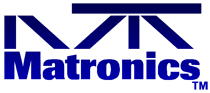 |
Matronics Email Lists Web Forum Interface to the Matronics Email Lists
|
View previous topic :: View next topic |
Author |
Message |
yourtcfg(at)aol.com Guest
|
Posted: Sun Sep 06, 2009 1:30 pm Post subject: Hydraulic Failures |
|
|
HI KIDS
I thought I might share with you some real world experience regarding hyd failures. Over my 30 years and well over 2000 hours of Commander experience, I have suffered three complete hydraulic failures. All in FAT nacelled Commanders. It would be good to spend a moment to discuss the difference in the systems of FLAT and FAT nacelled airplanes. The FAT nacelles do not have an electric hyd aux pump. They share the same basic system including the reservoir, but instead of an electric aux pump, they use a valve that isolates the stand pipe in the reservoir and a hand pump. The FLAT nacelled airplanes have an electric pump. There is a standpipe in the reservoir that is intended to isolate a small amount of fluid to be used in an emergency. The engine driven pumps only have access to the fluid from the standpipe. There is a fitting in the resiviour below the standpipe that feeds only the aux pump. The trouble with that system is the aux pump is operated by a pressure switch. So, if a leak occurs, the engine pump(s) will eventually pump all the fluid overboard. When the last of the fluid is gone, the pressure will drop, turning on the aux pump dumping the last of the fluid that was intended to be used to stop and steer the airplane. The FAT nacelled airplanes have the same standpipe for the engine driven pumps, but the emergency system requires that a valve in the floor of the cabin be selected to "Brakes only" and a hand pump is used to build pressure. Unlike the electric system, there is no way the emergency fluid can be pumped overboard without he pilot knowing it.
My first failure at least 25 years ago in a 560A, N2649B. I had completed a normal landing at Caldwell Idaho (EUL) and as I started to brake, the pedals simply went to the floor. I was slow to react but did finally break the code and switched the floor valve and as the end of the runway approached, I feverishly pumped the handle. The airplane stopped with only the nose wheel off the end!! I learned an important lesson that day. ALWAYS check the hyd gauge AND press on the brakes on short final (more later). A hard line in the belly of the airplane had failed, pumping all the fluid overboard.
Failure number two was about ten years ago in my current Commander 680E, N222JS. I had entered the pattern at Grove field (1W1) when I noticed the gear was not extending as usual. A quick glance at the pressure gauge confirmed a complete hyd failure. I elected to fly across he river to Troutdale Or (TLD). Grove field is only 2200 feet long for landing. The gear extended and locked. The flaps were of course up. I told the tower of my predicament but declined their offer to declare an emergency. I switched the valve in the floor and waited to touch down. The landing was normal, if a little fast, and as the nose wheel touched I depressed the rudder pedals and pumped the handle to regulated the braking pressure. I have found it nearly impossible, in the real world, to build sufficient pressure in advance to operate the brakes/steering. Better to depress the brakes and build the ne eded pressure. It worked very well and I was able to taxi to parking with no trouble. A flex line from the back side of the firewall had failed.
The last failure was only a couple months ago in a 680 Commander destined for a A&P school. Morris Kernick and I had spent considerable time preparing N87YA for its last gear down ferry. The airplane had only been flown once in the last 25 years. The hyd system would only indicate about 700psi, but since it was on a ferry permit and the gear would remain down and very locked, I was not overly concerned. The 2.5 hour flight was completely uneventfully. Those old engines ran great! When I entered the patter to land, I placed the flap handle fully down. With the gear extended. the airplane never flew out of the flap speed. As I turned final, I did my gauge and break check and to my surprise, there was NO pressure. The flaps I had called for never extended and the brakes were flat. I was committed to the landing and tried the hand pump. It worked, but since the flaps had been selected, they started down first, changing the airplanes trim. With touchdown only seconds away, I decided the best salvation was to abandon the flaps and I selected "brakes only" and again waited for the mains to touch. I had already pulled both throttles to full idle and as I flared the airplane began to swerve sharply to the left. As the nose touched I squeezed the brakes and pumped the hanle. The airplane used most of the runway width, but stayed on the blacktop and rolled to a stop on the centerline with plenty of room to spare. It was only then I noticed that the RH engine had quite and feathered itself. Hence the swerving on landing. With the drag from the windmilling LH propeller and the RH feathered, there was significant adverse yaw. I was able to restart the RH engine and again, taxied to parking using the hand pump. Thought this might be of value to some of you other Commander drivers. See ya at the fly-in (I hope!!)  ;
[quote][b]
| - The Matronics Commander-List Email Forum - | | Use the List Feature Navigator to browse the many List utilities available such as the Email Subscriptions page, Archive Search & Download, 7-Day Browse, Chat, FAQ, Photoshare, and much more:
http://www.matronics.com/Navigator?Commander-List |
|
|
|
Back to top |
|
 |
John Vormbaum
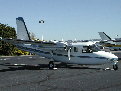
Joined: 21 Aug 2006 Posts: 273 Location: SF Bay Area, CA
|
Posted: Sun Sep 06, 2009 4:11 pm Post subject: Hydraulic Failures |
|
|
Hi all,
I also had a complete hyd. failure in my 500B a few years back. I cracked a hard line in the wing root, and had forgotten to pull the aux pump breaker on takeoff (lesson learned) so it pumped everything overboard...I had no hydraulic pressure at all. To compound the error, after putting the gear handle down & getting the mains locked, I got a few PSI back in the system and thought I could use it to cycle the gear & lock the nosegear. No luck....ended up blowing my chance to get all three wheels locked down, and had to land knowing the nose wasn't locked down.
Since I had no hydraulics for steering, flaps or brakes, I chose Stockton's long (10,000 foot?) runway. I landed on the mains, pulled the power back, and coasted awhile down the runway with the nosegear held off, under minimal power. That big Commander tail/rudder was more than sufficient for directional control. I finally lost full elevator authority at about 20 knots, and gently settled the nose onto the pavement. I rolled about 8 feet before the nosegear gently collapsed at about 10 knots. The only damage was a pair of nosegear doors, a bell crank, and some rivets.
I guess it's true what they say, "fly the airplane all the way until it stops".
Incidentally, I probably could have done the same landing in less than half the length. I actually had to roll some throttle in to keep the nose up & give me enough speed to roll through the last half of the runway...so I ended up doing a 9000-foot wheelie. The airplane really is balanced beautifully.
