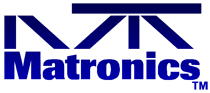 |
Matronics Email Lists Web Forum Interface to the Matronics Email Lists
|
View previous topic :: View next topic |
Author |
Message |
nuckolls.bob(at)aeroelect Guest
|
Posted: Mon Jun 29, 2009 8:23 pm Post subject: Time to Battery Exhaustion |
|
|
<eanderson(at)carolina.rr.com>
Having had some recent real-world experience with battery exhaustion, I
though some of you might be interested in actual flight duration with all
systems on - until the battery voltage dropped below that necessary to run
crucial flight systems.
<snip>
Next morning, once switch was placed in the proper position (connecting
battery to alternator) a test flight was made and all checked out and I
continued on to Texas. Flew back with no incident. However, I doubt the
battery would do as well a second time as the voltage had dropped to 6 volts
by the time I checked on the ground. From what I understand is that once a
battery undergoes that degree of discharge, its capacity is less than it
was.
This is why the Z-figures and other writings in
the 'Connection suggest ACTIVE NOTIFICATION OF
LOW VOLTAGE on the main bus. When you turn the
battery master on before cranking the engine, that
light is an irritating feature on the panel and
remains so until the alternator comes on to boost
the bus above 13.0 volts.
The battery is rated at 17 AH, don't know how much the engine start drained
but at 400 amp for say 5 second for engine start = 0.55 amp-hour leaving
theoretically 16.45 amp hour in the battery. Flew for 45 minutes before the
dropping voltage started undesirable things happening so 45/60 = .75 hour of
battery powered flight. That theoretically would indicate a 16.45/.75 = 21
amp/hour load. Clearly lots of estimation here but that load (with two 50
watt landing lights on) does not seem unreasonable to me.
See . . .
http://www.aeroelectric.com/Pictures/Curves/17AH_12V_Capacity_vs_Load.gif
The typical 17 a.h. battery being discharged in 40
minutes when presented with a 17A load. This yields
a useful capacity on the order of 17 x 0.7 or 12 ampere
hours.
But all things considered - the battery did a credible job of lasting as
long as it did. Just wanted to post a real world example of battery power
duration.
Lessons learned - stick in the isolation diode so battery will get
alternator juice regardless of essential bus switch
position.
Without seeing your power distribution diagram, I'm
not sure what the "isolation diode" is about. Active
and irritating notification of low voltage becomes
a expected event that cannot missed or ignored. I
requires no training and/or checklist activity for
making sure things are up and running before flight.
Bob . . .
| - The Matronics AeroElectric-List Email Forum - | | Use the List Feature Navigator to browse the many List utilities available such as the Email Subscriptions page, Archive Search & Download, 7-Day Browse, Chat, FAQ, Photoshare, and much more:
http://www.matronics.com/Navigator?AeroElectric-List |
|
|
|
Back to top |
|
 |
Ed Anderson
Joined: 10 Jan 2006 Posts: 475
|
Posted: Tue Jun 30, 2009 4:12 am Post subject: Time to Battery Exhaustion |
|
|
Hi Bob,
The "isolation diode" was a poor choice of words for the schokkty battery
feed diode between alternator power and the essential bus battery circuit.
If I had installed that diode 10 years ago (per your design) then having the
switch in the wrong position wouldn't have affected the ability of the
battery to get alternator voltage.
The problem with my "low voltage warning" indicator (both LED and Voltmeter)
was they were on the alternator circuit and NOT the battery. Since the
alternator was working fine and continued to produce power (until the
dropping battery voltage opened the master relay), these two devices never
indicated low voltage. IF I had thought to switch the voltmeter to the
battery then I would likely have noticed the decreasing battery voltage.
Thanks for the battery drain curve, appears my system does not have as much
current drain as I had estimated. Also looks like the powered required for
starting did not much affect the duration.
