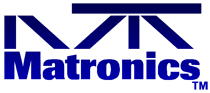 |
Matronics Email Lists Web Forum Interface to the Matronics Email Lists
|
View previous topic :: View next topic |
Author |
Message |
Laz
Joined: 04 Jan 2016 Posts: 30
|
Posted: Sat Aug 20, 2016 6:39 am Post subject: Voltage drop |
|
|
I was doing some checks on my RV8 electrical system that I just finished a few weeks ago. This is a brand new plane under construction. Before I fired up any of the Garmin G3x stuff, I tested the usual systems , starter , fuel pump lights etc. all seemed to work fine. I fired up the G3x and it also come on line with no problems.
Yesterday I had everything on line and tested the starter again. When the starter turned all my other electronics died. As soon as the starter stopped they came back on. It appears that the current draw from the starter took the voltage available to the other Items so low they shut down ( most of the G3X stuff shuts down below 11 volts or so). I have a new odyssey battery 680 and it appears to be charged. Here are my questions.
1. Battery solenoid gets warm with the battery master on. Is this normal?
2. Could this be a battery issue?
3. What test can I perform on the solenoid, battery etc. ?
Thanks
| - The Matronics AeroElectric-List Email Forum - | | Use the List Feature Navigator to browse the many List utilities available such as the Email Subscriptions page, Archive Search & Download, 7-Day Browse, Chat, FAQ, Photoshare, and much more:
http://www.matronics.com/Navigator?AeroElectric-List |
|
|
|
Back to top |
|
 |
user9253
Joined: 28 Mar 2008 Posts: 1926 Location: Riley TWP Michigan
|
Posted: Sat Aug 20, 2016 7:46 am Post subject: Re: Voltage drop |
|
|
Everything that you described sounds normal to me. Check out Bob's Z-10/8 electrical drawing with a brownout battery.
| - The Matronics AeroElectric-List Email Forum - | | Use the List Feature Navigator to browse the many List utilities available such as the Email Subscriptions page, Archive Search & Download, 7-Day Browse, Chat, FAQ, Photoshare, and much more:
http://www.matronics.com/Navigator?AeroElectric-List |
|
_________________ Joe Gores |
|
Back to top |
|
 |
Dave Saylor
Joined: 11 Jan 2015 Posts: 209 Location: GILROY, CA
|
Posted: Sat Aug 20, 2016 8:11 am Post subject: Voltage drop |
|
|
The contactor normally gets a little warm--no worries there.Â
Your battery is probably just fine. My 925 does the same thing.Â
You'll need some kind of back-up battery to prevent what you're describing. I use one from TCW that works great.
--Dave
On Saturday, August 20, 2016, Michael Lazarowicz <tllaz330(at)gmail.com (tllaz330(at)gmail.com)> wrote:
Quote: | I was doing some checks on my RV8 electrical system that I just finished a few weeks ago. This is a brand new plane under construction. Before I fired up any of the Garmin G3x stuff, I tested the usual systems , starter , fuel pump lights etc. all seemed to work fine. I fired up the G3x and it also come on line with no problems.
Yesterday I had everything on line and tested the starter again. When the starter turned all my other electronics died. As soon as the starter stopped they came back on. It appears that the current draw from the starter took the voltage available to the other Items so low they shut down ( most of the G3X stuff shuts down below 11 volts or so). I have a new odyssey battery 680 and it appears to be charged. Here are my questions.
1. Battery solenoid gets warm with the battery master on. Is this normal?
2. Could this be a battery issue?
3. What test can I perform on the solenoid, battery etc. ?
Thanks
|
| - The Matronics AeroElectric-List Email Forum - | | Use the List Feature Navigator to browse the many List utilities available such as the Email Subscriptions page, Archive Search & Download, 7-Day Browse, Chat, FAQ, Photoshare, and much more:
http://www.matronics.com/Navigator?AeroElectric-List |
|
_________________ --Dave
KWVI |
|
Back to top |
|
 |
nuckolls.bob(at)aeroelect Guest
|
Posted: Sat Aug 20, 2016 3:16 pm Post subject: Voltage drop |
|
|
Quote: |
Yesterday I had everything on line and tested the starter again. When the starter turned all my other electronics died. As soon as the starter stopped they came back on. It appears that the current draw from the starter took the voltage available to the other Items so low they shut down ( most of the G3X stuff shuts down below 11 volts or so). I have a new odyssey battery 680 and it appears to be charged. |
What engine, alternator and battery combination?
Quote: | Here are my questions. |
Your battery is either (1) not charged -OR- (2) too small -OR-
Both.
Quote: | 1. Battery solenoid gets warm with the battery master on. Is this normal? |
Yes
Quote: | 2. Could this be a battery issue? |
Probably . . .
Quote: | 3. What test can I perform on the solenoid, battery etc. ? |
Put a computer controlled charger on the battery
and leave it connected until the charger says, "it's
charged.
