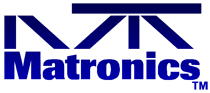 |
Matronics Email Lists Web Forum Interface to the Matronics Email Lists
|
View previous topic :: View next topic |
Author |
Message |
Patrick Brannan
Joined: 03 Mar 2019 Posts: 8
|
Posted: Mon May 16, 2022 7:13 am Post subject: two-battery, fuel pump circuit protection |
|
|
Hello all,
I have Bob's book and am working on a schematic for an electrically-dependent (SDS EFII) aircraft. SDS calls for redundant fuel pumps and a 15A fuse/cb for each pump. This makes good sense.
In Z-19 there are two engine busses. One called Master. The other I have renamed to backup. These busses bypass the contacters and are always hot. All that is required to power either engine is to turn the MASTER POWER, or BACKUP power switches on.
You will notice a FUEL PUMP fuse on both busses.
It seems to me that the #2 fuel pump should have it's own fuse / CB.
There should not be two fuses in series for either pump.
I'm not wild about running unprotected wire off a bus.
I think that leaves me with putting a backup fuel pump fuse on both the master and backup engine busses and using triple-throw switches for the engine switches.
Does anyone see a better way of handling this? I'm not wild about having redundant circuit protection for each fuel pump, I think it could be confusing, but I'm also not seeing a great alternative.
A partial screenshot of my schematic, created in Inkscape, is attached. It shows fuses for the primary fuel pump on both engine busses. I will probably use circuit breakers for this application instead, so don't take that too literally.
Thoughts on fuse vs circuit breaker for fuel pumps will also be appreciated.
Thanks,
Patrick
| - The Matronics AeroElectric-List Email Forum - | | Use the List Feature Navigator to browse the many List utilities available such as the Email Subscriptions page, Archive Search & Download, 7-Day Browse, Chat, FAQ, Photoshare, and much more:
http://www.matronics.com/Navigator?AeroElectric-List |
|
Description: |
|
Filesize: |
209.48 KB |
Viewed: |
3729 Time(s) |
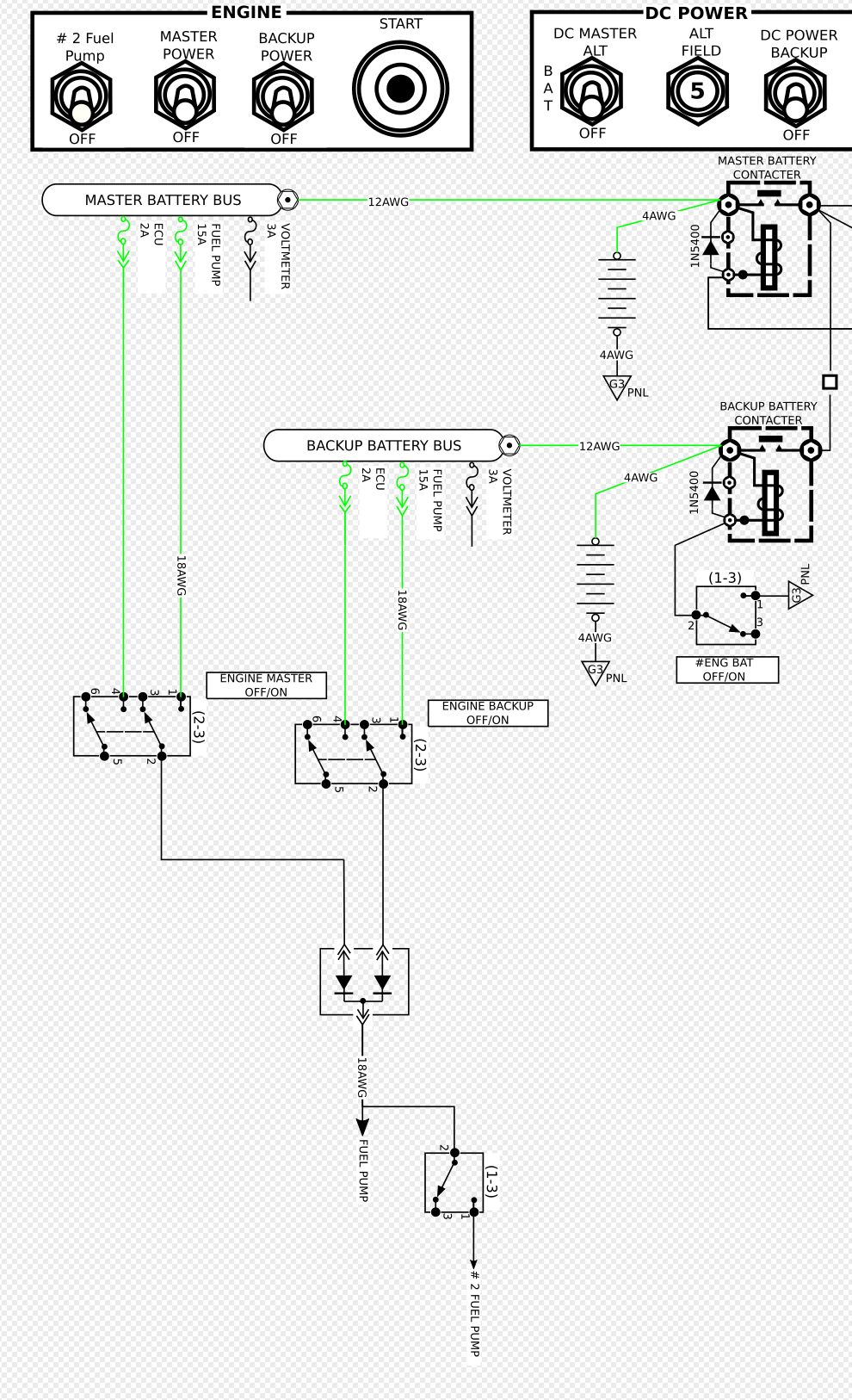
|
|
|
Back to top |
|
 |
rnjcurtis(at)charter.net Guest
|
