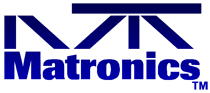 |
Matronics Email Lists Web Forum Interface to the Matronics Email Lists
|
View previous topic :: View next topic |
Author |
Message |
markfw
Joined: 28 Feb 2019 Posts: 27 Location: Seattle, WA
|
Posted: Fri Dec 13, 2019 2:19 pm Post subject: Questions as I Design My Circuit Diagram |
|
|
I am building an LSA Carbon Cub which will be electrically dependent. since I will be flying only day VFR, I have followed Bob's advice and I am following the KISS principle and wiring the plane like a C150 using the Z11 schematic as a starting point.
The only things I know about electrical systems is what I have learned reading Bob's book, so I am a total novice at this. As I design my own schematic I realize that I have questions that I cannot answer. They may be dumb, and if so I apologize.
1. I have read that all circuits should have overload protection to protect the wire. When I look at Z11 there doesn't appear to be a fuse or CB on the wire from the Battery Contactor to the Main Bus, nor on the wire from the Main Bus to the Endurance Bus. What is the convention in use here?
2. I have read that alternators only deliver 80% of their rated power, so I am missing 8 amps of power from my 40 amp rated Hartzell X-Drive. My 7 feet of 8AWG wire back to the battery accounts for less than 1 amp of the loss. Where does it go? Is this 80% number really true?
3. I am going to start with a single (big) EarthX battery in my plane. However the battery compartment under the pilot's seat is easily accessible (the seat tilts forward) and another EarthX would fit in nicely. I might want to add another battery at some point in the future when I fly over water or mountains here in the Northwest.
Bob has published elegant solutions to the 2 battery configuration, and I know that he has forgotten more than I will ever know about aircraft electrics. However I am wondering if there are reasons why I couldn't keep it simple and just wire up a 200 amp Marine battery switch as a simple A/B flip flop to a second battery? There probably are.
Thanks.
Mark
| - The Matronics AeroElectric-List Email Forum - | | Use the List Feature Navigator to browse the many List utilities available such as the Email Subscriptions page, Archive Search & Download, 7-Day Browse, Chat, FAQ, Photoshare, and much more:
http://www.matronics.com/Navigator?AeroElectric-List |
|
|
|
Back to top |
|
 |
nuckolls.bob(at)aeroelect Guest
|
Posted: Fri Dec 13, 2019 4:08 pm Post subject: Questions as I Design My Circuit Diagram |
|
|
At 04:19 PM 12/13/2019, you wrote:
Quote: | --> AeroElectric-List message posted by: "markfw" <markwheelermd(at)icloud.com>
I am building an LSA Carbon Cub which will be electrically dependent. since I will be flying only day VFR, I have followed Bob's advice and I am following the KISS principle and wiring the plane like a C150 using the Z11 schematic as a starting point. |
What have you changed and why?
Quote: | The only things I know about electrical systems is what I have learned reading Bob's book, so I am a total novice at this. As I design my own schematic I realize that I have questions that I cannot answer. They may be dumb, and if so I apologize.
1. I have read that all circuits should have overload protection to protect the wire. When I look at Z11 there doesn't appear to be a fuse or CB on the wire from the Battery Contactor to the Main Bus, nor on the wire from the Main Bus to the Endurance Bus. What is the convention in use here? |
The only wires needing protection are those
that feed some accessory from a source capable
of burning the wire.
Bus feeders (referred to here on the list as
'fat wires" are generally not at risk for
burning . . . there are no probable faults
'hard' enough to put those wires at risk
with one exception: Rolling your airplane up
in a ball on the rocks . . . which is why
the wire-burning source (battery) is expected
to be off line (battery master off) before
you hit the rocks.
Z11 is correct and complete as published.
Quote: | 2. I have read that alternators only deliver 80% of their rated power, so I am missing 8 amps of power from my 40 amp rated Hartzell X-Drive. My 7 feet of 8AWG wire back to the battery accounts for less than 1 amp of the loss. Where does it go? Is this 80% number really true? |
No. The general rule is that maximum
anticipated running loads for your airplane
should not be greater than 80% of the
alternator's ratings. This leaves 20% for
battery replenishment after takeoff.
