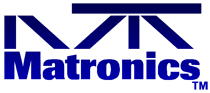 |
Matronics Email Lists Web Forum Interface to the Matronics Email Lists
|
View previous topic :: View next topic |
Author |
Message |
david(at)carter.net Guest
|
|
Back to top |
|
 |
Ceengland
Joined: 11 Oct 2020 Posts: 393 Location: MS
|
Posted: Wed Sep 22, 2021 3:57 pm Post subject: SDS CPI-2 Circuit Protection Question |
|
|
On 9/22/2021 1:10 PM, David Carter wrote:
I think that there is, for multiple reasons. 1st, the coil circuits are *really* noisy. With a common wire feeding both, the noise has a direct path into the supply for the ECU. (The 'filter' method, the battery, would be a long ways away.) 2nd, if he's using the system fuse to protect the cpu (not good practice, but many avionics makers have been known to do it), 10A won't do it. 3rd (for me, anyway), I'd fuse each coil block separately; not all coils on one fuse. All that separate fusing means a single failure can't take out something else, like the coil pack taking the ECU with it when the fuse blows. ATC/ATO fuse blocks are relatively cheap and very compact for many circuits, so it's easy to isolate each coil. If a coil goes shorted, separate fuses could at least keep one pair of cylinders firing. Might make the difference between the runway and the fence. (Failure modes effects analysis.)
One other thing that might be 'just me', but I would not put the engine circuits on the main bus, or any airframe bus. My reasoning is, training. Assuming that you have years of flying traditional a/c engines under your belt, if you ever have the very rare but heavily trained-for 'smoke in the cockpit' situation, what's the first thing you're trained do? Will you be able to override decades of trained-in muscle memory? I doubt I could, so my engine stuff is on a separate, dedicated engine bus.
FWIW,
Charlie
Virus-free. www.avast.com [url=#DAB4FAD8-2DD7-40BB-A1B8-4E2AA1F9FDF2] [/url]
| - The Matronics AeroElectric-List Email Forum - | | Use the List Feature Navigator to browse the many List utilities available such as the Email Subscriptions page, Archive Search & Download, 7-Day Browse, Chat, FAQ, Photoshare, and much more:
http://www.matronics.com/Navigator?AeroElectric-List |
|
_________________ Charlie |
|
Back to top |
|
 |
wsimpso1
Joined: 04 Nov 2018 Posts: 33 Location: Saline MI
|
Posted: Thu Sep 23, 2021 6:04 am Post subject: Re: SDS CPI-2 Circuit Protection Question |
|
|
First off, if Ross says run separate fusing and wiring to power things in his system, it is a darned good thing to heed.
I do not even pretend to know what Ross did inside the box, but I suspect that purple wires are sensor and computer power, while the red wires are stated as coil power. Big amp difference, big noise difference and tolerance for noise, different power needs, and suitable for separate fusing.
Had a conversation with a homebuilder of some note (who shall remain anonymous) who has chatted with Ross about doing diode isolated independent power feeds so that both engine buses are queued to power the ECU, spark coils, and injector coils. Ross approved with his standard caution to make sure the pieces are very secure or a wiring failure could be bad.
For electric fuel pumps, I would take the same perspective.
Power them from an always hot bus (or two) and know that none of this stuff can go down for anything short of massive airframe damage.
This way you can have everything required to keep running the engine backed up automatically, and in an emergency you can kill all other power to the airframe while keeping the engine running, and see if you really need to go deadstick...
Billski
| - The Matronics AeroElectric-List Email Forum - | | Use the List Feature Navigator to browse the many List utilities available such as the Email Subscriptions page, Archive Search & Download, 7-Day Browse, Chat, FAQ, Photoshare, and much more:
http://www.matronics.com/Navigator?AeroElectric-List |
|
|
|
Back to top |
|
 |
nuckolls.bob(at)aeroelect Guest
|
Posted: Thu Sep 23, 2021 12:57 pm Post subject: SDS CPI-2 Circuit Protection Question |
|
|
Quote: | I think that there is, for multiple reasons. 1st, the coil circuits are *really* noisy. With a common wire feeding both, the noise has a direct path into the supply for the ECU. (The 'filter' method, the battery, would be a long ways away.)� 2nd, if he's using the system fuse to protect the cpu (not good practice, but many avionics makers have been known to do it), 10A won't do it. 3rd (for me, anyway), I'd fuse each coil block separately; not all coils on one fuse. All that separate fusing means a single failure can't take out something else, like the coil pack taking the ECU with it when the fuse blows. ATC/ATO fuse blocks are relatively cheap and very compact for many circuits, so it's easy to isolate each coil. If a coil goes shorted, separate fuses could at least keep one pair of cylinders firing. Might make the difference between the runway and the fence. (Failure modes effects analysis.) |
Agreed. Do you KNOW what the current demands are on
each of those leads? I've communicated with perhaps
a half dozen electronic engine systems providers over
the years and I've yet to find one that could tell me
what the ENERGY requirements were on each supply line
nor could they define peak currents, duty cycles or
repetition rates. If they were being offered onto
a type certificated airplane, inquiring minds would
insist on knowing . . .
Quote: | One other thing that might be 'just me', but I would not put the engine circuits on the main bus, or any airframe bus. My reasoning is, training. Assuming that you have years of flying traditional a/c engines under your belt, if you ever have the very rare but heavily trained-for 'smoke in the cockpit' situation, what's the first thing you're trained do? Will you be able to override decades of trained-in muscle memory? I doubt I could, so my engine stuff is on a separate, dedicated engine bus.
|
Why not the battery bus? Fuseblock next to battery
contactor. Conservative fuses to individual feeds.
Switches have absolute control over 'what's hot'.
Stone simple, minimal parts count distribution
system. Yes, ignitions are hot with switches ON
with the rest of the airplane shut down. Isn't
that how magnetos have operated since day-one?
I'd run electric fuel pumps and any other engine
support loads from the battery bus too. You do
have the option of crafting a Z101 style, dual
path engine bus . . . but for a simple airplane,
I would favor the battery bus support of the engine.
During conditions under which you're forced
to fly dark-panel, engine-support switching-options
might be more distraction than you need just
then.
Bob . . .
Un impeachable logic: George Carlin asked, "If black boxes
survive crashes, why don't they make the whole airplane
out of that stuff?"
| - The Matronics AeroElectric-List Email Forum - | | Use the List Feature Navigator to browse the many List utilities available such as the Email Subscriptions page, Archive Search & Download, 7-Day Browse, Chat, FAQ, Photoshare, and much more:
http://www.matronics.com/Navigator?AeroElectric-List |
|
|
|
Back to top |
|
 |
Ceengland
Joined: 11 Oct 2020 Posts: 393 Location: MS
|
Posted: Thu Sep 23, 2021 4:21 pm Post subject: SDS CPI-2 Circuit Protection Question |
|
|
snipped
Quote: |
Quote: | One other thing that might be 'just me', but I would not put the engine circuits on the main bus, or any airframe bus. My reasoning is, training. Assuming that you have years of flying traditional a/c engines under your belt, if you ever have the very rare but heavily trained-for 'smoke in the cockpit' situation, what's the first thing you're trained do? Will you be able to override decades of trained-in muscle memory? I doubt I could, so my engine stuff is on a separate, dedicated engine bus.
|
�� Why not the battery bus?� Fuseblock next to battery
�� contactor. Conservative fuses to individual feeds.