Posted: Mon May 16, 2022 2:25 pm Post subject: two-battery, fuel pump circuit protection |
|
|
Sent from my Verizon Wireless 4G LTE smartphone
-------- Original message --------
From: Patrick Brannan <psbrannan(at)pm.me>
Date: 05/16/2022 11:13 (GMT-05:00)
To: AeroElectric-List Digest Server <aeroelectric-list(at)matronics.com>
Subject: AeroElectric-List: two-battery, fuel pump circuit protection
Hello all,
I have Bob's book and am working on a schematic for an electrically-dependent (SDS EFII) aircraft. SDS calls for redundant fuel pumps and a 15A fuse/cb for each pump. This makes good sense.
In Z-19 there are two engine busses. One called Master. The other I have renamed to backup. These busses bypass the contacters and are always hot. All that is required to power either engine is to turn the MASTER POWER, or BACKUP power switches on.
You will notice a FUEL PUMP fuse on both busses.
It seems to me that the #2 fuel pump should have it's own fuse / CB.
There should not be two fuses in series for either pump.
I'm not wild about running unprotected wire off a bus.
I think that leaves me with putting a backup fuel pump fuse on both the master and backup engine busses and using triple-throw switches for the engine switches.
Does anyone see a better way of handling this? I'm not wild about having redundant circuit protection for each fuel pump, I think it could be confusing, but I'm also not seeing a great alternative.
A partial screenshot of my schematic, created in Inkscape, is attached. It shows fuses for the primary fuel pump on both engine busses. I will probably use circuit breakers for this application instead, so don't take that too literally.
Thoughts on fuse vs circuit breaker for fuel pumps will also be appreciated.
Thanks,
Patrick
When I built my electrically dependent plane I did a very simple system:
I have 2 battery busses, located close to the batteries, just like you do. From bus 1 I have a fuse and a wire going to a spst switch and on to ignition 1. Also from bus 1 I have a fuse and wire going to another spst switch and to fuel pump 1. This exact configuration is repeated from bus 2 to ignition 2 and fuel pump 2. This is stupid simple and no single failure will shut down the engine.
