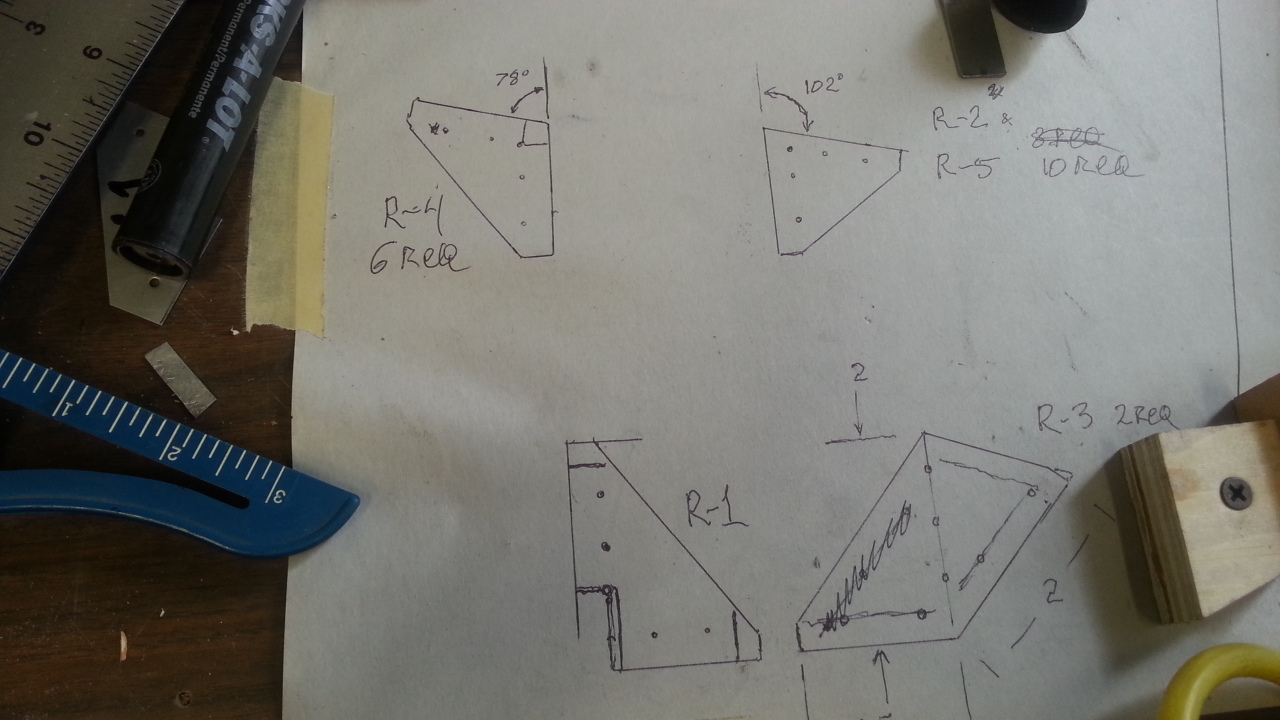
|
Description: |
|
Filesize: |
329.69 KB |
Viewed: |
16490 Time(s) |
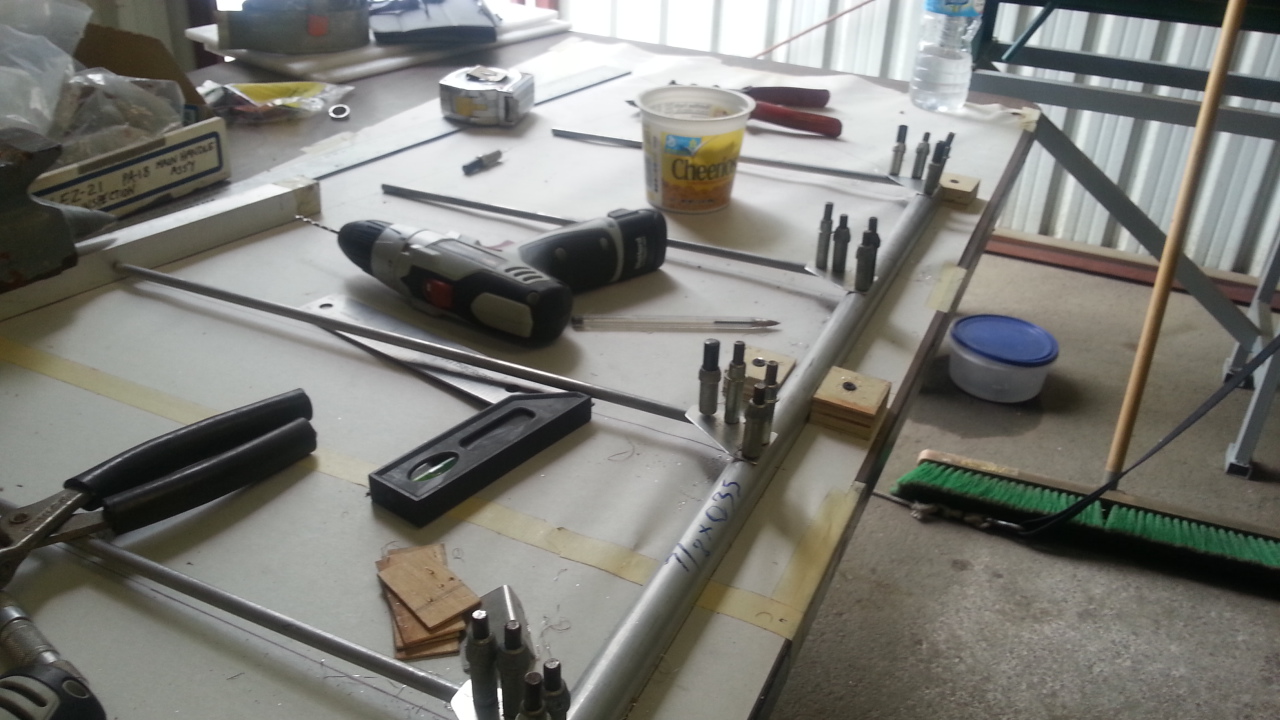
|
Description: |
|
Filesize: |
348.61 KB |
Viewed: |
16490 Time(s) |
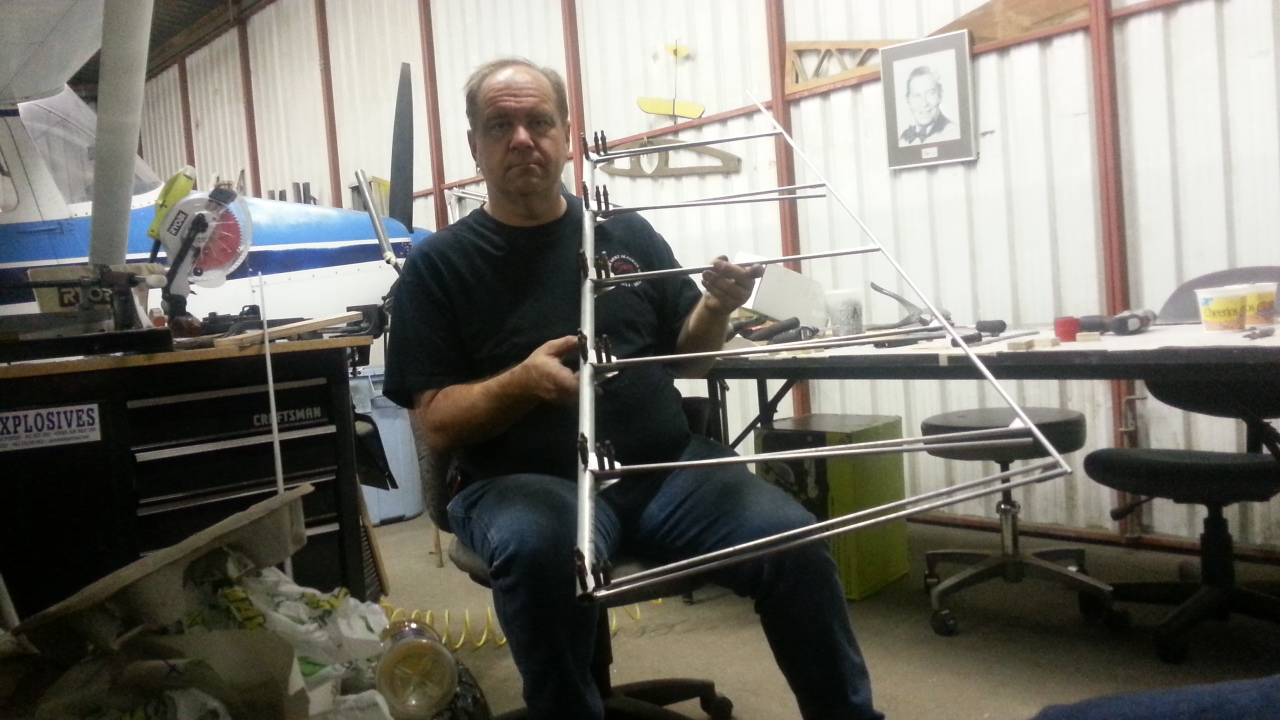
|
Description: |
|
Filesize: |
272.65 KB |
Viewed: |
16490 Time(s) |
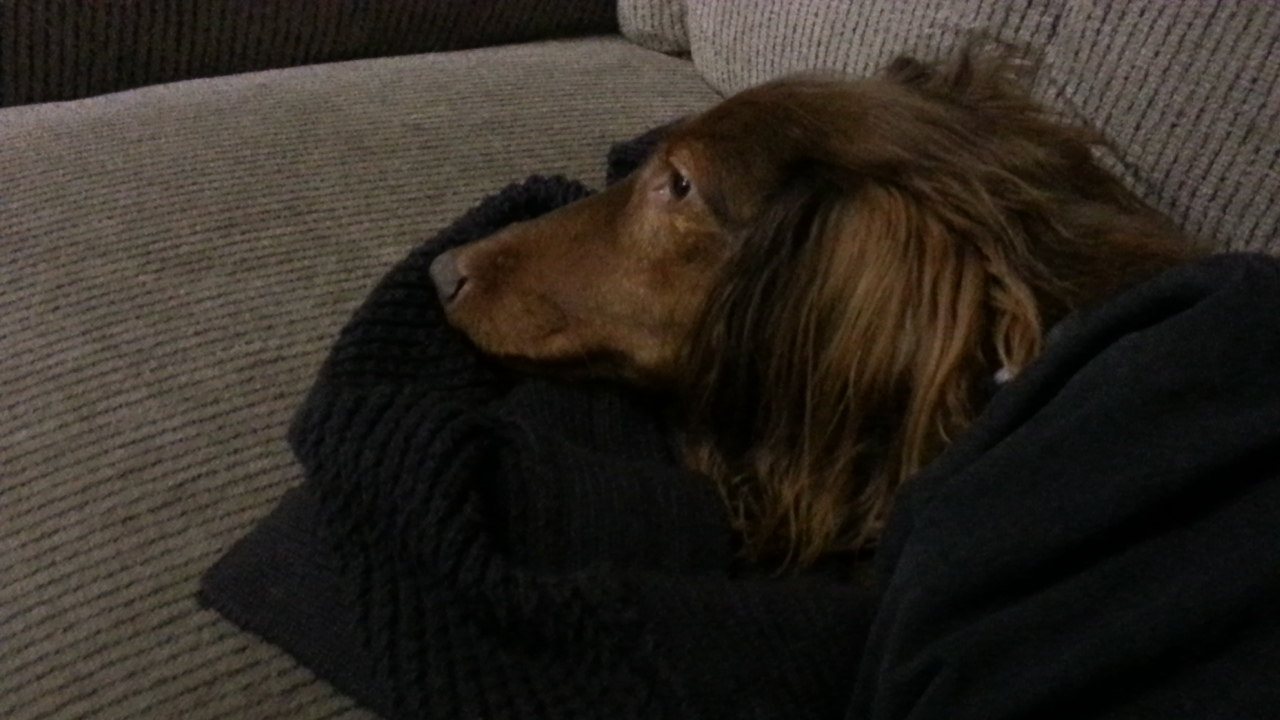
|
|
|
Back to top |
|
 |
victorbravo(at)sbcglobal. Guest
|
Posted: Fri May 20, 2016 2:00 pm Post subject: Kolb Firestar Progress report |
|
|