�� Switches have absolute control over 'what's hot'.
�� Stone simple, minimal parts count distribution
�� system. Yes, ignitions are hot with switches ON
�� with the rest of the airplane shut down. Isn't
�� that how magnetos have operated since day-one?
�� I'd run electric fuel pumps and any other engine
�� support loads from the battery bus too. You do
�� have the option of crafting a Z101 style, dual
�� path engine bus . . . but for a simple airplane,
�� I would favor the battery bus support of the engine.
�� During conditions under which you're forced
�� to fly dark-panel, engine-support switching-options
�� might be more distraction than you need just
�� then.
� Bob . . .
| As we're both thinking, the goal was to keep operational 'switchology' as close to mags/carb as was practical, given the forced reality differences. There are extra switches within the engine system that allow switching between ECUs, etc, but the basic 'mag switch(s) at one switch location; airframe master at another location' was a prime goal.
I've got one fusible link protected heavy duty switch that controls the engine bus (with a backup bus-tie switch to feed the bus from the main bus in the unlikely event of a switch failure).� All engine related stuff including both fuel pumps are on the engine bus.
I probably would have considered the battery bus if it was ignition only (very low current demand), but all the various full-bore electronic injection type systems are going to draw around 12-15 amps continuous when a fuel pump is included. Using a separate engine bus also allowed mounting the bus (fuse block) in a much more convenient location. Mine is not a 'cookie cutter' system even compared to the SDS, etc aftermarket controller systems, and convenient access for testing, mods, etc was one of the design goals.
Charlie
This email has been checked for viruses by Avast antivirus software.
www.avast.com [url=#DAB4FAD8-2DD7-40BB-A1B8-4E2AA1F9FDF2] [/url]
| - The Matronics AeroElectric-List Email Forum - | | Use the List Feature Navigator to browse the many List utilities available such as the Email Subscriptions page, Archive Search & Download, 7-Day Browse, Chat, FAQ, Photoshare, and much more:
http://www.matronics.com/Navigator?AeroElectric-List |
|
_________________ Charlie |
|
Back to top |
|
 |
schu(at)schu.net Guest
|
Posted: Fri Sep 24, 2021 8:56 am Post subject: SDS CPI-2 Circuit Protection Question |
|
|
On 9/23/21 1:56 PM, Robert L. Nuckolls, III wrote:
Quote: | Quote: | I think that there is, for multiple reasons. 1st, the coil circuits are *really* noisy. With a common wire feeding both, the noise has a direct path into the supply for the ECU. (The 'filter' method, the battery, would be a long ways away.) 2nd, if he's using the system fuse to protect the cpu (not good practice, but many avionics makers have been known to do it), 10A won't do it. 3rd (for me, anyway), I'd fuse each coil block separately; not all coils on one fuse. All that separate fusing means a single failure can't take out something else, like the coil pack taking the ECU with it when the fuse blows. ATC/ATO fuse blocks are relatively cheap and very compact for many circuits, so it's easy to isolate each coil. If a coil goes shorted, separate fuses could at least keep one pair of cylinders firing. Might make the difference between the runway and the fence. (Failure modes effects analysis.) |
�� Agreed. Do you KNOW what the current demands are on
�� each of those leads?� I've communicated with perhaps
�� a half dozen electronic engine systems providers over
�� the years and I've yet to find one that could tell me
�� what the ENERGY requirements were on each supply line
�� nor could they define peak currents, duty cycles or
�� repetition rates.� If they were being offered onto
�� a type certificated airplane, inquiring minds would
�� insist on knowing . . .
|
I'm the original poster of that VAF message.� A few messages down I posted this thread which explains what is going on:
https://vansairforce.net/community/showthread.php?p=1445172
It's as expected, they are worried about the coil being too noisy, but a counter point to this is when it switches to backup power, it pulls both ECU and coil power from a single 18g wire to the battery.
This begs a few questions:
1.� How much impedance does a switch vs a fuse vs a breaker impose on the system? � Does having a single switch and breaker directly attached to a battery with less than 2" of wire with both ECU and coil wires connected south of that make a significant noise difference compared to two switches and two breakers directly attached to the battery in the same manor with the ECU and coil on each?� From a wire perspective they are nearly the same with only 2" of wire sharing both systems so I doubt that would make a huge difference, but I'm less sure about the switches and breakers.
2.� With the talk of a dedicated engine bus, I'm assuming that it would be attached to the battery directly.� So, if you have 2ft 10g wire from a battery to an engine bus and another 2ft 10g wire from a battery to a main bus that has modern avionics on it, how much does that 4ft of 10G wire insulate the avionics from the noisy coil?
Seems to me that this has more to do with contact points, wire gauge, and length of runs over the simplistic "dedicated bus is good and shared bus is bad."
schu
�
| - The Matronics AeroElectric-List Email Forum - | | Use the List Feature Navigator to browse the many List utilities available such as the Email Subscriptions page, Archive Search & Download, 7-Day Browse, Chat, FAQ, Photoshare, and much more:
http://www.matronics.com/Navigator?AeroElectric-List |
|
|
|
Back to top |
|
 |
Ceengland
Joined: 11 Oct 2020 Posts: 393 Location: MS
|
Posted: Fri Sep 24, 2021 10:44 am Post subject: SDS CPI-2 Circuit Protection Question |
|
|
On 9/24/2021 11:55 AM, Matthew Schumacher wrote:
Quote: | On 9/23/21 1:56 PM, Robert L. Nuckolls, III wrote:
Quote: | Quote: | I think that there is, for multiple reasons. 1st, the coil circuits are *really* noisy. With a common wire feeding both, the noise has a direct path into the supply for the ECU. (The 'filter' method, the battery, would be a long ways away.) 2nd, if he's using the system fuse to protect the cpu (not good practice, but many avionics makers have been known to do it), 10A won't do it. 3rd (for me, anyway), I'd fuse each coil block separately; not all coils on one fuse. All that separate fusing means a single failure can't take out something else, like the coil pack taking the ECU with it when the fuse blows. ATC/ATO fuse blocks are relatively cheap and very compact for many circuits, so it's easy to isolate each coil. If a coil goes shorted, separate fuses could at least keep one pair of cylinders firing. Might make the difference between the runway and the fence. (Failure modes effects analysis.) |
�� Agreed. Do you KNOW what the current demands are on
�� each of those leads?� I've communicated with perhaps
�� a half dozen electronic engine systems providers over
�� the years and I've yet to find one that could tell me
�� what the ENERGY requirements were on each supply line
�� nor could they define peak currents, duty cycles or
�� repetition rates.� If they were being offered onto
�� a type certificated airplane, inquiring minds would
�� insist on knowing . . .
|
I'm the original poster of that VAF message.� A few messages down I posted this thread which explains what is going on:
https://vansairforce.net/community/showthread.php?p=1445172
It's as expected, they are worried about the coil being too noisy, but a counter point to this is when it switches to backup power, it pulls both ECU and coil power from a single 18g wire to the battery.