/John
PS: Nico, I have to ask, what's with the "feather the props on short final" thing? In a Commander, you'd be hard pressed to have a prop strike under any circumstances, even a straight belly landing. If you had one main gear unlocked, dumping it on a prop & needing a new engine still seems less expensive & life-threatening than sawing the airplane off the runway sideways at 75 knots...
From: owner-commander-list-server(at)matronics.com [mailto:owner-commander-list-server(at)matronics.com] On Behalf Of yourtcfg(at)aol.com
Sent: Sunday, September 06, 2009 2:29 PM
To: commander-list(at)matronics.com
Subject: Commander-List: Hydraulic Failures
HI KIDS
I thought I might share with you some real world experience regarding hyd failures. Over my 30 years and well over 2000 hours of Commander experience, I have suffered three complete hydraulic failures. All in FAT nacelled Commanders. It would be good to spend a moment to discuss the difference in the systems of FLAT and FAT nacelled airplanes. The FAT nacelles do not have an electric hyd aux pump. They share the same basic system including the reservoir, but instead of an electric aux pump, they use a valve that isolates the stand pipe in the reservoir and a hand pump. The FLAT nacelled airplanes have an electric pump. There is a standpipe in the reservoir that is intended to isolate a small amount of fluid to be used in an emergency. The engine driven pumps only have access to the fluid from the standpipe. There is a fitting in the resiviour below the standpipe that feeds only the aux pump. The trouble with that system is the aux pump is operated by a pressure switch. So, if a leak occurs, the engine pump(s) will eventually pump all the fluid overboard. When the last of the fluid is gone, the pressure will drop, turning on the aux pump dumping the last of the fluid that was intended to be used to stop and steer the airplane. The FAT nacelled airplanes have the same standpipe for the engine driven pumps, but the emergency system requires that a valve in the floor of the cabin be selected to "Brakes only" and a hand pump is used to build pressure. Unlike the electric system, there is no way the emergency fluid can be pumped overboard without he pilot knowing it.
My first failure at least 25 years ago in a 560A, N2649B. I had completed a normal landing at Caldwell Idaho (EUL) and as I started to brake, the pedals simply went to the floor. I was slow to react but did finally break the code and switched the floor valve and as the end of the runway approached, I feverishly pumped the handle. The airplane stopped with only the nose wheel off the end!! I learned an important lesson that day. ALWAYS check the hyd gauge AND press on the brakes on short final (more later). A hard line in the belly of the airplane had failed, pumping all the fluid overboard.
Failure number two was about ten years ago in my current Commander 680E, N222JS. I had entered the pattern at Grove field (1W1) when I noticed the gear was not extending as usual. A quick glance at the pressure gauge confirmed a complete hyd failure. I elected to fly across he river to Troutdale Or (TLD). Grove field is only 2200 feet long for landing. The gear extended and locked. The flaps were of course up. I told the tower of my predicament but declined their offer to declare an emergency. I switched the valve in the floor and waited to touch down. The landing was normal, if a little fast, and as the nose wheel touched I depressed the rudder pedals and pumped the handle to regulated the braking pressure. I have found it nearly impossible, in the real world, to build sufficient pressure in advance to operate the brakes/steering. Better to depress the brakes and build the ne eded pressure. It worked very well and I was able to taxi to parking with no trouble. A flex line from the back side of the firewall had failed.
The last failure was only a couple months ago in a 680 Commander destined for a A&P school. Morris Kernick and I had spent considerable time preparing N87YA for its last gear down ferry. The airplane had only been flown once in the last 25 years. The hyd system would only indicate about 700psi, but since it was on a ferry permit and the gear would remain down and very locked, I was not overly concerned. The 2.5 hour flight was completely uneventfully. Those old engines ran great! When I entered the patter to land, I placed the flap handle fully down. With the gear extended. the airplane never flew out of the flap speed. As I turned final, I did my gauge and break check and to my surprise, there was NO pressure. The flaps I had called for never extended and the brakes were flat. I was committed to the landing and tried the hand pump. It worked, but since the flaps had been selected, they started down first, changing the airplanes trim. With touchdown only seconds away, I decided the best salvation was to abandon the flaps and I selected "brakes only" and again waited for the mains to touch. I had already pulled both throttles to full idle and as I flared the airplane began to swerve sharply to the left. As the nose touched I squeezed the brakes and pumped the hanle. The airplane used most of the runway width, but stayed on the blacktop and rolled to a stop on the centerline with plenty of room to spare. It was only then I noticed that the RH engine had quite and feathered itself. Hence the swerving on landing. With the drag from the windmilling LH propeller and the RH feathered, there was significant adverse yaw. I was able to restart the RH engine and again, taxied to parking using the hand pump. Thought this might be of value to some of yo! u other Commander drivers. See ya at the fly-in (I hope!!) ;
[quote]
href="http://www.matronics.com/Navigator?Commander-List">http://www.matronics.com/Navigator?Commander-List
href="http://forums.matronics.com">http://forums.matronics.com
href="http://www.matronics.com/contribution">http://www.matronics.com/c
[b]
| - The Matronics Commander-List Email Forum - | | Use the List Feature Navigator to browse the many List utilities available such as the Email Subscriptions page, Archive Search & Download, 7-Day Browse, Chat, FAQ, Photoshare, and much more:
http://www.matronics.com/Navigator?Commander-List |
|
|
|
Back to top |
|
 |
nico(at)cybersuperstore.c Guest
|
Posted: Sun Sep 06, 2009 5:22 pm Post subject: Hydraulic Failures |
|
|
what's with the "feather the props on short final" thing
John,
Yup, I agree. As I said, it wasn't that smart.
Nico
From: owner-commander-list-server(at)matronics.com [mailto:owner-commander-list-server(at)matronics.com] On Behalf Of John Vormbaum
Sent: Sunday, September 06, 2009 5:10 PM
To: commander-list(at)matronics.com
Subject: RE: Hydraulic Failures
Hi all,
I also had a complete hyd. failure in my 500B a few years back. I cracked a hard line in the wing root, and had forgotten to pull the aux pump breaker on takeoff (lesson learned) so it pumped everything overboard...I had no hydraulic pressure at all. To compound the error, after putting the gear handle down & getting the mains locked, I got a few PSI back in the system and thought I could use it to cycle the gear & lock the nosegear. No luck....ended up blowing my chance to get all three wheels locked down, and had to land knowing the nose wasn't locked down.