Roger
| - The Matronics AeroElectric-List Email Forum - | | Use the List Feature Navigator to browse the many List utilities available such as the Email Subscriptions page, Archive Search & Download, 7-Day Browse, Chat, FAQ, Photoshare, and much more:
http://www.matronics.com/Navigator?AeroElectric-List |
|
|
|
Back to top |
|
 |
user9253
Joined: 28 Mar 2008 Posts: 1927 Location: Riley TWP Michigan
|
Posted: Mon May 16, 2022 3:47 pm Post subject: Re: two-battery, fuel pump circuit protection |
|
|
Patrick, The wire downstream of the dual diodes is a single point of failure. When it fails, both pumps stop working. The diodes can be eliminated and wire as Roger did. Another option is to install a second dual diode so that any single failure will not shut off both pumps.
| - The Matronics AeroElectric-List Email Forum - | | Use the List Feature Navigator to browse the many List utilities available such as the Email Subscriptions page, Archive Search & Download, 7-Day Browse, Chat, FAQ, Photoshare, and much more:
http://www.matronics.com/Navigator?AeroElectric-List |
|
_________________ Joe Gores |
|
Back to top |
|
 |
Ceengland
Joined: 11 Oct 2020 Posts: 391 Location: MS
|
Posted: Mon May 16, 2022 3:56 pm Post subject: two-battery, fuel pump circuit protection |
|
|
On 5/16/2022 10:13 AM, Patrick Brannan wrote:
Quote: | Hello all,
I have Bob's book and am working on a schematic for an electrically-dependent (SDS EFII) aircraft. SDS calls for redundant fuel pumps and a 15A fuse/cb for each pump. This makes good sense.
In Z-19 there are two engine busses. One called Master. The other I have renamed to backup. These busses bypass the contacters and are always hot. All that is required to power either engine is to turn the MASTER POWER, or BACKUP power switches on.
You will notice a FUEL PUMP fuse on both busses.
It seems to me that the #2 fuel pump should have it's own fuse / CB.
There should not be two fuses in series for either pump.
I'm not wild about running unprotected wire off a bus.
I think that leaves me with putting a backup fuel pump fuse on both the master and backup engine busses and using triple-throw switches for the engine switches.
Does anyone see a better way of handling this? I'm not wild about having redundant circuit protection for each fuel pump, I think it could be confusing, but I'm also not seeing a great alternative.
A partial screenshot of my schematic, created in Inkscape, is attached. It shows fuses for the primary fuel pump on both engine busses. I will probably use circuit breakers for this application instead, so don't take that too literally.
Thoughts on fuse vs circuit breaker for fuel pumps will also be appreciated.
Thanks,
Patrick
| Hi Patrick,
A few 'FWIW' comments.
I can see the logic of using the diode array for the primary pump and using separate buses for the two ignitions, but my choice was a single engine bus controlled by a high current switch, and an alternate feed path to the bus from the main airframe bus. My dual pumps are both on that engine bus, but have individual switches.
There's no way to avoid a more complicated control system when running electronic engine controls, but I tried to get 'buttonology' (really, the actions we've trained ourselves to take when we have engine issues in flight) to act like traditional engine troubleshooting. I can switch between engine controllers (mine is full fuel/ignition control) without switching pumps, and I can switch pumps without switching controllers.
The most significant FMEA issue I see with your drawing is the diode block. While failure may be very rare, if it does fail you lose both pumps. Sometimes we must accept single point of failure situations to accomplish something else, but this one seems pretty easy to fix. My choice would obviously to go with separate switches, but separate diode blocks (with outputs Y'd together) could mitigate the risk of one diode's failure taking out the other in a single block.
Charlie
Virus-free. www.avast.com [url=#DAB4FAD8-2DD7-40BB-A1B8-4E2AA1F9FDF2] [/url]
| - The Matronics AeroElectric-List Email Forum - | | Use the List Feature Navigator to browse the many List utilities available such as the Email Subscriptions page, Archive Search & Download, 7-Day Browse, Chat, FAQ, Photoshare, and much more:
http://www.matronics.com/Navigator?AeroElectric-List |
|
_________________ Charlie |
|
Back to top |
|
 |
johnbright
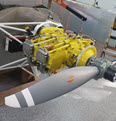
Joined: 14 Dec 2011 Posts: 166 Location: Newport News, VA
|
Posted: Mon May 16, 2022 4:34 pm Post subject: Re: two-battery, fuel pump circuit protection |
|
|
Patrick Brannan wrote: | ... I have Bob's book and am working on a schematic for an electrically-dependent (SDS EFI+I) aircraft.
.
.
In Z-19...
.
. |
Questions:
What engine and aircraft?
Dual ECUs?
Quick comments re your "engne-busses.png" and Z19:
Z19 was designed for automotive engines that do not accommodate two alternators. It shows one ECU but does not show the coils and injectors. Note how fuel pump 2 is powered in Z19.
You have SPOFs downstream of the fuel pump diodes.
You do not show the injectors or coilpacks.
