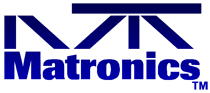 |
Matronics Email Lists Web Forum Interface to the Matronics Email Lists
|
View previous topic :: View next topic |
Author |
Message |
nuckolls.bob(at)aeroelect Guest
|
Posted: Wed May 27, 2009 8:21 am Post subject: Grounding philosophy |
|
|
At 09:05 AM 5/27/2009, you wrote:
<phillip.johnson(at)lmco.com>
Bob,
I read your message and went to your web link indicated below and I
can't accept that it is a good design. The problem that I see is that
your design does not create a single ground reference.
Yes it does. The architectures discussed in Figure Z-15 and
other writings suggeste the stud at the forest of tabs on the
firewall is the central point ground for the aircraft.
Ideally you want
the engine block to be the ground reference with all currents flowing
through it. To this end you need to connect the battery -ve to the
crankcase and then make all grounds connect, either directly or
indirectly, to the crankcase as well. In doing this there will be no
ground potential differences to upset the instrumentation.
Instrumentation is a special case where grounded automotive
sensors are at risk for suffering ground loop interference.
This has been discussed at length in various writings. If the
problem presents itself (usually manifest by a shift in
instrumentation readings in response to alternator loads),
then the "ground" leads for panel mounted instruments need
to be extended to the crankcase. However, if one has a very
low resistance net between he crankcase and the firewall
ground stud . . . then the "problem" may be reduced to
insignificant if not completely unobservable.
<snip>
The pilot now tries to start the engine and all of
the current tries to flow through this instrumentation ground. This
causes a melt down of the wiring and a potential ground fire and risk to
those expensive electronics.
Again, discussed in past publications and postings . . .
"Smoking ground returns" is easily avoided by not closing
the returns. Common occurrences include the risk of
instrumentation grounds for instruments not designed
to live in the real world of aircraft. Another common
risk happens when builders attached p-lead shields to
crankcase at one end and airframe at the other end.
All of my drawings illustrate technique for avoiding
that loop as well.
It is my opinion, and I believe that the automotive industry also adopts
this philosophy, that you connect the battery ground to the crankcase
and then strap the engine to the airframe/car body and system ground so
that the high current grounds pass only through the engine. Charging
ground currents, which can be extremely high, also only pass through the
engine block thereby preventing erroneous instrumentation and potential
fire risk.
Batteries go to crankcases in cars because the battery
always sits right next to the engine. The automotive
industry has adopted the same philosophy as every other
industry for minimizing the numbers of joints, fasteners
and pieces of wire in the fat-wire conduction paths.
Now, if one had a battery on the forward side of
the firewall then there is no electrical reason
NOT to ground the battery right to the crankcase.
There are mechanical reasons not to . . . we've
already established the value of a 2AWG equivalent
jumper from crankcase to ground stud. This same stud
becomes a practical spot to ground a battery as
well . . . and the 2AWG bonding strap makes sure
that voltage differences between the crankcase
and the ground stud are insignificantly small.
If the battery is aft of the firewall, then the
most practical battery ground is the firewall
ground stud . . . or to the airframe on an all
metal airplane.
OK I've now started to run and get my flame suit on.
Zero risk from me sir . . .
Bob . . .
| - The Matronics AeroElectric-List Email Forum - | | Use the List Feature Navigator to browse the many List utilities available such as the Email Subscriptions page, Archive Search & Download, 7-Day Browse, Chat, FAQ, Photoshare, and much more:
http://www.matronics.com/Navigator?AeroElectric-List |
|
|
|
Back to top |
|
 |
mprather(at)spro.net Guest
|
|
Back to top |
|
 |
phillip.johnson(at)lmco.c Guest
|
Posted: Thu May 28, 2009 6:21 am Post subject: Grounding philosophy |
|
|
Time: 09:21:48 AM PST US
From: "Robert L. Nuckolls, III" <nuckolls.bob(at)aeroelectric.com>
Subject:
At 09:05 AM 5/27/2009, you wrote:
<phillip.johnson(at)lmco.com>
Bob,
Quote: | I read your message and went to your web link indicated below and I
can't accept that it is a good design. The problem that I see is that
your design does not create a single ground reference.
|
>Yes it does. The architectures discussed in Figure Z-15 and
>other writings suggeste the stud at the forest of tabs on the
>firewall is the central point ground for the aircraft.
