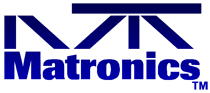 |
Matronics Email Lists Web Forum Interface to the Matronics Email Lists
|
View previous topic :: View next topic |
Author |
Message |
nuckolls.bob(at)aeroelect Guest
|
Posted: Wed May 27, 2020 11:24 am Post subject: DAS system |
|
|
Quote: | Bob and Eric, thanks for pointing out a much more elegant solution than a shunt farm!
Bob, I re-read the section of Chapter 7 on Hall effect sensors. I'm sure I read it around 30 years ago, but I had forgotten. |
They've become a LOT better and cheaper
since!
Quote: | One way this is more elegant is that it can be inserted into the ground path without disrupting the ground, which makes the physical wiring safer. (The shunt and fuse block in my van's wiring closet are a bit vulnerable right now.) |
You still have to break into the ground
path which involves terminations/splices
of some sort.
Quote: | The microcontrollers I'm planning to use have lots of A/D pins, so that's not a problem. They're Arduino compatible, but at 3.3V, so I wonder whether the LTS 6-NP must have a 5V supply voltage? If so, that'll factor in to the multiplier produced by the parallel wires, to make full scale no more than 3.3V. |
Which boards are you planning? I've got
an UNO DAS shield that was crafted to
mate with an Arduino R3. It's got one
dedicated LTS6NP sensor. The LTS6 has
three internal passes through the core
brought out on six pins. I've arranged
to exploit those internal passes with
terminals that place 1, 2 or all 3 in
series for 6, 3, and 2 amps full scale.
Of course, the drilled aperture is available
for customized passes on the monitored
conductor.
Quote: | I skimmed the data sheet on the LTS 6-NP. I'll have to read it more closely before I'll be able to put it to use! I believe I understand how the six primary leads are configured to the application, but not so much passing a conductor (or turns!) through the aperture. |
The device has
Quote: | Other than your clever 10X scaling, how does one choose between a conductor through the aperture vs. the primary leads?
And I'll want to understand more about the physical considerations: Does this device require some minimum clearance from other wiring/components? |
No
Quote: | I assume you specify a 1 foot length for each of the parallel 22AWG and 10AWG wires because 10AWG has a cross section about 9X 22AWG? Why 1 foot? What about just a shorter length of each, from one side of the sensor to the other? (I'm picturing a printed circuit board with the 22 AWG soldered near Fast-Ons or threaded studs to attach the 10AWG and the wires to ground and load/battery. Or, heck, just a bolt through to the chassis, like the ground block.) |
Nothing magical about the 1 foot length.
The goal is to take 10% of total current through
the aperture while taking 90% around the aperture.
10AWG is 1 mohm/ft; 20AWG is 10 mohm/ft. What we're
looking for is a total paralleled resistance
of 1 mohm (10% of the 20AWG thru conductor).
If you want to parallel 10 mohm with something to
give you 1/10 the total you'll need about 1.1 mohms.
This would work out to about 13.2 inches of 10AWG.
My DAS systems just record raw, uncompensated
data. So 1 foot of 10AWG paralleled with 1 foot
of 20AWG gives me a total of 0.0091 ohms or
about 10% low for being a calibrated shunt.
You CAN calibrate the shunt-wires but it takes
careful cutting, splicing and verification.
My data analysis software allows me to apply
offset and scale factors to raw data to derive
calibrated data. Hence, my shunt wires need only
be in the ball park.
Quote: | I wonder whether one could achieve the same multiplier (and current capacity) using a shorter wire through the aperture together with a generous area of printed circuit foil to carry the other 90% of the current? (I've never learned anything about the current capacity of printed circuit foil or how to predict its resistance.) Could that assembly be calibrated somehow? Would it be stable?
|
You need to strive for KNOWN, stable resistances . . .
unless you're using temperature stable resistance
materials, you'll want to use similar materials
for the two 'shunts'. Copper has a significant
positive temperature coefficient of resistance
and would normally make a 'rough' shunt. In
this instance, I don't care about the absolute
resistance, only the RATIO of the two resistances.