Be aware the injectors are not powered by the ECU but driven to ground by its open-collector driver section.
Preflight will require turning off pump 1 while pump 2 is running, your proposal "engne-busses.png" does not support this.
Preflight will want to depower a pump without depowering the ECUs.
I imagine you want Z101, it's not in the Aeroelectric Connection book at this time, find it in folder “Adobe_Architecture_Pdfs/" at https://www.aeroelectric.com/PPS/
IMO you chose the best EFI+I system, SDS. SDS has a cleaner injector installation compared to the other popular system. The other vendor also shows preventable SPOFs in their electrical power system. Makes a person wonder what SPOFs we can’t see.
FYI SDS has a recommended electrical power schematic, dual battery single alternator, simple. Search for “fusing” at http://www.sdsefi.com/aircraft.html
I would not pair 2/3 injectors on one fuse as optionally indicated.
Details of EFI+I system are omitted; I show details of a four-cylinder system as delivered in 2017 in folder 2/SDS EFI+I of my Google drive linked in my signature below.
I chose Z101 single battery dual alternator, also simple and does not rely on battery capacity to keep the engine running in case of a failed alternator or main master off.
Have a look at my Z101-inspired power schematic for dual SDS EFI+I equipped RV-6A if you like. It's in folder 1 of my Google drive linked in my signature below. It meets the spirit of FAR 23.1361 and allows for the fire-in-the-cockpit-main-master-off scenario with the engine still running. I also have a flight checklist and FMEA.
| - The Matronics AeroElectric-List Email Forum - | | Use the List Feature Navigator to browse the many List utilities available such as the Email Subscriptions page, Archive Search & Download, 7-Day Browse, Chat, FAQ, Photoshare, and much more:
http://www.matronics.com/Navigator?AeroElectric-List |
|
_________________ John Bright, RV-6A, at FWF, O-360
Z-101 single batt dual alt SDS EM-5-F.
john_s_bright@yahoo.com, Newport News, Va
N1921R links |
|
Back to top |
|
 |
Patrick Brannan
Joined: 03 Mar 2019 Posts: 8
|
Posted: Fri May 20, 2022 8:18 am Post subject: Re: two-battery, fuel pump circuit protection |
|
|
The engine is a Lycoming O-290-D2. The aircraft is a Marquart Charger, a 2-seat biplane. The system is SDS EFII, single ECU, dual coil packs.
The fact that I posted an incomplete schematic has confused everyone. I was trying to ask a conceptual question without providing full information. Nevertheless, the responses have been extremely helpful and I think I can now boil down my questions into easier to understand points.
With electrically dependent engine you need a backup electrical source. That source will either be a battery or an alternator. With a single battery system the battery can take down both alternators unless you do some special wiring. The SD8 alternator does not provide sufficient power to run my engine when at low RPMs. The fuel pumps are the main culprit.
Z-19 takes the approach of using 1 alternator and 2 batteries. I believe that 2-batteries can provide a simpler, more reliable solution.
Z-19 takes the approach of having 2 engine busses running into a diode array (half a bridge rectifier) for critical loads. The intent, in the notes, is that the rectifier (diode array) be mounted at the critical piece of equipment. So in my case the fuel pump bridge rectifier would be mounted to the fuel pump bracket with a short run from the rectifier to the pump. That still leave a short run of cable from the rectifier to the pump that, with two engine busses each with a 15A fuse, might get 30A if it was pulling from both busses. This is something to contemplate.
This gets at what I don't like about Z-19: 2 engine busses. As others have noted, I have not yet drawn in the injectors or coils. I will, but for now there's less spaghetti on the schematic without them. But if they were there it would be a lot of duplication.
The next aspect that I don't like about Z-19 is that the aux fuel pump can only be run from the main battery. So, as you can see in the attached schematic, I wired it like the main fuel pump, with a switch and a diode array.
I would rather use a Zener diode, switch, relay, or some other solution to power a single engine buss. It seems like I could do away with the backup battery buss entirely, run a line from the backup battery to a zener diode then a switch and then to the main engine buss. I believe, but cannot yet swear to it, that the max current with 2 fuel pumps running will be 20A. More likely is a running current of ~10A following an alternator failure as I would not have both fuel pumps running and would not be running at full power. Nevertheless the takeoff and landing procedure calls for both pumps on so the whatever I do has to handle the full load.
