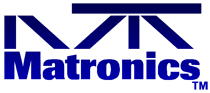 |
Matronics Email Lists Web Forum Interface to the Matronics Email Lists
|
View previous topic :: View next topic |
Author |
Message |
Afterfxllc(at)aol.com Guest
|
Posted: Fri Apr 25, 2008 5:06 pm Post subject: New Project Problems |
|
|
I just started building a new 601XL and last night I fitted the brakes and mounted the axles and tires and that took about 3 hours but then I started the mount the front fork to the main gear tube and looked at how far off the weld is.... I am a bit concerned that the QC is not up to par. You would think they would have a fixture made for this and they would be exact. I have added a link to a couple pics of the off set between the steering rods and the nose wheel fork.
http://www.project601xl.com/New_Plane.html
Jeff
Need a new ride? Check out the largest site for U.S. used car listings at AOL Autos.
[quote][b]
| - The Matronics Zenith-List Email Forum - | | Use the List Feature Navigator to browse the many List utilities available such as the Email Subscriptions page, Archive Search & Download, 7-Day Browse, Chat, FAQ, Photoshare, and much more:
http://www.matronics.com/Navigator?Zenith-List |
|
|
|
Back to top |
|
 |
bobefx(at)yahoo.com Guest
|
Posted: Fri Apr 25, 2008 5:44 pm Post subject: New Project Problems |
|
|
Jeff, My point, Quality Control, it is vary lacking.
'
Bobefx
---
| - The Matronics Zenith-List Email Forum - | | Use the List Feature Navigator to browse the many List utilities available such as the Email Subscriptions page, Archive Search & Download, 7-Day Browse, Chat, FAQ, Photoshare, and much more:
http://www.matronics.com/Navigator?Zenith-List |
|
|
|
Back to top |
|
 |
MHerder
Joined: 11 Feb 2008 Posts: 143 Location: Fort Worth TX
|
Posted: Fri Apr 25, 2008 7:42 pm Post subject: Re: New Project Problems |
|
|
My personal experience is that I have not encountered ANY quality control issues thus far. In fact every time that I have found an issue that I suspected was a QC issue I found that it was not after all. I would consider myself to be pretty picky too. Very picky.
But I will agree that perhaps your front gear is a little twisted. I'd be willing to bet my paycheck that all you would have to do is contact Shirley, send a pic and you will have a new one in a week or less.
| - The Matronics Zenith-List Email Forum - | | Use the List Feature Navigator to browse the many List utilities available such as the Email Subscriptions page, Archive Search & Download, 7-Day Browse, Chat, FAQ, Photoshare, and much more:
http://www.matronics.com/Navigator?Zenith-List |
|
_________________ Zodiac 601 HD
Jabiru 3300
Wood Sensinich 64x47
Finally Flying |
|
Back to top |
|
 |
Afterfxllc(at)aol.com Guest
|
Posted: Fri Apr 25, 2008 8:22 pm Post subject: New Project Problems |
|
|
I'm not upset about it and I know Zenith will make it right and this is my 3rd 601 so been there done that but the point was that this is such a simple welded piece that it should be dead on.
Quote: | My personal experience is that I have not encountered ANY quality control issues thus far. In fact every time that I have found an issue that I suspected was a QC issue I found that it was not after all. I would consider myself to be pretty picky too. Very picky.
But I will agree that perhaps your front gear is a little twisted. I'd be willing to bet my paycheck that all you would have to do is contact Shirley, send a pic and you will have a new one in a week or less. |
do not archive
Need a new ride? Check out the largest site for U.S. used car listings at AOL Autos.
[quote][b]
| - The Matronics Zenith-List Email Forum - | | Use the List Feature Navigator to browse the many List utilities available such as the Email Subscriptions page, Archive Search & Download, 7-Day Browse, Chat, FAQ, Photoshare, and much more:
http://www.matronics.com/Navigator?Zenith-List |
|
|
|
Back to top |
|
 |
craig(at)craigandjean.com Guest
|
Posted: Fri Apr 25, 2008 9:39 pm Post subject: New Project Problems |
|
|
I've had two quality problems with my QBK, both acknowledged by the factory:
- The holes in the upper motor mount brackets did not align with the holes
in the firewall. They were off by 1/8 of an inch. Zenith sent me new,
undrilled motor mount brackets but they were of the new triangular style so
I had to do some rework.
