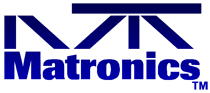 |
Matronics Email Lists Web Forum Interface to the Matronics Email Lists
|
View previous topic :: View next topic |
Author |
Message |
gtae07
Joined: 16 Jul 2017 Posts: 3 Location: Georgia
|
Posted: Mon Jul 17, 2017 6:15 am Post subject: Z14 with SDS EFI... |
|
|
I'm planning on a dual ECU SDS EFI system for my RV-7. I'm also planning to (eventually) equip for IFR. Given all that, I'm looking strongly at a Z14-based electrical architecture, but I have a few questions/concerns about it.
My plan was to split the critical engine systems and the PFDs across both battery buses, so the aircraft could run solely on one bus or the other. I wanted to maintain the ability to fly indefinitely after one failure and provide a minimum of two hours on battery power alone.
However, as I dug into it I started realizing that this plan might have a problem. Unlike the ignition, there aren't redundant injectors, so the install manual splits power for them across two (or four) separate sources for some level of redundancy (which I assume will give a rough engine but some reduced power). If I split two injectors to one bus and the other two on the second bus, I'm not fully redundant. If I lose one bus entirely, I'm down to two injectors. Plus, the way Z14 is drawn, if I lose either the main or aux contactor, that side's injectors are now running on battery power--the crossfeed doesn't help because it connects after the battery contactors.
That prompted a couple of ideas. First, is there any reason why the crosstie has to be "downstream" of the battery contactors? Could I not just place it directly between the batteries, and feed its switch through diodes off the battery bus? (I called this Mod 1 in the attached item)
Second, does anyone see a problem with feeding the injector power through diode bridges? (mod 1a)
As an expansion off that, does anyone see a problem with feeding an "engine bus" off a pair of Schottky diodes straight from the batteries? (mod 2)
Finally, does anyone see a problem with "hard wiring" (through fuses of course) components that will not draw power without the engine running--that is, the coils, injectors, and injector relays?
I've attached simple block diagrams of the above ideas. They aren't full wiring diagrams so please don't get wrapped up around wire protection or details like that yet.
| - The Matronics AeroElectric-List Email Forum - | | Use the List Feature Navigator to browse the many List utilities available such as the Email Subscriptions page, Archive Search & Download, 7-Day Browse, Chat, FAQ, Photoshare, and much more:
http://www.matronics.com/Navigator?AeroElectric-List |
|
Description: |
|
 Download |
Filename: |
electrical block diagram.pdf |
Filesize: |
75.09 KB |
Downloaded: |
598 Time(s) |
|
|
Back to top |
|
 |
yellowduckduo(at)gmail.co Guest
|
Posted: Mon Jul 17, 2017 9:28 am Post subject: Z14 with SDS EFI... |
|
|
With Z14, I run each of my separate EFI systems off it's own battery
buss on each of my two little 8 amp-Hr batteries. Neither goes thru a
battery contactor. I would not be comfortable running them thru a
contactor. There are no "battery contactors" between the crossfeed and
my batteries. I have one contactor that feeds the non engine busses
instead of a classic battery contactor that disconnects the battery. The
general advice here seems to be NOT to plan for 2 independent failures
on the same day or you tend to get tied up in overly complicated knots
with little or even sometimes negative safety advantage.
Losing half your injectors will lose MORE than half your power.
In my case I can maintain flight with one injector offline without
shaking the airplane apart. Not so much with 2 offline. I did look at
relays and feed diodes but my solution for simple operating procedures
and independent electronics was to simply weld in a second set of
injectors. It also avoided some other failure points that can take down
some dual ecu systems such as relying on a single mechanical fuel
pressure regulator that may be less reliable than the ecu's...
Two alternators plus 2 hours of battery power seems like a lot of
overkill. I can run for an unlimited time on either alternator so I
happily take advantage of small and light batteries. The crossfeed auto
closes during cranking so if the engine cranks smartly I know the
crossfeed is working which is it's operational check. Has worked well
for 11 years and 730 hours.
I can't comment on diode bridges.
Ken
On 17/07/2017 10:15 AM, gtae07 wrote:
Quote: |
I'm planning on a dual ECU SDS EFI system for my RV-7. I'm also planning to (eventually) equip for IFR. Given all that, I'm looking strongly at a Z14-based electrical architecture, but I have a few questions/concerns about it.
My plan was to split the critical engine systems and the PFDs across both battery buses, so the aircraft could run solely on one bus or the other. I wanted to maintain the ability to fly indefinitely after one failure and provide a minimum of two hours on battery power alone.
However, as I dug into it I started realizing that this plan might have a problem. Unlike the ignition, there aren't redundant injectors, so the install manual splits power for them across two (or four) separate sources for some level of redundancy (which I assume will give a rough engine but some reduced power). If I split two injectors to one bus and the other two on the second bus, I'm not fully redundant. If I lose one bus entirely, I'm down to two injectors. Plus, the way Z14 is drawn, if I lose either the main or aux contactor, that side's injectors are now running on battery power--the crossfeed doesn't help because it connects after the battery contactors.
That prompted a couple of ideas. First, is there any reason why the crosstie has to be "downstream" of the battery contactors? Could I not just place it directly between the batteries, and feed its switch through diodes off the battery bus? (I called this Mod 1 in the attached item)
Second, does anyone see a problem with feeding the injector power through diode bridges? (mod 1a)
As an expansion off that, does anyone see a problem with feeding an "engine bus" off a pair of Schottky diodes straight from the batteries? (mod 2)
Finally, does anyone see a problem with "hard wiring" (through fuses of course) components that will not draw power without the engine running--that is, the coils, injectors, and injector relays?
I've attached simple block diagrams of the above ideas. They aren't full wiring diagrams so please don't get wrapped up around wire protection or details like that yet.
Read this topic online here:
http://forums.matronics.com/viewtopic.php?p=471104#471104
Attachments:
http://forums.matronics.com//files/electrical_block_diagram_793.pdf
|
| - The Matronics AeroElectric-List Email Forum - | | Use the List Feature Navigator to browse the many List utilities available such as the Email Subscriptions page, Archive Search & Download, 7-Day Browse, Chat, FAQ, Photoshare, and much more:
http://www.matronics.com/Navigator?AeroElectric-List |
|
|
|
Back to top |
|
 |
user9253
Joined: 28 Mar 2008 Posts: 1927 Location: Riley TWP Michigan
|
Posted: Mon Jul 17, 2017 9:37 am Post subject: Re: Z14 with SDS EFI... |
|
|
gtae07,
Any of your options will work. Of them, I like MOD 1A the best. If the cross tie contactor is left on after shut down, both batteries will be run down.
