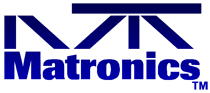 |
Matronics Email Lists Web Forum Interface to the Matronics Email Lists
|
View previous topic :: View next topic |
Author |
Message |
steve(at)tomasara.com Guest
|
Posted: Fri Feb 06, 2009 7:06 am Post subject: Screw Terminals on B&C breakers... |
|
|
Bob and the group,
While rewiring my not-yet-flown-by-me Longeze I've been attempting to
follow the interconnect philosophy (for power wiring) of:
Fast-ons preferred for appropriate (lower) current connections,
Studs w/ ring terminals (with either a self-locking nut or a 2nd (aka
jam-nut) nut) for higher current,
Screw-terminals, which aren't really lockable, to be avoided.
But I haven't been completely successful yet. What is recommended for:
-The screw-terminal B&C breaker used for the alternator field winding?
Blue locktite? Or use another breaker? Or don't worry about it? Of my
list, this one bothers me the most as the screws are small enough that
it's not clear to me I can tighten them enough to get an appropriately
gas-tight connection without stripping them. Not to mention the
(imagined?) possibility of inadvertently loosening them by poking around
behind the panel and moving the wire (and associated ring terminal) they
are attempting to clamp.
- The B+ connection on my alternator (ND external regulator type from a
Toyota) which uses a metric nut and doesn't have room on the stud for a
jam nut (I haven't looked for a high-temp self locking metric nut but
that's probably the answer if I can find one),
- The brass screw terminals for the amp-meter leads at the shunt (from
B&C) (blue locktite?)
On a related note, can anyone point me to the appropriate torque
standards for brass nuts onto brass studs (as on the B&C shunt and the
B&C grounding blocks...)
And, lastly, is there any (presumably metallurgical) reason it's a bad
idea to use a non-brass nut (or jam-nut) on a brass stud?
Thanks in advance,
Steve.
| - The Matronics AeroElectric-List Email Forum - | | Use the List Feature Navigator to browse the many List utilities available such as the Email Subscriptions page, Archive Search & Download, 7-Day Browse, Chat, FAQ, Photoshare, and much more:
http://www.matronics.com/Navigator?AeroElectric-List |
|
|
|
Back to top |
|
 |
nuckolls.bob(at)aeroelect Guest
|
Posted: Sat Feb 07, 2009 6:34 am Post subject: Screw Terminals on B&C breakers... |
|
|
At 09:01 AM 2/6/2009, you wrote:
Quote: |
Bob and the group,
While rewiring my not-yet-flown-by-me Longeze I've been attempting
to follow the interconnect philosophy (for power wiring) of:
Fast-ons preferred for appropriate (lower) current connections,
Studs w/ ring terminals (with either a self-locking nut or a 2nd
(aka jam-nut) nut) for higher current,
Screw-terminals, which aren't really lockable, to be avoided.
|
I'm not sure I can beat an enthusiastic drum
for "avoiding" screw terminals. After all, they've
been used in civil and military aircraft since day-one
and I'm aware of no considered movement to reduce
their numbers. The fasteners we really went after
were rivets when the molded/bonded composite structures
were conceived, crafted and qualified.
As we speak, there are hundreds of thousands of
airplanes in the word that use breakers like
and other devices with threaded fasteners not
unlike . . .
http://aeroelectric.com/Pictures/Wiring_Technique/A36_Firewall_A.jpg
http://aeroelectric.com/Pictures/Wiring_Technique/bus_bars_1.jpg
What I CAN suggest with enthusiasm is that
the non-professional assembler of components
has a higher probability of success (i.e. lower
risk of future failures) if the processes used
are "self calibrating". I.e. crimped as opposed to
soldered, fast-ons as opposed to torque sensitive
screws, etc. etc. A secondary consideration goes
to simple-reliability studies where all things
being equal, the lower parts-count assembly is
the more reliable.
Quote: | But I haven't been completely successful yet. What is recommended for:
-The screw-terminal B&C breaker used for the alternator field winding?
Blue locktite? Or use another breaker? Or don't worry about it?
|
It's not worthy of much worry. First because we're
building FAILURE TOLERANT aircraft . . . or at least
that's the goal. As you assemble EVERY bit and piece
of airplane, study the manner in which it might fail,
deduce whether or not the failure is pre-flight detectable,
deduce how you would become aware of the failure in
flight, deduce criticality of the failure and finally,
if loss of that component's functionality puts your
comfortable termination of flight at-risk, then
craft a Plan-B for dealing with it.
