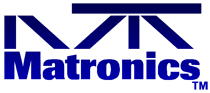 |
Matronics Email Lists Web Forum Interface to the Matronics Email Lists
|
View previous topic :: View next topic |
Author |
Message |
bsvantho
Joined: 16 Apr 2018 Posts: 3
|
Posted: Fri Apr 20, 2018 5:52 am Post subject: Z-12 contactor failure |
|
|
I know it is not a likely case, but I have experienced a contactor failure on a production plane in flight. It ended up that the root cause was a defective master switch - but the result was the same. Because there was no endurance bus alternate feed, it was a full electrical shutdown, in IMC no less!
I would like to know if there is a practical way to protect for contactor failure ( other than battery only operation ) with the Z-12 design. It would be nice to have a second path to the battery from aux alternator to ensure stable power if the master does fail. The appeal to me of having an aux alternator is to be able to continue flight on one alternator. This is only possible if either a battery connection is maintained always or it is a guarantee the alternator will provide stable power without a battery connection.
The Z-13/8 uses a relay with the SD-8 alternator to connect directly to battery. Is this design practical or even advisable with the SD-20 alternator? With Z-13/8 the aux alternator will provide power to battery bus and E-BUS if contactor fails.
Thoughts?
Thanks,
-Brendon
| - The Matronics AeroElectric-List Email Forum - | | Use the List Feature Navigator to browse the many List utilities available such as the Email Subscriptions page, Archive Search & Download, 7-Day Browse, Chat, FAQ, Photoshare, and much more:
http://www.matronics.com/Navigator?AeroElectric-List |
|
|
|
Back to top |
|
 |
BARRY CHECK 6
Joined: 15 Mar 2011 Posts: 738
|
Posted: Fri Apr 20, 2018 8:02 am Post subject: Z-12 contactor failure |
|
|
Brendon:
If the Master Switch failed why reinvent the wheel?
Since this was a certified plane you are forced to work with the design of the time.
What I have found is 99.982% of certified plane owners and A&P's, NEVER address the Master Switch during Annual.
It should be addressed every Annual and it is very easy to do:
1 - Spray the heck out of it with Contact Cleaner.
2 - Cycle the switch a couple of dozen times.
3 - Spray it with WD-40.
Side Note: This also goes for the micro-switch in the Stall Warning System.
On Experimental Aircraft you have a HUGE ADVANTAGE...
Use a Heavy Duty Master Switch and a Separate Heavy Duty Alternator Switch.
I use DPST switches and tie BOTH sides together. This DOUBLES the physical as well as the electrical rating of the switch.
Want to go extra fancy? Look for switches that are Sliver Plated.
You can also use switches that have a built in Dust/Moisture shield. OR... Install the dust/Moisture shield over the Toggle Lever.
Side Note: On certified planes with the standard split Master/Alt Switch, there are four (4) failure points:
1 - The Physical snap action of the switch.
2 - The Electrical contacts of the switch.
3 - Fast-On tabs on the back of the switch.
4 - The Physical MOUNTING of the switch. There is a snap in bezel that holds the switch into the panel.
This bezel fails as the ears either break off or loose their spring action.
Then the switch vibrates forward and shorts out to the aluminum panel.
The cure is to use two (2) sheet metal round head screws on either side to hold the bezel in place.
If the switch vibrates out it will short out and take your Master/Alt switch and Starter Relay out of the circuit.
If you are airborne - You loose even the ability to go to Battery Back-up.
Or do an in-flight re-start.
Scary!
Barry
On Fri, Apr 20, 2018 at 9:52 AM, bsvantho <bsvantho(at)gmail.com (bsvantho(at)gmail.com)> wrote:
Quote: | --> AeroElectric-List message posted by: "bsvantho" <bsvantho(at)gmail.com (bsvantho(at)gmail.com)>
I know it is not a likely case, but I have experienced a contactor failure on a production plane in flight. It ended up that the root cause was a defective master switch - but the result was the same. Because there was no endurance bus alternate feed, it was a full electrical shutdown, in IMC no less!
I would like to know if there is a practical way to protect for contactor failure ( other than battery only operation ) with the Z-12 design. It would be nice to have a second path to the battery from aux alternator to ensure stable power if the master does fail. The appeal to me of having an aux alternator is to be able to continue flight on one alternator. This is only possible if either a battery connection is maintained always or it is a guarantee the alternator will provide stable power without a battery connection.
The Z-13/8 uses a relay with the SD-8 alternator to connect directly to battery. Is this design practical or even advisable with the SD-20 alternator? With Z-13/8 the aux alternator will provide power to battery bus and E-BUS if contactor fails.
Thoughts?
Thanks,
-Brendon
Read this topic online here:
http://forums.matronics.com/viewtopic.php?p=479453#479453
====================================
-
Electric-List" rel="noreferrer" target="_blank">http://www.matronics.com/Navigator?AeroElectric-List
====================================
FORUMS -
eferrer" target="_blank">http://forums.matronics.com
====================================
WIKI -
errer" target="_blank">http://wiki.matronics.com
====================================
b Site -
-Matt Dralle, List Admin.
rel="noreferrer" target="_blank">http://www.matronics.com/contribution
====================================
|
| - The Matronics AeroElectric-List Email Forum - | | Use the List Feature Navigator to browse the many List utilities available such as the Email Subscriptions page, Archive Search & Download, 7-Day Browse, Chat, FAQ, Photoshare, and much more:
http://www.matronics.com/Navigator?AeroElectric-List |
|
|
|
Back to top |
|
 |
bob.verwey(at)gmail.com Guest
|
Posted: Fri Apr 20, 2018 8:27 am Post subject: Z-12 contactor failure |
|
|
Barry I can't see how applying a lubricant like WD40 can be advantageous to the contacts on the switch...surely there will be burning volatiles or lube which would affect the service or life of the part? On the moving parts yes but I don't know of a way to differentiate with a spray can.
On Fri, 20 Apr 2018, 6:13 PM FLYaDIVE <flyadive(at)gmail.com (flyadive(at)gmail.com)> wrote:
Quote: | Brendon:
If the Master Switch failed why reinvent the wheel?
Since this was a certified plane you are forced to work with the design of the time.
What I have found is 99.982% of certified plane owners and A&P's, NEVER address the Master Switch during Annual.
It should be addressed every Annual and it is very easy to do:
1 - Spray the heck out of it with Contact Cleaner.
2 - Cycle the switch a couple of dozen times.
3 - Spray it with WD-40.
Side Note: This also goes for the micro-switch in the Stall Warning System.
On Experimental Aircraft you have a HUGE ADVANTAGE...
Use a Heavy Duty Master Switch and a Separate Heavy Duty Alternator Switch.
I use DPST switches and tie BOTH sides together. This DOUBLES the physical as well as the electrical rating of the switch.
Want to go extra fancy? Look for switches that are Sliver Plated.
You can also use switches that have a built in Dust/Moisture shield. OR... Install the dust/Moisture shield over the Toggle Lever.
Side Note: On certified planes with the standard split Master/Alt Switch, there are four (4) failure points:
1 - The Physical snap action of the switch.
2 - The Electrical contacts of the switch.
3 - Fast-On tabs on the back of the switch.
4 - The Physical MOUNTING of the switch. There is a snap in bezel that holds the switch into the panel.
This bezel fails as the ears either break off or loose their spring action.
Then the switch vibrates forward and shorts out to the aluminum panel.
The cure is to use two (2) sheet metal round head screws on either side to hold the bezel in place.
If the switch vibrates out it will short out and take your Master/Alt switch and Starter Relay out of the circuit.
If you are airborne - You loose even the ability to go to Battery Back-up.
Or do an in-flight re-start.
Scary!
Barry
On Fri, Apr 20, 2018 at 9:52 AM, bsvantho <bsvantho(at)gmail.com (bsvantho(at)gmail.com)> wrote:
Quote: | --> AeroElectric-List message posted by: "bsvantho" <bsvantho(at)gmail.com (bsvantho(at)gmail.com)>
I know it is not a likely case, but I have experienced a contactor failure on a production plane in flight. It ended up that the root cause was a defective master switch - but the result was the same. Because there was no endurance bus alternate feed, it was a full electrical shutdown, in IMC no less!