- more seriously all four outer bolt holes in the center spare (two per
side) are 6 to 10 thousandths over. Because the other holes in the center
spar are within spec (and ALL the holes in the wing spare) is seem very
likely that the problem holes were enlarged when the holes in the spar
uprights (6B13-1) were line-drilled. The factory doesn't have a good fix for
this one. Roger quotes CH as saying that 12 thou is within spec but I don't
buy it. The plans called for all these holes to be precision reamed. Note
that because the corresponding holes in the wing spars are NOT oversized I
can't just use a larger bolt even if I could find one.
The only fix I can think of is to remove the center spar from the fuselage,
bolt it to each wing in turn and drill/ream the holes to 3/8ths. I don't
think it is feasible to do this with the center spar in the fuselage. But
another QBK builder is investigating that solution. Luckily I have had a lot
of practice drilling out rivets.
In a few years it will be interesting to look at quality issues (if any)
with Van's RV-12 and Ran's S-19.
BTW: the bottom plate on my front gear tube was square but shifted to one
side by a little under 1/8th of an inch.
-- Craig
--
| - The Matronics Zenith-List Email Forum - | | Use the List Feature Navigator to browse the many List utilities available such as the Email Subscriptions page, Archive Search & Download, 7-Day Browse, Chat, FAQ, Photoshare, and much more:
http://www.matronics.com/Navigator?Zenith-List |
|
|
|
Back to top |
|
 |
ashontz

Joined: 27 Dec 2006 Posts: 723
|
Posted: Sat Apr 26, 2008 3:37 am Post subject: Re: New Project Problems |
|
|
I don't think I'd open the holes to 3/8. The spar caps (the 1/4 x 1.5inch bar) is already pretty close to minimum edge distance, even with the 5/16 bolts.
When I drilled my center spar to spar clamped everything together and first went in with a small hole and an alignment bolt, then another alignment bolt, then another small alignment bolt etc... then started opening up each hole and reaming. Took a few hours, but all the reamed holes line up nicely.
do not archive
craig(at)craigandjean.com wrote: | I've had two quality problems with my QBK, both acknowledged by the factory:
- The holes in the upper motor mount brackets did not align with the holes
in the firewall. They were off by 1/8 of an inch. Zenith sent me new,
undrilled motor mount brackets but they were of the new triangular style so
I had to do some rework.
- more seriously all four outer bolt holes in the center spare (two per
side) are 6 to 10 thousandths over. Because the other holes in the center
spar are within spec (and ALL the holes in the wing spare) is seem very
likely that the problem holes were enlarged when the holes in the spar
uprights (6B13-1) were line-drilled. The factory doesn't have a good fix for
this one. Roger quotes CH as saying that 12 thou is within spec but I don't
buy it. The plans called for all these holes to be precision reamed. Note
that because the corresponding holes in the wing spars are NOT oversized I
can't just use a larger bolt even if I could find one.
The only fix I can think of is to remove the center spar from the fuselage,
bolt it to each wing in turn and drill/ream the holes to 3/8ths. I don't
think it is feasible to do this with the center spar in the fuselage. But
another QBK builder is investigating that solution. Luckily I have had a lot
of practice drilling out rivets.
In a few years it will be interesting to look at quality issues (if any)
with Van's RV-12 and Ran's S-19.
BTW: the bottom plate on my front gear tube was square but shifted to one
side by a little under 1/8th of an inch.
-- Craig
-- |
| - The Matronics Zenith-List Email Forum - | | Use the List Feature Navigator to browse the many List utilities available such as the Email Subscriptions page, Archive Search & Download, 7-Day Browse, Chat, FAQ, Photoshare, and much more:
http://www.matronics.com/Navigator?Zenith-List |
|
|
|
Back to top |
|
 |
craig(at)craigandjean.com Guest
|
Posted: Sat Apr 26, 2008 9:39 am Post subject: New Project Problems |
|
|
Unlike rivets there is no hard and fast edge-distance for a bolt. The
factory has agreed that in principal that the hole can be upsized.