Being of similar material, the division ratio
is relatively independent of ambient
temp and temperature rise due to current
flow.
You haven't shared how many apples are already
in your 'cart' . . . don't what to toss off
too much effort but be aware of availability
of the DAS shield illustrated. The assembled
Arduino boards includes an SD memory card
socket. The software allows user selected
sample rates and writes data to comma delimited
ASCII files. If you'd like to explore this
hardware in more detail, I'll get you the
schematics. AEC-Lister Paul Fisher has put
considerable effort into the supporting
software. I'm pretty sure he'd be interested
in spooling this project up again.
Bob . . .
| - The Matronics AeroElectric-List Email Forum - | | Use the List Feature Navigator to browse the many List utilities available such as the Email Subscriptions page, Archive Search & Download, 7-Day Browse, Chat, FAQ, Photoshare, and much more:
http://www.matronics.com/Navigator?AeroElectric-List |
|
Description: |
|
Filesize: |
126.57 KB |
Viewed: |
4173 Time(s) |
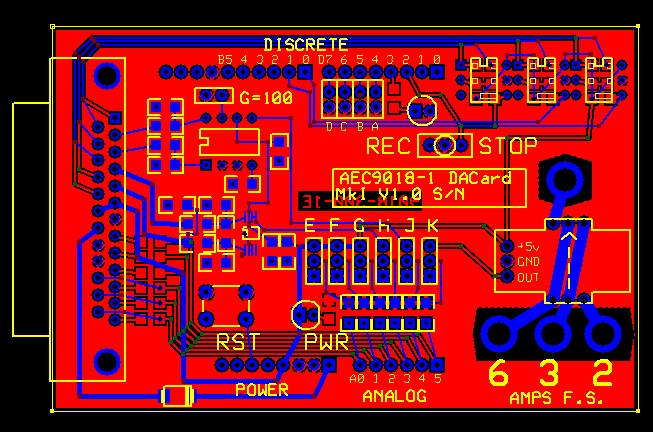
|
Description: |
|
Filesize: |
82.5 KB |
Viewed: |
4173 Time(s) |
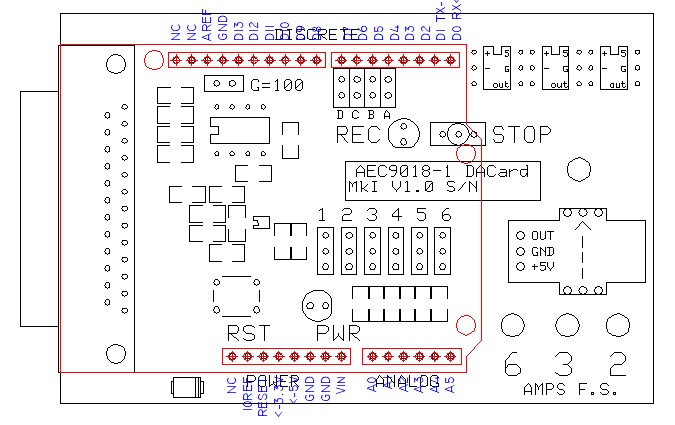
|
|
|
Back to top |
|
 |
sbw(at)sbw.org Guest
|
Posted: Fri May 29, 2020 1:14 pm Post subject: DAS system |
|
|
On 5/27/2020 12:21 PM, Robert L. Nuckolls, III wrote:
Quote: | > Bob and Eric, thanks for pointing out a much more elegant solution
> than a shunt farm!
>
> Bob, I re-read the section of Chapter 7 on Hall effect sensors. I'm
> sure I read it around 30 years ago, but I had forgotten.
They've become a LOT better and cheaper
since!
|
I can see that!
Quote: | > One way this is more elegant is that it can be inserted into the
> ground path without disrupting the ground, which makes the physical
> wiring safer. (The shunt and fuse block in my van's wiring closet are
> a bit vulnerable right now.)