So that we are all on the same page: This is an aerobatic biplane. It will not be flown IFR or at night over the Rockies. I will put lights on it and may fly it night VFR a few times. That's about it. What I need is sufficient run time to get to an airport from the point where I know there is a failure.
Attached is a PDF version of the schematic as adopted from Z-19. Only the fuel pumps and ECU are included.
johnbright wrote: | Patrick Brannan wrote: | ... I have Bob's book and am working on a schematic for an electrically-dependent (SDS EFI+I) aircraft.
.
.
In Z-19...
.
. |
Questions:
What engine and aircraft?
Dual ECUs?
Quick comments re your "engne-busses.png" and Z19:
Z19 was designed for automotive engines that do not accommodate two alternators. It shows one ECU but does not show the coils and injectors. Note how fuel pump 2 is powered in Z19.
You have SPOFs downstream of the fuel pump diodes.
You do not show the injectors or coilpacks.
Be aware the injectors are not powered by the ECU but driven to ground by its open-collector driver section.
Preflight will require turning off pump 1 while pump 2 is running, your proposal "engne-busses.png" does not support this.
Preflight will want to depower a pump without depowering the ECUs.
I imagine you want Z101, it's not in the Aeroelectric Connection book at this time, find it in folder “Adobe_Architecture_Pdfs/" at https://www.aeroelectric.com/PPS/
IMO you chose the best EFI+I system, SDS. SDS has a cleaner injector installation compared to the other popular system. The other vendor also shows preventable SPOFs in their electrical power system. Makes a person wonder what SPOFs we can’t see.
FYI SDS has a recommended electrical power schematic, dual battery single alternator, simple. Search for “fusing” at http://www.sdsefi.com/aircraft.html
I would not pair 2/3 injectors on one fuse as optionally indicated.
Details of EFI+I system are omitted; I show details of a four-cylinder system as delivered in 2017 in folder 2/SDS EFI+I of my Google drive linked in my signature below.
I chose Z101 single battery dual alternator, also simple and does not rely on battery capacity to keep the engine running in case of a failed alternator or main master off.
Have a look at my Z101-inspired power schematic for dual SDS EFI+I equipped RV-6A if you like. It's in folder 1 of my Google drive linked in my signature below. It meets the spirit of FAR 23.1361 and allows for the fire-in-the-cockpit-main-master-off scenario with the engine still running. I also have a flight checklist and FMEA. |
| - The Matronics AeroElectric-List Email Forum - | | Use the List Feature Navigator to browse the many List utilities available such as the Email Subscriptions page, Archive Search & Download, 7-Day Browse, Chat, FAQ, Photoshare, and much more:
http://www.matronics.com/Navigator?AeroElectric-List |
|
Description: |
|
 Download |
Filename: |
schematic.pdf |
Filesize: |
53.57 KB |
Downloaded: |
229 Time(s) |
|
|
Back to top |
|
 |
johnbright
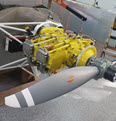
Joined: 14 Dec 2011 Posts: 166 Location: Newport News, VA
|
Posted: Sat May 21, 2022 9:06 am Post subject: Re: two-battery, fuel pump circuit protection |
|
|
Patrick Brannan wrote: | The engine is a Lycoming O-290-D2. The aircraft is a Marquart Charger, a 2-seat biplane. The system is SDS EFII, single ECU, dual coil packs.
|
OK, similar to my RV-6A in terms of four-cylinder lycoming, tractor configuration. And if the battery(s) are on the hot side of the firewall that's another similarity.
I have dual ECUs. Must be that with single ECU, both coil packs are triggered by the one ECU.
Quote: | ...
With electrically dependent engine you need a backup electrical source. That source will either be a battery or an alternator.
|
Or both, ref Z14. But AFAIK Bob Nuckolls believes Z101 single battery dual alternator is as reliable as Z14 dual battery dual alternator.
Quote: |
With a single battery system the battery can take down both alternators unless you do some special wiring.
|
Please explain battery failure modes and special wiring.
Quote: |
The SD8 alternator does not provide sufficient power to run my engine when at low RPMs. The fuel pumps are the main culprit.
|
Why such a small backup alternator when B&C 410, 425, and 462 and Monkworkz MZ-30L are available?
Quote: |
Z-19 takes the approach of using 1 alternator and 2 batteries. I believe that 2-batteries can provide a simpler, more reliable solution.
|
Dual alternators with one alternator inop gives you endurance of fuel on board regardless of battery capacity.