Fire up the engine and report back on
your observations . . . in particular, what
is the bus voltage with the engine running,
alternator ON, normal running loads ON.
| - The Matronics AeroElectric-List Email Forum - | | Use the List Feature Navigator to browse the many List utilities available such as the Email Subscriptions page, Archive Search & Download, 7-Day Browse, Chat, FAQ, Photoshare, and much more:
http://www.matronics.com/Navigator?AeroElectric-List |
|
|
|
Back to top |
|
 |
nuckolls.bob(at)aeroelect Guest
|
Posted: Sat Aug 20, 2016 3:33 pm Post subject: Voltage drop |
|
|
At 11:10 AM 8/20/2016, you wrote:
Quote: | The contactor normally gets a little warm--no worries there.Â
Your battery is probably just fine. My 925 does the same thing.Â
You'll need some kind of back-up battery to prevent what you're describing. I use one from TCW that works great. |
Oops . . . I stubbed my toe here. If you have any
electro-whizzies that reboot when presented with
a bus voltage below 11.0 volts . . . then they almost
certainly will reboot every time you start the engine.
I'm somewhat chagrined that folks who build and qualify
these panel mounted super-computers don't either (1)
study the real world of bus voltage behaviors during
engine start and/or (2) advise the customer that their
product WILL reboot during a start-up transient that
has ALWAYS existed on EVERY airplane.
To my mind, the simplest work-around is simply not to turn
on . . . or depend on these gizmos until after engine start.
Yeah, I know, our instructors taught us to concentrate on
the oil pressure display after engine start with a finger
on the mag switches lest the pressure not come up as expected.
But I would be interested to hear if anyone on this list
has ever experienced an failure of oil circulation that did
not manifest until right after start up. No doubt, Lindbergh
and contemporaries had good reason to worry about such things.
Those guys carried tool boxes around in the rear cockpit
with an eye toward needing off field maintenance of one
kind or another.
Now we have a new suite of technology which, for reasons
we'll never know, was NOT designed to replace
legacy instrumentation. DO-160 requires a qualified
product to (1) not be damaged by and (2) recover gracefully
from bus voltage brownouts quantified in the test
requirements document.
Problem is, graceful recovery has not been interpreted
to mean that the oil pressure display on the glass screen
needs to be as available and responsive as their steam
gage counterparts during the first few seconds after engine
start.
This leaves the system integrator (YOU) with a problem.
If you're going to pay homage to the legacy philosophy
for monitoring engine parameters that were of intense interest
to Charles Lindbergh, then we have to ADD power supply
brown-out buffers for these new electro-whizzies . . . that
COULD have been designed to accommodate such brown-outs.
The question becomes, are we adding cost, weight and complexity
to a system striving to honor a operating practice that
has been around since Lindbergh? What are the demonstrated
risks for cranking up an engine 'blind' an waiting for
the 'new' technology to wake up and report for duty?
Bob . . .
| - The Matronics AeroElectric-List Email Forum - | | Use the List Feature Navigator to browse the many List utilities available such as the Email Subscriptions page, Archive Search & Download, 7-Day Browse, Chat, FAQ, Photoshare, and much more:
http://www.matronics.com/Navigator?AeroElectric-List |
|
|
|
Back to top |
|
 |
Kellym
Joined: 10 Jan 2006 Posts: 1705 Location: Sun Lakes AZ
|
Posted: Sat Aug 20, 2016 4:03 pm Post subject: Voltage drop |
|
|
The only situation I have experienced where oil pressure response time
was important is for a cold start, as in below freezing, where the
amount of pre-heat is questionable as to whether it was applied long
enough. As in if pressure doesn't come up in 30 seconds, one should shut
down and apply heat longer to the engine compartment. Seems like some
electrowhizzy engine monitors take 30 seconds to boot. On the other
hand, most of them respond well to a small backup battery that keeps
input voltage high enough to prevent a reboot.
On 8/20/2016 4:06 PM, Robert L. Nuckolls, III wrote:
To my mind, the simplest work-around is simply not to turn
Quote: | on . . . or depend on these gizmos until after engine start.
Yeah, I know, our instructors taught us to concentrate on
the oil pressure display after engine start with a finger
on the mag switches lest the pressure not come up as expected.
|
Quote: | Now we have a new suite of technology which, for reasons
we'll never know, was NOT designed to replace
legacy instrumentation. DO-160 requires a qualified
product to (1) not be damaged by and (2) recover gracefully
from bus voltage brownouts quantified in the test
requirements document.
|
Quote: | The question becomes, are we adding cost, weight and complexity
to a system striving to honor a operating practice that
has been around since Lindbergh? What are the demonstrated
risks for cranking up an engine 'blind' an waiting for
the 'new' technology to wake up and report for duty?
Bob . . .
|
| - The Matronics AeroElectric-List Email Forum - | | Use the List Feature Navigator to browse the many List utilities available such as the Email Subscriptions page, Archive Search & Download, 7-Day Browse, Chat, FAQ, Photoshare, and much more:
http://www.matronics.com/Navigator?AeroElectric-List |
|
_________________ Kelly McMullen
A&P/IA, EAA Tech Counselor # 5286
KCHD |
|
Back to top |
|
 |
theidtke(at)cox.net Guest
|
Posted: Sat Aug 20, 2016 4:09 pm Post subject: Voltage drop |
|
|
Fairly common occurrence with the new electronic panels.
