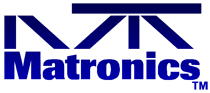 |
Matronics Email Lists Web Forum Interface to the Matronics Email Lists
|
View previous topic :: View next topic |
Author |
Message |
nuckolls.bob(at)aeroelect Guest
|
Posted: Sun Sep 20, 2020 9:52 am Post subject: who wudda thunk it? |
|
|
I'm replacing an in-dash radio in the family chariot . . .
seems the venerable ol' Kenwood CD player radio just
doesn't cut it any more. Nobody carries CDs in the
car and everyone wants to link their mobile phone
to the radio via blue tooth. Ahhh fair Kenwood, tho
has served me well . . . RIP.
The vehicle to radio adapter harness needs to
transition from Kenwood to JVC. Its a harness
I built about 6 years ago. I was surprised to
find that about some of the shrink over splices
between radio and vehicle connectors had MIGRATED to
locations that no longer cover the solder joint.
I know that the shrink had a good grip on the
irregularities of the solder joint when the harness
was built. But after years of temperature cycles
under the dash, the heat shrink kinda un-shrunk!
It became more round and released it's grip on
the joint. This allowed the tubing to vibrate
clear of the solder joint! Only a few actually
moved but all were loose and could be easily
moved.
We now know a lot more than we understand. Funky
brand of HS? Normal behavior for a polyolfin
shrink? I'm getting ready to mod the harness
with a new radio connector . . . I think I'll
use something different for joints. Perhaps
crimp-shrink butt splices, solder sleeves or
maybe double wall heat shrink with the internal
adhesive. So many choices but no doubt all
of them better than the choice I made last
time.
Just a heads-up guys.
Bob . . .
| - The Matronics AeroElectric-List Email Forum - | | Use the List Feature Navigator to browse the many List utilities available such as the Email Subscriptions page, Archive Search & Download, 7-Day Browse, Chat, FAQ, Photoshare, and much more:
http://www.matronics.com/Navigator?AeroElectric-List |
|
Description: |
|
Filesize: |
108.18 KB |
Viewed: |
2667 Time(s) |
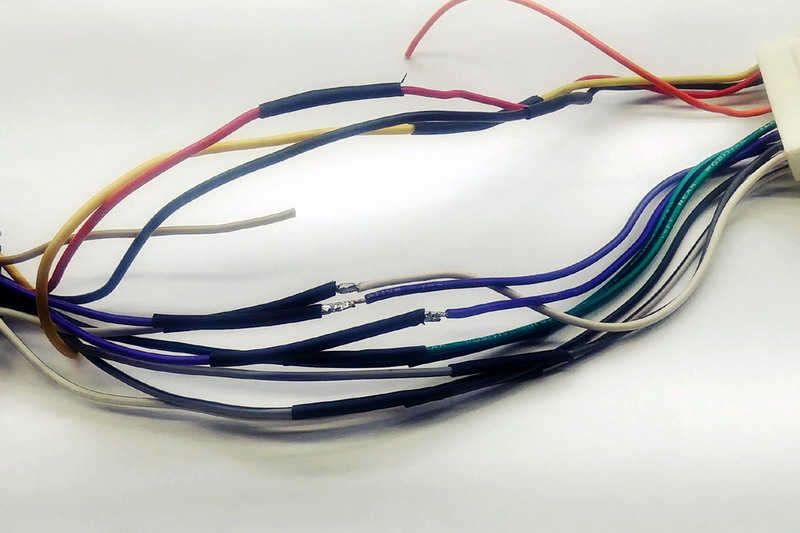
|
|
|
Back to top |
|
 |
ceengland7(at)gmail.com Guest
|
Posted: Sun Sep 20, 2020 12:25 pm Post subject: who wudda thunk it? |
|
|
On 9/20/2020 12:48 PM, Robert L. Nuckolls, III wrote:
Quote: |
I'm replacing an in-dash radio in the family chariot . . .
seems the venerable ol' Kenwood CD player radio just
doesn't cut it any more. Nobody carries CDs in the
car and everyone wants to link their mobile phone
to the radio via blue tooth. Ahhh fair Kenwood, tho
has served me well . . . RIP.
The vehicle to radio adapter harness needs to
transition from Kenwood to JVC. Its a harness
I built about 6 years ago. I was surprised to
find that about some of the shrink over splices
between radio and vehicle connectors had MIGRATED to
locations that no longer cover the solder joint.
I know that the shrink had a good grip on the
irregularities of the solder joint when the harness
was built. But after years of temperature cycles
under the dash, the heat shrink kinda un-shrunk!
It became more round and released it's grip on
the joint. This allowed the tubing to vibrate
clear of the solder joint! Only a few actually
moved but all were loose and could be easily
moved.