Loosing a battery contactor does not cause a loss of power because power comes from the alternator, not the battery. Most alternators will keep on working if the battery is disconnected, although the voltage could be unstable.
Another option is to wire an automotive 40-amp relay in parallel with the battery contactor. The relay must be disabled during engine cranking.
| - The Matronics AeroElectric-List Email Forum - | | Use the List Feature Navigator to browse the many List utilities available such as the Email Subscriptions page, Archive Search & Download, 7-Day Browse, Chat, FAQ, Photoshare, and much more:
http://www.matronics.com/Navigator?AeroElectric-List |
|
_________________ Joe Gores |
|
Back to top |
|
 |
ceengland7(at)gmail.com Guest
|
Posted: Mon Jul 17, 2017 10:41 am Post subject: Z14 with SDS EFI... |
|
|
On 7/17/2017 9:15 AM, gtae07 wrote:
Quote: |
I'm planning on a dual ECU SDS EFI system for my RV-7. I'm also planning to (eventually) equip for IFR. Given all that, I'm looking strongly at a Z14-based electrical architecture, but I have a few questions/concerns about it.
My plan was to split the critical engine systems and the PFDs across both battery buses, so the aircraft could run solely on one bus or the other. I wanted to maintain the ability to fly indefinitely after one failure and provide a minimum of two hours on battery power alone.
However, as I dug into it I started realizing that this plan might have a problem. Unlike the ignition, there aren't redundant injectors, so the install manual splits power for them across two (or four) separate sources for some level of redundancy (which I assume will give a rough engine but some reduced power). If I split two injectors to one bus and the other two on the second bus, I'm not fully redundant. If I lose one bus entirely, I'm down to two injectors. Plus, the way Z14 is drawn, if I lose either the main or aux contactor, that side's injectors are now running on battery power--the crossfeed doesn't help because it connects after the battery contactors.
That prompted a couple of ideas. First, is there any reason why the crosstie has to be "downstream" of the battery contactors? Could I not just place it directly between the batteries, and feed its switch through diodes off the battery bus? (I called this Mod 1 in the attached item)
Second, does anyone see a problem with feeding the injector power through diode bridges? (mod 1a)
As an expansion off that, does anyone see a problem with feeding an "engine bus" off a pair of Schottky diodes straight from the batteries? (mod 2)
Finally, does anyone see a problem with "hard wiring" (through fuses of course) components that will not draw power without the engine running--that is, the coils, injectors, and injector relays?
I've attached simple block diagrams of the above ideas. They aren't full wiring diagrams so please don't get wrapped up around wire protection or details like that yet.
I can't hit every point, but do have a few thoughts. I wouldn't split
|
injector power across buses. If you lose a bus & half your injectors,
you've lost close to 75% of your power, & stuff could break just from
the abnormal firing with only two cyls working.
My choice (full disclosure: not yet flying) is to do something closer to
what you have as mod 2. My attitude is to build a good engine bus, make
sure my wiring practice is sound, and live with it, just as I live
without backups for my single pair of wings (redundant controllers on
the same bus). I have the luxury (automotive engine) of running
identical alternators, so I have only one battery. I have one engine
bus, controlled with a high current toggle switch (no contactor) fed
directly from the battery utilizing a fusible link in the feed. The
'rest of the airplane' bus is controlled by a master contactor, as is
typical. I have an emergency crossfeed switch (same high current model)
so that either bus can draw on the other, as needed. I can shut down
either alternator's output, either bus's feed (and crossfeed from the
other bus), or if there's a serious fire, I can still shut down all
electrical power if needed as a last resort ('standard' aviation design
practice).
As drawn, your mod 2 has no way to isolate anything from the batteries;
the contactors just interrupt power from the alternators. is that what
you intend? It also doesn't show the 'rest of the airplane' buss
(avionics, etc). How will that be integrated?
Charlie
---
This email has been checked for viruses by Avast antivirus software.
https://www.avast.com/antivirus
| - The Matronics AeroElectric-List Email Forum - | | Use the List Feature Navigator to browse the many List utilities available such as the Email Subscriptions page, Archive Search & Download, 7-Day Browse, Chat, FAQ, Photoshare, and much more:
http://www.matronics.com/Navigator?AeroElectric-List |
|
|
|
Back to top |
|
 |
ceengland7(at)gmail.com Guest
|
Posted: Mon Jul 17, 2017 10:47 am Post subject: Z14 with SDS EFI... |
|
|
Ken,
How big are your batteries? With two alternators you shouldn't ever need
to know battery capacity, but I can tell you that most automotive style
engine controllers (high pressure injection) will suck a PC680 dry in
about 40 minutes. That's just the electrical loads of the engine itself
+ fuel pump; no avionics, etc.
Charlie
On 7/17/2017 12:28 PM, C&K wrote:
Quote: |
With Z14, I run each of my separate EFI systems off it's own battery
buss on each of my two little 8 amp-Hr batteries. Neither goes thru a
battery contactor. I would not be comfortable running them thru a
contactor. There are no "battery contactors" between the crossfeed and
my batteries. I have one contactor that feeds the non engine busses
instead of a classic battery contactor that disconnects the battery.
The general advice here seems to be NOT to plan for 2 independent
failures on the same day or you tend to get tied up in overly
complicated knots with little or even sometimes negative safety
advantage.
Losing half your injectors will lose MORE than half your power.
In my case I can maintain flight with one injector offline without
shaking the airplane apart. Not so much with 2 offline. I did look at
relays and feed diodes but my solution for simple operating procedures
and independent electronics was to simply weld in a second set of
injectors. It also avoided some other failure points that can take
down some dual ecu systems such as relying on a single mechanical fuel
pressure regulator that may be less reliable than the ecu's...
Two alternators plus 2 hours of battery power seems like a lot of
overkill. I can run for an unlimited time on either alternator so I
happily take advantage of small and light batteries. The crossfeed
auto closes during cranking so if the engine cranks smartly I know the
crossfeed is working which is it's operational check. Has worked well
for 11 years and 730 hours.
I can't comment on diode bridges.
Ken
On 17/07/2017 10:15 AM, gtae07 wrote:
>
>
> I'm planning on a dual ECU SDS EFI system for my RV-7. I'm also
> planning to (eventually) equip for IFR. Given all that, I'm looking
> strongly at a Z14-based electrical architecture, but I have a few
> questions/concerns about it.