You still have to break into the ground
path which involves terminations/splices
of some sort.
|
Yes, but no injection losses. A shunt on the low side would make the
ground float around, which is never good.
Quote: | > The microcontrollers I'm planning to use have lots of A/D pins, so
> that's not a problem. They're Arduino compatible, but at 3.3V, so I
> wonder whether the LTS 6-NP must have a 5V supply voltage? If so,
> that'll factor in to the multiplier produced by the parallel wires, to
> make full scale no more than 3.3V.
Which boards are you planning?
|
I have one of each of these coming from Adafruit next week for
experimentation:
Feather M0 Express: https://urlzr.mp/dqb (adafruit.com)
Feather nRF52840 Express: https://urlzr.mp/eqb (adafruit.com)
Each has six ADC pins, which should be plenty. The ADCs can measure
0-3.6mV.
The nRF52840 is faster than the M0, has a lot more flash and RAM for
firmware, and Bluetooth low energy, in case I want to use a smartphone
app to display the data.
There are lots of other Feathers with various capabilities:
https://learn.adafruit.com/adafruit-feather
I'll also need this "Featherwing" (like a shield) to carry the SD card
and provide an accurate realtime clock:
Adalogger FeatherWing: https://urlzr.mp/fqb (adafruit.com)
Quote: | I've got
an UNO DAS shield that was crafted to
mate with an Arduino R3. It's got one
dedicated LTS6NP sensor. The LTS6 has
three internal passes through the core
brought out on six pins. I've arranged
to exploit those internal passes with
terminals that place 1, 2 or all 3 in
series for 6, 3, and 2 amps full scale.
Of course, the drilled aperture is available
for customized passes on the monitored
conductor.
|
And thanks for sending the schematics separately. I reviewed the
schematics closely, and I have some questions I may send you.
But I understand the LTS6NP better after reading the data sheet more
closely. I can use your parallel-wires method to scale to more than 6A.
Quote: | > I assume you specify a 1 foot length for each of the parallel 22AWG
> and 10AWG wires because 10AWG has a cross section about 9X 22AWG? Why
> 1 foot? What about just a shorter length of each, from one side of
> the sensor to the other? (I'm picturing a printed circuit board with
> the 22 AWG soldered near Fast-Ons or threaded studs to attach the
> 10AWG and the wires to ground and load/battery. Or, heck, just a bolt
> through to the chassis, like the ground block.)
Nothing magical about the 1 foot length.
The goal is to take 10% of total current through
the aperture while taking 90% around the aperture.
10AWG is 1 mohm/ft; 20AWG is 10 mohm/ft. What we're
looking for is a total paralleled resistance
of 1 mohm (10% of the 20AWG thru conductor).
If you want to parallel 10 mohm with something to
give you 1/10 the total you'll need about 1.1 mohms.
This would work out to about 13.2 inches of 10AWG.
|
The LTS6NP requires 5V and outputs 0-5V, whereas the Feathers can
measure only 0-3.6V. The LTS 6-NP outputs 3.6V at 2.64A. So I would
adjust the parallel wires to carry only about 2.5A through the aperture,
if that makes sense.
But here's the next gotcha: I want to measure separate currents FROM the
charging sources and FROM the battery, so I don't need any of the
negative current range of the LTS devices, which output 2.5V at 0A.
That wastes most the resolution! The Feathers use 12-bit ADCs.
Measuring only over 2.5-3.6V leaves only about 1,250 bits of resolution.
At 60A (from the alternator) that's about 50mA per bit. Is that
enough resolution?
Ideas for using more of the range?
Quote: | My DAS systems just record raw, uncompensated
data. So 1 foot of 10AWG paralleled with 1 foot
of 20AWG gives me a total of 0.0091 ohms or
about 10% low for being a calibrated shunt.
You CAN calibrate the shunt-wires but it takes
careful cutting, splicing and verification.
|
Yes. It'll be interesting to see how repeatable the assembly can be.