I would like to know if there is a practical way to protect for contactor failure ( other than battery only operation ) with the Z-12 design. It would be nice to have a second path to the battery from aux alternator to ensure stable power if the master does fail. The appeal to me of having an aux alternator is to be able to continue flight on one alternator. This is only possible if either a battery connection is maintained always or it is a guarantee the alternator will provide stable power without a battery connection.
The Z-13/8 uses a relay with the SD-8 alternator to connect directly to battery. Is this design practical or even advisable with the SD-20 alternator? With Z-13/8 the aux alternator will provide power to battery bus and E-BUS if contactor fails.
Thoughts?
Thanks,
-Brendon
Read this topic online here:
http://forums.matronics.com/viewtopic.php?p=479453#479453
===========
-
Electric-List" rel="noreferrer" target="_blank">http://www.matronics.com/Navigator?AeroElectric-List
===========
FORUMS -
eferrer" target="_blank">http://forums.matronics.com
===========
WIKI -
errer" target="_blank">http://wiki.matronics.com
===========
b Site -
-Matt Dralle, List Admin.
rel="noreferrer" target="_blank">http://www.matronics.com/contribution
===========
|
|
| - The Matronics AeroElectric-List Email Forum - | | Use the List Feature Navigator to browse the many List utilities available such as the Email Subscriptions page, Archive Search & Download, 7-Day Browse, Chat, FAQ, Photoshare, and much more:
http://www.matronics.com/Navigator?AeroElectric-List |
|
|
|
Back to top |
|
 |
BARRY CHECK 6
Joined: 15 Mar 2011 Posts: 738
|
Posted: Fri Apr 20, 2018 9:43 am Post subject: Z-12 contactor failure |
|
|
Bob:
Yup! There are all sorts of 'possible' possibilities, all without proof, but it DOES WORK!
Many of our aircraft are 40+ years old. The original lubricants in the switches have long disappeared.
They are NOT sealed switches.
What has worked for many years are now failing. Just look Brandon's post.
And, when it comes to the Stall Warning micro switch - Replacement with NEW is $1200+ used, about $600 to $700.
All this can be prevented with a can of WD-40!
Not needed on sealed DPST Toggle Switches. AND they are NOT 40+ years old.
Barry
On Fri, Apr 20, 2018 at 12:25 PM, Bob Verwey <bob.verwey(at)gmail.com (bob.verwey(at)gmail.com)> wrote:
Quote: | Barry I can't see how applying a lubricant like WD40 can be advantageous to the contacts on the switch...surely there will be burning volatiles or lube which would affect the service or life of the part? On the moving parts yes but I don't know of a way to differentiate with a spray can.
On Fri, 20 Apr 2018, 6:13 PM FLYaDIVE <flyadive(at)gmail.com (flyadive(at)gmail.com)> wrote:
Quote: | Brendon:
If the Master Switch failed why reinvent the wheel?
Since this was a certified plane you are forced to work with the design of the time.
What I have found is 99.982% of certified plane owners and A&P's, NEVER address the Master Switch during Annual.
It should be addressed every Annual and it is very easy to do:
1 - Spray the heck out of it with Contact Cleaner.
2 - Cycle the switch a couple of dozen times.
3 - Spray it with WD-40.
Side Note: This also goes for the micro-switch in the Stall Warning System.
On Experimental Aircraft you have a HUGE ADVANTAGE...
Use a Heavy Duty Master Switch and a Separate Heavy Duty Alternator Switch.
I use DPST switches and tie BOTH sides together. This DOUBLES the physical as well as the electrical rating of the switch.
Want to go extra fancy? Look for switches that are Sliver Plated.
You can also use switches that have a built in Dust/Moisture shield. OR... Install the dust/Moisture shield over the Toggle Lever.
Side Note: On certified planes with the standard split Master/Alt Switch, there are four (4) failure points:
1 - The Physical snap action of the switch.
2 - The Electrical contacts of the switch.
3 - Fast-On tabs on the back of the switch.
4 - The Physical MOUNTING of the switch. There is a snap in bezel that holds the switch into the panel.
This bezel fails as the ears either break off or loose their spring action.
Then the switch vibrates forward and shorts out to the aluminum panel.
The cure is to use two (2) sheet metal round head screws on either side to hold the bezel in place.
If the switch vibrates out it will short out and take your Master/Alt switch and Starter Relay out of the circuit.
If you are airborne - You loose even the ability to go to Battery Back-up.
Or do an in-flight re-start.
Scary!
Barry
On Fri, Apr 20, 2018 at 9:52 AM, bsvantho <bsvantho(at)gmail.com (bsvantho(at)gmail.com)> wrote:
Quote: | --> AeroElectric-List message posted by: "bsvantho" <bsvantho(at)gmail.com (bsvantho(at)gmail.com)>
I know it is not a likely case, but I have experienced a contactor failure on a production plane in flight. It ended up that the root cause was a defective master switch - but the result was the same. Because there was no endurance bus alternate feed, it was a full electrical shutdown, in IMC no less!
I would like to know if there is a practical way to protect for contactor failure ( other than battery only operation ) with the Z-12 design. It would be nice to have a second path to the battery from aux alternator to ensure stable power if the master does fail. The appeal to me of having an aux alternator is to be able to continue flight on one alternator. This is only possible if either a battery connection is maintained always or it is a guarantee the alternator will provide stable power without a battery connection.
The Z-13/8 uses a relay with the SD-8 alternator to connect directly to battery. Is this design practical or even advisable with the SD-20 alternator? With Z-13/8 the aux alternator will provide power to battery bus and E-BUS if contactor fails.
Thoughts?
Thanks,
-Brendon
Read this topic online here:
http://forums.matronics.com/viewtopic.php?p=479453#479453
===========
-
Electric-List" rel="noreferrer" target="_blank">http://www.matronics.com/Navigator?AeroElectric-List
===========
FORUMS -
eferrer" target="_blank">http://forums.matronics.com
===========
WIKI -
errer" target="_blank">http://wiki.matronics.com
===========
b Site -
-Matt Dralle, List Admin.
rel="noreferrer" target="_blank">http://www.matronics.com/contribution
===========
|
|
|
| - The Matronics AeroElectric-List Email Forum - | | Use the List Feature Navigator to browse the many List utilities available such as the Email Subscriptions page, Archive Search & Download, 7-Day Browse, Chat, FAQ, Photoshare, and much more:
http://www.matronics.com/Navigator?AeroElectric-List |
|
|
|
Back to top |
|
 |
alec(at)alecmyers.com Guest
|
Posted: Fri Apr 20, 2018 9:53 am Post subject: Z-12 contactor failure |
|
|
Calling WD40 "a lubricant" is like calling a 1969 Chateauneuf “a liquid”!
On Apr 20, 2018, at 1:41 PM, FLYaDIVE <flyadive(at)gmail.com> wrote:
Bob:
Yup! There are all sorts of 'possible' possibilities, all without proof, but it DOES WORK!
Many of our aircraft are 40+ years old. The original lubricants in the switches have long disappeared.
They are NOT sealed switches.
What has worked for many years are now failing. Just look Brandon's post.
And, when it comes to the Stall Warning micro switch - Replacement with NEW is $1200+ used, about $600 to $700.
All this can be prevented with a can of WD-40!
Not needed on sealed DPST Toggle Switches. AND they are NOT 40+ years old.
Barry
On Fri, Apr 20, 2018 at 12:25 PM, Bob Verwey <bob.verwey(at)gmail.com> wrote:
Barry I can't see how applying a lubricant like WD40 can be advantageous to the contacts on the switch...surely there will be burning volatiles or lube which would affect the service or life of the part? On the moving parts yes but I don't know of a way to differentiate with a spray can.
On Fri, 20 Apr 2018, 6:13 PM FLYaDIVE <flyadive(at)gmail.com> wrote:
Brendon:
If the Master Switch failed why reinvent the wheel?
Since this was a certified plane you are forced to work with the design of the time.
What I have found is 99.982% of certified plane owners and A&P's, NEVER address the Master Switch during Annual.
It should be addressed every Annual and it is very easy to do:
1 - Spray the heck out of it with Contact Cleaner.
2 - Cycle the switch a couple of dozen times.
3 - Spray it with WD-40.
Side Note: This also goes for the micro-switch in the Stall Warning System.
On Experimental Aircraft you have a HUGE ADVANTAGE...
Use a Heavy Duty Master Switch and a Separate Heavy Duty Alternator Switch.