Modern, light weight alternators generally
have much more snort than required by our
airplanes. Have you done a load analysis for
your project? In TC aircraft designs, this
is one of the FIRST studies started and
then maintained through certification. It's
a critical part of the certification process.
Quote: | 3. I am going to start with a single (big) EarthX battery in my plane. However the battery compartment under the pilot's seat is easily accessible (the seat tilts forward) and another EarthX would fit in nicely. I might want to add another battery at some point in the future when I fly over water or mountains here in the Northwest. |
What engine is in your airplane?
Quote: |
Bob has published elegant solutions to the 2 battery configuration, and I know that he has forgotten more than I will ever know about aircraft electrics. However I am wondering if there are reasons why I couldn't keep it simple and just wire up a 200 amp Marine battery switch as a simple A/B flip flop to a second battery? There probably are. |
This has been suggested many times here
on the List over the years. Given the
proximity of your battery to the cabin,
a manual switch is a perfectly acceptable
substituted for a master contactor. I took
dual instruction in a Piper TriPacer that
had manual switches for both the battery
master and the starter.
Bob . . .
| - The Matronics AeroElectric-List Email Forum - | | Use the List Feature Navigator to browse the many List utilities available such as the Email Subscriptions page, Archive Search & Download, 7-Day Browse, Chat, FAQ, Photoshare, and much more:
http://www.matronics.com/Navigator?AeroElectric-List |
|
|
|
Back to top |
|
 |
user9253
Joined: 28 Mar 2008 Posts: 1925 Location: Riley TWP Michigan
|
Posted: Fri Dec 13, 2019 7:48 pm Post subject: Re: Questions as I Design My Circuit Diagram |
|
|
2. An alternator will deliver 100 percent of its rated power if the load
demands it. However, the alternator could overheat if fully loaded unless it is
adequately cooled. Amperage is not lost over a length of wire, voltage is
lost. Where does it go? Lost energy is turned into heat that warms the wire.
8 AWG wire should carry 40 amps with minimal voltage loss. Loading an
alternator to 80 percent of its capacity is a rule of thumb to ensure that it
does not overheat. Modern avionics in a VFR Carbon Cub are unlikely to
draw more 10 amps.
-
3. After engine start, the aircraft electrical system gets its power from the
alternator, not the battery. The battery serves as a backup in case the
alternator fails. Usually a backup to a backup is not necessary in a VFR aircraft.
| - The Matronics AeroElectric-List Email Forum - | | Use the List Feature Navigator to browse the many List utilities available such as the Email Subscriptions page, Archive Search & Download, 7-Day Browse, Chat, FAQ, Photoshare, and much more:
http://www.matronics.com/Navigator?AeroElectric-List |
|
_________________ Joe Gores |
|
Back to top |
|
 |
markfw
Joined: 28 Feb 2019 Posts: 27 Location: Seattle, WA
|
Posted: Sat Dec 14, 2019 11:04 am Post subject: Re: Questions as I Design My Circuit Diagram |
|
|
Bob,
Thank you for your reply.
I changed Z11 in four ways:
1. I am using an EFI system so I enlarged the Endurance Bus to incorporate all of the EFI component circuits;
2. I added a Lighting Bus with C/B's just to make wiring the panel easier and because I was out of fuse positions on my Port side fuse block;
3. I did not incorporate the E-Bus alternate feed;
4. I used SSR relays rather than contactors.
I assumed that Z11 was correct. I was only asking about the reasoning about when to use fuses for my own education.
Does 8AWG wire qualify as "fat" in this context of circuit protection?
I will have an O-340 from LyCon as my engine.
My load analysis is attached to this e-mail.
Joe, I was not asking about a second battery to backup my primary battery. I was asking about it as a way to extend my flight time in the Alternator Out situation. With my EFI my ALT OUT cruise power consumption is 20A so a 7 pound ETX1200 battery would give me approximately an hour of flight time, which should work for most of my needs. I was just exploring what it would take to add in a second battery for certain higher risk trips over water or mountains so I would not have to carry that extra weight all of the time.