Since I had no hydraulics for steering, flaps or brakes, I chose Stockton's long (10,000 foot?) runway. I landed on the mains, pulled the power back, and coasted awhile down the runway with the nosegear held off, under minimal power. That big Commander tail/rudder was more than sufficient for directional control. I finally lost full elevator authority at about 20 knots, and gently settled the nose onto the pavement. I rolled about 8 feet before the nosegear gently collapsed at about 10 knots. The only damage was a pair of nosegear doors, a bell crank, and some rivets.
I guess it's true what they say, "fly the airplane all the way until it stops".
Incidentally, I probably could have done the same landing in less than half the length. I actually had to roll some throttle in to keep the nose up & give me enough speed to roll through the last half of the runway...so I ended up doing a 9000-foot wheelie. The airplane really is balanced beautifully.
/John
PS: Nico, I have to ask, what's with the "feather the props on short final" thing? In a Commander, you'd be hard pressed to have a prop strike under any circumstances, even a straight belly landing. If you had one main gear unlocked, dumping it on a prop & needing a new engine still seems less expensive & life-threatening than sawing the airplane off the runway sideways at 75 knots...
From: owner-commander-list-server(at)matronics.com [mailto:owner-commander-list-server(at)matronics.com] On Behalf Of yourtcfg(at)aol.com
Sent: Sunday, September 06, 2009 2:29 PM
To: commander-list(at)matronics.com
Subject: Commander-List: Hydraulic Failures
HI KIDS
I thought I might share with you some real world experience regarding hyd failures. Over my 30 years and well over 2000 hours of Commander experience, I have suffered three complete hydraulic failures. All in FAT nacelled Commanders. It would be good to spend a moment to discuss the difference in the systems of FLAT and FAT nacelled airplanes. The FAT nacelles do not have an electric hyd aux pump. They share the same basic system including the reservoir, but instead of an electric aux pump, they use a valve that isolates the stand pipe in the reservoir and a hand pump. The FLAT nacelled airplanes have an electric pump. There is a standpipe in the reservoir that is intended to isolate a small amount of fluid to be used in an emergency. The engine driven pumps only have access to the fluid from the standpipe. There is a fitting in the resiviour below the standpipe that feeds only the aux pump. The trouble with that system is the aux pump is operated by a pressure switch. So, if a leak occurs, the engine pump(s) will eventually pump all the fluid overboard. When the last of the fluid is gone, the pressure will drop, turning on the aux pump dumping the last of the fluid that was intended to be used to stop and steer the airplane. The FAT nacelled airplanes have the same standpipe for the engine driven pumps, but the emergency system requires that a valve in the floor of the cabin be selected to "Brakes only" and a hand pump is used to build pressure. Unlike the electric system, there is no way the emergency fluid can be pumped overboard without he pilot knowing it.
My first failure at least 25 years ago in a 560A, N2649B. I had completed a normal landing at Caldwell Idaho (EUL) and as I started to brake, the pedals simply went to the floor. I was slow to react but did finally break the code and switched the floor valve and as the end of the runway approached, I feverishly pumped the handle. The airplane stopped with only the nose wheel off the end!! I learned an important lesson that day. ALWAYS check the hyd gauge AND press on the brakes on short final (more later). A hard line in the belly of the airplane had failed, pumping all the fluid overboard.
Failure number two was about ten years ago in my current Commander 680E, N222JS. I had entered the pattern at Grove field (1W1) when I noticed the gear was not extending as usual. A quick glance at the pressure gauge confirmed a complete hyd failure. I elected to fly across he river to Troutdale Or (TLD). Grove field is only 2200 feet long for landing. The gear extended and locked. The flaps were of course up. I told the tower of my predicament but declined their offer to declare an emergency. I switched the valve in the floor and waited to touch down. The landing was normal, if a little fast, and as the nose wheel touched I depressed the rudder pedals and pumped the handle to regulated the braking pressure. I have found it nearly impossible, in the real world, to build sufficient pressure in advance to operate the brakes/steering. Better to depress the brakes and build the ne eded pressure. It worked very well and I was able to taxi to parking with no trouble. A flex line from the back side of the firewall had failed.
The last failure was only a couple months ago in a 680 Commander destined for a A&P school. Morris Kernick and I had spent considerable time preparing N87YA for its last gear down ferry. The airplane had only been flown once in the last 25 years. The hyd system would only indicate about 700psi, but since it was on a ferry permit and the gear would remain down and very locked, I was not overly concerned. The 2.5 hour flight was completely uneventfully. Those old engines ran great! When I entered the patter to land, I placed the flap handle fully down. With the gear extended. the airplane never flew out of the flap speed. As I turned final, I did my gauge and break check and to my surprise, there was NO pressure. The flaps I had called for never extended and the brakes were flat. I was committed to the landing and tried the hand pump. It worked, but since the flaps had been selected, they started down first, changing the airplanes trim. With touchdown only seconds away, I decided the best salvation was to abandon the flaps and I selected "brakes only" and again waited for the mains to touch. I had already pulled both throttles to full idle and as I flared the airplane began to swerve sharply to the left. As the nose touched I squeezed the brakes and pumped the hanle. The airplane used most of the runway width, but stayed on the blacktop and rolled to a stop on the centerline with plenty of room to spare. It was only then I noticed that the RH engine had quite and feathered itself. Hence the swerving on landing. With the drag from the windmilling LH propeller and the RH feathered, there was significant adverse yaw. I was able to restart the RH engine and again, taxied to parking using the hand pump. Thought this might be of value to some of yo! u other Commander drivers. See ya at the fly-in (I hope!!) ;
[quote]
href="http://www.matronics.com/Navigator?Commander-List">http://www.matronics.com/Navigator?Commander-List
href="http://forums.matronics.com">http://forums.matronics.com
href="http://www.matronics.com/contribution">http://www.matronics.com/c
href="http://www.matronics.com/Navigator?Commander-List">http://www.matronics.com/Navigator?Commander-List
href="http://forums.matronics.com">http://forums.matronics.com
href="http://www.matronics.com/contribution">http://www.matronics.com/c
[b]
| - The Matronics Commander-List Email Forum - | | Use the List Feature Navigator to browse the many List utilities available such as the Email Subscriptions page, Archive Search & Download, 7-Day Browse, Chat, FAQ, Photoshare, and much more:
http://www.matronics.com/Navigator?Commander-List |
|
|
|
Back to top |
|
 |
John Vormbaum
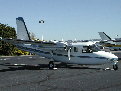
Joined: 21 Aug 2006 Posts: 273 Location: SF Bay Area, CA
|
Posted: Sun Sep 06, 2009 5:41 pm Post subject: Hydraulic Failures |
|
|
Oh I misread that then....I thought you had good reason and I somehow missed it .