Quote: | Here is a picture of the two little
tube drill jigs I designed. They allow drilling through the
gusset and the tube at the same time, with the drill point
located on the centerline (apex) of the tube.
Bill Berle
|
| - The Matronics Kolb-List Email Forum - | | Use the List Feature Navigator to browse the many List utilities available such as the Email Subscriptions page, Archive Search & Download, 7-Day Browse, Chat, FAQ, Photoshare, and much more:
http://www.matronics.com/Navigator?Kolb-List |
|
Description: |
|
Filesize: |
113.52 KB |
Viewed: |
16489 Time(s) |
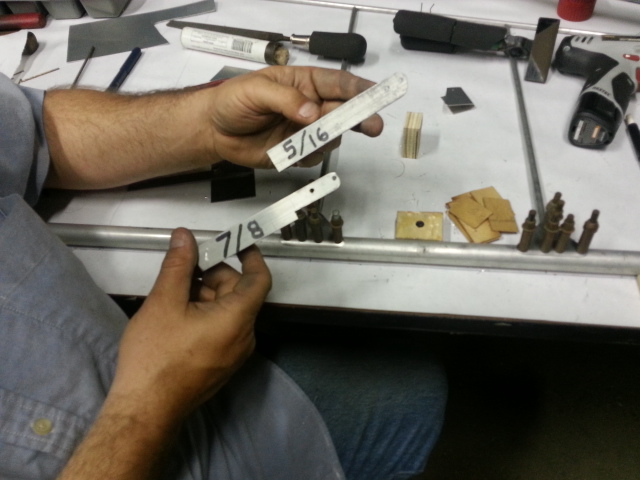
|
|
|
Back to top |
|
 |
victorbravo(at)sbcglobal. Guest
|
Posted: Fri May 20, 2016 2:01 pm Post subject: Kolb Firestar Progress report |
|
|
Quote: | Made progress on the first elevator
half tonight. Similar to rudder, triangular sheet metal
gussets at the intersections. Home-made quickie rivet
locator tool works well. I will probably make a better steel
one when I get to the ailerons because the ones I made from
aluminum are starting to wear after about 50 holes.