Mark
P.S. Is there any way to respond to replies to an original post individually rather than as a group?
| - The Matronics AeroElectric-List Email Forum - | | Use the List Feature Navigator to browse the many List utilities available such as the Email Subscriptions page, Archive Search & Download, 7-Day Browse, Chat, FAQ, Photoshare, and much more:
http://www.matronics.com/Navigator?AeroElectric-List |
|
Description: |
|
 Download |
Filename: |
Current Electric Loads - V5.xlsx |
Filesize: |
21.6 KB |
Downloaded: |
346 Time(s) |
|
|
Back to top |
|
 |
ceengland7(at)gmail.com Guest
|
Posted: Sun Dec 15, 2019 1:44 pm Post subject: Questions as I Design My Circuit Diagram |
|
|
On Sun, Dec 15, 2019 at 3:18 PM Robert L. Nuckolls, III <nuckolls.bob(at)aeroelectric.com (nuckolls.bob(at)aeroelectric.com)> wrote:
Quote: | At 01:04 PM 12/14/2019, you wrote:
Quote: | --> AeroElectric-List message posted by: "markfw" <markwheelermd(at)icloud.com (markwheelermd(at)icloud.com)>
Bob,
Thank you for your reply.
I changed Z11 in four ways:
1. I am using an EFI system so I enlarged the Endurance Bus to incorporate all of the EFI component circuits |
Okay, in the 'endurance mode' what are your
design goals for battery only operations? The
E-bus plus Battery bus loads generally define
alternator-out loads. Not real clear from
the load analysis narrative.
Quote: | 2. I added a Lighting Bus with C/B's just to make wiring the panel easier and because I was out of fuse positions on my Port side fuse block; |
added cbs? Why not another small fuse
block?
Quote: | 3. I did not incorporate the E-Bus alternate feed; |
then you don't have an e-bus . . . it's just
an extension of the main bus.
Quote: | 4. I used SSR relays rather than contactors. |
Z-11 doesn't care what kind of contactor.
The Z drawings are about architecture and
failure mode effects mitigation.
Quote: | I assumed that Z11 was correct. I was only asking about the reasoning about when to use fuses for my own education. |
Very good.
Quote: | Does 8AWG wire qualify as "fat" in this context of circuit protection? |
yes
Quote: | I will have an O-340 from LyCon as my engine. |
Do you have an otherwise unused vacuum pump
pad? Why not a second alternator?
Quote: | My load analysis is attached to this e-mail. |
Do your injectors really draw 1.5A average or
6A for the suite of injectors?
Quote: | Joe, I was not asking about a second battery to backup my primary battery. I was asking about it as a way to extend my flight time in the Alternator Out situation. With my EFI my ALT OUT cruise power consumption is 20A so a 7 pound ETX1200 battery would give me approximately an hour of flight time, which should work for most of my needs. I was just exploring what it would take to add in a second battery for certain higher risk trips over water or mountains so I would not have to carry that extra weight all of the time. |
An pad-driven alternator would easily carry
your anticipated system loads, have a lower
cost of ownership than a second battery. The
'e bus' goes away. Would recommend a battery
bus that would support all vital engine functions
so that the panel could be made 'max dark' without
killing the engine.
We would sure like to see a schematic
of this system. Schematics are the fundamental
language for FFA (Function and Failure Analysis).
It appears that you have a 50A b-lead breaker
on the panel? That hasn't been done on most TC
aircraft in decades . . . it's not illustrated
on any z-figure.
You speak to an 'essential bus' but with
no narrative or schematic as to how this
bus gets isolated for energy management
in an alternator-out condition?
Bob . . .
|
Bob,
I can't directly address your Q about individual injector current draw. They tend to 'peak' at each trigger, but duty cycle varies wildly, and how they're operated varies wildly among control techniques (true timed injection which is rare in a/c vs 'batch fire' vs 'semi-sequential' vs ??). But the alt engine guys have been flying auto-style electronic engine control for a lot longer than the Lyc guys, and common numbers by numerous guys flying this type of *system* for a high pressure fuel pump, injectors, igniters, and computer would be 12-15 amps; likely leaning toward the high side of that spread. I have a friend who's a retired P-W engineer who tested his system in flight for battery-only operation. With a healthy PC680, IIRC he flew for ~40 minutes before seeing voltage drop to near 'discharge state' before bringing the alternator back on line. I don't recall what power setting he was using for the test. Obviously, operating at higher power levels requires more energy for the various electronic bits.
