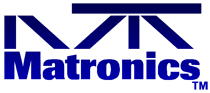 |
Matronics Email Lists Web Forum Interface to the Matronics Email Lists
|
View previous topic :: View next topic |
Author |
Message |
amyvega2005(at)earthlink. Guest
|
Posted: Tue Jun 10, 2008 4:00 pm Post subject: question for Juan( Good article pertaining to LOP) |
|
|
Student pilots and renters rarely worry much about the red knob or lever that controls the fuel/air mixture to their engines; owners worry about it a lot. For a while, there has been a big controversy about how far to lean engines: as the fuel/air mixture gets leaner (more air/less fuel), each cylinder’s exhaust gas temperature (EGT) gets higher and higher; then, if you keep leaning, the EGT drops again. The hottest possible exhaust temperature is called peak EGT. If you lean the mixture at peak EGT (i.e. reduce the fuel flow), the EGT drops and you are running lean of peak, or just LOP; if you enrich the mixture at peak EGT (i.e. increase the fuel flow), the EGT also drops and you are running rich of peak, or ROP. Which is better?
The LOP vs. ROP debate was pretty ferocious for a few years, but the LOP pilots seem to be gaining ground — after all, isn’t it better to cool your engine by burning more (free) air and less fuel, than by burning more fuel and less air? Besides, extra, unburned air doesn’t gunk up the engine, while extra, unburned fuel leaves all kinds of nasty stuff behind, as well as producing a significant amount of carbon monoxide (a big threat to winter fliers like me). Aside from the cost of fuel and the risk of CO poisoning, however, there’s also the question of engine health; after all, an early overhaul will cost a lot more than a bit of extra fuel.
Running Hot and Cold
The previous paragraph already mentioned gunk from flying ROP — for example, lead deposits that foul spark plugs — but the biggest threat to an engine is heat, not in the exhaust gas but in the cylinder itself. Many planes, including my Warrior, do not have a gauge installed for measuring cylinder head temperature (CHT), and most of those that do have a probe in only one of the four or six cylinders. The opponents of LOP (including some less-than-educated mechanics) used to claim that flying LOP increased cylinder temperatures and thus shortened cylinder life. In fact, it turns out that peak CHT — the hottest possible temperature inside the cylinder — actually occurs during ROP flight, specifically when the exhaust temperature has fallen about 25-50 degF on the rich side of peak EGT. In other words, if you lean your engine to peak EGT and then enrich slightly, you will be closer to peak CHT (and to damaging your engine); if you lean your engine to peak EGT and then lean a little further, you will be further from peak CHT. The chart that demonstrates this should be present in any engine operator’s manual (I’m using the one on page 3-13 of the Lycoming Operator’s manual for the O-320 and IO-320 series), but John Deakin also has one online here that shows the same thing (after you stare at it for 45 minutes or so; the best source of information on LOP operations, by the way, is John Deakin’s columns on AvWeb — see engine-related columns in the sidebar).
Bad Vibrations
So why not always fly LOP? One problem is that some engines just cannot do it. The fuel/air distribution to the cylinders is not always even, so one cylinder might be running much richer than another; by the time you lean far enough to get the richest cylinder LOP, the leanest cylinder might no longer have enough fuel to ignite at all, and the engine will start vibrating violently. Carbureted engines mix the fuel and air together in a single place (the carburetor) then send the mixture to all of the cylinders, where it arrives in various states (sometimes more air will get through, and sometimes more fuel). Fuel-injected engines actually mix the fuel and air separately for each cylinder, so it should be possible to adjust them so that all cylinders get exactly the same mixture.
In fact, the original factory injectors almost never work that well, but GAMI makes third-party injectors that do a much better job; not surprisingly, the company and its founder, George Braly, are strong advocates of flying LOP. Lycoming, one of the two major engine manufacturers, has just as strongly opposed LOP, using articles like this one. Essentially, Lycoming’s argument is that with a constant-speed propeller pilots have no way to read their power setting directly, so if they lean the mixture and increase manifold pressure to compensate for the lost power, they might end up flying lean at a dangerously high power setting. That argument does not apply to engines with fixed-pitch propellers, like the one on my Warrior, because there the power setting corresponds directly to the RPM at any given density altitude (or, in plain English, it’s no harder to figure out the power setting LOP than ROP). Even with a constant-speed propeller, the same horsepower should produce the same indicated airspeed no matter where the mixture is set, so it’s not that hard to manage the power setting.
Wide-Open Throttle!