This begs a few questions:
1.� How much impedance does a switch vs a fuse vs a breaker impose on the system? � Does having a single switch and breaker directly attached to a battery with less than 2" of wire with both ECU and coil wires connected south of that make a significant noise difference compared to two switches and two breakers directly attached to the battery in the same manor with the ECU and coil on each?� From a wire perspective they are nearly the same with only 2" of wire sharing both systems so I doubt that would make a huge difference, but I'm less sure about the switches and breakers.
2.� With the talk of a dedicated engine bus, I'm assuming that it would be attached to the battery directly.� So, if you have 2ft 10g wire from a battery to an engine bus and another 2ft 10g wire from a battery to a main bus that has modern avionics on it, how much does that 4ft of 10G wire insulate the avionics from the noisy coil?
Seems to me that this has more to do with contact points, wire gauge, and length of runs over the simplistic "dedicated bus is good and shared bus is bad."
schu
�
| If the entire backup power is supposed to be supplied on a single 18 ga wire, then you might want to get a 2nd opinion on the quality of the design. The system will need the same current and noise immunity from the backup supply as the primary, unless some current consumer is deleted in backup mode. What would that current consumer be? Why is it not needed in backup mode, but it is needed in primary mode?
1. Don't understand the 2" of wire reference. No practical system will have that. The battery is effectively a rather large 'filter'. If noise from the high-power noise generator (the coils) has to flow all the way back to the battery before traveling down the other power wire to the ECU, the battery can at least partially attenuate some of that noise. And noise isn't the only issue, as has been pointed out in other posts.
2. My requirement in my system for a separate engine bus, as stated in other posts, has nothing to do with noise, or resistance, or impedance. It's an *operational* requirement for me, to keep fundamental engine control isolated from fundamental airframe electrical control. 'Mag switches' independent of the airframe 'Master switch'. The goal is to mimic as closely as possible the emergency procedures we were all trained to follow when we suspect an electrical issue in flight. The dedicated bus also eliminates multiple potential failure points in the supply path to the engine which are not in the loop in traditional a/c systems (master switch, master contactor, etc).
Charlie
This email has been checked for viruses by Avast antivirus software.
www.avast.com [url=#DAB4FAD8-2DD7-40BB-A1B8-4E2AA1F9FDF2] [/url]
| - The Matronics AeroElectric-List Email Forum - | | Use the List Feature Navigator to browse the many List utilities available such as the Email Subscriptions page, Archive Search & Download, 7-Day Browse, Chat, FAQ, Photoshare, and much more:
http://www.matronics.com/Navigator?AeroElectric-List |
|
_________________ Charlie |
|
Back to top |
|
 |
schu(at)schu.net Guest
|
Posted: Fri Sep 24, 2021 1:02 pm Post subject: SDS CPI-2 Circuit Protection Question |
|
|
On 9/24/21 11:47 AM, Charlie England wrote:
Quote: | If the entire backup power is supposed to be supplied on a single 18 ga wire, then you might want to get a 2nd opinion on the quality of the design. The system will need the same current and noise immunity from the backup supply as the primary, unless some current consumer is deleted in backup mode. What would that current consumer be? Why is it not needed in backup mode, but it is needed in primary mode?
|
This is how it's designed:
http://www.sdsefi.com/cpi2switches.jpg
There are two wires for normal power, the red coil wire and the purple ECU wire.� For the backup battery both the coil and ECU are powered through a single 18g wire through a fuse:
http://www.sdsefi.com/battbox1.jpg
My current plan is to tie the battery backup to my aux bus which has it's own SD-8 alternator and a small battery.� This conforms to their recommendation of
"Please note, this battery will run a dual system for about 20 minutes at 2500 rpm in the event that the main alternator and main battery go down. If you need more power duration for your typical missions, we suggest you install a larger battery than this one and/or a second backup alternator."
Then, in the system, I would disable the charging circuit as my alternator does that.
Quote: |
1. Don't understand the 2" of wire reference. No practical system will have that. The battery is effectively a rather large 'filter'. If noise from the high-power noise generator (the coils) has to flow all the way back to the battery before traveling down the other power wire to the ECU, the battery can at least partially attenuate some of that noise. And noise isn't the only issue, as has been pointed out in other posts.
|
The battery is not usually mounted near this stuff, typically you would bring battery power to a bus bar with a large gauge wire, then from that to your breakers and switches then to the device.� In that case, what exactly is the difference between powering each leg through a single switch/breaker or dual switch/breakers assuming that the switches and breakers are within inches of the bus bar. If there is a large difference, how much of it is the short length of shared wire between the bus bar and switch/breaker and how much of it is the fact that you are sharing a switch/breaker?
Perhaps a picture is best.� How much noise rejection difference would one expect in the following:
[img]cid:part1.BBE86B4B.E86D1E95(at)schu.net[/img]
Quote: | 2. My requirement in my system for a separate engine bus, as stated in other posts, has nothing to do with noise, or resistance, or impedance. It's an *operational* requirement for me, to keep fundamental engine control isolated from fundamental airframe electrical control. 'Mag switches' independent of the airframe 'Master switch'. The goal is to mimic as closely as possible the emergency procedures we were all trained to follow when we suspect an electrical issue in flight. The dedicated bus also eliminates multiple potential failure points in the supply path to the engine which are not in the loop in traditional a/c systems (master switch, master contactor, etc).
| Noted.� Thanks for that feedback.