I use DPST switches and tie BOTH sides together. This DOUBLES the physical as well as the electrical rating of the switch.
Want to go extra fancy? Look for switches that are Sliver Plated.
You can also use switches that have a built in Dust/Moisture shield. OR... Install the dust/Moisture shield over the Toggle Lever.
Side Note: On certified planes with the standard split Master/Alt Switch, there are four (4) failure points:
1 - The Physical snap action of the switch.
2 - The Electrical contacts of the switch.
3 - Fast-On tabs on the back of the switch.
4 - The Physical MOUNTING of the switch. There is a snap in bezel that holds the switch into the panel.
This bezel fails as the ears either break off or loose their spring action.
Then the switch vibrates forward and shorts out to the aluminum panel.
The cure is to use two (2) sheet metal round head screws on either side to hold the bezel in place.
If the switch vibrates out it will short out and take your Master/Alt switch and Starter Relay out of the circuit.
If you are airborne - You loose even the ability to go to Battery Back-up.
Or do an in-flight re-start.
Scary!
Barry
On Fri, Apr 20, 2018 at 9:52 AM, bsvantho <bsvantho(at)gmail.com> wrote:
I know it is not a likely case, but I have experienced a contactor failure on a production plane in flight. It ended up that the root cause was a defective master switch - but the result was the same. Because there was no endurance bus alternate feed, it was a full electrical shutdown, in IMC no less!
I would like to know if there is a practical way to protect for contactor failure ( other than battery only operation ) with the Z-12 design. It would be nice to have a second path to the battery from aux alternator to ensure stable power if the master does fail. The appeal to me of having an aux alternator is to be able to continue flight on one alternator. This is only possible if either a battery connection is maintained always or it is a guarantee the alternator will provide stable power without a battery connection.
The Z-13/8 uses a relay with the SD-8 alternator to connect directly to battery. Is this design practical or even advisable with the SD-20 alternator? With Z-13/8 the aux alternator will provide power to battery bus and E-BUS if contactor fails.
Thoughts?
Thanks,
-Brendon
Read this topic online here:
http://forums.matronics.com/viewtopic.php?p=479453#479453
===========
-
Electric-List" rel="noreferrer" target="_blank">http://www.matronics.com/Navigator?AeroElectric-List
===========
FORUMS -
eferrer" target="_blank">http://forums.matronics.com
===========
WIKI -
errer" target="_blank">http://wiki.matronics.com
===========
b Site -
-Matt Dralle, List Admin.
rel="noreferrer" target="_blank">http://www.matronics.com/contribution
===========
| - The Matronics AeroElectric-List Email Forum - | | Use the List Feature Navigator to browse the many List utilities available such as the Email Subscriptions page, Archive Search & Download, 7-Day Browse, Chat, FAQ, Photoshare, and much more:
http://www.matronics.com/Navigator?AeroElectric-List |
|
|
|
Back to top |
|
 |
BARRY CHECK 6
Joined: 15 Mar 2011 Posts: 738
|
Posted: Fri Apr 20, 2018 10:38 am Post subject: Z-12 contactor failure |
|
|
Not calling it a lubricant is proof you consumed too much 1969 Chateauneuf.
I guess you don't call soapstone a lubricant either!
On Fri, Apr 20, 2018 at 1:52 PM, Alec Myers <alec(at)alecmyers.com> wrote:
[quote]
Calling WD40 "a lubricant" is like calling a 1969 Chateauneuf “a liquid”!
On Apr 20, 2018, at 1:41 PM, FLYaDIVE <flyadive(at)gmail.com> wrote:
Bob:
Yup! There are all sorts of 'possible' possibilities, all without proof,
but it DOES WORK!
Many of our aircraft are 40+ years old. The original lubricants in the
switches have long disappeared.
They are NOT sealed switches.
What has worked for many years are now failing. Just look Brandon's post
| - The Matronics AeroElectric-List Email Forum - | | Use the List Feature Navigator to browse the many List utilities available such as the Email Subscriptions page, Archive Search & Download, 7-Day Browse, Chat, FAQ, Photoshare, and much more:
http://www.matronics.com/Navigator?AeroElectric-List |
|
|
|
Back to top |
|
 |
bsvantho
Joined: 16 Apr 2018 Posts: 3
|
Posted: Fri Apr 20, 2018 11:18 am Post subject: Re: Z-12 contactor failure |
|
|
Agree the certified electrical system is much weaker and I found first hand that master switches are not well maintained, but I will attempt to bring this back around to the intent of my original post...
Not trying to reinvent anything. This will most likely remain a philosophical discussion for me as Z-12 is already quite robust as compared to the certified planes I fly in that E-bus devices will still be available on battery + internal battery backups, etc.
I have found very little information specific to protecting for master contactor failure. So is the philosophy for Z-12 that it is not worth worrying about since E-bus will still operate? I can accept this, I just am confused when I see Z-13/8 that connects the alternator on the battery side. Can anyone explain the reason for the difference?
Thanks,
-Brendon
| - The Matronics AeroElectric-List Email Forum - | | Use the List Feature Navigator to browse the many List utilities available such as the Email Subscriptions page, Archive Search & Download, 7-Day Browse, Chat, FAQ, Photoshare, and much more:
http://www.matronics.com/Navigator?AeroElectric-List |
|
|
|
Back to top |
|
 |
BARRY CHECK 6
Joined: 15 Mar 2011 Posts: 738
|
Posted: Fri Apr 20, 2018 12:30 pm Post subject: Z-12 contactor failure |
|
|
Brendon:
Here is the schematic of the Z-13/8
http://www.aeroelectric.com/PPS/Adobe_Architecture_Pdfs/Z13-8T.pdf
The NOTES are not on this schematic.
But, you can see the Alternator is on the LOAD side of Relay / Battery Contactor. So, the relay has to be closed
for Alternator to function.
I could not find a link for the Z-12 ;-(
But, consider this:
Many people like a Avionics Master Switch.
The switch itself has a BACK-UP.
It is usually a SECOND heavy duty switch either in Parallel with the main Avionics Master Switch <-- Used when the Main switch is the ONLY means closing the circuit.
The other location is across a Avionics Master Relay. The Main Avionics Master Switch closes a Relay <-- Not the best way of doing things but it works. So, when the BACK-UP Avionics Master Switch is closed it bypasses the relay and applies power to the Avionics circuit.
Using this same type of configuration you can use for the MASTER SWITCH. Put a BACK-UP Master Switch in Parallel with the Main Master Switch. The only problem there is you have to REMEMBER to Shut Off the MAIN MASTER SWITCH and Double Check that the BACK-UP switch is OFF.
Totally doable on Experimental. Not doable on certified, not without a 337!
Barry
On Fri, Apr 20, 2018 at 3:18 PM, bsvantho <bsvantho(at)gmail.com (bsvantho(at)gmail.com)> wrote:
Quote: | --> AeroElectric-List message posted by: "bsvantho" <bsvantho(at)gmail.com (bsvantho(at)gmail.com)>
Agree the certified electrical system is much weaker and I found first hand that master switches are not well maintained, but I will attempt to bring this back around to the intent of my original post...
Not trying to reinvent anything. This will most likely remain a philosophical discussion for me as Z-12 is already quite robust as compared to the certified planes I fly in that E-bus devices will still be available on battery + internal battery backups, etc.
I have found very little information specific to protecting for master contactor failure. So is the philosophy for Z-12 that it is not worth worrying about since E-bus will still operate? I can accept this, I just am confused when I see Z-13/8 that connects the alternator on the battery side. Can anyone explain the reason for the difference?
Thanks,
-Brendon
Read this topic online here:
http://forums.matronics.com/viewtopic.php?p=479462#479462
====================================
-
Electric-List" rel="noreferrer" target="_blank">http://www.matronics.com/Navigator?AeroElectric-List
====================================
FORUMS -
eferrer" target="_blank">http://forums.matronics.com
====================================
WIKI -
errer" target="_blank">http://wiki.matronics.com
====================================
b Site -
-Matt Dralle, List Admin.
rel="noreferrer" target="_blank">http://www.matronics.com/contribution
====================================
|
| - The Matronics AeroElectric-List Email Forum - | | Use the List Feature Navigator to browse the many List utilities available such as the Email Subscriptions page, Archive Search & Download, 7-Day Browse, Chat, FAQ, Photoshare, and much more:
http://www.matronics.com/Navigator?AeroElectric-List |
|
|
|
Back to top |
|
 |
ceengland7(at)gmail.com Guest
|
Posted: Fri Apr 20, 2018 12:49 pm Post subject: Z-12 contactor failure |
|
|
On 4/20/2018 2:18 PM, bsvantho wrote:
Quote: |
Agree the certified electrical system is much weaker and I found first hand that master switches are not well maintained, but I will attempt to bring this back around to the intent of my original post...
