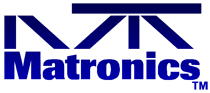 |
Matronics Email Lists Web Forum Interface to the Matronics Email Lists
|
View previous topic :: View next topic |
Author |
Message |
kearney(at)shaw.ca Guest
|
Posted: Fri Nov 17, 2006 8:13 am Post subject: One of the best moves I've made yet |
|
|
Hi
Since starting to build a couple of weeks ago, I have limited my work to things that I felt I could do without too much risk of error. Namely, small fabrication, priming, deburring, drilling, deburring, priming. Did I mention deburring?
My plan all along was to advance enough that I could then hire an experienced builder for some detailed one on one instruction. I have just completed two very full days with this chap and now believe that I am well equipped to proceed on my own (at least for now). In October I did a two day “sheet metal course” that gave me the basics on a couple of small scale “projects – a small airfoil section being one”. It is a bit different when you are looking at a large, very expensive vertical stab skin that you have just spent hours prepping. The decision to get someone to look over my shoulder and to demonstrate [proper technique and what to look for was the best decision I have made so far. Here’s why:
On Wednesday, I started with dimpling 101. Although I had previously dimpled the rudder and vertical stab skins these did not meet the standard set by Ralph (my instructor). He demonstrated how to tell if the dimples were correctly formed and more importantly, how to correct those that weren’t. After redoing the dimpling, we moved on to backrivetting the rudder stiffeners to the skins. At that point we departed from the plans and cut an electric trim access panel into the rudder skin. Here Ralph demonstrated how to cut access panel holes without deforming the skins and getting nice clean edges. If I had tried this on my own, I would be buying a new rudder skin by now! Before starting we also discussed the location of the trim tab and we decided to move it lower on the rudder. We also gave thought to the rivet pattern for the doubler and access plate, Ralph suggesting that we consider the esthetics of matching the existing rivet pattern when placing the doubler and access panel.
Next we tackled the trailing edge of the rudder. Another builder suggested using angle aluminum to hold the trailing edge straight after the edge wedge was glued in. The problem with this was that the edge wedge is a wedge and a cleco will not sit flat on the skin due to the angle through the wedge. To compensate I used (temporarily) the horizontal stab wedge material to provide a completely flat clecoing surface. The cleco went through:
- Extra edge wedge (pointing forward)
- Rudder edge wedge (point aft of course)
- Rudder skin
- Angle aluminum
Every hole was clecoed overnight while the glue set. The next morning I had a perfectly straight rudder skin and edge wedge.
Thursday morning Ralph showed me how to use a carpenter’s angle to check that the rib flange angles were correct. This would ensure that the skins wouldn’t pucker due to the rib flanges being bent to far in/out. We riveted the trim access panel double and also fabricated a cover plate. Here I was shown how to bend the cover plate edges so that the plate would sit flat on the doubler (and the corners wouldn’t turn up).
We then discussed how the trim servo would be mounted and decided we could cut the servo cable into the skin as well given that we sorted out where the trim tab would be and how great it’s range of movement would be. I cut this hole, finished it and trimmed a rudder cable fairing to fit. We riveted it on and then stood back being quite smug with our work!
We completed the rudder back riveting and spliced the two sides together with op rivets. I then started setting the trailing edge rivets with my squeezer. After back riveting the trailing edge, I now have a rudder that is al most complete – a rudder with an arrow straight trailing edge.
Late in the day, we still hadn’t bucked any vertical stab rivets. This was the last bit of “experience” I wanted. We setup and Ralph gave me a step by step instruction on how to rivet these skins and what to be careful of so as not to dent the skins. He spent time on how to hold the bucking bar, how to ensure you are on the rivet and how to rivet very carefully. He also warned me to not use my mushroom set and to get a swivel set. After doing a few rivets, I understand why. Before we called it a day, we completed about half of one side of the stab skin. Perhaps the hardest part for Ralph was watching me rivet the forward center rivets of the skin, perhaps the riskiest of the lot. But they came out fine!
There must have been a hundred different thgings Ralh showed me including how to use my tools correctly and a few oithes to buy. Most importantly, I was able to make a lot of mistakes (not fatal) and was shown how to correct them. Also, I learned a great deal about how to work with aluminium – if nothing else, the rudder trim “extra” was invaluble in this respect.
This may be a bit rambling, but it was a fun couple of days. For any one else who has 0, zero, nadda, zilch, zippo experience like I do (did), this is a great way to build confidence and acquire skills. Unforrttunately spending two weeks a buikld center was impossible and in many respects, I believe that this approach was better. I used my tools, in my work area and I have an umbilicus to an individual who knows me and my project. The cost was also a fraction of the cost of build center.
Cheers
Les Kearney
RV10 # 40643 - Vertical Stab / Rudder in various stages of disrepair
Do not archive
[quote][b]
| - The Matronics RV10-List Email Forum - | | Use the List Feature Navigator to browse the many List utilities available such as the Email Subscriptions page, Archive Search & Download, 7-Day Browse, Chat, FAQ, Photoshare, and much more:
http://www.matronics.com/Navigator?RV10-List |
|
|
|
Back to top |
|
 |
Tim(at)MyRV10.com Guest
|
Posted: Fri Nov 17, 2006 2:43 pm Post subject: One of the best moves I've made yet |
|
|
Les, that sounds like a fantastic way to start off. I had an RV-4
building buddy get me started for 2 or 3 hours, and I helped on his
project for a couple hours too. It's very comforting to work with
someone with good skills and have time to learn. It sounds as if
you had a very skillful guy in Ralph. Now you can use those skills
to have a really good quality outcome on the rest of your project.