The most fanatical faction of the LOP group — and the one to which I belong — is the group that flies lean of peak/wide-open throttle (LOP/WOT). Using this technique, you do not touch the throttle at all until you’re descending for landing; instead, you leave the throttle wide open the way it was for takeoff, and then you use the mixture (red button or lever) exclusively to control power, going leaner to reduce power, or richer to increase it. That way, you’re always flying the leanest possible for any given power setting (you cannot open the throttle any further to get more air), so there’s no hard brain-work involved. Of course, you need an engine that runs well LOP to pull this off, either a fuel-injected engine with GAMIjectors or a four-cylinder carbureted engine with good distribution like the O-320 (a six-cylinder carbureted engine is unlikely to work, because it’s impossible for all six cylinders to be the same distance from the carburetor). The fuel savings can be spectacular: I burn about 20% less fuel in my Warrior flying just as fast, and I have cleaner plugs and minimal risk of CO poisoning if the muffler ever leaks into my cabin heater. In fact, I am especially fortunate, because in the early 1980’s, Piper’s Warrior II POH actually recommended LOP/WOT far ahead of its time:
For Best Economy cruise, a simplified leaning procedure which consistently allows accurate achievement of best engine efficiency has been developed. Best Economy Cruise performance is obtained with the throttle fully open. To obtain a desired cruise power setting, set the throttle and mixture control full forward, taking care not to exceed the engine speed limitation, then begin leaning the mixture. The RPM will increase slightly but will then begin to decrease. Continue leaning until the desired cruise engine RPM is reached. This will provide best fuel economy and maximum miles per gallon for a given power setting. See following CAUTION when using this procedure.
CAUTION
Prolonged engine operation at powers above 75% with a leaned mixture can result in engine damage. While establishing Best Economy Cruise Mixture, below 6,000 feet, care must be taken not to remain in the range above 75% power more than 15 seconds while leaning. Above 6,000 feet the engine is incapable of generating more than 75%.
For my Warrior’s 160 hp O-320-D3G Lycoming engine, it seems to be RPM rather than power setting that determines things: my engine will almost always run smoothly LOP/WOT at 2500 RPM or above, and will sometimes let me get down to 2400 RPM. Obviously, then, I do better at higher density altitudes, where these RPMs give me safe power settings
--
| - The Matronics Zenith-List Email Forum - | | Use the List Feature Navigator to browse the many List utilities available such as the Email Subscriptions page, Archive Search & Download, 7-Day Browse, Chat, FAQ, Photoshare, and much more:
http://www.matronics.com/Navigator?Zenith-List |
|
|
|
Back to top |
|
 |
amyvega2005(at)earthlink. Guest
|
Posted: Tue Jun 10, 2008 4:00 pm Post subject: question for Juan( Good article pertaining to LOP) |
|
|
Student pilots and renters rarely worry much about the red knob or lever that controls the fuel/air mixture to their engines; owners worry about it a lot. For a while, there has been a big controversy about how far to lean engines: as the fuel/air mixture gets leaner (more air/less fuel), each cylinder’s exhaust gas temperature (EGT) gets higher and higher; then, if you keep leaning, the EGT drops again. The hottest possible exhaust temperature is called peak EGT. If you lean the mixture at peak EGT (i.e. reduce the fuel flow), the EGT drops and you are running lean of peak, or just LOP; if you enrich the mixture at peak EGT (i.e. increase the fuel flow), the EGT also drops and you are running rich of peak, or ROP. Which is better?
The LOP vs. ROP debate was pretty ferocious for a few years, but the LOP pilots seem to be gaining ground — after all, isn’t it better to cool your engine by burning more (free) air and less fuel, than by burning more fuel and less air? Besides, extra, unburned air doesn’t gunk up the engine, while extra, unburned fuel leaves all kinds of nasty stuff behind, as well as producing a significant amount of carbon monoxide (a big threat to winter fliers like me). Aside from the cost of fuel and the risk of CO poisoning, however, there’s also the question of engine health; after all, an early overhaul will cost a lot more than a bit of extra fuel.
Running Hot and Cold
The previous paragraph already mentioned gunk from flying ROP — for example, lead deposits that foul spark plugs — but the biggest threat to an engine is heat, not in the exhaust gas but in the cylinder itself. Many planes, including my Warrior, do not have a gauge installed for measuring cylinder head temperature (CHT), and most of those that do have a probe in only one of the four or six cylinders. The opponents of LOP (including some less-than-educated mechanics) used to claim that flying LOP increased cylinder temperatures and thus shortened cylinder life. In fact, it turns out that peak CHT — the hottest possible temperature inside the cylinder — actually occurs during ROP flight, specifically when the exhaust temperature has fallen about 25-50 degF on the rich side of peak EGT. In other words, if you lean your engine to peak EGT and then enrich slightly, you will be closer to peak CHT (and to damaging your engine); if you lean your engine to peak EGT and then lean a little further, you will be further from peak CHT. The chart that demonstrates this should be present in any engine operator’s manual (I’m using the one on page 3-13 of the Lycoming Operator’s manual for the O-320 and IO-320 series), but John Deakin also has one online here that shows the same thing (after you stare at it for 45 minutes or so; the best source of information on LOP operations, by the way, is John Deakin’s columns on AvWeb — see engine-related columns in the sidebar).