So Ground point number one is the "forest of tabs" and ground point
number two is the engine crankcase when the alternator, starter motor,
and most engine sensors make their ground. I.e. there is not a single
point ground. In an ideal world where #2 gauge wires and
interconnections have zero resistance but, as you point out in your
document, this is not the case.
Quote: | >Ideally you want
>the engine block to be the ground reference with all currents flowing
>through it. To this end you need to connect the battery -ve to the
>crankcase and then make all grounds connect, either directly or
>indirectly, to the crankcase as well. In doing this there will be no
>ground potential differences to upset the instrumentation.
|
>Instrumentation is a special case where grounded automotive
>sensors are at risk for suffering ground loop interference.
>This has been discussed at length in various writings. If the
>problem presents itself (usually manifest by a shift in
>instrumentation readings in response to alternator loads),
>then the "ground" leads for panel mounted instruments need
>to be extended to the crankcase. However, if one has a very
>low resistance net between he crankcase and the firewall
>ground stud . . . then the "problem" may be reduced to
>insignificant if not completely unobservable.
They should not have to be a special case if wired correctly. When
everything references the crankcase there is no special case. The
problem is that when the installation is done all the connections are
clean and the installer usually knows what he is doing. A few years
down the road an unknowledgeable person does not prepare the electrical
bonding surface as well as he should and then problems start happening
when current starts to flow through the circuit. Using the philosophy
that I have given, these problems are reduced significantly, which in my
opinion makes for a better design.
Quote: | >The pilot now tries to start the engine and all of
>the current tries to flow through this instrumentation ground. This
>causes a melt down of the wiring and a potential ground fire and risk
to
|
Quote: | >those expensive electronics.
|
>Again, discussed in past publications and postings . . .
>"Smoking ground returns" is easily avoided by not closing
>the returns. Common occurrences include the risk of
>instrumentation grounds for instruments not designed
>to live in the real world of aircraft. Another common
>risk happens when builders attached p-lead shields to
>crankcase at one end and airframe at the other end.
>All of my drawings illustrate technique for avoiding
>that loop as well.
Again, "Smoking ground returns" are avoided if you use my design
solution.
Quote: | >It is my opinion, and I believe that the automotive industry also
adopts
|
Quote: | >this philosophy, that you connect the battery ground to the crankcase
>and then strap the engine to the airframe/car body and system ground
so
|
Quote: | >that the high current grounds pass only through the engine. Charging
>ground currents, which can be extremely high, also only pass through
the
|
Quote: | >engine block thereby preventing erroneous instrumentation and
potential
|
>Batteries go to crankcases in cars because the battery
>always sits right next to the engine.
In the old days the battery ground went straight to the bodywork and
then there was an engine strap in a different location which coupled the
body to the engine. I'm not sure when the change occurred but I would
guess that it occurred somewhere soon after the first electronic systems
were implemented. I changed the battery on my neighbours Audi a couple
of years ago and that had the battery under the rear seats. The ground
lead did not go straight to the body but I can't be sure that it went
all the way to the front either. I surmise that if it did not go
directly to the body it would probably make the full journey to the
engine.
>The automotive
>industry has adopted the same philosophy as every other
>industry for minimizing the numbers of joints, fasteners
>and pieces of wire in the fat-wire conduction paths.
Agreed
>Now, if one had a battery on the forward side of
>the firewall then there is no electrical reason
>NOT to ground the battery right to the crankcase.
>There are mechanical reasons not to . . . we've
>already established the value of a 2AWG equivalent
>jumper from crankcase to ground stud. This same stud
>becomes a practical spot to ground a battery as
>well . . . and the 2AWG bonding strap makes sure
>that voltage differences between the crankcase
>and the ground stud are insignificantly small.