schu
| - The Matronics AeroElectric-List Email Forum - | | Use the List Feature Navigator to browse the many List utilities available such as the Email Subscriptions page, Archive Search & Download, 7-Day Browse, Chat, FAQ, Photoshare, and much more:
http://www.matronics.com/Navigator?AeroElectric-List |
|
Description: |
|
Filesize: |
53.83 KB |
Viewed: |
5051 Time(s) |
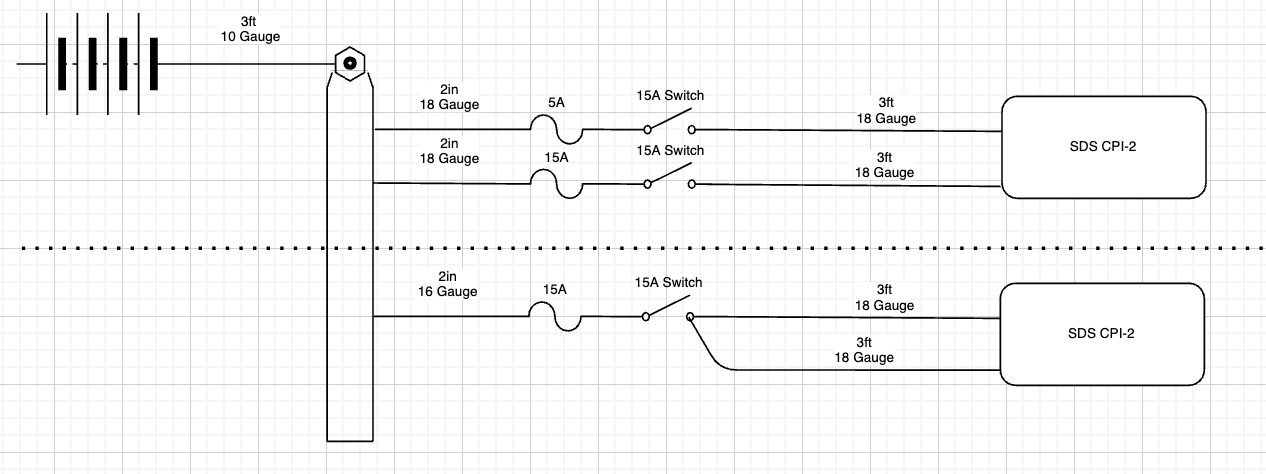
|
|
|
Back to top |
|
 |
Ceengland
Joined: 11 Oct 2020 Posts: 393 Location: MS
|
Posted: Fri Sep 24, 2021 3:03 pm Post subject: SDS CPI-2 Circuit Protection Question |
|
|
On Fri, Sep 24, 2021 at 4:07 PM Matthew Schumacher <schu(at)schu.net (schu(at)schu.net)> wrote:
Quote: | On 9/24/21 11:47 AM, Charlie England wrote:
Quote: | If the entire backup power is supposed to be supplied on a single 18 ga wire, then you might want to get a 2nd opinion on the quality of the design. The system will need the same current and noise immunity from the backup supply as the primary, unless some current consumer is deleted in backup mode. What would that current consumer be? Why is it not needed in backup mode, but it is needed in primary mode?
|
This is how it's designed:
http://www.sdsefi.com/cpi2switches.jpg
There are two wires for normal power, the red coil wire and the purple ECU wire. For the backup battery both the coil and ECU are powered through a single 18g wire through a fuse:
http://www.sdsefi.com/battbox1.jpg
My current plan is to tie the battery backup to my aux bus which has it's own SD-8 alternator and a small battery. This conforms to their recommendation of
"Please note, this battery will run a dual system for about 20 minutes at 2500 rpm in the event that the main alternator and main battery go down. If you need more power duration for your typical missions, we suggest you install a larger battery than this one and/or a second backup alternator."
Then, in the system, I would disable the charging circuit as my alternator does that.
Quote: |
1. Don't understand the 2" of wire reference. No practical system will have that. The battery is effectively a rather large 'filter'. If noise from the high-power noise generator (the coils) has to flow all the way back to the battery before traveling down the other power wire to the ECU, the battery can at least partially attenuate some of that noise. And noise isn't the only issue, as has been pointed out in other posts.
|
The battery is not usually mounted near this stuff, typically you would bring battery power to a bus bar with a large gauge wire, then from that to your breakers and switches then to the device. In that case, what exactly is the difference between powering each leg through a single switch/breaker or dual switch/breakers assuming that the switches and breakers are within inches of the bus bar. If there is a large difference, how much of it is the short length of shared wire between the bus bar and switch/breaker and how much of it is the fact that you are sharing a switch/breaker?
Perhaps a picture is best. How much noise rejection difference would one expect in the following:
Quote: | 2. My requirement in my system for a separate engine bus, as stated in other posts, has nothing to do with noise, or resistance, or impedance. It's an *operational* requirement for me, to keep fundamental engine control isolated from fundamental airframe electrical control. 'Mag switches' independent of the airframe 'Master switch'. The goal is to mimic as closely as possible the emergency procedures we were all trained to follow when we suspect an electrical issue in flight. The dedicated bus also eliminates multiple potential failure points in the supply path to the engine which are not in the loop in traditional a/c systems (master switch, master contactor, etc).
| Noted. Thanks for that feedback.
schu
|
Ah..the plot thins.
That 2" of #18 is telling you that no more than 2" of the small gauge wire should be between 'unlimited' current and the fuses. That minimizes risk from a shorted wire in the unprotected run to the fuse. The switches *should* be able to be mounted where ever it's convenient, and if the wire run is longer, the wire gets upsized to reduce voltage drop.
Your question about 1 wire for the backup vs 2 for normal operation is a valid one, and should be addressed to SDS, and if you don't get a satisfactory answer, get a 2nd opinion. If the system needs separate wires, why is a single wire safe? If it doesn't need separate wires, then why complicate the wiring? FWIW, the controller I'm personally familiar with (not SDS or the other common Lyc controller) specifies a separate feed for the ECU, and a separate feed for the coils, and a separate feed for the injectors. I know the engineer that designed the system, and I trust his opinion because he's who he is, and because it lines up with my decades of experience in other fields dealing with electrical noise & interference.
BTW, there's been at least one a/c running an electronic controller system that was lost when the master bus went down, taking the engine electrical power with it. Food for thought....
Charlie
| - The Matronics AeroElectric-List Email Forum - | | Use the List Feature Navigator to browse the many List utilities available such as the Email Subscriptions page, Archive Search & Download, 7-Day Browse, Chat, FAQ, Photoshare, and much more:
http://www.matronics.com/Navigator?AeroElectric-List |
|
_________________ Charlie |
|
Back to top |
|
 |
nuckolls.bob(at)aeroelect Guest
|
Posted: Tue Sep 28, 2021 9:22 am Post subject: SDS CPI-2 Circuit Protection Question |
|
|
Quote: | Quote: | 2. My requirement in my system for a separate engine bus, as stated in other posts, has nothing to do with noise, or resistance, or impedance. It's an *operational* requirement for me, to keep fundamental engine control isolated from fundamental airframe electrical control. 'Mag switches' independent of the airframe 'Master switch'. The goal is to mimic as closely as possible the emergency procedures we were all trained to follow when we suspect an electrical issue in flight. The dedicated bus also eliminates multiple potential failure points in the supply path to the engine which are not in the loop in traditional a/c systems (master switch, master contactor, etc). |
|
I am mystified by incorporation of a backup battery with
this system. Are we confessing to an inability to craft
a failure tolerant electrical supply to a DUAL electronic
ignition system?
Will the engine run on ONE of the two systems? If
your engine driven supply is compromised, is there
sufficient standby power generation to sustain
flight? This means your design STARTS with a
load analysis of what items are included on the
plan-b actions list.