Going from 5/16th to 3/8th is an increase of 1/16th. The edges of the hole
will move half that or 1/32nd which is 31.25 thou. I'm comfortable with
loosing that much metal. Note that I would only have to do this to 4 of the
12 holes.
-- Craig
--
| - The Matronics Zenith-List Email Forum - | | Use the List Feature Navigator to browse the many List utilities available such as the Email Subscriptions page, Archive Search & Download, 7-Day Browse, Chat, FAQ, Photoshare, and much more:
http://www.matronics.com/Navigator?Zenith-List |
|
|
|
Back to top |
|
 |
Afterfxllc(at)aol.com Guest
|
Posted: Sat Apr 26, 2008 10:55 am Post subject: New Project Problems |
|
|
Zenith told me that it isn't as much the bolt hole tolerance that is critical but the clamping pressure of the bolt that is more important just like the prop. I haven't had any problems with the spars on 3 kits but will check my spars and center section before I install it in the plane. I also fixed the front gear problem by shifting the fork about 1/8 inch it doesn't look all the professional but the wheel pant will cover it.
Jeff
www.aeroliteproducts.com
www.project601xl.com
Unlike rivets there is no hard and fast edge-distance for a bolt. The
factory has agreed that in principal that the hole can be upsized.
Going from 5/16th to 3/8th is an increase of 1/16th. The edges of the hole
will move half that or 1/32nd which is 31.25 thou. I'm comfortable with
loosing that much metal. Note that I would only have to do this to 4 of the
12 holes.
-- Craig
-----Original Message-----
From: owner-zenith-list-server(at)matronics.com
[mailto:owner-zenith-list-server(at)matronics.com] On Behalf Of ashontz
Sent: Saturday, April 26, 2008 5:37 AM
To: zenith-list(at)matronics.com
Subject: Re: New Project Problems
--> Zenith-List message posted by: "ashontz" <ashontz(at)nbme.org>
I don't think I'd open the holes to 3/8. The spar caps (the 1/4 x 1.5inch
bar) is already pretty close to minimum edge distance, even with the 5/16
bolts.
When I drilled my center spar to spar clamped everything together and first
went in with a small hole and an alignment bolt, then another alignment
bolt, then another small alignment bolt etc... then started opening up each
hole and reaming. Took a few hours, but all the reamed holes line up nicely.
do not archive
craig(at)craigandjean.com wrote:
Quote: | I've had two quality problems with my QBK, both acknowledged by the
factory:
|
Quote: |
- The holes in the upper motor mount brackets did not align with the holes
in the firewall. They were off by 1/8 of an inch. Zenith sent me new,
undrilled motor mount brackets but they were of the new triangular style
so
|
Quote: | I had to do some rework.
- more seriously all four outer bolt holes in the center spare (two per
side) are 6 to 10 thousandths over. Because the other holes in the center
spar are within spec (and ALL the holes in the wing spare) is seem very
likely that the problem holes were enlarged when the holes in the spar
uprights (6B13-1) were line-drilled. The factory doesn't have a good fix
for
|
Quote: | this one. Roger quotes CH as saying that 12 thou is within spec but I
don't
|
Quote: | buy it. The plans called for all these holes to be precision reamed. Note
that because the corresponding holes in the wing spars are NOT oversized I
can't just use a larger bolt even if I could find one.
The only fix I can think of is to remove the center spar from the
fuselage,
|
Quote: | bolt it to each wing in turn and drill/ream the holes to 3/8ths. I don't
think it is feasible to do this with the center spar in the fuselage. But
another QBK builder is investigating that solution. Luckily I have had a
lot
|
Quote: | of practice drilling out rivets.
In a few years it will be interesting to look at quality issues (if any)
with Van's RV-12 and Ran's S-19.