Did a fair amount of research on this before deciding to feed at least one glass panel with an alternate battery so that in addition to not being affected by startup (having immediate engine instrumentation awareness when I do), tasks like doing flight plans can be done with the engine off.
Just a thought
Anyway, Bob has a few 2 battery diagrams in his book that were extremely helpful when I did my panel/avionics/engine monitoring system.
Trent
From: owner-aeroelectric-list-server(at)matronics.com [mailto:owner-aeroelectric-list-server(at)matronics.com] On Behalf Of Robert L. Nuckolls, III
Sent: Saturday, August 20, 2016 4:07 PM
To: aeroelectric-list(at)matronics.com
Subject: Re: Voltage drop
At 11:10 AM 8/20/2016, you wrote:
The contactor normally gets a little warm--no worries there.Â
Your battery is probably just fine. My 925 does the same thing.Â
You'll need some kind of back-up battery to prevent what you're describing. I use one from TCW that works great.
Oops . . . I stubbed my toe here. If you have any
electro-whizzies that reboot when presented with
a bus voltage below 11.0 volts . . . then they almost
certainly will reboot every time you start the engine.
I'm somewhat chagrined that folks who build and qualify
these panel mounted super-computers don't either (1)
study the real world of bus voltage behaviors during
engine start and/or (2) advise the customer that their
product WILL reboot during a start-up transient that
has ALWAYS existed on EVERY airplane.
To my mind, the simplest work-around is simply not to turn
on . . . or depend on these gizmos until after engine start.
Yeah, I know, our instructors taught us to concentrate on
the oil pressure display after engine start with a finger
on the mag switches lest the pressure not come up as expected.
But I would be interested to hear if anyone on this list
has ever experienced an failure of oil circulation that did
not manifest until right after start up. No doubt, Lindbergh
and contemporaries had good reason to worry about such things.
Those guys carried tool boxes around in the rear cockpit
with an eye toward needing off field maintenance of one
kind or another.
Now we have a new suite of technology which, for reasons
we'll never know, was NOT designed to replace
legacy instrumentation. DO-160 requires a qualified
product to (1) not be damaged by and (2) recover gracefully
from bus voltage brownouts quantified in the test
requirements document.
Problem is, graceful recovery has not been interpreted
to mean that the oil pressure display on the glass screen
needs to be as available and responsive as their steam
gage counterparts during the first few seconds after engine
start.
This leaves the system integrator (YOU) with a problem.
If you're going to pay homage to the legacy philosophy
for monitoring engine parameters that were of intense interest
to Charles Lindbergh, then we have to ADD power supply
brown-out buffers for these new electro-whizzies . . . that
COULD have been designed to accommodate such brown-outs.
The question becomes, are we adding cost, weight and complexity
to a system striving to honor a operating practice that
has been around since Lindbergh? What are the demonstrated
risks for cranking up an engine 'blind' an waiting for
the 'new' technology to wake up and report for duty?
Bob . . .
| - The Matronics AeroElectric-List Email Forum - | | Use the List Feature Navigator to browse the many List utilities available such as the Email Subscriptions page, Archive Search & Download, 7-Day Browse, Chat, FAQ, Photoshare, and much more:
http://www.matronics.com/Navigator?AeroElectric-List |
|
|
|
Back to top |
|
 |
Laz
Joined: 04 Jan 2016 Posts: 30
|
Posted: Sat Aug 20, 2016 5:59 pm Post subject: Voltage drop |
|
|
Thanks Bob,
I do have a backup battery that is already wired in but have it
disconnected because there is no charging going on. The other problem is
that my odyssey battery (680) was more discharged than I thought . It is
on a charger now and it should rectify the problem. I was just concerned I
had a bad relay or miss-wired something. The good news is I checked all my
wiring Battery/ Alt. switch etc. They were all fine.
I do have a basic question that I cannot seem to answer in my mind. When
the Battery switch is on, there is power going to the alternator via the
main B lead. Since that lead is connected directly to the output side of
the battery relay dose it not draw a significant amount of current when the
Battery master is on and the alternator is not running. In you book it
show hat lead connected to coils that are stationary in the alternator,
then to ground believe. My non electrical mind just cannot figure that out
| - The Matronics AeroElectric-List Email Forum - | | Use the List Feature Navigator to browse the many List utilities available such as the Email Subscriptions page, Archive Search & Download, 7-Day Browse, Chat, FAQ, Photoshare, and much more:
http://www.matronics.com/Navigator?AeroElectric-List |
|
|
|
Back to top |
|
 |
nuckolls.bob(at)aeroelect Guest
|
Posted: Sun Aug 21, 2016 6:03 am Post subject: Voltage drop |
|
|
At 06:59 PM 8/20/2016, you wrote:
Quote: | --> AeroElectric-List message posted by: Kelly McMullen <kellym(at)aviating.com>
The only situation I have experienced where oil pressure response time was important is for a cold start, as in below freezing, where the amount of pre-heat is questionable as to whether it was applied long enough. As in if pressure doesn't come up in 30 seconds, one should shut down and apply heat longer to the engine compartment. Seems like some electrowhizzy engine monitors take 30 seconds to boot. On the other hand, most of them respond well to a small backup battery that keeps input voltage high enough to prevent a reboot. |
Yeah. I recall getting ready to depart
Kansas City one morning when the airplane
had sat out in -10F weather. We heated the
engine and used ground power to supplement
a cold battery. Engine started readily
but the oil pressure didn't really start to
move for a really long time (didn't have the stop
watch out). The oil pressure gage was connected
to the engine through a small bore copper line.
