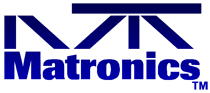 |
Matronics Email Lists Web Forum Interface to the Matronics Email Lists
|
View previous topic :: View next topic |
Author |
Message |
nuckolls.bob(at)aeroelect Guest
|
Posted: Fri Jan 25, 2019 10:04 am Post subject: When / where to use dielectric grease? |
|
|
At 05:26 AM 1/24/2019, you wrote:
Quote: | --> AeroElectric-List message posted by: "sha664817" <sha664817(at)gmail.com>
There's a lot of chatter about the use of dielectric grease. Permeate suggests that Dielectric Tune-Up Grease is a good barrier to oxidation at plugs, connectors and terminals. There are some online comments at forums that say not to place dielectric grease on connector pins.
I've gone to the Permeate site, and the information is vague:
"Protects electrical connections and wiring from salt, dirt and corrosion. Extends the life of bulb sockets. Prevents voltage leakage around any electrical connection. Also prevents spark plugs from fusing to boots. Required for modern high energy ignition systems."
Directions for Connectors: 1. Make sure ignition system is off. 2. Clean surface with Permeate Contact Cleaner. 3. Coat both parts of terminal contact with Dielectric Grease. 4. Reassemble, maintaining metal-to-metal contact.
In the PDF, Permatex cites uses for the Permatex Dielectric Tune-Up Grease:
TYPICAL APPLICATIONS
• Spark plug boots
• Distributor cap nipples
• Battery terminals
• Ignition coil connectors
• Headlamp connectors
• Trailer electrical connectors |
Dielectric greases and coatings are proven prophylactics
that ward off the effects of adverse environments for
which the potential 'victim' is ill-equipped to
manage on its own.
Borrowing from the assertions of another competent
observer of really big numbers, let us consider what
must be 'billions and billions' of mated conductors
in connectors that have performed over the LIFETIMES
of the target technology with no 'extra' protection
squeezed out of a tube or brushed on from a bottle.
Does this mean that such products have no useful
place? Not at all. My FIRST experience with dielectric
grease moisture protection was 175' up on
a tower where the boss told me that filling the
mated coax connectors with DC4 before assembly
had a demonstrated value for shielding connectors
exposed to Kansas climate way up in the air.
Over the years, I have had occasion to open factory
assembled connectors that were obviously offered
the benefits of protection above and beyond those
offered by the enclosure. This includes lamp sockets
on tail and back-up lights, marker lights and
yes, trailer connectors.
These instances were most common on fixtures
especially exposed to splash or run-down. When
refurbishing equipment that succumbed to
contamination induced corrosion, the
'rule of thumb' called for protecting
the replacement hardware with a good
dielectric grease. But it was also a good
idea to see if some gasket had failed
allowing ingress of moisture.
[img]cid:.0[/img]
In years since, designers for electrical
connectors improved designs to improve
performance in harsh environments.
The moisture seal bellows on this
connector is one example.
[img]cid:.1[/img]
It's been a long time since I've opened
a connector that contained any previously
applied protection against moisture.
It stands to reason that suppliers of
such products want to sell as much as
the market will purchase. The marketing
problem is that it's seldom necessary/beneficial.
The only time I've used the stuff is
to provide an extra layer of protection
for components that replaced victims
of moisture damage . . . or selected
instances of extra-ordinary risk . . .
like difficult-to-access 175' up on a tower.
The short story is that these products
are best applied during replacement
of parts that have succumbed to moisture
effects. But when such damage is
discovered, be sure to evaluate
the circumstances of the failure.
Was the connector a poor choice to
begin with? Was it subjected to
environmental stresses outside original
design goals? Does a sealing feature of
the enclosure need refurbishment?
I have a 4oz tube of DC4 that is probably
40 years old and barely shows signs of having
been squeezed. Dielectric grease is
a band-aid on a marginal design.
Bob . . .