Bill Berle
www.ezflaphandle.com - safety & performance upgrade
for light aircraft
www.grantstar.net      - winning proposals for
non-profit and for-profit entities
-
|
| - The Matronics Kolb-List Email Forum - | | Use the List Feature Navigator to browse the many List utilities available such as the Email Subscriptions page, Archive Search & Download, 7-Day Browse, Chat, FAQ, Photoshare, and much more:
http://www.matronics.com/Navigator?Kolb-List |
|
Description: |
|
Filesize: |
363.65 KB |
Viewed: |
16489 Time(s) |
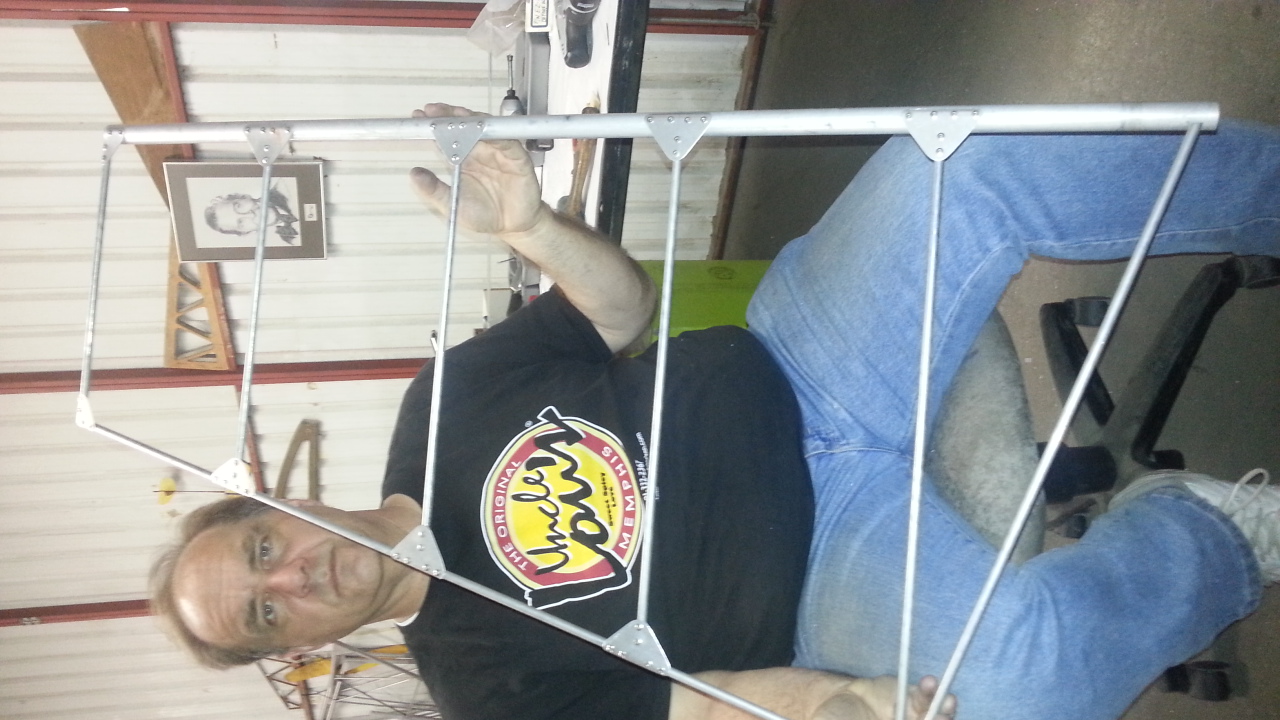
|
Description: |
|
Filesize: |
260.64 KB |
Viewed: |
16489 Time(s) |
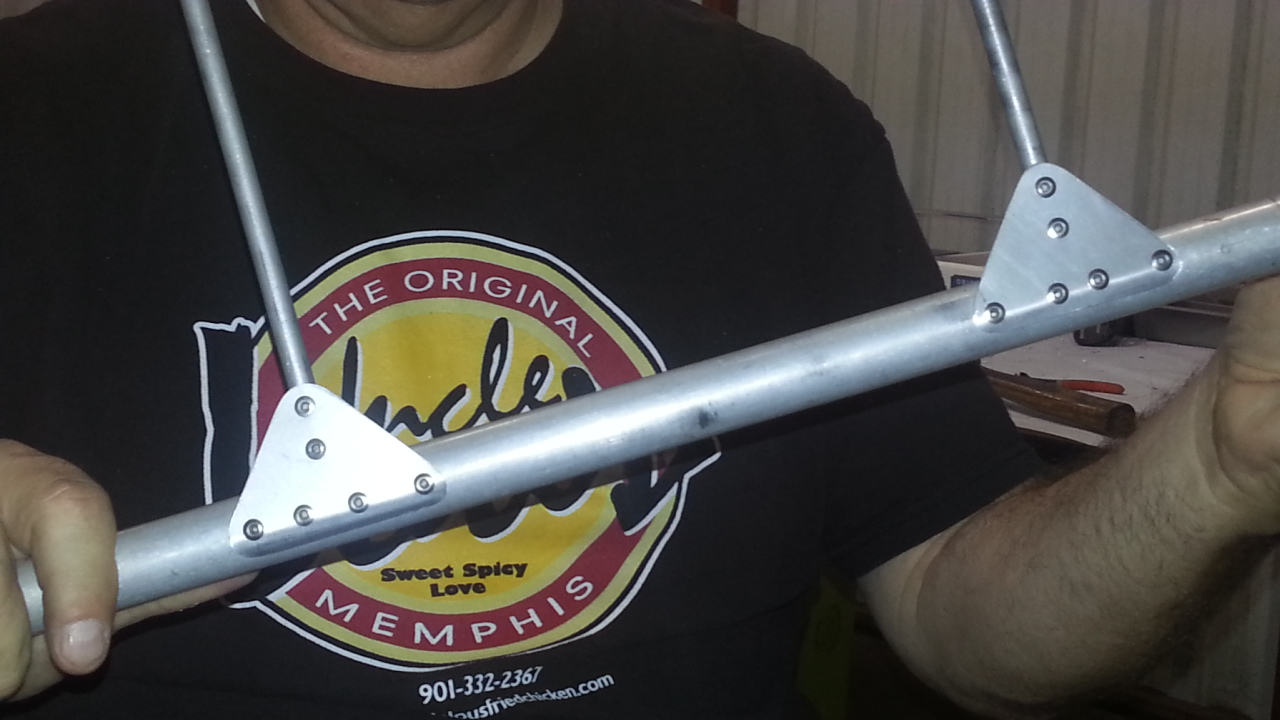
|
|
|
Back to top |
|
 |
Eugene Zimmerman

Joined: 10 Jan 2006 Posts: 392
|
Posted: Mon May 30, 2016 3:24 pm Post subject: Kolb Firestar Progress report |
|
|
Bill, Your photos show single tubes from leading edge to trailing edge. Is this according to your Kolb plans or your own modification? Every Kolb flight surface I’ve ever built required a second tube for triangulation in order to transfer the input torque to the control surface.Here is a graphic that will hopefully show what I’m concerned about.