Oil in that line behind the fire wall did not
get warmed in pre-heat . . . and was essentially
the consistency of peanut butter.
Under some circumstances, even the legacy
steam gage can take some time to offer useful
information.
Bob . . .
| - The Matronics AeroElectric-List Email Forum - | | Use the List Feature Navigator to browse the many List utilities available such as the Email Subscriptions page, Archive Search & Download, 7-Day Browse, Chat, FAQ, Photoshare, and much more:
http://www.matronics.com/Navigator?AeroElectric-List |
|
|
|
Back to top |
|
 |
nuckolls.bob(at)aeroelect Guest
|
Posted: Sun Aug 21, 2016 7:49 am Post subject: Voltage drop |
|
|
Posted this eariler and got a bounce from the
ListServer about having exceeded attachment
limits. Need to look into that.
In the mean time, here's a repost with links
to images:
At 08:57 PM 8/20/2016, you wrote:
Quote: | Thanks Bob,
I do have a backup battery that is already wired in but have it disconnected because there is no charging going on. |
Don't understand this . . . is this a system
battery that is part of your airplane's architecture
or is it associated with a specific appliance
as part of its design?
Quote: |  The other problem is that my odyssey battery (680) was more discharged than I thought . It is on a charger now and it should rectify the problem. I was just concerned I had a bad relay or miss-wired something. The good news is I checked all my wiring Battery/ Alt. switch etc. They were all fine. |
. . . good connecting of the dots . . .
Quote: | I do have a basic question that I cannot seem to answer in my mind. When the Battery switch is on, there is power going to the alternator via the main B lead. Since that lead is connected directly to the output side of the battery relay dose it not draw a significant amount of current when the Battery master is on and the alternator is not running. In you book it show hat lead connected to coils that are stationary in the alternator, then to ground believe. My non electrical mind just cannot figure that out. |
An alternator generally has two connections
to the ship's electrical system. (1) The "B-Lead"
or battery lead that is a power-output connection
and an input lead that is (2a) excitation from the
regulator to the field . . .
http://www.aeroelectric.com/List_Files/Externally_Regulated-s.jpg
. . . or (2b) on/off control to the internal
regulator.
http://www.aeroelectric.com/List_Files/Internally_Regulated-s.jpg
In both cases, you can see that the B-lead
connects to the + side of a three-phase
rectifier . . . diodes that convert the
internally generated AC into DC while
preventing any back flow of current from
the battery into the alternator.
In all automotive applications, you will find that
the b-lead is always connected to the vehicle's
battery. The factory stock (+) battery cable for
my truck comes with two wires, a fat wire to the
starter solenoid and a not-so-fat wire running
directly to the alternator b-lead - power never
flows into this lead as long as the diodes
are intact.
The only 'input' lead to an externally regulated
alternator draws current when the alternator
control switch is ON. This is field current
from the regulator attempting to control
bus voltage. If the engine is not yet running,
the regulator will 'full field' the alternator
causing as much as 3 amps of draw on the
battery.
The modern internally regulated alternator
often features an integrated circuit that
'watches' for the presence of ac voltage
from the stator windings. If no AC present
then the alternator is not rotating . . . and
field current is shut off. This prevents
the otherwise inevitable, non-productive
drain during times the engine is not running.
Quote: | It's been 5 years since I retired, but I do remember some screen interruption, all be it small and fast during engine starts on some if not all the planes I flew to make a buck. Usually when changing from
APU power to the engine driven generators. Â I guess its just part of the program |
Correct. This is a function of time-to-boot-up
inherent in the design of the appliance.
As I recall, all of the screens in the
line of Beech products pretty much came
alive in a second or less after application
of operating power whether first-on or
post brown-out . . . so we KNOW it can
be done. All of my software driven products
are wide-eyed, bright-eyed and bushy-tailed
milliseconds after power up.
But ever since the Blue Mountain days of
EFIS products offered to owner built and
maintained aircraft, there have be a variety
of instances where boot-up times were sometimes
distressingly long (Blue Mountain had a HARD
DRIVE!!). So not only did that product
need to load an operating system, it might
take many seconds after the software woke
up until the analog rate integration
calculations could get stood up in deducing
the gravity vector.
We've come a long way baby . . . but it's
still disappointing that some of the big
guns in the electronic instrumentation
business for light aircraft are not not
implementing the best we know how to do
in managing power-up/brown-outs events.
Bob . . .
Bob . . .
| - The Matronics AeroElectric-List Email Forum - | | Use the List Feature Navigator to browse the many List utilities available such as the Email Subscriptions page, Archive Search & Download, 7-Day Browse, Chat, FAQ, Photoshare, and much more:
http://www.matronics.com/Navigator?AeroElectric-List |
|
|
|
Back to top |
|
 |
ashleysc(at)broadstripe.n Guest
|
Posted: Sun Aug 21, 2016 8:19 am Post subject: Voltage drop |
|
|
Hi Bob;
Neat and very understandable schematics for externally and internally regulated alternators. Would you care to provide one for a internally regulated, permanent magnet alternator, so as to cover the subject exhaustively? I think I can deduce same, but would feel better to have it "from the horse's mouth."