Charlie
| - The Matronics AeroElectric-List Email Forum - | | Use the List Feature Navigator to browse the many List utilities available such as the Email Subscriptions page, Archive Search & Download, 7-Day Browse, Chat, FAQ, Photoshare, and much more:
http://www.matronics.com/Navigator?AeroElectric-List |
|
|
|
Back to top |
|
 |
markfw
Joined: 28 Feb 2019 Posts: 27 Location: Seattle, WA
|
Posted: Sun Dec 15, 2019 3:23 pm Post subject: Re: Questions as I Design My Circuit Diagram |
|
|
Bob,
My design goals for Alt Out operations are approximately 1 hour of flight time to get on the ground while continuing use of my EFI, EFIS, EIS 1 radio and the transponder.
As an overarching design constraint, I am LSA so I am weight sensitive in all of my decisions.
I am using surface mounted fuse blocks on the cockpit quarter panels where I can see if there has been a blown fuse because an LED lights up. No I don't intend to change them in flight, but I want to know. I have a space constraint for mounting another fuse block, so I decided to use C/B's. However, I will say that I went back and forth on this and this morning I actually moved them onto the existing fuse block rather than keeping some spare circuits. Weight is about a wash either way.
It's clear that I don't understand the difference between an E-Bus and an Endurance Bus. What I am calling an E-Bus is a bus fed by the battery that can power my essential electrical needs (approximately 20 amps) for an hour. My main Bus is on a switch so I can dump all of my non-essential loads easily. The Alt Field is on a separate switch, so I would also turn that off.
I have attached my current schematic which is A WORK IN PROGRESS (wire gauges are wrong, no grounds, no sheet for the EFI itself, etc). I do plan to submit it here when I am happy with it. However it certainly is tough for you to give me advice without any idea at all about what I am up to.
Since I am very weight conscious I decided early on that I would use the light weight ECI accessory pad which does not provide a vacuum or prop governor. This saves 1.5 pounds. The B&C SD-20 spine driven alternator is 5.75 pounds, plus creates space issues for me under the cowl. I thought that I would rather spend that 7.25 pounds on a spare battery if my mission needed it.
The injectors draw 1.5 - 2.0 amps each depending on load. The vendor recommends 5 amp fuses.
The 50 amp b-lead breaker is simply copied from what Cubcrafters does on their certified Carbon Cubs. What is the right answer? An ANL fuse somewhere?
Mark
| - The Matronics AeroElectric-List Email Forum - | | Use the List Feature Navigator to browse the many List utilities available such as the Email Subscriptions page, Archive Search & Download, 7-Day Browse, Chat, FAQ, Photoshare, and much more:
http://www.matronics.com/Navigator?AeroElectric-List |
|
Description: |
|
 Download |
Filename: |
N36CX EDraw Circuit Diagram - V1.pdf |
Filesize: |
926.17 KB |
Downloaded: |
343 Time(s) |
|
|
Back to top |
|
 |
markfw
Joined: 28 Feb 2019 Posts: 27 Location: Seattle, WA
|
Posted: Sun Dec 15, 2019 7:35 pm Post subject: Re: Questions as I Design My Circuit Diagram |
|
|
Bob,
You were right. My spreadsheet numbers (and my memory of the correct numbers) were wrong.
The range of energy consumption per injection according to their vendor is .5 - 1.5 amps depending on load.
My load (5 gph) is at the bottom of his range.
It doesn’t change my design, but I have to eat humble pie.
Mark
| - The Matronics AeroElectric-List Email Forum - | | Use the List Feature Navigator to browse the many List utilities available such as the Email Subscriptions page, Archive Search & Download, 7-Day Browse, Chat, FAQ, Photoshare, and much more:
http://www.matronics.com/Navigator?AeroElectric-List |
|
|
|
Back to top |
|
 |
|
|
You cannot post new topics in this forum You cannot reply to topics in this forum You cannot edit your posts in this forum You cannot delete your posts in this forum You cannot vote in polls in this forum You cannot attach files in this forum You can download files in this forum
|
Powered by phpBB © 2001, 2005 phpBB Group
|