We now know a lot more than we understand. Funky
brand of HS? Normal behavior for a polyolfin
shrink? I'm getting ready to mod the harness
with a new radio connector . . . I think I'll
use something different for joints. Perhaps
crimp-shrink butt splices, solder sleeves or
maybe double wall heat shrink with the internal
adhesive. So many choices but no doubt all
of them better than the choice I made last
time.
Just a heads-up guys.
Bob . . .
Now that's interesting. Did the sleeves 'unshrink' to normal looking
|
original diameter, with no evidence of distortion where the solder
joints would have been?
If you re-apply heat, do they re-shrink?
Calling up memories of tricks I'm capable of....Any chance they were
never shrunk? Perhaps that task was delegated to an assistant?
Charlie
--
This email has been checked for viruses by Avast antivirus software.
https://www.avast.com/antivirus
| - The Matronics AeroElectric-List Email Forum - | | Use the List Feature Navigator to browse the many List utilities available such as the Email Subscriptions page, Archive Search & Download, 7-Day Browse, Chat, FAQ, Photoshare, and much more:
http://www.matronics.com/Navigator?AeroElectric-List |
|
|
|
Back to top |
|
 |
art(at)zemon.name Guest
|
Posted: Sun Sep 20, 2020 2:10 pm Post subject: who wudda thunk it? |
|
|
That's wild, Bob. So many non-obvious things to consider when selecting stuff that looks mundane. I have never done any testing on what happens to already-shrunk HS tubing when you heat it back up to 120 to 150 degrees. It makes me wonder what would happen to the wiring harness in my airplane if I parked it outdoors in the summer more often.
  -- Art Z.
On Sun, Sep 20, 2020 at 1:12 PM Robert L. Nuckolls, III <nuckolls.bob(at)aeroelectric.com (nuckolls.bob(at)aeroelectric.com)> wrote:
Quote: |
I'm replacing an in-dash radio in the family chariot . . .
seems the venerable ol' Kenwood CD player radio just
doesn't cut it any more. Nobody carries CDs in the
car and everyone wants to link their mobile phone
to the radio via blue tooth. Ahhh fair Kenwood, tho
has served me well . . . RIP.
The vehicle to radio adapter harness needs to
transition from Kenwood to JVC. Its a harness
I built about 6 years ago. I was surprised to
find that about some of the shrink over splices
between radio and vehicle connectors had MIGRATED to
locations that no longer cover the solder joint.
I know that the shrink had a good grip on the
irregularities of the solder joint when the harness
was built. But after years of temperature cycles
under the dash, the heat shrink kinda un-shrunk!
It became more round and released it's grip on
the joint. This allowed the tubing to vibrate
clear of the solder joint! Only a few actually
moved but all were loose and could be easily
moved.
We now know a lot more than we understand. Funky
brand of HS? Normal behavior for a polyolfin
shrink? I'm getting ready to mod the harness
with a new radio connector . . . I think I'll
use something different for joints. Perhaps
crimp-shrink butt splices, solder sleeves or
maybe double wall heat shrink with the internal
adhesive. So many choices but no doubt all
of them better than the choice I made last
time.
Just a heads-up guys.
  Bob . . . |
--
https://CheerfulCurmudgeon.com/Each of us is worth only what we are willing to give away to others. -- Lynn Schusterman
| - The Matronics AeroElectric-List Email Forum - | | Use the List Feature Navigator to browse the many List utilities available such as the Email Subscriptions page, Archive Search & Download, 7-Day Browse, Chat, FAQ, Photoshare, and much more:
http://www.matronics.com/Navigator?AeroElectric-List |
|
|
|
Back to top |
|
 |
nuckolls.bob(at)aeroelect Guest
|
Posted: Sun Sep 20, 2020 2:44 pm Post subject: who wudda thunk it? |
|
|
Quote: | Now that's interesting. Did the sleeves 'unshrink' to normal looking original diameter, |
pretty much . . . the tubing was snug on the
wires before shrinking.
Quote: | with no evidence of distortion where the solder joints would have been? |
Only the slightest visible 'ripples' in the surface
that would have been over the joint.
Quote: | If you re-apply heat, do they re-shrink? |
Had to go dig it out of the trash and check. Yeah,
they would pull down tight. Took some pieces off
completely and they would shrink waaayyy down.
Quote: | Calling up memories of tricks I'm capable of....Any chance they were never
shrunk? Perhaps that task was delegated to an assistant? |
Almost wish that were true. My long held
notions of how the stuff works have been
roughed up a bit! But no, they were originally
heated.
They did not return to the as-purchased state.