Cheers! Stu.
From: "Robert L. Nuckolls, III" <nuckolls.bob(at)aeroelectric.com>
To: aeroelectric-list(at)matronics.com
Sent: Sunday, August 21, 2016 7:57:50 AM
Subject: Re: Voltage drop
Posted this eariler and got a bounce from the
ListServer about having exceeded attachment
limits. Need to look into that.
In the mean time, here's a repost with links
to images:
At 08:57 PM 8/20/2016, you wrote:
Quote: | Thanks Bob,
I do have a backup battery that is already wired in but have it disconnected because there is no charging going on. |
Don't understand this . . . is this a system
battery that is part of your airplane's architecture
or is it associated with a specific appliance
as part of its design?
Quote: |  The other problem is that my odyssey battery (680) was more discharged than I thought . It is on a charger now and it should rectify the problem. I was just concerned I had a bad relay or miss-wired something. The good news is I checked all my wiring Battery/ Alt. switch etc. They were all fine. |
. . . good connecting of the dots . . .
Quote: | I do have a basic question that I cannot seem to answer in my mind. When the Battery switch is on, there is power going to the alternator via the main B lead. Since that lead is connected directly to the output side of the battery relay dose it not draw a significant amount of current when the Battery master is on and the alternator is not running. In you book it show hat lead connected to coils that are stationary in the alternator, then to ground believe. My non electrical mind just cannot figure that out. |
An alternator generally has two connections
to the ship's electrical system. (1) The "B-Lead"
or battery lead that is a power-output connection
and an input lead that is (2a) excitation from the
regulator to the field . . .
http://www.aeroelectric.com/List_Files/Externally_Regulated-s.jpg
. . . or (2b) on/off control to the internal
regulator.
http://www.aeroelectric.com/List_Files/Internally_Regulated-s.jpg
In both cases, you can see that the B-lead
connects to the + side of a three-phase
rectifier . . . diodes that convert the
internally generated AC into DC while
preventing any back flow of current from
the battery into the alternator.
In all automotive applications, you will find that
the b-lead is always connected to the vehicle's
battery. The factory stock (+) battery cable for
my truck comes with two wires, a fat wire to the
starter solenoid and a not-so-fat wire running
directly to the alternator b-lead - power never
flows into this lead as long as the diodes
are intact.
The only 'input' lead to an externally regulated
alternator draws current when the alternator
control switch is ON. This is field current
from the regulator attempting to control
bus voltage. If the engine is not yet running,
the regulator will 'full field' the alternator
causing as much as 3 amps of draw on the
battery.
The modern internally regulated alternator
often features an integrated circuit that
'watches' for the presence of ac voltage
from the stator windings. If no AC present
then the alternator is not rotating . . . and
field current is shut off. This prevents
the otherwise inevitable, non-productive
drain during times the engine is not running.
Quote: | It's been 5 years since I retired, but I do remember some screen interruption, all be it small and fast during engine starts on some if not all the planes I flew to make a buck. Usually when changing from
APU power to the engine driven generators. Â I guess its just part of the program |
Correct. This is a function of time-to-boot-up
inherent in the design of the appliance.
As I recall, all of the screens in the
line of Beech products pretty much came
alive in a second or less after application
of operating power whether first-on or
post brown-out . . . so we KNOW it can
be done. All of my software driven products
are wide-eyed, bright-eyed and bushy-tailed
milliseconds after power up.
But ever since the Blue Mountain days of
EFIS products offered to owner built and
maintained aircraft, there have be a variety
of instances where boot-up times were sometimes
distressingly long (Blue Mountain had a HARD
DRIVE!!). So not only did that product
need to load an operating system, it might
take many seconds after the software woke
up until the analog rate integration
calculations could get stood up in deducing
the gravity vector.
We've come a long way baby . . . but it's
still disappointing that some of the big
guns in the electronic instrumentation
business for light aircraft are not not
implementing the best we know how to do
in managing power-up/brown-outs events.
Bob . . .
Bob . . .
| - The Matronics AeroElectric-List Email Forum - | | Use the List Feature Navigator to browse the many List utilities available such as the Email Subscriptions page, Archive Search & Download, 7-Day Browse, Chat, FAQ, Photoshare, and much more:
http://www.matronics.com/Navigator?AeroElectric-List |
|
|
|
Back to top |
|
 |
nuckolls.bob(at)aeroelect Guest
|
Posted: Sun Aug 21, 2016 11:09 am Post subject: Voltage drop |
|
|
At 11:18 AM 8/21/2016, you wrote:
Quote: | Hi Bob;
Neat and very understandable schematics for externally and internally regulated alternators. Would you care to provide one for a internally regulated, permanent magnet alternator, so as to cover the subject exhaustively? I think I can deduce same, but would feel better to have it "from the horse's mouth."
Cheers! Stu. |
I'm not sure such a critter exitsts.