This was the kind of thinking from which the endurance
bus was crafted about 30 years ago. Question: how much
WELL MAINTAINED BATTERY is needed to keep the airplane
comfortably airborne for a period of time equal to or
greater than design goals?
I had builders crafting systems in LongEz ships
that would exhaust a full tank of fuel during
battery only operations.
Your design goals are your own but the tools
for achieving them are ancient protocol. Know
your energy budget then provide sources to equal
or exceed that budget as determined by
analysis on the bench and confirmed by
demonstration in the air.
If you've got more than one battery on board,
you're overlooking something. If you have two
engine driven power sources, will the smaller
of the two sustain cruising flight while holding
the battery in reserve for descent and approach
to landing? If you're worrying about multiple
failures of critical items, what are the failure
modes and what are probabilities of loosing
two such devices during the consumption of one
tank of fuel?
The elegant system architecture achieves design
goals with a minimum of hardware, cockpit controls,
weight, cost, etc.
Thought problem: Z101 style engine bus. Triple
energy source (60 + 30 alternators) and a
well maintained battery sized to be determined.
Engine bus energy supplied by two delivery pathways.
All functional engine loads supplied by the bus.
No standby battery.
Failure of what system feature would put this
system at risk for unplanned arrival with the
dirt? What are the limiting factors for achieving
design goals (endurance) after having experienced
the failure?
I am concerned with talk of 'noise' in this
ignition/fuel system? Exactly what has been
demonstrated as a noise problem? Is the source
identified? What appliances are victims of this
'noise'? What is being done to bring the
antagonist into a neighborly coexistence with
all players in the electrical sandbox?
| - The Matronics AeroElectric-List Email Forum - | | Use the List Feature Navigator to browse the many List utilities available such as the Email Subscriptions page, Archive Search & Download, 7-Day Browse, Chat, FAQ, Photoshare, and much more:
http://www.matronics.com/Navigator?AeroElectric-List |
|
|
|
Back to top |
|
 |
Ceengland
Joined: 11 Oct 2020 Posts: 393 Location: MS
|
Posted: Tue Sep 28, 2021 10:39 am Post subject: SDS CPI-2 Circuit Protection Question |
|
|
On 9/28/2021 12:21 PM, Robert L. Nuckolls, III wrote:
Quote: | Quote: | Quote: | 2. My requirement in my system for a separate engine bus, as stated in other posts, has nothing to do with noise, or resistance, or impedance. It's an *operational* requirement for me, to keep fundamental engine control isolated from fundamental airframe electrical control. 'Mag switches' independent of the airframe 'Master switch'. The goal is to mimic as closely as possible the emergency procedures we were all trained to follow when we suspect an electrical issue in flight. The dedicated bus also eliminates multiple potential failure points in the supply path to the engine which are not in the loop in traditional a/c systems (master switch, master contactor, etc). | |
�� I am mystified by incorporation of a backup battery with
�� this system. Are we confessing to an inability to craft
�� a failure tolerant electrical supply to a DUAL electronic
�� ignition system?
�� Will the engine run on ONE of the two systems?� If
�� your engine driven supply is compromised, is there
�� sufficient standby power generation to sustain
�� flight? This means your design STARTS with a
�� load analysis of what items are included on the
�� plan-b actions list.
�� This was the kind of thinking from which the endurance
�� bus was crafted about 30 years ago. Question: how much
�� WELL MAINTAINED BATTERY is needed to keep the airplane
�� comfortably airborne for a period of time equal to or
�� greater than design goals?
�� I had builders crafting systems in LongEz ships
�� that would exhaust a full tank of fuel during
�� battery only operations.
�� Your design goals are your own but the tools
�� for achieving them are ancient protocol. Know
�� your energy budget then provide sources to equal
�� or exceed that budget as determined by
�� analysis on the bench and confirmed by
�� demonstration in the air.
�� If you've got more than one battery on board,
�� you're overlooking something. If you have two
�� engine driven power sources, will the smaller
�� of the two sustain cruising flight while holding
�� the battery in reserve for descent and approach
�� to landing? If you're worrying about multiple
�� failures of critical items, what are the failure
�� modes and what are probabilities of loosing
�� two such devices during the consumption of one
�� tank of fuel?
�� The elegant system architecture achieves design
�� goals with a minimum of hardware, cockpit controls,
�� weight, cost, etc.
�� Thought problem: Z101 style engine bus. Triple
�� energy source (60 + 30 alternators) and a
�� well maintained battery sized to be determined.
�� Engine bus energy supplied by two delivery pathways.
�� All functional engine loads supplied by the bus.
�� No standby battery.
�� Failure of what system feature would put this
�� system at risk for unplanned arrival with the
�� dirt? What are the limiting factors for achieving
�� design goals (endurance) after having experienced
�� the failure?
�� I am concerned with talk of 'noise' in this
�� ignition/fuel system? Exactly what has been
�� demonstrated as a noise problem? Is the source
�� identified? What appliances are victims of this
�� 'noise'? What is being done to bring the
�� antagonist into a neighborly coexistence with
�� all players in the electrical sandbox?
� | Uh, not that I disagree with most of what you wrote, but you quoted my response to the OP, not his posts. I did *speculate* on several different possible reasons that SDS recommended separate feeders for the ECU vs coils and/or injectors.
I do think you need to remember that this:
I had builders crafting systems in LongEz ships
�� that would exhaust a full tank of fuel during
�� battery only operations.
only applies to mags, or electronic ignition-only systems. The combo of electronic ignition, electronic injectors, and high current fuel pump means that a PC680 equivalent battery is good for about 40 minutes, as long as all other airframe electrical loads are minimal. If there are 5-10 amps of unshed panel loads (not unusual these days), battery-only operation could be as short as 15-20 minutes.
Automotive style injection changes the battery-only operation equations by a bunch.
Thanks,
Charlie
Virus-free. www.avast.com [url=#DAB4FAD8-2DD7-40BB-A1B8-4E2AA1F9FDF2] [/url]
| - The Matronics AeroElectric-List Email Forum - | | Use the List Feature Navigator to browse the many List utilities available such as the Email Subscriptions page, Archive Search & Download, 7-Day Browse, Chat, FAQ, Photoshare, and much more:
http://www.matronics.com/Navigator?AeroElectric-List |
|
_________________ Charlie |
|
Back to top |
|
 |
kenryan
Joined: 20 Oct 2009 Posts: 426
|
Posted: Tue Sep 28, 2021 10:49 am Post subject: SDS CPI-2 Circuit Protection Question |
|
|
Wearing a "belt and suspenders" is not elegant, but it is not necessarily a bad idea either.