Quote: | Of my list, this one bothers me the most as the screws are small
enough that it's not clear to me I can tighten them enough to get an
appropriately gas-tight connection without stripping them. Not to
mention the (imagined?) possibility of inadvertently loosening them
by poking around behind the panel and moving the wire (and
associated ring terminal) they are attempting to clamp.
|
At the current levels this breaker operates at, it's
not essential that the whole mating surface area under
the head of the screw be gas-tight. At the microscopic
level, you will find that when these 6-32 screws are
torqued "in the ball park", surface irregularities
(yeah it LOOKS and FEELS smooth . . . but the earth
is smoother than a billiard ball) will come together
with sufficient pressure to make the electrical joint.
That gas-tightness thing for the whole surface area
has more to do with keeping moisture/oxidants out
for longevity of the joint . . . that's when we get
the wrench out and crank that fat wire terminal down
good. Stuff behind the panel is not subject to much
splash.
Quote: | - The B+ connection on my alternator (ND external regulator type
from a Toyota) which uses a metric nut and doesn't have room on the
stud for a jam nut (I haven't looked for a high-temp self locking
metric nut but that's probably the answer if I can find one),
|
Yeah, and as I recall those threads were pretty
coarse too. In fact, b-lead terminals are pretty
high on the list of reasons that alternators are
returned to B&C for repair. The nut works loose
and the terminal burns.
Quote: | - The brass screw terminals for the amp-meter leads at the shunt
(from B&C) (blue locktite?)
On a related note, can anyone point me to the appropriate torque
standards for brass nuts onto brass studs (as on the B&C shunt and
the B&C grounding blocks...)
|
If you have a torque wrench and your confidence
goes up by using it, then my all means. I can
tell you that none of the threaded fasteners
in the photos above were precision torqued. The
the band of satisfactory assembly between too
loose and too tight is really pretty big.
Most brasses have a tensile strength on the
order of 50K PSI, so look up the torque values
for any steel part of the same thread (AC43-13
has some tables) and adjust the value for brass
downward in proportion to their relative strengths.
Just for grins, take a 6-32 steel screw and a
brass nut (breaker combo) and see how hard it
is to fail the parts by twisting on them. If you
DO achieve failure, do it a couple of times. This
will give you some sense of limits for doing the
same task in your airplane. I think you'll find
that you're not inclined to put nearly so much
force on the parts to achieve satisfactory
"snugness".
Quote: | And, lastly, is there any (presumably metallurgical) reason it's a
bad idea to use a non-brass nut (or jam-nut) on a brass stud?
|
Not sure I'd worry about it. The fat wires go onto
studs that are larger and fine threaded. Cranking
these puppies down without further "insurance"
is common practice.
Locktite on the automotive threaded b-lead
nut is about the only place I'd consider the
use of a magic elixir useful for fixture.
It's more important that fat wires on studs
not impart strong rotational moments under
vibration. Note the techniques used to
bundle wires in this photo.
http://aeroelectric.com/Pictures/Wiring_Technique/A36_Firewall_B.jpg
Bob . . .
Quote: | Thanks in advance,
Steve.
Checked by AVG - www.avg.com
02/04/09 16:35:00
|
Bob . . .
----------------------------------------)
( . . . a long habit of not thinking )
( a thing wrong, gives it a superficial )
( appearance of being right . . . )
( )
( -Thomas Paine 1776- )
----------------------------------------
| - The Matronics AeroElectric-List Email Forum - | | Use the List Feature Navigator to browse the many List utilities available such as the Email Subscriptions page, Archive Search & Download, 7-Day Browse, Chat, FAQ, Photoshare, and much more:
http://www.matronics.com/Navigator?AeroElectric-List |
|
|
|
Back to top |
|
 |
|
|
You cannot post new topics in this forum You cannot reply to topics in this forum You cannot edit your posts in this forum You cannot delete your posts in this forum You cannot vote in polls in this forum You cannot attach files in this forum You can download files in this forum
|
Powered by phpBB © 2001, 2005 phpBB Group
|