BTW: the bottom plate on my front gear tube was square but shifted to one
side by a little under 1/8th of an inch.
-- Craig
--
|
--------
Andy Shontz
CH601XL - Corvair
www.mykitlog.com/ashontz
Need a new ride? Check out the largest site for U.S. used car listings at AOL Autos.
[quote][b]
| - The Matronics Zenith-List Email Forum - | | Use the List Feature Navigator to browse the many List utilities available such as the Email Subscriptions page, Archive Search & Download, 7-Day Browse, Chat, FAQ, Photoshare, and much more:
http://www.matronics.com/Navigator?Zenith-List |
|
|
|
Back to top |
|
 |
craig(at)craigandjean.com Guest
|
Posted: Sat Apr 26, 2008 11:27 am Post subject: New Project Problems |
|
|
Quote: | Zenith told me that it isn't as much the bolt hole tolerance that is critical but the clamping pressure of the bolt that is more important just like the prop.
|
They told me the same thing. But it is at odds with the requirement that the holes be precision reamed. On an RV-7 the equivalent holes are burnished. I’ve attached a close-up of a shot of Lance Gingell’s RV-7a spar. He is making great progress: http://lancegingell.blogspot.com/
BTW: the only way I have found to get an accurate measurement on the hole sizes is to use plug gauges. I bought a set from Grizzly but Zenith has been loaning a handful of gauges near the correct size to other builders to check theirs.
-- Craig
| - The Matronics Zenith-List Email Forum - | | Use the List Feature Navigator to browse the many List utilities available such as the Email Subscriptions page, Archive Search & Download, 7-Day Browse, Chat, FAQ, Photoshare, and much more:
http://www.matronics.com/Navigator?Zenith-List |
|
Description: |
|
Filesize: |
99.27 KB |
Viewed: |
465 Time(s) |

|
|
|
Back to top |
|
 |
n801bh(at)netzero.com Guest
|
Posted: Sat Apr 26, 2008 4:34 pm Post subject: New Project Problems |
|
|
The forces acting on that joint are in shear, not tension. A reamed hole is critical. Period!!!!
do not archive
Quote: | Zenith told me that it isn't as much the bolt hole tolerance that is critical but the clamping pressure of the bolt that is more important just like the prop.<?xml:namespace prefix = o ns = "urn:schemas-microsoft-com:office:office" />
|
They told me the same thing. But it is at odds with the requirement that the holes be precision reamed. On an RV-7 the equivalent holes are burnished. I’ve attached a close-up of a shot of Lance Gingell’s RV-7a spar. He is making great progress: http://lancegingell.blogspot.com/
BTW: the only way I have found to get an accurate measurement on the hole sizes is to use plug gauges. I bought a set from Grizzly but Zenith has been loaning a handful of gauges near the correct size to other builders to check theirs.
-- Craig
_____________________________________________________________
Prepare for the unexpected. Click now to prepare a living trust.
[quote][b]
| - The Matronics Zenith-List Email Forum - | | Use the List Feature Navigator to browse the many List utilities available such as the Email Subscriptions page, Archive Search & Download, 7-Day Browse, Chat, FAQ, Photoshare, and much more:
http://www.matronics.com/Navigator?Zenith-List |
|
|
|
Back to top |
|
 |
rsteele(at)rjsit.com Guest
|
Posted: Sat Apr 26, 2008 6:21 pm Post subject: New Project Problems |
|
|
Coming from a structures background, this seems completely backward, so I googled a bit and found that for aerospace applications, bolted connections are usually designed with bolts in shear - a no-no for structures. I'm a curious as to why. All the web pages I found that might talk about this require a membership. Could you educate the group a bit on why aerospace connections rely on shear rather than clamping pressure, the norm for most applications?
do not archive
Ron
On Apr 27, 2008, at 12:28 AM, n801bh(at)netzero.com (n801bh(at)netzero.com) wrote:
[quote]
The forces acting on that joint are in shear, not tension. A reamed hole is critical. Period!!!!
do not archive
Quote: | Zenith told me that it isn't as much the bolt hole tolerance that is critical but the clamping pressure of the bolt that is more important just like the prop.
|
They told me the same thing. But it is at odds with the requirement that the holes be precision reamed. On an RV-7 the equivalent holes are burnished. I’ve attached a close-up of a shot of Lance Gingell’s RV-7a spar. He is making great progress: http://lancegingell.blogspot.com/
BTW: the only way I have found to get an accurate measurement on the hole sizes is to use plug gauges. I bought a set from Grizzly but Zenith has been loaning a handful of gauges near the correct size to other builders to check theirs.