Not trying to reinvent anything. This will most likely remain a philosophical discussion for me as Z-12 is already quite robust as compared to the certified planes I fly in that E-bus devices will still be available on battery + internal battery backups, etc.
I have found very little information specific to protecting for master contactor failure. So is the philosophy for Z-12 that it is not worth worrying about since E-bus will still operate? I can accept this, I just am confused when I see Z-13/8 that connects the alternator on the battery side. Can anyone explain the reason for the difference?
Thanks,
-Brendon
I *think* that what you're seeing in z13-8 is that the primary alt is
|
connected conventionally, to the bus side of the master contactor. The
*backup* (much lower current capability) alt is connected to the battery
side of the contactor, so that in the event of a primary alt failure,
you can shed the load of the main bus *and* the load of the master
contactor (coil consumes 1/2-1 1/2 amps just to keep it engaged), and
still have the backup alt available to sustain the battery bus and
endurance bus. If it was on the other side of the master contactor, you
couldn't shed the main bus and contactor loads in the event of a main
alt failure.
Charlie
---
This email has been checked for viruses by Avast antivirus software.
https://www.avast.com/antivirus
| - The Matronics AeroElectric-List Email Forum - | | Use the List Feature Navigator to browse the many List utilities available such as the Email Subscriptions page, Archive Search & Download, 7-Day Browse, Chat, FAQ, Photoshare, and much more:
http://www.matronics.com/Navigator?AeroElectric-List |
|
|
|
Back to top |
|
 |
bsvantho
Joined: 16 Apr 2018 Posts: 3
|
Posted: Fri Apr 20, 2018 1:13 pm Post subject: Re: Z-12 contactor failure |
|
|
ceengland7(at)gmail.com wrote: | On 4/20/2018 2:18 PM, bsvantho wrote:
Quote: |
Agree the certified electrical system is much weaker and I found first hand that master switches are not well maintained, but I will attempt to bring this back around to the intent of my original post...
Not trying to reinvent anything. This will most likely remain a philosophical discussion for me as Z-12 is already quite robust as compared to the certified planes I fly in that E-bus devices will still be available on battery + internal battery backups, etc.
I have found very little information specific to protecting for master contactor failure. So is the philosophy for Z-12 that it is not worth worrying about since E-bus will still operate? I can accept this, I just am confused when I see Z-13/8 that connects the alternator on the battery side. Can anyone explain the reason for the difference?
Thanks,
-Brendon
I *think* that what you're seeing in z13-8 is that the primary alt is
|
connected conventionally, to the bus side of the master contactor. The
*backup* (much lower current capability) alt is connected to the battery
side of the contactor, so that in the event of a primary alt failure,
you can shed the load of the main bus *and* the load of the master
contactor (coil consumes 1/2-1 1/2 amps just to keep it engaged), and
still have the backup alt available to sustain the battery bus and
endurance bus. If it was on the other side of the master contactor, you
couldn't shed the main bus and contactor loads in the event of a main
alt failure.
Charlie
---
This email has been checked for viruses by Avast antivirus software.
https://www.avast.com/antivirus |
This makes perfect sense to me. Now look at Z-12 - the primary and backup alternators are both connected the same way - to the main bus. If you turn off the master both alternators are isolated from the battery. This means battery only operation unless the alternators remain stable without battery. Why do it this way? The only difference I see is the backup alternator is the larger 20A vs 8A.
To ask another way. Why not connect the larger 20A backup alternator in the same way as Z-13/8 ( with relay and switch )? Is this not advisable due to the higher current being switched or some other reason?
-Brendon
| - The Matronics AeroElectric-List Email Forum - | | Use the List Feature Navigator to browse the many List utilities available such as the Email Subscriptions page, Archive Search & Download, 7-Day Browse, Chat, FAQ, Photoshare, and much more:
http://www.matronics.com/Navigator?AeroElectric-List |
|
|
|
Back to top |
|
 |
ceengland7(at)gmail.com Guest
|
Posted: Fri Apr 20, 2018 1:51 pm Post subject: Z-12 contactor failure |
|
|
On 4/20/2018 4:13 PM, bsvantho wrote:
Quote: |
ceengland7(at)gmail.com wrote:
> On 4/20/2018 2:18 PM, bsvantho wrote:
>
>>
>>
>> Agree the certified electrical system is much weaker and I found first hand that master switches are not well maintained, but I will attempt to bring this back around to the intent of my original post...
>>
>> Not trying to reinvent anything. This will most likely remain a philosophical discussion for me as Z-12 is already quite robust as compared to the certified planes I fly in that E-bus devices will still be available on battery + internal battery backups, etc.
>>
>> I have found very little information specific to protecting for master contactor failure. So is the philosophy for Z-12 that it is not worth worrying about since E-bus will still operate? I can accept this, I just am confused when I see Z-13/8 that connects the alternator on the battery side. Can anyone explain the reason for the difference?
>>
>> Thanks,
>>
>> -Brendon
>>
>> I *think* that what you're seeing in z13-8 is that the primary alt is
>>
> connected conventionally, to the bus side of the master contactor. The
> *backup* (much lower current capability) alt is connected to the battery
> side of the contactor, so that in the event of a primary alt failure,
> you can shed the load of the main bus *and* the load of the master
> contactor (coil consumes 1/2-1 1/2 amps just to keep it engaged), and
> still have the backup alt available to sustain the battery bus and
> endurance bus. If it was on the other side of the master contactor, you
> couldn't shed the main bus and contactor loads in the event of a main
> alt failure.
>
> Charlie
>
> ---
> This email has been checked for viruses by Avast antivirus software.
> https://www.avast.com/antivirus
This makes perfect sense to me. Now look at Z-12 - the primary and backup alternators are both connected the same way - to the main bus. If you turn off the master both alternators are isolated from the battery. This means battery only operation unless the alternators remain stable without battery. Why do it this way? The only difference I see is the backup alternator is the larger 20A vs 8A.
To ask another way. Why not connect the larger 20A backup alternator in the same way as Z-13/8 ( with relay and switch )? Is this not advisable due to the higher current being switched or some other reason?
-Brendon
I'd bet that the reason is implied in the text descriptions preceding
|
the drawings. With the bigger backup alt, there's no reason to turn off
the master (except fire, in which case you want the alternators off line
just like the rest of the electrical system). Note also that the larger
backup alt uses an external regulator to supply field voltage, so the
regulator would have to be moved to the endurance bus, as well, if you
intend to shut off the master & keep the backup on line.
I confess it's been a while since I studied the diagrams, but they've
endured for quite a while with people prodding at them, so I suspect
that the real issue is discovering the logic, rather than questioning
whether there is logic. 
| - The Matronics AeroElectric-List Email Forum - | | Use the List Feature Navigator to browse the many List utilities available such as the Email Subscriptions page, Archive Search & Download, 7-Day Browse, Chat, FAQ, Photoshare, and much more:
http://www.matronics.com/Navigator?AeroElectric-List |
|
|
|
Back to top |
|
 |
nuckolls.bob(at)aeroelect Guest
|
Posted: Fri Apr 20, 2018 2:22 pm Post subject: Z-12 contactor failure |
|
|
At 03:28 PM 4/20/2018, you wrote:
not necessarily so . . . some alternators
need some help from the battery to get
started but once excited and on-line, they
will continue to function even if the battery
contactor is opened
Bonanzas and Barons are fitted with alternators
that self excite . . . the alternator(s) and
battery are on separate switches. The POH speaks
to alternator-only operations which are permissable.
The e-bus is a work-around for contactor failure.
The s/b alternator in z13/8 will come on line
whether or not the battery contactor is closed.
Contactor failure in flight is exceedingly rare.
A contactor that's going bad will offer some issues
for getting the engine started . . . your FIRST
and very valuable clue that it's time to change
the puppy out.