> My plan was to split the critical engine systems and the PFDs across
> both battery buses, so the aircraft could run solely on one bus or
> the other. I wanted to maintain the ability to fly indefinitely
> after one failure and provide a minimum of two hours on battery power
> alone.
>
> However, as I dug into it I started realizing that this plan might
> have a problem. Unlike the ignition, there aren't redundant
> injectors, so the install manual splits power for them across two (or
> four) separate sources for some level of redundancy (which I assume
> will give a rough engine but some reduced power). If I split two
> injectors to one bus and the other two on the second bus, I'm not
> fully redundant. If I lose one bus entirely, I'm down to two
> injectors. Plus, the way Z14 is drawn, if I lose either the main or
> aux contactor, that side's injectors are now running on battery
> power--the crossfeed doesn't help because it connects after the
> battery contactors.
>
> That prompted a couple of ideas. First, is there any reason why the
> crosstie has to be "downstream" of the battery contactors? Could I
> not just place it directly between the batteries, and feed its switch
> through diodes off the battery bus? (I called this Mod 1 in the
> attached item)
>
> Second, does anyone see a problem with feeding the injector power
> through diode bridges? (mod 1a)
>
> As an expansion off that, does anyone see a problem with feeding an
> "engine bus" off a pair of Schottky diodes straight from the
> batteries? (mod 2)
> Finally, does anyone see a problem with "hard wiring" (through fuses
> of course) components that will not draw power without the engine
> running--that is, the coils, injectors, and injector relays?
>
> I've attached simple block diagrams of the above ideas. They aren't
> full wiring diagrams so please don't get wrapped up around wire
> protection or details like that yet.
|
---
This email has been checked for viruses by Avast antivirus software.
https://www.avast.com/antivirus
| - The Matronics AeroElectric-List Email Forum - | | Use the List Feature Navigator to browse the many List utilities available such as the Email Subscriptions page, Archive Search & Download, 7-Day Browse, Chat, FAQ, Photoshare, and much more:
http://www.matronics.com/Navigator?AeroElectric-List |
|
|
|
Back to top |
|
 |
yellowduckduo(at)gmail.co Guest
|
Posted: Mon Jul 17, 2017 11:59 am Post subject: Z14 with SDS EFI... |
|
|
Charlie
Yes I would not want to count on my little Dekka 8 amp-hr for much more
than 10 or maybe 15 minutes at most based on my typical 16 amp primary
system load and original testing. (I run a few things like strobes off
the other alternator.) The BRL (Big Red flashing Light) low volts light
from the EIS is pretty attention getting though and it just takes a
switch flick to fix things. The second alternator certainly removes
worrying much about battery capacity. It's not a capacity check, but
these 120 CCA batteries do fairly well on 60 and 100 amp load tests
even after 5 to 12 years. Interestingly I picked up a new one a few
months ago special order at Lowes (America not Canada). $60. was a
better price than anywhere else I found on the internet and it was
manufactured in PA within the previous month.
Ken
On 17/07/2017 2:49 PM, Charlie England wrote:
Quote: |
<ceengland7(at)gmail.com>
Ken,
How big are your batteries? With two alternators you shouldn't ever
need to know battery capacity, but I can tell you that most automotive
style engine controllers (high pressure injection) will suck a PC680
dry in about 40 minutes. That's just the electrical loads of the
engine itself + fuel pump; no avionics, etc.
Charlie
On 7/17/2017 12:28 PM, C&K wrote:
>
>
> With Z14, I run each of my separate EFI systems off it's own battery
> buss on each of my two little 8 amp-Hr batteries. Neither goes thru a
> battery contactor. I would not be comfortable running them thru a
> contactor. There are no "battery contactors" between the crossfeed
> and my batteries. I have one contactor that feeds the non engine
> busses instead of a classic battery contactor that disconnects the
> battery. The general advice here seems to be NOT to plan for 2
> independent failures on the same day or you tend to get tied up in
> overly complicated knots with little or even sometimes negative
> safety advantage.
>
> Losing half your injectors will lose MORE than half your power.
>
> In my case I can maintain flight with one injector offline without
> shaking the airplane apart. Not so much with 2 offline. I did look at
> relays and feed diodes but my solution for simple operating
> procedures and independent electronics was to simply weld in a second
> set of injectors. It also avoided some other failure points that can
> take down some dual ecu systems such as relying on a single
> mechanical fuel pressure regulator that may be less reliable than the
> ecu's...
>
> Two alternators plus 2 hours of battery power seems like a lot of
> overkill. I can run for an unlimited time on either alternator so I
> happily take advantage of small and light batteries. The crossfeed
> auto closes during cranking so if the engine cranks smartly I know
> the crossfeed is working which is it's operational check. Has worked
> well for 11 years and 730 hours.
>
> I can't comment on diode bridges.
>
> Ken
> On 17/07/2017 10:15 AM, gtae07 wrote:
>>
>>
>> I'm planning on a dual ECU SDS EFI system for my RV-7. I'm also
>> planning to (eventually) equip for IFR. Given all that, I'm looking
>> strongly at a Z14-based electrical architecture, but I have a few
>> questions/concerns about it.
>>
>>
>> My plan was to split the critical engine systems and the PFDs across
>> both battery buses, so the aircraft could run solely on one bus or
>> the other. I wanted to maintain the ability to fly indefinitely
>> after one failure and provide a minimum of two hours on battery
>> power alone.
>>
>> However, as I dug into it I started realizing that this plan might
>> have a problem. Unlike the ignition, there aren't redundant
>> injectors, so the install manual splits power for them across two
>> (or four) separate sources for some level of redundancy (which I
>> assume will give a rough engine but some reduced power). If I split
>> two injectors to one bus and the other two on the second bus, I'm
>> not fully redundant. If I lose one bus entirely, I'm down to two
>> injectors. Plus, the way Z14 is drawn, if I lose either the main or
>> aux contactor, that side's injectors are now running on battery
>> power--the crossfeed doesn't help because it connects after the
>> battery contactors.
>>
>> That prompted a couple of ideas. First, is there any reason why the
>> crosstie has to be "downstream" of the battery contactors? Could I
>> not just place it directly between the batteries, and feed its
>> switch through diodes off the battery bus? (I called this Mod 1 in
>> the attached item)
>>
>> Second, does anyone see a problem with feeding the injector power
>> through diode bridges? (mod 1a)
>>
>> As an expansion off that, does anyone see a problem with feeding an
>> "engine bus" off a pair of Schottky diodes straight from the
>> batteries? (mod 2)
>>
>>
>> Finally, does anyone see a problem with "hard wiring" (through fuses
>> of course) components that will not draw power without the engine
>> running--that is, the coils, injectors, and injector relays?