-- Craig
_____________________________________________________________
Prepare for the unexpected. Click now to prepare a living trust.
Quote: |
href="http://www.matronics.com/Navigator?Zenith-List">http://www.matronics.com/Navigator?Zenith-List
href="http://forums.matronics.com">http://forums.matronics.com
href="http://www.matronics.com/contribution">http://www.matronics.com/contribution
| [b]
| - The Matronics Zenith-List Email Forum - | | Use the List Feature Navigator to browse the many List utilities available such as the Email Subscriptions page, Archive Search & Download, 7-Day Browse, Chat, FAQ, Photoshare, and much more:
http://www.matronics.com/Navigator?Zenith-List |
|
|
|
Back to top |
|
 |
ashontz

Joined: 27 Dec 2006 Posts: 723
|
Posted: Sun Apr 27, 2008 3:38 am Post subject: Re: New Project Problems |
|
|
I wholely agree. The torque value/clamp force, has been dicussed here before. I still think under enough cycles, that spr will move a bit if not reamed. Movement leads to fatigue, leads to failure.
The plans call for reaming, yet they say it's not critical. Doesn't mkae sense, particularly for that joint. Reaming is the way to go.
[quote="n801bh(at)netzero.com"]The forces acting on that joint are in shear, not tension. A reamed hole is critical. Period!!!!
do not archive
Quote: | Zenith told me that it isn't as much the bolt hole tolerance that is critical but the clamping pressure of the bolt that is more important just like the prop.<xml>
|
They told me the same thing. But it is at odds with the requirement that the holes be precision reamed. On an RV-7 the equivalent holes are burnished. I?ve attached a close-up of a shot of Lance Gingell?s RV-7a spar. He is making great progress: http://lancegingell.blogspot.com/
BTW: the only way I have found to get an accurate measurement on the hole sizes is to use plug gauges. I bought a set from Grizzly but Zenith has been loaning a handful of gauges near the correct size to other builders to check theirs.
-- Craig
_____________________________________________________________
Prepare for the unexpected. Click now to prepare a living trust.
| - The Matronics Zenith-List Email Forum - | | Use the List Feature Navigator to browse the many List utilities available such as the Email Subscriptions page, Archive Search & Download, 7-Day Browse, Chat, FAQ, Photoshare, and much more:
http://www.matronics.com/Navigator?Zenith-List |
|
|
|
Back to top |
|
 |
planecrazydld(at)yahoo.co Guest
|
Posted: Sun Apr 27, 2008 3:41 am Post subject: New Project Problems |
|
|
Hi Ron;
I am not the originator of the message but the shear values are simply the minimum load transfer condition - and even then they only apply when the joint is burr free and sheared up. Face to face friction due to clamping is a major transfer component.
Usually, in certificated aircraft, when you see an ultimate failure, you usually see rows of rivets popped intermingled with sheet failure in and out of those rows of holes. The butts or heads of those rivets are many times still present on one side of the other.
Design of a riveted joint involves knowing the bearing strength of the component(s) to be joined and the shear and tension capabilities of the fastener. The pattern and fastyener diameter is selected to give as nearly even a failure mode split between fastener shear and sheet bearing. Since our fasteners depend to a very great deal on the work hardening of the fastener during setting, the hole size and quality are VERY important - and not many people care about that anymore (or proper deburring) ...takes too long, is not critical, not building SSTs, etc.