Quote: | My data analysis software allows me to apply
offset and scale factors to raw data to derive
calibrated data. Hence, my shunt wires need only
be in the ball park.
|
Yes, there's no reason not to just measure each assembly on the bench
and put the empirical numbers into firmware.
In fact, since each of my desired measurements have different expected
ranges, I might use different lengths of wires for each, or even just
use the internal passes for lower currents.
Heck, I might go up to the LTS 15-NP for some of the lower current
sources (like my 8A marine charger), and just use the internal passes
for simplicity.
Quote: | You haven't shared how many apples are already
in your 'cart' . . . don't what to toss off
too much effort but be aware of availability
of the DAS shield illustrated. The assembled
Arduino boards includes an SD memory card
socket. The software allows user selected
sample rates and writes data to comma delimited
ASCII files. If you'd like to explore this
hardware in more detail, I'll get you the
schematics. AEC-Lister Paul Fisher has put
considerable effort into the supporting
software. I'm pretty sure he'd be interested
in spooling this project up again.
|
Thanks! I really want to explore the smaller Feather devices, but your
DAS shield is an excellent starting point, and much of Paul's software
may be usable since the Feathers support the Arduino IDE. (They also
have "Circuit Python," but I don't yet know the differences.)
| - The Matronics AeroElectric-List Email Forum - | | Use the List Feature Navigator to browse the many List utilities available such as the Email Subscriptions page, Archive Search & Download, 7-Day Browse, Chat, FAQ, Photoshare, and much more:
http://www.matronics.com/Navigator?AeroElectric-List |
|
|
|
Back to top |
|
 |
sbw(at)sbw.org Guest
|
Posted: Sat May 30, 2020 12:46 pm Post subject: DAS system |
|
|
Yesterday, discussing my project to create a data logger to measure
charge and discharge paths in my VW camper, I wrote that I'm planning to
use one of Adafruit's Feather microntrollers. Bob suggested the LTS
series hall effect current sensors. I wrote:
Quote: | (The Feathers have) six ADC pins, which should be plenty. The ADCs can measure > 0-3.6mV.> > ...> > The LTS6NP requires 5V and outputs 0-5V, whereas
the Feathers can > measure only 0-3.6V. The LTS 6-NP outputs 3.6V at
|
2.64A. So I would > adjust the parallel wires to carry only about 2.5A
through the aperture, > if that makes sense.> > But here's the next
gotcha: I want to measure separate currents FROM the > charging sources
and FROM the battery, so I don't need any of the > negative current
range of the LTS devices, which output 2.5V at 0A. That > wastes most
the resolution! The Feathers use 12-bit ADCs. Measuring > only over
2.5-3.6V leaves only about 1,250 bits of resolution. At 60A > (from the
alternator) that's about 50mA per bit. Is that enough > resolution?> >
Ideas for using more of the range?
Of course, I already know the answer: Use a simple op amp circuit to
shift and scale the 2.5-5V output range of the LTS to the 0-3.6V input
range of the Feather ADC.
I think I've found the resources I need to learn how to design that
circuit. More on that below.
But adding an op amp to adapt the output of the very elegant LTS series
devices makes me feel like I'm not using the ideal hall effect device.
So let me ask: Is there a device that can be applied more directly? The
ideal device would:
- Work with a supply voltage of 3.3V, like the Feathers, and output
0-3.3V. (The Feather ADCs can use the 3.3V supply voltage as the
reference or an internal 0.6V reference and 1/6 divider to measure 3.6V.)
- Or require a 5V supply voltage, but also a configurable full scale
voltage.
- And configurable to produce 0V output at 0A current.