The more compressed sections over the solder
joints appear to have been encouraged to
assume the larger diameters on each side
of the joint. The segments were still pretty
snug on the wires but they would slide easily
at room temp. Might have relaxed still more
at 'under the dash' temps (it does get really
toasty back there!).
But the fundamental feature of the shrink
seems to have been unaffected. It was originally
1/8" and closed to under 1/16" when
heated off the wire.
Just finished the install . . . today's harness
used double walled shrink. Don't know if I'm
going to have the car long enough to see how
the alternative material behaved. The new
bundles were string tied so even if the h.s.
relaxes, it can't slide. But I don't think
the gooey stuff inside would allow that.
Bob . . .
| - The Matronics AeroElectric-List Email Forum - | | Use the List Feature Navigator to browse the many List utilities available such as the Email Subscriptions page, Archive Search & Download, 7-Day Browse, Chat, FAQ, Photoshare, and much more:
http://www.matronics.com/Navigator?AeroElectric-List |
|
|
|
Back to top |
|
 |
nuckolls.bob(at)aeroelect Guest
|
Posted: Sun Sep 20, 2020 4:03 pm Post subject: who wudda thunk it? |
|
|
At 05:07 PM 9/20/2020, you wrote:
Quote: | That's wild, Bob. So many non-obvious things to consider when selecting stuff that looks mundane. I have never done any testing on what happens to already-shrunk HS tubing when you heat it back up to 120 to 150 degrees. It makes me wonder what would happen to the wiring harness in my airplane if I parked it outdoors in the summer more often. |
if you simply reheat, I think it would
just attempt to get tighter. The 'relaxation'
mode we've witnessed probably takes years
of temperature swings under the cowl,
behind the panel or under the dash. And
I'm thinking it didn't relax to as-new
dimensions, rather it was teased into assuming
the diameter of insulation on either side
of the solder joints thus allowing it
to slide on the wire.
Obviously, limiting your usage to
double wall, adhesive lined, 3:1
shrink ratio would preclude this
condition. But that stuff is a lot
harder to carve away if you ever
want access to the joint later.
https://tinyurl.com/y49us3jb
Further, you can see that my radio
harness was not bundled. Had I string-
tied the thing, like every good airplane
builder does, it would not have mattered
if the shrinks were loose enough to slide.
When I cut my teeth on aircraft practices
waaayyy back at Boeing in '61, we didn't
have heat shrink, just a clear plastic thin-wall
tubing called "irvolite" which I think was a
brand name. When using that material to
cover say a knife-splice, we used a string
tie right over the center of the splice.
This thread is more of an academic curiosity
than any sort of warning flag for process and
practice. But it was startling to find.
Bob . . .
| - The Matronics AeroElectric-List Email Forum - | | Use the List Feature Navigator to browse the many List utilities available such as the Email Subscriptions page, Archive Search & Download, 7-Day Browse, Chat, FAQ, Photoshare, and much more:
http://www.matronics.com/Navigator?AeroElectric-List |
|
|
|
Back to top |
|
 |
echristley(at)att.net Guest
|
Posted: Sun Sep 20, 2020 5:21 pm Post subject: who wudda thunk it? |
|
|
You seem to be saying that it is an older vehicle. Any chemical smells? Would the various and sundry hydrocarbons have enough concentration to cause the heat shrink to swell over time?
On Sunday, September 20, 2020, 8:04:43 PM EDT, Robert L. Nuckolls, III <nuckolls.bob(at)aeroelectric.com> wrote:
At 05:07 PM 9/20/2020, you wrote:
Quote: | That's wild, Bob. So many non-obvious things to consider when selecting stuff that looks mundane. I have never done any testing on what happens to already-shrunk HS tubing when you heat it back up to 120 to 150 degrees. It makes me wonder what would happen to the wiring harness in my airplane if I parked it outdoors in the summer more often. |
if you simply reheat, I think it would
just attempt to get tighter. The 'relaxation'
mode we've witnessed probably takes years
of temperature swings under the cowl,
behind the panel or under the dash. And
I'm thinking it didn't relax to as-new
dimensions, rather it was teased into assuming
the diameter of insulation on either side
of the solder joints thus allowing it
to slide on the wire.
Obviously, limiting your usage to
double wall, adhesive lined, 3:1
shrink ratio would preclude this
condition. But that stuff is a lot
harder to carve away if you ever
want access to the joint later.
https://tinyurl.com/y49us3jb
Further, you can see that my radio
harness was not bundled. Had I string-
tied the thing, like every good airplane
builder does, it would not have mattered
if the shrinks were loose enough to slide.
When I cut my teeth on aircraft practices
waaayyy back at Boeing in '61, we didn't
have heat shrink, just a clear plastic thin-wall
tubing called "irvolite" which I think was a
brand name. When using that material to
cover say a knife-splice, we used a string
tie right over the center of the splice.