/J
From: owner-commander-list-server(at)matronics.com [mailto:owner-commander-list-server(at)matronics.com] On Behalf Of nico css
Sent: Sunday, September 06, 2009 6:18 PM
To: commander-list(at)matronics.com
Subject: RE: Hydraulic Failures
what's with the "feather the props on short final" thing
John,
Yup, I agree. As I said, it wasn't that smart.
Nico
From: owner-commander-list-server(at)matronics.com [mailto:owner-commander-list-server(at)matronics.com] On Behalf Of John Vormbaum
Sent: Sunday, September 06, 2009 5:10 PM
To: commander-list(at)matronics.com
Subject: RE: Hydraulic Failures
Hi all,
I also had a complete hyd. failure in my 500B a few years back. I cracked a hard line in the wing root, and had forgotten to pull the aux pump breaker on takeoff (lesson learned) so it pumped everything overboard...I had no hydraulic pressure at all. To compound the error, after putting the gear handle down & getting the mains locked, I got a few PSI back in the system and thought I could use it to cycle the gear & lock the nosegear. No luck....ended up blowing my chance to get all three wheels locked down, and had to land knowing the nose wasn't locked down.
Since I had no hydraulics for steering, flaps or brakes, I chose Stockton's long (10,000 foot?) runway. I landed on the mains, pulled the power back, and coasted awhile down the runway with the nosegear held off, under minimal power. That big Commander tail/rudder was more than sufficient for directional control. I finally lost full elevator authority at about 20 knots, and gently settled the nose onto the pavement. I rolled about 8 feet before the nosegear gently collapsed at about 10 knots. The only damage was a pair of nosegear doors, a bell crank, and some rivets.
I guess it's true what they say, "fly the airplane all the way until it stops".
Incidentally, I probably could have done the same landing in less than half the length. I actually had to roll some throttle in to keep the nose up & give me enough speed to roll through the last half of the runway...so I ended up doing a 9000-foot wheelie. The airplane really is balanced beautifully.
/John
PS: Nico, I have to ask, what's with the "feather the props on short final" thing? In a Commander, you'd be hard pressed to have a prop strike under any circumstances, even a straight belly landing. If you had one main gear unlocked, dumping it on a prop & needing a new engine still seems less expensive & life-threatening than sawing the airplane off the runway sideways at 75 knots...
From: owner-commander-list-server(at)matronics.com [mailto:owner-commander-list-server(at)matronics.com] On Behalf Of yourtcfg(at)aol.com
Sent: Sunday, September 06, 2009 2:29 PM
To: commander-list(at)matronics.com
Subject: Commander-List: Hydraulic Failures
HI KIDS
I thought I might share with you some real world experience regarding hyd failures. Over my 30 years and well over 2000 hours of Commander experience, I have suffered three complete hydraulic failures. All in FAT nacelled Commanders. It would be good to spend a moment to discuss the difference in the systems of FLAT and FAT nacelled airplanes. The FAT nacelles do not have an electric hyd aux pump. They share the same basic system including the reservoir, but instead of an electric aux pump, they use a valve that isolates the stand pipe in the reservoir and a hand pump. The FLAT nacelled airplanes have an electric pump. There is a standpipe in the reservoir that is intended to isolate a small amount of fluid to be used in an emergency. The engine driven pumps only have access to the fluid from the standpipe. There is a fitting in the resiviour below the standpipe that feeds only the aux pump. The trouble with that system is the aux pump is operated by a pressure switch. So, if a leak occurs, the engine pump(s) will eventually pump all the fluid overboard. When the last of the fluid is gone, the pressure will drop, turning on the aux pump dumping the last of the fluid that was intended to be used to stop and steer the airplane. The FAT nacelled airplanes have the same standpipe for the engine driven pumps, but the emergency system requires that a valve in the floor of the cabin be selected to "Brakes only" and a hand pump is used to build pressure. Unlike the electric system, there is no way the emergency fluid can be pumped overboard without he pilot knowing it.
My first failure at least 25 years ago in a 560A, N2649B. I had completed a normal landing at Caldwell Idaho (EUL) and as I started to brake, the pedals simply went to the floor. I was slow to react but did finally break the code and switched the floor valve and as the end of the runway approached, I feverishly pumped the handle. The airplane stopped with only the nose wheel off the end!! I learned an important lesson that day. ALWAYS check the hyd gauge AND press on the brakes on short final (more later). A hard line in the belly of the airplane had failed, pumping all the fluid overboard.
Failure number two was about ten years ago in my current Commander 680E, N222JS. I had entered the pattern at Grove field (1W1) when I noticed the gear was not extending as usual. A quick glance at the pressure gauge confirmed a complete hyd failure. I elected to fly across he river to Troutdale Or (TLD). Grove field is only 2200 feet long for landing. The gear extended and locked. The flaps were of course up. I told the tower of my predicament but declined their offer to declare an emergency. I switched the valve in the floor and waited to touch down. The landing was normal, if a little fast, and as the nose wheel touched I depressed the rudder pedals and pumped the handle to regulated the braking pressure. I have found it nearly impossible, in the real world, to build sufficient pressure in advance to operate the brakes/steering. Better to depress the brakes and build the ne eded pressure. It worked very well and I was able to taxi to parking with no trouble. A flex line from the back side of the firewall had failed.