But assuming I use the LTS series, here's what I've found so far to help
me shift and scale its output:
I re-read Wikipedia on op amps:
https://en.wikipedia.org/wiki/Operational_amplifier
Then I asked DuckDuckGo to find me an "op amp designer":
https://ddg.gg/?q=op+amp+designer
That led me to TI's Design Resources page:
https://urlzr.mp/gqb (ti.com)
I selected "Amplifier circuits":
https://urlzr.mp/hqb (ti.com)
Under "Signal Conditioning," I selected "Non-inverting op amp with
non-inverting positive reference voltage circuit" to download the PDF:
http://www.ti.com/lit/sboa263 (PDF)
That's very informative, and it has a link to another PDF, "Designing
Gain and Offset in Thirty Seconds":
http://www.ti.com/lit/pdf/sloa097 (PDF)
I haven't yet applied that, but it looks like a great resource for a
DIYer like me! I'll try to create a proposed schematic and run it by
Bob for refinement.
In particular, I note in the DAS schematic Bob sent me that his signal
conditioning op amps have capacitors in various configurations around
the inputs. The TI tool produces just a basic circuit with resistors
for the offset and scale, so I'll be curious to find out what Bob's
capacitors add to the signal conditioning, and whether my use case needs
that.
I'm tempted to adapt TI's "30 Seconds" tool to Javascript, so
experimenters can use it through a web browser!
| - The Matronics AeroElectric-List Email Forum - | | Use the List Feature Navigator to browse the many List utilities available such as the Email Subscriptions page, Archive Search & Download, 7-Day Browse, Chat, FAQ, Photoshare, and much more:
http://www.matronics.com/Navigator?AeroElectric-List |
|
|
|
Back to top |
|
 |
ceengland7(at)gmail.com Guest
|
Posted: Sat May 30, 2020 4:00 pm Post subject: DAS system |
|
|
[snipped]
Quote: | In particular, I note in the DAS schematic Bob sent me that his signal
conditioning op amps have capacitors in various configurations around
the inputs. The TI tool produces just a basic circuit with resistors
for the offset and scale, so I'll be curious to find out what Bob's
capacitors add to the signal conditioning, and whether my use case
needs that.
I'm tempted to adapt TI's "30 Seconds" tool to Javascript, so
experimenters can use it through a web browser!
I haven't dug out my old linear device books in a couple of decades, but
|
the old 'cookbooks' and application notes for opamps and similar devices
typically included a section describing 'best practices' for bypassing
values/locations. If you do a little careful reading, I'll bet it's in
there somewhere, unless the new-tech stuff includes internal filtering.
If that's the case, it should be documented, as well.
Charlie
--
This email has been checked for viruses by Avast antivirus software.
https://www.avast.com/antivirus
| - The Matronics AeroElectric-List Email Forum - | | Use the List Feature Navigator to browse the many List utilities available such as the Email Subscriptions page, Archive Search & Download, 7-Day Browse, Chat, FAQ, Photoshare, and much more:
http://www.matronics.com/Navigator?AeroElectric-List |
|
|
|
Back to top |
|
 |
Eric Page
Joined: 15 Feb 2017 Posts: 247
|
Posted: Sun May 31, 2020 8:23 am Post subject: DAS system |
|
|
Quote: | On May 31, 2020, at 03:36, Steve Williams <sbw(at)sbw.org> wrote:
So let me ask: Is there a device that can be applied more directly? The ideal device would:
- Work with a supply voltage of 3.3V, like the Feathers, and output 0-3.3V. (The Feather ADCs can use the 3.3V supply voltage as the reference or an internal 0.6V reference and 1/6 divider to measure 3.6V.)
|
Here are 17 through-hole devices similar to the ones Bob suggested, from three manufacturers, all of which will operate at 3.3V:
https://preview.tinyurl.com/y7eo66u9
Pay particular attention to the LEM parts. You can play with their reference voltage to achieve current measurements well above their banner specs, and they have a hole to allow passing a wire through their core.
There are also 3.3V versions of the Allegro parts that I suggested a few days ago:
https://preview.tinyurl.com/y8z5am4t
Quote: | - Or require a 5V supply voltage, but also a configurable full scale voltage.
|
Any of the 5V parts could be used by simply putting their output through a resistor divider that scales it to a maximum of 3.3V (i.e. 13.7k over 26.7k). You can calibrate readings in your code. No op-amps required.