Ed
Ed Anderson
Rv-6A N494BW Rotary Powered
Matthews, NC
eanderson(at)carolina.rr.com
http://www.andersonee.com
http://www.dmack.net/mazda/index.html
http://www.flyrotary.com/
http://members.cox.net/rogersda/rotary/configs.htm#N494BW
http://www.rotaryaviation.com/Rotorhead%20Truth.htm
--
| - The Matronics AeroElectric-List Email Forum - | | Use the List Feature Navigator to browse the many List utilities available such as the Email Subscriptions page, Archive Search & Download, 7-Day Browse, Chat, FAQ, Photoshare, and much more:
http://www.matronics.com/Navigator?AeroElectric-List |
|
_________________ Ed Anderson
Rv-6A N494BW Rotary Powered
Matthews, NC
eanderson@carolina.rr.com |
|
Back to top |
|
 |
nuckolls.bob(at)aeroelect Guest
|
Posted: Tue Jun 30, 2009 6:15 am Post subject: Time to Battery Exhaustion |
|
|
At 07:09 AM 6/30/2009, you wrote:
Quote: | --> AeroElectric-List message posted by: "Ed Anderson" <eanderson(at)carolina.rr.com>
Hi Bob,
The "isolation diode" was a poor choice of words for the schokkty battery
feed diode between alternator power and the essential bus battery circuit.
If I had installed that diode 10 years ago (per your design) then having the
switch in the wrong position wouldn't have affected the ability of the
battery to get alternator voltage. |
I'm still not getting a mental image of
how you had it wired. How does the
existence or lack of the diode affect
connection between battery and alternator?
Quote: | The problem with my "low voltage warning" indicator (both LED and Voltmeter)
was they were on the alternator circuit and NOT the battery. Since the
alternator was working fine and continued to produce power (until the
dropping battery voltage opened the master relay), these two devices never
indicated low voltage. IF I had thought to switch the voltmeter to the
battery then I would likely have noticed the decreasing battery voltage. |
So have (or are you planning) you movee the low
voltage sensing point in your system?
Could you sketch and scan the distribution
system and share with us? Normally, alternator
has no way NOT to charge the battery if the
engine is running -AND- both the alternator
and battery control circuits are closed. I'm
having trouble visualizing how "both were
functioning" but the alternator was still not
connected to the battery.
Quote: | Thanks for the battery drain curve, appears my system does not have as much
current drain as I had estimated. Also looks like the powered required for
starting did not much affect the duration. |
While starters take a lot of POWER it is for
just a few seconds. The total ENERGY is quite
low. Even in large aircraft, the percentage of
battery energy used to start is a small fraction
of the total. In this start current curve we
took off a Beechjet . . .
http://www.aeroelectric.com/Pictures/Curves/turbine_start_a.jpg
. . . it takes about 20 seconds for cranking
current to taper from 800A to 300A and another
7 seconds to go to zero. Yet this 44 a.h. battery
is tapped for only 5 to 6 percent of total
stored energy. In piston singles where the engine
starts readily, it's about half that total.
You mentioned in the earlier post that you thought
you might have seriously whacked the battery's
ability to store energy when you allowed it to be
so severely depleted. This is generally no big
deal.
Brand new batteries subjected to a series of 90%
depletion cycles will slowly drop in capacity with
each cycle. Most RG batteries are good for several
hundred deep-cycles before they lose 20% of their
capacity.
[img]cid:.0[/img]
Here's an exemplar cycle-life performance curve for a
lithium battery . . . lead-acid curves are similar
they just don't go out to those really big numbers.
But a single deep discharge of your battery followed
by a recharging activity does not seriously affect
future performance.
Now, leaving the master switch on and leaving the
battery discharged for a couple of weeks is another
matter . . .
Bob . . .