So what's the source of the heartburn over contactor
failures?
Bob . . .
| - The Matronics AeroElectric-List Email Forum - | | Use the List Feature Navigator to browse the many List utilities available such as the Email Subscriptions page, Archive Search & Download, 7-Day Browse, Chat, FAQ, Photoshare, and much more:
http://www.matronics.com/Navigator?AeroElectric-List |
|
|
|
Back to top |
|
 |
nuckolls.bob(at)aeroelect Guest
|
Posted: Sat Apr 21, 2018 4:39 am Post subject: Z-12 contactor failure |
|
|
Agree the certified electrical system is much weaker and I found first hand that master switches are not well maintained, but I will attempt to bring this back around to the intent of my original post...
Not trying to reinvent anything. This will most likely remain a philosophical discussion for me as Z-12 is already quite robust as compared to the certified planes I fly in that E-bus devices will still be available on battery + internal battery backups, etc.
I have found very little information specific to protecting for master contactor failure.
Because it's so rare . . . and, with the carefully
contrived architecture and preventative maintenance,
it's failure does not represent a hazard to comfortable
termination of flight.
So is the philosophy for Z-12 that it is not worth worrying about since E-bus will still operate?
The whole airplane will probably operate. Z-12 is simply
an illustration of how the secondary, engine driven alternator
was incorporated into TC aircraft. It was simply added to
the distribution system as a second source with the ability
to support plenty of electro-whizzies on the panel.
I can accept this, I just am confused when I see Z-13/8 that connects the alternator on the battery side. Can anyone explain the reason for the difference?
Sure. Z13/8 is a three layer electrical system.
(1) Battery only. E-bus powered appliances, no contactor loads
Endurance implications: "Plan C" loads tailored to
known battery capacity such that battery-only endurance
goals are met.
(2) Battery + 8. E-bus powered appliances, contactor load
optional depending on "Plan B" loads. Loads tailored
to hold battery in reserve for descent and approach
to landing. Electrical endurance essentially unlimited.
Descent and approach to landing loads can depend on
known battery capacity to supplement the 8A engine
driven power source.
(3) Battery + Main Alternator. Normal "Plan A" ops. No
limits on electrical loads.
The three-layer system is practical only on OBAM aircraft
. . . the 337 or STC to convert a TC aircraft would be
prohibitive and would not materially reduce risk.
Bob . . .
| - The Matronics AeroElectric-List Email Forum - | | Use the List Feature Navigator to browse the many List utilities available such as the Email Subscriptions page, Archive Search & Download, 7-Day Browse, Chat, FAQ, Photoshare, and much more:
http://www.matronics.com/Navigator?AeroElectric-List |
|
|
|
Back to top |
|
 |
nuckolls.bob(at)aeroelect Guest
|
Posted: Sat Apr 21, 2018 9:14 am Post subject: Z-12 contactor failure |
|
|
Quote: |
This makes perfect sense to me. Now look at Z-12 - the primary and backup alternators are both connected the same way - to the main bus. If you turn off the master both alternators are isolated from the battery. This means battery only operation unless the alternators remain stable without battery. Why do it this way? The only difference I see is the backup alternator is the larger 20A vs 8A.
To ask another way. Why not connect the larger 20A backup alternator in the same way as Z-13/8 ( with relay and switch )? Is this not advisable due to the higher current being switched or some other reason? |
The e-bus was conceived one evening about 1988 in
conversation with a LongEz builder in California.
This fellow did a lot of long distance travel over
mountains. I don't recall if his airplane had a
starter . . . don't think it did because I do
recall that he was fitted with a pretty light
battery in the nose.
The design goal being pondered was how to create
a battery-only endurance greater than his fuel
endurance . . . which was rather long.
At that time, his electrical endurance loads were
as I recall, about 3 amps. A battery contactor draws
about 0.8A after warm up . . . enough snort to run
a couple of useful electro-whizzies yet this energy
was tossed off as heat. His SD-8 would support normal
flight loads including contactor.
[img]cid:.0[/img]
His endurance loads must have been a bit less than
3A because I recall we decided that a new 18a.h.
battery would carry his anticipated loads for 6
hours, hence his 4-hour design goal would be
satisfied to 75% of new capacity whereupon
the battery gets replaced.
So the e-bus was conceived as a method for setting
up a fixed, predictable battery-only endurance load
with a simple re-positioning of two switches.
Lots of Ez aircraft had only SD8 alternators on
the drive pad, no other alternator and no starter.
The B&C line of light weight starters and alternators
encouraged the Ez crowd on to the next evolutionary
step.
Added weight on the extreme rear of the a/c drove
a need for ballast in the nose . . . ballast
that was best achieved with a larger battery as
opposed to bags of lead shot! The 24 a.h. battery
was the next step up.
The SD-8 could be left in place on the drive pad for a
weight penalty of about 4 pounds. Hence, Z13/8 germinated
from the evolving goals of Long-Ez owners in the 1990
time frame.
At one time, I did have a Z13/20 architecture which
was discussed here on List and I think a few installations
were made. I was never happy with it as it offered
no particular advantages over Z12 and was un=necessarily
complex. There was no pressing need to eliminate contactor
loads on the much larger S/B alternator so it was
removed from the 'Connection after a few years.
Bob . . .
| - The Matronics AeroElectric-List Email Forum - | | Use the List Feature Navigator to browse the many List utilities available such as the Email Subscriptions page, Archive Search & Download, 7-Day Browse, Chat, FAQ, Photoshare, and much more:
http://www.matronics.com/Navigator?AeroElectric-List |
|
Description: |
|
Filesize: |
235.4 KB |
Viewed: |
21336 Time(s) |
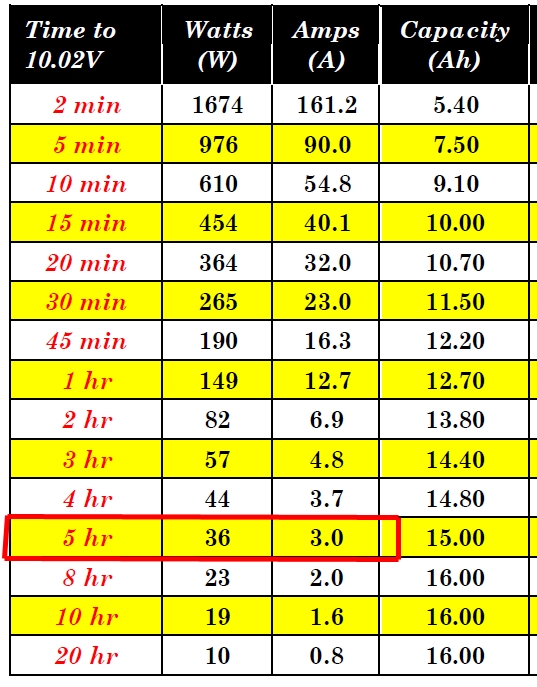
|
|
|
Back to top |
|
 |
nuckolls.bob(at)aeroelect Guest
|
Posted: Sat Apr 21, 2018 9:24 am Post subject: Z-12 contactor failure |
|
|
Quote: | His endurance loads must have been a bit less than
3A because I recall we decided that a new 18a.h.
battery would carry his anticipated loads for 6
hours, hence his 4-hour design goal would be
satisfied to 75% of new capacity whereupon
the battery gets replaced. |
Hmmmm . . . my recollection of details may be
a bit fuzzy after 30 years, 4 hours is 66%
of new . . . anyhow, this illustrates the
thought processes for design decisions.
Bob . . .
| - The Matronics AeroElectric-List Email Forum - | | Use the List Feature Navigator to browse the many List utilities available such as the Email Subscriptions page, Archive Search & Download, 7-Day Browse, Chat, FAQ, Photoshare, and much more:
http://www.matronics.com/Navigator?AeroElectric-List |
|
|
|
Back to top |
|
 |
nuckolls.bob(at)aeroelect Guest
|
Posted: Mon Apr 23, 2018 8:03 am Post subject: Z-12 contactor failure |
|
|
Bob:
Yup There are all sorts of 'possible' possibilities, all without proof, but it DOES WORK!
Many of our aircraft are 40+ years old. The original lubricants in the switches have long disappeared.
They are NOT sealed switches.
What has worked for many years are now failing. Just look Brandon's post.
