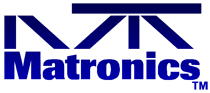 |
Matronics Email Lists Web Forum Interface to the Matronics Email Lists
|
View previous topic :: View next topic |
Author |
Message |
bobf(at)feldtman.com Guest
|
Posted: Thu Jun 19, 2008 7:57 am Post subject: Alternator Warranty Data Point - Rebuilt vs. New |
|
|
Bob - you bring up an interesting point - what is the best way (from an aicraft electrical standpoint) to "wash" an engine. Different A&Ps recommend different soaps, detergents, ways etc. I once lost a GM alternator on a truck when it was "Steam cleaned" - and the alternator did go out at an inopportune time. Obviously don't squirt anything into the alternator, but what about for all the other wires etc? I've never seen that addressed on the forum as to the best and safest way to clean up under the cowl!
thanks
bobf
125GS LOM powered Glastar
On 6/19/08, Robert L. Nuckolls, III <nuckolls.bob(at)cox.net (nuckolls.bob(at)cox.net)> wrote: [quote]--> AeroElectric-List message posted by: "Robert L. Nuckolls, III" <nuckolls.bob(at)cox.net (nuckolls.bob(at)cox.net)>
At 10:07 PM 6/18/2008 -0500, you wrote:
Quote: | Just a data point I thought might be interesting. I recently had the opportunity to review warranty rates on several of the major rotating electrical rebuilders for alternator warranty returns through autopart stores. Low number was 9.6% and high was 18%. This includes wholesale as well as retail sales with no data as to specific cause. The manufacturers all report "true" warranty rates at 5%- 8% on product tested after it was returned. Warranty on New Alternators was running 5.6% so they were substantially better. No numbers on the "true" rates for New product but I would think it about 3%. These numbers are very much in line with historical rates we saw several years ago. Also should note that warranty rates do vary considerably by specific application and these numbers apply to the category and not a particular unit.
It is interesting that while the technology involved in the rebuilding and testing processes has improved over the past few years, the actual return rates have not reflected the benefits of better processes. ( I attribute that to "trial and error" troubleshooting on the retail side.)
I would interpret this to say that if you are using an automotive alternator, the odds of a failure in the first few hours of operation are about double for rebuilt versus new and 1 bad rebuilt unit out of every 10-15 should be a normal expectation. For our purposes,&.. buy new if you can.
It would be very interesting to know what the return rate and actual failure rate is on B&C units after they have done all the extra tuning, balancing, etc. Maybe Bob could get that number for comparison?
|
I don't know that B&C keeps detailed records on such things
and I'm not personally cognizant of their field experience
over the last 6-8 years. But while I was working directly
� with and for B&C (during the production of first 2000
or so alternators) I can say that I witnessed an exceedingly
� low return rate. Probably on the order of 1% per year for
the FLEET of fielded product. I can also state that the
majority if not all returns were for installation or maintenance
induced damage. We replaced a number of b-lead studs
that were burned off due to loosened nuts. I recall one
alternator that needed new bearings . . . seems the guy
liked to wash his engine often with high-pressure, soap
laden water.
I never saw a brush failure or rectifier failure or
an opening of a joint either electrical or mechanical.
Of course this begs the question of just what warranty
is either implied or stated in writing. If one does
a Google search on the B&C website for the word "warranty"
you get one hit at:
http://www.bandc.biz/SYSTEM_DIAGRAMS.html
An this use of the word speaks only to reader's
options to adopt the design goals of any of the
electrical system architectures posted.
I worked 12 years running in the OSH booth for
B&C. A common question I fielded from attendees
was "what's the warranty on this stuff?". I could
� confidently answer, "Our warranty is no unhappy
customers. If you have an issue with a B&C
product, you call this guy over here (pointing
to Bill). If he doesn't take care of your
needs, you call me and I'll drive up to Newton
and find out what his problem is!"
The answer to your question does not stand simply
on consideration of "rebuilt" versus "new". It
cannot be divined from the study of published
warranty return numbers. The return on investment
for the user of any product starts with efficient
and robust satisfaction of design goals supported
by a sense of craftsmanship and customer service
from the time the first parts are assembled until
the customer is finished with the product and is
satisfied with the demonstrated service life.
In B&C's case, they start with a robust component
with a exemplary, demonstrated service life in
the field. They do only that which is necessary to
make that product fit the legacy design goals for
aircraft electrical system performance and control.
Finally, they stand behind their stated warranty
policy.
This isn't a numbers game, it's a say what you do,
do what you say game. In B&C's case up until 2000
or so, they said "no unhappy customers" and I believed
that because it was my job to help deliver to that
statement. I have no reason to believe that either
statement or policy has changed since that time.
I've worked in this industry for virtually all of
my professional career . . . and even in 'retirement'
my major cash flow comes from aviation. If I had
a major disappointment to share with you, it was
the huge shift from a satisfied, loyal customer
game to a numbers game. Our highest institutions
of learning have discovered ways to analyze the
hell out of any constellation of processes and
to chart the results in living color. Other
departments in those same institutions have neglected
to teach their students that those analysis techniques
are useful tools to help you fine tune performance
but must be applied and interpreted carefully so
as to avoid obscuring facts.