Quote: |
Z-19 takes the approach of having 2 engine busses running into a diode array (half a bridge rectifier) for critical loads. The intent, in the notes, is that the rectifier (diode array) be mounted at the critical piece of equipment.
|
Note 24: "...In any case, the diode bridge should be located as close as practical to the critical system’s input power connection."
I wonder why that is.
Quote: |
So in my case the fuel pump bridge rectifier would be mounted to the fuel pump bracket with a short run from the rectifier to the pump. That still leaves a short run of cable from the rectifier to the pump that, with two engine busses each with a 15A fuse, might get 30A if it was pulling from both busses. This is something to contemplate.
|
If you have the Walbro GSL393 pumps, I have the spec sheet in my files, folder 4. One pump draws 5-1/4 A at 45 PSI and 13.5 V.
https://drive.google.com/drive/folders/1u6GeZo6pmBWsKykLNVQMvu4o1VEVyP4K
Quote: |
This gets at what I don't like about Z-19: 2 engine busses. As others have noted, I have not yet drawn in the injectors or coils. I will, but for now there's less spaghetti on the schematic without them. But if they were there it would be a lot of duplication.
The next aspect that I don't like about Z-19 is that the aux fuel pump can only be run from the main battery. So, as you can see in the attached schematic, I wired it like the main fuel pump, with a switch and a diode array.
|
Why not have one engine bus, feed the engine bus from each battery by separate relays in series with diodes in the feeders from each battery, and put all engine related items on that one engine bus. I did this with Z14 before I switched to Z101.
Quote: |
I would rather use a Zener diode, switch, relay, or some other solution to power a single engine buss.
|
I don't understand Zener diode, I suppose you mean Schottky.
Quote: |
It seems like I could do away with the backup battery buss entirely, run a line from the backup battery to a Zener [Schottky] diode then a switch and then to the main engine buss.
|
Switch violates FAR 23.1361, a remotely-operated switch (relay) fixes that. Note the FAR calls for 5 A protection and CBs are allowed. Bob Nuckolls allows for 7-1/2 A fuses because fuses open faster than CBs.
Quote: |
I believe, but cannot yet swear to it, that the max current with 2 fuel pumps running will be 20A. More likely is a running current of ~10A following an alternator failure as I would not have both fuel pumps running and would not be running at full power. Nevertheless the takeoff and landing procedure calls for both pumps on so whatever I do has to handle the full load.
|
Ref my load analysis in my folder 3. Barring edits, row 19 in the spreadsheet has totals of engine loads, 9 A cruise, 14.2 A low altitude, and 7.9 A in what I call endurance mode (limited Amp-Hours available, turn off one coilpack and one pump). I would not argue with landing in endurance mode with the single alternator inop.
Engine power setting does not have a huge effect on current draw. Injector duty cycle varies with power setting. 10 GPH is 1.28A for four injectors and 5 GPH is 0.64 A. Ref my "Calculations Measurements and Specs" spreadwheet in my folder 3. Barring edits, ref rows 34 thru 42 in the spreadsheet.
https://drive.google.com/drive/folders/1u6GeZo6pmBWsKykLNVQMvu4o1VEVyP4K
Quote: |
So that we are all on the same page: This is an aerobatic biplane. It will not be flown IFR or at night over the Rockies. I will put lights on it and may fly it night VFR a few times. That's about it. What I need is sufficient run time to get to an airport from the point where I know there is a failure.
Attached is a PDF version of the schematic as adopted from Z-19. Only the fuel pumps and ECU are included.
|
| - The Matronics AeroElectric-List Email Forum - | | Use the List Feature Navigator to browse the many List utilities available such as the Email Subscriptions page, Archive Search & Download, 7-Day Browse, Chat, FAQ, Photoshare, and much more:
http://www.matronics.com/Navigator?AeroElectric-List |
|
_________________ John Bright, RV-6A, at FWF, O-360
Z-101 single batt dual alt SDS EM-5-F.