Quote: | - And configurable to produce 0V output at 0A current.
|
Most (all?) of the unidirectional parts will meet this spec. The bidirectional parts have to use Vcc/2 as their zero-current point in order to measure current in both directions.
Eric
| - The Matronics AeroElectric-List Email Forum - | | Use the List Feature Navigator to browse the many List utilities available such as the Email Subscriptions page, Archive Search & Download, 7-Day Browse, Chat, FAQ, Photoshare, and much more:
http://www.matronics.com/Navigator?AeroElectric-List |
|
|
|
Back to top |
|
 |
sbw(at)sbw.org Guest
|
Posted: Sun May 31, 2020 9:40 am Post subject: DAS system |
|
|
Wow, thanks again Eric. It'll take me some time to absorb that.
Looking at your links, I learned a bit better how to use Digikey's web
site to narrow down the selection. Very helpful.
On 5/31/2020 9:19 AM, Eric Page wrote:
Quote: | > On May 31, 2020, at 03:36, Steve Williams <sbw(at)sbw.org> wrote:
> So let me ask: Is there a device that can be applied more directly?
> Â The ideal device would:
>
> - Work with a supply voltage of 3.3V, like the Feathers, and output
> 0-3.3V. Â (The Feather ADCs can use the 3.3V supply voltage as the
> reference or an internal 0.6V reference and 1/6 divider to measure 3.6V.)
Here are 17 through-hole devices similar to the ones Bob suggested, from
three manufacturers, all of which will operate at 3.3V:
https://preview.tinyurl.com/y7eo66u9
Pay particular attention to the LEM parts. Â You can play with their
reference voltage to achieve current measurements well above their
banner specs, and they have a hole to allow passing a wire through their
core.
There are also 3.3V versions of the Allegro parts that I suggested a few
days ago:
https://preview.tinyurl.com/y8z5am4t
> - Or require a 5V supply voltage, but also a configurable full scale
> voltage.
Any of the 5V parts could be used by simply putting their output through
a resistor divider that scales it to a maximum of 3.3V (i.e. 13.7k over
26.7k). Â You can calibrate readings in your code. Â No op-amps required.
> - And configurable to produce 0V output at 0A current.
Most (all?) of the unidirectional parts will meet this spec. Â The
bidirectional parts have to use Vcc/2 as their zero-current point in
order to measure current in both directions.
Eric
|
| - The Matronics AeroElectric-List Email Forum - | | Use the List Feature Navigator to browse the many List utilities available such as the Email Subscriptions page, Archive Search & Download, 7-Day Browse, Chat, FAQ, Photoshare, and much more:
http://www.matronics.com/Navigator?AeroElectric-List |
|
|
|
Back to top |
|
 |
nuckolls.bob(at)aeroelect Guest
|
Posted: Sun May 31, 2020 5:03 pm Post subject: DAS system |
|
|
At 12:37 PM 5/31/2020, you wrote:
Quote: | --> AeroElectric-List message posted by: Steve Williams <sbw(at)sbw.org>
Wow, thanks again Eric. It'll take me some time to absorb that. |
Thanks from me too . . . just what I was thinking . . .
Quote: | Looking at your links, I learned a bit better how to use Digikey's web site to narrow down the selection. Very helpful. |
Of all the supplier websites I consult,
Digikey is head and shoulders above the
rest. I think Menards, Home Depot and
Lowes are all tied for the worst!
Bob . . .
| - The Matronics AeroElectric-List Email Forum - | | Use the List Feature Navigator to browse the many List utilities available such as the Email Subscriptions page, Archive Search & Download, 7-Day Browse, Chat, FAQ, Photoshare, and much more:
http://www.matronics.com/Navigator?AeroElectric-List |
|
|
|
Back to top |
|
 |
|
|
You cannot post new topics in this forum You cannot reply to topics in this forum You cannot edit your posts in this forum You cannot delete your posts in this forum You cannot vote in polls in this forum You cannot attach files in this forum You can download files in this forum
|
Powered by phpBB © 2001, 2005 phpBB Group
|