Ronald Steele <rsteele(at)rjsit.com> wrote:[quote] Coming from a structures background, this seems completely backward, so I googled a bit and found that for aerospace applications, bolted connections are usually designed with bolts in shear - a no-no for structures. I'm a curious as to why. All the web pages I found that might talk about this require a membership. Could you educate the group a bit on why aerospace connections rely on shear rather than clamping pressure, the norm for most applications?
do not archive
Ron
On Apr 27, 2008, at 12:28 AM, n801bh(at)netzero.com (n801bh(at)netzero.com) wrote:
[quote]The forces acting on that joint are in shear, not tension. A reamed hole is critical. Period!!!!
do not archive
> Zenith told me that it isn't as much the bolt hole tolerance that is critical but the clamping pressure of the bolt that is more important just like the prop.
They told me the same thing. But it is at odds with the requirement that the holes be precision reamed. On an RV-7 the equivalent holes are burnished. I’ve attached a close-up of a shot of Lance Gingell’s RV-7a spar. He is making great progress: http://lancegingell.blogspot.com/
BTW: the only way I have found to get an accurate measurement on the hole sizes is to use plug gauges. I bought a set from Grizzly but Zenith has been loaning a handful of gauges near the correct size to other builders to check theirs.
-- Craig
_____________________________________________________________
Prepare for the unexpected. Click now to prepare a living trust.
[quote]
href="http://www.matronics.com/Navigator?Zenith-List">http://www.matronics.com/Navigator?Zenith-List
href="http://forums.matronics.com">http://forums.matronics.com
href="http://www.matronics.com/contribution">http://www.matronics.com/contribution
Be a better friend, newshound, and [quote][b]
| - The Matronics Zenith-List Email Forum - | | Use the List Feature Navigator to browse the many List utilities available such as the Email Subscriptions page, Archive Search & Download, 7-Day Browse, Chat, FAQ, Photoshare, and much more:
http://www.matronics.com/Navigator?Zenith-List |
|
|
|
Back to top |
|
 |
psm(at)att.net Guest
|
Posted: Wed Apr 30, 2008 4:35 am Post subject: New Project Problems |
|
|
Hi Ron,
Just a guess on my part . . .
With aviation, the overwhelming characteristic of any design feature
is how much it weighs. A kit designer wrote in his newsletter a few
decades ago - "If you are considering adding something to my design,
throw it up in the air. If it comes back down it is too heavy."
This may explain why aircraft bolts are some three times as strong as
normal hardware store bolts and stronger than automotive bolts. They
cost more to make because of the alloys and machining difficulty, but
they weigh less for similar performance.
When a bolt is used in shear mode, the strength comes primarily from
the strength of the bolt rather than how well it is installed. So
long as it stays put, it does the job. That makes this a somewhat
more reliable connection than one that can be vibrated loose and fail
more easily. Indeed, you normally install aircraft bolts with the
threads facing downward. That means that even if the nut comes off
the bolt still does its job in shear strength.
Airplanes must be light and highly reliable. So my guess is the
reason for use of aircraft bolts in the common practice of shear mode
is done that way because it results in lighter and more reliable structures.
Paul
XL fuselage
do not archive
At 07:18 PM 4/26/2008, you wrote:
Quote: | Coming from a structures background, this seems completely backward,
so I googled a bit and found that for aerospace applications, bolted
connections are usually designed with bolts in shear - a no-no for
structures. I'm a curious as to why. All the web pages I found
that might talk about this require a membership. Could you educate
the group a bit on why aerospace connections rely on shear rather
than clamping pressure, the norm for most applications?
do not archive
Ron
|
| - The Matronics Zenith-List Email Forum - | | Use the List Feature Navigator to browse the many List utilities available such as the Email Subscriptions page, Archive Search & Download, 7-Day Browse, Chat, FAQ, Photoshare, and much more:
http://www.matronics.com/Navigator?Zenith-List |
|
|
|
Back to top |
|
 |
|
|
You cannot post new topics in this forum You cannot reply to topics in this forum You cannot edit your posts in this forum You cannot delete your posts in this forum You cannot vote in polls in this forum You cannot attach files in this forum You can download files in this forum
|
Powered by phpBB © 2001, 2005 phpBB Group
|