On Tue, Sep 28, 2021 at 10:43 AM Charlie England <ceengland7(at)gmail.com (ceengland7(at)gmail.com)> wrote:
Quote: | On 9/28/2021 12:21 PM, Robert L. Nuckolls, III wrote:
Quote: | Quote: | Quote: | 2. My requirement in my system for a separate engine bus, as stated in other posts, has nothing to do with noise, or resistance, or impedance. It's an *operational* requirement for me, to keep fundamental engine control isolated from fundamental airframe electrical control. 'Mag switches' independent of the airframe 'Master switch'. The goal is to mimic as closely as possible the emergency procedures we were all trained to follow when we suspect an electrical issue in flight. The dedicated bus also eliminates multiple potential failure points in the supply path to the engine which are not in the loop in traditional a/c systems (master switch, master contactor, etc). | |
I am mystified by incorporation of a backup battery with
this system. Are we confessing to an inability to craft
a failure tolerant electrical supply to a DUAL electronic
ignition system?
Will the engine run on ONE of the two systems? If
your engine driven supply is compromised, is there
sufficient standby power generation to sustain
flight? This means your design STARTS with a
load analysis of what items are included on the
plan-b actions list.
This was the kind of thinking from which the endurance
bus was crafted about 30 years ago. Question: how much
WELL MAINTAINED BATTERY is needed to keep the airplane
comfortably airborne for a period of time equal to or
greater than design goals?
I had builders crafting systems in LongEz ships
that would exhaust a full tank of fuel during
battery only operations.
Your design goals are your own but the tools
for achieving them are ancient protocol. Know
your energy budget then provide sources to equal
or exceed that budget as determined by
analysis on the bench and confirmed by
demonstration in the air.
If you've got more than one battery on board,
you're overlooking something. If you have two
engine driven power sources, will the smaller
of the two sustain cruising flight while holding
the battery in reserve for descent and approach
to landing? If you're worrying about multiple
failures of critical items, what are the failure
modes and what are probabilities of loosing
two such devices during the consumption of one
tank of fuel?
The elegant system architecture achieves design
goals with a minimum of hardware, cockpit controls,
weight, cost, etc.
Thought problem: Z101 style engine bus. Triple
energy source (60 + 30 alternators) and a
well maintained battery sized to be determined.
Engine bus energy supplied by two delivery pathways.
All functional engine loads supplied by the bus.
No standby battery.
Failure of what system feature would put this
system at risk for unplanned arrival with the
dirt? What are the limiting factors for achieving
design goals (endurance) after having experienced
the failure?
I am concerned with talk of 'noise' in this
ignition/fuel system? Exactly what has been
demonstrated as a noise problem? Is the source
identified? What appliances are victims of this
'noise'? What is being done to bring the
antagonist into a neighborly coexistence with
all players in the electrical sandbox?
| Uh, not that I disagree with most of what you wrote, but you quoted my response to the OP, not his posts. I did *speculate* on several different possible reasons that SDS recommended separate feeders for the ECU vs coils and/or injectors.
I do think you need to remember that this:
I had builders crafting systems in LongEz ships
that would exhaust a full tank of fuel during
battery only operations.
only applies to mags, or electronic ignition-only systems. The combo of electronic ignition, electronic injectors, and high current fuel pump means that a PC680 equivalent battery is good for about 40 minutes, as long as all other airframe electrical loads are minimal. If there are 5-10 amps of unshed panel loads (not unusual these days), battery-only operation could be as short as 15-20 minutes.
Automotive style injection changes the battery-only operation equations by a bunch.
Thanks,
Charlie
Virus-free. www.avast.com [url=#m_-420879808160912622_DAB4FAD8-2DD7-40BB-A1B8-4E2AA1F9FDF2] [/url]
|
| - The Matronics AeroElectric-List Email Forum - | | Use the List Feature Navigator to browse the many List utilities available such as the Email Subscriptions page, Archive Search & Download, 7-Day Browse, Chat, FAQ, Photoshare, and much more:
http://www.matronics.com/Navigator?AeroElectric-List |
|
|
|
Back to top |
|
 |
david(at)carter.net Guest
|
Posted: Tue Sep 28, 2021 1:25 pm Post subject: SDS CPI-2 Circuit Protection Question |
|
|
Let's also recall that the CPI-2 is an ignition-only product. It does not provide fuel injection. The PC680 would run much longer powering just a dual CPI-2 & minimal other loads. That said, I have two alternators & a single battery (Z101 architecture) in my CPI-2 equipped plane. As long as there is gas to power the engine, the ignition should have electrons. The redundantly-powered engine bus supplies both the primary & backup power feeds to both CPI-2 ECUs & coils.
---
David Carter
david(at)carter.net (david(at)carter.net)
On Tue, Sep 28, 2021 at 2:40 PM Charlie England <ceengland7(at)gmail.com (ceengland7(at)gmail.com)> wrote:
Quote: | On 9/28/2021 12:21 PM, Robert L. Nuckolls, III wrote:
Quote: | Quote: | Quote: | 2. My requirement in my system for a separate engine bus, as stated in other posts, has nothing to do with noise, or resistance, or impedance. It's an *operational* requirement for me, to keep fundamental engine control isolated from fundamental airframe electrical control. 'Mag switches' independent of the airframe 'Master switch'. The goal is to mimic as closely as possible the emergency procedures we were all trained to follow when we suspect an electrical issue in flight. The dedicated bus also eliminates multiple potential failure points in the supply path to the engine which are not in the loop in traditional a/c systems (master switch, master contactor, etc). | |
I am mystified by incorporation of a backup battery with
this system. Are we confessing to an inability to craft
a failure tolerant electrical supply to a DUAL electronic
ignition system?
Will the engine run on ONE of the two systems? If
your engine driven supply is compromised, is there
sufficient standby power generation to sustain
flight? This means your design STARTS with a
load analysis of what items are included on the
plan-b actions list.
This was the kind of thinking from which the endurance
bus was crafted about 30 years ago. Question: how much
WELL MAINTAINED BATTERY is needed to keep the airplane
comfortably airborne for a period of time equal to or
greater than design goals?
I had builders crafting systems in LongEz ships
that would exhaust a full tank of fuel during
battery only operations.
Your design goals are your own but the tools
for achieving them are ancient protocol. Know
your energy budget then provide sources to equal
or exceed that budget as determined by
analysis on the bench and confirmed by
demonstration in the air.
If you've got more than one battery on board,
you're overlooking something. If you have two
engine driven power sources, will the smaller
of the two sustain cruising flight while holding
the battery in reserve for descent and approach
to landing? If you're worrying about multiple
failures of critical items, what are the failure
modes and what are probabilities of loosing
two such devices during the consumption of one
tank of fuel?
The elegant system architecture achieves design
goals with a minimum of hardware, cockpit controls,
weight, cost, etc.
Thought problem: Z101 style engine bus. Triple
energy source (60 + 30 alternators) and a
well maintained battery sized to be determined.
Engine bus energy supplied by two delivery pathways.
All functional engine loads supplied by the bus.
No standby battery.
Failure of what system feature would put this
system at risk for unplanned arrival with the
dirt? What are the limiting factors for achieving
design goals (endurance) after having experienced
the failure?