The last failure was only a couple months ago in a 680 Commander destined for a A&P school. Morris Kernick and I had spent considerable time preparing N87YA for its last gear down ferry. The airplane had only been flown once in the last 25 years. The hyd system would only indicate about 700psi, but since it was on a ferry permit and the gear would remain down and very locked, I was not overly concerned. The 2.5 hour flight was completely uneventfully. Those old engines ran great! When I entered the patter to land, I placed the flap handle fully down. With the gear extended. the airplane never flew out of the flap speed. As I turned final, I did my gauge and break check and to my surprise, there was NO pressure. The flaps I had called for never extended and the brakes were flat. I was committed to the landing and tried the hand pump. It worked, but since the flaps had been selected, they started down first, changing the airplanes trim. With touchdown only seconds away, I decided the best salvation was to abandon the flaps and I selected "brakes only" and again waited for the mains to touch. I had already pulled both throttles to full idle and as I flared the airplane began to swerve sharply to the left. As the nose touched I squeezed the brakes and pumped the hanle. The airplane used most of the runway width, but stayed on the blacktop and rolled to a stop on the centerline with plenty of room to spare. It was only then I noticed that the RH engine had quite and feathered itself. Hence the swerving on landing. With the drag from the windmilling LH propeller and the RH feathered, there was significant adverse yaw. I was able to restart the RH engine and again, taxied to parking using the hand pump. Thought this might be of value to some of yo! u other Commander drivers. See ya at the fly-in (I hope!!) ;
[quote]
href="http://www.matronics.com/Navigator?Commander-List">http://www.matronics.com/Navigator?Commander-List
href="http://forums.matronics.com">http://forums.matronics.com
href="http://www.matronics.com/contribution">http://www.matronics.com/c
href="http://www.matronics.com/Navigator?Commander-List">http://www.matronics.com/Navigator?Commander-List
href="http://forums.matronics.com">http://forums.matronics.com
href="http://www.matronics.com/contribution">http://www.matronics.com/c
href="http://www.matronics.com/Navigator?Commander-List">http://www.matronics.com/Navigator?Commander-List
href="http://forums.matronics.com">http://forums.matronics.com
href="http://www.matronics.com/contribution">http://www.matronics.com/c
[b]
| - The Matronics Commander-List Email Forum - | | Use the List Feature Navigator to browse the many List utilities available such as the Email Subscriptions page, Archive Search & Download, 7-Day Browse, Chat, FAQ, Photoshare, and much more:
http://www.matronics.com/Navigator?Commander-List |
|
|
|
Back to top |
|
 |
aquadiver99(at)yahoo.com Guest
|
Posted: Sun Sep 06, 2009 5:53 pm Post subject: Hydraulic Failures |
|
|
Agreed John
Donnie Rose
205/492-8444
From: John Vormbaum <john(at)vormbaum.com>
To: commander-list(at)matronics.com
Sent: Sunday, September 6, 2009 7:09:40 PM
Subject: RE: Hydraulic Failures
Hi all,
I also had a complete hyd. failure in my 500B a few years back. I cracked a hard line in the wing root, and had forgotten to pull the aux pump breaker on takeoff (lesson learned) so it pumped everything overboard...I had no hydraulic pressure at all. To compound the error, after putting the gear handle down & getting the mains locked, I got a few PSI back in the system and thought I could use it to cycle the gear & lock the nosegear. No luck....ended up blowing my chance to get all three wheels locked down, and had to land knowing the nose wasn't locked down.
Since I had no hydraulics for steering, flaps or brakes, I chose Stockton's long (10,000 foot?) runway. I landed on the mains, pulled the power back, and coasted awhile down the runway with the nosegear held off, under minimal power. That big Commander tail/rudder was more than sufficient for directional control. I finally lost full elevator authority at about 20 knots, and gently settled the nose onto the pavement. I rolled about 8 feet before the nosegear gently collapsed at about 10 knots. The only damage was a pair of nosegear doors, a bell crank, and some rivets.
I guess it's true what they say, "fly the airplane all the way until it stops".
Incidentally, I probably could have done the same landing in less than half the length. I actually had to roll some throttle in to keep the nose up & give me enough speed to roll through the last half of the runway...so I ended up doing a 9000-foot wheelie. The airplane really is balanced beautifully.
/John
PS: Nico, I have to ask, what's with the "feather the props on short final" thing? In a Commander, you'd be hard pressed to have a prop strike under any circumstances, even a straight belly landing. If you had one main gear unlocked, dumping it on a prop & needing a new engine still seems less expensive & life-threatening than sawing the airplane off the runway sideways at 75 knots...
From: owner-commander-list-server(at)matronics.com [mailto:owner-commander-list-server(at)matronics.com] On Behalf Of yourtcfg(at)aol.com
Sent: Sunday, September 06, 2009 2:29 PM
To: commander-list(at)matronics.com
Subject: Hydraulic Failures
HI KIDS
I thought I might share with you some real world experience regarding hyd failures. Over my 30 years and well over 2000 hours of Commander experience, I have suffered three complete hydraulic failures. All in FAT nacelled Commanders. It would be good to spend a moment to discuss the difference in the systems of FLAT and FAT nacelled airplanes. The FAT nacelles do not have an electric hyd aux pump. They share the same basic system including the reservoir, but instead of an electric aux pump, they use a valve that isolates the stand pipe in the reservoir and a hand pump. The FLAT nacelled airplanes have an electric pump. There is a standpipe in the reservoir that is intended to isolate a small amount of fluid to be used in an emergency. The engine driven pumps only have access to the fluid from the standpipe. There is a fitting in the resiviour below the standpipe that feeds only the aux pump. The trouble with that system is the aux pump is operated by a pressure switch. So, if a leak occurs, the engine pump(s) will eventually pump all the fluid overboard. When the last of the fluid is gone, the pressure will drop, turning on the aux pump dumping the last of the fluid that was intended to be used to stop and steer the airplane. The FAT nacelled airplanes have the same standpipe for the engine driven pumps, but the emergency system requires that a valve in the floor of the cabin be selected to "Brakes only" and a hand pump is used to build pressure. Unlike the electric system, there is no way the emergency fluid can be pumped overboard without he pilot knowing it.
My first failure at least 25 years ago in a 560A, N2649B. I had completed a normal landing at Caldwell Idaho (EUL) and as I started to brake, the pedals simply went to the floor. I was slow to react but did finally break the code and switched the floor valve and as the end of the runway approached, I feverishly pumped the handle. The airplane stopped with only the nose wheel off the end!! I learned an important lesson that day. ALWAYS check the hyd gauge AND press on the brakes on short final (more later). A hard line in the belly of the airplane had failed, pumping all the fluid overboard.
Failure number two was about ten years ago in my current Commander 680E, N222JS. I had entered the pattern at Grove field (1W1) when I noticed the gear was not extending as usual. A quick glance at the pressure gauge confirmed a complete hyd failure. I elected to fly across he river to Troutdale Or (TLD). Grove field is only 2200 feet long for landing. The gear extended and locked. The flaps were of course up. I told the tower of my predicament but declined their offer to declare an emergency. I switched the valve in the floor and waited to touch down. The landing was normal, if a little fast, and as the nose wheel touched I depressed the rudder pedals and pumped the handle to regulated the braking pressure. I have found it nearly impossible, in the real world, to build sufficient pressure in advance to operate the brakes/steering. Better to depress the brakes and build the ne eded pressure. It worked very well and I was able to taxi to parking with no trouble. A flex line from the back side of the firewall had failed.