>>
>> I've attached simple block diagrams of the above ideas. They aren't
>> full wiring diagrams so please don't get wrapped up around wire
>> protection or details like that yet.
---
This email has been checked for viruses by Avast antivirus software.
https://www.avast.com/antivirus
|
| - The Matronics AeroElectric-List Email Forum - | | Use the List Feature Navigator to browse the many List utilities available such as the Email Subscriptions page, Archive Search & Download, 7-Day Browse, Chat, FAQ, Photoshare, and much more:
http://www.matronics.com/Navigator?AeroElectric-List |
|
|
|
Back to top |
|
 |
ceengland7(at)gmail.com Guest
|
Posted: Mon Jul 17, 2017 1:48 pm Post subject: Z14 with SDS EFI... |
|
|
Not to get too far into the weeds, but what are you testing at 60 & 100 amps? If you're just testing whether it will grunt the load for a few seconds or minutes, it won't tell you much about how long it will last when loaded at, say, 10-20 amps (typical range of automotive style injection plus fuel pump, depending on the system). There have been in-flight tests of PC680's, and they're good for around 40 minutes to an hour, tops, when being loaded at around 10-15 amps. If you look at Odessey's spec sheet for a PC680, it's a 16 ampere-hour battery, but with a 15 amp load, it lasts for ~45 minutes; a virtually exact match for 'real world' tests. When load gets close to or above the AH rating, life gets *really* short.
8AH batteries should be a lot cheaper than that. IIRC, I've bought from Apex in the past (and several other vendors, as well, and they have pretty good prices. Here's a pair for $20:
https://www.apexbattery.com/apc-back-ups-xs-900-12v-8ah-replacement-battery-160798.html?gclid=Cj0KCQjwwLHLBRDEARIsAN1A1Q67Bm55WDDHCRfTkPBhdUZNs9zNyRdHkiBlSIlgAhFDJMFcXbHCBGsaAr2oEALw_wcB
Not sure of their shipping prices. But Amazon has them for $20 each, free shipping if you have Prime.
Charlie
On Mon, Jul 17, 2017 at 2:58 PM, C&K <yellowduckduo(at)gmail.com (yellowduckduo(at)gmail.com)> wrote:
Quote: | --> AeroElectric-List message posted by: C&K <yellowduckduo(at)gmail.com (yellowduckduo(at)gmail.com)>
Charlie
Yes I would not want to count on my little Dekka 8 amp-hr for much more than 10 or maybe 15 minutes at most based on my typical 16 amp primary system load and original testing. (I run a few things like strobes off the other alternator.) The BRL (Big Red flashing Light) low volts light from the EIS is pretty attention getting though and it just takes a switch flick to fix things. The second alternator certainly removes worrying much about battery capacity. It's not a capacity check, but these 120 CCA batteries do fairly well on 60 and 100 amp load tests even after 5 to 12 years. Interestingly I picked up a new one a few months ago special order at Lowes (America not Canada). $60. was a better price than anywhere else I found on the internet and it was manufactured in PA within the previous month.
Ken
On 17/07/2017 2:49 PM, Charlie England wrote:
Quote: | --> AeroElectric-List message posted by: Charlie England <ceengland7(at)gmail.com (ceengland7(at)gmail.com)>
Ken,
How big are your batteries? With two alternators you shouldn't ever need to know battery capacity, but I can tell you that most automotive style engine controllers (high pressure injection) will suck a PC680 dry in about 40 minutes. That's just the electrical loads of the engine itself + fuel pump; no avionics, etc.
Charlie
On 7/17/2017 12:28 PM, C&K wrote:
Quote: | --> AeroElectric-List message posted by: C&K <yellowduckduo(at)gmail.com (yellowduckduo(at)gmail.com)>
With Z14, I run each of my separate EFI systems off it's own battery buss on each of my two little 8 amp-Hr batteries. Neither goes thru a battery contactor. I would not be comfortable running them thru a contactor. There are no "battery contactors" between the crossfeed and my batteries. I have one contactor that feeds the non engine busses instead of a classic battery contactor that disconnects the battery. The general advice here seems to be NOT to plan for 2 independent failures on the same day or you tend to get tied up in overly complicated knots with little or even sometimes negative safety advantage.
Losing half your injectors will lose MORE than half your power.
In my case I can maintain flight with one injector offline without shaking the airplane apart. Not so much with 2 offline. I did look at relays and feed diodes but my solution for simple operating procedures and independent electronics was to simply weld in a second set of injectors. It also avoided some other failure points that can take down some dual ecu systems such as relying on a single mechanical fuel pressure regulator that may be less reliable than the ecu's...
Two alternators plus 2 hours of battery power seems like a lot of overkill. I can run for an unlimited time on either alternator so I happily take advantage of small and light batteries. The crossfeed auto closes during cranking so if the engine cranks smartly I know the crossfeed is working which is it's operational check. Has worked well for 11 years and 730 hours.
I can't comment on diode bridges.
Ken
On 17/07/2017 10:15 AM, gtae07 wrote:
Quote: | --> AeroElectric-List message posted by: "gtae07" <icebrain(at)gmail.com (icebrain(at)gmail.com)>
I'm planning on a dual ECU SDS EFI system for my RV-7. I'm also planning to (eventually) equip for IFR. Given all that, I'm looking strongly at a Z14-based electrical architecture, but I have a few questions/concerns about it.
My plan was to split the critical engine systems and the PFDs across both battery buses, so the aircraft could run solely on one bus or the other. I wanted to maintain the ability to fly indefinitely after one failure and provide a minimum of two hours on battery power alone.
However, as I dug into it I started realizing that this plan might have a problem. Unlike the ignition, there aren't redundant injectors, so the install manual splits power for them across two (or four) separate sources for some level of redundancy (which I assume will give a rough engine but some reduced power). If I split two injectors to one bus and the other two on the second bus, I'm not fully redundant. If I lose one bus entirely, I'm down to two injectors. Plus, the way Z14 is drawn, if I lose either the main or aux contactor, that side's injectors are now running on battery power--the crossfeed doesn't help because it connects after the battery contactors.