And, when it comes to the Stall Warning micro switch - Replacement with NEW is $1200+ used, about $600 to $700.
All this can be prevented with a can of WD-40!
WD40 can be useful in the maintenance of electro-whizzies
with moving parts . . . and indeed, it was not originally
designed to be a lubricant so much as a (W)ater (D)isplacer
and cleaner. As a side benefit, it does have some degree of
lubricity . . . as do many substances . . . but its service
life as a lubricant is far outpaced by other products designed
for lubrication.
https://goo.gl/sbPhXj
WD40 was major maintenance feature for the MQM107 target
we used to build at Beech.
https://goo.gl/otFkbp
The engine was a very short service life device with
minimal moving parts and INTENDED to become totally
immersed in seawater during an offshore recovery.
The first refurbishment move for the aircraft was to remove
the engine and submerge it in a barrel of WD40. When the
aircraft was ready to receive the engine, they hauled it out
with compressed air and bolted it back on the airframe[/b].
Not needed on sealed DPST Toggle Switches. AND they are NOT 40+ years old.
Obviously, a truly sealed switch cannot benefit from
spray on remedies . . .
[/b]I can't see how applying a lubricant like WD40 can be advantageous to the contacts on the switch...surely there will be burning volatiles or lube which would affect the service or life of the part? On the moving parts yes but I don't know of a way to differentiate with a spray can.
WD40 is often applied to moving part for
the purpose of loosening corrosion and flushing
out small particulates while displacing any
moisture present. The combustible VOLATILES are
just that . . .they quickly dissipate after carrying
WD40 'magic juice' to the intended surfaces.
[/b]If the Master Switch failed why reinvent the wheel?
Since this was a certified plane you are forced to work with the design of the time.
What I have found is 99.982% of certified plane owners and A&P's, NEVER address the Master Switch during Annual.
It should be addressed every Annual and it is very easy to do:
1 - Spray the heck out of it with Contact Cleaner.
2 - Cycle the switch a couple of dozen times.
3 - Spray it with WD-40.
My first job at Cessna extended over 5 years
in the technical publications department where,
among other things, I wrote repair and preventative
maintenance narratives in Cessna's service manuals.
[img]cid:.0[/img]
The policy of the company was to 'replace on condition'
meaning that devices like relays and toggle switches
were considered and sometimes tested to see that
they met service life design goals. If a such a device
were to mis-behave, it was time to replace it. Hence
no maintenance or refurbishment methods were offered
or required.
[/b]Side Note: This also goes for the micro-switch in the Stall Warning System.
The basic switch used on the legacy stall warning
sensor was a Honeywell BZ series commercial off
the shelf device with very low operating force
(measured in grams). Of course, as a component
in a PMA/TSO product, the owner operator was prohibited
from replacing said switch for $20 (and I wasn't
allowed to write a procedure for it either).
These are not sealed switches and they're mounted
in one of the more hostile environments on the airplane.
Depending on the mis-behavior mode, an application
of WD40 may well free up things and restore normal
operation . . . but a switch that was not working
normally was probably pretty long in the tooth. Depending
on criticality of the device, it may well be better
to replace as opposed to refurbish the individual
switch.
[/b]On Experimental Aircraft you have a HUGE ADVANTAGE...
Use a Heavy Duty Master Switch and a Separate Heavy Duty Alternator Switch.
I use DPST switches and tie BOTH sides together. This DOUBLES the physical as well as the electrical rating of the switch.
Paralleling contacts only doubles the CARRY
rating of a switch . . . it does not double
opening or closing ratings.
[/b]Want to go extra fancy? Look for switches that are Sliver Plated.
Silver plating or solid silver contacts are
rare and intended for specific applications . . .
which generally do not include switching
DC power. Cadmium Silver contacts are used in
the more robust designs favored by mil-spec
designs . . . but I suspect the Carling style
products used on hundreds of thousands of TC
aircraft are not so 'fancy' . . . yet demonstrably
adequate to task.
[/b]You can also use switches that have a built in Dust/Moisture shield. OR... Install the dust/Moisture shield over the Toggle Lever.
Side Note: On certified planes with the standard split Master/Alt Switch, there are four (4) failure points:
1 - The Physical snap action of the switch.
2 - The Electrical contacts of the switch.
3 - Fast-On tabs on the back of the switch.
4 - The Physical MOUNTING of the switch. There is a snap in bezel that holds the switch into the panel.
This bezel fails as the ears either break off or loose their spring action.
Then the switch vibrates forward and shorts out to the aluminum panel.
The cure is to use two (2) sheet metal round head screws on either side to hold the bezel in place.
If the switch vibrates out it will short out and take your Master/Alt switch and Starter Relay out of the circuit.
If you are airborne - You loose even the ability to go to Battery Back-up.
Or do an in-flight re-start.
Scary!
Can you cite any service difficulty report
that describes such a failure of the mounting?
These switches are used by hundreds of thousands
for about 50 years. I find it curious that
anyone would find them (1) lacking in design
to intended task and/or (2) figuring significantly
on the list of probable failure that creates
a hazard to flight.
[/b]I know it is not a likely case, but I have experienced a contactor failure on a production plane in flight. It ended up that the root cause was a defective master switch - but the result was the same. Because there was no endurance bus alternate feed, it was a full electrical shutdown, in IMC no less!
Then it wasn't a contactor failure but a switch failure.
How did it manifest in flight? i.e. how did you become
aware of the failure? Did things simply go black?
[/b]I would like to know if there is a practical way to protect for contactor failure ( other than battery only operation ) with the Z-12 design. It would be nice to have a second path to the battery from aux alternator to ensure stable power if the master does fail.
You can move the aux alternator wiring to the
hot side of the battery contactor . . . it's
just that simple.
[/b]The appeal to me of having an aux alternator is to be able to continue flight on one alternator. This is only possible if either a battery connection is maintained always or it is a guarantee the alternator will provide stable power without a battery connection.
Batteryless operation is likely but cannot
be guaranteed without testing on your airplane
with your constellation of hardware. As I've mentioned,
there are Beechcraft piston aircraft wherein battery-off
operation is described and permitted as a matter of
design and verification by flight testing. It's covered
in the POH.
For this forum cannot make configuration/operation
recommendations without conducting similar investigations
as to meeting design goals
[/b]The Z-13/8 uses a relay with the SD-8 alternator to connect directly to battery. Is this design practical or even advisable with the SD-20 alternator? With Z-13/8 the aux alternator will provide power to battery bus and E-BUS if contactor fails.
Exactly. If you wish, you can certainly wire the SD20
in a manner suggested by Z13/8. There are no 'rules'
that would prohibit you from doing so.
When I took Z13/20 off the table about 10 years ago,
it was because it added a degree of complexity
over Z12 that did not materially reduce risk.
In fight contactor failure is exceedingly rare.
Smoke in the cockpit probably has a higher degree
of probability . . . in which instance you may
wish to shot the whole system down anyhow.
Any of you who have attended my weekend seminars
may remember this slide:
[/b][img]cid:.0[/img][/b]
The last 200-300 hours of my flying days were
carried out with these three items in my flight
bag. Since I flew nothing but rentals, I had little
insight as to the history of electrical/electronics
systems. I was prepared to continue flight to intended
destination with the master switch OFF.
Indeed, the performance of these $100 hand-held
gps receivers so exceeded the panel mounted stuff
that those last hundreds of hours were flown with
DUAL gps receivers 'mounted' to the glare-shield
and windshield with little blobs of windshield
sealant. Never touched a VOR receiver or even
the panel mounted GPS receivers again.
As I describe in Chapter 17 of the 'Connection,
system reliability has far more to do with pilot
skills and careful crafting of a Plan-B than it
does on any selection of system hardware. The
carefully crafted architecture and pilot's personal
bag of tricks strives for failure tolerance . . . not
failure proofing. The later cannot be achieved.