| - The Matronics AeroElectric-List Email Forum - | | Use the List Feature Navigator to browse the many List utilities available such as the Email Subscriptions page, Archive Search & Download, 7-Day Browse, Chat, FAQ, Photoshare, and much more:
http://www.matronics.com/Navigator?AeroElectric-List |
|
Description: |
|
Filesize: |
81.17 KB |
Viewed: |
3059 Time(s) |
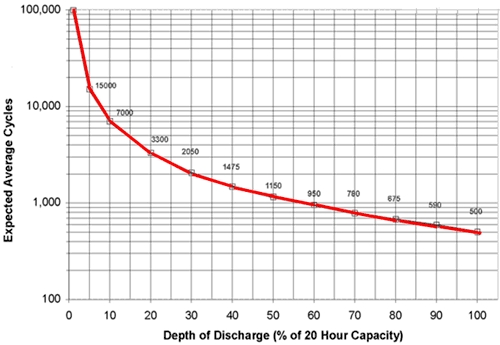
|
|
|
Back to top |
|
 |
Ed Anderson
Joined: 10 Jan 2006 Posts: 475
|
Posted: Tue Jun 30, 2009 7:14 am Post subject: Time to Battery Exhaustion |
|
|
Ok, Bob, here is a crude sketch of the essential elements
ALT B Lead ------------------- Aircraft Bus---------------------------------------------------- None Essential Load
| |
| |
| |
Switch Diode (not installed at time of incident)
Essential Bus Load ---------------------------- |---------- |
| |
Battery
The alternator B lead feeds the aircraft main bus. The switch is designed to be closed during normal operation permitting the alternator to charge/ recharge the battery – in this incident it became open – therefore no alternator voltage to charge battery. The diode would have permitted the alternator to charge the battery (regardless of switch position) IF I had installed it back 10 years ago. The idea back then was that if the alternator failed, I could remove the battery and essential load from that circuit by opening the switch. The diode (if I had installed it) would have prevent the very problem I encountered – that of the battery being exhausted because it could get no voltage from the alternator due to the inadvertently opened switch. Why a diode and a switch – well, diodes can fail, switches can fail – unlikely both would at the same time. – In reality, I have never moved the switch from the Alternator connection position in 10 years of flying – until, of course, this incident.
The idea of having the low voltage warning LED tied to the alternator circuit was that it would give first notice (before the battery started to drain) if there was a problem with alternator. The volt meter has a toggle switch so I can monitor either alternator or battery voltage. Unfortunately, I had it set to alternator and therefore it didn’t register the deteriorating battery voltage. Of course, if the switch in question is ON then alternator and battery voltage will read the same – so to check the battery voltage solely, I would need to open the Switch removing the alternator temporarily from feeding the battery.
This all seemed reasonable 10 years ago, less so since the incident - as you might imagine. Providing this so others may avoid my mistakes – certainly not trying to defend what in hindsight are obvious {:>) deficiencies in my design.
Ed
Ed Anderson
Rv-6A N494BW Rotary Powered
Matthews, NC
eanderson(at)carolina.rr.com
http://www.andersonee.com
http://www.dmack.net/mazda/index.html
http://www.flyrotary.com/
http://members.cox.net/rogersda/rotary/configs.htm#N494BW
http://www.rotaryaviation.com/Rotorhead%20Truth.htm[url=http://www.dmack.net/mazda/index.html][/url]
From: owner-aeroelectric-list-server(at)matronics.com [mailto:owner-aeroelectric-list-server(at)matronics.com] On Behalf Of Robert L. Nuckolls, III
Sent: Tuesday, June 30, 2009 10:12 AM
To: aeroelectric-list(at)matronics.com
Subject: RE: AeroElectric-List: Re: Time to Battery Exhaustion
At 07:09 AM 6/30/2009, you wrote:
--> AeroElectric-List message posted by: "Ed Anderson" <eanderson(at)carolina.rr.com>
Hi Bob,
The "isolation diode" was a poor choice of words for the schokkty battery
feed diode between alternator power and the essential bus battery circuit.
If I had installed that diode 10 years ago (per your design) then having the
switch in the wrong position wouldn't have affected the ability of the
battery to get alternator voltage.
I'm still not getting a mental image of
how you had it wired. How does the
existence or lack of the diode affect
connection between battery and alternator?
The problem with my "low voltage warning" indicator (both LED and Voltmeter)
was they were on the alternator circuit and NOT the battery. Since the
alternator was working fine and continued to produce power (until the
dropping battery voltage opened the master relay), these two devices never
indicated low voltage. IF I had thought to switch the voltmeter to the
battery then I would likely have noticed the decreasing battery voltage.
So have (or are you planning) you movee the low
voltage sensing point in your system?
Could you sketch and scan the distribution
system and share with us? Normally, alternator
has no way NOT to charge the battery if the
engine is running -AND- both the alternator
and battery control circuits are closed. I'm
having trouble visualizing how "both were
functioning" but the alternator was still not
connected to the battery.
Thanks for the battery drain curve, appears my system does not have as much
current drain as I had estimated. Also looks like the powered required for
starting did not much affect the duration.