That prompted a couple of ideas. First, is there any reason why the crosstie has to be "downstream" of the battery contactors? Could I not just place it directly between the batteries, and feed its switch through diodes off the battery bus? (I called this Mod 1 in the attached item)
Second, does anyone see a problem with feeding the injector power through diode bridges? (mod 1a)
As an expansion off that, does anyone see a problem with feeding an "engine bus" off a pair of Schottky diodes straight from the batteries? (mod 2)
Finally, does anyone see a problem with "hard wiring" (through fuses of course) components that will not draw power without the engine running--that is, the coils, injectors, and injector relays?
I've attached simple block diagrams of the above ideas. They aren't full wiring diagrams so please don't get wrapped up around wire protection or details like that yet.
|
|
---
This email has been checked for viruses by Avast antivirus software.
https://www.avast.com/antivirus
|
====================================
-
Electric-List" rel="noreferrer" target="_blank">http://www.matronics.com/Navigator?AeroElectric-List
====================================
FORUMS -
eferrer" target="_blank">http://forums.matronics.com
====================================
WIKI -
errer" target="_blank">http://wiki.matronics.com
====================================
b Site -
-Matt Dralle, List Admin.
rel="noreferrer" target="_blank">http://www.matronics.com/contribution
====================================
|
| - The Matronics AeroElectric-List Email Forum - | | Use the List Feature Navigator to browse the many List utilities available such as the Email Subscriptions page, Archive Search & Download, 7-Day Browse, Chat, FAQ, Photoshare, and much more:
http://www.matronics.com/Navigator?AeroElectric-List |
|
|
|
Back to top |
|
 |
yellowduckduo(at)gmail.co Guest
|
Posted: Mon Jul 17, 2017 2:55 pm Post subject: Z14 with SDS EFI... |
|
|
Agree with most of what you are saying but don't forget that there are
relatively cheap standby power AGM batteries and then there are power
sports batteries that are rated and capable of cranking engines. In
that last group there are ones with proven reliability such as the
Odysey and Dekka lines. You won't find those for $20.
Ken
On 17/07/2017 5:44 PM, Charlie England wrote:
Quote: | Not to get too far into the weeds, but what are you testing at 60 &
100 amps? If you're just testing whether it will grunt the load for a
few seconds or minutes, it won't tell you much about how long it will
last when loaded at, say, 10-20 amps (typical range of automotive
style injection plus fuel pump, depending on the system). There have
been in-flight tests of PC680's, and they're good for around 40
minutes to an hour, tops, when being loaded at around 10-15 amps. If
you look at Odessey's spec sheet for a PC680, it's a 16 ampere-hour
battery, but with a 15 amp load, it lasts for ~45 minutes; a virtually
exact match for 'real world' tests. When load gets close to or above
the AH rating, life gets *really* short.
8AH batteries should be a lot cheaper than that. IIRC, I've bought
from Apex in the past (and several other vendors, as well, and they
have pretty good prices. Here's a pair for $20:
https://www.apexbattery.com/apc-back-ups-xs-900-12v-8ah-replacement-battery-160798.html?gclid=Cj0KCQjwwLHLBRDEARIsAN1A1Q67Bm55WDDHCRfTkPBhdUZNs9zNyRdHkiBlSIlgAhFDJMFcXbHCBGsaAr2oEALw_wcB
Not sure of their shipping prices. But Amazon has them for $20 each,
free shipping if you have Prime.
Charlie
On Mon, Jul 17, 2017 at 2:58 PM, C&K <yellowduckduo(at)gmail.com
<mailto:yellowduckduo(at)gmail.com>> wrote:
<yellowduckduo(at)gmail.com <mailto:yellowduckduo(at)gmail.com>>
Charlie
Yes I would not want to count on my little Dekka 8 amp-hr for much
more than 10 or maybe 15 minutes at most based on my typical 16
amp primary system load and original testing. (I run a few things
like strobes off the other alternator.) The BRL (Big Red flashing
Light) low volts light from the EIS is pretty attention getting
though and it just takes a switch flick to fix things. The second
alternator certainly removes worrying much about battery
capacity. It's not a capacity check, but these 120 CCA batteries
do fairly well on 60 and 100 amp load tests even after 5 to 12
years. Interestingly I picked up a new one a few months ago
special order at Lowes (America not Canada). $60. was a better
price than anywhere else I found on the internet and it was
manufactured in PA within the previous month.
Ken
On 17/07/2017 2:49 PM, Charlie England wrote:
<ceengland7(at)gmail.com <mailto:ceengland7(at)gmail.com>>
Ken,
How big are your batteries? With two alternators you shouldn't
ever need to know battery capacity, but I can tell you that
most automotive style engine controllers (high pressure
injection) will suck a PC680 dry in about 40 minutes. That's
just the electrical loads of the engine itself + fuel pump; no
avionics, etc.
Charlie
On 7/17/2017 12:28 PM, C&K wrote:
<yellowduckduo(at)gmail.com <mailto:yellowduckduo(at)gmail.com>>
With Z14, I run each of my separate EFI systems off it's
own battery buss on each of my two little 8 amp-Hr
batteries. Neither goes thru a battery contactor. I would
not be comfortable running them thru a contactor. There
are no "battery contactors" between the crossfeed and my
batteries. I have one contactor that feeds the non engine
busses instead of a classic battery contactor that
disconnects the battery. The general advice here seems to
be NOT to plan for 2 independent failures on the same day
or you tend to get tied up in overly complicated knots
with little or even sometimes negative safety advantage.
Losing half your injectors will lose MORE than half your
power.
In my case I can maintain flight with one injector offline
without shaking the airplane apart. Not so much with 2
offline. I did look at relays and feed diodes but my
solution for simple operating procedures and independent
electronics was to simply weld in a second set of
injectors. It also avoided some other failure points that
can take down some dual ecu systems such as relying on a
single mechanical fuel pressure regulator that may be less
reliable than the ecu's...
Two alternators plus 2 hours of battery power seems like a
lot of overkill. I can run for an unlimited time on either
alternator so I happily take advantage of small and light
batteries. The crossfeed auto closes during cranking so if
the engine cranks smartly I know the crossfeed is working
which is it's operational check. Has worked well for 11
years and 730 hours.
I can't comment on diode bridges.
Ken
On 17/07/2017 10:15 AM, gtae07 wrote:
<icebrain(at)gmail.com <mailto:icebrain(at)gmail.com>>
I'm planning on a dual ECU SDS EFI system for my
RV-7. I'm also planning to (eventually) equip for
IFR. Given all that, I'm looking strongly at a
Z14-based electrical architecture, but I have a few
questions/concerns about it.