I have a Cozy MK IV with the battery on the cockpit side of the
firewall. I have approximately two feet of cable connecting the -ve to
crankcase ground so length cant be an issue. The issue is that there
are two additional connections and a couple of feet of #2 cable
separating the engine ground from the "forest of tabs". Using the
numbers from your paper this gives 1.3 mohm of resistance. Assuming you
have an alternator sourcing say 40 amps you now have 50 mV ground
difference which is also rectified AC i.e. noise. Now as you have said
it is difficult to get better than 0.5miliohm per connection and with
time and sloppy maintenance the number grows to something that is
unacceptable. All this just because the ground reference was not
defined appropriately.
>If the battery is aft of the firewall, then the
>most practical battery ground is the firewall
>ground stud . . . or to the airframe on an all
>metal airplane.
OK I have a plastic aeroplane so airframe is not an option but I still
feel the firewall is a bad choice.
Quote: | >OK I've now started to run and get my flame suit on.
|
>Zero risk from me sir . . .
Bob . . .
| - The Matronics AeroElectric-List Email Forum - | | Use the List Feature Navigator to browse the many List utilities available such as the Email Subscriptions page, Archive Search & Download, 7-Day Browse, Chat, FAQ, Photoshare, and much more:
http://www.matronics.com/Navigator?AeroElectric-List |
|
|
|
Back to top |
|
 |
nuckolls.bob(at)aeroelect Guest
|
Posted: Thu May 28, 2009 1:07 pm Post subject: Grounding philosophy |
|
|
So Ground point number one is the "forest of tabs" and ground point
number two is the engine crankcase when the alternator, starter motor,
and most engine sensors make their ground. I.e. there is not a single
point ground. In an ideal world where #2 gauge wires and
interconnections have zero resistance but, as you point out in your
document, this is not the case.
Let's not get wrapped around the axle for defining
"single point ground". The better term is perhaps
a central ground point from which the rest of the
ground system radiates. Now, there can be and often
is further spreading from nodes remote from the
central ground. One example is the crankcase from which
numerous grounded sensors find a reference. See
Figure Z-15 (three sheets).
Risks of system performance degrading due to currents
circulating in the ground system are reduced if not
eliminated by first avoiding multiple grounds within
any single system that are not co-located. In the
case of engine instruments with grounded sensors,
taking the ground returns for panel mounted instruments
back to the crankcase makes the crankcase a "single
point ground" for that suite of instruments.
Figure Z-15 speaks to a variety of grounding options
for accessories located all over the airplane. None
of those illustrations suggests that ALL grounds
be brought to a single-point be it the crankcase
or forest of tabs. What those drawing DO illustrate
is making a distinction between potential noise
victims, noise antagonists and breaking the ground
loop coupling mode.
They should not have to be a special case if wired correctly. When
everything references the crankcase there is no special case. The
problem is that when the installation is done all the connections are
clean and the installer usually knows what he is doing. A few years
down the road an unknowledgeable person does not prepare the electrical
bonding surface as well as he should and then problems start happening
when current starts to flow through the circuit. Using the philosophy
that I have given, these problems are reduced significantly, which in my
opinion makes for a better design.
Define "wired correctly". In the TC aviation world
we're very much aware of the problems associated
with engine sensors conforming to legacy automotive
conventions of grounding to the block. In the 1957
Chevy, the grounded oil pressure "sender" is
"wired correctly". In a 1995 Beechjet, this product
would not be considered for a host of reasons not
the least of which is "incorrect wiring" for design
goals imposed on the project. But if my boss says
"Put this 1957 oil pressure gage in that airplane"
I can get 'er done with zero risk of degraded
performance induced by poor grounding decisions.
Again, "Smoking ground returns" are avoided if you use my design
solution.
I'm not suggesting that there is but one solution
for avoiding smoking grounds or ground loop induced
noise. If you choose to use the crankcase as your
"single point ground" . . . is it your intention to
take all the ground wires from ship's electro-whizzies
to the crankcase? That could make for a really big
bundle of wires through the firewall. If you grounded
EVERYTHING to the crankcase, would you still ground
the p-lead shields at both ends?