The last failure was only a couple months ago in a 680 Commander destined for a A&P school. Morris Kernick and I had spent considerable time preparing N87YA for its last gear down ferry. The airplane had only been flown once in the last 25 years. The hyd system would only indicate about 700psi, but since it was on a ferry permit and the gear would remain down and very locked, I was not overly concerned. The 2.5 hour flight was completely uneventfully. Those old engines ran great! When I entered the patter to land, I placed the flap handle fully down. With the gear extended. the airplane never flew out of the flap speed. As I turned final, I did my gauge and break check and to my surprise, there was NO pressure. The flaps I had called for never extended and the brakes were flat. I was committed to the landing and tried the hand pump. It worked, but since the flaps had been selected, they started down first, changing the airplanes trim. With touchdown only seconds away, I decided the best salvation was to abandon the flaps and I selected "brakes only" and again waited for the mains to touch. I had already pulled both throttles to full idle and as I flared the airplane began to swerve sharply to the left. As the nose touched I squeezed the brakes and pumped the hanle. The airplane used most of the runway width, but stayed on the blacktop and rolled to a stop on the centerline with plenty of room to spare. It was only then I noticed that the RH engine had quite and feathered itself. Hence the swerving on landing. With the drag from the windmilling LH propeller and the RH feathered, there was significant adverse yaw. I was able to restart the RH engine and again, taxied to parking using the hand pump. Thought this might be of value to some of yo! u other Commander drivers. See ya at the fly-in (I hope!!) ;
Quote: |
href="http://www.matronics.com/Navigator?Commander-List">http://www.matronics.com/Navigator?Commander-Listhref="http://forums.matronics.com">http://forums.matronics.com
href="http://www.matronics.com/contribution">http://www.matronics.com/c
[b] |
| - The Matronics Commander-List Email Forum - | | Use the List Feature Navigator to browse the many List utilities available such as the Email Subscriptions page, Archive Search & Download, 7-Day Browse, Chat, FAQ, Photoshare, and much more:
http://www.matronics.com/Navigator?Commander-List |
|
|
|
Back to top |
|
 |
yourtcfg(at)aol.com Guest
|
Posted: Sun Sep 06, 2009 6:22 pm Post subject: Hydraulic Failures |
|
|
Great story John..
That brings up another great point. The landing gear should extend without hyd pressure. The main gear uses bungee chords to assist them. These are easy to check visually and should be replaced every couple years if the airplane is hangared, every year if it sits outside. The nose gear is another story. The nose gear is extended by spring located in the RH inspection door, just ahead of where the rudder pedals live. These need inspected and lubricated every year, more often if the airplane is parked out. To inspect them, one must get on your knees. get a strong light and look forward and up through the aforementioned inspection panel. I have seen one that had corroded, stuck and was completely broken in half!! These are often overlooked by mechanics. Also, your mechanic should do an emergency extension each annual. This is done on jacks, with the gear up and locked. Then,&nbs p;by bleeding the hyd pressure to zero by running the flaps up and down. It takes awhile! Next, place the gear handle down. All the gear should go down and lock with some gusto. If any are "sleepy", investigate. There are several grease fittings so make certain they are all properly greased. jb
--
| - The Matronics Commander-List Email Forum - | | Use the List Feature Navigator to browse the many List utilities available such as the Email Subscriptions page, Archive Search & Download, 7-Day Browse, Chat, FAQ, Photoshare, and much more:
http://www.matronics.com/Navigator?Commander-List |
|
|
|
Back to top |
|
 |
John Vormbaum
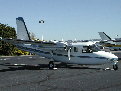
Joined: 21 Aug 2006 Posts: 273 Location: SF Bay Area, CA
|
Posted: Sun Sep 06, 2009 7:43 pm Post subject: Hydraulic Failures |
|
|
Hi Jimbob,
Believe me, the vision of that spring was in my head after I tried to cycle the gear again. All I could think was, "stupid, stupid, stupid." I KNEW that the gear would lock if I just LEFT THE HANDLE ALONE after putting it in the down position the first time. Of course, I got impatient and jumped at the lever when I saw a bit of pressure come back into the system. Once I hit the gear lever the second time, I'd shot my one chance at having the gear go down via spring/gravity....no chance it'll go back over center, right?
Nothing like a $7,000 repair bill to remind you of the one dumb thing you did during the event. There's a good chance that if I had just left the lever where it was, the nosegear would have locked and it would have been an uneventful landing, even without flaps, brakes or steering. I guarantee I'll do it differently next time!
/J
From: owner-commander-list-server(at)matronics.com [mailto:owner-commander-list-server(at)matronics.com] On Behalf Of yourtcfg(at)aol.com
Sent: Sunday, September 06, 2009 7:16 PM
To: commander-list(at)matronics.com
Subject: Re: Hydraulic Failures
Great story John..
That brings up another great point. The landing gear should extend without hyd pressure. The main gear uses bungee chords to assist them. These are easy to check visually and should be replaced every couple years if the airplane is hangared, every year if it sits outside. The nose gear is another story. The nose gear is extended by spring located in the RH inspection door, just ahead of where the rudder pedals live. These need inspected and lubricated every year, more often if the airplane is parked out. To inspect them, one must get on your knees. get a strong light and look forward and up through the aforementioned inspection panel. I have seen one that had corroded, stuck and was completely broken in half!! These are often overlooked by mechanics. Also, your mechanic should do an emergency extension each annual. This is done on jacks, with the gear up and locked. Then,&nbs p;by bleeding the hyd pressure to zero by running the flaps up and down. It takes awhile! Next, place the gear handle down. All the gear should go down and lock with some gusto. If any are "sleepy", investigate. There are several grease fittings so make certain they are all properly greased. jb
--
| - The Matronics Commander-List Email Forum - | | Use the List Feature Navigator to browse the many List utilities available such as the Email Subscriptions page, Archive Search & Download, 7-Day Browse, Chat, FAQ, Photoshare, and much more:
http://www.matronics.com/Navigator?Commander-List |
|
|
|
Back to top |
|
 |
yourtcfg(at)aol.com Guest
|
Posted: Sun Sep 06, 2009 8:15 pm Post subject: Hydraulic Failures |
|
|
It had a happy ending, so hey, you did good. How is your new engine?? jb
--
| - The Matronics Commander-List Email Forum - | | Use the List Feature Navigator to browse the many List utilities available such as the Email Subscriptions page, Archive Search & Download, 7-Day Browse, Chat, FAQ, Photoshare, and much more:
http://www.matronics.com/Navigator?Commander-List |
|
|
|
Back to top |
|
 |
John Vormbaum
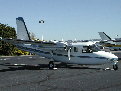
Joined: 21 Aug 2006 Posts: 273 Location: SF Bay Area, CA
|
Posted: Sun Sep 06, 2009 8:59 pm Post subject: Hydraulic Failures |
|
|
Haha thanks....the engine looks good. The airplane has been together for a while but I haven't had time to test fly yet. I'm going to do that this week. I'm sure it'll be in good shape for the fly-in.