| - The Matronics AeroElectric-List Email Forum - | | Use the List Feature Navigator to browse the many List utilities available such as the Email Subscriptions page, Archive Search & Download, 7-Day Browse, Chat, FAQ, Photoshare, and much more:
http://www.matronics.com/Navigator?AeroElectric-List |
|
Description: |
|
Filesize: |
116.19 KB |
Viewed: |
1646 Time(s) |
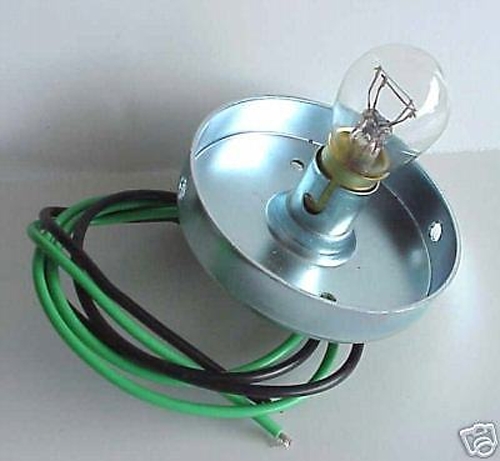
|
Description: |
|
Filesize: |
133.2 KB |
Viewed: |
1646 Time(s) |
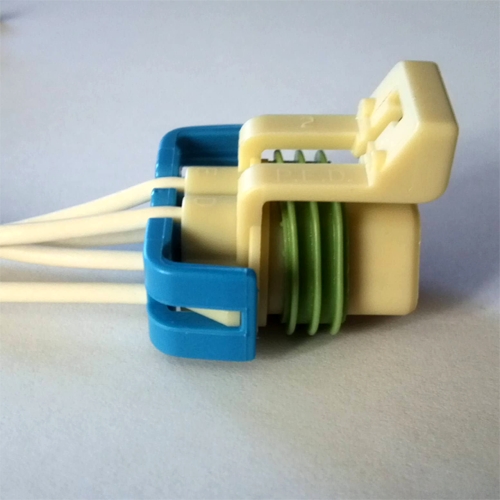
|
|
|
Back to top |
|
 |
nuckolls.bob(at)aeroelect Guest
|
Posted: Sat Jan 26, 2019 10:35 am Post subject: When / where to use dielectric grease? |
|
|
At 12:45 AM 1/26/2019, you wrote:
Quote: | --> AeroElectric-List message posted by: rayj <raymondj(at)frontiernet.net>
I can only comment from my experience on boats and docks. I have seen less corrosion problems on connections treated with dielectric grease. The difference can be seen in a matter of a couple of seasons, especially on ones that are removed and replaced frequently, such as removable anchor lights and cigar lighter type connectors. Admitted these are not high buck sealed connections designed for the harsh maritime environment, but using grease changes them from problematic designs to being reliable connectors. |
. . . which re-enforces my point . . .
Dielectric greases are invaluable in cases
of environmental extremes. Salt air
would certainly be considered an extreme.
My first observations of how bad it
can be was on a trip to South Padre with
my young family about 50 years ago.
Got to know some commercial fisher
persons and spent some time on the
docks and boats . . .
There is a tank on the beach of
Culebra Island, PR that has been sitting
there since WWII. Dug around through
the interior a few years back.
[img]cid:.0[/img]
The salt water has literally dissolved
major cross sections of steel. On the
other hand, one could have stored this
machine next to a tenant of the Davis
Monthan 'bone yard' . .
[img]cid:.1[/img]
. . . and the machine might well be
operational with nothing more than some
fuel and a grease job.
A 4oz tube of DC4 has lasted me for
decades in KS . . . but in St. Pete
Beach? Maybe not so much.
Bob . . .
| - The Matronics AeroElectric-List Email Forum - | | Use the List Feature Navigator to browse the many List utilities available such as the Email Subscriptions page, Archive Search & Download, 7-Day Browse, Chat, FAQ, Photoshare, and much more:
http://www.matronics.com/Navigator?AeroElectric-List |
|
Description: |
|
Filesize: |
119.97 KB |
Viewed: |
1640 Time(s) |
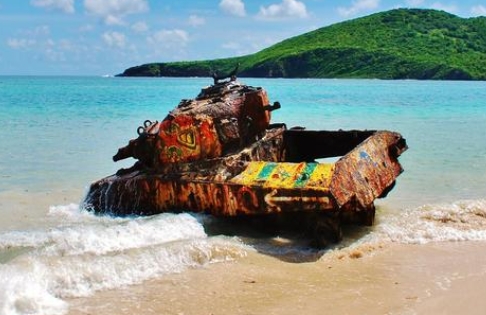
|
Description: |
|
Filesize: |
218.47 KB |
Viewed: |
1640 Time(s) |
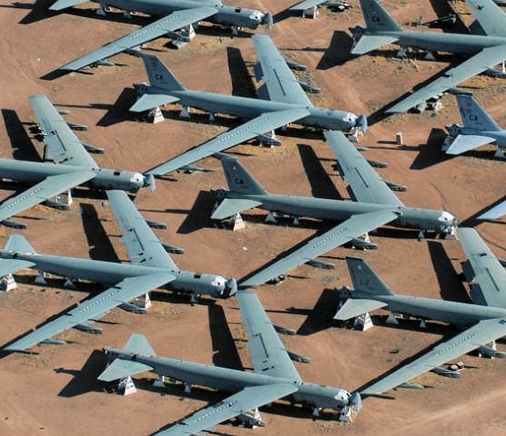
|
|
|
Back to top |
|
 |
|
|
You cannot post new topics in this forum You cannot reply to topics in this forum You cannot edit your posts in this forum You cannot delete your posts in this forum You cannot vote in polls in this forum You cannot attach files in this forum You can download files in this forum
|
Powered by phpBB © 2001, 2005 phpBB Group
|