[img]cid:F4D9642B-6148-41FD-B79D-F3757A9C64EA(at)PK5001Z[/img]
Quote: | On May 20, 2016, at 6:00 PM, Bill Berle <victorbravo(at)sbcglobal.net (victorbravo(at)sbcglobal.net)> wrote:
Quote: | Made progress on the first elevatorhalf tonight. Similar to rudder, triangular sheet metalgussets at the intersections. Home-made quickie rivetlocator tool works well. I will probably make a better steelone when I get to the ailerons because the ones I made fromaluminum are starting to wear after about 50 holes.Bill Berlewww.ezflaphandle.com - safety & performance upgradefor light aircraftwww.grantstar.net - winning proposals fornon-profit and for-profit entities- | <Elevator Under Construction.jpg><Elevator Gussets 1.jpg>
|
| - The Matronics Kolb-List Email Forum - | | Use the List Feature Navigator to browse the many List utilities available such as the Email Subscriptions page, Archive Search & Download, 7-Day Browse, Chat, FAQ, Photoshare, and much more:
http://www.matronics.com/Navigator?Kolb-List |
|
Description: |
|
Filesize: |
42.85 KB |
Viewed: |
16435 Time(s) |
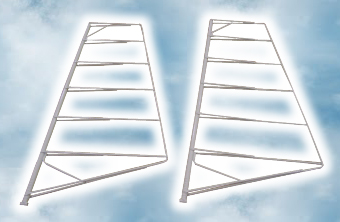
|
|
|
Back to top |
|
 |
victorbravo(at)sbcglobal. Guest
|
Posted: Mon May 30, 2016 10:04 pm Post subject: Kolb Firestar Progress report |
|
|
Hi Gene, thank you for the inquiry. I probably attached a photo to the original e-mail that showed the elevator under construction, not completed.
My control surfaces do indeed have "triangulation". There is an upper and lower structural rib "cap" at each rib location. The "Caps" are standard Kolb 5/16" tubes just like the plans show.
BUT... instead of the standard Kolb design of riveting the tubes directly to the leading edge and trailing edge, I attached them using .032" aluminum gusset plates. This is actually permitted and shown on the Kolb plans near the back of the plan set as an alternate method of attaching the (upper) rib tubes to the trailing edge tube.
What I did that was completely different than the plans is this:
1) The front of the upper and lower rib tube attach is done using a gusset at the top and another gusset at the bottom, with the rib tubes approximately FLUSH with the top and bottom of the leading edge tube. This is somewhat like the method used in the Graham Lee and Robert Baslee Nieuport replicas
| - The Matronics Kolb-List Email Forum - | | Use the List Feature Navigator to browse the many List utilities available such as the Email Subscriptions page, Archive Search & Download, 7-Day Browse, Chat, FAQ, Photoshare, and much more:
http://www.matronics.com/Navigator?Kolb-List |
|
|
|
Back to top |
|
 |
mojavjoe
Joined: 23 Dec 2013 Posts: 64
|
Posted: Tue May 31, 2016 2:47 am Post subject: Kolb Firestar Progress report |
|
|
Hi Bill
I built replicas of your new design while transferring parts from my FSII to my FSSS, found them significantly heavier and went back to the old design. I redesigned the alerions as well using .032 sheet to form ribs. Once again too heavy and I'm back to the old design. I wish you luck in your build.
Joe.
From: "Bill Berle" <victorbravo(at)sbcglobal.net>
To: "kolb-list" <kolb-list(at)matronics.com>
Sent: Tuesday, May 31, 2016 2:01:50 AM
Subject: Re: Kolb-List: Fw: Re: Kolb Firestar Progress report
Hi Gene, thank you for the inquiry. I probably attached a photo to the original e-mail that showed the elevator under construction, not completed.
My control surfaces do indeed have "triangulation". There is an upper and lower structural rib "cap" at each rib location. The "Caps" are standard Kolb 5/16" tubes just like the plans show.
BUT... instead of the standard Kolb design of riveting the tubes directly to the leading edge and trailing edge, I attached them using .032" aluminum gusset plates. This is actually permitted and shown on the Kolb plans near the back of the plan set as an alternate method of attaching the (upper) rib tubes to the trailing edge tube.
What I did that was completely different than the plans is this:
1) The front of the upper and lower rib tube attach is done using a gusset at the top and another gusset at the bottom, with the rib tubes approximately FLUSH with the top and bottom of the leading edge tube. This is somewhat like the method used in the Graham Lee and Robert Baslee Nieuport replicas.
2) At the trailing edge, the method I used starts off like the Kolb "optional" method at the back of the plans. A small triangular gusset sits "Across" the 90 degree joint between the top rib tube and trailing edge tube. Then, the bottom rib tube comes back at a very slight angle to rest NEXT TO the top rib tube, nesting against the same triangular gusset attaching the top rib tube. This way the thickness of the trailing edge is not increased, it is still one 5/16" tube.