Bob . . .
| - The Matronics AeroElectric-List Email Forum - | | Use the List Feature Navigator to browse the many List utilities available such as the Email Subscriptions page, Archive Search & Download, 7-Day Browse, Chat, FAQ, Photoshare, and much more:
http://www.matronics.com/Navigator?AeroElectric-List |
|
Description: |
|
Filesize: |
79.03 KB |
Viewed: |
21310 Time(s) |
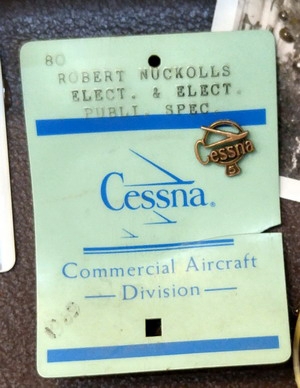
|
|
|
Back to top |
|
 |
BARRY CHECK 6
Joined: 15 Mar 2011 Posts: 738
|
Posted: Mon Apr 23, 2018 6:14 pm Post subject: Z-12 contactor failure |
|
|
Bob:
You are going off on tangents - - -
On Mon, Apr 23, 2018 at 12:02 PM, Robert L. Nuckolls, III <
nuckolls.bob(at)aeroelectric.com> wrote:
[quote] Bob:
Yup There are all sorts of 'possible' possibilities, all without proof,
but it DOES WORK!
Many of our aircraft are 40+ years old. The original lubricants in the
switches have long disappeared.
They are NOT sealed switches.
What has worked for many years are now failing. Just look Brandon's post
| - The Matronics AeroElectric-List Email Forum - | | Use the List Feature Navigator to browse the many List utilities available such as the Email Subscriptions page, Archive Search & Download, 7-Day Browse, Chat, FAQ, Photoshare, and much more:
http://www.matronics.com/Navigator?AeroElectric-List |
|
|
|
Back to top |
|
 |
bob.verwey(at)gmail.com Guest
|
Posted: Mon Apr 23, 2018 9:06 pm Post subject: Z-12 contactor failure |
|
|
Gee Wizz Barry,
Many have taken on Bob N, and many have failed....
In all the 15 + years I have been a member of this forum, the thing that has impressed me most is the decorum of the participants....just sayin!
Best...Bob Verwey
082 331 2727
[img]https://docs.google.com/uc?export=download&id=0B5d7rgAInTuTUUZsUjY4QmJsdVU&revid=0B5d7rgAInTuTdDJDaXRFZVh3b3lMa3FWL0s3MFdzc01YRlNvPQ[/img]
On 24 April 2018 at 04:12, FLYaDIVE <flyadive(at)gmail.com (flyadive(at)gmail.com)> wrote:
Quote: | Bob:
You are going off on tangents - - -
On Mon, Apr 23, 2018 at 12:02 PM, Robert L. Nuckolls, III <nuckolls.bob(at)aeroelectric.com (nuckolls.bob(at)aeroelectric.com)> wrote:
Quote: | Bob:
Yup There are all sorts of 'possible' possibilities, all without proof, but it DOES WORK!
Many of our aircraft are 40+ years old. The original lubricants in the switches have long disappeared.
They are NOT sealed switches.
What has worked for many years are now failing. Just look Brandon's post.
And, when it comes to the Stall Warning micro switch - Replacement with NEW is $1200+ used, about $600 to $700.
All this can be prevented with a can of WD-40!
WD40 can be useful in the maintenance of electro-whizzies
with moving parts . . . and indeed, it was not originally
designed to be a lubricant so much as a (W)ater (D)isplacer
and cleaner. As a side benefit, it does have some degree of
lubricity . . . as do many substances . . . but its service
life as a lubricant is far outpaced by other products designed
for lubrication.
| Barry - Nobody said it was being used as a lubricant, only you. It will work as a lubrcant to the contact areas of plastic switches and even the metal pivot points. How long will it last? I don't know... As I said in my post; A&P seldom address switches and many of these switches are 40 + years old. So, anything that one can do to extend their life or rejuvenate them is a good thing. Back to the WD... It is being used
as a WD and as a CLEANER!
Oh wait... Can it be used as a cleaner???
DEFINITELY YES!
Do you have proof that it can't be?
Quote: | https://goo.gl/sbPhXj
WD40 was major maintenance feature for the MQM107 target
we used to build at Beech.
| Barry - So!!! Who cares!
Quote: |
https://goo.gl/otFkbp
The engine was a very short service life device with
minimal moving parts and INTENDED to become totally
immersed in seawater during an offshore recovery.
| Barry - Want more info on this subject? I did salvage and artifact recovery way-way back in the 70's and 80's .
Who cares!
Quote: |
The first refurbishment move for the aircraft was to remove
the engine and submerge it in a barrel of WD40. When the
aircraft was ready to receive the engine, they hauled it out
with compressed air and bolted it back on the airframe.
Not needed on sealed DPST Toggle Switches. AND they are NOT 40+ years old.
Obviously, a truly sealed switch cannot benefit from
spray on remedies . . .
| Barry - That's why I said you CYCLE the Switches a couple dozen times.
Why are you going off on so many tangents?
Quote: |
I can't see how applying a lubricant like WD40 can be advantageous to the contacts on the switch...surely there will be burning volatiles or lube which would affect the service or life of the part? On the moving parts yes but I don't know of a way to differentiate with a spray can.
WD40 is often applied to moving part for
the purpose of loosening corrosion and flushing
out small particulates while displacing any
moisture present. The combustible VOLATILES are
just that . . .they quickly dissipate after carrying
WD40 'magic juice' to the intended surfaces.
| Barry - You advertise yourself as an engineer.
If so, why are you so closed minded to other possibilities?
There are curtain things in physics that cannot be changed, but how a product can be used and to Great Advantages is sure out there.
Quote: |
If the Master Switch failed why reinvent the wheel?
Since this was a certified plane you are forced to work with the design of the time.
What I have found is 99.982% of certified plane owners and A&P's, NEVER address the Master Switch during Annual.
It should be addressed every Annual and it is very easy to do:
1 - Spray the heck out of it with Contact Cleaner.
2 - Cycle the switch a couple of dozen times.
3 - Spray it with WD-40.
My first job at Cessna extended over 5 years
in the technical publications department where,
among other things, I wrote repair and preventative
maintenance narratives in Cessna's service manuals.
| Barry - So what? Anybody can sit down behind a desk and write a manual.
I have for a few dozen Environmental Test procedures. ANYTHING can be written.
Ask the A&P and IA that is TRY to follow
what some paper-pusher wrote IF it is possible.
Ask the plane owner who has to pay the bill why a simple thing like the Cessna Seat Rail Tracks has to be replace and WHY it is so expensive! Or how to replace the Flap Motor on a Cessna.
Quote: |
[img]cid:.0[/img]
The policy of the company was to 'replace on condition'
meaning that devices like relays and toggle switches
were considered and sometimes tested to see that
they met service life design goals. If a such a device
were to mis-behave, it was time to replace it. Hence
no maintenance or refurbishment methods were offered
or required.
Side Note: This also goes for the micro-switch in the Stall Warning System.
The basic switch used on the legacy stall warning
sensor was a Honeywell BZ series commercial off
the shelf device with very low operating force
(measured in grams). Of course, as a component
in a PMA/TSO product, the owner operator was prohibited
from replacing said switch for $20 (and I wasn't
allowed to write a procedure for it either).
These are not sealed switches and they're mounted
in one of the more hostile environments on the airplane.
Depending on the mis-behavior mode, an application
of WD40 may well free up things and restore normal
operation . . . but a switch that was not working
normally was probably pretty long in the tooth. Depending
on criticality of the device, it may well be better
to replace as opposed to refurbish the individual
switch.
On Experimental Aircraft you have a HUGE ADVANTAGE...
Use a Heavy Duty Master Switch and a Separate Heavy Duty Alternator Switch.
I use DPST switches and tie BOTH sides together. This DOUBLES the physical as well as the electrical rating of the switch.
Paralleling contacts only doubles the CARRY
rating of a switch . . . it does not double
opening or closing ratings.
Want to go extra fancy? Look for switches that are Sliver Plated.
Silver plating or solid silver contacts are
rare and intended for specific applications . . .
which generally do not include switching
DC power. Cadmium Silver contacts are used in
the more robust designs favored by mil-spec
designs . . . but I suspect the Carling style
products used on hundreds of thousands of TC
aircraft are not so 'fancy' . . . yet demonstrably
adequate to task.
|
Barry - YES - They Are! But, as the fellow whom had the failure was talking and as I was saying:
These switches have NOT been addressed during Annuals over MANY - MANY YEARS!
The Experimental Owner has Great Advantages over the Certified Owner by making small changes that GREATLY extend the life and as you are so vigorous to report on 'Reduction of Failure Points'. So, why shouldn't they look for the better switch.