john_s_bright@yahoo.com, Newport News, Va
N1921R links
Last edited by johnbright on Sat May 21, 2022 6:50 pm; edited 3 times in total |
|
Back to top |
|
 |
Patrick Brannan
Joined: 03 Mar 2019 Posts: 8
|
Posted: Sat May 21, 2022 9:34 am Post subject: Re: two-battery, fuel pump circuit protection |
|
|
user9253 wrote: | Patrick, The wire downstream of the dual diodes is a single point of failure. When it fails, both pumps stop working. The diodes can be eliminated and wire as Roger did. Another option is to install a second dual diode so that any single failure will not shut off both pumps. |
Thanks! I appreciate the input. For what it's worth, I believe that the intent is that the diode array be mounted at the fuel pumps.
| - The Matronics AeroElectric-List Email Forum - | | Use the List Feature Navigator to browse the many List utilities available such as the Email Subscriptions page, Archive Search & Download, 7-Day Browse, Chat, FAQ, Photoshare, and much more:
http://www.matronics.com/Navigator?AeroElectric-List |
|
|
|
Back to top |
|
 |
Patrick Brannan
Joined: 03 Mar 2019 Posts: 8
|
Posted: Sat May 21, 2022 7:42 pm Post subject: Re: two-battery, fuel pump circuit protection |
|
|
Thanks for the input John. Very helpful.
Yes, one ECU can run two coil packs. At least according to Ross.
As far as 2-alternator, 1-battery setups go. I have a PowerSonic LiFePO4 battery that I have load tested at predicted current draws. Just one battery would run the plane at least 2 hours. I'll run out of gas before I run out of electrons with 2 batteries at reasonable charge levels. I'm open to 2 alternators, it just seems like an expensive and unnecessary research project for this application. This is not an IFR all WX cross country machine. With LifePO there is a small possibility that the BMS takes the battery off line completely. The B&C people told me that if the battery dropped off line, the alternator would too. I do know that some alternators can run w/o battery, but not my field of expertise and seemingly not an endeavor worth pursuing for this aircraft.
johnbright wrote: | Please explain battery failure modes and special wiring. |
Are all alternators self-exciting now? Maybe I don't understand something correctly, but what I bel
johnbright wrote: | Note 24: "...In any case, the diode bridge should be located as close as practical to the critical system’s input power connection."
I wonder why that is.
|
We all know why that is:) Having thought about all of the responses I've pretty much moved on from the 2-bus idea to single-bus w/ backup.
johnbright wrote: | I don't understand Zener diode, I suppose you mean Schottky. |
Yes. That was a brain fart. Not building a power supply.
Your load analysis matches my guesses pretty well except that you have a huge amount of equipment that I will not have. Are those measured numbers?
I'm curious, do RV's actually need defrost fans? Seems like there would be ram air somewhere.
| - The Matronics AeroElectric-List Email Forum - | | Use the List Feature Navigator to browse the many List utilities available such as the Email Subscriptions page, Archive Search & Download, 7-Day Browse, Chat, FAQ, Photoshare, and much more:
http://www.matronics.com/Navigator?AeroElectric-List |
|
|
|
Back to top |
|
 |
johnbright
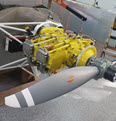
Joined: 14 Dec 2011 Posts: 166 Location: Newport News, VA
|
Posted: Sun May 22, 2022 4:12 pm Post subject: Re: two-battery, fuel pump circuit protection |
|
|
Hi Patrick,
Yea, I figured out one ECU can trigger two coilpacks.
AFAIK if the battery becomes disconnected a B&C wound field alternator will keep running but if you were to turn the alternator off it would not come back on unless you removed all or almost all loads so the residual magnetism in the alternator could get it started, maybe, seems like you can't count on the alternator restarting, especially given your propeller is windmilling so alternator RPM is reduced.
A PM alternator will self start because it does not need field current. The Monkworkz MZ-30L will self start and run well with no battery present and puts out 30 A at 1800 Lycoming RPM. A B&C SD-8 will self start AFAIK but only puts out 8.4 A and that's at 2700 Lycoming RPM, at 1900 RPM it puts out 4.7 A. Ref summary from alternator spec sheets at the top of my "Calculations Measurements and Specs" spreadsheet in my folder 3. https://drive.google.com/drive/folders/1u6GeZo6pmBWsKykLNVQMvu4o1VEVyP4K
I'd say the MX-30L is in the early adopter stage. There will be a July, 2022 Kitplanes Paul Dye article on it ( https://www.kitplanes.com/the-monkworkz-mz-30l-direct-drive-generator/ )and it has a VAF thread at https://vansairforce.net/community/showthread.php?t=206179
You have not said what alternators you are considering for your single alternator dual battery system.