Bad Vibrations
So why not always fly LOP? One problem is that some engines just cannot do it. The fuel/air distribution to the cylinders is not always even, so one cylinder might be running much richer than another; by the time you lean far enough to get the richest cylinder LOP, the leanest cylinder might no longer have enough fuel to ignite at all, and the engine will start vibrating violently. Carbureted engines mix the fuel and air together in a single place (the carburetor) then send the mixture to all of the cylinders, where it arrives in various states (sometimes more air will get through, and sometimes more fuel). Fuel-injected engines actually mix the fuel and air separately for each cylinder, so it should be possible to adjust them so that all cylinders get exactly the same mixture.
In fact, the original factory injectors almost never work that well, but GAMI makes third-party injectors that do a much better job; not surprisingly, the company and its founder, George Braly, are strong advocates of flying LOP. Lycoming, one of the two major engine manufacturers, has just as strongly opposed LOP, using articles like this one. Essentially, Lycoming’s argument is that with a constant-speed propeller pilots have no way to read their power setting directly, so if they lean the mixture and increase manifold pressure to compensate for the lost power, they might end up flying lean at a dangerously high power setting. That argument does not apply to engines with fixed-pitch propellers, like the one on my Warrior, because there the power setting corresponds directly to the RPM at any given density altitude (or, in plain English, it’s no harder to figure out the power setting LOP than ROP). Even with a constant-speed propeller, the same horsepower should produce the same indicated airspeed no matter where the mixture is set, so it’s not that hard to manage the power setting.
Wide-Open Throttle!
The most fanatical faction of the LOP group — and the one to which I belong — is the group that flies lean of peak/wide-open throttle (LOP/WOT). Using this technique, you do not touch the throttle at all until you’re descending for landing; instead, you leave the throttle wide open the way it was for takeoff, and then you use the mixture (red button or lever) exclusively to control power, going leaner to reduce power, or richer to increase it. That way, you’re always flying the leanest possible for any given power setting (you cannot open the throttle any further to get more air), so there’s no hard brain-work involved. Of course, you need an engine that runs well LOP to pull this off, either a fuel-injected engine with GAMIjectors or a four-cylinder carbureted engine with good distribution like the O-320 (a six-cylinder carbureted engine is unlikely to work, because it’s impossible for all six cylinders to be the same distance from the carburetor). The fuel savings can be spectacular: I burn about 20% less fuel in my Warrior flying just as fast, and I have cleaner plugs and minimal risk of CO poisoning if the muffler ever leaks into my cabin heater. In fact, I am especially fortunate, because in the early 1980’s, Piper’s Warrior II POH actually recommended LOP/WOT far ahead of its time:
For Best Economy cruise, a simplified leaning procedure which consistently allows accurate achievement of best engine efficiency has been developed. Best Economy Cruise performance is obtained with the throttle fully open. To obtain a desired cruise power setting, set the throttle and mixture control full forward, taking care not to exceed the engine speed limitation, then begin leaning the mixture. The RPM will increase slightly but will then begin to decrease. Continue leaning until the desired cruise engine RPM is reached. This will provide best fuel economy and maximum miles per gallon for a given power setting. See following CAUTION when using this procedure.
CAUTION
Prolonged engine operation at powers above 75% with a leaned mixture can result in engine damage. While establishing Best Economy Cruise Mixture, below 6,000 feet, care must be taken not to remain in the range above 75% power more than 15 seconds while leaning. Above 6,000 feet the engine is incapable of generating more than 75%.
For my Warrior’s 160 hp O-320-D3G Lycoming engine, it seems to be RPM rather than power setting that determines things: my engine will almost always run smoothly LOP/WOT at 2500 RPM or above, and will sometimes let me get down to 2400 RPM. Obviously, then, I do better at higher density altitudes, where these RPMs give me safe power settings
--
| - The Matronics Zenith-List Email Forum - | | Use the List Feature Navigator to browse the many List utilities available such as the Email Subscriptions page, Archive Search & Download, 7-Day Browse, Chat, FAQ, Photoshare, and much more:
http://www.matronics.com/Navigator?Zenith-List |
|
|
|
Back to top |
|
 |
|
|
You cannot post new topics in this forum You cannot reply to topics in this forum You cannot edit your posts in this forum You cannot delete your posts in this forum You cannot vote in polls in this forum You cannot attach files in this forum You can download files in this forum
|
Powered by phpBB © 2001, 2005 phpBB Group
|