Ron Lendon
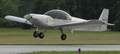
Joined: 10 Jan 2006 Posts: 685 Location: Clinton Twp., MI
|
Posted: Tue May 08, 2007 6:59 pm Post subject: Welding 601XL Fuel Tanks |
|
|
Group,
I am pleased to announce that I have successfully welded and tested for leaks my right fuel tank. The 5mm .032 flange welding was actually very easy once I figured what my problem was, the arc was so small I couldn't see the puddle. What I did was get the strongest reading glasses I could find and found one of the newer Miller Syncrowave welders with Pulse and Balance controls. It just so happens my EAA Tech Consoler has the equipment.
Here are the details:
Bought some 4043 rod in 1/16 and 3/32 diameters. Set the welder up to Pulse at 2.3 and the Balance 5.0, the amperage goes up to 200 but I kept it dialed down for a maxium of 180.
The .032 5mm flanges fuse with only about 27 to 28 amps so a small 1/16 dia 2% thoriated tungsten was used to fuse the metals. First scuff the area to be welded with a stainless wire brush, reserved only for this purpose. The Filler neck flange goes on the inside, tack it first then weld sections making sure to join your welds. If/when you contaminate the tungsten, STOP and clean/grind the tungsten then using the stainless wire brush, scuff the area and start the welding again. Scuff, Tack, Scuff, Weld is the process. The material oxidizes quickly so that is most important.
Next assemble the ends and and tack weld every 3-4 inches, scuff, tack, scuff, tack. Once you have the ends and the long flange tacked together, scuff, weld, scuff weld, scuff, weld. I used very little 1/16 filler rod on the seams, it was just to help get the weld started and touch ups. The 3.25 reading glasses made all the difference, the weld puddle was visible. Just watch the puddle and scuff, weld, scuff weld.
If/when you stop welding always scuff just before striking the next arc.
Just wanted to let you guys know it can be done and it ain't hard if you get the glasses and the right welding equipment.
| - The Matronics Zenith-List Email Forum - | | Use the List Feature Navigator to browse the many List utilities available such as the Email Subscriptions page, Archive Search & Download, 7-Day Browse, Chat, FAQ, Photoshare, and much more:
http://www.matronics.com/Navigator?Zenith-List |
|
Description: |
Same view after scuffing it up with the stainless wire brush. |
|
Filesize: |
132.04 KB |
Viewed: |
268 Time(s) |
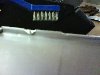
|
Description: |
See the black soot from where I dipped the tungsten into the puddle? |
|
Filesize: |
118.45 KB |
Viewed: |
214 Time(s) |
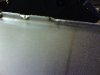
|
_________________ Ron Lendon
WW Corvair with Roy's Garage 5th bearing
CH 601 XLB
N601LT - Flying
http://www.mykitlog.com/rlendon
Corvair Engine Prints:
https://sites.google.com/site/corvairenginedata/ |
|