No, I don't know why Note 24 in Aeroelectric Connection says "...In any case, the diode bridge should be located as close as practical to the critical system’s input power connection." In Z101, feeds in and out of the diodes are short and infused.
In my load analysis spreadsheet there's a column that says where I got the current draw info. None of the currents have been measured in situ.
Thinking about engine current requirements vs RPM... I forgot to mention coilpack current... there's some info about that in my spreadsheet "Calculations Measurements and Specs" in my folder 3... at this time starting at row 90. https://drive.google.com/drive/folders/1u6GeZo6pmBWsKykLNVQMvu4o1VEVyP4K
Speaking of the side-by-side RV's I am familiar with, most install defrost fans in the glareshield, PC muffin fans. In addition to defrost function, they also serve to vent warm air generated by panel instruments. Cabin air vents plumbed from the NACA scoops are left and right below the IP.
| - The Matronics AeroElectric-List Email Forum - | | Use the List Feature Navigator to browse the many List utilities available such as the Email Subscriptions page, Archive Search & Download, 7-Day Browse, Chat, FAQ, Photoshare, and much more:
http://www.matronics.com/Navigator?AeroElectric-List |
|
_________________ John Bright, RV-6A, at FWF, O-360
Z-101 single batt dual alt SDS EM-5-F.
john_s_bright@yahoo.com, Newport News, Va
N1921R links
Last edited by johnbright on Thu May 26, 2022 7:38 pm; edited 7 times in total |
|
Back to top |
|
 |
Patrick Brannan
Joined: 03 Mar 2019 Posts: 8
|
Posted: Thu May 26, 2022 7:45 am Post subject: Re: two-battery, fuel pump circuit protection |
|
|
johnbright wrote: |
You have not said what alternators you are considering for your single alternator dual battery system.
No, I don't know why Note 24 in Aeroelectric Connection says "...In any case, the diode bridge should be located as close as practical to the critical system’s input power connection." In Z101, feeds in and out of the diodes are short and infused.
|
I think the diode bridge being located close to the equipment is because the downstream wiring is a single point of failure. It also has two fuses in parallel feeding it. I'm not sure I've thought through all the ramifications of that setup. Maybe I have it wrong.
I have the B&C LX60 with the LR3D-14 controller.
I think it's best that backup battery is isolated from the charging system and main battery in normal operation. Putting an appropriate diode and fuse, SDS recommends 30A, between each battery and the engine bus seems like the best way to keep the backup online and feeding the engine regardless of what happens to the rest of the system. There also needs to be switches and / or relays to isolate the batteries for testing.
Depending on the backup battery used, having a contactor or relay that allows the backup to be charged by the alternator and to provide emergency power to the field and critical equipment might be a good idea. I lean toward having two batteries, each capable of starting the engine. SDS makes a point that you cannot hand prop an engine with the SDS system installed. I'm assuming that means that if the prop stops in air, I will need to use the starter to get it going again. I need to verify this with SDS.
At low altitude I would keep the aux battery contactor (the alternate feed to the main bus not the engine bus) off so that the only thing the backup battery can do is run the engine.
The 20 or 30 amp, self-exciting backup alternator is tempting. But I'm not sure it's justified in this case. I have inverted oil system that picks up oil from the vacuum pump pad. That's all set up already. I know that there is an adapter that can pull oil even if a vacuum pump is installed, but not sure it's worth the effort and do not know how oil flow might be affected. Two batteries, each of which will keep the plane in the air for at least one hour, seems adequate. I just have to make sure that the pilot knows when there is a failure.
Preflight will include checking the charge levels of both batteries.
Regarding your defrost, I've had two "interesting" experiences with canopies frosting over. Once in a sailplane and once in an A-6. It's one of those things you don't think about until it all goes wrong.
| - The Matronics AeroElectric-List Email Forum - | | Use the List Feature Navigator to browse the many List utilities available such as the Email Subscriptions page, Archive Search & Download, 7-Day Browse, Chat, FAQ, Photoshare, and much more:
http://www.matronics.com/Navigator?AeroElectric-List |
|
|
|
Back to top |
|
 |
|
|
You cannot post new topics in this forum You cannot reply to topics in this forum You cannot edit your posts in this forum You cannot delete your posts in this forum You cannot vote in polls in this forum You cannot attach files in this forum You can download files in this forum
|
Powered by phpBB © 2001, 2005 phpBB Group
|