Looking from the side view, you would see the trailing edge tube with one of the rib tubes butting up against it, and you would not see the other rib tube because it would be behind the first one. Then you would see the edge of the .032 gusset sitting on the top of the intersection.
So the finished elevator ribs actually look like what you can see in the photo attached tot his e-mail....
Bill Berle
www.ezflaphandle.com - safety & performance upgrade for light aircraft
www.grantstar.net - winning proposals for non-profit and for-profit entities
--------------------------------------------
On Mon, 5/30/16, Eugene Zimmerman <etzimm(at)gmail.com> wrote:
Subject: Re: Fw: Re: Kolb Firestar Progress report
To: "Kolb list" <kolb-list(at)matronics.com>
Date: Monday, May 30, 2016, 4:24 PM
Bill, Your photos show single tubes
from leading edge to trailing edge. Is this according to
your Kolb plans or your own modification? Every Kolb flight
surface I’ve ever built required a second tube for
triangulation in order to transfer the input torque to the
control surface.Here is a graphic
that will hopefully show what I’m concerned
about.
On May 20,
2016, at 6:00 PM, Bill Berle <victorbravo(at)sbcglobal.net>
wrote:
Made progress on the first elevator
half tonight. Similar to rudder,
triangular sheet metal
gussets at
the intersections. Home-made quickie rivet
locator tool works well. I will
probably make a better steel
one
when I get to the ailerons because the ones I made from
aluminum are starting to wear after
about 50 holes.
Bill Berle
www.ezflaphandle.com -
safety & performance upgrade
for light aircraft
www.grantstar.net
- winning proposals for
non-profit and for-profit entities
-<Elevator
Under Construction.jpg><Elevator
Gussets 1.jpg>
| - The Matronics Kolb-List Email Forum - | | Use the List Feature Navigator to browse the many List utilities available such as the Email Subscriptions page, Archive Search & Download, 7-Day Browse, Chat, FAQ, Photoshare, and much more:
http://www.matronics.com/Navigator?Kolb-List |
|
|
|
Back to top |
|
 |
Eugene Zimmerman

Joined: 10 Jan 2006 Posts: 392
|
Posted: Tue May 31, 2016 3:04 am Post subject: Kolb Firestar Progress report |
|
|
Quote: | On May 31, 2016, at 2:01 AM, Bill Berle <victorbravo(at)sbcglobal.net (victorbravo(at)sbcglobal.net)> wrote:
Hi Gene, thank you for the inquiry. I probably attached a photo to the original e-mail that showed the elevator under construction, not completed.
|
Bill.
My concern is satisfied. The photo of completed elevator looks very good.
Thanks,
Gene
| - The Matronics Kolb-List Email Forum - | | Use the List Feature Navigator to browse the many List utilities available such as the Email Subscriptions page, Archive Search & Download, 7-Day Browse, Chat, FAQ, Photoshare, and much more:
http://www.matronics.com/Navigator?Kolb-List |
|
|
|
Back to top |
|
 |
John Hauck
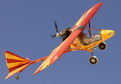
Joined: 09 Jan 2006 Posts: 4639 Location: Titus, Alabama (hauck's holler)
|
Posted: Tue May 31, 2016 4:08 am Post subject: Kolb Firestar Progress report |
|
|
I'm not an engineer. Been getting along with a little horse sense all these years.
Seems to me Bill B has reduced the angle of triangulation by moving the attach point inside rather than outside on the apex of the leading edge tube. I think a reduced angle would also reduce strength of the elevator, especially the inboard ribs which are much longer than the outboard ribs.
Only advantages I see are aesthetic and a little easier to cover, not having to work around the bumps.
Disadvantages:
-Increased weight
-Reduced strength
john h
mkIII
Titus, Alabama
From: owner-kolb-list-server(at)matronics.com [mailto:owner-kolb-list-server(at)matronics.com] On Behalf Of mojavjoe(at)comcast.net
Sent: Tuesday, May 31, 2016 5:47 AM
To: kolb-list
Subject: Re: Fw: Re: Kolb Firestar Progress report
Hi Bill
I built replicas of your new design while transferring parts from my FSII to my FSSS, found them significantly heavier and went back to the old design. I redesigned the alerions as well using .032 sheet to form ribs. Once again too heavy and I'm back to the old design. I wish you luck in your build.
Joe.
From: "Bill Berle" <victorbravo(at)sbcglobal.net (victorbravo(at)sbcglobal.net)>
To: "kolb-list" <kolb-list(at)matronics.com (kolb-list(at)matronics.com)>
Sent: Tuesday, May 31, 2016 2:01:50 AM
Subject: Re: Fw: Re: Kolb Firestar Progress report
Hi Gene, thank you for the inquiry. I probably attached a photo to the original e-mail that showed the elevator under construction, not completed.
| - The Matronics Kolb-List Email Forum - | | Use the List Feature Navigator to browse the many List utilities available such as the Email Subscriptions page, Archive Search & Download, 7-Day Browse, Chat, FAQ, Photoshare, and much more:
http://www.matronics.com/Navigator?Kolb-List |
|
_________________ John Hauck
MKIII/912ULS
hauck's holler
Titus, Alabama |
|
Back to top |
|
 |
brubakermal(at)yahoo.com Guest
|
Posted: Tue May 31, 2016 7:46 am Post subject: Kolb Firestar Progress report |
|
|
Hay kold list guys we are in Alaska and looking for other Kolbers
Sent from Yahoo Mail on Android
Quote: | On Mon, May 30, 2016 at 3:24 PM, Eugene Zimmerman
<etzimm(at)gmail.com> wrote:
Bill, Your photos show single tubes from leading edge to trailing edge. Is this according to your Kolb plans or your own modification? Every Kolb flight surface I’ve ever built required a second tube for triangulation in order to transfer the input torque to the control surface.Here is a graphic that will hopefully show what I’m concerned about.