This thread is more of an academic curiosity
than any sort of warning flag for process and
practice. But it was startling to find.
Bob . . .
| - The Matronics AeroElectric-List Email Forum - | | Use the List Feature Navigator to browse the many List utilities available such as the Email Subscriptions page, Archive Search & Download, 7-Day Browse, Chat, FAQ, Photoshare, and much more:
http://www.matronics.com/Navigator?AeroElectric-List |
|
|
|
Back to top |
|
 |
nuckolls.bob(at)aeroelect Guest
|
Posted: Sun Sep 20, 2020 6:17 pm Post subject: who wudda thunk it? |
|
|
At 08:18 PM 9/20/2020, you wrote:
Quote: | You seem to be saying that it is an older vehicle. Any chemical smells? Would the various and sundry hydrocarbons have enough concentration to cause the heat shrink to swell over time?
|
No. It's a 2006 and the radio was installed about 2014.
All the wiring was in the cabin.
I think the forcing function came from adjacent
ends of insulation on the spliced wires . . . not
from native tendencies to shrink . . . for
indeed, this stuff un-shrunk. When heat was applied to
carcasses removed from the harness, they shrank
tightly with expected dispatch.
Bob . . .
| - The Matronics AeroElectric-List Email Forum - | | Use the List Feature Navigator to browse the many List utilities available such as the Email Subscriptions page, Archive Search & Download, 7-Day Browse, Chat, FAQ, Photoshare, and much more:
http://www.matronics.com/Navigator?AeroElectric-List |
|
|
|
Back to top |
|
 |
rv8iator
Joined: 11 Apr 2006 Posts: 144 Location: Newberg, OR
|
Posted: Mon Sep 21, 2020 5:53 am Post subject: who wudda thunk it? |
|
|
A couple of data points... re. heat shrink tubing
I have harnesses that are 40+ years old. I built them for similar duty, auto audio systems. They served well but were removed for upgrades. IIRC they were in service for around 20 years. (yes I keep vehicles typically for 300k miles). Again IIRC the heatshrink is Raychem showing no signs of releasing or expanding.
My employer builds their own wire harness' albeit for fairly benign environs. I have observed them after 30 years in service without any loss of "shrink". They cover line voltage (120/240vac) connections. The products are UL certified so if there were failures of the heat shrink that caused a failure it would likely be reported. Again Raychem heat shrink, clear as it is a medical equipment application.
...chris
On Sun, Sep 20, 2020 at 11:01 AM Robert L. Nuckolls, III <nuckolls.bob(at)aeroelectric.com (nuckolls.bob(at)aeroelectric.com)> wrote:
Quote: |
I'm replacing an in-dash radio in the family chariot . . .
seems the venerable ol' Kenwood CD player radio just
doesn't cut it any more. Nobody carries CDs in the
car and everyone wants to link their mobile phone
to the radio via blue tooth. Ahhh fair Kenwood, tho
has served me well . . . RIP.
The vehicle to radio adapter harness needs to
transition from Kenwood to JVC. Its a harness
I built about 6 years ago. I was surprised to
find that about some of the shrink over splices
between radio and vehicle connectors had MIGRATED to
locations that no longer cover the solder joint.
I know that the shrink had a good grip on the
irregularities of the solder joint when the harness
was built. But after years of temperature cycles
under the dash, the heat shrink kinda un-shrunk!
It became more round and released it's grip on
the joint. This allowed the tubing to vibrate
clear of the solder joint! Only a few actually
moved but all were loose and could be easily
moved.
We now know a lot more than we understand. Funky
brand of HS? Normal behavior for a polyolfin
shrink? I'm getting ready to mod the harness
with a new radio connector . . . I think I'll
use something different for joints. Perhaps
crimp-shrink butt splices, solder sleeves or
maybe double wall heat shrink with the internal
adhesive. So many choices but no doubt all
of them better than the choice I made last
time.
Just a heads-up guys.
  Bob . . . |
| - The Matronics AeroElectric-List Email Forum - | | Use the List Feature Navigator to browse the many List utilities available such as the Email Subscriptions page, Archive Search & Download, 7-Day Browse, Chat, FAQ, Photoshare, and much more:
http://www.matronics.com/Navigator?AeroElectric-List |
|
_________________ C. Stone (RV8iator) |
|
Back to top |
|
 |
|
|
You cannot post new topics in this forum You cannot reply to topics in this forum You cannot edit your posts in this forum You cannot delete your posts in this forum You cannot vote in polls in this forum You cannot attach files in this forum You can download files in this forum
|
Powered by phpBB © 2001, 2005 phpBB Group
|