/J
From: owner-commander-list-server(at)matronics.com [mailto:owner-commander-list-server(at)matronics.com] On Behalf Of yourtcfg(at)aol.com
Sent: Sunday, September 06, 2009 9:08 PM
To: commander-list(at)matronics.com
Subject: Re: Hydraulic Failures
It had a happy ending, so hey, you did good. How is your new engine?? jb
--
| - The Matronics Commander-List Email Forum - | | Use the List Feature Navigator to browse the many List utilities available such as the Email Subscriptions page, Archive Search & Download, 7-Day Browse, Chat, FAQ, Photoshare, and much more:
http://www.matronics.com/Navigator?Commander-List |
|
|
|
Back to top |
|
 |
aquadiver99(at)yahoo.com Guest
|
Posted: Mon Sep 07, 2009 8:52 am Post subject: Hydraulic Failures |
|
|
Hi John, pulling that breaker is not in my POH but it makes sense.
Is the idea to push it in and leave after TO for the duration or in just prior to landing?
Donnie Rose
205/492-8444
From: John Vormbaum <john(at)vormbaum.com>
To: commander-list(at)matronics.com
Sent: Sunday, September 6, 2009 7:09:40 PM
Subject: RE: Hydraulic Failures
Hi all,
I also had a complete hyd. failure in my 500B a few years back. I cracked a hard line in the wing root, and had forgotten to pull the aux pump breaker on takeoff (lesson learned) so it pumped everything overboard...I had no hydraulic pressure at all. To compound the error, after putting the gear handle down & getting the mains locked, I got a few PSI back in the system and thought I could use it to cycle the gear & lock the nosegear. No luck....ended up blowing my chance to get all three wheels locked down, and had to land knowing the nose wasn't locked down.
Since I had no hydraulics for steering, flaps or brakes, I chose Stockton's long (10,000 foot?) runway. I landed on the mains, pulled the power back, and coasted awhile down the runway with the nosegear held off, under minimal power. That big Commander tail/rudder was more than sufficient for directional control. I finally lost full elevator authority at about 20 knots, and gently settled the nose onto the pavement. I rolled about 8 feet before the nosegear gently collapsed at about 10 knots. The only damage was a pair of nosegear doors, a bell crank, and some rivets.
I guess it's true what they say, "fly the airplane all the way until it stops".
Incidentally, I probably could have done the same landing in less than half the length. I actually had to roll some throttle in to keep the nose up & give me enough speed to roll through the last half of the runway...so I ended up doing a 9000-foot wheelie. The airplane really is balanced beautifully.
/John
PS: Nico, I have to ask, what's with the "feather the props on short final" thing? In a Commander, you'd be hard pressed to have a prop strike under any circumstances, even a straight belly landing. If you had one main gear unlocked, dumping it on a prop & needing a new engine still seems less expensive & life-threatening than sawing the airplane off the runway sideways at 75 knots...
From: owner-commander-list-server(at)matronics.com [mailto:owner-commander-list-server(at)matronics.com] On Behalf Of yourtcfg(at)aol.com
Sent: Sunday, September 06, 2009 2:29 PM
To: commander-list(at)matronics.com
Subject: Hydraulic Failures
HI KIDS
I thought I might share with you some real world experience regarding hyd failures. Over my 30 years and well over 2000 hours of Commander experience, I have suffered three complete hydraulic failures. All in FAT nacelled Commanders. It would be good to spend a moment to discuss the difference in the systems of FLAT and FAT nacelled airplanes. The FAT nacelles do not have an electric hyd aux pump. They share the same basic system including the reservoir, but instead of an electric aux pump, they use a valve that isolates the stand pipe in the reservoir and a hand pump. The FLAT nacelled airplanes have an electric pump. There is a standpipe in the reservoir that is intended to isolate a small amount of fluid to be used in an emergency. The engine driven pumps only have access to the fluid from the standpipe. There is a fitting in the resiviour below the standpipe that feeds only the aux pump. The trouble with that system is the aux pump is operated by a pressure switch. So, if a leak occurs, the engine pump(s) will eventually pump all the fluid overboard. When the last of the fluid is gone, the pressure will drop, turning on the aux pump dumping the last of the fluid that was intended to be used to stop and steer the airplane. The FAT nacelled airplanes have the same standpipe for the engine driven pumps, but the emergency system requires that a valve in the floor of the cabin be selected to "Brakes only" and a hand pump is used to build pressure. Unlike the electric system, there is no way the emergency fluid can be pumped overboard without he pilot knowing it.
My first failure at least 25 years ago in a 560A, N2649B. I had completed a normal landing at Caldwell Idaho (EUL) and as I started to brake, the pedals simply went to the floor. I was slow to react but did finally break the code and switched the floor valve and as the end of the runway approached, I feverishly pumped the handle. The airplane stopped with only the nose wheel off the end!! I learned an important lesson that day. ALWAYS check the hyd gauge AND press on the brakes on short final (more later). A hard line in the belly of the airplane had failed, pumping all the fluid overboard.
Failure number two was about ten years ago in my current Commander 680E, N222JS. I had entered the pattern at Grove field (1W1) when I noticed the gear was not extending as usual. A quick glance at the pressure gauge confirmed a complete hyd failure. I elected to fly across he river to Troutdale Or (TLD). Grove field is only 2200 feet long for landing. The gear extended and locked. The flaps were of course up. I told the tower of my predicament but declined their offer to declare an emergency. I switched the valve in the floor and waited to touch down. The landing was normal, if a little fast, and as the nose wheel touched I depressed the rudder pedals and pumped the handle to regulated the braking pressure. I have found it nearly impossible, in the real world, to build sufficient pressure in advance to operate the brakes/steering. Better to depress the brakes and build the ne eded pressure. It worked very well and I was able to taxi to parking with no trouble. A flex line from the back side of the firewall had failed.