Silver Plated or CadSilver?
GAUD! Which way did you part the gnat's hairs on that one?
Walking into a electronics store, the Simple question: Do you have any Silver Plated Contact Switch? Will result in the SAME results! When I order Manure I don't care if it is horse or cow. Either one will work!
Quote: |
You can also use switches that have a built in Dust/Moisture shield. OR... Install the dust/Moisture shield over the Toggle Lever.
Side Note: On certified planes with the standard split Master/Alt Switch, there are four (4) failure points:
1 - The Physical snap action of the switch.
2 - The Electrical contacts of the switch.
3 - Fast-On tabs on the back of the switch.
4 - The Physical MOUNTING of the switch. There is a snap in bezel that holds the switch into the panel.
This bezel fails as the ears either break off or loose their spring action.
Then the switch vibrates forward and shorts out to the aluminum panel.
The cure is to use two (2) sheet metal round head screws on either side to hold the bezel in place.
If the switch vibrates out it will short out and take your Master/Alt switch and Starter Relay out of the circuit.
If you are airborne - You loose even the ability to go to Battery Back-up.
Or do an in-flight re-start.
Scary!
Can you cite any service difficulty report
that describes such a failure of the mounting?
| Barry - You must LOVE AD's!
I found the problem twice. I fixed the problem twice.
YES! The switches have lasted for many years. Does that mean they cannot fail? And, as I said: It was not the switch. It was the mounting bezel.
Just because a FAA 8070-1 report not exist AND I do not know if one does or does not exist, does not mean the problem does not exist.
Just look at the design of the retaining bezel and even you should be able to see there is a potential failure point.
ESPECIALLY! When the switch is removed in tracking down a wiring issue.
There are more things in Heaven and Earth Horatio than even Bob has knowledge on.
Barry
Quote: | These switches are used by hundreds of thousands
for about 50 years. I find it curious that
anyone would find them (1) lacking in design
to intended task and/or (2) figuring significantly
on the list of probable failure that creates
a hazard to flight.
|
|
| - The Matronics AeroElectric-List Email Forum - | | Use the List Feature Navigator to browse the many List utilities available such as the Email Subscriptions page, Archive Search & Download, 7-Day Browse, Chat, FAQ, Photoshare, and much more:
http://www.matronics.com/Navigator?AeroElectric-List |
|
Description: |
|
Filesize: |
79.03 KB |
Viewed: |
21300 Time(s) |
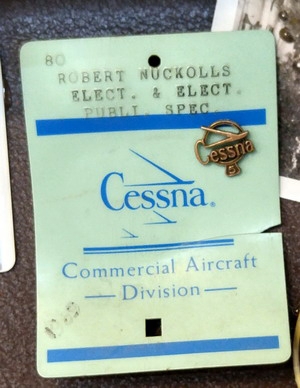
|
|
|
Back to top |
|
 |
skywagon
Joined: 11 Feb 2006 Posts: 184
|
Posted: Tue Apr 24, 2018 8:20 am Post subject: Z-12 contactor failure |
|
|
. . . . Not wanting to venture into the dark side of some of these "conversations", I just want to relay what I have personally viewed on this subject of old switches and WD40.....
Some legacy Cessna switches were simple pull-push, like a Master. I have repaired 2 of them. If one is (very) careful bending the retaining tabs the switch can be worked apart and resealed. What I found in both was severely hardened original lubricate. Hardened to the point that if a piece gets into the contacts, it can cause a faults.
Cleaning with the usual sprays and re-lubing with modern electrical grease has fixed both and they are still working today.... but, it was the old lube that caused random failure. These were master switches.
About WD40, . . .I have used it on a lot to things, but this comment is about use on guns. I have pulled rifles from several years of storage and not been able to operate the bolt action. The one flaw I see with WD40 is that once the lighter carry fluids evaporate, it leaves a strong, thick film that can almost seize close fitting parts. Other than that issue, it does great duty as a penetrate and shield from water and rust. . . .
Virus-free. www.avast.com [url=#DAB4FAD8-2DD7-40BB-A1B8-4E2AA1F9FDF2] [/url]
| - The Matronics AeroElectric-List Email Forum - | | Use the List Feature Navigator to browse the many List utilities available such as the Email Subscriptions page, Archive Search & Download, 7-Day Browse, Chat, FAQ, Photoshare, and much more:
http://www.matronics.com/Navigator?AeroElectric-List |
|
|
|
Back to top |
|
 |
nuckolls.bob(at)aeroelect Guest
|
Posted: Tue Apr 24, 2018 9:04 am Post subject: Z-12 contactor failure |
|
|
At 09:12 PM 4/23/2018, you wrote:
Quote: | Bob:
You are going off on tangents |
I would like to think that I'm reviewing background
that supports ideas and design goals for reducing
risk. Airplanes are exceedingly unforgiving things . . .
but they are well understood. We can climb into these
machines and launch into hazardous environs with
confidence when we (1) don't routinely push the
'boundaries of the envelope'. (2) build and operate
with a degree of understanding that promotes
failure tolerance. (3) pay attention to the failings
that produce the vast majority of unhappy days in
the cockpit . . . most off-airport arrivals with
the earth have root cause in ignorance of or
inattention to important things.
There are no procedures in the legacy annual inspections
for switches, relays, contactors, light bulbs, etc.
Because these things DO cease to function with regularity
that has nothing to do with the calendar. If things
didn't break, FBOs would be out of business.
"Replace on condition" is the mantra of those who
endeavor to become licensed aviation mechanics
and technicians. Certification follows education
delivered hopefully by competent teachers. If
you've read any of my works on the website or
in the 'Connection, you will see that I try
to lay foundation for both the physics and the
philosophies I am reviewing.
The materials and practices we've grown up with
in TC aviation are a good place to start as
we strive for 'self certification' . . . indeed,
few folks bucking rivets on or stringing wires in an
RV are 'qualified' to work for an FBO. Hence, the
mission for the AeroElectric-List is to bring
the best-we've-learned-how-to-do in 100 years of
TC aviation into to the world of OBAM aviation.
And then, because we are not burdened with
the albatross of prolific regulation and bureaucracy,
ADVANCE the art in careful, considered steps that
do not increase risk.
This thread was about contactor failures. Yes,
they've been known to crap out. Cessna Service-Parts
sells a boat load of new ones every year. Yet
how many unhappy days in the cockpit are attributed
to contactor failures . . . or switches, relays, etc?
This suggest that they are a low risk failure in
TC aircraft . . . and with careful analysis of
failure modes, OBAM aviation is free to reduce those
risks still further.
The narrative of WD40 WAS anecdotal but I hope
useful. The flags that arose in my thinking were
about the notions you were citing about the lack
of refurbishment and/or regular inspection intervals.
Most devices give us advance clues as to their
distress before they fail outright. I suggest that
the FIRST time a switch, relay or contactor demonstrates
an electrical infirmity, it is time to replace it.
Some mechanical infirmities may benefit from
a lubrication/cleaning operation . . . but hopefully,
the decision is made from a position of informed
competence.
Bailing wire and pliers served my grandpa well . . .
indeed, proper dress for my friends out here
in the hinterlands includes a leather holster for
a robust pair of pliers. My son gave me a Leatherman for
Father's Day about 5 years ago . . . it too has become part
of my 'uniform'. My friends also carry cans of WD40
on their trucks. They may be running re-grooved tires
on their swathers. Some have no doubt dropped little
doses of 'magic elixir' into the filler caps on a
faltering battery.
My point is that any refurbishment activity on a
component of our airplanes is worthy of evaluation
for return on investment, assessment of risk and,
as we've learned in a century of TC aviation, REPLACE
ON CONDITION is never a bad idea.
Bob . . .
| - The Matronics AeroElectric-List Email Forum - | | Use the List Feature Navigator to browse the many List utilities available such as the Email Subscriptions page, Archive Search & Download, 7-Day Browse, Chat, FAQ, Photoshare, and much more:
http://www.matronics.com/Navigator?AeroElectric-List |
|
|
|
Back to top |
|
 |
|
|
You cannot post new topics in this forum You cannot reply to topics in this forum You cannot edit your posts in this forum You cannot delete your posts in this forum You cannot vote in polls in this forum You cannot attach files in this forum You can download files in this forum
|
Powered by phpBB © 2001, 2005 phpBB Group
|