My plan was to split the critical engine systems and
the PFDs across both battery buses, so the aircraft
could run solely on one bus or the other. I wanted to
maintain the ability to fly indefinitely after one
failure and provide a minimum of two hours on battery
power alone.
However, as I dug into it I started realizing that
this plan might have a problem. Unlike the ignition,
there aren't redundant injectors, so the install
manual splits power for them across two (or four)
separate sources for some level of redundancy (which I
assume will give a rough engine but some reduced
power). If I split two injectors to one bus and the
other two on the second bus, I'm not fully redundant.
If I lose one bus entirely, I'm down to two injectors.
Plus, the way Z14 is drawn, if I lose either the main
or aux contactor, that side's injectors are now
running on battery power--the crossfeed doesn't help
because it connects after the battery contactors.
That prompted a couple of ideas. First, is there any
reason why the crosstie has to be "downstream" of the
battery contactors? Could I not just place it directly
between the batteries, and feed its switch through
diodes off the battery bus? (I called this Mod 1 in
the attached item)
Second, does anyone see a problem with feeding the
injector power through diode bridges? (mod 1a)
As an expansion off that, does anyone see a problem
with feeding an "engine bus" off a pair of Schottky
diodes straight from the batteries? (mod 2)
Finally, does anyone see a problem with "hard wiring"
(through fuses of course) components that will not
draw power without the engine running--that is, the
coils, injectors, and injector relays?
I've attached simple block diagrams of the above
ideas. They aren't full wiring diagrams so please
don't get wrapped up around wire protection or details
like that yet.
---
This email has been checked for viruses by Avast antivirus
software.
https://www.avast.com/antivirus <https://www.avast.com/antivirus>
====================================
-
Electric-List" rel="noreferrer"
target="_blank">http://www.matronics.com/Navigator?AeroElectric-List
====================================
FORUMS -
eferrer" target="_blank">http://forums.matronics.com
====================================
WIKI -
errer" target="_blank">http://wiki.matronics.com
====================================
b Site -
-Matt Dralle, List Admin.
rel="noreferrer" target="_blank">http://www.matronics.com/contribution
====================================
|
| - The Matronics AeroElectric-List Email Forum - | | Use the List Feature Navigator to browse the many List utilities available such as the Email Subscriptions page, Archive Search & Download, 7-Day Browse, Chat, FAQ, Photoshare, and much more:
http://www.matronics.com/Navigator?AeroElectric-List |
|
|
|
Back to top |
|
 |
nuckolls.bob(at)aeroelect Guest
|
Posted: Tue Jul 18, 2017 9:17 am Post subject: Z14 with SDS EFI... |
|
|
At 09:15 AM 7/17/2017, you wrote:
Quote: | --> AeroElectric-List message posted by: "gtae07" <icebrain(at)gmail.com>
I'm planning on a dual ECU SDS EFI system for my RV-7. I'm also planning to (eventually) equip for IFR. Given all that, I'm looking strongly at a Z14-based electrical architecture, but I have a few questions/concerns about it.
My plan was to split the critical engine systems and the PFDs across both battery buses, so the aircraft could run solely on one bus or the other. I wanted to maintain the ability to fly indefinitely after one failure and provide a minimum of two hours on battery power alone. |
It seems you have abandoned the fundamental feature
of Z-14 . . .
With two alternators, you should be designing for
continued flight to intended destination using the
energy from only one of the two alternators.
Batteries are there to add stability to the system
dynamics and start the engine.
Recall that the single most reliable sources of
energy on any airplane is the judiciously maintained
battery. Then comes the engine driven alternator . . .
a more prone to failure but still a rare source
of anxiety in the cockpit.
Adding a second alternator not only sidesteps
probability of declaring an emergency because
of one alternator failure, it also reduces the
need for tailoring battery capacity(ies) to
design goals for battery-only endurance.
Have you crafted a load analysis for all electro-
whizzies needed for competent/comfortable termination
of flight?
I'm particularly mystified by the spreading of
engine critical accessories across both systems.
Z-14, as published, offers reliability on the same
order as modern biz-jets . . . better than King Airs.
Spreading things around the bus structures only
adds complexity without reducing risk.
Let's back up. You have two itty-bitty batteries
which, I presume, are used in tandem for cranking.
What size alternators? Suppose your engineering
design manager says, "Okay, load up the 4 busses
with system accessories and explain your decisions."
After you have everything hooked up, then do the
FMEA . . . what kind of failure will cause you to
re-position some switches? After re-configuration,
what new limits (if any) are imposed on the probability
of comfortable termination of flight?
Bob . . .
| - The Matronics AeroElectric-List Email Forum - | | Use the List Feature Navigator to browse the many List utilities available such as the Email Subscriptions page, Archive Search & Download, 7-Day Browse, Chat, FAQ, Photoshare, and much more:
http://www.matronics.com/Navigator?AeroElectric-List |
|
|
|
Back to top |
|
 |
a.s.elliott(at)cox.net Guest
|
Posted: Tue Jul 18, 2017 2:06 pm Post subject: Z14 with SDS EFI... |
|
|
Minor comment in line with some of the others – Why do you have/need main and aux contactors? I ran an electrically-dependent airplane (for about 5 years before I sold it) with a rock-simple marine battery selector switch with off-1-2-both positions. Used 1 alternator and 2 pc680’s and, IAW group guidance, changed one battery every year.
That said, that particular airplane had electronic ignition, but did not have EFI, and would easily run >1 hour on one battery alone. In the case of the higher loads of EFI, I might agree with using two alternators instead, one belt drive and one pad-mounted, and one battery.
FWIW,
Andy
--------------------------
Andy Elliott, N127VE, GP-4
CL: 480-695-9568
“If things seem under control, you’re just not going fast enough.” - Mario Andretti
| - The Matronics AeroElectric-List Email Forum - | | Use the List Feature Navigator to browse the many List utilities available such as the Email Subscriptions page, Archive Search & Download, 7-Day Browse, Chat, FAQ, Photoshare, and much more:
http://www.matronics.com/Navigator?AeroElectric-List |
|
|
|
Back to top |
|
 |
gtae07
Joined: 16 Jul 2017 Posts: 3 Location: Georgia
|
Posted: Wed Jul 19, 2017 3:00 am Post subject: Re: Z14 with SDS EFI... |
|
|
yellowduckduo(at)gmail.co wrote: | With Z14, I run each of my separate EFI systems off it's own battery buss on each of my two little 8 amp-Hr batteries. Neither goes thru a battery contactor. I would not be comfortable running them thru a contactor. There are no "battery contactors" between the crossfeed and my batteries. I have one contactor that feeds the non engine busses instead of a classic battery contactor that disconnects the battery. The general advice here seems to be NOT to plan for 2 independent failures on the same day or you tend to get tied up in overly complicated knots with little or even sometimes negative safety advantage. |
I'm not planning to run engine loads through any contactors. They'd all be wired right off a battery bus; some components would have their own switches and others would be hard-wired on (with a fuse to pull if needed for maintenance).