The only PM alternators I'm aware
of are exceedingly simple arrays of
magnets rotated about a stator winding
of suitable wire. Check out the images
at . . .
http://tinyurl.com/z27kpv4
These are PM alternators characteristic
of all such products from the lowly SD-8 up
through the 30A, 3-phase machines on some
small tractors.
Spinning magnets, stationary wires.
The energy coming out of these machines is
an AC current with frequency and voltage
proportional to engine RPM.
This is why the 'regulators' paired with
these devices are more properly called
RECTIFIER-REGULATORS.
They must not only convert the AC to DC
(like the diodes in the wound field
alternators) they must CONTROL that voltage
through devices that must CARRY the full
load current. Hence, there are no nifty,
itty-bitty regulators like those found in
wound field machines . . . instead, the R-R
is a rather robust device obviously designed
to dissipate HEAT.
It's a whole other breed of cat . . . so
sayeth the north end of the northbound
horse.
Bob . . .
| - The Matronics AeroElectric-List Email Forum - | | Use the List Feature Navigator to browse the many List utilities available such as the Email Subscriptions page, Archive Search & Download, 7-Day Browse, Chat, FAQ, Photoshare, and much more:
http://www.matronics.com/Navigator?AeroElectric-List |
|
|
|
Back to top |
|
 |
cbirdsall6(at)cox.net Guest
|
Posted: Sun Aug 21, 2016 12:27 pm Post subject: Voltage drop |
|
|
Bob,
With respect to your 4th paragraph - I work in the TC maintenance side of the aviation industry, and have seen oil delivery system failure manifest itself first during engine start. The majority of those times the failure was either maintenance-induced or were on aircraft that have sat for extended periods with no attempt to pre-oil before starting (one of the bigger offenders in the latter in my experience has been geared, turbocharged Continentals in Cessna 400 series aircraft, for some reason). A few, however were mechanical failures that were clued-in by oil pressure goofiness.
One of those involved a pipeline patrol aircraft whose operator said that he didn't think the engine was developing full power. He also mentioned casually that the oil pressure was jumping up high right away after engine start, and had been doing that for several flights. That little tidbit led us to the oil filter, which was chock full o metal bits. (After further clue-taking the engine was replaced...)
My take on this is that oil pressure behavior is one of several clues to engine health. If the behavior departs from the norm then it's time to start asking why. It's also the last chance you get to discover that after draining the oil for an oil change, you forgot to put oil back in - before it gets turned into very expensive paper weights. It's why I'd recommend having some sort of backup for use during engine start or other times when the electrical system has failed. In the TC world that's usually a backup battery (a la G1000), but even a simple idiot light attached to an oil pressure switch would help.
Chuck
On Aug 20, 2016, at 6:06 PM, Robert L. Nuckolls, III <nuckolls.bob(at)aeroelectric.com (nuckolls.bob(at)aeroelectric.com)> wrote:
At 11:10 AM 8/20/2016, you wrote:
Quote: | The contactor normally gets a little warm--no worries there.Â
Your battery is probably just fine. My 925 does the same thing.Â
You'll need some kind of back-up battery to prevent what you're describing. I use one from TCW that works great. |
Oops . . . I stubbed my toe here. If you have any
electro-whizzies that reboot when presented with
a bus voltage below 11.0 volts . . . then they almost
certainly will reboot every time you start the engine.
I'm somewhat chagrined that folks who build and qualify
these panel mounted super-computers don't either (1)
study the real world of bus voltage behaviors during
engine start and/or (2) advise the customer that their
product WILL reboot during a start-up transient that
has ALWAYS existed on EVERY airplane.
To my mind, the simplest work-around is simply not to turn
on . . . or depend on these gizmos until after engine start.
Yeah, I know, our instructors taught us to concentrate on
the oil pressure display after engine start with a finger
on the mag switches lest the pressure not come up as expected.
But I would be interested to hear if anyone on this list
has ever experienced an failure of oil circulation that did
not manifest until right after start up. No doubt, Lindbergh
and contemporaries had good reason to worry about such things.
Those guys carried tool boxes around in the rear cockpit
with an eye toward needing off field maintenance of one
kind or another.
Now we have a new suite of technology which, for reasons
we'll never know, was NOT designed to replace
legacy instrumentation. DO-160 requires a qualified
product to (1) not be damaged by and (2) recover gracefully
from bus voltage brownouts quantified in the test
requirements document.
Problem is, graceful recovery has not been interpreted
to mean that the oil pressure display on the glass screen
needs to be as available and responsive as their steam
gage counterparts during the first few seconds after engine
start.
This leaves the system integrator (YOU) with a problem.
If you're going to pay homage to the legacy philosophy
for monitoring engine parameters that were of intense interest
to Charles Lindbergh, then we have to ADD power supply
brown-out buffers for these new electro-whizzies . . . that
COULD have been designed to accommodate such brown-outs.
The question becomes, are we adding cost, weight and complexity
to a system striving to honor a operating practice that
has been around since Lindbergh? What are the demonstrated
risks for cranking up an engine 'blind' an waiting for
the 'new' technology to wake up and report for duty?