>Batteries go to crankcases in cars because the battery
>always sits right next to the engine.
In the old days the battery ground went straight to the bodywork and
then there was an engine strap in a different location which coupled the
body to the engine. I'm not sure when the change occurred but I would
guess that it occurred somewhere soon after the first electronic systems
were implemented. I changed the battery on my neighbours Audi a couple
of years ago and that had the battery under the rear seats. The ground
lead did not go straight to the body but I can't be sure that it went
all the way to the front either. I surmise that if it did not go
directly to the body it would probably make the full journey to the
engine.
Which is anecdotal to what we're discussing here.
Exactly how you achieve low resistance, minimum
parts count, no-loop architecture for grounds in
your airplane has many recipes for success as long
as the components are assembled with understanding.
But let us take care that we don't confuse 1800+
readers of this List with some notion that the crankcase
is the touchstone of grounds . . . this simply isn't so.
I have a Cozy MK IV with the battery on the cockpit side of the
firewall. I have approximately two feet of cable connecting the -ve to
crankcase ground so length cant be an issue. The issue is that there
are two additional connections and a couple of feet of #2 cable
separating the engine ground from the "forest of tabs". Using the
numbers from your paper this gives 1.3 mohm of resistance. Assuming you
have an alternator sourcing say 40 amps you now have 50 mV ground
difference which is also rectified AC i.e. noise. Now as you have said
it is difficult to get better than 0.5miliohm per connection and with
time and sloppy maintenance the number grows to something that is
unacceptable. All this just because the ground reference was not
defined appropriately.
I think you're sifting the sand here. There
is NO electrical system for any vehicle that is
not plagued with beeps, burps, hums, spikes and
assorted perturbations of voltage a LOT bigger
than your hypothesis. In the TC aircraft world
we KNOW that those noises exist and we design
to live with them. See:
http://www.aeroelectric.com/articles/DO-160.pdf
The voltage levels you hypothesize are of
no significance if potentially vulnerable
systems don't see them because ground loops have
been eliminated. Making sure the loops don't exist
is easy if you understand your system integration
task. It matters not whether the system follows
legacy automotive design goals or modern aviation
design goals. BOTH technologies can be successfully
integrated into the OBAM aircraft.
>If the battery is aft of the firewall, then the
>most practical battery ground is the firewall
>ground stud . . . or to the airframe on an all
>metal airplane.
OK I have a plastic aeroplane so airframe is not an option but I still
feel the firewall is a bad choice.
A "bad choice" only if you allow ground
loops to exist without evaluating their potential
for influencing system performance. Please
wire in any manner that gives you comfort.
All I'm offering is a constellation of options
based on many recipes for success. Virtually
ALL of those recipes call for elimination of
ground loops that offer a potential for problems.
NONE of those recipes treats any location or
component of the ground system as the Nirvana
of grounds.
The forest-of-tabs offers a level of convenience
for the majority of system grounds for devices
both sides of the firewall. Having this device
be 'central' to the ship's ground system
makes sense . . . especially if the engine
sensors are "wired correctly" in observance of
modern aircraft design goals. But even if they
are not, the third sheet of Z15 suggests how the
1950's design goals can be accommodated in a 2009
RV.
Bob . . .
| - The Matronics AeroElectric-List Email Forum - | | Use the List Feature Navigator to browse the many List utilities available such as the Email Subscriptions page, Archive Search & Download, 7-Day Browse, Chat, FAQ, Photoshare, and much more:
http://www.matronics.com/Navigator?AeroElectric-List |
|
|
|
Back to top |
|
 |
|
|
You cannot post new topics in this forum You cannot reply to topics in this forum You cannot edit your posts in this forum You cannot delete your posts in this forum You cannot vote in polls in this forum You cannot attach files in this forum You can download files in this forum
|
Powered by phpBB © 2001, 2005 phpBB Group
|