[img]cid:CNRr1qUPAmmf0HY2dlU4[/img]
Quote: | On May 20, 2016, at 6:00 PM, Bill Berle <[url=javascript:return]victorbravo(at)sbcglobal.net[/url]> wrote:
Quote: | Made progress on the first elevatorhalf tonight. Similar to rudder, triangular sheet metalgussets at the intersections. Home-made quickie rivetlocator tool works well. I will probably make a better steelone when I get to the ailerons because the ones I made fromaluminum are starting to wear after about 50 holes.Bill Berlewww.ezflaphandle.com - safety & performance upgradefor light aircraftwww.grantstar.net - winning proposals fornon-profit and for-profit entities- | <Elevator Under Construction.jpg><Elevator Gussets 1.jpg>
|
|
| - The Matronics Kolb-List Email Forum - | | Use the List Feature Navigator to browse the many List utilities available such as the Email Subscriptions page, Archive Search & Download, 7-Day Browse, Chat, FAQ, Photoshare, and much more:
http://www.matronics.com/Navigator?Kolb-List |
|
Description: |
|
Filesize: |
42.85 KB |
Viewed: |
16417 Time(s) |

|
|
|
Back to top |
|
 |
victorbravo(at)sbcglobal. Guest
|
Posted: Tue May 31, 2016 10:16 am Post subject: Kolb Firestar Progress report |
|
|
Thank you all for the replies. I enjoy this discussion, and I enjoy having people call my ideas into question, which keeps me sharp and makes me defend my decisions. As such, PLEASE do not take any offense at me for going through my "defense" below, as an exercise to quantify and qualify the reasonableness of the decision.
As far as the weight gain by doing the control surfaces slightly different than the plans, I was well aware that there was going to be a weight gain but I believe it is very small. At each individual rib station, the difference would be as follows:
1) Bottom rib tube (5/16") will be about 4 inches longer (heavier) at the rear, because it reaches all the way to the trailing edge.
2) Top and bottom rib will each be about 3/8 inches shorter (lighter), because they no longer overlap the leading edge tube.
3) Addition of two gussets at top/bottom of the leading edge, approx. .032 x 6 square inches total.
4) Addition of one gusset at the top of the trailing edge, approx. .032 x 3 square inches.
5) Eight additional 1/8" steel pop rivets (12 instead of 4)
Quote: | From Aircraft spruce website:
|
.032" aluminum sheet weighs .45 pounds per square foot. That is .0031 pounds per square inch. 9 square inches is .0282 pounds, or .45 ounces for all three gussets.
5/16" x .049 wall tube (slightly heavier than .035 wall) is .0423 pounds per foot, and 4 inches is a third of a foot, so that extra piece of tube is .0141 pounds, or .2256 ounces (slightly less than a quarter of an ounce).
The rivets weigh something, but Aircraft Spruce doesn't list the weight. I will GUESS that 8 rivets weigh about a quarter of an ounce. Now remember, 80% of the rivet mandrel is broken off and goes into the garbage can, so we only count the weight of the rivet parts left int he airplane.
So as a rough approximate, it appears that my modified rib assemblies will weigh about an ounce more than the stock rib. So what did I get in return for the extra time and effort and weight?
Although the rib tubes do not sit on top of the leading edge tube any more, and as John H points out they are indeed closer to the center of the leading edge tube, the "shear plane", or the actual contact point between the two parts is in the same place... at the top and bottom tangent point of the leading edge tube. So if the loads on the rib tubes were critical (the structure is "maxed out" and on the verge of collapse), the rib tubes could buckle in compression a little sooner on my design than on the original Kolb design. BUT, the Kolb design holds the entire rib tube / leading edge tube joint together with one rivet, it is very likely that the rib tube is on the verge of a compression failure.
But on my version, there are six rivets and a reinforcement gusset, which spreads that shear load (the rib moving fore-aft or side-side relative to the leading edge tube) across six rivets, and prevents any rotation (rib tube swinging around the original single rivet). So it seems to me that there is not only a greater amount of strength (resistance to pulling the joint apart) but also a large improvement in stiffness (movement before it pulls apart).
Near the trailing edge of the rib, the original Kolb rib "ends the triangulation" several inches forward of the trailing edge. This means that the last few inches of the entire control surface is simply one thickness of 5/16" rib tube and a trailing edge tube. Considering that the Kolb instruction manual tells you that this 5/16" tube is easy enough to bend by hand, it certainly seems to me that there is a very small amount of stiffness or bend resistance anywhere aft of the triangulation joint. On my modified design, the lower rib tube goes all the way to the back, and so the "triangle" is rigid all the way to the trailing edge. This results in a stiffer and stronger control surface.