While starters take a lot of POWER it is for
just a few seconds. The total ENERGY is quite
low. Even in large aircraft, the percentage of
battery energy used to start is a small fraction
of the total. In this start current curve we
took off a Beechjet . . .
http://www.aeroelectric.com/Pictures/Curves/turbine_start_a.jpg
. . . it takes about 20 seconds for cranking
current to taper from 800A to 300A and another
7 seconds to go to zero. Yet this 44 a.h. battery
is tapped for only 5 to 6 percent of total
stored energy. In piston singles where the engine
starts readily, it's about half that total.
You mentioned in the earlier post that you thought
you might have seriously whacked the battery's
ability to store energy when you allowed it to be
so severely depleted. This is generally no big
deal.
Brand new batteries subjected to a series of 90%
depletion cycles will slowly drop in capacity with
each cycle. Most RG batteries are good for several
hundred deep-cycles before they lose 20% of their
capacity.
[img]cid:image001.jpg(at)01C9F971.E0F91250[/img]
Here's an exemplar cycle-life performance curve for a
lithium battery . . . lead-acid curves are similar
they just don't go out to those really big numbers.
But a single deep discharge of your battery followed
by a recharging activity does not seriously affect
future performance.
Now, leaving the master switch on and leaving the
battery discharged for a couple of weeks is another
matter . . .
Bob . . .
__________ Information from ESET NOD32 Antivirus, version of virus signature database 3267 (20080714) __________
The message was checked by ESET NOD32 Antivirus.
__________ Information from ESET NOD32 Antivirus, version of virus signature database 3267 (20080714) __________
The message was checked by ESET NOD32 Antivirus.
__________ Information from ESET NOD32 Antivirus, version of virus signature database 3267 (20080714) __________
The message was checked by ESET NOD32 Antivirus.
| - The Matronics AeroElectric-List Email Forum - | | Use the List Feature Navigator to browse the many List utilities available such as the Email Subscriptions page, Archive Search & Download, 7-Day Browse, Chat, FAQ, Photoshare, and much more:
http://www.matronics.com/Navigator?AeroElectric-List |
|
Description: |
|
Filesize: |
81.17 KB |
Viewed: |
3057 Time(s) |
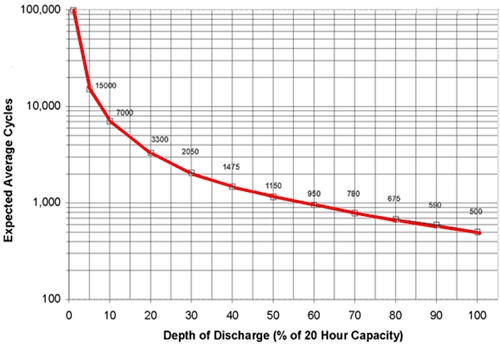
|
_________________ Ed Anderson
Rv-6A N494BW Rotary Powered
Matthews, NC
eanderson@carolina.rr.com |
|
Back to top |
|
 |
jon(at)finleyweb.net Guest
|
Posted: Tue Jun 30, 2009 9:14 am Post subject: Time to Battery Exhaustion |
|
|
Thank you Ed,
I have learned a number of things due to your willingness to share your experience and system configuration.
Jon Finley
N314JF - Q2 - Subaru EJ-22
http://www.finleyweb.net/Q2Subaru.aspx
--
| - The Matronics AeroElectric-List Email Forum - | | Use the List Feature Navigator to browse the many List utilities available such as the Email Subscriptions page, Archive Search & Download, 7-Day Browse, Chat, FAQ, Photoshare, and much more:
http://www.matronics.com/Navigator?AeroElectric-List |
|
|
|
Back to top |
|
 |
nuckolls.bob(at)aeroelect Guest
|
Posted: Tue Jun 30, 2009 10:31 am Post subject: Time to Battery Exhaustion |
|
|
At 10:02 AM 6/30/2009, you wrote:
Quote: |
Ok, Bob, here is a crude sketch of the essential elements
ALT B Lead ------------------- Aircraft Bus---------------------------------------------------- None Essential Load
| |
| |
| |
Switch Diode (not installed at time of incident)
Essential Bus Load ---------------------------- |---------- |
| |
Battery
The alternator B lead feeds the aircraft main bus. The switch is designed to be closed during normal operation permitting the alternator to charge/ recharge the battery – in this incident it became open – therefore no alternator voltage to charge battery. The diode would have permitted the alternator to charge the battery (regardless of switch position) IF I had installed it back 10 years ago. The idea back then was that if the alternator failed, I could remove the battery and essential load from that circuit by opening the switch. The diode (if I had installed it) would have prevent the very problem I encountered – that of the battery being exhausted because it could get no voltage from the alternator due to the inadvertently opened switch. Why a diode and a switch – well, diodes can fail, switches can fail – unlikely both would at the same time. – In reality, I have never moved the switch from the Alternator connection position in 10 years of flying – until, of course, this incident. |
Understand. Know that there are a host of reasons why
Z-11 is crafted the way it's illustrated in the
'Connection. This is a step-up from the legacy power
distribution common to 99.9% of all single-engine aircraft
ever flown.