Besides that, those hours probably were more fun as well.
Tim Olson - RV-10 N104CD - Flying
do not archive
Les Kearney wrote:
Quote: | Hi
Since starting to build a couple of weeks ago, I have limited my work to
things that I felt I could do without too much risk of error. Namely,
small fabrication, priming, deburring, drilling, deburring, priming. Did
I mention deburring?
My plan all along was to advance enough that I could then hire an
experienced builder for some detailed one on one instruction. I have
just completed two very full days with this chap and now believe that I
am well equipped to proceed on my own (at least for now). In October I
did a two day “sheet metal course” that gave me the basics on a couple
of small scale “projects – a small airfoil section being one”. It is a
bit different when you are looking at a large, very expensive vertical
stab skin that you have just spent hours prepping. The decision to get
someone to look over my shoulder and to demonstrate [proper technique
and what to look for was the best decision I have made so far. Here’s why:
On Wednesday, I started with dimpling 101. Although I had previously
dimpled the rudder and vertical stab skins these did not meet the
standard set by Ralph (my instructor). He demonstrated how to tell if
the dimples were correctly formed and more importantly, how to correct
those that weren’t. After redoing the dimpling, we moved on to
backrivetting the rudder stiffeners to the skins. At that point we
departed from the plans and cut an electric trim access panel into the
rudder skin. Here Ralph demonstrated how to cut access panel holes
without deforming the skins and getting nice clean edges. If I had tried
this on my own, I would be buying a new rudder skin by now! Before
starting we also discussed the location of the trim tab and we decided
to move it lower on the rudder. We also gave thought to the rivet
pattern for the doubler and access plate, Ralph suggesting that we
consider the esthetics of matching the existing rivet pattern when
placing the doubler and access panel.
Next we tackled the trailing edge of the rudder. Another builder
suggested using angle aluminum to hold the trailing edge straight after
the edge wedge was glued in. The problem with this was that the edge
wedge is a wedge and a cleco will not sit flat on the skin due to the
angle through the wedge. To compensate I used (temporarily) the
horizontal stab wedge material to provide a completely flat clecoing
surface. The cleco went through:
* Extra edge wedge (pointing forward)
* Rudder edge wedge (point aft of course)
* Rudder skin
* Angle aluminum
Every hole was clecoed overnight while the glue set. The next morning I
had a perfectly straight rudder skin and edge wedge.
Thursday morning Ralph showed me how to use a carpenter’s angle to check
that the rib flange angles were correct. This would ensure that the
skins wouldn’t pucker due to the rib flanges being bent to far in/out.
We riveted the trim access panel double and also fabricated a cover
plate. Here I was shown how to bend the cover plate edges so that the
plate would sit flat on the doubler (and the corners wouldn’t turn up).
We then discussed how the trim servo would be mounted and decided we
could cut the servo cable into the skin as well given that we sorted out
where the trim tab would be and how great it’s range of movement would
be. I cut this hole, finished it and trimmed a rudder cable fairing to
fit. We riveted it on and then stood back being quite smug with our work!
We completed the rudder back riveting and spliced the two sides together
with op rivets. I then started setting the trailing edge rivets with my
squeezer. After back riveting the trailing edge, I now have a rudder
that is al most complete – a rudder with an arrow straight trailing edge.
Late in the day, we still hadn’t bucked any vertical stab rivets. This
was the last bit of “experience” I wanted. We setup and Ralph gave me a
step by step instruction on how to rivet these skins and what to be
careful of so as not to dent the skins. He spent time on how to hold the
bucking bar, how to ensure you are on the rivet and how to rivet very
carefully. He also warned me to not use my mushroom set and to get a
swivel set. After doing a few rivets, I understand why. Before we called
it a day, we completed about half of one side of the stab skin. Perhaps
the hardest part for Ralph was watching me rivet the forward center
rivets of the skin, perhaps the riskiest of the lot. But they came out fine!
There must have been a hundred different thgings Ralh showed me
including how to use my tools correctly and a few oithes to buy. Most
importantly, I was able to make a lot of mistakes (not fatal) and was
shown how to correct them. Also, I learned a great deal about how to
work with aluminium – if nothing else, the rudder trim “extra” was
invaluble in this respect.
This may be a bit rambling, but it was a fun couple of days. For any one
else who has 0, zero, nadda, zilch, zippo experience like I do (did),
this is a great way to build confidence and acquire skills.
Unforrttunately spending two weeks a buikld center was impossible and
in many respects, I believe that this approach was better. I used my
tools, in my work area and I have an umbilicus to an individual who
knows me and my project. The cost was also a fraction of the cost of
build center.
Cheers
Les Kearney
RV10 # 40643 - Vertical Stab / Rudder in various stages of disrepair
Do not archive
*
*
|
| - The Matronics RV10-List Email Forum - | | Use the List Feature Navigator to browse the many List utilities available such as the Email Subscriptions page, Archive Search & Download, 7-Day Browse, Chat, FAQ, Photoshare, and much more:
http://www.matronics.com/Navigator?RV10-List |
|
|
|
Back to top |
|
 |
|
|
You cannot post new topics in this forum You cannot reply to topics in this forum You cannot edit your posts in this forum You cannot delete your posts in this forum You cannot vote in polls in this forum You cannot attach files in this forum You can download files in this forum
|
Powered by phpBB © 2001, 2005 phpBB Group
|