For FLIGHT loads, the trailing edge itself does not do very much... it's only there to wrap the fabric around. This can be proven out by looking at hundreds of WW1 airplanes that used only a thin wire as the trailing edge of the control surfaces. But the loads put on this area during off-airport operations, rolling through brush, and ground handling, folding the tails, trailering, and brushing past the controls... those are probably far more of a damage risk than anything that you will get in the air. That may be why Kolb originally accepted the weight and left the trailing edge tube on instead of using a string or wire like an old WW! plane??
One person was kind enough to post that they had tried sheet metal ribs instead of the tubes, but it was too heavy. My Cessna 172 might not even use .032" sheet metal in the control surface ribs, I'm guessing it's .025 or perhaps even .020. Certainly for a very light aircraft like a Kolb, .016 or .020 would be plenty of thickness for the aileron ribs.
Another possible justification for my "stronger" control surfaces is that I will be using the 60HP HKS engine, and this will probably create a little more thrust than the 447/503 engines. A little extra thrust will create a bit more air loads on the control surfaces. Since this will primarily be an off-road machine, I will probably wind up whacking a few more bushes and ground shrubs than some other types of flying.
BUT... the fact remains that if for any reason I'm unhappy with the control surface weight, I have the options to rebuild these back to stock, or to build new stock controls.
Anyway, thanks to everyone again for participating in this, and keeping me on my toes. I appreciate it.
Bill Berle
www.ezflaphandle.com - safety & performance upgrade for light aircraft
www.grantstar.net      - winning proposals for non-profit and for-profit entities
--------------------------------------------
On Tue, 5/31/16, John Hauck <jhauck(at)elmore.rr.com> wrote:
Subject: RE: Fw: Re: Kolb Firestar Progress report
To: kolb-list(at)matronics.com
Date: Tuesday, May 31, 2016, 5:08 AM
I'm not an engineer. Been
getting along with a little horse sense all these
years. Â Seems to me Bill B has reduced
the angle of triangulation by moving the attach point inside
rather than outside on the apex of the leading edge tube.Â
I think a reduced angle would also reduce strength of the
elevator, especially the inboard ribs which are much longer
than the outboard ribs. Â Only advantages I see are
aesthetic and a little easier to cover, not having to work
around the bumps.  Disadvantages:  -Increased weight  -Reduced strength  john hmkIIITitus, Alabama     From: owner-kolb-list-server(at)matronics.com
[mailto:owner-kolb-list-server(at)matronics.com] On Behalf
Of mojavjoe(at)comcast.net
Sent: Tuesday, May 31, 2016 5:47 AM
To: kolb-list
Subject: Re: Fw: Re: Kolb Firestar
Progress report  Hi
Bill
 I
built replicas of your new design while transferring parts
from my FSII to my FSSS, found them significantly heavier
and went back to the old design. I redesigned the alerions
as well using .032 sheet to form ribs. Once again too heavy
and I'm back to the old design. I wish you luck in your
build.
 Joe.Â
 From: "Bill Berle" <victorbravo(at)sbcglobal.net>
To: "kolb-list" <kolb-list(at)matronics.com>
Sent: Tuesday, May 31, 2016 2:01:50 AM
Subject: Re: Fw: Re: Kolb Firestar
Progress report
 Hi Gene, thank you for the
inquiry. I probably attached a photo to the original e-mail
that showed the elevator under construction, not
completed.
Â
Â
| - The Matronics Kolb-List Email Forum - | | Use the List Feature Navigator to browse the many List utilities available such as the Email Subscriptions page, Archive Search & Download, 7-Day Browse, Chat, FAQ, Photoshare, and much more:
http://www.matronics.com/Navigator?Kolb-List |
|
|
|
Back to top |
|
 |
John Hauck
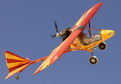
Joined: 09 Jan 2006 Posts: 4639 Location: Titus, Alabama (hauck's holler)
|
Posted: Tue May 31, 2016 11:25 am Post subject: Kolb Firestar Progress report |
|
|
All Kolb models use the same design and material for elevator construction. Many of us are running 100 hp 912uls engines on our MKIIIs and Slingshots.
One 1/8" rivet holding a rib tube is more than satisfactory for the application. That single rivet is not close to failure. If it was, I guarantee you some of us would have already proven it during hard flight, mishandling, and crashes.
Many have gone before you flying Kolbs in the rough. The elevator is as good as the durability of the fabric, which is pretty delicate when it comes to anything sharp, or that whips when striking the leading edge of the stabilizers. I experienced this many years ago, 1994, landing on an abandoned strip south of Delta Junction, Alaska. I still carry the scars/patches from that episode that nearly ended my first flight to Alaska.
Ailerons, elevators, and rudder utilize the same rib construction, and have since the early 1980s. I'm happy with them.
john h
mkIII
Titus, Alabama
--
| - The Matronics Kolb-List Email Forum - | | Use the List Feature Navigator to browse the many List utilities available such as the Email Subscriptions page, Archive Search & Download, 7-Day Browse, Chat, FAQ, Photoshare, and much more:
http://www.matronics.com/Navigator?Kolb-List |
|
_________________ John Hauck
MKIII/912ULS
hauck's holler
Titus, Alabama |
|
Back to top |
|
 |
|
|
You cannot post new topics in this forum You cannot reply to topics in this forum You cannot edit your posts in this forum You cannot delete your posts in this forum You cannot vote in polls in this forum You cannot attach files in this forum You can download files in this forum
|
Powered by phpBB © 2001, 2005 phpBB Group
|