The design goals call for main bus, battery and alternator
to be firmly in connection with each other. The purpose
of the endurance bus isolation diode is to prevent back-feeding
power from the e-bus while the e-bus alternate feed switch
is supplying power directly from the battery. The diode
has no function with respect to the relationship between
alternator and battery.
Quote: |
The idea of having the low voltage warning LED tied to the alternator circuit was that it would give first notice (before the battery started to drain) if there was a problem with alternator. The volt meter has a toggle switch so I can monitor either alternator or battery voltage. Unfortunately, I had it set to alternator and therefore it didn’t register the deteriorating battery voltage. Of course, if the switch in question is ON then alternator and battery voltage will read the same – so to check the battery voltage solely, I would need to open the Switch removing the alternator temporarily from feeding the battery.
This all seemed reasonable 10 years ago, less so since the incident - as you might imagine. Providing this so others may avoid my mistakes – certainly not trying to defend what in hindsight are obvious {:>) deficiencies in my design. |
Understand. Suggest you re-configure to Z-11 as soon
as practical if you you haven't already . . .
Bob . . . [quote][b]
| - The Matronics AeroElectric-List Email Forum - | | Use the List Feature Navigator to browse the many List utilities available such as the Email Subscriptions page, Archive Search & Download, 7-Day Browse, Chat, FAQ, Photoshare, and much more:
http://www.matronics.com/Navigator?AeroElectric-List |
|
|
|
Back to top |
|
 |
Ed Anderson
Joined: 10 Jan 2006 Posts: 475
|
Posted: Tue Jun 30, 2009 12:27 pm Post subject: Time to Battery Exhaustion |
|
|
You’re welcome, Jon
That’s the entire intention - to share my screw-ups, so that other’s won’t make the same ones – advance the state of the art – make a new one {:>).
Ed
Ed Anderson
Rv-6A N494BW Rotary Powered
Matthews, NC
eanderson(at)carolina.rr.com
http://www.andersonee.com
http://www.dmack.net/mazda/index.html
http://www.flyrotary.com/
http://members.cox.net/rogersda/rotary/configs.htm#N494BW
http://www.rotaryaviation.com/Rotorhead%20Truth.htm[/url]
From: owner-aeroelectric-list-server(at)matronics.com [mailto:owner-aeroelectric-list-server(at)matronics.com] On Behalf Of jon(at)finleyweb.net
Sent: Tuesday, June 30, 2009 1:00 PM
To: aeroelectric-list(at)matronics.com
Subject: RE: FW: Re: Time to Battery Exhaustion
Thank you Ed,
I have learned a number of things due to your willingness to share your experience and system configuration.
Jon Finley
N314JF - Q2 - Subaru EJ-22
[url=http://www.finleyweb.net/Q2Subaru.aspx]http://www.finleyweb.net/Q2Subaru.aspx
[quote][b]
| - The Matronics AeroElectric-List Email Forum - | | Use the List Feature Navigator to browse the many List utilities available such as the Email Subscriptions page, Archive Search & Download, 7-Day Browse, Chat, FAQ, Photoshare, and much more:
http://www.matronics.com/Navigator?AeroElectric-List |
|
_________________ Ed Anderson
Rv-6A N494BW Rotary Powered
Matthews, NC
eanderson@carolina.rr.com |
|
Back to top |
|
 |
|
|
You cannot post new topics in this forum You cannot reply to topics in this forum You cannot edit your posts in this forum You cannot delete your posts in this forum You cannot vote in polls in this forum You cannot attach files in this forum You can download files in this forum
|
Powered by phpBB © 2001, 2005 phpBB Group
|