I have seen a warranty returns investigation that
was ultimately "resolved" by cutting the warranty
period from two down to one year. The bleeding fell by
90%. The change of one word on a piece of paper
saved the company about a quarter million a year!
An the warranty return numbers for that device
jumped dramatically . . . and some bureaucrat
got to take credit for it.
This same industry drives design decisions based on
so-called reliability studies. We get out the
holy-watered documents that tell us how to predict
the failure rates of components used in electronics.
We enter all the components into this big computer
model and crunch the numbers to see what number
falls out for predicted mean time between failure
(MTBF). My customers live and die on MTBF numbers.
Sitting in a conference room last year I had to
struggle to keep a straight face when our customer's
purchase specification called for a 20,000 hour
MTBF on our proposed product. The byproduct of these
numbers games is almost total BS. After ten years
of production on the finished product, it is
axiomatic that we will have made numerous repairs
to fielded systems for a combination of reasons
not limited to design error, manufacturing error,
installation error, maintenance error, operating
error or conditions that were never anticipated
in the original design . . . and NONE of those
systems will have been in service for 20,000
hours!
Nonetheless, somebody will massage and tweak the
so-called MTBF "study" until the computer model
coughs out the desired number whereupon our customer
smiles and signs the check that purchases a few
million dollars worth of this "golden product".
The global warming cult has applied computer
modeling tools to their particular social engineering
goals with great success.
As consumers, our faith in such numbers needs to
be tempered with understanding of how they were
generated. The warranty return rate for brand
X may appear a whole lot better than brand Y simply
because brand X has a 90 day warranty and brand
Y has a 1 year warranty.
Further, their numbers may or may not reflect
returns based on careful analysis of manufacturer's
culpability. I can say that all the returns on
B&C alternators I witnessed were for installation
or maintenance induced failures but we fixed them
under warranty anyhow . . . not because the product
failed to meet performance expectations but because
the warranty was "no unhappy customers".
The true answer to your question comes from the
search for an unhappy B&C customer. I've heard
many a tale from guys who heard that a second
cousin of their friend thought B&C and or
AeroElectric Connection stuff was junk. But even
after offering cash rewards for these unhappy
customers to step forward and at least get their
money back, silence from the=====
& Download, 7-Day Browse, Chat, FAQ,
return top.js.OpenExtLink(window,event,this)" href="http://www.matronics.com/Navigator?AeroElectric-List" target="_blank">http://www.matronics.com/Navigator?AeroElectric-List
op.js.OpenExtLink(window,event,this)" href="http://forums.matronics.com/" target="_blank">http://forums.matronics.com
-Matt Dralle, List Admin.
is)" href="http://www.matronics.com/contribution" target="_blank">http:========================
[b]
| - The Matronics AeroElectric-List Email Forum - | | Use the List Feature Navigator to browse the many List utilities available such as the Email Subscriptions page, Archive Search & Download, 7-Day Browse, Chat, FAQ, Photoshare, and much more:
http://www.matronics.com/Navigator?AeroElectric-List |
|
|
|
Back to top |
|
 |
BobsV35B(at)aol.com Guest
|
Posted: Thu Jun 19, 2008 8:13 am Post subject: Alternator Warranty Data Point - Rebuilt vs. New |
|
|
Good Morning Bob,
Different Bob here, but I never do any cleaning within my cowl other than wiping with a rag. On the very rare and unlikely occasion when a small bit of grime gets in a difficult corner, I will use a small paint brush moistened with mineral spirits to loosen things up.
Other than that, it is a rag only.
That rag may or may not be moistened with mineral spirits or another appropriate cleaner.
Works for me!
Happy Skies,
Old Bob
AKA
Bob Siegfried
Ancient Aviator
628 West 86th Street
Downers Grove, IL 60516
630 985-8502
Stearman N3977A
Brookeridge Air Park LL22
In a message dated 6/19/2008 11:00:00 A.M. Central Daylight Time, bobf(at)feldtman.com writes:
Quote: | Bob - you bring up an interesting point - what is the best way (from an aicraft electrical standpoint) to "wash" an engine. Different A&Ps recommend different soaps, detergents, ways etc. I once lost a GM alternator on a truck when it was "Steam cleaned" - and the alternator did go out at an inopportune time. Obviously don't squirt anything into the alternator, but what about for all the other wires etc? I've never seen that addressed on the forum as to the best and safest way to clean up under the cowl!
thanks
bobf
125GS LOM powered Glastar
|
Gas prices getting you down? Search AOL Autos for fuel-efficient used cars.
[quote][b]
| - The Matronics AeroElectric-List Email Forum - | | Use the List Feature Navigator to browse the many List utilities available such as the Email Subscriptions page, Archive Search & Download, 7-Day Browse, Chat, FAQ, Photoshare, and much more:
http://www.matronics.com/Navigator?AeroElectric-List |
|
|
|
Back to top |
|
 |
|
|
You cannot post new topics in this forum You cannot reply to topics in this forum You cannot edit your posts in this forum You cannot delete your posts in this forum You cannot vote in polls in this forum You cannot attach files in this forum You can download files in this forum
|
Powered by phpBB © 2001, 2005 phpBB Group
|