Anything going through a contactor is non-essential or an alternator.
ceengland7(at)gmail.com wrote: | I can't hit every point, but do have a few thoughts. I wouldn't split injector power across buses. If you lose a bus & half your injectors, you've lost close to 75% of your power, & stuff could break just from the abnormal firing with only two cyls working.
My choice (full disclosure: not yet flying) is to do something closer to what you have as mod 2. My attitude is to build a good engine bus, make sure my wiring practice is sound, and live with it, just as I live without backups for my single pair of wings (redundant controllers on the same bus). I have the luxury (automotive engine) of running identical alternators, so I have only one battery. I have one engine bus, controlled with a high current toggle switch (no contactor) fed directly from the battery utilizing a fusible link in the feed. The 'rest of the airplane' bus is controlled by a master contactor, as is typical. I have an emergency crossfeed switch (same high current model) so that either bus can draw on the other, as needed. I can shut down either alternator's output, either bus's feed (and crossfeed from the other bus), or if there's a serious fire, I can still shut down all electrical power if needed as a last resort ('standard' aviation design practice).
As drawn, your mod 2 has no way to isolate anything from the batteries; the contactors just interrupt power from the alternators. is that what you intend? It also doesn't show the 'rest of the airplane' buss (avionics, etc). How will that be integrated? |
"Rest of airplane" loads would come after the contactors, per usual practice. I'm not worried about those right now.
My biggest concern right now is to make sure the juice (electrical and hydrocarbon) keeps flowing to the engine. I know running on half the injectors would be bad so I'm trying to figure out a way around that. The other thing I'm trying to do is minimize the amount of switch-flipping in the cockpit, and minimize the number of contacts, break points, etc. between electrical power sources and my engine. I'm kind of weighing the options between "hard wiring" and putting a switch on either every component, or on each side of the engine bus.
nuckolls.bob(at)aeroelect wrote: | At 09:15 AM 7/17/2017, you wrote:
Quote: | --> AeroElectric-List message posted by: "gtae07" <icebrain>
I'm planning on a dual ECU SDS EFI system for my RV-7. I'm also planning to (eventually) equip for IFR. Given all that, I'm looking strongly at a Z14-based electrical architecture, but I have a few questions/concerns about it.
My plan was to split the critical engine systems and the PFDs across both battery buses, so the aircraft could run solely on one bus or the other. I wanted to maintain the ability to fly indefinitely after one failure and provide a minimum of two hours on battery power alone. |
It seems you have abandoned the fundamental feature of Z-14 . . .
With two alternators, you should be designing for continued flight to intended destination using the energy from only one of the two alternators.
Batteries are there to add stability to the system dynamics and start the engine.
Recall that the single most reliable sources of energy on any airplane is the judiciously maintained battery. Then comes the engine driven alternator . . . a more prone to failure but still a rare source of anxiety in the cockpit.
Adding a second alternator not only sidesteps probability of declaring an emergency because of one alternator failure, it also reduces the need for tailoring battery capacity(ies) to design goals for battery-only endurance.
Have you crafted a load analysis for all electro-whizzies needed for competent/comfortable termination of flight? |
I have. Engine/pump/ECU/coil and PFD load comes to about 12 amps. With radios and IFR GPS it's closer to 15 amps (IIRC; electrical budget is at work right now).
nuckolls.bob(at)aeroelect wrote: | I'm particularly mystified by the spreading of engine critical accessories across both systems. |
The idea is that each bus powers the equipment to keep the engine running by itself. So, bus 1 powers the primary ECU, the coil driven by the primary ECU, one fuel pump, etc. and it's enough to keep the engine running on its own.
The secondary bus would power the backup ECU, its coil, the other fuel pump, and the injector switching relay (which isn't powered when running the primary ECU).
The problem I ran across is that I didn't realize (until I really sat down to start planning this out) that the injectors were powered separately and just triggered by the ECU. That means I need to find a way to power all of the injectors regardless of which bus is online. Unlike ECUs, pumps, and coils, there's not a redundant set of injectors. I don't know how I'd go about installing a second set as mentioned by another poster.
nuckolls.bob(at)aeroelect wrote: | Let's back up. You have two itty-bitty batteries which, I presume, are used in tandem for cranking. What size alternators? Suppose your engineering design manager says, "Okay, load up the 4 busses with system accessories and explain your decisions." |
I'm looking at a pair of EarthX ETX900s, which which each have plenty of cranking juice on their own. Each battery could power the engine loads and PFD for about 70 minutes, or those plus IFR GPS and radios for almost 50 minutes, based on their published discharge curves.
Primary bus alternator would be 70A conventional, and the secondary bus a 20A gear-driven.
For the buses:
Main battery - primary ECU/coil/fuel pump, injectors, PFD 1, IFR GPS, (com 1?)
Aux battery - secondary ECU/coil/fuel pump, injectors, injector switching relay, PFD 2
Main bus - pitot heat, seat heat, 5VDC accessory outlets, flaps, lights
Aux bus - Com 2, ???
nuckolls.bob(at)aeroelect wrote: | After you have everything hooked up, then do the FMEA . . . what kind of failure will cause you to re-position some switches? After re-configuration, what new limits (if any) are imposed on the probability of comfortable termination of flight? |
I'm getting there. Will be working on more detailed wiring today as I'm laid up from minor surgery.
| - The Matronics AeroElectric-List Email Forum - | | Use the List Feature Navigator to browse the many List utilities available such as the Email Subscriptions page, Archive Search & Download, 7-Day Browse, Chat, FAQ, Photoshare, and much more:
http://www.matronics.com/Navigator?AeroElectric-List |
|
|
|
Back to top |
|
 |
ceengland7(at)gmail.com Guest
|
Posted: Wed Jul 19, 2017 4:28 pm Post subject: Z14 with SDS EFI... |
|
|
On 7/19/2017 6:00 AM, gtae07 wrote:
Quote: |
yellowduckduo(at)gmail.co wrote:
> With Z14, I run each of my separate EFI systems off it's own battery buss on each of my two little 8 amp-Hr batteries. Neither goes thru a battery contactor. I would not be comfortable running them thru a contactor. There are no "battery contactors" between the crossfeed and my batteries. I have one contactor that feeds the non engine busses instead of a classic battery contactor that disconnects the battery. The general advice here seems to be NOT to plan for 2 independent failures on the same day or you tend to get tied up in overly complicated knots with little or even sometimes negative safety advantage.