The last failure was only a couple months ago in a 680 Commander destined for a A&P school. Morris Kernick and I had spent considerable time preparing N87YA for its last gear down ferry. The airplane had only been flown once in the last 25 years. The hyd system would only indicate about 700psi, but since it was on a ferry permit and the gear would remain down and very locked, I was not overly concerned. The 2.5 hour flight was completely uneventfully. Those old engines ran great! When I entered the patter to land, I placed the flap handle fully down. With the gear extended. the airplane never flew out of the flap speed. As I turned final, I did my gauge and break check and to my surprise, there was NO pressure. The flaps I had called for never extended and the brakes were flat. I was committed to the landing and tried the hand pump. It worked, but since the flaps had been selected, they started down first, changing the airplanes trim. With touchdown only seconds away, I decided the best salvation was to abandon the flaps and I selected "brakes only" and again waited for the mains to touch. I had already pulled both throttles to full idle and as I flared the airplane began to swerve sharply to the left. As the nose touched I squeezed the brakes and pumped the hanle. The airplane used most of the runway width, but stayed on the blacktop and rolled to a stop on the centerline with plenty of room to spare. It was only then I noticed that the RH engine had quite and feathered itself. Hence the swerving on landing. With the drag from the windmilling LH propeller and the RH feathered, there was significant adverse yaw. I was able to restart the RH engine and again, taxied to parking using the hand pump. Thought this might be of value to some of yo! u other Commander drivers. See ya at the fly-in (I hope!!) ;
Quote: |
href="http://www.matronics.com/Navigator?Commander-List">http://www.matronics.com/Navigator?Commander-Listhref="http://forums.matronics.com">http://forums.matronics.com
href="http://www.matronics.com/contribution">http://www.matronics.com/c
[b] |
| - The Matronics Commander-List Email Forum - | | Use the List Feature Navigator to browse the many List utilities available such as the Email Subscriptions page, Archive Search & Download, 7-Day Browse, Chat, FAQ, Photoshare, and much more:
http://www.matronics.com/Navigator?Commander-List |
|
|
|
Back to top |
|
 |
yourtcfg(at)aol.com Guest
|
Posted: Mon Sep 07, 2009 9:26 am Post subject: Hydraulic Failures |
|
|
As soon as the first engine is started, pull the breaker and do no push in until the next start. It is not in the POH but should be. We have been advocating this for years and I have had two members call me to thank me. They were able to manage a complete hyd failure. jb
--
| - The Matronics Commander-List Email Forum - | | Use the List Feature Navigator to browse the many List utilities available such as the Email Subscriptions page, Archive Search & Download, 7-Day Browse, Chat, FAQ, Photoshare, and much more:
http://www.matronics.com/Navigator?Commander-List |
|
|
|
Back to top |
|
 |
aquadiver99(at)yahoo.com Guest
|
Posted: Mon Sep 07, 2009 10:22 am Post subject: Hydraulic Failures |
|
|
By "next start" do you mean the second engine? And if so, does'nt that only provide protection from full hyd fluid loss for those few seconds? It seams the leak would occur in a more stressfull scenario such as take off.
Donnie Rose
205/492-8444
From: "yourtcfg(at)aol.com" <yourtcfg(at)aol.com>
To: commander-list(at)matronics.com
Sent: Monday, September 7, 2009 12:25:08 PM
Subject: Re: Hydraulic Failures
As soon as the first engine is started, pull the breaker and do no push in until the next start. It is not in the POH but should be. We have been advocating this for years and I have had two members call me to thank me. They were able to manage a complete hyd failure. jb
--
| - The Matronics Commander-List Email Forum - | | Use the List Feature Navigator to browse the many List utilities available such as the Email Subscriptions page, Archive Search & Download, 7-Day Browse, Chat, FAQ, Photoshare, and much more:
http://www.matronics.com/Navigator?Commander-List |
|
|
|
Back to top |
|
 |
LLOYDSSS11(at)MSN.COM Guest
|
Posted: Mon Sep 07, 2009 1:37 pm Post subject: Hydraulic Failures |
|
|
<?xml:namespace prefix="v" /><?xml:namespace prefix="o" /><![endif]--> RE: THE NOSE GEAR SPRING INSPECTIONDOOR, IS THIS OUTSIDE THE AIRCRAFT OR INSIDE ABOVE THE RUDDER PEDALS. MINE HAS NEVER BEEN LUBED OR INSPECTED AS FAR AS I KNOW. THANKS,LLOYD
[quote] ---
| - The Matronics Commander-List Email Forum - | | Use the List Feature Navigator to browse the many List utilities available such as the Email Subscriptions page, Archive Search & Download, 7-Day Browse, Chat, FAQ, Photoshare, and much more:
http://www.matronics.com/Navigator?Commander-List |
|
|
|
Back to top |
|
 |
tfisher(at)commandergroup Guest
|
Posted: Mon Sep 07, 2009 1:54 pm Post subject: Hydraulic Failures |
|
|
What pushes the gear down is mainly (pun intended) the Nitrogen cylinder on the outboard side of each gear.
I was advised that the bungees are a six month item.
Tom
formally C-GISS
[quote] ---
| - The Matronics Commander-List Email Forum - | | Use the List Feature Navigator to browse the many List utilities available such as the Email Subscriptions page, Archive Search & Download, 7-Day Browse, Chat, FAQ, Photoshare, and much more:
http://www.matronics.com/Navigator?Commander-List |
|
|
|
Back to top |
|
 |
yourtcfg(at)aol.com Guest
|
Posted: Mon Sep 07, 2009 6:25 pm Post subject: Hydraulic Failures |
|
|
HI TOM
The nitrogen does assist the main gear extension on the twisty gear Commanders, not so on the fat nacelle airplanes. The nose gear is on its own on all models. The bungees and the spring finsh what gravity and nitrogen started and ensure the the gear remains locked after touchdown and at anytime there in no hyd pressure present. There is no official TBO on the bungee's. They should be replaced on condition but, for sure Tom, sooner is better than later!!
The access panel to inspect the nose spring is located on the fuselage skin RH (Co-pilot) side low It is just ahead of the forward bulkhead that separates the nose section from the cabin, just ahead of the rudder pedals.
The circuit breaker should be pushed in only long enough to bring up the hyd pressure so you have brakes to start the engines, then be pulled and should remain pulled until the next engine start. I kinda answerd the last three posts at once, hope nobody minds. jb
--
| - The Matronics Commander-List Email Forum - | | Use the List Feature Navigator to browse the many List utilities available such as the Email Subscriptions page, Archive Search & Download, 7-Day Browse, Chat, FAQ, Photoshare, and much more:
http://www.matronics.com/Navigator?Commander-List |
|
|
|
Back to top |
|
 |
|
|
You cannot post new topics in this forum You cannot reply to topics in this forum You cannot edit your posts in this forum You cannot delete your posts in this forum You cannot vote in polls in this forum You cannot attach files in this forum You can download files in this forum
|
Powered by phpBB © 2001, 2005 phpBB Group
|