I am concerned with talk of 'noise' in this
ignition/fuel system? Exactly what has been
demonstrated as a noise problem? Is the source
identified? What appliances are victims of this
'noise'? What is being done to bring the
antagonist into a neighborly coexistence with
all players in the electrical sandbox?
| Uh, not that I disagree with most of what you wrote, but you quoted my response to the OP, not his posts. I did *speculate* on several different possible reasons that SDS recommended separate feeders for the ECU vs coils and/or injectors.
I do think you need to remember that this:
I had builders crafting systems in LongEz ships
that would exhaust a full tank of fuel during
battery only operations.
only applies to mags, or electronic ignition-only systems. The combo of electronic ignition, electronic injectors, and high current fuel pump means that a PC680 equivalent battery is good for about 40 minutes, as long as all other airframe electrical loads are minimal. If there are 5-10 amps of unshed panel loads (not unusual these days), battery-only operation could be as short as 15-20 minutes.
Automotive style injection changes the battery-only operation equations by a bunch.
Thanks,
Charlie
Virus-free. www.avast.com [url=#m_-1793440618398720696_DAB4FAD8-2DD7-40BB-A1B8-4E2AA1F9FDF2] [/url]
|
| - The Matronics AeroElectric-List Email Forum - | | Use the List Feature Navigator to browse the many List utilities available such as the Email Subscriptions page, Archive Search & Download, 7-Day Browse, Chat, FAQ, Photoshare, and much more:
http://www.matronics.com/Navigator?AeroElectric-List |
|
|
|
Back to top |
|
 |
nuckolls.bob(at)aeroelect Guest
|
Posted: Tue Sep 28, 2021 3:24 pm Post subject: SDS CPI-2 Circuit Protection Question |
|
|
Quote: |
I do think you need to remember that this:
I had builders crafting systems in LongEz ships
that would exhaust a full tank of fuel during
battery only operations.
only applies to mags, or electronic ignition-only systems. The combo of electronic ignition, electronic injectors, and high current fuel pump means that a PC680 equivalent battery is good for about 40 minutes, as long as all other airframe electrical loads are minimal. If there are 5-10 amps of unshed panel loads (not unusual these days), battery-only operation could be as short as 15-20 minutes.
Automotive style injection changes the battery-only operation equations by a bunch. |
How big is 'a bunch'? I'm not suggesting that
anyone strive for multi-hour cruising ops
battery only either. I'm reading a lot of
discussion wrapped in worries with
zero quantitative analysis for meeting an
as yet un-defined design goal. There's
also a sprinkling of worries about multiple
failures which are exceedingly rare.
We had some discussions here on the List
years ago on this same topic. Some of the
participants were really hard over on
keeping BOTH ignitions running when the
engine performance was adequate on one
ignition with a significant savings of
endurance energy.
Those few Ez drivers looking for extra
ordinary battery-only endurance were flying
SD-8 but most LongEz projects needed nose
ballast. So why not make it 'useful lead'
as opposed to 'dead lead'?
Seems the really important question for
a dual alternator system is whether or not
one can sustain flight on the smaller of
the two alternators? Can CRUISING loads
be reduced to a value that CAN be supported?
If you can do that, then combined with a
properly maintained battery you've got
power to burn. Once the airport is in sight,
fire up all the electro-whizzies.
But to validate that plan-b, you need ENERGY
requirements and a checklist of what can be
put in reserve during endurance cruise.
There's a youtube presentation that measures
energy demands for this ignition system. Haven't
found one for the fuel system.
One would to well to know exactly what the
energy demands are for running an engine
fitted with these systems. We have to do
it to TC a spam-can . . . there's a good
reason for that!
Bob . . .
Un impeachable logic: George Carlin asked, "If black boxes
survive crashes, why don't they make the whole airplane
out of that stuff?"
| - The Matronics AeroElectric-List Email Forum - | | Use the List Feature Navigator to browse the many List utilities available such as the Email Subscriptions page, Archive Search & Download, 7-Day Browse, Chat, FAQ, Photoshare, and much more:
http://www.matronics.com/Navigator?AeroElectric-List |
|
|
|
Back to top |
|
 |
Ceengland
Joined: 11 Oct 2020 Posts: 393 Location: MS
|
Posted: Tue Sep 28, 2021 6:50 pm Post subject: SDS CPI-2 Circuit Protection Question |
|
|
On 9/28/2021 6:23 PM, Robert L. Nuckolls, III wrote:
Quote: | Quote: |
I do think you need to remember that this:
I had builders crafting systems in LongEz ships
�� that would exhaust a full tank of fuel during
�� battery only operations.
only applies to mags, or electronic ignition-only systems. The combo of electronic ignition, electronic injectors, and high current fuel pump means that a PC680 equivalent battery is good for about 40 minutes, as long as all other airframe electrical loads are minimal. If there are 5-10 amps of unshed panel loads (not unusual these days), battery-only operation could be as short as 15-20 minutes.
Automotive style injection changes the battery-only operation equations by a bunch. |
�� How big is 'a bunch'?� I'm not suggesting that
�� anyone strive for multi-hour cruising ops
�� battery only either. I'm reading a lot of
�� discussion wrapped in worries with
�� zero quantitative analysis for meeting an
�� as yet un-defined design goal. There's
�� also a sprinkling of worries about multiple
�� failures which are exceedingly rare.
�� We had some discussions here on the List
�� years ago on this same topic. Some of the
�� participants were really hard over on
�� keeping BOTH ignitions running when the
�� engine performance was adequate on one
�� ignition with a significant savings of
�� endurance energy.
�� Those few Ez drivers looking for extra
�� ordinary battery-only endurance were flying
�� SD-8 but most LongEz projects needed nose
�� ballast. So why not make it 'useful lead'
�� as opposed to 'dead lead'?
�� Seems the really important question for
�� a dual alternator system is whether or not
�� one can sustain flight on the smaller of
�� the two alternators? Can CRUISING loads
�� be reduced to a value that CAN be supported?
�� If you can do that, then combined with a
�� properly maintained battery you've got
�� power to burn. Once the airport is in sight,
�� fire up all the electro-whizzies.
�� But to validate that plan-b, you need ENERGY
�� requirements and a checklist of what can be
�� put in reserve during endurance cruise.
�� There's a youtube presentation that measures
� energy demands for this ignition system. Haven't
�� found one for the fuel system.
�� One would to well to know exactly what the
�� energy demands are for running an engine
�� fitted with these systems. We have to do
�� it to TC a spam-can . . . there's a good
�� reason for that!
� Bob . . .
� Un impeachable logic: George Carlin asked, "If black boxes
� survive crashes, why don't they make the whole airplane
� out of that stuff?"
| Well, I didn't just pull those numbers out of one of my body's orifices. I'm pretty sure that if you ask SDS or any of the other automotive injection makers, they'll quote a number in the 10A+ range, minimum.