I'm not planning to run engine loads through any contactors. They'd all be wired right off a battery bus; some components would have their own switches and others would be hard-wired on (with a fuse to pull if needed for maintenance).
Anything going through a contactor is non-essential or an alternator.
snipped////
|
Not a requirement, but a 'typical' consideration is being able to shut
down the entire electrical system (even the engine's electrical power)
in case of fire or emergency (potential crash) landing for other
possible reasons. Lots of switches/fuses/breakers do make that harder to
manage in an emergency. Not saying don't do it; just do it with eyes
open. My choice is one bus, with two ways to power it. I can take my
system down with one *carefully placed* motion.
---
This email has been checked for viruses by Avast antivirus software.
https://www.avast.com/antivirus
| - The Matronics AeroElectric-List Email Forum - | | Use the List Feature Navigator to browse the many List utilities available such as the Email Subscriptions page, Archive Search & Download, 7-Day Browse, Chat, FAQ, Photoshare, and much more:
http://www.matronics.com/Navigator?AeroElectric-List |
|
|
|
Back to top |
|
 |
gtae07
Joined: 16 Jul 2017 Posts: 3 Location: Georgia
|
Posted: Thu Jul 20, 2017 2:19 am Post subject: Re: Z14 with SDS EFI... |
|
|
ceengland7(at)gmail.com wrote: | Not a requirement, but a 'typical' consideration is being able to shut down the entire electrical system (even the engine's electrical power) in case of fire or emergency (potential crash) landing for other possible reasons. Lots of switches/fuses/breakers do make that harder to manage in an emergency. Not saying don't do it; just do it with eyes open. My choice is one bus, with two ways to power it. I can take my system down with one *carefully placed* motion. |
That's the other thing I'm weighing out. I've accidentally killed the master switch before in another airplane (turbulence). The engine was conventional (carb/mag) but thanks to a latent fault in the EFIS backup battery that kept it from activating, I killed everything. That wasn't a big deal as I was VFR, but I don't want one switch accidentally taking down the entire engine. I suppose a way around that would be to go with my last option and just put heavy-duty switches on the engine bus, but that's another failure point...
I suppose the question is, which is more likely--a latent component/connection failure killing power to the engine, or there's a situation where I need to kill power but can't?
| - The Matronics AeroElectric-List Email Forum - | | Use the List Feature Navigator to browse the many List utilities available such as the Email Subscriptions page, Archive Search & Download, 7-Day Browse, Chat, FAQ, Photoshare, and much more:
http://www.matronics.com/Navigator?AeroElectric-List |
|
|
|
Back to top |
|
 |
ceengland7(at)gmail.com Guest
|
Posted: Thu Jul 20, 2017 4:15 am Post subject: Z14 with SDS EFI... |
|
|
On Thu, Jul 20, 2017 at 5:19 AM, gtae07 <icebrain(at)gmail.com (icebrain(at)gmail.com)> wrote:
Quote: | --> AeroElectric-List message posted by: "gtae07" <icebrain(at)gmail.com (icebrain(at)gmail.com)>
ceengland7(at)gmail.com wrote:
> Not a requirement, but a 'typical' consideration is being able to shut down the entire electrical system (even the engine's electrical power) in case of fire or emergency (potential crash) landing for other possible reasons. Lots of switches/fuses/breakers do make that harder to manage in an emergency. Not saying don't do it; just do it with eyes open. My choice is one bus, with two ways to power it. I can take my system down with one *carefully placed* motion.
That's the other thing I'm weighing out. I've accidentally killed the master switch before in another airplane (turbulence). The engine was conventional (carb/mag) but thanks to a latent fault in the EFIS backup battery that kept it from activating, I killed everything. That wasn't a big deal as I was VFR, but I don't want one switch accidentally taking down the entire engine. I suppose a way around that would be to go with my last option and just put heavy-duty switches on the engine bus, but that's another failure point...
I suppose the question is, which is more likely--a latent component/connection failure killing power to the engine, or there's a situation where I need to kill power but can't?
| Agreed on the inadvertent shutdown issue, but my way of dealing with that is, I guess, ergonomics. The 'kill everything' switches are kept away from any other commonly used switches/controls, and out of reach of any passenger, unless they reach completely across the pilot.
| - The Matronics AeroElectric-List Email Forum - | | Use the List Feature Navigator to browse the many List utilities available such as the Email Subscriptions page, Archive Search & Download, 7-Day Browse, Chat, FAQ, Photoshare, and much more:
http://www.matronics.com/Navigator?AeroElectric-List |
|
|
|
Back to top |
|
 |
Dennis Glaeser
Joined: 10 Jan 2006 Posts: 53 Location: Rochester Hills, Michigan
|
Posted: Thu Jul 20, 2017 7:46 am Post subject: Re: Z14 with SDS EFI... |
|
|
I have an all electric engine (Subaru) and put locking switches on both the main and aux ignitions and fuel pumps. Solves the inadvertent bumping issue.
All of my switches mounted low, and Up=On, so inadvertent bumps typically turn things on, not off. You can also use switch guards...
I have an SDS ignition as well - one unit for all 6 EFIs and ignitions (coil on plug). Dual power feeds (one from each battery) through diodes to the SDS unit.
The ignition and fuel pumps are powered directly from the respective battery bus (Main and Aux).
My electrical architecture is very close to Z-14 (mine was done before Z-14 was published).
I've been flying 9 years with no issues (that I didn't cause myself, like leaving the master on )
Dennis Glaeser
| - The Matronics AeroElectric-List Email Forum - | | Use the List Feature Navigator to browse the many List utilities available such as the Email Subscriptions page, Archive Search & Download, 7-Day Browse, Chat, FAQ, Photoshare, and much more:
http://www.matronics.com/Navigator?AeroElectric-List |
|
|
|
Back to top |
|
 |
|
|
You cannot post new topics in this forum You cannot reply to topics in this forum You cannot edit your posts in this forum You cannot delete your posts in this forum You cannot vote in polls in this forum You cannot attach files in this forum You can download files in this forum
|
Powered by phpBB © 2001, 2005 phpBB Group
|