Bob . . .
| - The Matronics AeroElectric-List Email Forum - | | Use the List Feature Navigator to browse the many List utilities available such as the Email Subscriptions page, Archive Search & Download, 7-Day Browse, Chat, FAQ, Photoshare, and much more:
http://www.matronics.com/Navigator?AeroElectric-List |
|
|
|
Back to top |
|
 |
nuckolls.bob(at)aeroelect Guest
|
Posted: Sun Aug 21, 2016 4:13 pm Post subject: Voltage drop |
|
|
At 03:24 PM 8/21/2016, you wrote:
Quote: | Bob,
With respect to your 4th paragraph - I work in the TC maintenance side of the aviation industry, and have seen oil delivery system failure manifest itself first during engine start. The majority of those times the failure was either maintenance-induced or were on aircraft that have sat for extended periods with no attempt to pre-oil before starting (one of the bigger offenders in the latter in my experience has been geared, turbocharged Continentals in Cessna 400 series aircraft, for some reason). A few, however were mechanical failures that were clued-in by oil pressure goofiness. | Yes, aviation has been plagued with numerous examples of engines that operated on the edge of self destruction . . . the C175 engines come to mind also. But again, what are the probabilities that upon starting an engine predominant in OBAM aviation aircraft that it will present with a loss of oil pressure . . . given that it taxied an airplane to parking in the not too distant past?
Further, an aviation maintenance career puts you in situations like doctors . . . who never see anyone but sick people. My last five years at Beech concentrated on a series of seemingly intractable difficulties . . . but for every airplane I touched, there were thousands that did not need or would benefit from my attention.
Quote: | My take on this is that oil pressure behavior is one of several clues to engine health. If the behavior departs from the norm then it's time to start asking why. It's also the last chance you get to discover that after draining the oil for an oil change, you forgot to put oil back in - before it gets turned into very expensive paper weights. | But do the FMEA on these hypothetical scenarios. It's one thing that a particular engine/airframe combination has a history of difficulties related to loss of oil pressure . . . is anyone here on the List flying such a machine? Forgetting to put the oil in . . . any owner/op at elevated risk for such errors has dozens of opportunities for equal if not or more hazardous examples of absent minded events.
If anyone is truly concerned about immediate notification of oil pressure after start up, I suggest that an oil pressure switch and warning light would be a simpler, lower cost, lighter weight and nearly zero maintenance solution compared with any sort of battery installation. Such switches are not subject to the effects of brown-out.
Bob . . .
| - The Matronics AeroElectric-List Email Forum - | | Use the List Feature Navigator to browse the many List utilities available such as the Email Subscriptions page, Archive Search & Download, 7-Day Browse, Chat, FAQ, Photoshare, and much more:
http://www.matronics.com/Navigator?AeroElectric-List |
|
|
|
Back to top |
|
 |
Jim Baker
Joined: 30 Mar 2006 Posts: 181 Location: Sayre, PA
|
Posted: Sun Aug 21, 2016 5:19 pm Post subject: Voltage drop |
|
|
Learned to fly a J3 with my Dad as the instructor. Even the old C65 was prone to startup oil pressure issues. Had to watch carefully to see if pressure would develop immediately after the hand prop. If not, you'd have to pull the pressure line off the back of the pump and prime it with a squirt can so the gears would have something to work with.
Jim Baker
405 426 5377
--
| - The Matronics AeroElectric-List Email Forum - | | Use the List Feature Navigator to browse the many List utilities available such as the Email Subscriptions page, Archive Search & Download, 7-Day Browse, Chat, FAQ, Photoshare, and much more:
http://www.matronics.com/Navigator?AeroElectric-List |
|
|
|
Back to top |
|
 |
ashleysc(at)broadstripe.n Guest
|
Posted: Sun Aug 21, 2016 6:16 pm Post subject: Voltage drop |
|
|
Hi Bob;
One such critter is DB Electrical APM0009, which is a 12 V., 20 Amp, internally regulated permanent magnet alternator.
Cheers! Stu.
From: "Robert L. Nuckolls, III" <nuckolls.bob(at)aeroelectric.com>
To: aeroelectric-list(at)matronics.com
Sent: Sunday, August 21, 2016 11:17:35 AM
Subject: Re: Voltage drop
At 11:18 AM 8/21/2016, you wrote:
Quote: | Hi Bob;
Neat and very understandable schematics for externally and internally regulated alternators. Would you care to provide one for a internally regulated, permanent magnet alternator, so as to cover the subject exhaustively? I think I can deduce same, but would feel better to have it "from the horse's mouth."
Cheers! Stu. |
I'm not sure such a critter exitsts.
The only PM alternators I'm aware
of are exceedingly simple arrays of
magnets rotated about a stator winding
of suitable wire. Check out the images
at . . .
http://tinyurl.com/z27kpv4
These are PM alternators characteristic
of all such products from the lowly SD-8 up
through the 30A, 3-phase machines on some
small tractors.
Spinning magnets, stationary wires.
The energy coming out of these machines is
an AC current with frequency and voltage
proportional to engine RPM.
This is why the 'regulators' paired with
these devices are more properly called
RECTIFIER-REGULATORS.