A single automotive style injection system, when the injection pump is included, is going to draw at least 10 amps; likely closer to 15 amps to keep the engine running. The 40 minutes of PC680 battery-only endurance was demonstrated by an engineer friend during testing of his new electronic injected RV9A (back in the pre-EFIS days, with minimal current draw from the instrument panel), and can be sanity checked using Odyssey's published discharge curves. He did the test in the air, alternator off, at low/mid engine power levels, and discontinued the test (brought the alternator back on line) when battery voltage equaled Odyssey's published voltage for a discharged battery.
I repeat: It's not about keeping two, or even one, *ignitions* running. It's about keeping the entire engine control system running, which includes not just the ignition (most of the auto style systems will fire all the plugs, by default), but the injectors (which require quantifiable higher current than the coils), the ECU (relatively low power of an amp or two, but certainly not insignificant), and the fuel pump, which is significant at a bare minimum of 4-6 amps, and more typically at 6-8 amps.
The alternative engine guys have been dealing with this for at least a decade or two longer than the 'traditional' aircraft engine guys and the numbers I'm giving have been pretty consistent among multiple users for many years.
Charlie
Virus-free. www.avast.com [url=#DAB4FAD8-2DD7-40BB-A1B8-4E2AA1F9FDF2] [/url]
| - The Matronics AeroElectric-List Email Forum - | | Use the List Feature Navigator to browse the many List utilities available such as the Email Subscriptions page, Archive Search & Download, 7-Day Browse, Chat, FAQ, Photoshare, and much more:
http://www.matronics.com/Navigator?AeroElectric-List |
|
_________________ Charlie |
|
Back to top |
|
 |
Ceengland
Joined: 11 Oct 2020 Posts: 393 Location: MS
|
Posted: Wed Sep 29, 2021 12:33 pm Post subject: SDS CPI-2 Circuit Protection Question |
|
|
Well, this is obviously my 'Duhh' moment. I thought we were talking about the full SDS engine control system. A 15 A feed just for ignition coils threw me a curve.
My apologies to everyone involved for hammering on the injection issue.
Charlie
On 9/28/2021 4:24 PM, David Carter wrote:
Quote: | Let's also recall that the CPI-2 is an ignition-only product. It does not provide fuel injection. The PC680 would run much longer powering just a dual CPI-2 & minimal other loads. That said, I have two alternators & a single battery (Z101 architecture) in my CPI-2 equipped plane. As long as there is gas to power the engine, the ignition should have electrons. The redundantly-powered engine bus supplies both the primary & backup power feeds to both CPI-2 ECUs & coils.
---
David Carter
david(at)carter.net (david(at)carter.net)
On Tue, Sep 28, 2021 at 2:40 PM Charlie England <ceengland7(at)gmail.com (ceengland7(at)gmail.com)> wrote:
Quote: | On 9/28/2021 12:21 PM, Robert L. Nuckolls, III wrote:
Quote: | Quote: | Quote: | 2. My requirement in my system for a separate engine bus, as stated in other posts, has nothing to do with noise, or resistance, or impedance. It's an *operational* requirement for me, to keep fundamental engine control isolated from fundamental airframe electrical control. 'Mag switches' independent of the airframe 'Master switch'. The goal is to mimic as closely as possible the emergency procedures we were all trained to follow when we suspect an electrical issue in flight. The dedicated bus also eliminates multiple potential failure points in the supply path to the engine which are not in the loop in traditional a/c systems (master switch, master contactor, etc). | |
I am mystified by incorporation of a backup battery with
this system. Are we confessing to an inability to craft
a failure tolerant electrical supply to a DUAL electronic
ignition system?
Will the engine run on ONE of the two systems? If
your engine driven supply is compromised, is there
sufficient standby power generation to sustain
flight? This means your design STARTS with a
load analysis of what items are included on the
plan-b actions list.
This was the kind of thinking from which the endurance
bus was crafted about 30 years ago. Question: how much
WELL MAINTAINED BATTERY is needed to keep the airplane
comfortably airborne for a period of time equal to or
greater than design goals?
I had builders crafting systems in LongEz ships
that would exhaust a full tank of fuel during
battery only operations.
Your design goals are your own but the tools
for achieving them are ancient protocol. Know
your energy budget then provide sources to equal
or exceed that budget as determined by
analysis on the bench and confirmed by
demonstration in the air.
If you've got more than one battery on board,
you're overlooking something. If you have two
engine driven power sources, will the smaller
of the two sustain cruising flight while holding
the battery in reserve for descent and approach
to landing? If you're worrying about multiple
failures of critical items, what are the failure
modes and what are probabilities of loosing
two such devices during the consumption of one
tank of fuel?
The elegant system architecture achieves design
goals with a minimum of hardware, cockpit controls,
weight, cost, etc.
Thought problem: Z101 style engine bus. Triple
energy source (60 + 30 alternators) and a
well maintained battery sized to be determined.
Engine bus energy supplied by two delivery pathways.
All functional engine loads supplied by the bus.
No standby battery.
Failure of what system feature would put this
system at risk for unplanned arrival with the
dirt? What are the limiting factors for achieving
design goals (endurance) after having experienced
the failure?
I am concerned with talk of 'noise' in this
ignition/fuel system? Exactly what has been
demonstrated as a noise problem? Is the source
identified? What appliances are victims of this
'noise'? What is being done to bring the
antagonist into a neighborly coexistence with
all players in the electrical sandbox?
| Uh, not that I disagree with most of what you wrote, but you quoted my response to the OP, not his posts. I did *speculate* on several different possible reasons that SDS recommended separate feeders for the ECU vs coils and/or injectors.
I do think you need to remember that this:
I had builders crafting systems in LongEz ships
that would exhaust a full tank of fuel during
battery only operations.
only applies to mags, or electronic ignition-only systems. The combo of electronic ignition, electronic injectors, and high current fuel pump means that a PC680 equivalent battery is good for about 40 minutes, as long as all other airframe electrical loads are minimal. If there are 5-10 amps of unshed panel loads (not unusual these days), battery-only operation could be as short as 15-20 minutes.
Automotive style injection changes the battery-only operation equations by a bunch.
Thanks,
Charlie
Virus-free. www.avast.com [url=#m_-1793440618398720696_DAB4FAD8-2DD7-40BB-A1B8-4E2AA1F9FDF2] [/url]
|
|
| - The Matronics AeroElectric-List Email Forum - | | Use the List Feature Navigator to browse the many List utilities available such as the Email Subscriptions page, Archive Search & Download, 7-Day Browse, Chat, FAQ, Photoshare, and much more:
http://www.matronics.com/Navigator?AeroElectric-List |
|
_________________ Charlie |
|
Back to top |
|
 |
|
|
You cannot post new topics in this forum You cannot reply to topics in this forum You cannot edit your posts in this forum You cannot delete your posts in this forum You cannot vote in polls in this forum You cannot attach files in this forum You can download files in this forum
|
Powered by phpBB © 2001, 2005 phpBB Group
|