They must not only convert the AC to DC
(like the diodes in the wound field
alternators) they must CONTROL that voltage
through devices that must CARRY the full
load current. Hence, there are no nifty,
itty-bitty regulators like those found in
wound field machines . . . instead, the R-R
is a rather robust device obviously designed
to dissipate HEAT.
It's a whole other breed of cat . . . so
sayeth the north end of the northbound
horse.
Bob . . .
| - The Matronics AeroElectric-List Email Forum - | | Use the List Feature Navigator to browse the many List utilities available such as the Email Subscriptions page, Archive Search & Download, 7-Day Browse, Chat, FAQ, Photoshare, and much more:
http://www.matronics.com/Navigator?AeroElectric-List |
|
|
|
Back to top |
|
 |
ceengland7(at)gmail.com Guest
|
Posted: Mon Aug 22, 2016 6:32 am Post subject: Voltage drop |
|
|
On 8/22/2016 7:28 AM, Robert L. Nuckolls, III wrote:
Quote: | At 09:15 PM 8/21/2016, you wrote:
Quote: | Hi Bob;
One such critter is DB Electrical APM0009, which is a 12 V., 20 Amp, internally regulated permanent magnet alternator.
Cheers! Stu.
|
Cool! Thanks for the heads-up! Well, if there's
one such device, there must be others.
The really interesting thing about this amalgam
of technologies is the relative dearth of heat
dissipation features for a 20 AMP rating.
There appears to be several devices of this
style
http://tinyurl.com/jyt7wul
They have Lester numbers which suggests that
the parts are manufactured in large quantities
for the industrial/automotive world. The
Arrowhead brand is a new one too . . . pretty
big outfit.
http://tinyurl.com/hthwy29
I'm tempted to order one of these things to
'play' with.
Bob . . . I think that if you inspect that photo carefully, it's apparent that
these 'internally regulated' units are basically the original PM
alternator with the regulator bolted to the back. More convenient
packaging, perhaps, but not really different from bolting an older style
reg to the back of the old style PM alt.
|
| - The Matronics AeroElectric-List Email Forum - | | Use the List Feature Navigator to browse the many List utilities available such as the Email Subscriptions page, Archive Search & Download, 7-Day Browse, Chat, FAQ, Photoshare, and much more:
http://www.matronics.com/Navigator?AeroElectric-List |
|
|
|
Back to top |
|
 |
nuckolls.bob(at)aeroelect Guest
|
Posted: Mon Aug 22, 2016 7:18 am Post subject: Voltage drop |
|
|
Quote: | I think that if you inspect that photo carefully, it's apparent that these 'internally regulated' units are basically the original PM alternator with the regulator bolted to the back. More convenient packaging, perhaps, but not really different from bolting an older style reg to the back of the old style PM alt. |
Oh sure . . . but perhaps we're splitting
hairs . . . the rectifier-regulator is an
integral component of the assembly . . .
Had the designers added an all-enclosing
shroud or cooling plenum on the back, the
r-r could easily be deemed 'internal'
I think the most noteworthy features of this
product are the apparent output (20A) but
with nothing obvious in the way of aggressive
cooling. They may have achieved something
of an energy management ooup here.
Bob . . .
| - The Matronics AeroElectric-List Email Forum - | | Use the List Feature Navigator to browse the many List utilities available such as the Email Subscriptions page, Archive Search & Download, 7-Day Browse, Chat, FAQ, Photoshare, and much more:
http://www.matronics.com/Navigator?AeroElectric-List |
|
|
|
Back to top |
|
 |
mike(at)vision499.com Guest
|
Posted: Mon Aug 22, 2016 8:26 am Post subject: Voltage drop |
|
|
MGL makes a product called an "AVIOGUARD" that gives you a steady 13.8v
out with input between 9v and 36v.
On 2016-08-20 16:37, Michael Lazarowicz wrote:
Quote: | I was doing some checks on my RV8 electrical system that I just
finished a few weeks ago. This is a brand new plane under
construction. Before I fired up any of the Garmin G3x stuff, I tested
the usual systems , starter , fuel pump lights etc. all seemed to work
fine. I fired up the G3x and it also come on line with no problems.
Yesterday I had everything on line and tested the starter again. When
the starter turned all my other electronics died. As soon as the
starter stopped they came back on. It appears that the current draw
from the starter took the voltage available to the other Items so low
they shut down ( most of the G3X stuff shuts down below 11 volts or
so). I have a new odyssey battery 680 and it appears to be charged.
Here are my questions.
1. Battery solenoid gets warm with the battery master on. Is this
normal?
2. Could this be a battery issue?
3. What test can I perform on the solenoid, battery etc. ?
Thanks
|
| - The Matronics AeroElectric-List Email Forum - | | Use the List Feature Navigator to browse the many List utilities available such as the Email Subscriptions page, Archive Search & Download, 7-Day Browse, Chat, FAQ, Photoshare, and much more:
http://www.matronics.com/Navigator?AeroElectric-List |
|
|
|
Back to top |
|
 |
|
|
You cannot post new topics in this forum You cannot reply to topics in this forum You cannot edit your posts in this forum You cannot delete your posts in this forum You cannot vote in polls in this forum You cannot attach files in this forum You can download files in this forum
|
Powered by phpBB © 2001, 2005 phpBB Group
|